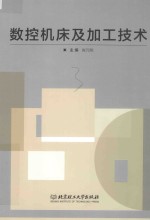
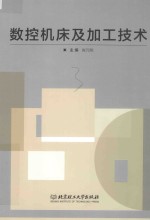
数控机床及加工技术PDF电子书下载
- 电子书积分:12 积分如何计算积分?
- 作 者:崔元刚主编
- 出 版 社:北京:北京理工大学出版社
- 出版年份:2016
- ISBN:9787568228961
- 页数:321 页
第一章 数控机床概述 1
1.1 认识数控机床 2
1.1.1 数控机床概念 2
1.1.2 数控概念 2
1.1.3 数控机床基本组成 4
1.1.4 数控加工一般过程 6
1.1.5 数控加工特点 7
1.2 认识各种类别的数控机床 9
1.2.1 普通数控机床 9
1.2.2 加工中心机床(MC) 11
1.2.3 柔性制造 13
1.2.4 计算机集成制造系统(CIMS) 13
1.3 数控机床的坐标系规定 14
1.3.1 进给运动与坐标系 14
1.3.2 数控机床标准坐标系规定 14
1.3.3 典型的数控机床坐标系规定 16
1.3.4 参考点及回参考点操作 18
1.3.5 设定工件坐标系 19
1.4 认识机床数控系统 19
1.4.1 数控系统概述 19
1.4.2 数控系统硬件体系结构 19
1.4.3 数控系统软件的功能结构 22
1.4.4 计算机数控系统的控制功能 22
第二章 数控机床运动控制 26
2.1 进给插补 26
2.1.1 插补的概述 26
2.1.2 插补方法举例——逐点比较法 28
2.2 进给伺服系统 30
2.2.1 进给伺服系统的概念 30
2.2.2 开环进给伺服系统 31
2.2.3 闭环进给伺服系统 33
2.3 进给系统机械 37
2.3.1 进给机械简介 37
2.3.2 典型的进给机械部分 38
2.4 数控机床主轴驱动 41
2.4.1 数控机床主轴驱动要求 41
2.4.2 主轴驱动装置及驱动特性 41
2.4.3 主轴传动 44
2.4.4 主轴自动控制功能 45
2.5 数控机床主轴支承 48
2.5.1 主轴的回转精度 48
2.5.2 数控机床上常用主轴轴承 48
2.5.3 主轴的轴承配置形式 50
第三章 数控加工程序 54
3.1 加工程序基本规定 55
3.1.1 加工程序概述 55
3.1.2 加工程序指令字格式 55
3.1.3 加工程序指令字的种类 57
3.1.4 FANUC系统常用G指令格式及应用 60
3.1.5 FANUC铣削系统常用M指令 66
3.1.6 其他指令应用说明 67
3.1.7 加工程序格式 68
3.1.8 编制数控加工程序举例 69
3.2 刀具补偿指令及其应用 70
3.2.1 刀具半径补偿 70
3.2.2 刀具长度补偿 76
第四章 数控加工工艺设计知识 82
4.1 数控加工工艺设计过程 83
4.1.1 零件机械加工工艺总规划 83
4.1.2 数控加工工序设计 86
4.2 数控加工装夹设计 90
4.2.1 工件的定位 90
4.2.2 工件夹紧 96
42.3 数控车削装夹 97
4.2.4 数控铣、加工中心常用夹具 100
4.2.5 夹具选用 101
4.3 熟悉数控刀具及选用 103
4.3.1 数控刀具要求 103
4.3.2 了解刀具类型及选用 104
4.3.3 刀具基本几何参数及选用 105
4.3.4 刀具材料选择 107
4.3.5 可转位刀具 110
4.3.6 数控工具系统 113
4.4 数控加工刀具路径拟定 115
4.4.1 规划安全的刀具路径 116
4.4.2 规划保证加工质量的刀具路径 118
4.4.3 规划高效率的刀具路径 121
4.5 切削用量选用一般方法 122
4.5.1 刀具切削用量的概念 122
4.5.2 切削用量选择原则 124
4.5.2 切削用量选用方法 126
4.6 先导案例的解决 127
4.6.1 壳体零件加工工艺规程 127
4.6.2 壳体加工中心工序工艺设计 128
第五章 数控车床应用 133
5.1 数控车床概述 134
5.1.1 数控车床类型 134
5.1.2 典型的数控车床组成 134
5.1.3 数控车削的主要加工对象 137
5.2 数控车床对刀与偏置、补偿应用 137
5.2.1 数控车床坐标系及机床各点 137
5.2.2 数控车床的零点偏置与长度补偿 140
5.2.3 刀具磨损偏置及应用 142
5.2.4 FANUC车削系统刀具T指令 144
5.3 FANUC系统数控车床编程简介 144
5.3.1 FANUC数控车床指令 144
5.3.2 部分FANUC数控车削指令应用说明 146
5.4 外圆车削工艺及编程 149
5.4.1 车削外圆表面工艺 149
5.4.2 G01车削外圆 150
5.4.3 G90单一循环车削圆柱面 151
5.4.4 G90单一循环车削圆锥面 152
5.4.5 G71多重复合循环粗车外径 154
5.4.6 精车固定循环G70 156
5.4.7 G73成型加工复合循环粗车外径 157
5.5 端面车削工艺及编程 159
5.5.1 车削端面 159
5.5.2 G01单次车削端面 160
5.5.3 G94单一循环切削端面 160
5.5.4 G94单一循环切削端锥面 162
5.5.5 G72复合循环切削端锥面 163
5.6 可转位车刀片的刀尖圆弧及半径补偿应用 165
5.6.1 可转位车刀片的刀尖圆弧及选用 165
5.6.2 带刀尖圆弧可转位刀片的应用 166
5.7 内孔加工工艺及编程 170
5.7.1 数控车床上孔加工工艺概述 170
5.7.2 数控车床上孔加工编程 172
5.7.3 数控车床上孔加工工艺及编程实例 174
5.8 切槽、切断工艺及编程 176
5.8.1 凹槽加工工艺要点 176
5.8.2 简单凹槽切削工艺编程 178
5.8.3 精确凹槽加工技术 179
5.8.4 G75沟槽复合循环 181
5.8.5 子程序在多槽加工中的应用实例 184
5.8.6 切断 185
5.9 螺纹车削加工工艺及编程 187
5.9.1 螺纹加工概念及加工工艺 187
5.9.2 G32螺纹切削指令应用 190
5.9.3 螺纹切削单一固定循环G92 192
5.9.4 螺纹切削复合循环G76 193
5.9.5 内螺纹切削编程示例 195
5.10 先导案例解决 196
5.10.1 加工工艺分析 196
5.10.2 加工程序 198
第六章 数控铣削加工 205
6.1 数控铣床及选用 206
6.1.1 认识数控铣床 206
6.1.2 数控铣床或加工中心选用 207
6.1.3 数控铣削加工对象 208
6.2 CNC铣床零点偏置和长度补偿 209
6.2.1 数控铣床零点偏置 209
6.2.2 基于零点偏置的X、Y向对刀方法 211
6.2.3 数控铣床Z向对刀 213
6.3 平面铣削工艺编程 215
6.3.1 平面铣削加工的内容、要求 215
6.3.2 平面铣削方法 215
6.3.3 面铣刀及选用 216
6.3.4 平面铣削的路线设计 217
6.3.5 平面铣削用量 218
6.3.6 单次面铣的加工实例 219
6.3.7 大平面铣削时的刀具路线 221
6.4 立铣刀及铣削工艺选择 221
6.4.1 立铣刀及选用 222
6.4.2 立铣刀切削用量选用 225
6.4.3 顺铣与逆铣方式选用 226
6.5 轮廓铣削工艺及编程 227
6.5.1 轮廓铣削实例 227
6.5.2 子程序在分层铣削中的应用 229
6.5.3 正六边形轮廓铣削实例 231
6.6 槽铣削工艺及编程 233
6.6.1 铣槽加工工艺简介 233
6.6.2 半开放窄槽加工实例 236
6.6.3 封闭窄槽加工工艺实例 237
6.7 型腔铣削工艺及编程 238
6.7.1 型腔铣削加工的内容、要求 238
6.7.2 型腔铣削方法 239
6.7.3 型腔铣削加工实例 240
6.8 简化的编程方法 244
6.8.1 极坐标编程 244
6.8.2 比例缩放指令及应用 246
6.8.3 坐标系旋转指令应用 247
6.9 先导案例解决 249
6.9.1 工件工艺设计先导案例 249
6.9.2 编写加工程序 252
第七章 加工中心应用 257
7.1 加工中心自动换刀 257
7.1.1 刀库形式 258
7.1.2 刀具选择方式及ATC换刀的特点 259
7.1.3 刀具换刀装置和交换方式 261
7.1.4 换刀程序的编制 263
7.1.5 加工中心自动换刀程序 265
7.2 孔加工要求及孔加工固定循环 267
7.2.1 孔加工概述 267
7.2.2 孔加工固定循环格式 267
7.2.3 钻孔加工循环及应用 270
7.3 钻孔、扩孔、锪孔加工工艺及编程 274
7.3.1 实体上钻孔加工 274
7.3.2 扩孔加工 278
7.3.3 锪孔加工 279
7.3.4 孔加工工艺编程实例 280
7.4 攻丝工艺及编程 283
7.4.1 攻丝加工的内容、要求 283
7.4.2 丝锥及选用 284
7.4.3 CNC机床攻丝工艺与编程 286
7.4.4 攻内螺纹工艺编程实例 289
7.5 铰孔工艺及编程 291
7.5.1 铰孔加工工艺 291
7.5.2 铰孔工艺编程实例 294
7.6 镗孔工艺及编程 296
7.6.1 镗孔加工概述 296
7.6.2 镗刀及选用 297
7.6.3 镗孔循环 298
7.6.4 镗孔工艺和编程实例 300
7.7 加工中心Z向对刀方案设计 304
7.7.1 机床、刀具、工件的位置点及Z向对刀问题 304
7.7.2 机床、刀具、工件在Z方向相对位置值及寄存 305
7.7.3 典型Z向对刀方案设计 306
7.8 先导案例解决 309
7.8.1 刀具编号及程序结构设计 309
7.8.2 自动换刀多刀加工程序 309
附表 315
附表1 硬质合金外圆车刀切削速度参考值 315
附表2 硬质合金车刀粗车外圆、端面的进给量 316
附表3 按工件表面粗糙度选择车削进给量的参考值 316
附表4 成量集团公司数控刀具硬质合金铣刀切削用量选用参考 317
附表5 硬质合金内孔钻削、扩削切削用量选用参考 318
附表6 高速钢铰刀切削用量选用参考 318
附表7 镗削用量选用参考 319
附表8 内螺纹攻丝切削速度选用参考 319
参考文献 321
- 《代用茶加工学》黄友谊主编 2017
- 《题诗加评聊斋志异外集》留仙后人著 1930
- 《光栅尺支架夹具设计及数控加工》张方阳 2019
- 《数控机床主轴系统在线动平衡技术》王展 2020
- 《航空复杂零件数控加工工艺设计与优化》任军学 2018
- 《VERICUT数控仿真实例教程》黄雪梅编著 2019
- 《数控铣削编程与加工 第2版》赵刚主编 2019
- 《UG NX 8.5数控加工自动编程经典实例 第3版》(中国)钟平福 2019
- 《Mastercam2018数控加工实例教程 第2版》贺建群编著;贺学农主审 2019
- 《翦伯赞全集 第10卷 中外历史年表 主编》翦伯赞著 2008
- 《大学计算机实验指导及习题解答》曹成志,宋长龙 2019
- 《指向核心素养 北京十一学校名师教学设计 英语 七年级 上 配人教版》周志英总主编 2019
- 《大学生心理健康与人生发展》王琳责任编辑;(中国)肖宇 2019
- 《大学英语四级考试全真试题 标准模拟 四级》汪开虎主编 2012
- 《大学英语教学的跨文化交际视角研究与创新发展》许丽云,刘枫,尚利明著 2020
- 《北京生态环境保护》《北京环境保护丛书》编委会编著 2018
- 《复旦大学新闻学院教授学术丛书 新闻实务随想录》刘海贵 2019
- 《大学英语综合教程 1》王佃春,骆敏主编 2015
- 《大学物理简明教程 下 第2版》施卫主编 2020
- 《指向核心素养 北京十一学校名师教学设计 英语 九年级 上 配人教版》周志英总主编 2019