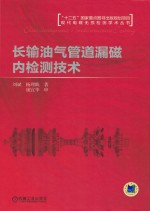
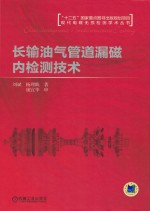
长输油气管道漏磁内检测技术PDF电子书下载
- 电子书积分:10 积分如何计算积分?
- 作 者:刘斌,杨理践著
- 出 版 社:北京:机械工业出版社
- 出版年份:2017
- ISBN:9787111557128
- 页数:243 页
第1章 管道漏磁内检测基础知识 1
1.1 管道基本概念 1
1.2 长输油气管道腐蚀及其防护 1
1.3 管道漏磁内检测技术的发展状况 2
1.4 漏磁检测原理 4
1.4.1 缺陷漏磁场的形成机理 4
1.4.2 缺陷漏磁场的分布 6
1.5 漏磁检测的磁化技术 7
1.5.1 磁化方式 7
1.5.2 磁化强度的选择 7
1.6 漏磁场信号的测量 8
1.6.1 基本要求 8
1.6.2 磁测量元件 9
第2章 管道漏磁内检测系统 11
2.1 管道漏磁内检测技术 11
2.2 管道漏磁内检测系统概述 11
2.2.1 管道漏磁内检测系统的基本组成 11
2.2.2 管道漏磁内检测系统的特点 12
2.2.3 管道漏磁内检测装置的要求 13
2.2.4 管道漏磁内检测装置的技术指标 13
2.3 管道漏磁内检测装置机械设计 14
2.3.1 总体机械结构 14
2.3.2 部件功能 14
2.4 检测装置的可靠性工艺 17
2.4.1 装置的密封及耐压工艺 17
2.4.2 检测装置的耐温及耐油工艺 18
2.4.3 消除影响被测磁场分布因素的工艺措施 19
第3章 管道轴向励磁漏磁内检测技术 20
3.1 管道轴向励磁方式检测原理 20
3.2 管道轴向励磁漏磁检测信号特征及影响因素 20
3.2.1 漏磁信号特征量的定义与提取 21
3.2.2 缺陷长度对漏磁信号的影响 22
3.2.3 缺陷深度对漏磁信号的影响 24
3.2.4 传感器提离值对漏磁信号的影响 26
3.2.5 磁化器提离值对漏磁信号的影响 28
3.2.6 共同发生提离值对漏磁信号的影响 29
3.2.7 不同类型提离值对漏磁信号的影响 30
3.2.8 焊缝对漏磁信号的影响 31
3.2.9 检测器运行速度对漏磁信号的影响 32
3.3 轴向励磁实验结果及分析 33
3.3.1 不同类型缺陷的对比 33
3.3.2 不同宽度缺陷的对比 35
3.3.3 不同深度缺陷的对比 35
3.3.4 不同长度缺陷的对比 37
3.3.5 螺旋焊缝信号分析 39
第4章 管道周向励磁漏磁内检测技术 41
4.1 管道周向励磁检测方法的检测原理 41
4.2 磁化系统优化设计 42
4.2.1 磁化器结构 42
4.2.2 等效磁回路 44
4.2.3 磁回路计算程序设计 45
4.2.4 永磁体参数 46
4.3 管道周向励磁漏磁检测信号特征及影响因素 48
4.3.1 漏磁信号及其特征量定义 48
4.3.2 缺陷距磁极的距离对漏磁信号的影响 49
4.3.3 缺陷深度对漏磁信号的影响 54
4.3.4 缺陷周向宽度对漏磁信号的影响 56
4.3.5 缺陷轴向长度对漏磁信号的影响 58
4.4 缺陷参数定量化研究 60
4.4.1 多元回归分析理论 61
4.4.2 缺陷宽度的量化 61
4.4.3 缺陷长度的量化 61
4.4.4 缺陷深度的量化 62
第5章 管道磁记忆应力内检测技术 63
5.1 力-磁耦合模型的建立 63
5.2 力-磁耦合关系的计算 64
5.2.1 力-磁耦合关系的计算方法 64
5.2.2 力-磁耦合关系基态特性计算 64
5.2.3 计算结果与讨论 65
5.3 磁记忆效应影响因素的研究 68
5.3.1 掺杂效应的影响 68
5.3.2 晶格畸变的影响 69
5.3.3 外界磁场作用的影响 70
第6章 漏磁内检测器速度控制技术 71
6.1 气体管道的结构特点 71
6.2 内检测器与加速度计 72
6.3 加速度控制系统模型 72
6.3.1 水平直管道中的加速度控制系统模型 72
6.3.2 坡道上升管道中的加速度控制系统模型 74
6.3.3 坡道下降管道中的加速度控制系统模型 75
6.3.4 垂直上升管道中的加速度控制系统模型 75
6.3.5 垂直下降管道中的加速度控制系统模型 76
6.4 控制算法介绍 76
6.4.1 PID控制 76
6.4.2 模糊逻辑系统的结构 77
6.4.3 T-S模糊模型 78
6.5 速度控制器设计 79
6.5.1 PI速度控制器 79
6.5.2 T-S模糊模型确定PI速度控制器的参数 81
6.6 仿真计算 83
第7章 管道惯性测绘内检测技术 84
7.1 管道惯性测绘内检测技术基础 84
7.1.1 惯性技术概述 84
7.1.2 管道惯性测绘技术的发展 86
7.1.3 管道惯性测绘内检测的工程解决方案 87
7.2 管道惯性测绘内检测关键技术 88
7.2.1 参考坐标系及坐标转换方法 88
7.2.2 捷联惯性导航技术 92
7.2.3 捷联惯性导航初始对准算法 99
7.2.4 捷联惯性导航系统的卡尔曼滤波方程 101
7.2.5 捷联惯性导航系统/里程轮组合导航系统的信息融合 109
7.2.6 管道地理坐标的终止点校正算法 111
7.2.7 磁标记在长输管道内检测中的应用 114
7.2.8 IMU传感器原始数据去噪效果的评价方法 117
7.3 管道惯性测绘内检测典型工程实验 118
7.3.1 实验系统概述 118
7.3.2 典型实验及简要分析 119
第8章 管道漏磁内检测数据处理方法 127
8.1 基于FPGA的多通道高速数据采集系统 127
8.1.1 现场可编程逻辑门阵列(1PGA)的特点和设计流程 127
8.1.2 基于FPGA的多通道高速数据采集系统概述 131
8.1.3 系统硬件设计 132
8.2 数据压缩方法 135
8.2.1 数据压缩方法分析 135
8.2.2 编码的基本理论和实现方法 138
8.2.3 管道漏磁检测数据的检测无损压缩方法 146
8.2.4 压缩算法的FPGA实现 152
第9章 管道漏磁内检测缺陷量化方法 155
9.1 漏磁内检测中的正问题和反问题 155
9.2 多变量统计分析方法 156
9.2.1 曲线拟合基本理论 156
9.2.2 管道漏磁曲线拟合的MATLAB实现 159
9.2.3 共轭梯度迭代法在管道漏磁内检测缺陷量化中的应用 163
9.3 神经网络量化方法 168
9.3.1 BP神经网络的结构及算法 168
9.3.2 基于BP神经网络的缺陷量化 170
9.4 支持向量机量化方法 171
9.4.1 支持向量机基础理论 171
9.4.2 LIBSVM支持向量机工具 179
9.4.3 支持向量机缺陷量化 179
第10章 管道漏磁内检测工程项目的实施 182
10.1 内检测器检测作业 182
10.1.1 检测前的准备工作 182
10.1.2 内检测器现场调试 182
10.1.3 检测器的投放 182
10.1.4 检测器的跟踪 183
10.1.5 检测器的接收 184
10.1.6 检测器的检查和维修 184
10.2 检测数据预处理 184
10.2.1 检测数据备份与分析 184
10.2.2 检测数据预处理 185
10.3 检测数据的分析与判读 185
10.3.1 管道连接焊缝的判别 185
10.3.2 管道缺陷补疤的判别 186
10.3.3 管道缺陷的判别 187
10.4 缺陷所在位置的确定 187
10.5 开挖验证 188
第11章 基于漏磁内检测的长输油气管道评价技术 190
11.1 长输油气管道评价技术 190
11.2 管道完整性评价标准 192
11.2.1 ASME B31G标准 192
11.2.2 RSTRENG标准 195
11.2.3 DNV RP-F101标准 197
11.2.4 评价管道完整性的主要参数 201
11.2.5 腐蚀缺陷的修复时限 202
11.2.6 管道维护维修方法 202
11.3 管道完整性评价软件 204
11.3.1 管道完整性评价软件简介 205
11.3.2 逐点分析评价 206
11.3.3 漏磁缺陷表导入评价 213
11.4 腐蚀缺陷参数对评价标准的影响 217
11.4.1 不同评价标准的评价结果 217
11.4.2 腐蚀缺陷长度对安全运行压力的影响 220
11.4.3 腐蚀缺陷深度对安全运行压力的影响 223
11.5 有限元仿真方法 225
11.5.1 管道失效判定准则 225
11.5.2 基于ANSYS的有限元仿真 226
11.5.3 腐蚀缺陷参数对等效应力的影响 228
11.6 评价标准与有限元仿真对比分析 236
11.6.1 不同长度腐蚀缺陷评价结果对比分析 237
11.6.2 不同深度腐蚀缺陷评价结果对比分析 237
11.6.3 不同宽度腐蚀缺陷评价结果对比分析 238
11.6.4 不同位置腐蚀缺陷评价结果对比分析 239
参考文献 241
- 《钒产业技术及应用》高峰,彭清静,华骏主编 2019
- 《现代水泥技术发展与应用论文集》天津水泥工业设计研究院有限公司编 2019
- 《异质性条件下技术创新最优市场结构研究 以中国高技术产业为例》千慧雄 2019
- 《Prometheus技术秘笈》百里燊 2019
- 《中央财政支持提升专业服务产业发展能力项目水利工程专业课程建设成果 设施农业工程技术》赵英编 2018
- 《药剂学实验操作技术》刘芳,高森主编 2019
- 《林下养蜂技术》罗文华,黄勇,刘佳霖主编 2017
- 《脱硝运行技术1000问》朱国宇编 2019
- 《催化剂制备过程技术》韩勇责任编辑;(中国)张继光 2019
- 《信息系统安全技术管理策略 信息安全经济学视角》赵柳榕著 2020
- 《指向核心素养 北京十一学校名师教学设计 英语 七年级 上 配人教版》周志英总主编 2019
- 《北京生态环境保护》《北京环境保护丛书》编委会编著 2018
- 《高等教育双机械基础课程系列教材 高等学校教材 机械设计课程设计手册 第5版》吴宗泽,罗圣国,高志,李威 2018
- 《指向核心素养 北京十一学校名师教学设计 英语 九年级 上 配人教版》周志英总主编 2019
- 《高等院校旅游专业系列教材 旅游企业岗位培训系列教材 新编北京导游英语》杨昆,鄢莉,谭明华 2019
- 《中国十大出版家》王震,贺越明著 1991
- 《近代民营出版机构的英语函授教育 以“商务、中华、开明”函授学校为个案 1915年-1946年版》丁伟 2017
- 《新工业时代 世界级工业家张毓强和他的“新石头记”》秦朔 2019
- 《智能制造高技能人才培养规划丛书 ABB工业机器人虚拟仿真教程》(中国)工控帮教研组 2019
- 《AutoCAD机械设计实例精解 2019中文版》北京兆迪科技有限公司编著 2019