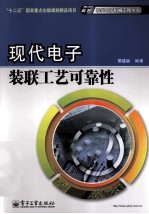
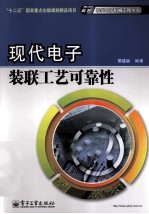
现代电子装联工艺可靠性PDF电子书下载
- 电子书积分:12 积分如何计算积分?
- 作 者:樊融融编著
- 出 版 社:北京:电子工业出版社
- 出版年份:2012
- ISBN:9787121161308
- 页数:310 页
第1章 现代电子装联工艺可靠性概论 1
1.1 电子设备可靠性的基本概念 1
1.1.1 电子设备可靠性问题的产生 1
1.1.2 电子设备可靠性的定义与数学描述 1
1.1.3 可靠性准则 5
1.1.4 可靠性的数量特征 5
1.2 现代电子装联工艺可靠性 10
1.2.1 电子装联工艺的变迁和发展 10
1.2.2 现代电子装联工艺可靠性问题的提出 11
1.2.3 现代电子装联工艺可靠性的研究对象和现实意义 14
第2章 影响现代电子装联工艺可靠性的因素 17
2.1 概述 17
2.1.1 现代电子装联工艺可靠性的内涵 17
2.1.2 现代电子装联焊接过程中的缺陷现象 17
2.1.3 应用中焊点可靠性的蜕变现象 20
2.2 电子元器件电极表面状态对互连焊接可靠性的影响 22
2.2.1 从可靠性看对电子元器件引脚材料的技术要求 22
2.2.2 电子元器件引脚用材料对焊接可靠性的影响 22
2.2.3 引脚的可焊性涂层对焊接可靠性的影响 24
2.3 PCB焊盘涂层对焊接可靠性的影响 28
2.3.1 PCB常用可焊性涂层的特性描述 28
2.3.2 目前国内外电子业界在PCB镀层的应用情况和评价 31
2.3.3 综合提升PCB镀层可焊性和抗环境侵蚀能力对改善工艺可靠性的现实意义 31
2.3.4 Im-Sn+重熔工艺在恶劣环境下改善抗腐蚀能力和可焊性的机理 32
2.4 镀层可焊性的储存期试验及试验方法 34
2.4.1 储存期对可焊性的影响 34
2.4.2 加速老化处理试验 35
第3章 焊接界面合金层的形成及其对焊点可靠性的影响 36
3.1 焊接界面 36
3.1.1 焊接界面的物理状态 36
3.1.2 界面合金层的形成 36
3.1.3 影响合金层生长的因素 41
3.2 IMC对焊点可靠性的影响 45
3.2.1 IMC对焊接连接的意义 45
3.2.2 IMC状态对焊点可靠性的影响 46
3.2.3 IMC厚度对焊点可靠性的影响 48
3.2.4 IMC微组织结构对焊点可靠性的影响 49
第4章 环境因素对电子装备可靠性的影响及工艺可靠性加固 52
4.1 在环境作用下电子产品性能的变化 52
4.1.1 湿度的影响 52
4.1.2 热和冷的影响 54
4.1.3 大气压力的影响 56
4.1.4 日光、灰尘和沙粒的影响 56
4.2 大气中腐蚀性元素和气体对电子装备可靠性的影响 56
4.2.1 大气中腐蚀性元素和气体的种类及其容许的浓度 56
4.2.2 大气腐蚀 57
4.2.3 在天然水介质中的腐蚀 58
4.2.4 接触腐蚀 58
4.2.5 离子迁移现象的机理及其对可靠性的危害 59
4.3 金属镀层的腐蚀(氧化)对可靠性的危害 59
4.3.1 金属腐蚀的定义 59
4.3.2 腐蚀介质的分类 59
4.3.3 引脚基体金属和镀层间的电化学腐蚀现象 61
4.3.4 非金属及金属的接触偶电极电位对可靠性的潜在影响 63
4.4 工艺可靠性加固措施 66
4.5 免清洗助焊剂在应用中的隐患 68
4.5.1 助焊剂残余物的潜在危险性 68
4.5.2 助焊剂残余物的分类及其对可靠性影响的预防 69
第5章 影响电子产品在服役期间的工艺可靠性问题 70
5.1 产品服役期的工艺可靠性 70
5.1.1 概述 70
5.1.2 影响产品制造缺陷的工艺可靠性问题 71
5.1.3 影响市场服役期故障的工艺可靠性问题 71
5.2 金属偏析现象 71
5.2.1 偏析的定义及分类 71
5.2.2 偏析对焊点可靠性的影响 72
5.2.3 焊接过程中Pb偏析形成机理 73
5.2.4 抑制焊点出现偏析的措施 74
5.3 黑色焊盘现象 74
5.3.1 黑盘现象 74
5.3.2 黑盘现象的形成机理 75
5.3.3 有关“黑盘现象”隐患的背景资料 77
5.4 Au脆现象 78
5.4.1 Au脆现象的发现 78
5.4.2 焊点中Au含量对脆性的影响 78
5.4.3 Au脆现象发生的冶金机制 80
5.4.4 Au脆的控制 81
5.4.5 Au脆危害可靠性的案例 81
5.5 金属离子迁移现象 83
5.5.1 金属离子迁移的定义和分类 83
5.5.2 Ag离子迁移现象的发现 83
5.5.3 Ag离子的迁移机理 84
5.5.4 Ag迁移现象对可靠性的危害 85
5.5.5 导电阳极细丝(CAF)现象 86
5.5.6 CAF的生长机理及危害 87
5.5.7 对CAF生成因素的控制 87
5.6 钎料的电子迁移现象 88
5.6.1 钎料电子迁移概述 88
5.6.2 电子迁移对接合界面的影响 89
5.6.3 电子迁移对倒装片接续的影响 90
5.7 Sn晶须生长现象 91
5.7.1 金属晶须 91
5.7.2 Sn晶须生成的环境条件 92
5.7.3 Sn晶须生长的机理 95
5.7.4 Sn晶须生长的抑制 97
5.8 爬行腐蚀现象 98
5.8.1 问题的提出 98
5.8.2 爬行腐蚀 99
5.8.3 对爬行腐蚀的防护措施 101
5.8.4 爬行腐蚀、离子迁移枝晶及CAF等的异同 101
5.8.5 失效案例分析 101
5.9 柯肯多尔空洞 104
5.9.1 柯肯多尔空洞的形成 104
5.9.2 柯肯多尔空洞对焊点可靠性的影响 104
5.10 产品在用户服役期中工艺可靠性的蜕变现象 105
5.10.1 工艺可靠性蜕变现象 105
5.10.2 固相老化中显微组织演化 105
第6章 理想焊点的质量模型及其影响因素 107
6.1 软钎接焊点对电子系统可靠性的贡献 107
6.1.1 软钎接在电子装联工艺中的地位 107
6.1.2 软钎接是影响电子产品制造质量的主要根源 107
6.2 理想焊点接续界面的质量模型 107
6.2.1 理想焊点界面结构的质量要求 107
6.2.2 理想焊点的质量模型对提高产品质量的贡献 108
6.3 构成理想焊点质量模型的主要条件分析 108
6.3.1 低的基板Z轴方向的CTE值 108
6.3.2 平整且厚度合适的均匀IMC层 110
6.3.3 界面体内粒度小于100nm的微细强化粒子 114
6.3.4 偏析少的钎料组织 117
6.3.5 弱的氧化膜 121
6.4 软钎接焊点在用户服役中所能耐受的最高温度 122
第7章 有铅和无铅混合组装的工艺可靠性 124
7.1 有铅和无铅混合组装 124
7.1.1 概述 124
7.1.2 有铅向无铅技术转变的过渡时期 124
7.1.3 有铅与无铅混合组装的相容性 125
7.2 混合组装合金焊点的可靠性 126
7.2.1 概述 126
7.2.2 Intel公司组织的对混合合金焊点的可靠性试验和评估 127
7.2.3 Jennifer Nguyen等人对混合合金焊点的可靠性评估 133
7.2.4 混合合金焊点的可靠性综合评估 136
7.3 影响混合合金焊点工艺可靠性的因素 136
7.3.1 无铅、有铅混用所带来的工艺问题 136
7.3.2 混合合金焊点的工艺可靠性设计 137
7.3.3 PCB焊盘及元器件引脚焊端涂敷层 138
7.3.4 混合组装再流焊接时应注意的事项 138
7.3.5 混合组装再流焊接温度曲线的优化 140
第8章 电子产品无Pb制程的工艺可靠性问题 142
8.1 电子产品无Pb制程工艺可靠性概述 142
8.1.1 前言 142
8.1.2 无Pb制程定义及系统考虑 142
8.1.3 电子产品无Pb制程工艺可靠性 143
8.2 影响电子产品无Pb制程工艺可靠性的因素 144
8.2.1 影响无Pb焊点工艺可靠性的因素 144
8.2.2 钎料合金 144
8.2.3 元器件 145
8.2.4 PCB 146
8.2.5 工艺因素 149
8.2.6 对环境的适应性 151
8.2.7 环境影响因素 151
8.2.8 导电阳极丝及柯肯多尔空洞 152
8.3 脆变现象 152
8.3.1 无Pb焊接脆弱性问题 152
8.3.2 脆变机理 153
8.4 无Pb焊点的质量和可靠性测试 154
8.4.1 无Pb制程所面临的挑战 154
8.4.2 无Pb焊点的质量和可靠性试验 155
8.5 无Pb制程焊点可靠性评估(与SnPb钎料比较) 155
8.5.1 等温机械疲劳测试 155
8.5.2 热疲劳测试 156
8.5.3 热机械负荷测试 159
8.5.4 高温和高低温温度冲击试验 159
8.5.5 BGA、CSP由有Pb到无Pb制程的可靠性变化 160
8.5.6 无Pb钎料的机械振动 161
8.5.7 微组织和合金层 161
8.6 无Pb再流焊冷却速率对焊点可靠性的影响 162
8.6.1 问题的提出 162
8.6.2 冷却对无Pb钎料的影响 163
8.6.3 冷却在生产中的应用 164
8.7 无Pb焊点特有的工艺缺陷现象 165
8.7.1 凝固过程生成的缺陷 165
8.7.2 Pb污染引起的现象 172
第9章 波峰焊接焊点的工艺可靠性设计 175
9.1 概述 175
9.1.1 波峰焊接焊点接头工艺可靠性设计的意义 175
9.1.2 波峰焊接焊点的形成过程及控制因素 175
9.2 焊点的接头 175
9.2.1 焊点的接头模型 175
9.2.2 波峰焊接的基本接头结构和工艺设计要求 176
9.3 焊接接头结构设计对接头机电性能的影响 178
9.3.1 接头的几何形状设计及对强度的影响 178
9.3.2 焊接接头的电气特性 180
9.4 影响焊接接头机械强度的因素 183
9.4.1 施用的钎料量对焊点剪切强度的影响 183
9.4.2 与熔化钎料接触的时间对焊点剪切强度的影响 184
9.4.3 焊接温度对接头剪切强度的影响 184
9.4.4 接头厚度对强度的影响 185
9.4.5 接头强度随钎料合金成分和基体金属的变化 186
9.4.6 钎料接头的蠕变强度 187
9.5 基体金属的可焊性和焊点的可靠性 189
9.5.1 可焊性 189
9.5.2 影响焊点可靠性的因素 190
9.5.3 波峰焊接表面的净度和电子污染 192
9.5.4 镀层可焊性的储存期试验及试验方法 194
第10章 SMT再流焊接焊点的工艺可靠性设计 196
10.1 SMT再流焊接焊点的结构特征 196
10.2 再流焊接接合部工艺可靠性设计概述 198
10.2.1 接合部工艺可靠性设计的目的和任务 198
10.2.2 接合部工艺可靠性设计的定义和内容 198
10.3 片式元器件再流焊接接合部工艺可靠性设计及举例 200
10.3.1 片式元器件焊点工艺可靠性设计 200
10.3.2 片式元器件焊点工艺可靠性设计举例 207
10.4 QFP再流焊接接合部工艺可靠性设计及举例 210
10.4.1 QFP接合部工艺可靠性设计 210
10.4.2 QFP接合部工艺可靠性设计举例 213
10.5 BGA、CSP再流焊接接合部工艺可靠性设计 217
10.5.1 工艺可靠性设计(确定必要的钎料量) 217
10.5.2 焊盘设计 219
10.5.3 印刷钢网开口尺寸的确定 220
第11章 PCBA常见的危及可靠性的故障现象及其分析 222
11.1 PCBA和故障 222
11.1.1 概述 222
11.1.2 失效分析基础 222
11.1.3 PCBA失效分析的层次和原则 223
11.1.4 失效分析方法 224
11.2 PCBA在生产过程中发生的缺陷现象 224
11.2.1 PCBA的翘曲和应力 224
11.2.2 再流焊接的爆板 226
11.2.3 再流焊接中的分层现象 230
11.2.4 潮湿敏感元器件的爆米花现象 231
11.2.5 拼板安装分板时对产品质量和可靠性的影响 233
11.2.6 某键盘板再流焊接后焊盘变黑 233
11.2.7 某按键镀金面变色 234
11.2.8 USB尾插焊后脱落 236
11.2.9 功放过孔断线现象 241
11.3 PCBA服役期中发生的缺陷现象 243
11.3.1 服役期中PCBA板面发现化学腐蚀 243
11.3.2 某背板产品在用户服役期间焊点发白 244
11.3.3 某背板产品在加电工作中因绝缘击穿而烧毁 247
11.3.4 PTH绿油塞孔口发生黑色物堆集现象 248
11.4 PCBA多余物 250
11.5 PCBA的清洁度标准 251
11.5.1 概述 251
11.5.2 PCBA清洁度要求 252
第12章 PCBA焊点失效分析 254
12.1 PCBA焊点失效分析基础 254
12.1.1 名词及定义 254
12.1.2 损坏机制和焊点失效概述 254
12.1.3 焊点和焊接层类型 255
12.1.4 焊接连接部失效 256
12.2 虚焊及冷焊 258
12.2.1 概述 258
12.2.2 虚焊 259
12.2.3 冷焊 261
12.3 BGA焊点的常见失效模式及机理 265
12.3.1 界面失效 265
12.3.2 钎料疲劳失效 265
12.3.3 张力载荷引起蠕变断裂 267
12.3.4 弯曲试验常见的失效 267
12.4 BGA组装异常案例分析 268
12.4.1 概述 268
12.4.2 BGA焊盘定义 269
12.4.3 BGA钎料球过度坍塌 269
12.4.4 焊膏的印刷状态 269
12.4.5 BGA中介层的变形 270
12.4.6 焊接的焊点状态 271
12.5 生产中PCBA焊点失效典型案例 273
12.5.1 案例1:MP3主板器件焊点脱落 273
12.5.2 案例2:某单板角焊点断裂 275
12.5.3 案例3:某批终端产品在生产中发生不开机现象 278
12.6 PCBA在服役期焊点失效的典型案例 279
12.6.1 案例1:某产品PCBA主板在用户服役中BGA焊点断裂 279
12.6.2 案例2:X-FPBA失效 283
12.6.3 案例3:某计算机用PCBA上BGA的部分钎料球焊点开裂 285
12.7 焊点可靠性蜕变现象讨论 286
12.7.1 镀层因素 286
12.7.2 老化与IMC长厚 287
第13章 工艺可靠性试验 289
13.1 工艺可靠性试验概论 289
13.1.1 工艺可靠性试验的目的 289
13.1.2 试验分类和检测技术的适用性 290
13.2 主要的试验内容和方法 291
13.2.1 外观检查 291
13.2.2 接合强度评价 292
13.2.3 X射线透视检查 294
13.2.4 红外热敏成像 296
13.2.5 红外显微镜分析(FT) 297
13.2.6 声频显微扫描检测技术 297
13.2.7 扫描电镜与能谱分析 298
13.2.8 内窥镜光学检验 299
13.2.9 着色探伤检测法 300
13.2.10 金相切片 301
13.2.11 温度循环试验 303
13.3 获得焊点可靠性的基础——基体金属的可焊性试验 304
13.3.1 可焊性的定义 304
13.3.2 可焊性和可靠性 305
13.3.3 焊接过程中与可焊性相关的物理参数 305
13.3.4 可焊性试验 305
参考文献 309
- 《电子测量与仪器》人力资源和社会保障部教材办公室组织编写 2009
- 《少儿电子琴入门教程 双色图解版》灌木文化 2019
- 《葡萄酒工艺与鉴赏 第3版》廖祖宋 2019
- 《化学工程与工艺专业实验指导》郭跃萍主编 2019
- 《美物之道 日本手工艺》(日)柳宗悦著 2019
- 《通信电子电路原理及仿真设计》叶建芳 2019
- 《电子应用技术项目教程 第3版》王彰云 2019
- 《中国电子政务发展报告 2018-2019 数字中国战略下的政府管理创新》何毅亭主编 2019
- 《电子管风琴伴奏中外经典合唱曲集》主编;王永刚副主编;宋尧尧陈宏赵雪陈海涛 2019
- 《有色金属冶金新工艺与新技术》俞娟,王斌,方钊,崔雅茹,袁艳 2019
- 《市政工程基础》杨岚编著 2009
- 《家畜百宝 猪、牛、羊、鸡的综合利用》山西省商业厅组织技术处编著 1959
- 《《道德经》200句》崇贤书院编著 2018
- 《高级英语阅读与听说教程》刘秀梅编著 2019
- 《计算机网络与通信基础》谢雨飞,田启川编著 2019
- 《看图自学吉他弹唱教程》陈飞编著 2019
- 《法语词汇认知联想记忆法》刘莲编著 2020
- 《培智学校义务教育实验教科书教师教学用书 生活适应 二年级 上》人民教育出版社,课程教材研究所,特殊教育课程教材研究中心编著 2019
- 《国家社科基金项目申报规范 技巧与案例 第3版 2020》文传浩,夏宇编著 2019
- 《流体力学》张扬军,彭杰,诸葛伟林编著 2019
- 《电子测量与仪器》人力资源和社会保障部教材办公室组织编写 2009
- 《少儿电子琴入门教程 双色图解版》灌木文化 2019
- 《指向核心素养 北京十一学校名师教学设计 英语 七年级 上 配人教版》周志英总主编 2019
- 《北京生态环境保护》《北京环境保护丛书》编委会编著 2018
- 《指向核心素养 北京十一学校名师教学设计 英语 九年级 上 配人教版》周志英总主编 2019
- 《通信电子电路原理及仿真设计》叶建芳 2019
- 《高等院校旅游专业系列教材 旅游企业岗位培训系列教材 新编北京导游英语》杨昆,鄢莉,谭明华 2019
- 《电子应用技术项目教程 第3版》王彰云 2019
- 《中国十大出版家》王震,贺越明著 1991
- 《近代民营出版机构的英语函授教育 以“商务、中华、开明”函授学校为个案 1915年-1946年版》丁伟 2017