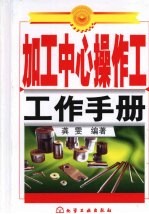
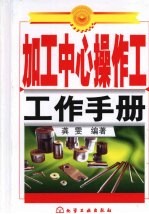
加工中心操作工工作手册PDF电子书下载
- 电子书积分:17 积分如何计算积分?
- 作 者:龚雯编著
- 出 版 社:北京:化学工业出版社
- 出版年份:2007
- ISBN:9787122006875
- 页数:587 页
第1章 常用资料与计算 1
1.1 常用字母及符号 1
1.1.1 希腊字母 1
1.1.2 主要元素的化学符号 1
1.2 常用计量单位及其换算 1
1.2.1 公制计量单位 1
1.2.2 英制长度单位 1
1.2.3 角度与弧度 4
1.2.4 各种硬度对照表 5
1.3 常用三角函数计算 5
1.3.1 常用三角函数计算公式 5
1.3.2 特殊角度的三角函数值 7
1.4 点的坐标 7
1.4.1 坐标系 7
1.4.2 直角坐标系与极坐标系的互换 8
1.5 平面解析几何 8
1.5.1 直线方程 8
1.5.2 点、直线的位置关系 9
1.5.3 二次曲线 9
1.5.4 常见图形轮廓节点计算 12
1.6 数控技术常用术语 12
1.7 常用工程材料 18
1.7.1 金属材料的力学性能 18
1.7.2 钢的热处理 21
1.7.3 钢的表面热处理 23
1.7.4 常用钢的牌号、用途及热处理 25
1.7.5 铸铁 33
1.7.6 有色金属及其合金 43
1.7.7 工程塑料 47
1.8 切削液的功效与选用 51
1.8.1 切削液的作用 51
1.8.2 切削液的种类 52
1.8.3 切削液的选用原则 54
1.8.4 铣削用切削液的选用 54
第2章 极限与配合、形位公差、表面粗糙度 56
2.1 尺寸极限与配合 56
2.1.1 标准公差的概念及其等级 56
2.1.2 极限偏差 56
2.1.3 基本偏差 56
2.1.4 基准制 60
2.1.5 公差带代号 60
2.1.6 配合 60
2.1.7 未注公差的线性和角度尺寸的一般公差 61
2.2 形位公差 63
2.2.1 形位公差项目及其公差带 63
2.2.2 形位公差的标注 73
2.2.3 公差原则 73
2.2.4 形位公差的选择与应用 78
2.2.5 形位公差的等级与公差值 87
2.3 表面粗糙度 91
2.3.1 常用的表面粗糙度评定参数 91
2.3.2 表面粗糙度符号和代号 92
2.3.3 表面粗糙度与光洁度的新旧对照 92
2.3.4 主要工业国家表面粗糙度及其数值对照 92
2.4 金属切削加工零件结构要素 103
2.4.1 中心孔 103
2.4.2 各类槽的尺寸和形式 104
2.4.3 球面半径 114
第3章 加工中心 115
3.1 加工中心分类 115
3.1.1 加工中心的分类 115
3.1.2 加工中心的型号 116
3.2 加工中心的结构 119
3.3 加工中心主轴系统 121
3.3.1 主轴传动系统 121
3.3.2 主轴部件结构 123
3.4 加工中心的进给伺服系统 125
3.4.1 进给伺服系统结构 125
3.4.2 进给伺服系统的典型元件 127
3.5 加工中心刀库 130
3.5.1 刀库形式 130
3.5.2 自动换刀装置 131
3.6 位置检测装置 133
3.6.1 光栅 133
3.6.2 光电式增量编码器 134
3.7 加工中心的维护保养 134
3.7.1 CNC系统日常维护的内容 134
3.7.2 刀库及换刀机械手的维护内容 135
3.7.3 滚珠丝杠副维护内容 138
3.7.4 主传动链的维护内容 138
3.7.5 液压系统维护内容 139
3.7.6 气动系统维护内容 139
3.8 加工中心的检验与验收 139
3.8.1 加工中心验收依据 140
3.8.2 试车和空载运行 140
3.8.3 机床几何精度检测 141
3.8.4 机床定位精度检验 146
3.8.5 机床切削精度检验 154
3.8.6 加工中心性能验收 158
3.8.7 加工中心外观检查 162
3.9 加工中心安全操作规程 163
第4章 加工中心常用刀具及辅具 166
4.1 对加工中心刀具的要求 166
4.2 加工中心刀具的材料及其选用 167
4.2.1 高速钢 167
4.2.2 硬质合金 172
4.2.3 陶瓷 175
4.2.4 金刚石 179
4.2.5 立方氮化硼(CBN) 181
4.3 刀具基础知识 181
4.3.1 刀具切削部分的组成 181
4.3.2 刀具几何角度参考系 182
4.3.3 刀具的标注角度 183
4.3.4 刀具工作角度及定义 184
4.3.5 刀具角度正负的规定 185
4.4 加工中心常用孔加工刀具 186
4.4.1 麻花钻 186
4.4.2 深孔钻 198
4.4.3 扩孔钻 201
4.4.4 锪钻 202
4.4.5 扁钻 203
4.4.6 孔加工刀具尺寸确定 204
4.5 镗削刀具 206
4.5.1 镗刀的类型及结构 206
4.5.2 镗刀的选择 209
4.6 铰刀 209
4.6.1 铰刀的结构和种类 210
4.6.2 铰刀主要结构要素对铰削过程的影响 211
4.6.3 铰刀切削部分的几何角度 213
4.7 复合孔加工刀具 214
4.8 螺纹加工刀具 215
4.8.1 丝锥的结构与几何参数 215
4.8.2 丝锥的选用 216
4.9 铣削刀具及其选择 216
4.9.1 立铣刀 216
4.9.2 端铣刀 225
4.9.3 模具铣刀 230
4.9.4 键槽铣刀 231
4.9.5 鼓形铣刀 231
4.9.6 成形铣刀 232
4.9.7 铣刀角度的换算 233
4.10 刀具失效形式及可靠性 234
4.10.1 刀具的失效形式 234
4.10.2 刀具磨损标准 235
4.10.3 加工中心刀具的可靠性 237
4.10.4 改善刀具磨损的途径 239
4.11 加工中心的对刀装置 244
4.11.1 对刀装置的种类 244
4.11.2 对刀装置的使用 244
4.12 镗铣类工具系统 248
4.12.1 整体式数控工具系统 248
4.12.2 模块式工具系统 250
4.12.3 加工中心刀柄选择 253
第5章 技术测量及量具 280
5.1 测量的一般概念 280
5.1.1 测量器具的参数和特性 280
5.1.2 与测量精度有关的几个概念 280
5.2 量具选择 283
5.2.1 计量器具的不确定度 283
5.2.2 几种常用计量器具的不确定度 283
5.2.3 常用量具可测的工件精度等级 285
5.3 基准量具的使用与维护方法 286
5.3.1 量块 286
5.3.2 角度块 292
5.4 游标量具 296
5.4.1 游标卡尺 296
5.4.2 公制双排刻线游标卡尺 301
5.4.3 带表卡尺 302
5.4.4 高度游标卡尺 302
5.4.5 深度游标卡尺 305
5.5 千分尺 306
5.5.1 外径千分尺 306
5.5.2 内径千分尺 308
5.5.3 深度千分尺 311
5.6 指示表类量具 313
5.6.1 百分表 313
5.6.2 内径百分表 314
5.6.3 杠杆百分表 316
5.6.4 千分表 318
5.7 角度测量量具 319
5.7.1 万能角度尺 319
5.7.2 直角尺 321
5.7.3 刀口角尺 323
5.7.4 正弦规 323
5.7.5 框式水平仪 329
5.7.6 光学合像水平仪 337
5.8 其他量具、量规 338
5.8.1 塞尺 338
5.8.2 半径样板 340
5.9 量仪 342
5.9.1 万能工具显微镜 342
5.9.2 轮廓投影仪 344
5.9.3 三坐标测量机 345
第6章 加工中心编程方法 347
6.1 数控编程的方法 347
6.2 数控机床的坐标系和运动方向 348
6.2.1 标准坐标系的命名原则 348
6.2.2 坐标轴运动方向的判定方法 349
6.2.3 绝对坐标系与增量坐标系 350
6.2.4 数控机床坐标系的设定 350
6.3 编程格式 351
6.3.1 程序的结构 351
6.3.2 程序段格式 352
6.3.3 程序段内各字说明 353
6.4 编程规则 364
6.4.1 绝对值编程和增量编程 364
6.4.2 小数点编程 365
6.4.3 自保持功能 365
6.4.4 指令的取消和替代 366
6.5 程序编制中的数值计算 366
6.5.1 基点坐标的计算 366
6.5.2 节点坐标的计算 368
6.6 常用指令的编程方法 376
6.6.1 工件坐标系和编程零点 376
6.6.2 与坐标系有关的指令 377
6.6.3 工件坐标系选取指令G54~G59 378
6.6.4 自动返回参考点G27、G28、G29 379
6.6.5 刀具长度补偿指令G43、G44、G49 380
6.6.6 刀具半径补偿指令G41、G42、G40 381
6.6.7 快速定位指令G00 381
6.6.8 直线插补指令G01 382
6.6.9 圆弧插补指令G02、G03 382
6.6.10 暂停指令G04 384
6.6.11 英制/公制转换指令 385
6.7 刀具功能T、进给功能F、主轴转速功能S的编程方法 385
6.7.1 刀具功能T编程方法 385
6.7.2 进给功能F编程方法 386
6.7.3 主轴转速功能S编程方法 387
6.8 固定循环功能的编程方法 387
6.8.1 FANUC系统常用固定循环 388
6.8.2 FAGOR系统常用固定循环 397
6.9 子程序编程方法 400
6.9.1 子程序的概念及应用 400
6.9.2 子程序的嵌套 401
6.9.3 子程序的编写格式 401
6.9.4 子程序调用格式 402
6.9.5 子程序编程示例 402
第7章 加工中心选用与操作 404
7.1 加工中心的选用 404
7.1.1 加工中心类型的选用 404
7.1.2 加工中心规格的选用 405
7.1.3 加工中心精度的选用 406
7.1.4 加工中心数控系统的选择 407
7.1.5 工作台自动分度功能选择 408
7.1.6 刀库容量和自动换刀装置(ATC)选择 408
7.1.7 冷却方式选择 409
7.1.8 加工中心附件、刀柄的选择 409
7.2 工件在加工中心上的安装 410
7.2.1 定位基准选择 410
7.2.2 零件在机床工作台上装夹的位置 411
7.3 加工中心夹具 412
7.3.1 对夹具的基本要求 412
7.3.2 通用夹具 413
7.3.3 组合夹具 414
7.3.4 通用可调夹具 422
7.3.5 成组夹具 425
7.4 加工中心的对刀与换刀 426
7.4.1 对刀点与换刀点的确定 426
7.4.2 对刀方法 427
7.4.3 卧式加工中心多工位加工中的对刀问题 429
7.5 几种常用加工中心的操作方法 434
7.5.1 JCS-081A立式加工中心操作方法(FANUC-6M系统) 435
7.5.2 TH5660A立式加工中心的操作方法(FAGOR 8055M系统) 447
7.5.3 国内加工中心选用数控系统情况 454
第8章 加工中心加工工艺 456
8.1 加工中心加工工艺的编制步骤 456
8.2 零件图的数控加工工艺性分析 457
8.2.1 检查零件图的完整性和正确性 457
8.2.2 零件结构工艺性分析及处理 458
8.2.3 加工内容选择 458
8.3 加工中心加工工艺方案设计 459
8.3.1 加工方法选择 459
8.3.2 加工阶段划分和工序顺序安排 461
8.3.3 加工进给路线的确定 463
8.3.4 数控铣削型腔的几种典型加工方法 469
8.3.5 加工余量的确定 474
8.3.6 工序尺寸及公差的确定方法 475
8.3.7 切削用量的选择 488
8.4 数控加工工艺文件的编写 495
8.4.1 数控加工编程任务书 496
8.4.2 数控加工工序卡 496
8.4.3 数控机床调整单 497
8.4.4 数控加工刀具调整单 500
8.4.5 数控加工进给路线图 501
8.4.6 数控加工程序单 502
第9章 典型零件加工 504
9.1 齿轮泵泵体加工实例 504
9.1.1 零件工艺分析 505
9.1.2 零件加工工艺方案设计 505
9.1.3 加工程序编制 507
9.2 定位板加工 514
9.2.1 零件工艺分析 514
9.2.2 零件加工工艺方案设计 515
9.2.3 加工程序编制 516
9.3 配合件加工实例 530
9.3.1 零件工艺分析 530
9.3.2 零件加工工艺方案设计 531
9.3.3 加工程序编制 531
第10章 加工中心常见故障及其排除 539
10.1 数控机床故障诊断方法 539
10.1.1 数控机床故障分类 539
10.1.2 数控机床故障诊断与维修的基本原则 541
10.1.3 常用诊断仪器 542
10.2 加工中心常见机械故障与维修 547
10.2.1 主轴部件故障与维修 547
10.2.2 滚珠丝杠与螺母 550
10.2.3 刀库与换刀装置 553
10.3 数控系统故障诊断与维修 556
10.3.1 数控系统故障诊断方法 556
10.3.2 故障诊断与维修的准备工作 559
10.3.3 数控系统的软件故障诊断与排除 560
10.4 主轴伺服系统故障及诊断 562
10.4.1 主轴伺服系统故障分类 562
10.4.2 主轴伺服系统故障诊断与排除 562
10.5 进给伺服系统故障与诊断 564
10.5.1 CRT上显示报警内容的故障(软件报警故障) 565
10.5.2 报警指示灯报警的故障(硬件报警故障) 568
10.5.3 无报警显示的故障 569
10.6 加工中心维修实例 571
10.6.1 机械手无法从主轴和刀库中取刀具 571
10.6.2 位置检测装置维修实例 577
10.6.3 加工中心主传动系统故障维修 579
10.6.4 JCS-018立式加工中心故障排除实例 583
参考文献 586
- 《激光加工实训技能指导理实一体化教程 下》王秀军,徐永红主编;刘波,刘克生副主编 2017
- 《药剂学实验操作技术》刘芳,高森主编 2019
- 《BBC人体如何工作》(英)爱丽丝.罗伯茨 2019
- 《Maya 2018完全实战技术手册》来阳编著 2019
- 《先进激光加工技能实训》肖海兵主编 2019
- 《高等教育双机械基础课程系列教材 高等学校教材 机械设计课程设计手册 第5版》吴宗泽,罗圣国,高志,李威 2018
- 《慢性呼吸系统疾病物理治疗工作手册》(荷)瑞克·考斯林克(RikGosselink) 2020
- 《战略情报 情报人员、管理者和用户手册》(澳)唐·麦克道尔(Don McDowell)著 2019
- 《实用内科手册》黄清,阮浩航主编 2016
- 《掌控工作》邵文瀚著 2020
- 《市政工程基础》杨岚编著 2009
- 《家畜百宝 猪、牛、羊、鸡的综合利用》山西省商业厅组织技术处编著 1959
- 《《道德经》200句》崇贤书院编著 2018
- 《高级英语阅读与听说教程》刘秀梅编著 2019
- 《计算机网络与通信基础》谢雨飞,田启川编著 2019
- 《看图自学吉他弹唱教程》陈飞编著 2019
- 《法语词汇认知联想记忆法》刘莲编著 2020
- 《培智学校义务教育实验教科书教师教学用书 生活适应 二年级 上》人民教育出版社,课程教材研究所,特殊教育课程教材研究中心编著 2019
- 《国家社科基金项目申报规范 技巧与案例 第3版 2020》文传浩,夏宇编著 2019
- 《流体力学》张扬军,彭杰,诸葛伟林编著 2019