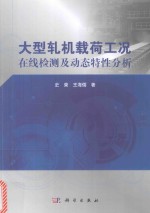
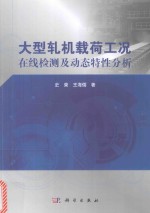
大型轧机载荷工况在线检测及动态特性分析PDF电子书下载
- 电子书积分:10 积分如何计算积分?
- 作 者:史荣,王海儒著
- 出 版 社:北京:科学出版社
- 出版年份:2015
- ISBN:9787030454539
- 页数:243 页
第1章 侧压调宽机动态特性在线检测与故障分析 1
1.1 SP侧压调宽机构简介 1
1.2 SP轧机动态特性试验方法 2
1.2.1 测点选择 2
1.2.2 传感器的选择与安装 3
1.2.3 测试软件的应用 4
1.3 SP轧机侧压机构运动学仿真 5
1.3.1 机构简化 5
1.3.2 侧压机构的数学模型 6
1.3.3 侧压模块运动规律仿真分析 7
1.4 SP轧机侧压模块运动状态试验结果分析 8
1.4.1 侧压模块的加速度与速度 8
1.4.2 侧压框架的加速度与速度 9
1.4.3 仿真结果的试验验证 10
1.4.4 两侧侧压机构的相位比较 11
1.4.5 侧压模块加速度信号频谱 12
1.5 SP轧机侧压过程的金属流动状态数值模拟及冲击力计算 13
1.5.1 侧压冲击力的有限元模拟 13
1.5.2 模拟结果分析 15
1.5.3 基于试验的侧压过程冲击力计算 17
1.6 SP轧机侧压机构动力学仿真 19
1.6.1 侧压机构动力学模型的建立 19
1.6.2 侧压机构的刚弹耦合动力学分析 20
1.6.3 仿真结果分析 22
1.7 衬板的疲劳寿命分析 27
1.7.1 衬板受力状态试验研究 27
1.7.2 试验方法 28
1.7.3 试验结果分析 29
1.8 衬板疲劳极限测定 32
1.8.1 试验设备 32
1.8.2 衬板试件制备 32
1.8.3 试验结果分析 33
1.8.4 影响衬板寿命的主要因素 34
1.8.5 衬板结构的改进 37
第2章 1580 PC轧机轴向力在线检测及辊系交叉状态分析 38
2.1 PC轧机辊系交叉机构简介 38
2.2 自适应均载机构工作原理 40
2.2.1 均载机构的力学模型 40
2.2.2 均载机构的移动轨迹仿真 41
2.2.3 工作辊 PC轮与支承辊耳座的均载特征 42
2.3 PC轧机辊系交叉状态分析 42
2.3.1 工作辊与支承辊交叉状态解析 43
2.3.2 工作辊之间的交叉状态 45
2.3.3 计算实例 46
2.4 PC轧机的零调偏差 46
2.4.1 零调静偏差成因 47
2.4.2 轧制力静偏差的有限元模拟 49
2.4.3 辊系动偏差的产生 51
2.5 轧辊轴向力与轧制力动偏差 52
2.5.1 轧辊轴向力计算实例 52
2.5.2 轴向力对轧制力动偏差的影响 53
2.6 交叉头磨损与轧制力偏差 56
2.7 PC轧机轴向力在线检测 57
2.7.1 轧机基本参数 58
2.7.2 试验目的与试验内容 58
2.7.3 试验原理及试验方法 58
2.7.4 传感器设计 60
2.7.5 轴向力测试系统 63
2.7.6 测试系统的标定 63
2.7.7 相关参数的检测及设备维护 65
2.7.8 试验步骤 66
2.8 PC轧机零调过程相关参数实测结果分析 66
2.8.1 轧机的零调过程 66
2.8.2 零调过程实测信号的动态特性 68
2.8.3 动态零调过程的轴向力 69
2.8.4 零调过程的辊系交叉状态分析 71
2.9 轴向力与轧制力偏差试验结果分析 72
2.9.1 轧制过程被测信号动态特性 72
2.9.2 PC角与轧制力偏差实测结果分析 75
2.9.3 PC角与支承辊轴向力实测结果分析 77
2.9.4 工作辊轴向力实测结果分析 80
2.10 轧制力偏差影响因素的模拟试验 83
2.10.1 模拟试验轧机设计 83
2.10.2 试验目的与方法 84
2.10.3 轴承座侧隙对轧制力偏差的影响 86
2.10.4 辊系交叉状态对轧制力偏差的影响 87
2.10.5 交叉点移动对轧制力偏差的影响 91
2.11 零调偏差控制方法研究 91
2.11.1 传统零调工艺分析 91
2.11.2 辊系两侧刚度差及垂直方向尺寸差控制 92
2.11.3 交叉头间隙的自位补偿 92
2.11.4 自位补偿法的试验验证 96
2.12 PC轧机主传动系统的扭振分析 97
2.12.1 PC轧机扭矩实测 97
2.12.2 试验结果分析 99
2.12.3 扭矩放大系数 100
第3章 2050 CVC轧机载荷工况在线检测 102
3.1 轧机基本参数 102
3.2 测试系统组成 103
3.3 生产过程的轧制力跟踪 103
3.3.1 轧制力信号的采集 103
3.3.2 轧制力信号波形 104
3.3.3 轧制力实测结果统计分析 107
3.4 实测轧制力矩 109
3.4.1 扭矩检测原理及扭矩信号的传输 109
3.4.2 重载转子的扭矩标定 110
3.4.3 扭矩信号测点布置 112
3.4.4 扭矩信号实测波形 112
3.4.5 轧制力矩统计分析 115
3.4.6 扭矩放大倍数 119
3.5 实测轧制速度 120
3.6 F4轧机齿轮分配箱齿轮轴的轴向力 121
3.6.1 单斜齿齿轮轴基本参数 121
3.6.2 斜齿齿轮轴的轴向力 121
3.6.3 轴向力计算结果分析 122
3.7 主传动系统扭振分析 123
3.7.1 扭振力学模型 123
3.7.2 扭振数学模型的建立 124
3.7.3 F1轧机主传动系统固有频率与主振型 125
3.7.4 F4主传动系统固有频率与主振型 126
3.7.5 固有频率实测值 127
3.7.6 主传动系统动态响应 129
3.7.7 速度对轧机主传动系统力学特性的影响 131
3.7.8 基于试验结果的含间隙系统动力学特性 132
3.8 CVC轧机工作辊轴承载荷工况在线检测 133
3.8.1 轴承结构与测试内容 134
3.8.2 轴承径向压力分布试验设计 134
3.8.3 轴承轴向载荷测试方案 134
3.8.4 轴承座内温度测量 135
3.8.5 测试系统组成 135
3.8.6 试验结果分析 136
第4章 1780热连轧卷板生产线主要设备载荷工况在线检测与振动分析 139
4.1 R1轧机动态特性分析 140
4.1.1 主传动系统扭振分析 141
4.1.2 轧机垂直振动分析 144
4.1.3 垂扭耦合振动分析 148
4.1.4 轧机扭矩在线检测与分析 152
4.1.5 基于试验的R1主传动系统扭振分析 159
4.1.6 轧制力在线检测及分析 161
4.1.7 工作辊轴承座振动状态分析 164
4.2 F1精轧机载荷工况及动态特性 167
4.2.1 轧机结构与基本参数 167
4.2.2 实测扭矩幅值及放大倍数 168
4.2.3 主传动系统扭振分析 172
4.2.4 实测轧制力分析 175
4.2.5 支承辊轴承座振动分析 178
4.3 F7轧机力能参数检测 182
4.3.1 轧机结构与基本参数 182
4.3.2 轧制力矩及动态特性 183
4.3.3 扭矩放大倍数 185
4.3.4 轧制力分布 188
第5章 宽厚板轧机主传动系统力学特性分析及关键零部件应力计算 191
5.1 4300mm中厚板轧机主传动系统力学特性分析 192
5.1.1 轧机基本结构及基本参数 192
5.1.2 轧机扭矩在线检测 193
5.1.3 测点选择 196
5.1.4 扭矩信号的时域特征 196
5.1.5 扭矩实测结果分析 199
5.1.6 典型产品轧制过程的扭矩实测结果统计 201
5.1.7 主传动链实测扭矩比较 205
5.1.8 轧机主传动系统扭振分析 207
5.1.9 主传动系统关键部位应力检测 215
5.1.10 轧机主传动系统动态特性分析 221
5.1.11 传动系统主要零件应力分析 227
5.2 5m宽厚板轧机主传动系统扭振分析 229
5.2.1 轧机主传动系统简介 230
5.2.2 主传动系统扭振分析 230
5.2.3 扭矩放大倍数 234
5.2.4 主传动系统动态特性试验研究 235
5.2.5 试验结果分析 236
5.2.6 十字节叉头异常损坏分析 239
参考文献 242
- 《食品接触材料中成分迁移特性及实践》张双灵著 2018
- 《DNA小分子检测技术及其应用》刘云国,叶乃好编著 2016
- 《中国食品药品检验检测技术系列丛书 中国药品检验标准操作规范 2019版》中国食品药品检定研究院 2019
- 《岩体力学特性尺寸效应与工程实践》张春生等著 2019
- 《新型摆线针轮传动系统动力学特性的研究》单丽君,何卫东著 2019
- 《在用机动车排气污染物检测》赵乐晨主编 2018
- 《功能性纺织产品功能性评价及检测》党敏主编 2019
- 《应用化学综合实验 新能源电极材料的制备检测 软包装锂离子电池的组装》王红强主编 2019
- 《脆塑性岩石类材料破坏后区力学特性研究》史贵才编;朱珉责编 2019
- 《中等应变速率花岗岩的动态力学特性研究》夏祥著 2018
- 《哈里森内科学 第19版 双语版 上》(美)丹尼斯·L.卡斯帕(Dennis L. Kasper),(美)安东尼·S.福奇由(Anthony S.Fauci),(美)斯蒂芬·L.豪泽(Stephen L.Hauser)著;王海译 2019
- 《献给祖国的歌 经典合唱曲谱精选》王海灵主编 2019
- 《新时代商务英语综合教程 教师用书 1》王立非总主编;孔宪遂主编;丁芬,阮岳湘,张斐瑞副主编;王海萍,王莹,金红卫编著;(英)LAN WOOD,ANNE WILLIAMS原著作者 2019
- 《常春藤传记馆 探索中亚的史诗 张骞传》王海威 2018
- 《软件工程 软件开发成本度量规范释义》王海青主编 2019
- 《中国古典舞基训 女班》王海英 2019
- 《汽车传动系统检修》李新,冯丽敏,张金友主编;王海红,韩茂松,莫嘉林副主编;王龙参编 2018
- 《外科实习医师手册》张必翔主编;卫积书,王磊,王海波,韦伟等编者 2019
- 《开发幼儿语言运用能力的实践探索》王海澜主编 2018
- 《居里夫人 伟大的镭元素之母》王海娜编著 2012
- 《指向核心素养 北京十一学校名师教学设计 英语 七年级 上 配人教版》周志英总主编 2019
- 《《走近科学》精选丛书 中国UFO悬案调查》郭之文 2019
- 《北京生态环境保护》《北京环境保护丛书》编委会编著 2018
- 《中医骨伤科学》赵文海,张俐,温建民著 2017
- 《美国小学分级阅读 二级D 地球科学&物质科学》本书编委会 2016
- 《指向核心素养 北京十一学校名师教学设计 英语 九年级 上 配人教版》周志英总主编 2019
- 《强磁场下的基础科学问题》中国科学院编 2020
- 《小牛顿科学故事馆 进化论的故事》小牛顿科学教育公司编辑团队 2018
- 《小牛顿科学故事馆 医学的故事》小牛顿科学教育公司编辑团队 2018
- 《高等院校旅游专业系列教材 旅游企业岗位培训系列教材 新编北京导游英语》杨昆,鄢莉,谭明华 2019