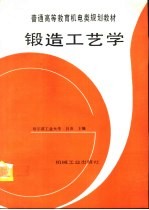
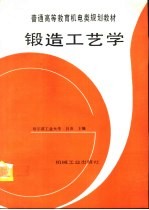
锻造工艺学PDF电子书下载
- 电子书积分:12 积分如何计算积分?
- 作 者:哈尔滨工业大学,吕炎主编
- 出 版 社:北京:机械工业出版社
- 出版年份:1995
- ISBN:7111044258
- 页数:301 页
第一章 绪论 1
一、锻造生产的特点及其在国民经济中的作用 1
二、锻造方法的分类及工艺流程 2
三、我国锻造生产的历史、现状及发展趋势 2
四、本课程的性质与任务 4
第二章 锻造用原材料及下料方法 5
第一节 锻造用钢锭及型材 5
一、钢锭的冶炼 5
二、钢锭的结构 5
三、钢锭的内部缺陷 6
四、型材的常见缺陷 7
第二节 下料方法 7
一、剪切法 8
二、锯切法 9
三、砂轮片切割法 10
四、折断法 10
五、气割法 10
六、其它下料方法 10
第三章 锻造的热规范 11
第一节 金属的锻前加热 11
一、加热的目的 11
二、加热方法 11
第二节 金属加热时产生的缺陷及防止措施 13
一、氧化 13
二、脱碳 15
三、过热 16
四、过烧 17
五、裂纹 17
第三节 锻造温度范围的确定 19
一、始锻温度的确定 19
二、终锻温度的确定 20
第四节 金属的加热规范 21
一、加热规范制定的原则及方法 21
二、钢锭的加热规范 27
三、中、小型钢坯的加热规范 28
第五节 少无氧化加热 29
一、快速加热 29
二、介质保护加热 30
三、少无氧化火焰加热 30
第六节 金属的锻后冷却 31
一、锻后冷却常见缺陷产生的原因和防止措施 33
二、锻件的冷却方法 33
三、锻件的冷却规范 34
第七节 锻件的热处理 34
一、中、小锻件热处理 35
二、大型锻件热处理 35
第四章 自由锻主要工序分析 38
第一节 概述 38
一、影响金属塑性变形流动的几个基本因素 38
二、局部加载时沿加载方向的应力分布规律 39
三、金属塑性变形的不均匀性 40
四、塑性变形时金属的流动方向 40
第二节 镦粗 46
一、镦粗工序的主要质量问题和变形流动特点 46
二、镦粗时时的注意事项 50
第三节 拔长 51
一、矩形截面坯料的拔长 51
二、圆截面坯料的拔长 56
三、空心件拔长 59
第四节 冲孔 61
一、冲孔的受力变形分析 61
二、冲孔的质量分析 64
第五节 扩孔 65
一、冲子扩孔 66
二、芯轴扩孔 66
三、辗压扩孔 68
第六节 弯曲 69
第五章 自由锻工艺 70
第一节 自由锻件的分类 70
第二节 自由锻件变形方案的确定 70
第三节 自由锻工艺过程的制定 75
一、锻件图的制定 75
二、确定坯料的重量和尺寸 76
二、确定变形工艺和锻造比 78
四、确定锻造设备吨位 79
五、自由锻工艺过程制定举例 82
第四节 大型锻件锻造的特点 84
一、钢锭冶金质量对锻件的影响 84
二、大型钢锭的加热特点 85
三、热锻变形对金属组织和性能的影响 85
四、大锻件变形工艺分析 88
五、大型锻造工艺实例 92
第六章 模锻成形工序分析 100
第一节 概述 100
一、控制锻件的最终形状和尺寸 100
二、控制金属的流动方向 100
三、控制塑性变形区 100
四、提高金属的塑性 101
五、控制坯料失稳提高成形极限 101
第二节 开式模锻 101
一、开式模锻各阶段的应力应变分析 102
二、开式模锻时影响金属成形的主要因素 104
第三节 闭式模锻 109
一、闭式模锻的变形过程分析 109
二、坯料体积和模膛体积变化对锻件尺寸的影响 111
三、打击能量和模压力对成形质量的影响 111
四、各类锻压设备闭式模锻的特点 111
第四节 挤压 114
一、挤压的应力应变分析 114
二、挤压时筒内金属的变形流动 114
三、关于“死区”的应力应变分析 117
四、挤压时常见缺陷的分析 118
五、径向挤压 121
第五节 顶镦 123
一、顶镦 123
二、电热镦粗 125
三、在带有导向的模具中镦粗 126
第七章 模锻工艺 127
第一节 常用模锻设备及其工艺特点 127
一、模锻锤 127
二、热模锻压力机 128
三、螺旋压力机 130
四、平锻机 131
第二节 模锻工艺及模锻件分类 133
一、长轴类锻件 133
二、短轴类(圆饼类)锻件 135
三、顶镦类锻件 136
四、复合类型锻件 136
第三节 模锻件图设计 136
一、锤上模锻锻件图设计 137
二、热模锻压力机上模锻件图设计特点 144
三、螺旋压力机上模锻件图设计特点 145
四、平锻机上模锻件图设计特点 146
第四节 模锻工艺过程制定的内容和模锻工艺方案选择 148
一、模锻工艺过程制定的内容 148
二、模锻工艺方案选择 148
第五节 模锻变形工步的确定 151
一、长轴类锻件制坯工步选择 151
二、短轴类锻件制坯工步选择 156
三、顶镦类锻件变形工步确定 157
第六节 坯料尺寸的确定 162
一、长轴类锻件 162
二、短轴类锻件 164
三、顶镦类锻件 164
第七节 设备吨位的确定 165
一、模锻锤吨位的确定 165
二、热模锻压力机吨位的确定 168
三、螺旋压力机吨位的确定 168
四、平锻机吨位的确定 169
第八章 锻模设计 170
第一节 锤用锻模 170
—、模锻模膛设计 170
二、制坯模膛设计 178
三、锻模结构设计 185
第二节 热模锻压力机用锻模 197
一、模膛设计特点 198
二、锻模结构特点 201
第三节 螺旋压力机用锻模 207
一、锻模设计特点 208
二、锻模结构特点 210
第四节 平锻机用锻模 215
一、平锻模的固定及固定空间 215
二、平锻模结构设计特点 217
三、模膛设计 217
第五节 自由锻锤上模锻与胎模锻锻模 222
一、胎模锻锻模 222
二、固定模模锻锻模 222
第六节 锻模材料 225
一、锤锻模用材料 225
二、摩擦压力机锻模用材料 226
三、热模锻压力机锻模用材料 226
四、平锻机锻模用材料 227
五、液压机锻模用材料 227
第七节 锻模设计实例 228
一、锻件图设计 228
二、计算锻件的主要参数 229
三、锻锤吨位的确定 229
四、确定飞边槽的型式和尺寸 230
五、终锻模膛设计 230
六、预锻模膛设计 230
七、绘制计算毛坯图 231
八、制坯工步选择 234
九、确定坯料尺寸 234
十、制坯模膛设计 235
十一、锻模结构设计 236
十二、连杆模锻工艺流程 237
第九章 模锻的后续工序 238
第一节 切边、冲孔及其模具设计 238
一、切边和冲孔的基本方式及模具类型 238
二、切边模 239
三、冲孔模和切边冲孔复合模 243
四、切边力和冲孔力的计算 244
第二节 精压和校正的应用及模具设计 245
一、精压 245
二、校正 247
第三节 模锻件的表面清理 248
第十章 精密模锻工艺 250
第一节 概述 250
第二节 关于锻件精度问题的分析 251
一、坯料体积的偏差 251
二、模膛的尺寸精度和磨损 252
三、模具温度和锻件温度的波动 252
四、模具和锻件的弹性变形 253
五、锻件的形状与尺寸 253
六、成形方案 253
七、模膛和摸具结构的设计 253
八、润滑情况 253
九、设备 254
十、工艺操作 254
第三节 精密模锻的成形方法 254
第四节 关于精密模锻时模膛充填问题的分析 256
第五节 精密模锻工艺设计特点 256
一、精锻件图的设计特点 257
二、加热、清理和冷却 257
第六节 精密模锻模具设计特点 259
一、模具结构类型 259
二、模膛设计中的几个问题 261
三、模具的强度设计 262
四、模具的刚度问题 263
第七节 精密模锻的润滑 264
第八节 精密模锻实例 265
一、直齿圆锥齿轮的精密模锻 265
二、十字轴闭塞式锻造 267
第十一章 高合金钢和有色金属的锻造特点 269
第一节 高合金钢的分类和锻造特点 269
一、高合金钢的分类 269
二、高合金钢的锻造特点 269
第二节 高速钢的锻造 270
一、对高速钢使用性能的要求 270
二、高速钢的碳化物偏析及其对性能的影响 270
三、高速钢锻造前的加热 271
四、高速钢的锻造方法 273
五、锻后冷却和热处理 276
第三节 不锈钢的锻造 276
一、不铸钢的分类 276
二、不锈钢的可锻性 276
三、各类不锈钢的锻造特点 277
四、锻造不锈钢的注意事项 278
第四节 铝合金的锻造 280
一、铝合金的可锻性 280
二、锻造温度范围 281
三、锻模设计特点 281
四、锻造工艺过程 282
第五节 铜合金的锻造 283
一、铜合金的可锻性 283
二、锻造温度范围 283
三、锻造工艺过程 285
第六节 钛合金的锻造 287
—、钛合金的可锻性 287
二、锻造温度范围 287
三、锻模设计特点 288
四、锻造工艺过程 288
第十二章 锻造工艺方案的技术经济分析 291
第一节 工艺方案技术经济分析的一般程序 291
一、确定分析目标 291
二、搜集基础资料 291
三、选定评价的技术经济指标 292
四、列举可能的方案 293
五、计算技术参数 293
六、计算经济参数 293
七、排队、选优 293
八、敏感性分析 293
九、定性分析对比 294
十、可能性分析 294
十一、结论或决策 294
第二节 工艺方案确定的原则 294
第三节 锻造工艺方案的比较 296
一、锻件成本估算 296
二、成本批量曲线及方案比较 297
三、锻件的合理生产批量 298
参考文献 299
- 《葡萄酒工艺与鉴赏 第3版》廖祖宋 2019
- 《化学工程与工艺专业实验指导》郭跃萍主编 2019
- 《美物之道 日本手工艺》(日)柳宗悦著 2019
- 《有色金属冶金新工艺与新技术》俞娟,王斌,方钊,崔雅茹,袁艳 2019
- 《洗涤剂生产工艺与技术》宋小平,韩长日主编 2019
- 《皮革用化学品生产工艺与技术》宋小平,韩长日著 2018
- 《玉米淀粉绿色精益制造 新工艺、新设备、新理念》佟毅 2018
- 《天然气净化工艺技术进展》顾晓峰编著 2019
- 《中国工艺美术史》王树良 2019
- 《化学工程与工艺专业实验》李岩梅,周丽主编 2018
- 《指向核心素养 北京十一学校名师教学设计 英语 七年级 上 配人教版》周志英总主编 2019
- 《北京生态环境保护》《北京环境保护丛书》编委会编著 2018
- 《高等教育双机械基础课程系列教材 高等学校教材 机械设计课程设计手册 第5版》吴宗泽,罗圣国,高志,李威 2018
- 《指向核心素养 北京十一学校名师教学设计 英语 九年级 上 配人教版》周志英总主编 2019
- 《高等院校旅游专业系列教材 旅游企业岗位培训系列教材 新编北京导游英语》杨昆,鄢莉,谭明华 2019
- 《中国十大出版家》王震,贺越明著 1991
- 《近代民营出版机构的英语函授教育 以“商务、中华、开明”函授学校为个案 1915年-1946年版》丁伟 2017
- 《新工业时代 世界级工业家张毓强和他的“新石头记”》秦朔 2019
- 《智能制造高技能人才培养规划丛书 ABB工业机器人虚拟仿真教程》(中国)工控帮教研组 2019
- 《AutoCAD机械设计实例精解 2019中文版》北京兆迪科技有限公司编著 2019