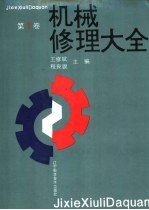
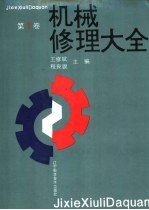
机械修理大全 第1卷PDF电子书下载
- 电子书积分:36 积分如何计算积分?
- 作 者:王修斌,程良骏主编
- 出 版 社:沈阳:辽宁科学技术出版社
- 出版年份:1993
- ISBN:7538116745
- 页数:1545 页
第一篇 机械修理基础 1
第一章 机修常用金属材料及热处理 1
第一节 金属材料的基本性能 1
一、金属材料的力学性能 1
二、金属的物理、化学性能 1
三、金属材料的工艺性能 2
第二节 机修常用金属材料 3
一、常用金属材料的性能及用途 3
二、常用钢材的识别 15
第三节 钢的热处理 19
一、钢铁的金相组织 19
二、热处理的一般工艺 24
第四节 常用有色金属材料 27
一、铝及其合金 28
二、铜及其合金 30
第五节 机修材料的选择 37
一、机修选材的一般原则 37
三、典型零件的选材 38
二、按机械的性能指标选材 38
第一节 尺寸链的组成 41
一、尺寸链的组成 41
二、尺寸链的分类 41
第二章 尺寸链原理及其在机修中的应用 41
第二节 机修尺寸链的分析与计算 43
一、机修尺寸链的分析 43
二、机修尺寸链的计算 43
三、尺寸链在机修中的应用 46
一、合理选择修理基准 52
四、计算组成环尺寸精度时应考虑的问题 52
第三节 修理基准和修理程序的确定 52
二、修理程序的安排 54
第四节 尺寸链原理在机修中的应用举例 55
一、修理件尺寸公差的计算 55
二、配件加工的尺寸公差的计算 56
三、尺寸链原理在机修中的应用实例 56
三、故障分析的一般过程与步骤 58
二、机械系统的常见故障类型 58
第二节 动力系统的常见故障 58
第三章 机械系统的常见故障 58
第一节 机械系统的常见故障与分析 58
一、概述 58
一、动力源的常见故障 59
二、动力机故障 59
三、动力传输系统供气热管道的常见故障 59
第三节 机械紧固件的常见故障 60
一、紧固件失效的起因 60
二、紧固件失效分析 60
三、紧固件的失效处理 60
第四节 润滑系统的常见故障 60
一、液动压润滑系统的故障 60
二、液静压润滑系统的故障 60
三、弹性液动压润滑系统的故障 60
第五节 传动系统的常见故障 61
二、齿轮类零件的故障分析 61
一、轴类零件的故障分析 61
四、边界润滑系统的失效 61
五、润滑剂失效导致磨损 61
第六节 弹簧的故障分析 62
一、弹簧失效的主要原因 62
二、弹簧失效的形式 62
第七节 机械系统的温升失效 62
一、滑动轴承的温升失效 62
二、其它机械噪声故障 63
第九节 机械系统故障的诊断与预防技术 63
三、电磁、液压系统及润滑系统的噪声故障 63
三、传动系统的温升失效 63
一、齿轮噪音故障 63
第八节 机械系统的噪声故障 63
二、滚动轴承的电点蚀失效 63
一、机械系统故障的诊断 64
二、机械系统故障预防 64
二、受力分析与强度计算 65
一、机械零件失效基本概念 65
第四章 机械零件常见失效分析与处理 65
第一节 机械零件的失效概述 65
三、机械零件在外加载荷作用下的力学行为及其力学性能 73
四、机械零件失效形式分类 73
五、机械零件的失效分析 73
第二节 机械零件的变形失效与处理 73
一、变形失效特征分析 74
二、变形失效分析 74
三、机械零件变形失效的检测与判断方法 75
四、机械零件变形失效分析与处理实例 75
第三节 机械零件的断裂失效与处理 77
一、断裂的基本现象和概述 77
二、机械零件的断口分析 78
三、裂纹分析 84
四、机械零件的断裂失效分析 91
第四节 磨损失效的分析判断及预防 95
一、磨损的基本类型 95
二、磨损机理 96
三、磨损失效判断和改善耐磨性的措施 97
四、减少磨损的途经及预防措施 99
第五章 机械修理的组织与准备 102
第一节 机械修理的技术准备 102
一、机器设备图册的编制 102
二、机械零件测绘时应注意的事项 103
三、修理前的技术准备 103
二、机械零件修复工艺的选择 104
一、机械零件修复工艺的分类 104
第二节 机械修理方案与工艺选择 104
三、机械修理方案的编制 105
第三节 机械修理的组织形式 109
一、集中修理组织形式 109
二、分散修理组织形式 109
五、填写验收卡片 110
四、机械负载运转后的验收 110
三、机械的负载运转验收 110
二、机械的空运转检查验收 110
一、试车验收前的准备 110
第四节 机械修理的验收 110
三、混合修理组织形式 110
第六章 机械零部件的拆装 113
第一节 机械零部件的拆卸 113
一、拆卸前的准备工作 113
二、拆卸的一般原则 113
三、拆卸时的注意事项 113
四、常用零部件的拆卸方法 114
第二节 机械零部件的装配 118
一、装配综述 118
二、装配的一般工艺要点 118
第三节 机械零部件的装配调整 124
第七章 机械零件修复的一般工艺 127
第一节 机械零件的焊接修理 127
一、手工电弧焊 127
二、振动堆焊 131
三、CO2气体保护堆焊 133
四、等离子弧堆焊 134
五、埋弧堆焊 135
六、气焊 137
七、有色金属零件的焊修 139
八、焊接缺陷及检验 153
九、焊接修理应用举例 155
第二节 机械零件的电镀修理 157
一、概述 157
二、镀铁 158
三、镀铬 163
四、刷镀 165
五、其它电镀方法简介 168
第三节 机械零件的喷涂修理 169
一、金属喷涂 169
二、氧--乙炔火焰喷焊 173
三、应用举例--金属喷涂修复曲轴工艺 174
一、胶粘工艺的特点和应用 176
第四节 机械零件的胶粘修理 176
二、常用胶粘剂的性能及组成 177
三、胶粘质量的主要影响因素 180
四、胶粘技术在机械修理中的应用举例 184
第五节 机械零件的机械和压力加工修理 186
一、修理尺寸法 186
二、镶套修理法 186
三、掠夺与扩张修理法 187
四、零件的局部更换、转向和翻转修理法 188
第八章 圆柱齿轮传动的修理 189
第一节 渐开线圆柱齿轮传动的基本概念与尺寸计算 189
一、圆柱齿轮传动几何要素的名称及代号 189
二、圆柱齿轮传动基本几何要素意义 189
三、一对渐开线齿轮的啮合传动 192
四、标准圆柱齿轮传动的几何计算 193
五、变位齿轮传动 195
一、渐开线圆柱齿轮精度国家标准简介 202
第二节 渐开线齿轮传动精度的应用 202
二、精度等级的选择 206
三、齿轮精度检验项目的选择 207
四、修理齿轮精度等级的确定 208
第三节 齿轮传动的失效及材料选择 210
一、齿轮传动的失效形式及其分析 210
二、齿轮传动异常现象的检查和处理 210
三、齿轮常用材料 213
四、修理齿轮的材料及热处理选择 215
第四节 渐开线圆柱齿轮传动的测绘 216
一、齿轮测绘概述 216
二、齿轮测绘的前期工作 216
三、渐开线直齿圆柱齿轮的测绘 216
四、平行轴斜(人字)齿圆柱齿轮的测绘 225
五、交叉轴齿轮传动的测绘 230
六、齿条的测绘 230
二、轮齿失效后的修复 231
一、修复齿轮应满足的基本要求 231
七、内齿轮传动的测绘 231
第五节 渐开线圆柱齿轮传动的修复 231
三、轮缘或轮辐裂损后的修复 235
四、齿轮键槽损坏后的修复 235
五、齿轮轮毂孔磨损后的修复 236
六、齿轮轮毂裂纹和轮毂端面磨损后的修复 237
七、渐开线圆柱齿轮传动质量的改善 237
第六节 渐开线圆柱齿轮传动的配换 237
二、齿轮配换原则和配换齿轮传动的确定 238
一、齿轮配换的应用 238
三、齿轮配换修理举例 239
第九章 圆锥齿轮传动的修理 243
第一节 圆锥齿轮传动的基本概念与尺寸计算 243
一、锥齿轮传动的类型及特点 243
二、锥齿轮传动几何要素名称及代号 244
三、锥齿轮传动基本概念 244
四、锥齿轮传动的几何计算 248
一、圆锥齿轮精度标准(GB11365-89)简介 250
第二节 圆锥齿轮精度 250
二、圆锥齿轮精度标准的应用 254
第三节 圆锥齿轮传动的测绘 258
一、锥齿轮测绘特点 258
二、测绘锥齿轮的一般程序与方法 258
三、锥齿轮及其齿轮付几何尺寸及有关数据的测定 258
四、锥齿轮基本参数的确定 260
五、锥齿轮的齿形制度辨别 262
七、锥齿轮测绘举例 263
六、锥齿轮的简化测绘 263
第四节 锥齿轮的修复与配换 265
一、修理锥齿轮传动应遵行的原则 265
二、锥齿轮的修复 265
三、单个配换锥齿轮的应用及配对设计要求 265
四、锥齿轮的齿型替代 265
五、锥齿轮的零配切齿工艺 269
六、锥齿轮零配方法简介 269
二、齿轮付的装配与调整 273
一、拆卸 273
第五节 齿轮传动的拆装与调整 273
第六节 齿轮传动质量的改善 276
一、轮齿修形 277
二、合理选择齿根过渡曲线半径,以提高轮齿的弯曲强度 278
三、选用线膨胀系数相同或相近的材料制造齿轮及其支承部件 280
四、增强轮体、支承壳体和轴承的刚性 280
五、尽量使轮体不存在薄弱环节 281
七、改善齿轮传动的润滑 282
六、易损部位的分离或改进 282
第十章 蜗杆传动的修理 285
第一节 蜗杆传动的基本知识 285
一、蜗杆传动的特点及其应用 285
二、蜗杆传动的分类 285
三、普通圆柱蜗杆传动的基本参数及几何尺寸计算 285
四、蜗杆传动的失效形式及材料选择 290
五、蜗杆、蜗轮的结构 290
二、精度等级 292
一、适用范围 292
第二节 圆柱蜗杆传动的精度及公差 292
三、蜗杆、蜗轮及传动的公差组 293
四、蜗杆、蜗轮公差项目检验组 293
五、蜗杆、蜗轮的公差及其数值 293
六、传动的检验及公差值 294
七、传动侧隙 301
八、传样标注 303
九、圆柱蜗杆传动公差或偏差应用示例 306
一、普通圆柱蜗杆螺旋面类型鉴别 307
第三节 蜗杆、蜗轮的测绘 307
二、蜗杆、蜗轮的几何尺寸测量 308
三、蜗杆、蜗轮基本参数的确定 309
四、蜗杆、蜗轮测绘方法及步骤 312
第四节 蜗杆、蜗轮的修配 313
一、蜗杆、蜗轮修换的一般原则 313
二、蜗杆、蜗轮及蜗杆付误差检验 313
三、蜗杆、蜗轮的损伤分析及修配方案选择 313
四、蜗杆齿形修复方法 319
五、蜗轮齿形修复方法 320
第五节 蜗杆副的安装及调整 332
一、蜗杆副的安装工艺 332
二、蜗杆副的安装调整 334
第六节 改善蜗杆传动质量的措施 335
一、合理选择蜗杆副的材料及传动参数,以提高蜗杆传动的承载能力和传动效率 335
二、合理选择蜗杆传动的润滑方式及润滑剂以提高传动的抗磨损、抗胶合能力 337
三、提高蜗杆、蜗轮的制造和安装精度,以利提高蜗杆传动的精度、承载能力及使用寿命 338
一、滚动轴承的基本构造 343
二、滚动轴承的优缺点分析 343
第十一章 滚动轴承的修理 343
第一节 滚动轴承的特点与代号 343
三、滚动轴承的分类 344
四、滚动轴承的代号 345
第二节 滚动轴承的选用 347
一、常用滚动轴承的类型及主要性能 347
二、选用滚动轴承类型的一般原则 349
二、轴承的安装方法 350
一、安装前的准备工作 350
三、选择滚动轴承的步骤 350
第三节 滚动轴承的安装 350
三、轴承游隙的调整 351
四、轴承安装后的检查 352
第四节 滚动轴承的拆卸 352
一、轴承拆卸时的注意事项 353
二、拆卸方法 353
三、带紧定套轴承和带退卸套轴承的拆卸 353
第五节 滚动轴承的常见故障及其原因 354
一、滚动轴承的鉴别 354
二、滚动轴承的常见故障及原因分析 354
第六节 滚动轴承的代用 355
一、滚动轴承的代用原则 355
二、滚动轴承的一般代用方法 355
三、滚动轴承的改制代用 356
一、修理轴承的拆套 357
二、轴承零件的除油去锈处理 357
第七节 滚动轴承的修理 357
三、几种简易的修复方法 358
四、常用几类轴承的修理 359
五、轴承的组装 361
六、轴承修理后的质量检验标准 362
第八节 滚动轴承的润滑和密封 364
一、滚动轴承的润滑方法 364
二、滚动轴承的密封 364
一、滑动轴承的特点 365
三、滑动轴承的典型结构 365
二、滑动轴承的分类 365
第一节 滑动轴承概述 365
第二十章 滑动轴承的修理 365
四、常用的轴瓦材料 368
五、轴瓦的结构 369
六、滑动轴承润滑剂的选择 370
第二节 滑动轴承的损坏形式及分析 371
一、异常磨损 371
二、擦伤 371
三、划伤 372
四、粘着 372
五、咬死 372
八、轴承减摩层变形 373
九、疲劳 373
六、杂质入侵 373
七、过热 373
十、腐蚀 374
十一、电火花浸蚀 374
十二、气蚀 374
十三、微动磨损和微动腐蚀磨损 374
十四、浸蚀 375
十五、机械的故障 375
十六、气泡、气孔与夹杂物 375
第三节 滑动轴承的修理 375
一、巴氏合金的浇铸 375
二、铜铅合金的浇铸 377
三、轴承的校合 378
一、概述 380
二、普通V型带传动及修理 380
第十三章 带传动和链传动的修理 380
第一节 带传动的修理 380
三、平带传动及修理 383
四、同步齿形带传动及其修理 389
第二节 链传动的修理 394
一、链传动的故障及修理 394
二、链条清洗与拆装 394
三、链轮的修理 395
第十四章 轴类零件的修理 399
第一节 轴类零件的常见失效形式与分析 399
一、轴类零件的常见失效形式与分析 399
二、电镀修理法 401
一、修理尺寸法 401
三、金属喷涂修理法 401
第二节 轴类零件的磨损修理 401
四、镶套修理法 403
五、堆焊修理法 403
第三节 轴类零件断裂修理 404
七、轴上圆角磨损的修理 404
一、轴上裂纹的修理 404
六、过盈配合轴颈磨损的修复 404
第四节 轴类零件变形后的修复 405
一、轴弯曲变形后的修复 405
二、断轴的修理 405
二、轴扭曲变形后的修复 408
第五节 细长轴的修理 408
第六节 花键轴的修理 409
第七节 曲轴的修理 411
一、曲轴的测量 411
二、曲轴的磨削 412
三、曲轴轴颈磨损超限后的修复 414
第八节 锥形轴的修理 415
第十五章 螺旋传动 417
第一节 螺旋传动的材料 417
第二节 梯形螺纹标准和公差 417
第三节 丝杠传动的修理 421
第十六章 固定联接的修理 424
第一节 螺纹联接的修理 424
一、螺纹联接的装配 424
二、螺纹联接的拆卸 425
三、螺纹的修理 425
第二节 键联接的修理 426
一、平键 426
二、斜键 427
三、花键 428
第一节 联轴器修理应注意的问题 434
第二节 联轴器及修理 434
一、刚性固定式联轴器 434
第十七章 联轴器的修理 434
二、刚性可移式联轴器 436
三、弹性联轴器 438
二、轴类零件的非正常失效与分析 440
第十八章 铸件的修理 444
第一节 铸件缺陷及其修补 444
一、常见的铸件缺陷及其检验 444
二、铸件缺陷的修补 444
第二节 修复大型铸件的金属扣合法 445
一、强固扣合法 445
二、强密扣合法 447
三、优级扣合法 447
四、热扣合法 448
第十九章 工程塑料及其在机修中的应用 450
一、塑料的分类 450
二、工程塑料的性能 450
三、工程塑料的加工 458
四、常用工程塑料的性能及应用举例 459
五、塑料材料选用的一般原则 462
六、工程塑料在机修中的应用 462
二、计划预防修理制度的主要内容 471
一、计划预防修理制度的特点 471
第二十章 机械修理制度和修理决策技术 471
第一节 计划预防修理制度 471
三、设备的修理周期结构 472
四、设备修理复杂系数和修理定额 473
五、设备维修的计划和滚动计划法 474
第二节 以状态监测为基础的修理制 474
一、以状态监测为基础的修理制的特点 474
二、设备点检制 475
二、修理方式决策 477
一、概述 477
第三节 针对性修理制和修理决策技术 477
三、修理时机和范围决策 479
第二篇 常用修理工具和量具 483
第一章 手工工具 483
一、手钳 483
二、扳手 486
三、螺钉旋具 488
二、锉刀 491
第二章 钳工工具 491
一、虎钳 491
三、钢锯 493
四、手钻 493
五、手锤 495
六、刮刀,錾子 495
七、丝锥 496
八、板牙 497
九、扳手 499
十、手砂轮 499
十一、划线工具 500
十二、冲子 500
第三章 管工工具 502
一、管子台虎钳 502
二、扳手 502
三、管子割刀 502
四、管子铰板 502
五、扩管器 503
第四章 电工工具 504
一、电工钳 504
二、电工刀 505
三、电烙铁 505
四、测电器 505
第五章 焊工器具 506
一、电焊器材 506
二、电焊工具 514
三、气焊器材 514
四、气焊工具 520
第六章 拉、压及起重工具 523
一、拉器 523
二、压力机 523
三、起重工具 523
第七章 测量工具 527
一、量具 527
二、量规 531
三、量仪 537
一、计划预修制和修理周期 542
第一节 计划预修制和排除故障修理 542
第三篇 金属切削机床修理 542
第一章 机床修理的特性 542
二、机床的排除故障修理 544
第二节 机床修理后的质量要求 544
一、金属切削机床精度等级的划分 545
二、金属切削机床修理通用技术条件 546
三、金属切削机床电气修理通用技术条件 552
第三节 机床大修理工艺流程和零件的修换原则 556
一、机床大修理的工艺流程 556
二、机床零件的修理、更换原则 557
三、制造新零件应注意的问题 561
第二章 机床的拆卸、装配与调整 562
第一节 机床的拆卸与清洗 562
一、拆卸的常用工具 562
二、机床拆卸的一般步骤 562
三、部件拆卸 563
五、零件的清洗与清理 565
四、机床零件拆卸应注意的问题 565
第二节 机床修理的装配与调整 567
一、滑动轴承的修理、装配与调整 567
二、滚动轴承的装配与调整 582
三、滚珠丝杠螺母机构的拆、装及调整 588
第三章 机床修理精度检测方法 592
第一节 机床基础件的精度检测方法 592
一、导轨直线度的检测方法 592
二、导轨平行度的检测方法 598
三、工作台平面度的检测方法 599
第二节 位置精度的检测方法 603
一、部件间垂直度的检测方法 603
二、部件间平行度的检测方法 604
三、同轴度的检测方法 606
四、轴线相交度的检测方法 607
五、等高度的检测方法 607
第三节 机床部件的运动精度检测方法 608
一、部件运动的直线度检测方法 608
三、部件运动的垂直度检测方法 609
二、部件运动的平行度检测方法 609
四、机床部件运动的倾斜度检测 611
第四节 机床主轴及工作台旋转精度的检测方法 611
一、经向跳动的检测方法 611
二、周期性轴向窜动的检测方法 613
三、端面跳动的检测方法 613
第五节 分度精度的检测方法 614
一、打表法 614
二、多面棱体检测法 614
三、比较测量法 615
四、经纬仪检测法 616
第六节 定位精度的检测方法 616
一、全程定位精度的检测 616
二、重复定位精度的检测 616
三、原点复归精度的检测 617
四、定位精度的检测的数据处理 617
三、点轮机床和螺纹机床的精度论断 619
二、机床故障与相关项目的监测论断 619
第四章 机床传动精度论断与提高 619
一、机床精度论断对机修的意义 619
第一节 机床修理与精度论断 619
第二节 机床传动误差来源简介 621
一、机床传动误差的来源 621
二、机床传动误差形式 622
三、角度传动误差 622
四、线性传动误差 622
第三节 传动链传动误差的测量与处理 622
一、测量方法简介 623
二、测量仪器的型式与特点 623
三、静态测量举例 623
四、动态测量举例 624
第四节 滚齿机传动误差的测量与处理 627
一、被测滚齿机简介 627
二、测量系统及工作过程 628
四、误差处理及分析 629
三、传动误差测量结果 629
五、误差频谱实用计算公式 630
六、传动误差频谱计算实例 630
七、误差频谱的处理 632
第五节 滚齿机传动精度分析与提高 632
一、展成链传动精度分析 632
二、差动链传动精度分析 634
三、滚齿机传动精度分析要点 634
四、滚齿机传动精度提高方法 635
第六节 插齿机传动精度分析与提高 636
一、精度分析 636
二、精度的提高 637
第七节 螺纹机床传动精度分析与提高 637
一、精度分析 637
二、精度分析举例 638
三、精度的提高 638
一、液压泵的修理 640
第三节 机床液压元件的修理和调整 640
第二节 液压油的污染和防污 640
第一节 概述 640
第五章 机床液压系统修理及机床治漏 640
二、液压马达的修理、检测 655
三、液压缸的修理 658
四、方向、压力、流量控制阀的修理 668
五、液压辅助元件的选择和维护 683
第四节 机床液压系统清洗、安装、调试和维护 686
一、机床液压系统的清洗 686
二、机床液压系统的安装 687
三、机床液压系统的调试 688
四、机床液压系统的维护 689
第五节 机床液压系统常见故障分析及排除方法 690
一、液压系统建立不起压力或压力提不高 690
二、循环动作不能正常实现 691
三、执行元件的工作速度在负载下有显著变化 691
四、换向精度差 692
六、换向出现死点 693
五、换向冲出量大 693
七、换向启动慢 694
八、执行元件起动时突然前冲 695
九、执行元件换向停留时间不稳定 695
十、工作台往复运动速度不一致 696
十一、尾架顶尖动作失灵 697
十二、进给系统不稳定 697
十三、系统泄漏 698
十四、温升过高 699
十五、系统产生振动和噪音 700
十六、执行元件爬行 703
十七、液压冲击现象 705
十八、静压导轨系统故障及排除 707
十九、静压轴承系统故障及排除 711
二十、静压丝杆系统故障及排除 716
第六节 典型机床液压系统常见故障及排除方法 717
一、组合机床液压系统 717
二、车床仿形刀架液压系统 722
三、B690牛头刨床液压系统 723
四、磨床液压系统 726
第七节 机床漏油的治理 731
一、机床漏油的原因 731
二、机床设备治漏的几种方法 731
三、多种切削机床漏油治理举例 733
第六章 软带在修理机床导轨上的应用 756
第一节 概述 756
一、软带对金属滑动导轨的特点 756
二、软带的特性 756
第二节 软带的粘接 758
一、胶粘剂 758
二、粘接工艺 760
三、粘接实例 763
四、应用效果 765
第三节 应注意的问题 766
第一节 普通车床修理精度检验(几何精度) 768
第七章 普通车床修理 768
第二节 卧式车床常见故障分析及排除 777
一、普通车床常见故障分析与排除 777
二、6140型精密车床故障分析与排除 781
第三节 普通车床修理工艺 783
一、机床的拆卸与修理顺序 783
二、普通车床关键零部件的修理工艺 783
三、总装配 821
一、机床空运转试验 830
第四节 试车验收 830
二、机床负荷试验规范 832
第八章 立式车床的修理 834
第一节 立式车床修理标准 834
第二节 立式车床的故障分析与排除 843
一、工作台跳动超差 843
二、加工件圆度超差 843
三、车削平面不平 843
九、横梁升降阻力大 844
八、上下进刀箱的传动光杆在工作中发热 844
十、车工件时跳刀 844
十一、刀架导轨研伤 844
六、工作锥度超差 844
七、重切削时,工作台和床身结合面松动 844
五、刀架移动过程中走曲线 844
四、五角刀台多工位加工时中心不重合 844
十二、传动件噪声过大 845
十三、滑动件在移动中产生爬行 845
十四、车出工件表面粗糙度不够 845
十五、部件中漏油 845
十六、刀架手轮缓量大 845
十七、工作台使用高转速时润滑油压力下降较大 845
第三节 立车关键部件的修理 845
一、主要部件修理顺序 845
二、关键部件修理工艺 845
三、调整方法 852
第四节 立车修理后的试车、验收 854
一、空运转试验 854
三、工作精度试验及几何精度复查 855
二、负荷试验规范 855
第九章 铣床的修理 858
第一节 铣床的修理精度检验 858
一、升降台铣床修理精度检验 858
二、万能工具铣床修理精度检验 868
三、龙门铣床修理精度检验 885
第二节 铣床的故障分析与排除 898
一、升降台式铣床的故障分析及排除 898
二、万能工具铣床的故障分析及排除 908
三、龙门铣床的故障分析及排除 913
第三节 升降台铣床主要部件的修理 917
一、修前的准备工作 917
二、所需的工具及仪器 917
三、机床的传动系统及主要技术参数 917
四、主要部件的拆卸及修理顺序 923
五、主要部件的修理工艺 923
一、机床空运转试验 951
第四节 升降台铣床修理精度的验收 951
三、机床的工作精度的检验 952
四、机床的几何精度的检验 952
二、机床的负荷试验 952
第十章 万能外圆磨床的修理 953
第一节 机床的修理精度 953
第二节 机床的常见故障的分析与排除 964
一、机床启动时工作台断续运动 964
二、机床工作时噪音过大 964
三、工作台的往返行程过度误差大,在慢速时更为显著 964
四、工件表面有螺旋线 964
五、工件表面有鱼鳞皮纹 965
六、工件表面有突然拉毛的痕迹 965
七、工件表面有细微的拉毛痕迹 965
十、工件圆度超差 966
十一、磨削内孔时,工件表面有螺旋线 966
八、工件表面有直波形(多角形) 966
九、工件表面形状超差,出现鼓形和鞍形误差 966
十五、砂轮主轴发生抱轴现象 967
十七、工作台换向时冲击太大 967
十六、工作台换向迟缓 967
十八、滑鞍快速移动时冲击过大 967
十四、磨削内孔时,工件圆度超差 967
十三、磨削内孔时,工件表面有鱼鳞波纹 967
十二、磨削内孔时,工件表面有多角形 967
第三节 机床修理工艺 968
一、修前工作 968
二、床身导轨的修理 968
三、下工作台的修理 973
四、上工作台的修理 974
五、头架的修理 976
六、尾架的修理 980
七、砂轮架的修理 981
八、内圆磨具的修理 984
一、机床的空运转试验 986
第四节 机床修理后的验收 986
二、空运转后的检测 987
三、机床工作精度的检测 988
四、机床几何精度的检查 988
第十一章 龙门刨床的修理 989
第一节 机床的修理精度 989
四、横梁分别在上下位置时平行度超差 999
三、精加工工件表面粗糙度差 999
二、工作台运动不稳定 999
一、床身导轨局部磨损较严重,有咬毛、拉沟损伤 999
第二节 机床常见故障的分析与排除 999
五、在床身的接缝处有较严重的漏油现象 1000
第三节 机床的修理工艺 1000
一、修养工作 1000
二、床身的修理 1001
三、立柱的修理 1007
四、立柱的安装 1007
五、联接梁和龙门顶的安装 1008
六、工作台的修理 1009
七、横梁的修理 1012
八、刀架的修理 1016
九、侧刀架部件的组装 1022
十、横梁部件的组装 1023
第四节 机床修理后的验收 1023
一、机床空运转试验 1023
二、负荷试验 1024
四、机床几何精度的检查 1025
三、工作精度试验 1025
第十二章 摇臂钻床的修理 1026
第一节 摇臂钻床的修理标准 1026
一、修理精度检验 1026
二、刚度检验标准 1028
第二节 摇臂钻床的故障分析与排除 1029
一、摩擦离合器失灵 1029
二、加工孔圆度超差或孔经变大 1029
六、摇臂升降时有冲击或啸叫现象 1030
五、主轴套筒上下移动松紧不匀 1030
三、主轴箱移动时轻重不均匀 1030
四、加工工件孔的轴线倾斜 1030
十、立柱钻孔定位不准,锁紧时中心产生位移 1031
第三节 摇臂钻床关键零部件的修理 1031
十一、有油液渗漏现象 1031
一、主要部件修理顺序 1031
九、自动进给手柄椎入后拉不出 1031
八、摇臂转动时太重 1031
七、立柱液压夹紧机构失灵 1031
二、关键部件修理工艺及调整 1032
第四节 摇臂钻床修理后的试车、验收 1037
一、空运转试验 1037
二、负荷试验规范及精度复查 1037
第十三章 滚齿机的修理 1039
第一节 检验机修精度的准则依据 1039
一、几何精度检验 1039
二、传动链精度检验 1050
三、工作精度检验 1053
第二节 滚齿机常见故障分析及排除 1055
一、加工误差来源 1055
二、滚齿机常见故障及排除方法 1055
第三节 修前准备及拆修顺序 1061
一、修前准备 1061
二、大修拆卸顺序 1061
三、主要部件修理顺序 1061
第四节 重点部件的修理 1062
一、床身导轨的修理 1063
二、立柱导轨的修理 1064
三、外支架修理简介 1066
四、刀架垂直进给丝杠的修理 1068
五、主变速箱的修理 1070
第五节 工作台部件的修理 1070
一、常见故障 1070
二、修理方法与基准的选择 1071
三、工作台与底座的修理 1072
四、分度蜗轮的修理 1074
五、分度蜗杆的修理 1086
七、分度蜗轮副啮合侧隙的调整 1088
六、蜗杆机架的修理 1088
第六节 重型滚齿机分度蜗轮副的修理与调整 1091
一、常见故障及分析 1091
二、修理方法选择 1091
三、分度蜗杆的研磨修复法 1091
四、分离蜗轮的刮研修复法 1092
五、双蜗杆分离副的调整 1093
一、刀架滑板的修理 1094
第七节 刀架滑板和刀架部件的修理 1094
二、刀架部件的修理 1095
第八节 总装配 1099
一、总装配要求 1099
二、总装配步骤 1099
第九节 试车验收 1100
一、准备工作 1100
六、几何精度检验 1101
五、传动链精度检验 1101
七、滚齿机精度性故障分析 1101
三、机床负荷试验 1101
四、工作精度试验 1101
二、空运转试验 1101
第十四章 插齿机的修理 1104
第一节 检验修理精度的准则依据 1104
一、几何精度检验 1104
二、传动链精度检验 1109
三、工作精度检验 1110
第二节 故障分析与排除 1110
一、插齿与滚齿的加工误差分析特点 1110
二、插齿机故障分析及排除 1111
第三节 修理顺序及主要零部件的修理 1113
一、修前准备 1113
二、修理顺序 1114
三、工作台部件的修理 1114
四、刀架部件的修理 1119
四、工作精度试验 1125
三、负荷试验 1125
五、几何精度检验 1125
第四节 修后试车验收 1125
二、空运转试验 1125
一、空运转试验前准备工作 1125
第四篇 锻压设备篇 1126
第一章 空气锤的修理 1126
第一节 空气锤的主要技术参数和精度标准 1126
一、空气锤的主要技术参数 1126
二、空气锤的精度检测标准 1126
第二节 空气锤的故障分析 1130
一、锤身的损坏 1130
二、锤杆活塞的损坏 1130
三、导程的损坏 1131
四、压缩活塞的损坏 1131
三、其它部分的拆卸 1132
二、压缩缸部分的拆卸 1132
一、工作缸部分的拆卸 1132
第三节 空气锤的拆卸 1132
九、基础的损坏 1132
七、曲轴的损坏 1132
六、气阀的损坏 1132
五、活塞环的损坏 1132
八、砧座的损坏 1132
第四节 空气锤零部件的修理 1133
一、锤身的修理 1133
二、锤杆活塞的修理 1134
五、活塞环的修理 1135
六、曲轴的修理 1135
四、导程的修理 1135
三、压缩活塞的修理 1135
七、气阀的修理 1136
八、砧座的修理 1137
九、基础的修理 1138
第五节 空气锤修理后的装配、调试与验收 1138
一、装配与调试 1138
一、锻锤胶带砧垫的应用 1139
第六节 空气锤修理中的技术改造 1139
二、修理后的试验与验收 1139
二、空气锤工作缸滑合副的改造 1146
三、锤杆导程滑合副的改造 1146
四、空气锤氟塑料活塞环改装设计 1147
五、4KN空气锤传动部分的改造 1149
六、双作用空气锤止回阀的改造 1149
八、定期改变曲轴的旋转方向 1150
第七节 空气锤的常见故障及其排除措施 1150
七、上、下操纵旋阀的改造 1150
第二章 蒸汽-空气自由锻锤的修理 1153
第一节 蒸汽-空气自由锻锤的主要技术参数和精度检测标准 1153
一、主要技术参数 1153
二、蒸汽-空气自由锻锤的精度标准 1154
第二节 蒸汽-空气自由锻锤的安装与拆卸 1155
一、安装程序 1155
二、汽缸体和下法兰的结构改造 1156
一、蒸汽-空气自由锻锤砧下直接隔振 1156
第三节 蒸汽-空气自由锻锤修理中的技术改造 1156
二、拆卸 1156
三、润滑系统的改造 1157
四、延长盘根使用寿命的方法 1157
第四节 蒸汽-空气自由锻锤的常见故障及排除措施 1157
第三章 蒸汽-空气模锻锤的修理 1160
第一节 模锻锤的型式与基本参数 1160
第二节 模锻锤的精度检测标准 1161
第三节 蒸汽-空气模锻锤的安装 1162
一、砧座的安装 1162
二、部件的安装与调整 1163
三、各活动部位常温状态下间隙的确定 1164
四、模锻锤使用不同工作介质时的调节 1165
第四节 蒸汽-空气模锻锤修理专用工具 1165
一、平模 1165
六、活动钩 1166
五、撞锤 1166
四、锤头支管 1166
三、杠杆拉具 1166
二、冲头 1166
七、凸台圆盘 1167
八、带柄方钢 1167
九、落锤 1167
第五节 蒸汽-空气模锻锤主要零部件的拆装 1168
一、退锤杆 1168
二、锤头的拆卸与安装 1171
一、砧座的修理 1173
第六节 蒸汽-空气模锻锤的修理 1173
三、盘根铜套的拆卸与安装 1173
二、立柱的修理 1175
三、导轨的修理 1176
四、锤头的修理 1176
五、模座的修理 1177
六、气缸垫板的修理 1178
七、气缸的修理 1178
八、操纵机构的修理 1178
三、活塞的改进 1179
二、活塞环的改进 1179
第七节 蒸汽-空气模锻锤修理中的技术改造 1179
一、活塞与锤杆的改进 1179
四、导轨的改进 1181
五、盘根的改进 1182
六、模座的改进 1183
七、气缸套装配尺寸的改进 1183
第八节 蒸汽-空气模锻锤的常见故障及其排除方法 1183
第四章 摩擦压力机的修理 1187
第一节 双盘摩擦压力机的主要技术参数、技术要求和精度检测标准 1187
一、双盘摩擦压力机的主要技术参数 1187
二、双盘摩擦压力机的技术要求 1187
三、双盘摩擦压力机的精度及其检查标准 1190
四、双盘摩擦压力机的力能试验 1192
第二节 双盘摩擦压力机的故障分析 1192
一、机身的损坏 1192
二、滑块的损坏 1193
八、摩擦盘的损坏 1194
九、基础的损坏 1194
七、飞轮的损坏 1194
十、导向套的损坏 1194
三、铜螺母的损坏 1194
六、横轴的损坏 1194
五、工作台垫板的损坏 1194
四、主螺杆的损坏 1194
第三节 双盘摩擦压力机的拆卸 1195
一、操纵部分的拆卸 1195
二、横轴的拆卸 1195
二、横轴的拆卸 1195
三、滑块的拆卸 1195
四、机身的拆卸 1195
第四节 双盘摩擦压力机零部件的修理 1196
一、机身部分的修理 1196
二、主传动系统的修理 1198
三、工作部分的修理 1198
四、操纵系统的修理 1201
五、制动装置的修理 1202
六、顶出装置的修理 1203
第五节 双盘摩擦压力机修理后的调试与检测 1204
一、双盘摩擦压力机修理后的调试 1204
二、双盘摩擦压力机修理后的检测 1205
第六节 双盘摩擦压力机的常见故障及其排除措施 1205
一、滑块打击无力 1205
二、打击后滑块不能回升 1205
三、横轴两端轴承温升过高 1206
四、机身或滑块导轨拉伤 1206
五、导轨温升过高 1206
六、滑块撞横梁或飞轮撞横轴 1206
七、操纵不灵敏气压油压下降过快 1206
八、机械顶出装置顶不出锻件 1206
九、气动或液压顶出装置顶不出锻件 1207
十、螺杆或螺母表面拉伤磨损严重 1207
四、开式压力机的精度标准 1208
五、闭式单点压力要的精度标准 1208
三、闭式双点压力机的基本参数 1208
六、闭式双点压力机的精度标准 1208
第一节 通用压力机的基本参数和精度标准 1208
二、闭式单点压力机的基本参数 1208
一、开式压力机的基本参数 1208
第五章 通用压力机的修理 1208
第二节 主传动系统的修理 1215
一、主传动系统的故障及消除方法 1216
二、主传动系统的修理 1217
第三节 离合器与制动器的修理 1223
一、转键离合器的修理 1223
二、单盘嵌块式摩擦离合器的修理 1224
三、多盘摩擦离合器的修理 1228
第四节 曲柄滑块机构的修理 1235
一、曲柄滑块机构的常见故障及其排除方法 1235
二、曲柄滑块机构的修理 1235
第五节 拉深垫的修理 1242
一、拉深垫的常见故障及其排除方法 1244
二、拉深垫的修理 1245
一、开式机身的修理 1246
第六节 机身的修理 1246
二、组合式机身的修理 1247
第七节 润滑系统的维修 1250
第八节 气路系统的维修 1252
第九节 多点压力机滑块运动精度的调整 1253
一、影响滑块运动精度的因素 1253
二、滑块运动精度分析举例 1257
三、滑块运动精度的调整 1259
第一节 平锻机修理的技术标准 1261
第六章 平锻机的修理 1261
第二节 平锻机的拆卸 1262
第三节 平锻机的修理 1262
一、机身部件的修理 1262
二、主滑块部件的修理 1264
三、夹紧机构的修理 1265
四、离合器的修理 1266
五、曲轴部件的修理 1267
二、前滚轮结构改进 1268
第四节 平锻机修理中的技术改造 1268
一、主滑块槽部结构的改进 1268
三、夹紧机构大立轴装配结构改进 1269
第五节 平锻机的装配、调整和试车 1270
一、平锻机的装配 1270
二、平锻机的调整和试车 1270
第六节 平锻机的故障分析及其排除 1270
一、水平分模平锻机的故障分析与排除 1270
二、垂直分模平锻机的故障分析与排除 1272
第七章 剪切机的修理 1275
第一节 剪切机的基本参数和精度标准 1275
一、剪板机的型式与基本参数 1275
二、剪板机的精度标准 1277
三、剪板刀纵放联合冲剪机的型式及其本参数 1279
四、联合冲剪机的精度标准 1280
第二节 板料剪切机的修理 1284
一、闸式剪板机的修理 1284
二、摆式剪板机的修理 1288
三、圆盘剪板机的修理 1290
第三节 联合冲剪机的修理 1292
一、主要检修内容 1292
二、联合冲剪机的调整 1294
第四节 剪切机大修后的验收 1295
一、装配质量 1295
二、检验与试车 1296
第八章 液压机的修理 1298
第一节 液压机主要技术参数、精度检测标准及其型号 1298
一、液压机主要技术参数 1298
二、液压机精度与检测标准 1303
三、液压机型号 1315
第二节 液压机工作原理 1316
一、泵直接传动型式 1317
二、泵一蓄势器传动型式 1318
一、上横梁零部件的修理 1319
第三节 四柱液压机本体的修理 1319
二、工作缸的修理 1320
三、柱塞或活塞杆的修理 1321
四、回程缸的修理 1323
五、活动横梁的修理 1325
六、立柱的修理 1326
七、下横梁的修理 1330
第四节 四柱液压机本体大修理 1332
一、拆卸方法与要求 1332
二、液压机吊装方法与要求 1335
第五节 其他结构液压机本体修理 1339
第六节 液压机液压系统的修理 1342
一、液压机液压系统的类型 1342
二、泵一蓄势器联合传动液压系统修理 1347
三、泵直接传动液压系统的修理 1355
附录一 锻压设备完好标准 1362
附录二 锻压设备操作维护规程 1363
附录三 锻压设备大修理通用技术条件 1366
附录四 锻压机械通用技术条件(JB1829-86) 1371
附录五 锻压机械安全技术条件(JB4203-86) 1378
附录六 锻压机械精度检验通则(GB10923-89) 1383
第五篇 铸造机械修理 1400
第一章 造型设备的维修 1400
第一节 中低压造型机 1400
一、工作原理和结构特点 1400
二、修理工艺 1402
三、常见故障及排除方法 1406
一、工作原理和结构特点 1407
二、修理工艺 1407
四、试车与验收 1407
第二节 高压造型机 1407
三、常见故障及排除方法 1410
四、试车验收 1410
第三节 造型线的修理 1411
一、结构及工作原理 1411
二、修理工艺 1413
三、辅机常见故障及排除方法 1414
四、试车验收 1415
第四节 造型机易损零部件的修理 1415
一、易损件的检验 1415
二、易损零件的修理工艺和方法 1415
第二章 制芯设备的修理 1419
第一节 热芯盒射芯机 1419
一、结构及工作原理 1419
二、易损零部件的修理 1419
三、常见故障及排除方法 1421
四、修后验收 1421
第二节 壳芯机 1422
一、结构及工作原理 1422
二、修理工艺 1422
三、常见故障及排除方法 1423
四、试车与验收 1423
二、常见故障及排除方法 1425
一、工作原理和结构特点 1425
第三章 砂处理主要设备 1425
第一节 辗轮式混砂机 1425
三、故障分析与改进 1426
四、试车 1434
第二节 摆轮式混砂机 1434
一、工作原理和结构特点 1434
二、常见故障及处理措施 1434
三、部分零部件修理 1434
一、工作原理和结构 1436
二、常见故障及处理措施 1436
第三节 埋刮板输送机 1436
四、试车 1436
三、故障分析和部件改进 1438
四、试车验收 1439
第四节 带式输送机 1440
一、用途及结构 1440
二、常见故障及处理措施 1441
三、故障分析和部件改进 1441
一、工作原理和结构特点 1446
第五节 气力输送装置 1446
二、气动输送存在的主要问题解决措施 1447
第四章 特种铸造设备 1453
第一节 压铸机的修理 1453
一、工作原理和结构特点 1453
二、修理工艺 1454
三、压铸机常见故障及排除方法 1454
第二节 熔模铸造设备 1455
一、化蜡设备 1455
四、压铸机的维护 1455
二、碎蜡设备 1457
三、搅蜡设备 1458
四、压蜡设备 1458
第六篇 泵类机械修理 1463
第一章 泵的术语和性能规格 1463
第一节 叶片泵的术语及其概念 1463
一、性能参数术语及其概念 1463
二、泵的性能曲线 1464
一、单级单吸悬臂式离心泵 1465
第二节 常用叶片泵的性能规格 1465
三、水泵的比转数 1465
四、泵的汽蚀 1465
二、单级双吸式离心泵 1478
三、DA型多级分段式离心泵 1487
四、蜗壳式混流泵 1488
五、导叶式混流泵 1489
六、轴流泵 1491
第二章 泵的拆卸与装配 1497
第一节 悬臂式离心泵的拆卸与装配 1497
一、B型泵的拆卸 1497
二、B型泵的装配 1497
第二节 单级双吸式离心泵的拆卸与装配 1498
一、Sh型泵的拆卸 1498
第三节 单级多吸分段式离心泵的的拆卸与装配 1499
一、DA型泵的拆卸 1499
三、井上部分 1500
二、输水管及内设传动轴 1500
二、DA型泵的装配 1500
一、泵体部分 1500
第四节 深井泵的拆卸与装配 1500
第五节 轴流泵的拆卸与装配安装 1502
第六节 混流泵的拆卸与装配 1508
第七节 潜水泵的拆卸与装配 1509
第三章 泵的常规修理项目 1512
第一节 叶轮、密封环及叶片与泵壳间隙修理 1512
一、叶轮修理 1512
二、密封环和片泵与泵壳间隙标准 1512
三、密封环修理 1513
第二节 叶轮静平衡校正 1514
一、允许不平衡量 1514
二、静平衡校正方法 1515
第三节 泵轴的修理 1516
第四节 轴封装置修理 1519
第五节 泵壳修理 1520
第六节 泵轴承的修理 1521
第四章 泵零部件的录蚀、磨损和腐蚀修理 1527
第一节 非金属材料涂敷修理 1527
一、基本材料 1527
二、环氧树脂和环氧材料的组成 1529
三、环氧材料的几种配方及配制工艺 1530
四、修补涂敷工艺 1530
五、几点注意事项 1531
第二节 剥蚀磨蚀(损)和腐蚀伤痕的补焊修理 1531
一、焊条的选择 1531
二、补焊工艺 1532
第五章 离心、混流和轴流泵的故障和排除方法 1534
第一节 泵装置的基本类型 1534
第二节 离心泵及蜗壳式混流泵的故障和排除方法 1535
第三节 轴流泵及导叶式混流泵的故障和排除方法 1538
第四节 深井泵的故障及排除方法 1539
第五节 潜水泵故障和排除方法 1543
- 《大数据Hadoop 3.X分布式处理实战》吴章勇,杨强 2020
- 《高等教育双机械基础课程系列教材 高等学校教材 机械设计课程设计手册 第5版》吴宗泽,罗圣国,高志,李威 2018
- 《2020考研英语大趋势 历年真题完形+翻译+新题型精讲精练》商志 2019
- 《待我有罪时 大结局》丁墨 2019
- 《超强大·英语10000+常考单词+常用搭配,随身带随时用》朱晓琴 2019
- 《大数据环境下的信息管理方法技术与服务创新丛书 俄罗斯档案事业改革与发展研究》徐胡乡责编;肖秋会 2019
- 《大女孩》孟翔勇著 2000
- 《AutoCAD机械设计实例精解 2019中文版》北京兆迪科技有限公司编著 2019
- 《德国发展报告 2019 大变局时代的德国》郑春荣主编 2019
- 《高效记忆法 51个记忆秘诀速查速用大全集》许大鹏著 2020
- 《钒产业技术及应用》高峰,彭清静,华骏主编 2019
- 《现代水泥技术发展与应用论文集》天津水泥工业设计研究院有限公司编 2019
- 《异质性条件下技术创新最优市场结构研究 以中国高技术产业为例》千慧雄 2019
- 《Prometheus技术秘笈》百里燊 2019
- 《中央财政支持提升专业服务产业发展能力项目水利工程专业课程建设成果 设施农业工程技术》赵英编 2018
- 《药剂学实验操作技术》刘芳,高森主编 2019
- 《林下养蜂技术》罗文华,黄勇,刘佳霖主编 2017
- 《脱硝运行技术1000问》朱国宇编 2019
- 《催化剂制备过程技术》韩勇责任编辑;(中国)张继光 2019
- 《信息系统安全技术管理策略 信息安全经济学视角》赵柳榕著 2020