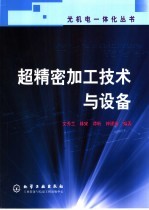
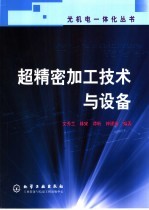
超精密加工技术与设备PDF电子书下载
- 电子书积分:12 积分如何计算积分?
- 作 者:文秀兰等编著
- 出 版 社:北京:化学工业出版社
- 出版年份:2006
- ISBN:7502584498
- 页数:341 页
1.1 超精密加工技术的内容 1
1.1.1 超精密加工的范畴 1
1.1.2 超精密加工方法 1
第1章 超精密加工技术概论 1
1.1.3 纳米加工技术 4
1.2 超精密加工技术的作用 5
1.2.1 超精密加工技术的重要性 5
1.2.2 超精密加工的需求 6
1.3 超精密加工的关键技术 9
1.3.1 超精密主轴 9
1.3.2 超精密导轨 9
1.3.3 传动系统 10
1.3.4 超精密刀具 11
1.3.5 精密测量技术 11
1.3.8 环境控制技术 12
1.3.6 微进给技术 12
1.3.7 加工原理 12
1.3.9 超精密数控技术 13
1.4 超精密加工技术的发展状况与趋势 13
1.4.1 超精密加工技术的发展状况 13
1.4.2 超精密加工机理研究前沿 16
1.4.3 超精密加工技术的发展特点与趋势 18
1.4.4 新形势下面临的任务 19
第2章 超精密机械加工方法 21
2.1 超精密切削加工 22
2.1.1 概述 22
2.1.2 超精密切削加工的机理 22
2.1.3 超精密切削加工的特点 27
2.1.4 保证超精密切削加工质量的措施与方法 28
2.1.5 硬脆光学晶体材料的超精密切削简介 30
2.2.1 超精密磨削机理 32
2.2 超精密磨削加工 32
2.2.2 超精密磨削的工艺特点 33
2.2.3 超硬材料微粉砂轮超精密磨削技术 34
2.2.4 超精密砂带磨削技术 38
2.2.5 硬脆材料的塑性域超精密磨削加工 40
2.3 超精密研磨与抛光 41
2.3.1 研磨加工的机理 42
2.3.2 抛光加工的机理 42
2.3.3 影响超精密研磨、抛光的主要工艺因素 43
2.3.4 化学机械抛光 43
2.3.5 利用新原理的超精密研磨抛光 47
3.1 超精密加工机床 51
3.1.1 概况 51
第3章 超精密加工机床与设备 51
3.1.2 超精密机床的分类 54
3.1.3 对超精密机床的基本要求 55
3.1.4 超精密机床的基础元部件及其关键技术 55
3.1.5 超精密加工机床实例 78
3.2 超精密加工刀具与刃磨技术 86
3.2.1 超精密切削对刀具的要求 86
3.2.2 金刚石的性能与结构特性 87
3.2.3 金刚石刀具的刃磨 88
3.2.4 超精密切削刀具材料的发展 92
3.3 超精密夹具设计 95
3.3.1 夹具定位的稳定性与可靠性 95
3.3.2 夹具对工件的定位精度 95
3.3.3 采取有效措施保证精密夹具的设计要求 96
3.3.4 超精密夹具设计应用实例 96
4.1.3 超精密特种加工技术的内容 99
4.1.2 超精密特种加工的适用范围 99
第4章 超精密特种加工技术 99
4.1 概述 99
4.1.1 超精密特种加工技术特点 99
4.2 激光加工 100
4.2.1 激光加工原理 100
4.2.2 激光加工的特点 100
4.2.3 激光加工设备的组成 101
4.2.4 激光微细加工技术与应用实例 101
4.3 电子束微细加工 110
4.3.1 电子束加工原理 110
4.3.2 电子束加工的特点与应用范围 110
4.3.3 电子束加工装置的组成 111
4.3.4 电子束微细加工应用技术 112
4.4.2 离子束微细加工的特点 116
4.4.3 离子束微细加工设备 116
4.4.1 离子束微细加工原理 116
4.4 离子束微细加工 116
4.4.4 离子束加工的应用 117
4.5 微细电火花加工 120
4.5.1 概述 120
4.5.2 微细电火花加工特点 121
4.5.3 微细电火花加工的工艺和设备技术 121
4.5.4 加工应用 125
4.6 超声波微细加工 126
4.6.1 超声加工原理 126
4.6.2 超声微细加工的特点 127
4.6.3 超声加工机床组成 127
4.6.4 超声微细复合加工 128
4.7 电化学加工 133
4.7.1 电解抛光 134
4.7.2 电化学机械复合加工 137
4.8 ELID镜面磨削技术 141
4.8.1 ELID磨削镜面形成机理 141
4.8.2 ELID磨削技术的工艺特点 141
4.8.3 ELID磨削装置的组成 142
4.8.4 ELID磨削技术的应用实例 143
4.9 微细磨料流动加工 144
4.9.1 磨料流加工的基本原理 144
4.9.2 磨料流加工的三大要素 144
4.9.3 磨料流加工的基本特性 146
4.9.4 磨料流加工的工艺特点 146
4.9.5 磨料流复合加工应用实例 146
4.10.1 磁力研磨加工 148
4.10 磁力研磨加工和磁力电解研磨加工 148
4.10.2 磁力电解研磨 151
4.11 磁流变抛光技术 152
4.11.1 磁流变抛光机理 153
4.11.2 磁流变液的组成及性质 153
4.11.3 磁流变抛光方法的特点与关键技术 154
4.11.4 磁流变抛光的应用 155
4.12 等离子体加工 155
4.12.1 等离子体 155
4.12.2 等离子弧加工 155
4.12.3 等离子体辅助抛光 157
4.13 基于微机器人的超精密加工技术 157
4.13.1 概述 157
4.13.2 微机器人超精密加工的类型及应用 158
5.1.1 精密测量技术 160
5.1 超精密加工精度检测 160
第5章 超精密加工的检测、误差补偿技术 160
5.1.2 典型几何量的测量与误差评定方法 166
51.3 超精密加工测量技术应用与实例 178
5.2 在线检测 187
5.2.1 概述 187
5.2.2 在线检测的基本原理 189
5.2.3 在线检测实例 190
5.3 误差补偿 191
5.3.1 误差补偿方法 191
5.3.2 误差补偿系统应用实例 192
5.4 检测设备与仪器 195
5.4.1 双频激光干涉仪 195
5.4.2 光栅检测系统 201
6.1.1 超精密加工对材料的基本要求 207
6.1.2 超精密加工材料的分类 207
第6章 超精密加工材料 207
6.1 概述 207
6.2 工件材料方面诸因素对切削加工性的影响 208
6.2.1 工件材料的物理、力学性能对切削加工性的影响 208
6.2.2 金属材料的化学成分对切削加工性的影响 209
6.2.3 热处理状态和金相组织对切削加工性的影响 210
6.3 超精密加工常用金属材料 211
6.3.1 钢 211
6.3.2 铸铁 214
6.3.3 有色金属 214
6.3.4 精密合金 216
6.4 常用非金属材料 217
6.4.1 陶瓷 217
6.4.3 复合材料 227
6.4.2 工程塑料 227
6.4.4 其他材料 231
第7章 超精密加工的环境控制 234
7.1 空气环境 234
7.1.1 空气中微粒的分布情况及对超精密加工的影响 234
7.1.2 空气的洁净度标准 235
7.1.3 净化空气的方法和措施 236
7.2 温度环境 242
7.2.1 温度对超精密加工的影响 242
7.2.2 恒温条件 242
7.2.3 环境温度的控制 242
7.3.2 湿度对超精密加工的影响 245
7.3.4 温湿度的控制方法与实例 245
7.3.3 湿度的范围与控制标准 245
7.3.1 湿度概念 245
7.3 湿度环境 245
7.4 振动环境 248
7.4.1 振动对超精密加工的影响 248
7.4.2 主要振源及防震措施 248
7.4.3 超精密机床防震实例 250
7.5 噪声环境 253
7.5.1 噪声及其危害 253
7.5.2 噪声源 253
7.5.3 控制噪声的基本途径 254
7.6 其他环境 257
7.6.1 静电环境 257
7.6.2 光环境 257
7.6.3 电磁波环境 257
7.7 超精密加工环境设施 257
8.1.1 光学非球面零件的性能特点 259
8.1 概述 259
第8章 光学非球面零件的超精密加工技术与设备 259
8.1.2 光学非球面零件的制作工艺 260
8.1.3 非球面的切除加工方法 260
8.2 非球面零件超精密加工技术 261
8.2.1 非球面零件超精密切削机床 262
8.2.2 非球面零件超精密磨削加工技术 262
8.2.3 光学非球面零件的ELID镜面磨削技术 263
8.2.4 非球面零件的超精密抛光(研磨)技术 264
8.2.5 非球面零件复制技术 265
8.2.6 非球面零件离子束加工 265
8.2.7 非球面磁流变研磨加工 265
8.3 光学非球面零件的检测技术 266
8.3.1 光学非球面零件的形状精度 266
8.3.2 非球面的非接触测试仪 266
8.4.1 计算机控制光学表面成形技术 268
8.4 大型非球面镜的研抛加工 268
8.4.2 应力盘抛光技术 270
8.4.3 离子束成形技术 272
8.5 超精密非球曲面加工机床实例 274
8.5.1 大型非球面加工机床的设计 274
8.5.2 超精密非球面加工机床Nanosystem300 276
8.6 超精密非球面加工技术的发展趋势 279
第9章 大直径硅片的超精密加工 281
9.1 概述 281
9.2 硅片的加工工艺 281
9.2.1 硅片的传统加工工艺 281
9.2.2 大直径硅片的现代加工工艺 283
9.3 大直径硅片的高效超精密磨削加工技术 284
9.3.1 旋转工作台式磨削 284
9.3.2 硅片自旋转磨削 285
9.3.3 微粉金刚石磨盘的研磨和磨抛工艺 287
9.4 硅片背面减薄加工技术 287
9.4.1 硅片背面减薄技术的分类 288
9.4.2 硅片背面磨削减薄技术 289
9.5 大尺寸硅片的超精密平坦化技术 291
9.5.1 保证硅片平坦化的方法——化学机械抛光 292
9.5.2 硅片平坦化技术的新进展 293
第10章 纳米加工技术 297
10.1 纳米加工技术概述 297
10.1.1 纳米加工技术的特点 298
10.1.2 纳米加工的方法及设备 298
10.1.3 发展纳米加工技术的途径 301
10.2 扫描隧道显微加工技术 302
10.2.1 扫描隧道显微技术的原理 302
10.2.2 STM在纳米加工中的应用 304
10.2.3 SPM在纳米加工中的应用 308
10.3 LIGA技术 310
10.3.1 LIGA技术 310
10.3.2 准LIGA技术进展 313
10.3.3 SLIGA技术 315
10.3.4 M2LIGA技术 316
10.3.5 抗蚀剂回流LIGA技术 316
10.4 纳米材料制造技术 317
10.4.1 纳米材料的分类与应用 318
10.4.2 纳米材料的制备方法及特点 320
10.5 纳米加工检测技术 332
10.5.1 纳米测量与定位控制技术 332
10.5.2 基于自然基准的纳米检测技术 334
10.5.3 纳米微粒粒径的检测方法 336
参考文献 338
- 《钒产业技术及应用》高峰,彭清静,华骏主编 2019
- 《现代水泥技术发展与应用论文集》天津水泥工业设计研究院有限公司编 2019
- 《激光加工实训技能指导理实一体化教程 下》王秀军,徐永红主编;刘波,刘克生副主编 2017
- 《异质性条件下技术创新最优市场结构研究 以中国高技术产业为例》千慧雄 2019
- 《Prometheus技术秘笈》百里燊 2019
- 《中央财政支持提升专业服务产业发展能力项目水利工程专业课程建设成果 设施农业工程技术》赵英编 2018
- 《药剂学实验操作技术》刘芳,高森主编 2019
- 《林下养蜂技术》罗文华,黄勇,刘佳霖主编 2017
- 《脱硝运行技术1000问》朱国宇编 2019
- 《催化剂制备过程技术》韩勇责任编辑;(中国)张继光 2019
- 《市政工程基础》杨岚编著 2009
- 《家畜百宝 猪、牛、羊、鸡的综合利用》山西省商业厅组织技术处编著 1959
- 《《道德经》200句》崇贤书院编著 2018
- 《高级英语阅读与听说教程》刘秀梅编著 2019
- 《计算机网络与通信基础》谢雨飞,田启川编著 2019
- 《看图自学吉他弹唱教程》陈飞编著 2019
- 《法语词汇认知联想记忆法》刘莲编著 2020
- 《培智学校义务教育实验教科书教师教学用书 生活适应 二年级 上》人民教育出版社,课程教材研究所,特殊教育课程教材研究中心编著 2019
- 《国家社科基金项目申报规范 技巧与案例 第3版 2020》文传浩,夏宇编著 2019
- 《流体力学》张扬军,彭杰,诸葛伟林编著 2019