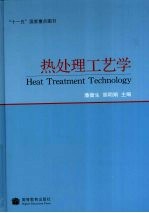
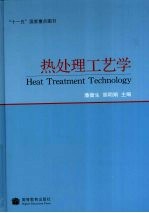
热处理工艺学PDF电子书下载
- 电子书积分:19 积分如何计算积分?
- 作 者:潘健生,胡明娟主编(上海交通大学)
- 出 版 社:北京:高等教育出版社
- 出版年份:2009
- ISBN:9787040224207
- 页数:660 页
第一章 导论 1
1.1热处理在制造业中的作用 1
1.1.1热处理技术的进步推动制造业的创新 1
1.1.2热处理是提高产品寿命和性能的决定性因素 2
1.1.3改进预先热处理工艺可大幅度降低零件的加工成本 7
1.2热处理技术的特点 8
1.2.1合理的热处理工艺应视工件特点而异 8
1.2.2没有最好,只有更好 11
1.2.3质量控制难度大 14
1.2.4从“技艺型”向“高度知识密集型”技术方向发展 15
1.3怎样搞好热处理 15
1.3.1质量第一,严字当头 15
1.3.2重视理论对热处理生产的指导作用,将基础研究成果转化为实用技术 16
1.3.3重视生产实践 21
1.3.4掌握生产流程中各个环节对热处理及材料质量影响的规律,以全局的视野分析和解决问题 24
1.3.5用信息技术改造和提升热处理技术 25
参考文献 26
第二章 金属材料的加热和冷却 27
2.1加热和冷却过程中的传热学计算 27
2.1.1近似计算法 27
2.1.2薄件加热的传热计算 29
2.1.3导热偏微分方程 31
2.1.4导热偏微分方程的分析解 32
2.1.5求解非稳态温度场的有限元法 36
2.1.6温度场与相变的耦合 44
2.1.7温度场有限元分析应用实例 50
2.2加热介质 59
2.2.1可控气氛加热 59
2.2.2真空加热 66
2.3钢的冷却 71
2.3.1钢件热处理的冷却过程 71
2.3.2钢的淬透性 81
2.3.3淬火冷却介质 83
参考文献 110
第三章 工具热处理概述 113
3.1工具热处理的特点 113
3.2工具钢的冶金质量及冶金厂的热处理 115
3.3工具钢的改锻 118
3.4工具钢的预先热处理 120
3.4.1原始组织对加工工艺性能的影响 121
3.4.2退火组织对过共析工具钢淬火后的组织与性能的影响 121
3.4.3工具钢球化退火工艺 126
3.5工具钢的最终热处理 129
3.5.1淬火加热 129
3.5.2淬火冷却 132
3.5.3微畸变淬火 136
3.5.4回火 137
3.5.5稳定化处理 139
3.6硬质合金与钢结硬质合金 139
3.6.1硬质合金 139
3.6.2钢结硬质合金及其热处理 140
3.7工具的化学热处理与表面强化 143
3.7.1化学热处理与表面涂层的作用 143
3.7.2化学热处理与表面涂层在工具中的应用 144
3.7.3超硬涂层在工具中的应用 147
参考文献 147
第四章 高速钢刀具热处理 149
4.1退火 149
4.2淬火 151
4.2.1淬火加热用设备的主要优缺点 151
4.2.2淬火加热温度 153
4.2.3淬火显微组织检验及质量控制 156
4.2.4淬火加热时间 157
4.2.5淬火冷却 160
4.3回火 166
4.3.1回火温度与时间的互换性 166
4.3.2常规回火工艺 166
4.3.3回火质量的检测 168
4.3.4大型复杂件的回火 168
4.3.5快速回火 168
4.4冷处理 169
4.5高速钢的化学及表面处理 170
4.5.1蒸汽处理 171
4.5.2渗氮 173
4.5.3渗碳 178
4.5.4气相沉积 181
4.5.5激光热处理 184
参考文献 187
第五章 滚动轴承用高碳铬轴承钢的热处理及质量控制 189
5.1滚动轴承用钢的工作条件及基本性能要求 189
5.2高碳铬轴承钢的冶炼技术概述 191
5.2.1真空脱气及炉外精炼技术 191
5.2.2真空冶炼 192
5.2.3其他冶炼技术 193
5.2.4发达国家的冶炼技术 194
5.3高碳铬轴承钢的成分与原材料检验 195
5.3.1化学成分 195
5.3.2成分设计特点 196
5.3.3原材料检验 197
5.4轴承钢的组织转变 201
5.4.1Fe-C-Cr平衡状态图 201
5.4.2加热时的转变 203
5.4.3奥氏体晶粒度及其控制 204
5.4.4GCr15钢过冷奥氏体的转变 206
5.4.5GCr15钢在回火过程中的组织转变和应力变化 209
5.5高碳铬轴承钢滚动轴承零件热处理工艺概述 209
5.5.1轴承零件加工、热处理工序及其作用 209
5.5.2正火工艺 211
5.5.3球化退火工艺 211
5.5.4淬火工艺 215
5.5.5冷处理 219
5.5.6回火和附加回火工艺研究 220
5.6影响轴承寿命的材料因素及其控制 220
5.6.1影响轴承寿命的材料因素 220
5.6.2影响轴承寿命的材料因素的控制 229
5.7其他较常用的轴承材料 232
5.7.1中碳轴承钢 232
5.7.2渗碳轴承钢 232
5.7.3不锈轴承钢 233
5.7.4高温轴承钢 233
5.7.5其他较常用的钢种或合金 233
5.7.6保持器常用的金属材料 234
参考文献 234
第六章 热作模具材料及其热处理 236
6.1热作模具材料的主要性能要求 236
6.1.1热作模具钢的分类 236
6.1.2热作模具材料的使用性能要求 237
6.1.3热作模具材料的工艺性能要求 237
6.2热作模具材料的成分特点 238
6.3低耐热高韧性热作模具钢及其热处理 239
6.3.15CrNiMo、5CrMnMo钢 239
6.3.2其他低耐热高韧性热作模具钢 245
6.4中耐热热作模具钢及其热处理 246
6.4.14Cr5MoSiV、4Cr5MoSiV1钢 247
6.4.2Cr-Mo系钢(3Cr-3Mo系) 253
6.4.3其他中耐热热作模具钢 255
6.5高耐热热作模具钢及其热处理 256
6.5.13Cr2W8V钢 256
6.5.2其他高耐热热作模具钢 262
6.6特殊用途的热作模具钢 263
6.6.1奥氏体耐热钢 263
6.6.2析出沉淀硬化型热作模具钢 263
6.6.3高速钢、基体钢 264
6.6.4马氏体时效钢 264
6.6.5高温合金、难熔合金 264
参考文献 264
第七章 冷作模具材料及其热处理 266
7.1冷挤压模 266
7.1.1黑色金属冷挤压凸模的选材 267
7.1.2高速钢碳化物偏析的控制 270
7.1.3冷挤压凸模的淬火与回火 274
7.1.4冷挤压凸模的表面强化 275
7.1.5冷挤压凹模的选材和热处理 278
7.2冷镦模、冷锻模 278
7.3冲裁模 281
7.3.1高铬莱氏体钢的锻造 282
7.3.2高铬莱氏体钢的退火 282
7.3.3高铬莱氏体钢的淬火与回火 282
7.3.4冲裁模热处理畸变的控制 283
参考文献 286
第八章 机器零件的热处理 287
8.1零件的制造过程 287
8.2结构钢机器零件的加工工艺过程 288
8.3机器零件热处理工艺选择的一般原则 290
8.4零件设计及机械加工与热处理工艺的关系 291
8.4.1选材 291
8.4.2拟定合理的热处理技术条件 292
8.4.3合理的零件结构设计 293
8.4.4机械加工与热处理的正确配合 297
8.4.5热处理与切削加工性的关系 297
8.5典型零件热处理工艺举例 300
8.5.1连杆螺栓——要求整体具有良好综合力学性能的零件 300
8.5.2活塞销——耐磨、抗弯曲疲劳的零件 303
8.5.3曲轴——耐磨、抗弯曲疲劳、扭转疲劳和易发生热处理畸变的零件 305
8.5.4连杆——承受拉压疲劳的零件 314
8.5.5齿轮——量大面广、热处理形式多样化的零件 316
8.5.6轴类零件——大长径比的高精度零件 326
8.5.7机床零件——要求高精度、稳定性好的零件 335
8.5.8在满足使用性能要求的前提下通过改变热处理方式来优化制造方法的几个例子 347
8.5.9热处理定形处理的薄板、薄片件 352
参考文献 355
第九章 大锻件的热处理 357
9.1概述 357
9.1.1大锻件及其应用 357
9.1.2大锻件热处理的特点 357
9.2冶金因素对大锻件质量的影响 358
9.2.1冶炼质量对大锻件质量的影响 359
9.2.2铸锭工艺对大锻件质量的影响 361
9.2.3锻造工艺对大锻件质量的影响 364
9.3大锻件的第一热处理 369
9.3.1第一热处理的目的 369
9.3.2大锻件中的氢和白点 370
9.3.3大锻件的晶粒细化问题 376
9.3.4大锻件的第一热处理工艺 378
9.4大锻件的最终热处理 384
9.4.1概述 384
9.4.2大锻件的淬火、正火 387
9.4.3大锻件的回火 400
9.4.4大锻件的最终热处理工艺实例 404
参考文献 407
第十章 气体渗碳 408
10.1概述 408
10.2气体渗碳与传统的碳势控制方法 410
10.3气体渗碳的平衡问题 412
10.4多组分体系中几个反应的相互影响 415
10.5碳势控制方法的讨论 415
10.6钢中碳的活度及合金元素的影响 417
10.7气体渗碳过程中的物质传递问题 418
10.7.1物质传递数学模型及其解析解 418
10.7.2数值解法及其应用 420
10.7.3传递系数的测定 425
10.7.4简化的近似计算方法 426
10.8渗碳工艺 428
10.8.1渗碳温度的选择 428
10.8.2渗碳时间 430
10.8.3一段渗碳、两段渗碳及动态碳势控制 431
10.8.4渗碳工艺的发展 433
10.9渗碳后的热处理 436
10.9.1直接淬火法 436
10.9.2重新加热淬火 436
10.9.3回火 436
10.9.4高合金钢渗碳件的热处理 437
10.10内氧化的热力学条件 438
10.11碳化物形态的控制 442
参考文献 445
第十一章 渗氮 447
11.1概述 447
11.2渗氮层的组织及性能 447
11.2.1典型的渗氮层显微组织 447
11.2.2Fe-N状态图 453
11.2.3纯铁和碳钢的渗层组织 454
11.2.4合金钢渗氮的组织和扩散层中的沉淀硬化 461
11.2.5疲劳强度 464
11.2.6抗腐蚀性 465
11.3渗氮热力学 466
11.3.1氨分解反应 466
11.3.2Fe-N系中氮的活度 469
11.3.3氮势 471
11.3.4渗氮气体与Fe-N系中各相平衡的条件 473
11.3.5氮势与氨分解率及炉气成分的关系 476
11.4合金钢渗氮的热力学问题 478
11.5可控渗氮的动力学问题 483
11.5.1氮势门槛值 483
11.5.2氮势门槛值曲线的理论公式 483
11.5.3测定门槛值曲线的简捷方法 485
11.5.4渗氮过程物质传递数学模型的数值解法 486
11.6渗氮工艺 489
11.6.1常规渗氮工艺 489
11.6.2可控渗氮工艺 492
11.6.3微型计算机氮势动态控制 494
11.6.4渗氮件的变形问题 498
11.6.5钢的原始组织对渗氮后质量的影响 504
11.7渗氮工艺的发展 506
11.7.1表面纳米化渗氮 507
11.7.2渗氮氧化复合处理 507
11.7.3短时渗氮与脉冲渗氮 507
11.7.4高速钢的短时渗氮 510
11.7.5深层渗氮 510
参考文献 511
第十二章 氮碳共渗 513
12.1铁素体氮碳共渗 513
12.1.1气相反应 514
12.1.2Fe-N-C状态图 519
12.1.3铁素体氮碳共渗的渗层组织 521
12.1.4高速钢气体铁素体氮碳共渗组织 529
12.1.5气体铁素体氮碳共渗的渗层性能 530
12.1.6铁素体氮碳共渗与短时渗氮的比较 535
12.2奥氏体氮碳共渗 537
12.2.1气相反应 538
12.2.2渗层组织 540
12.2.3奥氏体氮碳共渗工艺 557
12.2.4奥氏体渗氮 561
参考文献 564
第十三章 表面工程技术 566
13.1传统工艺 566
13.1.1化学与表面热处理 566
13.1.2化学与电化学沉积 567
13.1.3化学、电化学转化 575
13.1.4表面涂覆技术 579
13.1.5表面形变强化 580
13.2物理气相沉积 582
13.2.1真空蒸镀 582
13.2.2溅射镀 594
13.2.3离子镀 616
13.3化学气相沉积 628
13.3.1化学气相沉积原理 629
13.3.2常压化学气相沉积 632
13.3.3低压化学气相沉积 633
13.3.4等离子体化学气相沉积 633
13.3.5金属有机化学气相沉积 636
13.3.6激光化学气相沉积 637
13.4高能束表面改性技术 638
13.4.1激光束表面改性技术 639
13.4.2电子束表面改性技术 645
13.4.3离子注入 648
13.5其他表面工程技术 654
13.5.1外延技术 654
13.5.2溶胶-凝胶法 656
13.5.3表面工程复合处理技术 657
参考文献 659
- 《葡萄酒工艺与鉴赏 第3版》廖祖宋 2019
- 《大数据Hadoop 3.X分布式处理实战》吴章勇,杨强 2020
- 《化学工程与工艺专业实验指导》郭跃萍主编 2019
- 《美物之道 日本手工艺》(日)柳宗悦著 2019
- 《有色金属冶金新工艺与新技术》俞娟,王斌,方钊,崔雅茹,袁艳 2019
- 《洗涤剂生产工艺与技术》宋小平,韩长日主编 2019
- 《皮革用化学品生产工艺与技术》宋小平,韩长日著 2018
- 《玉米淀粉绿色精益制造 新工艺、新设备、新理念》佟毅 2018
- 《天然气净化工艺技术进展》顾晓峰编著 2019
- 《中国工艺美术史》王树良 2019
- 《全国高等中医药行业“十三五”创新教材 中医药学概论》翟华强 2019
- 《培智学校义务教育实验教科书教师教学用书 生活适应 二年级 上》人民教育出版社,课程教材研究所,特殊教育课程教材研究中心编著 2019
- 《指向核心素养 北京十一学校名师教学设计 英语 七年级 上 配人教版》周志英总主编 2019
- 《习近平总书记教育重要论述讲义》本书编写组 2020
- 《办好人民满意的教育 全国教育满意度调查报告》(中国)中国教育科学研究院 2019
- 《高等数学试题与详解》西安电子科技大学高等数学教学团队 2019
- 《北京生态环境保护》《北京环境保护丛书》编委会编著 2018
- 《教育学考研应试宝典》徐影主编 2019
- 《语文教育教学实践探索》陈德收 2018
- 《家庭音乐素养教育》刘畅 2018