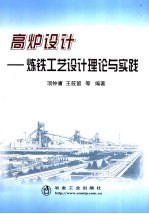
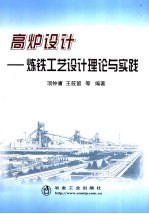
高炉设计 高炉炼铁工艺设计规范的理论与实践PDF电子书下载
- 电子书积分:21 积分如何计算积分?
- 作 者:项钟庸,王筱留等编著
- 出 版 社:北京:冶金工业出版社
- 出版年份:2007
- ISBN:7502443495
- 页数:758 页
1 我国炼铁工业发展现状 1
1.1 我国炼铁工业发展历程及现状 1
1.2 我国炼铁工业面临的形势 3
1.2.1 我国工业化进程为钢铁产业提供广阔的发展前景 3
1.2.2 产能扩张压力大 3
1.2.3 炼铁工业存在着结构性的矛盾和生产布局不合理 4
1.2.4 资源、能源、供给、运输、环境生态压力增大 4
1.2.5 技术创新能力弱 5
1.3 贯彻科学发展观和贯彻钢铁产业发展政策 6
1.3.1 提高资源、能源及市场竞争力,实现产业升级 6
1.3.2 提高炼铁工业的集中度,搞好产业布局 7
1.3.3 改变增长方式 8
1.3.4 提高创新能力 10
1.4 高炉技术指标及确定 10
1.4.1 《规范》使用的术语 11
1.4.2 合理确定高炉技术指标 13
1.4.3 高炉装备水平的确定 15
1.4.4 高炉长寿 18
2 炼铁工业可持续发展的保障条件 19
2.1 我国铁矿石资源及生产 19
2.1.1 我国铁矿石资源状况 19
2.1.2 我国铁矿石生产现状 21
2.2 世界铁矿石资源、生产及贸易 26
2.2.1 世界铁矿石资源状况 26
2.2.2 世界铁矿石生产状况及发展趋势 28
2.2.3 世界主要铁矿石出口企业的生产状况 29
2.2.4 世界铁矿石产能扩张分析 41
2.2.5 未来全球铁矿石产能预测及面临的问题 42
2.3 我国煤炭资源及生产现状 42
2.3.1 我国煤炭资源状况 43
2.3.2 我国炼焦煤生产 45
2.3.3 我国炼焦煤的洗选情况 46
2.3.4 我国无烟煤的资源及生产能力 47
2.3.5 影响国内煤炭市场的因素 47
2.4 世界煤炭资源 48
2.4.1 世界煤炭资源状况 48
2.4.2 世界煤炭产量、消费量及贸易量 49
2.4.3 世界煤炭价格及走势分析 52
2.5 结语 52
参考文献 52
3 炼铁精料 53
3.1 高炉炼铁对原燃料的要求 53
3.2 提高含铁原料的质量 55
3.2.1 提高入炉品位 56
3.2.2 提高烧结矿的质量 59
3.2.3 提高球团矿的质量 63
3.2.4 天然块矿 67
3.2.5 喷煤对原料质量的要求 69
3.3 提高燃料的质量 70
3.3.1 高炉冶炼和喷煤对焦炭质量的要求 71
3.3.2 提高焦炭质量的途径 78
3.3.3 焦炭质量要求 80
3.3.4 高炉喷煤和冶炼对煤粉质量的要求 84
3.3.5 喷吹用原煤的质量要求 86
3.4 辅助原料 87
3.4.1 高炉冶炼对辅助原料的质量要求 87
3.4.2 辅助原料的质量要求 88
3.5 入炉有害杂质 89
3.5.1 有害杂质对高炉生产的影响 89
3.5.2 碱金属的危害及其控制 91
3.5.3 高炉内的锌危害及其控制 93
参考文献 94
4 发展循环经济,降低资源和能源消耗 95
4.1 循环经济是我国经济和环境保护发展的必然选择 95
4.2 循环经济和清洁生产是高炉炼铁环境保护设计的指导思想 95
4.3 发展循环经济的基本途径和对策 97
4.3.1 “减量化”是实现可持续发展的根本 97
4.3.2 清洁生产和绿色技术是推行循环经济的支撑 97
4.3.3 建立工业生态循环方式 98
4.3.4 循环经济是系统工程 98
4.3.5 建立绿色经济核算体系 98
4.4 在高炉炼铁设计、生产中,贯彻科学发展观 98
4.4.1 改变高炉炼铁的设计、生产理念 99
4.4.2 “精料”是贯彻“减量化”生产的基础 100
4.4.3 确定高炉炼铁生产指标时,应贯彻“减量化”生产的思想 100
4.4.4 采取替代紧缺资源的技术 101
4.5 合理利用能源 101
4.5.1 高炉炼铁能耗状况 101
4.5.2 充分利用高炉煤气 103
4.5.3 余热、余能利用 104
4.5.4 脱湿鼓风 104
4.5.5 节电和减少能源介质、辅助材料的消耗 105
4.6 资源综合利用 105
4.6.1 炉渣综合利用 105
4.6.2 含铁尘泥综合利用 106
4.7 水资源循环利用 107
4.8 污染治理 109
4.8.1 废气治理 110
4.8.2 废水治理 111
4.8.3 噪声控制 112
4.8.4 环境风险 113
4.8.5 绿化 113
参考文献 114
5 降低燃料比和焦比的措施 117
5.1 合理布料 117
5.1.1 布料的调节手段 117
5.1.2 合理煤气流分布 122
5.1.3 提高煤气利用率的措施 123
5.2 高风温 123
5.2.1 风温对节焦的影响 124
5.2.2 风温对高炉冶炼的影响 125
5.3 喷吹煤粉 125
5.3.1 煤种选择和优化 126
5.3.2 煤粉成分控制 127
5.3.3 提高煤粉利用率 128
5.3.4 提高煤焦置换比的措施 133
5.4 脱湿鼓风 135
5.4.1 脱湿鼓风对高炉过程的影响 136
5.4.2 脱湿鼓风对燃料比的影响 137
5.5 冶炼强度对燃料比的影响 138
5.5.1 冶炼强度与燃料比的综合情况 138
5.5.2 各级高炉合适的冶炼强度 140
5.5.3 用冶炼强度来衡量高炉强化程度所遇到的问题 143
5.5.4 采用冶炼强度来衡量高炉强化程度是不合适的 144
5.6 低硅冶炼 145
5.6.1 低硅冶炼的意义 145
5.6.2 国内外低硅冶炼水平 145
5.6.3 低硅冶炼的理论与实践 145
5.6.4 降低铁水硅含量的措施 147
5.7 降低高炉热量损失 149
5.7.1 高炉炉体热负荷计算方法 150
5.7.2 影响炉体热负荷的因素 150
5.7.3 气流分布对热负荷的影响 151
5.7.4 确定合理的热负荷 153
5.7.5 热负荷变化对焦比的影响 153
参考文献 154
6 强化高炉冶炼的途径 155
6.1 高炉炉内的煤气流动阻力 155
6.1.1 散料层的煤气流动阻力 156
6.1.2 高炉炉料性能和未燃煤粉对透气性的影响 157
6.1.3 软熔带和滴落带的煤气流动阻力 160
6.2 高炉炉腹煤气量与透气阻力系数 164
6.2.1 炉腹煤气量和透气阻力系数 164
6.2.2 实际炉腹煤气量与透气阻力系数的关系 165
6.3 限制高炉强化的气体力学因素 166
6.3.1 高炉上部的流态化现象 166
6.3.2 高炉下部的液泛现象 168
6.4 高炉炉内温度对高炉强化的影响 171
6.4.1 风口循环区 171
6.4.2 风口前燃烧温度和软熔带热量消耗与高炉操作区域 174
6.4.3 热流强度与炉内温度分布 178
6.5 提高利用系数的措施 180
6.5.1 降低燃料比和焦比 180
6.5.2 富氧鼓风 181
6.5.3 提高炉顶压力 183
6.5.4 增加鼓风量 186
6.6 以炉腹煤气量指数取代冶炼强度 188
6.6.1 限制高炉强化因素的回顾 188
6.6.2 高炉炉腹煤气量指数 188
6.6.3 影响高炉炉腹煤气量指数的因素 190
6.6.4 炉腹煤气量指数的使用价值 191
6.7 提高高炉高效,稳定运行时间 192
6.8 结语 193
参考文献 194
7 延长高炉寿命的措施 195
7.1 高炉寿命的现状 195
7.1.1 高炉的长寿化 195
7.1.2 高炉大型化 195
7.1.3 实现高炉长寿是一项系统工程 198
7.2 高炉损坏的原因 199
7.2.1 破损调查及分析 199
7.2.2 高炉炉底和炉缸的化学侵蚀和侵蚀进程的分析 201
7.2.3 有害元素对炉体的损坏 205
7.3 合理的操作制度 211
7.3.1 烘炉和开炉 212
7.3.2 高炉顺行与长寿 212
7.3.3 控制边缘气流 212
7.3.4 适宜造渣制度和活跃炉缸中心 215
7.3.5 高炉热负荷的监测与控制 215
7.3.6 冷却水量、水质调节及控制 219
7.3.7 合理的出铁制度及出铁口的维护 220
7.3.8 钛矿护炉 224
7.4 高炉的功能性检修 226
7.4.1 高炉内衬的诊断 226
7.4.2 炉缸、出铁口及风口的维修技术 229
7.4.3 高炉炉体内衬的修复技术 232
7.4.4 冷却设备的修理 236
7.4.5 炉壳开裂的修补 238
7.5 热风炉长寿 240
7.5.1 热风炉的破损 240
7.5.2 主要热态维修技术 243
参考文献 245
8 炼铁工艺计算 247
8.1 高炉炼铁工艺计算的意义 247
8.2 联合计算法 247
8.2.1 A.H.拉姆联合计算法 248
8.2.2 J.G.皮西和W.G.达文波特联合计算法(P.D.R联合计算法) 258
8.3 线性配料计算 262
8.3.1 应用A.H.拉姆联合计算法时的线性配料计算 263
8.3.2 应用P.D.R联合计算法时的线性配料计算 264
8.3.3 线性规划配料计算 265
8.4 理论最低碳的计算 267
8.4.1 氧化铁还原的还原剂碳消耗 267
8.4.2 氧化铁还原热量需求的碳消耗 268
8.4.3 理论最低碳比和吨铁最低燃料比 269
8.5 高炉操作线计算 269
8.5.1 里斯特操作线的画法 271
8.5.2 操作线的特点 272
8.6 影响高炉炼铁焦比诸因素的计算 274
8.6.1 A.H.拉姆联合计算法的应用 275
8.6.2 应用P.D.R联合计算法计算 277
8.6.3 应用里斯特操作线图计算 277
8.7 理论燃烧温度计算 282
8.7.1 循环区内生成的煤气成分数量和炉腹煤气成分及数量 282
8.7.2 燃料带入循环区的热量 283
参考文献 284
9 高炉鼓风机的选择 285
9.1 高炉鼓风量及鼓风压力的确定 285
9.1.1 吨铁耗风量的确定 285
9.1.2 高炉最大风量的确定 287
9.1.3 高炉产量、入炉风量和富氧率之间的关系 290
9.1.4 鼓风机风压的确定 297
9.2 高炉鼓风机能力的确定 300
9.2.1 鼓风机的稳定运行范围和有效使用范围 300
9.2.2 高炉配置的鼓风机 304
9.3 脱湿鼓风 310
9.3.1 脱湿鼓风的发展 310
9.3.2 高炉脱湿鼓风的作用 310
9.3.3 各种脱湿方法及其特点 313
9.3.4 冷却脱湿鼓风的作用 317
参考文献 318
10 高炉炉体 319
10.1 高炉内型 319
10.1.1 高炉容积的定义及内型尺寸代号 319
10.1.2 高炉内型设计 321
10.1.3 操作内型及薄壁内型设计 324
10.1.4 死料堆的运动及死铁层的深度 328
10.2 炉底、炉缸冷却和砌体结构 330
10.2.1 炉底、炉缸冷却结构 330
10.2.2 炉底、炉缸砌体结构 332
10.2.3 炉底、炉缸用耐火材料 336
10.3 炉底、炉缸结构的分析 340
10.3.1 铁水渗透和侵蚀 340
10.3.2 铁水流动冲刷力的分析 345
10.3.3 热应力形成炭砖脆裂带 350
10.4 炉腹、炉腰和炉身冷却和砌体结构 355
10.4.1 炉腹、炉腰和炉身下部工作条件 356
10.4.2 炉腹、炉腰和炉身冷却结构 357
10.4.3 炉腹、炉腰和炉身砌体结构 361
10.4.4 炉腹、炉腰和炉身用耐火材料 362
10.5 炉腹、炉腰和炉身耐材损坏的分析 366
10.5.1 炉腹、炉腰和炉身下部的热应力破坏 366
10.5.2 炉腹、炉腰和炉身下部耐材的热震破坏 370
10.6 高炉冷却设备 373
10.6.1 冷却壁的材料及其传热分析 373
10.6.2 铸铁冷却壁 377
10.6.3 铸铁冷却壁的损坏分析 383
10.6.4 铜冷却壁和铜冷却板 385
10.7 高炉冷却系统 393
10.7.1 冷却介质 394
10.7.2 冷却系统的分类及水质控制 394
10.7.3 软水密闭循环冷却系统设计 397
10.8 高炉炉体钢结构 405
10.8.1 钢结构框架 405
10.8.2 炉壳 406
10.8.3 炉体平台走梯 409
10.9 结语 410
参考文献 410
11 高炉炉顶装料和供料系统 411
11.1 高炉矿槽、焦槽及供料系统 411
11.1.1 矿槽、焦槽及槽上运输 411
11.1.2 矿槽、焦槽及料斗的设计 414
11.2 料批重量及批数 415
11.2.1 料批重量的确定 415
11.2.2 高炉昼夜装料批数及一批料的时间 418
11.3 供料系统的选择及作业时间顺序 419
11.3.1 供料系统的选择 419
11.3.2 供料系统的能力及作业时间顺序 422
11.4 供料系统设备 427
11.4.1 焦槽槽下设备及能力的确定 427
11.4.2 矿槽槽下设备及能力的确定 430
11.4.3 废铁清除装置 434
11.4.4 取样装置 435
11.4.5 上料胶带运输机 435
11.5 炉顶装料系统 436
11.5.1 无料钟炉顶装料设备及其特点 437
11.5.2 炉顶装料系统能力的确定 441
11.5.3 炉顶装料设备 447
11.5.4 无料钟装料设备三电控制 452
11.6 炉顶均排压系统 455
11.6.1 无料钟炉顶均排压系统 455
11.6.2 炉顶均压煤气回收系统 456
11.6.3 无料钟炉顶液压系统及润滑站 457
11.6.4 料面探测设备 457
11.7 炉顶结构及设备检修设备 459
11.7.1 炉顶结构 459
11.7.2 高炉炉顶除尘及设备维修 459
参考文献 460
12 热风炉 463
12.1 热风炉蓄热室热交换理论 463
12.1.1 蓄热过程 464
12.1.2 蓄热室纵向温度分布 465
12.1.3 蓄热室热交换过程的解析 468
12.1.4 基谐波振荡——零次特征函数 470
12.1.5 蓄热室末端的温度变化及其对热交换的影响 479
12.2 热风炉内的燃烧过程及气体运动 484
12.2.1 燃烧器及其研究方法 485
12.2.2 金属燃烧器的研究 487
12.2.3 陶瓷燃烧器的实验研究 488
12.2.4 燃烧过程的数学模拟 500
12.2.5 燃烧振动 506
12.2.6 烟气和冷风的分布 508
12.3 热风炉的使用情况和结构形式 510
12.3.1 热风炉的使用情况 510
12.3.2 热风炉结构形式及其优缺点 513
12.4 热风炉砌体结构及耐火材料 517
12.4.1 热风炉用耐火材料的发展 517
12.4.2 热风炉的砌筑结构 517
12.4.3 耐火材料中的应力 525
12.4.4 对耐火材料的要求 528
12.4.5 热风炉使用的耐火材料 530
12.4.6 不定形耐火材料 538
12.5 蓄热室设计的优化 541
12.5.1 优化热风炉的设计条件 541
12.5.2 优化热风炉的设计 542
12.5.3 蓄热室的最优化 543
12.5.4 格砖的最优化 545
12.6 热风炉金属结构及设备 548
12.6.1 晶界应力腐蚀的成因及预防措施 548
12.6.2 热风炉设备 550
12.7 热风炉废气热量利用及低发热值煤气提高热风温度的途径 556
12.7.1 废气热量利用 556
12.7.2 使用低发热值煤气获得高风温的方法 558
12.8 热风炉操作 563
12.8.1 烘炉 563
12.8.2 凉炉 565
12.8.3 热风炉的保温 567
12.8.4 热风炉的操作制度 567
12.8.5 热风炉的自动控制 572
参考文献 573
13 改善炉前劳动条件及高炉炉渣的综合利用 575
13.1 风口平台及出铁场 575
13.1.1 风口平台及出铁场布置 575
13.1.2 风口平台出铁场结构 579
13.2 改善炉前劳动条件,提高劳动生产率 581
13.2.1 渣铁沟的设计 581
13.2.2 炉前机械化 586
13.2.3 炉前渣铁沟内衬材料及其修理的工艺和设备 595
13.2.4 炉前通风除尘设施 602
13.3 高炉炉渣及其综合利用 610
13.3.1 沉淀过滤法 611
13.3.2 机械过滤设施 613
13.3.3 矿渣膨珠 623
13.3.4 干渣坑 625
13.3.5 冲渣水处理 626
13.3.6 高炉炉渣的综合利用 627
参考文献 627
14 高炉煤气净化及炉顶煤气余压发电 630
14.1 粗煤气除尘系统 630
14.1.1 粗煤气管道 630
14.1.2 重力除尘器 632
14.1.3 轴向旋风除尘器 633
14.1.4 重力除尘器和切向旋风除尘器 634
14.2 湿式除尘 635
14.2.1 环缝洗涤系统 635
14.2.2 双文丘里洗涤系统 638
14.2.3 环缝和文丘里洗涤系统的比较 639
14.3 干式除尘 640
14.3.1 干式布袋除尘 640
14.3.2 干式静电除尘 647
14.3.3 干式除尘器的特点及比较 648
14.3.4 干式除尘存在的问题及对策 648
14.3.5 干式除尘的社会效益和经济效益 650
14.4 炉顶煤气余压发电 651
14.4.1 概述 651
14.4.2 煤气余压回收装置的工艺流程及特点 652
14.4.3 炉顶煤气余压透平能力的确定 653
14.4.4 设备组成及结构 656
14.4.5 节能及效益 666
14.4.6 TRT业绩 668
参考文献 672
15 高炉喷吹煤粉 674
15.1 喷煤的效益和最佳喷煤量 674
15.1.1 喷煤的效益 674
15.1.2 最佳喷煤量的设定 675
15.2 喷煤工艺流程 678
15.2.1 喷煤工艺设施 678
15.2.2 喷煤车间的辅助设施 680
15.3 高炉喷煤工艺的分类 680
15.3.1 直接喷吹和间接喷吹 680
15.3.2 串罐与并罐 680
15.3.3 多支管和总管加分配器 681
15.3.4 上出料和下出料 682
15.3.5 并联喷吹罐的配置 683
15.4 喷煤车间主要设备的选择及其能力的确定 684
15.4.1 原煤仓 684
15.4.2 给煤机 685
15.4.3 磨煤机 685
15.4.4 布袋收粉器 687
15.4.5 煤粉仓 688
15.4.6 主排烟风机 689
15.4.7 煤粉仓下部流化装置、加煤分料管和阀门组 690
15.4.8 喷吹罐 691
15.4.9 二次补气器 693
15.4.10 煤粉筛 694
15.4.11 煤粉分配器 694
15.4.12 煤粉喷枪和氧煤喷枪 694
15.5 磨煤机热平衡简化计算 695
15.5.1 磨煤机的主要热量支出 695
15.5.2 磨煤机的主要热量收入 696
15.5.3 热平衡计算的步骤 696
15.6 喷煤管路的设计与计算 696
15.6.1 喷煤量与罐压 696
15.6.2 关于浓相输送 697
15.6.3 喷吹罐的工作压力 697
15.6.4 “以流量换压力”的条件 698
15.6.5 喷吹用气量及其计算 698
15.6.6 气、煤两相流总阻损的确定 699
15.7 喷吹烟煤设计中的安全措施 701
15.7.1 引起煤粉爆炸的条件 701
15.7.2 防爆措施 702
15.8 磨煤机烟气自循环工艺 702
15.8.1 烟气自循环工艺简介 702
15.8.2 烟气自循环工艺的形式 703
15.8.3 适用烟气自循环工艺的场合 704
15.8.4 烟气自循环工艺的理论依据 704
15.8.5 控制系统含氧率的措施 708
15.8.6 抑制高湿量烟气危害的措施 709
15.8.7 不脱水自循环工艺中主要参数的设定 709
参考文献 710
16 检测和自动化 711
16.1 高炉主要检测仪表 711
16.1.1 温度类仪表 712
16.1.2 压力类仪表 712
16.1.3 流量类仪表 713
16.1.4 物位类仪表 714
16.1.5 特殊仪表 715
16.2 高炉主要检测项目 725
16.2.1 无料钟炉顶检测项目 725
16.2.2 高炉本体检测项目 726
16.2.3 热风炉检测项目 729
16.3 高炉自动化控制 731
16.3.1 高炉自动化控制系统基本构成 732
16.3.2 基础自动化级L1的基本组成 732
16.3.3 基础自动化级L1的构成类型 735
16.3.4 过程控制级L2的基本组成 736
16.3.5 过程控制级L2的构成类型 737
16.3.6 自动化控制系统控制和管理范围 738
16.3.7 基础自动化L1的主要控制功能 739
16.3.8 HMI画面 746
16.3.9 过程自动化L2主要功能 748
16.3.10 自动化控制系统电源 749
16.4 高炉及热风炉数学模型 749
16.4.1 高炉数学模型 749
16.4.2 热风炉燃烧控制数学模型 754
参考文献 758
- 《指向核心素养 北京十一学校名师教学设计 英语 七年级 上 配人教版》周志英总主编 2019
- 《设计十六日 国内外美术院校报考攻略》沈海泯著 2018
- 《计算机辅助平面设计》吴轶博主编 2019
- 《语文教育教学实践探索》陈德收 2018
- 《彼得·布鲁克导演实践研究》邓小玲著 2019
- 《高校转型发展系列教材 素描基础与设计》施猛责任编辑;(中国)魏伏一,徐红 2019
- 《景观艺术设计》林春水,马俊 2019
- 《反思性实践》胡红梅, 2019
- 《高含硫气藏开发腐蚀控制技术与实践》唐永帆,张强 2018
- 《高等教育双机械基础课程系列教材 高等学校教材 机械设计课程设计手册 第5版》吴宗泽,罗圣国,高志,李威 2018
- 《市政工程基础》杨岚编著 2009
- 《家畜百宝 猪、牛、羊、鸡的综合利用》山西省商业厅组织技术处编著 1959
- 《《道德经》200句》崇贤书院编著 2018
- 《高级英语阅读与听说教程》刘秀梅编著 2019
- 《计算机网络与通信基础》谢雨飞,田启川编著 2019
- 《看图自学吉他弹唱教程》陈飞编著 2019
- 《法语词汇认知联想记忆法》刘莲编著 2020
- 《培智学校义务教育实验教科书教师教学用书 生活适应 二年级 上》人民教育出版社,课程教材研究所,特殊教育课程教材研究中心编著 2019
- 《国家社科基金项目申报规范 技巧与案例 第3版 2020》文传浩,夏宇编著 2019
- 《流体力学》张扬军,彭杰,诸葛伟林编著 2019
- 《指向核心素养 北京十一学校名师教学设计 英语 七年级 上 配人教版》周志英总主编 2019
- 《北京生态环境保护》《北京环境保护丛书》编委会编著 2018
- 《指向核心素养 北京十一学校名师教学设计 英语 九年级 上 配人教版》周志英总主编 2019
- 《高等院校旅游专业系列教材 旅游企业岗位培训系列教材 新编北京导游英语》杨昆,鄢莉,谭明华 2019
- 《中国十大出版家》王震,贺越明著 1991
- 《近代民营出版机构的英语函授教育 以“商务、中华、开明”函授学校为个案 1915年-1946年版》丁伟 2017
- 《新工业时代 世界级工业家张毓强和他的“新石头记”》秦朔 2019
- 《智能制造高技能人才培养规划丛书 ABB工业机器人虚拟仿真教程》(中国)工控帮教研组 2019
- 《陶瓷工业节能减排技术丛书 陶瓷工业节能减排与污染综合治理》罗民华著 2017
- 《全国职业院校工业机器人技术专业规划教材 工业机器人现场编程》(中国)项万明 2019