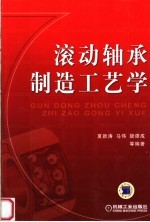
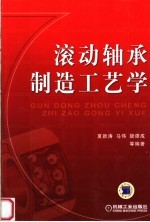
滚动轴承制造工艺学PDF电子书下载
- 电子书积分:15 积分如何计算积分?
- 作 者:夏新涛,马伟,颉谭成等编著
- 出 版 社:北京:机械工业出版社
- 出版年份:2007
- ISBN:9787111202172
- 页数:460 页
第一章 绪论 1
第一节 滚动轴承的基本知识与概念 1
一、轴承产品的基本结构 1
二、滚动轴承零件结构的常用术语 2
三、滚动轴承的公差与符号 4
第二节 滚动轴承产品的性能要求 6
第三节 滚动轴承零件的加工工艺特点 6
一、滚动轴承零件的生产特点 6
二、滚动轴承零件工艺过程的特殊性 7
第四节 滚动轴承生产的一般工艺过程 8
第五节 滚动轴承的工艺文件 9
第二章 套圈毛坯锻造 19
第一节 套圈锻造基本知识 19
一、概述 19
二、最小阻力定律与体积不变定律 20
三、锻造温度范围的确定 21
四、锻造加热与冷却规范 23
第二节 下料 24
一、剪切下料工艺 25
二、热剪切下料料段的缺陷 26
三、蓝脆折断下料工艺 28
四、其他下料工艺 29
五、国外下料概况 29
第三节 压力机上锻造 29
一、概述 29
二、挤压工艺 30
三、挤压-辗扩工艺 30
四、套锻-辗扩工艺 32
五、塔形-辗扩工艺 32
六、自由冲孔-辗扩工艺 34
第四节 辗扩和整形 35
一、概述 35
二、辗扩工艺 36
三、整形工艺 37
第五节 高速镦锻工艺 39
一、高速镦锻工艺特点及优越性 40
二、高速镦锻工艺介绍 41
三、轴承套圈毛坯采用高速镦锻工艺的技术经济效果 42
第六节 锻件的清理 44
一、锻件毛刺的清理 44
二、锻件氧化皮的清理 44
第七节 锻件加热炉 46
一、半煤气炉 46
二、煤气炉 46
三、油炉 47
四、感应电炉 47
第八节 温挤压工艺 48
一、轴承钢的挤压温度与挤压力 48
二、轴承套圈的成形方法 49
三、润滑 49
四、温挤件的质量 50
第九节 冷挤压工艺 51
一、冷挤压工艺流程 52
二、组合凹模的设计 52
三、凸模的设计 56
第十节 冷辗扩工艺 57
一、套圈毛坯的冷辗扩工艺 57
二、轴承套圈冷辗扩分析 61
第三章 套圈车削加工 65
第一节 套圈车削加工概述 65
一、车削加工的地位和作用 65
二、车削加工的内容和方法分类 66
第二节 套圈车削工艺过程的设计方法 66
一、套圈毛坯的选择 66
二、加工方法的确定 68
三、加工质量的保证 70
四、套圈车削投料加工典型工艺分析 76
五、特殊套圈的车削加工 85
第三节 套圈精整加工 89
一、精整加工的作用 89
二、精整加工的内容和方法 90
第四节 车削套圈的尺寸公差及余量的确定 94
第五节 套圈车削加工的切削用量 98
第六节 工序图的设计 100
第七节 套圈车削加工的夹具类型和夹紧力计算 104
一、套圈车削加工对夹具的要求 104
二、夹持毛坯表面的夹具类型和特点 104
三、夹持光整表面用的夹具 108
四、夹紧力的计算 112
第四章 套圈热处理 120
第一节 套圈热处理概述 120
一、轴承钢热处理基础 120
二、套圈热处理工序的位置 121
第二节 套圈热处理 121
一、套圈的正火 121
二、套圈的退火 123
三、套圈的淬火 124
四、套圈的回火 128
五、套圈的附加回火 129
六、套圈的冷处理 130
第三节 套圈的保护气氛热处理 131
一、保护气氛热处理的类型与作用 131
二、保护气氛热处理的工作原理 132
三、氮基保护气氛 134
四、氮基保护气氛辊底式热处理生产线 138
第四节 热处理对套圈质量的影响 141
一、热处理对套圈表面质量的影响 141
二、热处理对套圈精度的影响 142
第五节 GCr15轴承钢断裂韧性 145
一、淬火温度的影响 145
二、回火温度的影响 145
三、淬火冷却方法的影响 145
四、预处理方式的影响 146
五、淬火加热方式的影响 146
六、奥氏体化多循环处理的影响 147
第六节 GCr15轴承套圈连续变温形变复相淬火工艺 149
一、工艺流程 149
二、工艺特点及分析 149
第七节 新轴承材料热处理 151
一、GCr18Mo钢等温淬火 151
二、H10Cr4Mo4Ni4V热处理 152
三、16Cr2Ni4MA制薄壁套圈热处理 153
第八节 钢球热处理 154
第五章 套圈的磨削 157
第一节 套圈磨削加工概述 157
一、套圈的磨削工艺过程 157
二、磨削轴承套圈的砂轮选择 160
三、套圈磨削方法 162
四、套圈的磨削特点及发展 164
第二节 套圈端面磨削 165
一、立轴平面磨削方法 165
二、双端面磨削方法 166
第三节 外圆无心磨削 171
一、外圆无心磨削概述 171
二、外圆无心磨削的几何成圆理论 172
三、砂轮的修整 179
四、导轮的修整 179
第四节 套圈内圆磨削 180
一、内圆磨削原理与特点 181
二、内圆磨削误差复映规律 182
三、内圆磨削圆度误差复映系数优化 185
四、内圆磨削的尺寸分散与锥形内孔 188
五、内表面磨削砂轮轴刚度 188
第五节 滚道磨削 190
一、套圈滚道磨削方法与特点 190
二、滚道磨削精度 192
第六节 套圈挡边磨削 194
一、各种挡边的磨削方法 194
二、挡边轮廓形状的类型 196
三、内凹圆弧型挡边的磨削成形原理 197
四、直线型挡边的磨削成形原理 198
五、圆锥轴承内圈挡边磨削理论新发展 200
六、磨削烧伤与防止措施 201
第七节 套圈磨削用夹具 202
一、定心夹具及其特点 203
二、无心夹具及其特点 203
三、电磁无心夹具的力学原理 206
四、无心夹具的定位误差 208
五、组合移动式大型电磁无心夹具 214
六、电磁无心夹具支点印去除方法 217
第八节 套圈的控制力磨削 218
一、控制力磨削原理 218
二、控制力磨削的成圆过程 219
三、控制力磨削的优越性 221
第九节 谐波控制原理 222
一、谐波控制原理介绍 222
二、谐波控制方法 223
第十节 套圈的退磁原理 225
一、退磁的基本概念 225
二、退磁工艺 226
第六章 套圈滚动表面超精研加工第一节 套圈滚动表面的光整加工 229
一、光整加工的作用与要求 229
二、光整加工方法与特点 230
第二节 超精研加工概述 232
一、定义说明 232
二、超精加工的特点 233
三、超精加工对滚动轴承工作性能的影响 234
第三节 超精加工原理 234
一、超精加工条件 234
二、超精加工过程分析 235
第四节 超精加工工艺参数的选择分析 237
一、运动参数的选择分析 238
二、压力参数的选择分析及加工阶段分界图 241
三、超精加工留量的选择分析 244
第五节 超精加工对滚动表面几何形状的改善 245
一、超精加工对原有误差的改善能力 245
二、超精加工的油石包角效应 246
三、超精加工对滚动表面母线的影响 250
第六节 超精研方法 252
一、套圈沟道超精 252
二、套圈滚道超精 258
三、双半套圈角接触球轴承套圈超精 260
四、电化学加工 261
第七节 油石及润滑冷却液 264
一、油石的作用和对油石的要求 264
二、影响油石工作性能的因素 265
三、润滑冷却液的作用和要求 269
四、润滑冷却液的成分 270
第八节 套圈超精加工的质量检查及质量分析 270
一、表面质量分析 270
二、加工精度分析 272
第七章 滚子加工 273
第一节 概述 273
第二节 圆锥滚子制造 275
一、圆锥滚子技术条件 275
二、圆锥滚子加工过程 276
三、圆锥滚子主要加工工序分析 277
第三节 圆柱滚子制造 314
一、圆柱滚子技术条件说明 314
二、圆柱滚子加工方法概述 315
三、圆柱滚子制造过程 315
四、圆柱滚子主要加工工序分析 316
第四节 球面滚子制造 328
一、概述 328
二、球面滚子主要加工工序分析 328
第五节 滚针制造 332
一、概述 332
二、滚针主要加工工序分析 333
第六节 防止滚子碰磕伤 336
一、车制滚子旋转式缓冲装置 336
二、热处理淬火炉下料防碰磕伤装置 337
三、细磨过程的防碰磕伤装置 337
四、精、终磨过程的防碰磕伤装置 337
第八章 钢球加工 339
第一节 钢球加工概述 339
一、钢球的工作状态与损坏形式 339
二、钢球加工的基本工艺路线 341
第二节 钢球毛坯成形 342
一、冷镦压成形 342
二、镦压球坯形状的改进——锥鼓形球坯 344
三、热镦压和球化退火 346
四、轧制成形 346
五、锻造成形 346
六、钢球毛坯的有关计算 346
第三节 钢球毛坯的锉削与软磨 348
一、锉削加工 348
二、软磨加工 349
三、小型钢球的软窜和软研 349
四、φ26~φ48mm钢球毛坯去环带、粗锉及初磨 349
第四节 光磨加工 350
一、光磨加工原理 350
二、光磨机理 351
三、光磨板的材料 351
四、光磨板的修整 352
第五节 钢球的硬磨、硬研、初研和抛光 353
一、硬磨 353
二、硬研和初研 354
三、抛光 355
第六节 钢球的表面强化处理 355
一、钢球表面强化原理 355
二、强化时间对表面质量的影响 356
三、强化钢球表面硬度与应力分布 358
第七节 钢球的精研 359
一、精研加工方法 359
二、精研过程的特征 361
三、国外钢球研磨、初研、精研工艺及装备 361
四、精研盘沟槽 363
第八节 钢球加工余量 368
一、钢球加工余量的确定 368
二、钢球加工余量与钢球制造水平的关系 370
第九节 钢球加工的成圆条件 370
一、机床结构与输球方式 371
二、机床精度的影响 371
三、研磨盘沟槽形状的影响 372
四、磨盘参数的影响 373
五、加工参数的影响 373
六、“误差复映”规律的影响 374
第十节 陶瓷球加工工艺 374
一、陶瓷球加工的技术难点 375
二、陶瓷球加工方法 375
三、高精度陶瓷球批量加工技术 377
第九章 保持架加工 380
第一节 概述 380
一、保持架的作用和结构特征 380
二、保持架的基本种类 380
三、保持架的材料和热处理 382
第二节 冲压保持架 383
一、冲压保持架的工艺特点 383
二、冲压工艺基础 384
三、浪形保持架制造 397
四、圆锥保持架制造 405
五、球面保持架制造 417
六、冲压保持架制造的辅助工序和表面处理 420
第三节 车制保持架 423
一、概述 423
二、保持架的车制 423
三、车制保持架的喷砂处理工艺 425
四、车制保持架的钻铰孔加工 427
五、车制保持架的拉削加工 428
第四节 压铸保持架和注塑保持架简介 430
一、压铸法制造保持架 430
二、注塑法制造保持架 430
第十章 轴承装配原理 431
第一节 轴承装配概述 431
一、装配的基本概念和术语 431
二、轴承装配质量指标和基本要求 432
三、轴承的装配特点 432
四、轴承装配的一般过程 433
第二节 轴承配套计算方法 435
一、径向游隙的保证 436
二、轴承宽度的保证 437
第三节 轴承最优配套原理 440
一、保证径向游隙的配套公式 440
二、最高合套率条件 447
三、获得最高合套率的优选始值 448
第四节 圆锥滚子轴承随机装配原理 450
一、随机装配方法的产生 451
二、随机装配的本质 451
三、随机装配的数学描述 452
四、工艺过程的控制 454
思考题 456
参考文献 460
- 《葡萄酒工艺与鉴赏 第3版》廖祖宋 2019
- 《化学工程与工艺专业实验指导》郭跃萍主编 2019
- 《美物之道 日本手工艺》(日)柳宗悦著 2019
- 《有色金属冶金新工艺与新技术》俞娟,王斌,方钊,崔雅茹,袁艳 2019
- 《洗涤剂生产工艺与技术》宋小平,韩长日主编 2019
- 《皮革用化学品生产工艺与技术》宋小平,韩长日著 2018
- 《玉米淀粉绿色精益制造 新工艺、新设备、新理念》佟毅 2018
- 《天然气净化工艺技术进展》顾晓峰编著 2019
- 《中国工艺美术史》王树良 2019
- 《化学工程与工艺专业实验》李岩梅,周丽主编 2018
- 《市政工程基础》杨岚编著 2009
- 《家畜百宝 猪、牛、羊、鸡的综合利用》山西省商业厅组织技术处编著 1959
- 《《道德经》200句》崇贤书院编著 2018
- 《高级英语阅读与听说教程》刘秀梅编著 2019
- 《计算机网络与通信基础》谢雨飞,田启川编著 2019
- 《看图自学吉他弹唱教程》陈飞编著 2019
- 《法语词汇认知联想记忆法》刘莲编著 2020
- 《培智学校义务教育实验教科书教师教学用书 生活适应 二年级 上》人民教育出版社,课程教材研究所,特殊教育课程教材研究中心编著 2019
- 《国家社科基金项目申报规范 技巧与案例 第3版 2020》文传浩,夏宇编著 2019
- 《流体力学》张扬军,彭杰,诸葛伟林编著 2019
- 《指向核心素养 北京十一学校名师教学设计 英语 七年级 上 配人教版》周志英总主编 2019
- 《北京生态环境保护》《北京环境保护丛书》编委会编著 2018
- 《高等教育双机械基础课程系列教材 高等学校教材 机械设计课程设计手册 第5版》吴宗泽,罗圣国,高志,李威 2018
- 《指向核心素养 北京十一学校名师教学设计 英语 九年级 上 配人教版》周志英总主编 2019
- 《高等院校旅游专业系列教材 旅游企业岗位培训系列教材 新编北京导游英语》杨昆,鄢莉,谭明华 2019
- 《中国十大出版家》王震,贺越明著 1991
- 《近代民营出版机构的英语函授教育 以“商务、中华、开明”函授学校为个案 1915年-1946年版》丁伟 2017
- 《新工业时代 世界级工业家张毓强和他的“新石头记”》秦朔 2019
- 《智能制造高技能人才培养规划丛书 ABB工业机器人虚拟仿真教程》(中国)工控帮教研组 2019
- 《AutoCAD机械设计实例精解 2019中文版》北京兆迪科技有限公司编著 2019