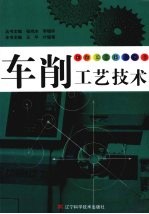
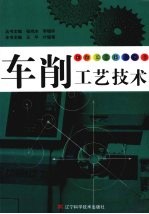
车削工艺技术PDF电子书下载
- 电子书积分:14 积分如何计算积分?
- 作 者:王平,叶晓苇本书主编
- 出 版 社:沈阳:辽宁科学技术出版社
- 出版年份:2009
- ISBN:9787538156348
- 页数:416 页
第一章 车床 1
1.1 机床的型号 1
1.1.1 机床型号的表示 1
1.1.2 机床型号的编制 1
1.1.3 车削加工的特点 4
1.2 车床的分类及结构 5
1.2.1 车床的分类 5
1.2.2 普通车床的结构组成 7
1.3 CA6140普通卧式车床 8
1.3.1 CA6140车床的传动系统 8
1.3.2 CA6140车床主要部件的结构 14
1.4 车床精度及其调整 17
1.4.1 车床精度的检测 17
1.4.2 车床精度的调整 22
1.5 车床的维护保养 26
1.5.1 车床一级保养的内容 26
1.5.2 车床的二级保养 26
1.5.3 车床的合理润滑 27
第二章 切削基本原理 29
2.1 切削运动、工件上的加工表面、切削用量与材料切除率 29
2.1.1 切削运动 29
2.1.2 工件上的加工表面 29
2.1.3 切削用量和材料切除率 30
2.2 切削过程与切屑类型 30
2.2.1 切削过程 30
2.2.2 切屑类型 31
2.3 积屑瘤 32
2.3.1 积屑瘤对加工的影响 32
2.3.2 积屑瘤的形成及防止 33
2.4 切削力及切削热 33
2.4.1 切削力 33
2.4.2 切削热与切削温度 35
2.4.3 刀具的磨损与刀具寿命 37
2.5 刀具切削部分 38
2.5.1 刀具切削部分的组成 39
2.5.2 确定刀具角度的三个辅助平面 39
2.5.3 车刀的切削角度及其作用 40
2.5.4 车刀切削角度的合理选择 41
2.6 切削用量的选择 46
2.6.1 切削用量选择的一般原则 46
2.6.2 不同切削条件下选择切削用量的几点原则 47
2.7 切削液及其合理选用 47
2.7.1 切削液的作用 47
2.7.2 切削液的种类 48
2.7.3 切削液的选用和使用注意事项 48
第三章 车床用刀具 49
3.1 刀具材料 49
3.1.1 高速钢 49
3.1.2 硬质合金刀具材料 50
3.1.3 其他常用车刀材料 52
3.2 车刀的种类及结构 55
3.2.1 车刀的种类 55
3.3 车刀的刃磨 72
3.3.1 车刀的磨钝标准 72
3.3.2 车刀的刃磨 73
3.3.3 车刀角度的测量 76
3.4 孔加工刀具 76
3.4.1 孔加工刀具的种类和用途 76
3.4.2 标准麻花钻 77
3.4.3 群钻 80
3.4.4 扩孔钻 82
3.4.5 锪钻 82
3.4.6 铰刀 83
第四章 车床夹具和辅具 85
4.1 定位 85
4.1.1 定位和基准 85
4.1.2 六点定位原理 86
4.1.3 工件的定位方法和定位元件 88
4.2 工件的夹紧 91
4.2.1 工件夹紧的基本原则 91
4.2.2 工件的夹紧方法和夹紧装置 92
4.3 车床典型夹具 95
4.3.1 车削夹具的分类和用途 95
4.3.2 通用夹具的结构 95
4.3.3 组合夹具 101
第五章 车削常用量具 103
5.1 游标读数量具 103
5.1.1 游标卡尺 103
5.1.2 深度游标卡尺和高度游标卡尺 104
5.1.3 游标万能角度尺 105
5.1.4 齿厚游标尺 106
5.2 带表尺和数显尺 107
5.2.1 带表卡尺和数显卡尺 107
5.2.2 圆标高度尺和数显高度尺 107
5.3 测微量具 108
5.3.1 外径千分尺 108
5.3.2 内径千分尺 110
5.3.3 深度千分尺 110
5.3.4 螺纹千分尺 110
5.3 指示式量具 111
5.4.1 钟面式百分表 111
5.4.2 杠杆式百分表 113
5.5 水平仪 114
第六章 轴类零件的车削 116
6.1 轴类零件的特点与技术要求 116
6.1.1 轴类零件的结构特点 116
6.1.2 轴类零件的技术要求 116
6.1.3 材料与热处理 117
6.1.4 毛坯选择 117
6.2 轴类零件的装夹 117
6.2.1 用三爪自定心卡盘装夹工件 118
6.2.2 用四爪单动卡盘装夹工件 118
6.2.3 用“双顶尖”装夹工件 118
6.2.4 用“一夹一顶”法装夹工件 123
6.2.5 中心架和跟刀架的使用 124
6.2.6 花盘安装 124
6.3 车削加工 124
6.3.1 车外圆 124
6.3.2 车端面 126
6.3.3 车台阶 127
6.3.4 切槽及切断加工 128
6.3.5 轴类零件的检测 133
6.4 车削加工经济精度与表面粗糙度 134
6.4.1 车削加工的工艺特点 134
6.4.2 车削加工的经济精度与表面粗糙度 134
6.5 轴类零件车削实例 139
6.5.1 结构工艺及技术要求分析 139
6.5.2 卧式车床主轴车削加工工艺方案 141
6.6 外圆车削加工中常见质量问题及防止措施 145
6.6.1 车床精度对加工质量的影响及消除方法 145
6.6.2 高精度工件车削车床的调整 147
6.6.3 强力车削车床的调整 148
第七章 盘套类零件的车削 149
7.1 盘套类零件的结构及一般技术要求 149
7.1.1 钻孔 149
7.1.2 扩孔 151
7.1.3 铰孔 151
7.1.4 镗孔 152
7.2 内孔的车削加工 152
7.2.1 刀具的安装 152
7.2.2 钻孔 153
7.2.3 扩孔和锪孔 155
7.2.4 镗孔(车孔) 156
7.2.5 内沟槽的车削 157
7.2.6 铰孔 158
7.3 盘套类零件的装夹 162
7.3.1 薄壁工件的装夹 162
7.3.2 保证内外圆位置精度要求的装夹 163
7.4 盘套类零件的检测 167
7.4.1 尺寸精度检验 167
7.4.2 几何形状精度检验 169
7.4.3 相互位置精度检验 169
7.5 盘套类零件车削实例 171
7.6 内孔加工常见质量问题及防止措施 172
7.6.1 钻孔时常见的质量问题 172
7.6.2 扩孔时常见的质量问题 174
7.6.3 镗孔(车孔)时常见的质量问题 175
7.6.4 铰孔时常见的质量问题 177
第八章 圆锥面的车削 181
8.1 圆锥面的基本参数 181
8.1.1 圆锥面的主要尺寸 181
8.1.2 圆锥各部分尺寸计算 181
8.1.3 常用的标准圆锥 182
8.2 外锥面的车削加工 183
8.2.1 转动小刀架法 184
8.2.2 偏移尾座法 186
8.2.3 仿形法(靠模法) 188
8.2.4 宽刃刀车削法 189
8.3 内锥面的车削加工 189
8.3.1 转动小刀架法 190
8.3.2 仿形法 190
8.3.3 铰内圆锥 190
8.4 圆锥尺寸的控制方法 191
8.4.1 计算法 192
8.4.2 移动大拖板法 192
8.5 圆锥面的检测 193
8.5.1 角度(或锥度)的检验 193
8.5.2 圆锥的尺寸检验 195
8.6 圆锥面车削加工实例 196
8.7 圆锥面车削常见质量问题及防止措施 197
8.7.1 锥度不正确 197
8.7.2 圆锥母线不直(双曲线误差) 198
8.7.3 圆锥面大、小端尺寸不正确 199
第九章 成形面的车削 200
9.1 用合成运动法车削成形面 200
9.2 用成形刀法车削成形面 202
9.2.1 成形刀的种类 202
9.2.2 成形刀的选择原则 204
9.3 用仿形法车削成形面 205
9.3.1 用仿形车床车削成形面 205
9.3.2 用床身靠模法车削成形面 206
9.3.3 用尾座靠模法车削成形面 206
9.3.4 用横向靠模法车削成形面 207
9.4 用专用工具车削成形面 208
9.4.1 手动车内外圆弧工具 208
9.4.2 蜗杆副车内外圆弧工具 209
9.4.3 用旋风切削法车削圆球面 209
9.4.4 成形面的检验 211
9.5 成形面车削加工应注意的问题 212
9.5.1 用仿形车床车削成形面的允许角度 212
9.5.2 用仿形车床车削内形面的允许角度 213
9.5.3 仿形车削时车刀主、副偏角 213
9.5.4 内仿形车削时车刀主、副偏角 214
9.6 成形面仿形车削常见质量问题及防止措施 215
9.6.1 仿形车削时外圆锥度 215
9.6.2 仿形车削阶梯轴 215
9.6.3 仿形车削时,工件的轴向尺寸 215
9.6.4 仿形车削时的倒角 216
9.6.5 仿形车削时,圆弧半径扩大 216
第十章 螺纹的车削 217
10.1 螺纹车刀及其安装 217
10.1.1 螺纹车刀几何形状要求 217
10.1.2 螺纹车刀的装夹 217
10.2 三角形螺纹的车削 218
10.2.1 螺纹车削进刀方式 219
10.2.2 低速车削三角形螺纹 220
10.2.3 高速车削三角形螺纹 220
10.2.4 螺纹车削时的安全知识 221
10.3 交换齿轮的计算和调整 222
10.3.1 交换齿轮计算公式 222
10.3.2 交换齿轮啮合规则 223
10.3.3 交换齿轮计算 224
10.3.4 交换齿轮组装注意事项 225
10.4 乱牙和预防方法 226
10.4.1 产生乱牙的原因 226
10.4.2 预防乱牙的方法 226
10.5 用板牙和丝锥切削螺纹 226
10.5.1 用板牙套螺纹 227
10.5.2 用丝锥攻螺纹 227
10.6 矩形螺纹车削 228
10.6.1 矩形螺纹的牙型和基本尺寸计算 229
10.6.2 矩形螺纹车刀 229
10.6.3 矩形螺纹的车削方法 230
10.7 梯形螺纹车削 230
10.7.1 梯形螺纹的标记 230
10.7.2 梯形螺纹的尺寸计算 231
10.7.3 梯形螺纹车刀 232
10.7.4 梯形外螺纹的车削 233
10.7.5 梯形内螺纹的加工方法 234
10.8 蜗杆的车削 236
10.8.1 蜗杆各部分尺寸计算 236
10.8.2 车削蜗杆时交换齿轮计算 238
10.8.3 蜗杆车刀 238
10.8.4 蜗杆的车削方法 240
10.9 多线螺纹的车削 241
10.9.1 多线螺纹车削时交换齿轮计算 241
10.9.2 多线螺纹车削时的分线方法 241
10.9.3 多线螺纹的车削步骤 243
10.10 螺纹的测量 243
10.10.1 综合测量 244
10.10.2 单项测量 244
10.11 螺纹加工产生废品及质量问题的原因及防止措施 247
10.11.1 车削螺纹时产生废品的原因及防止措施 247
10.11.2 攻螺纹和套螺纹时产生废品的原因及防止措施 248
10.11.3 不同的螺纹形状应选择不同的螺纹车削方法 248
10.11.4 螺纹车削常见质量问题及防止措施 250
第十一章 复杂、精密零件的车削 254
11.1 在花盘角铁上加工工件 254
11.1.1 基准面的选择 254
11.1.2 花盘与角铁的一般使用方法 259
11.1.3 在花盘上车削工件 261
11.1.4 在角铁上加工工件 263
11.1.5 花盘角铁上保证形位公差、中心距要求的方法 265
11.2 细长轴车削 265
11.2.1 细长轴的结构与工艺特点 266
11.2.2 中心架的使用方法 266
11.2.3 跟刀架的使用方法 267
11.2.4 细长轴的车削 267
11.2.5 细长轴车削常见问题及防止措施 270
11.3 偏心件和曲轴车削 274
11.3.1 偏心工件的划线方法 274
11.3.2 在四爪单动卡盘上车削偏心工件 275
11.3.3 在花盘上车削偏心孔工件 276
11.3.4 在两顶尖间车削偏心工件 276
11.3.5 在三爪自定心卡盘上车削偏心工件 276
11.3.6 用双卡盘车削偏心工件 277
11.3.7 用偏心卡盘车削偏心工件 277
11.3.8 在专用夹具上车削偏心工件 278
11.3.9 在通用可调整夹具中车削偏心工件 279
11.3.10 偏心距的测量方法 279
11.3.11 曲轴的车削方法 281
11.4 深孔加工 282
11.4.1 深孔加工排屑方式 282
11.4.2 深孔加工的方法 284
11.5 丝杠车削 287
11.5.1 丝杠螺纹车刀 288
11.5.2 丝杠螺纹的车削 288
11.5.3 螺距误差校正装置 288
11.5.4 丝杠螺距精度的测量 288
11.6 复杂、精密零件车削加工实例 289
11.6.1 丝杠的车削 289
11.6.2 多拐曲轴的车削 294
第十二章 难加工材料的车削 303
12.1 影响材料切削加工特性的因素 303
12.1.1 材料的化学成分 303
12.1.2 材料的物理性能 303
12.1.3 材料的力学性能 304
12.1.4 难切削材料的切削特点 304
12.2 常见难加工材料的车削 305
12.2.1 高强度及超高强度钢的车削 305
12.2.2 高锰钢的车削 306
12.2.3 淬硬钢、冷硬铸铁及耐磨合金铸铁的车削 308
12.2.4 不锈钢、高温合金的车削 310
12.2.5 橡胶、工程塑料及复合材料的车削 314
第十三章 数控车削加工基础 317
13.1 数控机床 317
13.1.1 数控机床的特点 317
13.1.2 数控机床的工作原理及组成 319
13.1.3 数控机床的分类 320
13.1.4 数控车床的保养 322
13.1.5 数控车床的安全操作规程 323
13.2 数控车削编程 324
13.2.1 数控车削的编程特点 324
13.2.2 车床数控系统的功能与指令代码 325
13.2.3 数控车削编程中的有关问题 327
13.3 数控车床基本指令编程 329
13.3.1 尺寸坐标系统 329
13.3.2 刀具功能T、主轴转速功能S和进给功能F 331
13.3.3 常用的辅助功能 332
13.3.4 插补指令编程 333
13.3.5 螺纹车削加工指令(G32/G33) 334
13.3.6 刀具补偿指令(G41、G42、G40) 336
13.3.7 固定循环. 337
13.4 编程实例 340
13.4.1 实例1 340
13.4.2 实例2 341
第十四章 华中(HNC—21/22T)车床数控系统 343
14.1 零件程序的结构 343
14.1.1 坐标系统 343
14.1.2 指令字的格式 344
14.1.3 程序的一般结构 345
14.2 HNC—21/22T数控系统的编程指令体系 345
14.2.1 辅助功能M指令代码 345
14.2.2 主轴功能S、进给功能F和刀具功能T 348
14.2.3 准备功能G指令代码 349
14.3 综合编程实例 377
第十五章 FANUC0i—TA车床数控系统 379
15.1 加工程序的结构 379
15.1.1 加工程序的组成 379
15.1.2 加工程序的格式 379
15.1.3 主要地址和指令值范围 380
15.2 坐标系 381
15.2.1 机床坐标系 381
15.2.2 工件坐标系 382
15.2.3 平面选择 386
15.3 FANUC0i—TA数控系统的编程指令体系 387
15.3.1 准备功能G指令 387
15.3.2 辅助功能M指令 389
15.3.3 F、T、S功能 391
15.4 FANUC0i—TA数控系统的基本编程指令 394
15.4.1 绝对值和增量值编程(G90、G91) 394
15.4.2 英制/米制转换(G20、G21) 394
15.4.3 插补功能 395
15.5 典型零件编程加工实例 408
附录 411
附录1 车削加工通用工艺守则 411
附录2 车床安全操作规程 413
附录3 蜗杆导程角γ0、量针测量距M值 414
参考文献 416
- 《钒产业技术及应用》高峰,彭清静,华骏主编 2019
- 《现代水泥技术发展与应用论文集》天津水泥工业设计研究院有限公司编 2019
- 《异质性条件下技术创新最优市场结构研究 以中国高技术产业为例》千慧雄 2019
- 《Prometheus技术秘笈》百里燊 2019
- 《中央财政支持提升专业服务产业发展能力项目水利工程专业课程建设成果 设施农业工程技术》赵英编 2018
- 《药剂学实验操作技术》刘芳,高森主编 2019
- 《林下养蜂技术》罗文华,黄勇,刘佳霖主编 2017
- 《脱硝运行技术1000问》朱国宇编 2019
- 《葡萄酒工艺与鉴赏 第3版》廖祖宋 2019
- 《催化剂制备过程技术》韩勇责任编辑;(中国)张继光 2019
- 《钒产业技术及应用》高峰,彭清静,华骏主编 2019
- 《现代水泥技术发展与应用论文集》天津水泥工业设计研究院有限公司编 2019
- 《异质性条件下技术创新最优市场结构研究 以中国高技术产业为例》千慧雄 2019
- 《Prometheus技术秘笈》百里燊 2019
- 《中央财政支持提升专业服务产业发展能力项目水利工程专业课程建设成果 设施农业工程技术》赵英编 2018
- 《药剂学实验操作技术》刘芳,高森主编 2019
- 《林下养蜂技术》罗文华,黄勇,刘佳霖主编 2017
- 《脱硝运行技术1000问》朱国宇编 2019
- 《催化剂制备过程技术》韩勇责任编辑;(中国)张继光 2019
- 《信息系统安全技术管理策略 信息安全经济学视角》赵柳榕著 2020