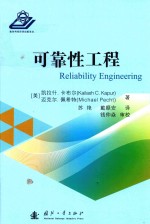
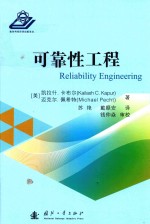
可靠性工程PDF电子书下载
- 电子书积分:15 积分如何计算积分?
- 作 者:凯拉什·卡布尔
- 出 版 社:北京:国防工业出版社
- 出版年份:2018
- ISBN:9787118116625
- 页数:459 页
第1章 21世纪的可靠性工程 1
1.1 质量 1
1.2 可靠性 3
1.2.1 执行预期功能的能力 3
1.2.2 指定的时间段 4
1.2.3 寿命周期条件 4
1.2.4 可靠性相关度量 5
1.3 质量和用户满意度/系统效能 5
1.4 性能、质量及可靠性 6
1.5 可靠性与系统寿命周期 8
1.6 故障后果 11
1.6.1 经济损失 12
1.6.2 违背公众信任 13
1.6.3 法律责任 14
1.6.4 无形损失 15
1.7 供应商与用户 15
1.8 小结 16
习题 16
参考文献 17
第2章 可靠性概念 19
2.1 可靠度 19
2.1.1 概率密度函数 23
2.2 风险率 25
2.2.1 风险率激励与发展 26
2.2.2 风险率函数的一些特性 27
2.2.3 条件可靠度 30
2.3 产品寿命百分数 31
2.4 失效时间 32
2.4.1 关于原点和均值的矩 32
2.4.2 预期寿命/平均失效前时间(MTTF) 33
2.4.3 方差/二阶矩 33
2.2.4 偏度系数 34
2.4.5 峰度系数 34
2.5 小结 36
习题 36
第3章 可靠性分析中的常用概率和寿命分布 40
3.1 离散分布 40
3.1.1 二项式分布 40
3.1.2 泊松分布 44
3.1.3 其他离散分布 44
3.2 连续分布 45
3.2.1 威布尔分布 48
3.2.2 指数分布 53
3.2.3 指数分布可靠性估算 56
3.2.4 正态(高斯)分布 59
3.2.5 对数正态分布 63
3.2.6 伽马分布 66
3.3 概率图 68
3.4 小结 73
习题 73
参考文献 75
第4章 六西格玛设计 76
4.1 什么是六西格玛 76
4.2 为什么采用六西格玛方法? 77
4.3 六西格玛如何施行 78
4.3.1 六西格玛过程的步骤 79
4.3.2 六西格玛步骤 83
4.4 六西格玛过程的优化问题 85
4.4.1 系统传递函数 85
4.4.2 方差传播方程 86
4.4.3 经济优化和质量改进 87
4.4.4 容差设计问题 88
4.5 六西格玛设计 88
4.5.1 (I)确定需求 90
4.5.2 (C)表征设计 91
4.5.3 (O)优化设计 91
4.5.4 (V)验证设计 92
4.6 小结 93
习题 93
参考文献 94
第5章 产品开发 96
5.1 产品需求和约束 96
5.2 产品寿命周期条件 97
5.3 可靠性能力 98
5.4 零部件和材料选择 99
5.5 人为因素与可靠性 100
5.6 演绎与归纳方法 101
5.7 失效模式、影响及危害性分析 102
5.8 故障树分析 103
5.8.1 FTA在决策中的作用 106
5.8.2 故障树分析步骤 106
5.8.3 构建故障树的基本样式 106
5.8.4 顶事件的定义 106
5.8.5 故障树的表征符号和运算规则 107
5.8.6 最小割集 111
5.9 失效物理 112
5.9.1 应力界限 112
5.9.2 失效机理的模型分析 113
5.9.3 降额设计 113
5.9.4 防护体系 113
5.9.5 冗余 114
5.9.6 预测 114
5.10 设计审查 115
5.11 鉴定 116
5.12 制造和装配 118
5.12.1 产品工艺性 118
5.12.2 工艺过程验证试验 119
5.13 产品失效及根本原因分析 120
5.14 小结 121
习题 121
参考文献 122
第6章 产品需求与约束 124
6.1 需求的定义 124
6.2 供应链的责任 125
6.2.1 多用户产品 125
6.2.2 单用户产品 126
6.2.3 定制产品 126
6.3 需求文档 127
6.4 规范 129
6.5 需求跟踪 129
6.6 结 130
习题 130
参考文献 130
第7章 寿命周期条件 131
7.1 定义寿命周期剖面 131
7.2 寿命周期事件 132
7.2.1 制造和装配 132
7.2.2 验收和测试 132
7.2.3 存储 133
7.2.4 运输 133
7.2.5 安装 133
7.2.6 操作 133
7.2.7 维修 133
7.3 应力及其影响 133
7.3.1 温度 136
7.3.2 湿度 136
7.3.3 振动与冲击 137
7.3.4 太阳辐射 138
7.3.5 电磁辐射 139
7.3.6 压强 139
7.3.7 化学物质 140
7.3.8 沙尘 140
7.3.9 电压 141
7.3.10 电流 141
7.3.11 人为因素 142
7.4 关于LCP开展的思考和建议 142
7.4.1 基于特殊极限的设计(全局环境和局部环境) 142
7.4.2 基于标准的文档资料 143
7.4.3 组合载荷条件 143
7.4.4 变化量值和变化率量值 146
7.5 估计寿命周期载荷的方法 146
7.5.1 市场调研和基于标准的剖面数据源 147
7.5.2 载荷条件的实地监测 147
7.5.3 现场测试记录、服务记录和失效记录 147
7.5.4 关于相似零件、装配体或产品的载荷历史的数据 147
7.6 小结 148
习题 148
参考文献 149
第8章 可靠性能力 150
8.1 能力成熟度模型 150
8.2 可靠性关键方法 150
8.2.1 可靠性要求和规划 151
8.2.2 培训和开发 152
8.2.3 可靠性分析 152
8.2.4 可靠性试验 153
8.2.5 供应链管理 153
8.2.6 失效数据跟踪分析 154
8.2.7 确认与验证 154
8.2.8 可靠性增长 155
8.3 结 155
习题 156
参考文献 156
第9章 零部件的选择与管理 158
9.1 零部件的评估过程 158
9.1.1 性能评估 159
9.1.2 质量评估 160
9.1.3 工序能力指数 160
9.1.4 平均检出质量 162
9.1.5 可靠性评估 163
9.1.6 装配评估 165
9.2 零部件管理 165
9.2.1 供应链管理 165
9.2.2 零部件变更管理 166
9.2.3 工业变更控制政策 168
9.3 风险管理 169
9.4 小结 170
习题 170
参考文献 171
第10章 失效模式、机理和影响分析 172
10.1 FMMEA的发展 172
10.2 失效模式、机理和影响分析方法 174
10.2.1 系统定义、单元和功能 174
10.2.2 潜在失效模式 175
10.2.3 潜在失效原因 175
10.2.4 潜在失效机理 176
10.2.5 失效模型 176
10.2.6 寿命周期剖面 176
10.2.7 失效机理优先级处理 177
10.2.8 文档 179
10.3 案例分析 180
10.4 结论 182
习题 183
参考文献 184
第11章 可靠性和安全性系数概率设计 186
11.1 可靠性设计 186
11.2 张力元件设计 186
11.3 可靠性模型的概率设计 188
11.4 概率设计以及可靠性指标设计示例 189
11.5 可靠性、安全系数和可变性之间的关系 190
11.6 函数随机变量 192
11.7 概率设计的步骤 195
11.8 小结 196
习题 196
参考文献 198
第12章 降额与升额 200
12.1 元器件额定值 200
12.1.1 绝对最大额定值 200
12.1.2 推荐工作条件 201
12.1.3 确定额定值的因素 201
12.2 降额 202
12.2.1 如何进行降额 203
12.2.2 降额方法的局限 207
12.2.3 如何确定极限 214
12.3 升额 214
12.3.1 元器件的选择和管理过程 216
12.3.2 升额能力的评估 216
12.3.3 升额方法 217
12.3.4 持续的保证 219
12.4 小结 220
习题 220
参考文献 221
第13章 可靠性评估技术 224
13.1 产品寿命周期内试验 224
13.1.1 概念设计和原型产品 225
13.1.2 设计规范性能验证 225
13.1.3 设计成熟度验证 225
13.1.4 设计和制造过程验收 225
13.1.5 小批量预生产 225
13.1.6 大批量生产 225
13.1.7 现场数据反馈 226
13.2 可靠性评估 226
13.3 产品质量鉴定与试验 226
13.3.1 PoF限制条件输入方式 228
13.3.2 加速应力试验的规划和开展 231
13.3.3 样本性能测试 233
13.3.4 加速寿命试验 235
13.3.5 虚拟试验 236
13.3.6 虚拟鉴定 237
13.3.7 输出 238
13.4 案例研究:封装系统坠落试验鉴定 238
13.4.1 步骤一:加速试验规划和开展 240
13.4.2 步骤二:样本性能测试 241
13.4.3 步骤三:加速寿命试验 243
13.4.4 步骤四:虚拟试验 246
13.4.5 全局FEA 247
13.4.6 模态贡献应变分布 248
13.4.7 加速曲线 248
13.4.8 局部FEA 249
13.4.9 步骤五:虚拟鉴定 250
13.4.10 PoF加速曲线 251
13.4.11 鉴定方法总结 251
13.5 统计基本概念 252
13.5.1 置信区间 252
13.5.2 置信水平的含义 253
13.5.3 置信区间与样本大小之间的关系 254
13.6 正态分布的置信区间 254
13.6.1 方差已知均值未知的正态分布 254
13.6.2 方差和均值均未知的正态分布 255
13.6.3 已知方差下的两总体均值之差 256
13.7 置信区间的比例 257
13.8 成功—失效测试的可靠性估计和置信区间 258
13.8.1 成功测试 260
13.9 指数分布的可靠性估计和置信区间 261
13.10 小结 265
习题 265
参考文献 266
第14章 过程控制与过程能力 267
14.1 过程控制系统 267
14.1.1 控制图:识别变异来源 268
14.1.2 变异来源 269
14.1.3 使用控制图进行问题识别 269
14.2 控制图 271
14.2.1 变量控制图 277
14.2.2 X图和R图 277
14.2.3 MR图案例 281
14.2.4 X图和S图 284
14.2.5 属性控制图 285
14.2.6 p图与np图 285
14.2.7 np图案例 285
14.2.8 c图和u图 287
14.2.9 c图案例 287
14.3 控制图优点 288
14.4 平均出厂质量 289
14.4.1 过程能力研究 290
14.5 高级控制图 295
14.5.1 CUSUM控制图 295
14.5.2 EWMA控制图 296
14.5.3 其他高级控制图 296
14.6 小结 297
习题 298
参考文献 303
第15章 产品筛选与老炼策略 305
15.1 老炼数据分析 306
15.2 老炼数据讨论 307
15.3 无筛选具有更高的现场可靠性 308
15.4 推荐方法 309
15.5 小结 310
习题 310
参考文献 311
第16章 分析产品失效机理和根因 312
16.1 根因分析过程 313
16.1.1 预先计划 314
16.1.2 为分析和评价直接原因收集数据 315
16.1.3 根因假设 316
16.1.4 证据的分析和说明 320
16.1.5 根因的识别和纠正措施 321
16.1.6 纠正措施评估 322
16.2 无故障发现 323
16.2.1 一种NFF评估方法 325
16.2.2 共模失效 328
16.2.3 共模失效的概念 329
16.2.4 建模和分析的相关可靠性分析 332
16.2.5 共模失效的根本原因 333
16.2.6 共模失效分析 335
16.2.7 共模失效的发生及减少影响 337
16.3 小结 344
习题 344
第17章 系统可靠性建模 347
17.1 可靠性框图 347
17.2 串联系统 348
17.3 有冗余的产品 352
17.3.1 工作冗余 352
17.3.2 旁联系统 356
17.3.3 切换并不理想的旁联系统 357
17.3.4 共享载荷的并联模型 359
17.3.5 (k,n)系统 361
17.3.6 冗余配置的局限 362
17.4 复杂系统的可靠性 363
17.4.1 完全列举法 363
17.4.2 条件概率法 365
17.4.3 关联结构的概念 366
17.5 小结 370
习题 370
参考文献 374
第18章 健康监测和预测 375
18.1 故障预测的概念模型 375
18.2 可靠性和故障预测 378
18.3 电子产品PHM 380
18.4 PHM的概念和方法 383
18.4.1 保险和预警装置 384
18.5 故障预兆的监测和推理 386
18.5.1 环境监测和损伤模型使用条件 390
18.6 子系统PHM的实施 395
18.7 小结 397
习题 397
参考文献 397
第19章 以可靠性为中心的维修分析 402
19.1 概述 402
19.2 基本理论 403
19.2.1 RCM的定义与作用 403
19.2.2 RCM维修思想 404
19.3 以可靠性为中心的维修分析 407
19.3.1 基本原理 407
19.3.2 RCMA实施流程 408
19.3.3 RCMA分析方法 410
19.3.4 RCMA要点 414
19.4 RCMA应用 415
19.4.1 重要功能部件确定 415
19.4.2 故障模式及影响分析 416
19.4.3 重要功能部件RCMA逻辑决断 417
习题 418
参考文献 418
第20章 保修分析 419
20.1 产品保修 419
20.2 保修返回信息 421
20.3 保修策略 422
20.4 保修性和可靠性 422
20.5 保修成本分析 425
20.5.1 保修成本模型因素 425
20.5.2 失效分布 426
20.5.3 成本建模计算 426
20.5.4 建模假设和记录 427
20.5.5 成本模型案例 427
20.5.6 信息需求 429
20.5.7 其他成本模型 431
20.6 保修与可靠性管理 432
20.7 小结 433
习题 434
参考文献 434
附录A:重要积分公式 437
附录B:高斯函数表 438
附录C:累积的标准正态分布表 440
附录D:t分布的百分点tα,v的值 443
附录E:卡方分布的百分点X2α,v 447
附录F:F分布的百分点 454
- 《市政工程基础》杨岚编著 2009
- 《工程静力学》王科盛主编 2019
- 《中央财政支持提升专业服务产业发展能力项目水利工程专业课程建设成果 设施农业工程技术》赵英编 2018
- 《化学反应工程》许志美主编 2019
- 《绿色过程工程与清洁生产技术 张懿院士论文集精选 上》《绿色过程工程与清洁生产技术》编写组编 2019
- 《软件工程》齐治昌,谭庆平,宁洪编著 2019
- 《化学工程与工艺专业实验指导》郭跃萍主编 2019
- 《天水师范学院60周年校庆文库 新工科视域下的工程基础与应用研究》《天水师范学院60周年校庆文库》编委会编 2019
- 《高等工程教育改革探析》李瀛心,吴价宝著 1997
- 《城市基坑工程设计施工实践与应用》李欢秋,刘飞,郭进军编著 2019
- 《弗利克家族》(德)托马斯·拉姆什著 2018
- 《昆虫记 图文典藏本》(法)法布尔著 2017
- 《大师和玛格丽特》(苏联)米哈伊尔·布尔加科夫 2019
- 《文艺复兴时期的战争艺术》(英)史蒂芬·特恩布尔(StephenTurnbull) 2019
- 《武士传奇》(英)斯蒂芬·特恩布尔(StephenTumbull)著 2019
- 《人体解剖图谱 汉英法拉对照》(法)J.M.布尔热里,N.H.雅各布著;徐坤译 2018
- 《伊斯坦布尔,伊斯坦布尔!》(土耳其)布尔汉·索恩梅兹 2019
- 《写给系统管理员的PYTHON脚本编程指南》(印度)甘尼什·桑吉夫·奈克著 2020
- 《自己动手做推荐引擎》(印)苏雷什·库马尔·戈拉卡拉(Suresh Kumar Gorakala)著 2020
- 《生成对抗网络项目实战=GENERATIVE ADVERSARIAL NETWORKS PROJECTS》(印)凯拉什·阿伊瓦著 2020
- 《指向核心素养 北京十一学校名师教学设计 英语 七年级 上 配人教版》周志英总主编 2019
- 《北京生态环境保护》《北京环境保护丛书》编委会编著 2018
- 《指向核心素养 北京十一学校名师教学设计 英语 九年级 上 配人教版》周志英总主编 2019
- 《抗战三部曲 国防诗歌集》蒲风著 1937
- 《高等院校旅游专业系列教材 旅游企业岗位培训系列教材 新编北京导游英语》杨昆,鄢莉,谭明华 2019
- 《中国十大出版家》王震,贺越明著 1991
- 《近代民营出版机构的英语函授教育 以“商务、中华、开明”函授学校为个案 1915年-1946年版》丁伟 2017
- 《新工业时代 世界级工业家张毓强和他的“新石头记”》秦朔 2019
- 《智能制造高技能人才培养规划丛书 ABB工业机器人虚拟仿真教程》(中国)工控帮教研组 2019
- 《陶瓷工业节能减排技术丛书 陶瓷工业节能减排与污染综合治理》罗民华著 2017