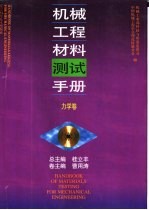
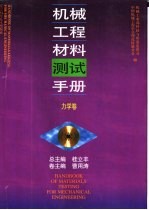
机械工程材料测试手册 力学卷PDF电子书下载
- 电子书积分:22 积分如何计算积分?
- 作 者:桂立丰总主编;曹用涛卷主编;机械工业部科技与质量监督司,中国机械工程学会理化检验分会编
- 出 版 社:沈阳:辽宁科学技术出版社
- 出版年份:2001
- ISBN:7538129545
- 页数:809 页
第1章概论 3
4.1.2肖维奈(Chauvenet)准则 (8 3
第1篇总论 3
第2章发展历史及展望 4
第3章力学性能试验方法 5
第5章应用力学性能判据的几个问题 8
第4章材料力学性能与结构强度的关系 8
参考文献 11
1.2单向应力状态的分析 15
第2篇材料力学性能试验基础 15
第1章概论 15
1概述 15
1.1应力状态 15
1.1.1一点的应力状态 15
1.1.2应力状态的分类 15
1.3.2图解法——莫尔圆法 16
1.3二向应力状态的分析 16
1.3.1解析法 16
1.4.1解析法 17
1.3.3工程实例 17
1.4三向应力状态的分析 17
1.4.2图解法 20
1.6应力张量的分解及应力偏量 21
1.5平衡微分方程 21
2.1.2应变与位移的关系 22
2应变分析 22
2.1应变状态 22
2.1.1一点的应变状态 22
2.3应变张量及其分解 23
2.2主应变 23
2.5应变莫尔圆 24
2.4协调方程 24
3.1广义胡克定律 25
3弹性力学中的广义胡克定律和基本方程 25
3.2按位移求解弹性力学问题 26
3.3按应力求解弹性力学问题 28
3.4平面问题和应力函数 29
4.1.2塑性变形的机理 30
4 弹性力学的基本方程 30
4.1塑性变形和塑性力学 30
4.1.1塑性变形的定义和特点 30
4.1.4材料单向拉伸时的应力-应变关系 31
4.1.3塑性力学问题的特点 31
4.2金属的形变强化 32
4.3.2密赛斯(Mises)条件 33
4.3屈服条件 33
4.3.1屈雷斯卡(Tresca)条件 33
4.4.1增量理论(流动理论) 34
4.4塑性力学的基本方程 34
5.1.1按断裂性质(性态)分类 35
4.4.2全量理论(形变理论) 35
5金属的断裂和强度理论 35
5.1断裂的分类 35
5.1.4按断裂机理分类 36
5.1.2按裂纹扩展路径分类 36
5.1.3按断裂面的取向分类 36
5.2断口的宏观特征 37
5.2.1静拉伸断口的宏观形貌 38
5.2.2高周疲劳断口的宏观形貌 39
5.3.1理论断裂强度 40
5.2.3冲击试样断口的宏观形态 40
5.3断裂强度 40
5.4强度理论 41
5.3.2缺口强度理论 41
5.4.2能量强度理论 42
5.4.1三个古典强度理论的主要内容 42
5.4.5联合强度理论 43
5.4.3四个强度理论的比较 43
5.4.4莫尔强度理论 43
1.3.2样坯切取的规则 45
第2章力学性能试验的试样制备 45
1概述 45
1.1材料的力学性能和力学性能试验 45
1.2力学性能试验的试样类型 45
1.3样坯切取的原则和规则 45
1.3.1样坯切取的原则 45
1.4.2棒材的取样 46
1.4取样方法 46
1.4.1型材的取样 46
1.4.3管材的取样 47
1.4.5焊接接头的取样 48
1.4.4钢板的取样 48
1.4.7铸钢的取样 52
1.4.6灰铸铁的取样 52
1.4.8球墨铸铁的取样 53
2.1.2对试样加工的要求 54
2试样的加工 54
2.1冲击试样 54
2.1.1夏比冲击试验所采用的试样类型 54
2.2.2疲劳试样的加工方法 55
2.2 疲劳试样 55
2.2.1制备疲劳试样的要求 55
2.3.1蠕变试样的制备 56
2.3 蠕变试样、持久强度试样和松弛试样 56
2.3.2持久强度试样的制备 57
2.3.3拉伸应力松弛试样的制备 58
1.2.2概率运算的基本法则 59
第3章试验数据的处理和误差分析 59
1概述 59
1.1随机事件 59
1.2概率的定义及基本运算法则 59
1.2.1概率的定义 59
1.4.1正态分布 60
1.3 随机变量及其概率分布 60
1.3.1随机变量 60
1.3.2概率分布 60
1.4几种重要的概率分布 60
1.4.3对数正态分布 62
1.4.2威布尔分布 62
2.1数理统计的内容和定义 66
2 数理统计的基本概念和方法 66
2.2.1点估计 67
2.2参数估计 67
2.2.2区间估计 68
2.3.1基本概念 71
2.3假设检验 71
2.3.2几种检验方法的应用 72
2.4.2一元线性回归 74
2.4回归分析 74
2.4.1基本概念 74
3.1.3误差的分类 77
3 误差的分类和处理 77
3.1误差的定义和分类 77
3.1.1误差的定义 77
3.1.2真值和平均值 77
3.2.2误差的表示方法 78
3.2 直接测定量的误差表示法 78
3.2.1误差的分布规律 78
3.2.3误差理论的应用实例 79
3.3.1误差传递公式 80
3.3间接测量中误差的传递 80
3.3.2误差传递中标准误差的计算公式 81
4.1.1拉依达准则 82
4 力学性能试验数据处理举例 82
4.1可疑观测值的取舍 82
4.1.4t检验准则 83
4.1.3格拉布斯(Grubbs)准则 83
4.1.5狄克逊(Dixon)准则 84
4.2.1符号检验法 85
4.2对比试验结果的统计处理 85
4.2.2秩和检验法 87
4.2.4成对对比试验 88
4.2.3成组对比试验 88
4.3.1估计母体中值所需的最少试样数 89
4.3考虑置信度时最少试样个数的确定 89
4.2.5对比两组试验结果分散性大小的F检验 89
4.3.2估计母体的百分位值所需的最小试样数 91
4.4单侧容限系数的确定 92
参考文献 93
3力学性能测试的自动化 97
2力学性能试验的标准化 97
第3篇金属常规力学性能试验 97
第1章概论 97
1概述 97
1概述 99
第2章金属拉伸试验 99
4力学性能测试的发展 99
4-5存活率估计量p=(1-i/n+1)× 100
2.2.1拉伸图 100
2拉力作用下的材料行为 100
2.1拉伸试验的力学分析 100
2.2拉伸图及工程应力-应变图 100
2.2.2工程应力-应变图 101
3.1拉伸试样的形状和尺寸 102
2.2.3真实应力-应变曲线 102
3拉伸试样 102
3.2试样尺寸及加工要求 103
4.2.1弹性模量的测定 104
4金属拉伸弹性阶段的性能 104
4.1单向拉伸应力状态下的胡克定律 104
4.2弹性模量及泊松比的测定方法 104
4.2.2泊松比的测定 105
5.2.1指针法 106
5屈服点 106
5.1屈服现象及屈服点 106
5.2屈服点、上屈服点及下屈服点的测定 106
6.2规定非比例伸长应力的测定 107
5.2.2图示法 107
5.3屈服点伸长率的测定 107
6规定伸长应力的测定 107
6.1规定伸长应力使用的术语和含义 107
6.2.2滞后环法 108
6.2.1用图解法测定规定非比例伸长应力σp 108
6.2.4逐级施力法 109
6.2.3逐步逼近法 109
6.3.1规定总伸长应力的测定方法 110
6.3规定总伸长应力的测定 110
6.4.2测定规定残余伸长应力σr0.2实例 111
6.3.2关于测定规定总伸长应力应用的几点说明 111
6.4规定残余伸长应力σr的测定 111
6.4.1规定残余伸长应力σr的测定方法 111
6.6测定σp、σt、σt及σs时的拉伸速度 112
6.4.3规定残余伸长应力的验证实验 112
6.4.4规定残余伸长应力σr应用的说明 112
6.5σp,σt及σr之间的关系 112
7.3最大力下的总伸长率和非比例伸长率及其测定 113
7抗拉强度及真实断裂强度 113
7.1抗拉强度及其测定 113
7.2真实断裂强度 113
8拉伸塑性指标及其测定 114
7.4颈缩 114
8.1.2断面收缩率及其测定 115
8.1塑性指标及其测定 115
8.1.1断后伸长率及其测定 115
8.3钢的伸长率换算 116
8.2条件应变与真应变 116
8.2.1均匀变形阶段的条件应变与真应变之间关系 116
8.2.2真实相对伸长及真实断面收缩率 116
9.1硬化指数n值的测定 119
9形变硬化指数 119
10拉伸试样的宏观断口形态 121
9.2形变硬化指数的工程意义 121
11.1电子万能试验机的结构原理 122
11拉伸试验机及引伸计 122
11.3引伸计的结构原理及选用 123
11.2对试验机的技术要求 123
12.3断面收缩率测量系统误差的估计 124
12拉伸试验测量误差的估计 124
12.1关于强度性能测量误差的估计 124
12.2断后伸长率的测量误差估计 124
13.2数字修约的规则 125
13关于测得性能数值修约的几个问题 125
13.1进行修约的原因 125
13.6.1实验结果无效 126
13.3有效数字位数的保留 126
13.4关于极限数值可否修约 126
13.5测定性能数值的修约 126
13.6实验结果的处理 126
13.6.2数据处理 127
1概述 128
第3章硬度试验 128
2布氏硬度 129
2.2压痕相似原理的应用 130
2.1试验原理 130
2.3试样 131
2.5操作要点 132
2.4试验设备 132
2.4.1布氏硬度计 132
2.4.2布氏硬度压痕测量装置 132
2.6试验结果及处理 133
2.7影响试验结果的主要因素 135
3.1试验原理 136
3洛氏硬度 136
3.3试验设备 137
3.2试样 137
3.4操作要点 138
3.5试验结果及处理 141
3.6表面洛氏硬度试验 142
3.7影响试验结果的主要因素 143
4维氏硬度 144
4.2试样 145
4.1试验原理 145
4.3试验设备 146
4.4操作要点 147
4.5试验结果及处理 149
4.6影响试验结果的主要因素 150
5.2试样 152
5肖氏硬度 152
5.1试验原理 152
5.6影响试验结果的主要因素 153
5.3试检设备 153
5.4操作要点 153
5.5试验结果及处理 153
6.2试样 154
6 里氏硬度 154
6.1试验原理 154
6.4操作要点 155
6.3试验设备 155
6.3.1冲击装置 155
6.3.2示装置 155
6.3.3示值误差和重复性 155
6.5试验结果及处理 156
1概述 157
6.6影响试验结果的主要因素 157
7各种硬度及硬度与强度之间的换算 157
第4章冲击试验 157
2.2冲击试样 158
2金属冲击试验方法 158
2.1金属冲击试验原理 158
3冲击功的分解 159
2.3试验操作要点 159
4.2评定材料在不同温度下的脆性转化趋势 160
4冲击试验的应用 160
4.1评定原材料的冶金质量及热加工后的产品质量 160
5.2控制与操作 161
4.3确定应变时效敏感性 161
4.4缺口敏感性指标 161
5低温冲击试验 161
5.1低温冲击试验设备及仪器 161
6.2韧脆转变温度的测定 162
6金属韧脆转变温度tk及低温系列冲击试验 162
6.1冷脆及韧脆转变温度tk 162
8高温冲击试验 164
7冲击试验的影响因素 164
9.2多次冲击试验方法 165
8.1高温冲击试验机 165
8.2高温冲击韧性的测定 165
9多次冲击试验 165
9.1多次冲击试验机构造 165
1概述 166
第5章扭转试验 166
3.1切变模量G 167
2扭转试样尺寸和测量 167
3扭转试验 167
3.3规定非比例扭转应力τp 169
3.2扭转屈服点的测定 169
3.5最大非比例切应变的测定 171
3.4抗扭强度τb 171
4.2试验机的操作要点 172
3.6测出扭转性能数值的修约 172
4扭转试验机 172
4.1对试验设备的要求 172
1压缩试验 173
5扭转试样的断口分析 173
第6章压缩、弯曲及剪切试验 173
1.2试验装置 174
1.1试样 174
1.3压缩性能指标的测定 175
1.4压缩试样的破坏形式 176
1.3.1板状试样实际压缩力 176
1.3.2规定非比例压缩应力 176
1.3.3压缩屈服点 176
1.3.4抗压强度 176
1.3.5压缩弹性模量 176
2.1弯曲试验原理 177
2金属弯曲试验 177
2.3试验设备 179
2.2试样 179
2.4.1规定非比例弯曲应力 180
2.4弯曲力学性能的测定 180
2.4.5弯曲弹性模量的测定 181
2.4.2规定残余弯曲应力 181
2.4.3抗弯强度的测定 181
2.4.4断裂挠度的测定 181
2.5缺口静弯试验 182
3.2双剪试验 183
3剪切试验 183
3.1单剪试验 183
参考文献 184
3.3冲孔式剪切试验 184
3-1由标距长度5.65 ?换算成不同定标距的换算因子β 186
附表常用数值表 186
3-2由比例标距4?换算成不同定标距的换算因子γ 187
3-3金属布氏硬度值 189
3-4金属维氏硬度数值表 210
3-5金属小负荷维氏硬度数值表(HV0.2~<HV5) 240
3-6金属显微维氏硬度数值表 273
3-7碳钢、低合金钢和铸钢(E≈*210000N·mm-2)D型冲击装置里氏硬度换算表 304
3-8铸铁D型冲击装置里氏硬度换算表 308
3-9铸铝合金(E=65~85kN·mm-2)D型冲击装置里氏硬度换算表 309
3-10铜锌合金(E=85~130kN·mm-2)D型冲击装置里氏硬度换算表 310
3-11铜铝合金及铜锡合金(E=94~130kN·mm-2)D型冲击装置里氏硬度换算表 311
3-12纯铜及低铜合金(E=110~135kN·mm-2)D型冲击装置里氏硬度换算表 312
3-13低碳钢、低合金钢及铸钢(E≈210kN·mm-2)G型冲击装置里氏硬度换算表 313
3-14灰口铸铁(GG)及球墨铸铁(GGG)(E=170~180kN·mm-2)G型冲击装置里氏硬度换算表 315
3-15低碳钢、低合金钢及铸钢(E≈210kN·mm-2)C型冲击装置里氏硬度换算表 316
3-16碳钢及合金钢硬度与强度换算表 319
3-17低碳钢硬度与强度换算表 323
3-18铜合金硬度与强度换算值表[适用于黄铜(H62、HPb59-1等)和铍青铜] 325
3-19首列为布氏硬度HB(F=10D2)的铝合金硬度与强度换算值表 340
3-20首列为布氏硬度HB(F=30D2)的铝合金硬度与强度换算值表 344
3-21首列为维氏硬度HV的铝合金硬度与强度换算值表 346
3-22首列为洛氏硬度HRB的铝合金硬度与强度换算值表 350
2疲劳发展简史 357
第4篇金属疲劳试验 357
第1章概论 357
1疲劳和疲劳试验的重要性 357
3.1疲劳裂纹萌生 358
3金属疲劳破坏机制 358
3.2疲劳裂纹扩展 359
4.2S-N曲线 360
3.3失稳断裂 360
4疲劳图 360
4.1应力循环 360
4.3频率曲线和概率密度函数 361
4.5.2 Haigh图 362
4.4p-S-N曲线 362
4.5疲劳极限线图 362
4.5.1Smith图 362
4.7循环σ-ε曲线 363
4.6等寿命图 363
5.1疲劳试验分类 364
4.8应变-寿命曲线 364
5疲劳试验与疲劳试验机分类 364
5.2疲劳试验机分类 365
1概述 366
第2章疲劳试样 366
2.2.2矩形试样 367
2试样设计 367
2.1对疲劳试样的一般要求 367
2.2试样尺寸 367
2.2.1圆试样 367
3.1.2外国标准 368
2.2.3缺口试样 368
2.2.4模拟试样 368
2.2.5全尺寸试样 368
3试样标准 368
3.1轴向疲劳试样 368
3.1.1中国国标 368
3.2.1中国国标 372
3.2旋转弯曲疲劳试样 372
3.2.2外国标准 373
3.4扭转疲劳试样 374
3.3平面弯曲疲劳试样 374
4.1试样制备的一般要求 375
3.5低周疲劳试样 375
3.5.1中国国标 375
3.5.2外国标准 375
4试样制备 375
1.1高周疲劳试验的特点 376
4.2中国国标推荐的试样加工工艺 376
4.2.1车削 376
4.2.2铣削 376
4.2.3磨削 376
4.2.4表面抛光 376
4.2.5缺口试样的加工 376
第3章高周疲劳试验方法及设备 376
1概述 376
1.5试验结果的表达 377
1.2试验机 377
1.3试样 377
1.4试验程序 377
2.2.1对轴向疲劳试验机的一般要求 378
1.6统计方法的应用 378
1.7试验报告 378
2轴向疲劳试验 378
2.1试验特点 378
2.2试验机 378
2.3.2同心度标定 379
2.2.2电磁式万能疲劳试验机 379
2.2.3液压式万能疲劳试验机 379
2.3轴向疲劳试验机的标定 379
2.3.1静载荷标定 379
2.3.3动态标定 381
3.1试验原理 382
2.4试样 382
2.5试验程序 382
2.6试验精度 382
3 旋转弯曲疲劳试验 382
3.2.2纯弯式旋转弯曲疲劳试验机 383
3.2试验机 383
3.2.1对旋转弯曲疲劳试验机的一般要求 383
3.3试样 384
3.2.3悬臂式旋转弯曲疲劳试验机 384
4.1试验原理 385
3.4试验程序 385
3.5试验精度 385
4平面弯曲疲劳试验 385
4.3试样 386
4.2试验机与夹具 386
5.2试验机与夹具 387
4.4试验程序 387
4.5试验精度 387
5 扭转疲劳试验 387
5.1试验原理 387
5.5试验精度 388
5.3试样 388
5.4试验程序 388
6.4弯-扭复合疲劳试验 389
6多轴应力疲劳试验 389
6.1双轴拉伸疲劳试验 389
6.2拉-扭疲劳试验 389
6.3拉伸-内压复合疲劳试验 389
7.1.2验证性疲劳试验 390
6.5三轴应力疲劳试验 390
7缩短试验时间 390
7.1试验基数的选择 390
7.1.1测定疲劳极限 390
1概述 391
7.1.3对比疲劳试验 391
7.2试验频率的选择 391
7.3同时试验几个试样 391
第4章高周疲劳性能测定 391
2.1常规试验方法 392
2疲劳极限和S-N曲线的测定方法 392
2.2升降法 394
2.3.1泊洛特法 395
2.3快速试验法 395
2.3.2罗卡提法 396
3.2.1按对数正态分布估计安全寿命 397
3 p-S-N曲线的测定 397
3.1可疑观察值的取舍 397
3.2安全寿命的测定 397
3.2.2按威布尔分布估计安全寿命 399
4.1成组对比试验 401
3.3 p-S-N曲线的绘制 401
4对比疲劳试验 401
4.2成对对比试验 403
1概述 404
4.3显著度的选取 404
第5章低周疲劳试验 404
2低周疲劳试验设备 405
3试验方法 406
4.1测定方法 408
4循环应力-应变曲线测定 408
4.2数据采集、处理和结果表达式 409
5应变-寿命曲线测定 410
1.2.1材料的疲劳强度 411
第6章随机疲劳试验 411
1概述 411
1.1等幅疲劳与随机疲劳 411
1.2材料与构件的随机疲劳强度 411
1.3随机疲劳试验与疲劳寿命估算框图 412
1.2.2构件的疲劳强度 412
1.2.3随机疲劳的累积损伤条件——有限寿命设计概念 412
2.1载荷谱与疲劳载荷谱 414
2疲劳载荷谱 414
2.2疲劳载荷谱的编制 415
2.4试验载荷谱与强化载荷谱 416
2.38级载荷谱及多工况合成谱 416
4.2试验载荷谱的程序块化 417
3载荷-时间历程重现疲劳试验 417
3.1应力仿真模拟疲劳试验 417
3.2载荷仿真模拟疲劳试验 417
4载荷谱程序块模拟疲劳试验 417
4.1试验谱的局部强化 417
5.1随机过程的时域环境模拟 418
4.3程序块疲劳试验的结果寿命 418
5功率谱法随机环境模拟疲劳试验 418
5.2.2模拟时域历程的损伤等效性 419
5.2时域环境随机过程模拟原理及方法 419
5.2.1时域环境模拟的数学方法 419
5.4.1谱仿真试验的原理框图 420
5.3随机疲劳环境模拟的装置 420
5.4谱仿真随机疲劳试验方法 420
6.1随机载荷对材料疲劳寿命的影响 422
5.4.2谱仿真试验方法的流程 422
6随机载荷下的材料S-N曲线疲劳试验 422
6.2随机载荷加载的材料疲劳试验方法 423
2高温疲劳试验 424
第7章环境介质中的疲劳试验 424
1概述 424
3低温疲劳试验 425
4.1热疲劳的应力-应变曲线 426
4热疲劳 426
4.2试验方法 427
5腐蚀疲劳 428
6.1试验方法 429
6接触疲劳 429
6.2数据处理 430
2.1化学成分和夹杂物的影响 432
第8章影响材料疲劳抗力的因素 432
1概述 432
2内部因素影响 432
2.2热处理和显微组织的影响 433
3缺口效应 434
2.3晶粒度和方向性的影响 434
3.3.2敏感度法 435
3.1疲劳缺口系数的定义和影响因素 435
3.2疲劳缺口系数试验 435
3.3常用的疲劳缺口系数确定方法 435
3.3.1图表法 435
4.1引起尺寸效应的原因 436
3.3.3应力梯度法 436
4尺寸效应 436
5.1.1影响机理 438
4.2尺寸系数试验曲线 438
5表面状况影响 438
5.1表面终加工方法 438
5.1.3表面加工系数线图 439
5.1.2切削用量的影响 439
5.2.1表面强化对疲劳强度的影响 440
5.1.4表面加工对疲劳缺口系数的影响 440
5.2表面强化 440
5.2.2表面淬火 441
5.2.3表面化学热处理 442
5.2.4表面冷作 443
6.2拉伸平均应力影响 444
6平均应力影响 444
6.1平均应力对疲劳强度影响的测定方法 444
7.1加载频率影响 445
6.3压缩平均应力影响 445
6.4扭转平均应力影响 445
7其他因素影响 445
7.3中间停歇影响 446
7.2应力波形影响 446
参考文献 447
4-4最少观测值个数(p=99.9%,γ=90%,δmax=5%) 448
附表常用数值表 448
4-1最少观测值个数(p=50%,γ=95%,δmax=5%) 448
4-2最少观测值个数(p=50%,γ=90%,δmax=5%) 448
4-3最少观测值个数(p=99.9%,γ=95%,δmax=5%) 448
4-6up和p数值表 449
4-8x2分布数值表 451
4-7相关系数检验表 451
4-9 t分布数值表 452
4-11F分布数值表之一(α=20%) 453
4-10标准差修正系数β值 453
4-12F分布数值表之二(α=10%) 454
4-13F分布数值表之三(α=5%) 455
4-14F分布数值表之四(α=2%) 456
4-15F分布数值表之五(α=1%) 457
4-17г函数表 458
4-16子样大小与[?]关系表 458
4-18点接触的系数 459
4-19最大似然估计斜率参数修偏系数表 461
4-20最佳线性不变估计系数 464
1.1裂纹的定义和三种受力模型 471
1线弹性断裂力学 471
第5篇金属材料断裂韧性试验 471
第1章概论 471
1.2.3应力强度因子K1 472
1.2.2平面应力和平面应变 472
1.2裂纹尖端的应力场和应力强度因子KI 472
1.2.1裂纹尖端的应力场 472
1.3裂纹尖端的塑性区 473
1.4.2KI的小范围屈服修正 474
1.4.1应力松弛对塑性区的影响 474
1.4KI的小范围屈服修正 474
1.5.3KI=KIC的应用范围 475
1.5.2KI和GI的关系 475
1.5线弹性断裂力学判据KI=KIC 475
1.5.1KI和KIC的物理含义 475
2.1裂纹尖端张开位移CTOD的模型理论 476
2弹塑性断裂力学的CTOD理论 476
2.2裂纹尖端张开位移CTOD的经验理论 477
3.1J积分的定义 478
3弹塑性断裂力学J积分理论 478
3.3J积分的计算 479
3.2J积分的性质 479
1.1断裂韧性的实验现象 481
1静载试验机、高频疲劳试验机、载荷传感器和位移传感器 481
第2章断裂韧性的试验设备 481
1.2.1对试验机的要求 482
1.2静载试验机 482
1.3.1结构简介 483
1.3高频疲劳试验机 483
1.2.2三点弯曲支座的设计 483
1.2.3紧凑拉伸夹具的设计 483
1.4.1构造与原理 484
1.4载荷传感器 484
1.3.2操作方法 484
1.5.1双悬臂夹式引伸计的设计和制作 485
1.5位移传感器 485
1.4.2主要技术指标 485
1.5.2引伸计的标定 486
2.1动态应变仪 487
2 动态应变仪、X-Y记录仪、电位测量仪和声发射仪 487
2.2.1构造和工作原理 488
2.2X-Y记录仪 488
2.1.1基本原理 488
2.1.2电桥电路 488
2.3.1直流电位测量仪 489
2.3电位测量仪 489
2.2.2操作及注意事项 489
2.3.2交流电位测量仪 490
2.4声发射仪 491
2.4.2试验方法 492
2.4.1构造与工作原理 492
1.3.1三点弯曲试样的KI表达式 493
1.3常用试样的型式及KI表达式 493
第3章平面应变断裂韧性KIC的测试 493
1概述 493
1.1平面应变断裂韧性KIC的定义 493
1.2保证平面应变状态所需的试样尺寸要求 493
1.3.3C形拉伸试样的KI表达式 494
1.3.2标准紧凑拉伸试样的KI表达式 494
2.1取样的方向和部位 495
2试样的制备 495
1.3.4圆形紧凑拉伸试样的KI表达式 495
2.2试样尺寸的确定 496
2.3试样的加工 497
2.4预制疲劳裂纹 498
3.2相对裂纹扩展量△α/α与相对裂纹张开位移△V/V的关系 499
3.1试验记录及F-V曲线的形式 499
3 试验方法 499
3.4KIC的计算及KIC有效性条件的检验 500
3.3裂纹α的测量方法 500
3.5KIC测试的误差分析 501
1.2.2对试样的要求 502
1.2.1试样的形状和尺寸 502
第4章金属材料裂纹尖端张开位移CTOD的测定 502
1概述 502
1.1裂纹尖端张开位移的定义 502
1.1.1 CTOD各项指标的定义 502
1.1.2试验的目的 502
1.2试样的制备 502
2.1.1多试样法 503
2.1试验方法 503
1.2.3预制疲劳裂纹 503
2试验方法和试验结果的处理 503
2.2.2的计算方法 505
2.2.1F-V曲线的类型和处理 505
2.1.2单试样法 505
2.2试验结果的分析和处理 505
2.3.1试验装置 508
2.3低温CTOD试验 508
2.2.3?的确定 508
2.2.4 δ0.05的确定 508
2.2.5 CTOD值的有效性检验 508
1概述 509
第5章金属材料延性断裂韧度JIC的试验方法 509
2.3.2试验条件 509
2试样的制备及试样的J积分计算式 510
3.2试验方法 511
3.1支座和夹具 511
3试验方法及数据处理 511
3.3试验结果的处理 516
3.4试验数据处理注意事项 516
1.3动态断裂力学所用的参量 517
1.2动态断裂力学 517
第6章动态断裂韧性KId的测定 517
1概述 517
1.1动态断裂 517
1.4动态断裂韧性KId与加载速率的关系 518
2.2动态扩展时的惯性力 519
2.1动态扩展时的能量平衡关系 519
2动态断裂韧性的测试原理 519
2.3动态应力强度因子的柔度标定法 520
3.1测试方法的分类 521
3动态断裂韧性的测试方法 521
2.4动态断裂韧性JId的测试原理 521
3.3起裂点的确定 522
3.2加载设备 522
4.233CrNi3Mo 523
4.115MnMoVCu 523
4若干工程材料的动态断裂韧性 523
4.430CrNiMo8 524
4.335CrMoA 524
4.616Mn和09MnTiCuRe及其焊缝 525
4.5A508 525
1.1疲劳裂纹扩展的特点和规律 526
1概述 526
第7章疲劳裂纹扩展速率da/dN的试验方法 526
2.1试样的形状尺寸和数量 527
2试样的制备 527
1.2疲劳裂纹扩展速率dα/dN的测定 527
2.2预制疲劳裂纹 528
3.2试验的方法细节及要求 529
3.1试验装置 529
3试验方法 529
4.2试验结果处理的两种方法 530
4.1裂纹曲率的修正 530
4试验结果的处理和计算 530
1.2测定△Kth的原理 532
1.1.2测定△Kth的目的 532
第8章 疲劳裂纹扩展门槛值△Kth的试验方法 532
1概述 532
1.1研究和测定△Kth的目的 532
1.1.1△Kth的定义 532
2.3.1三种降载方法 533
2.3降K试验法 533
2测试方法 533
2.1试样 533
2.2试验设备 533
2.3.2试验要点 534
2.4.2增K试验程序 535
2.4.1增K试验的目的 535
2.4增K试验法 535
2.5.2升降法试验数据处理 536
2.5.1升降法试验步骤 536
2.5升降法测△Kth 536
1.1.3晶粒尺寸的影响 537
1.1.2杂质元素的影响 537
第9章断裂韧性的影响因素及其与常规力学性能的关系 537
1概述 537
1.1断裂韧性与材料内部组织的关系 537
1.1.1合金成分的影响 537
1.1.6热处理的影响 538
1.1.5组织对断裂韧性的影响 538
1.1.4夹杂物和第二相的影响 538
1.2.1加载速率的影响 539
1.2断裂韧性与外在条件的关系 539
2.1断裂韧性与强度和塑性的关系 540
2断裂韧性与常规力学性能的关系 540
1.2.2温度的影响 540
1.2.3板厚的影响 540
参考文献 541
2.2断裂韧性与冲击韧性的关系 541
2高温下金属材料的性能 545
1概述 545
第6篇金属高温长时性能试验 545
第1章概论 545
3.2蠕变过程中组织结构的变化 546
3.1蠕变现象 546
3金属的蠕变 546
3.3蠕变过程变形与断裂的机制 547
3.4影响蠕变强度的因素 549
2.1蠕变曲线 551
2蠕变曲线及蠕变极限 551
第2章金属拉伸蠕变试验 551
1概述 551
3 蠕变试验机及技术要求 552
2.2蠕变极限 552
3.3温度测量及控制 553
3.2加热系统 553
3.1加荷系统 553
4.3安装试样 554
4.2试样测量与计算荷重 554
3.4变形测量系统 554
4蠕变试验操作要点 554
4.1试样 554
4.5关于中途停试的处理 555
4.4升温与加力 555
5.3.1等温线法 556
5.3蠕变极限的测定 556
5试验数据处理 556
5.1试验数据的获取 556
5.2蠕变速度的确定方法 556
5.3.2时间-温度参数法 557
6.3试样受力偏心的影响 558
6.2载荷的影响 558
6影响试验结果的因素 558
6.1温度的影响 558
1.1持久强度极限 559
1概述 559
6.4试样尺寸因素的影响 559
6.5试样表面氧化的影响 559
第3章持久强度试验 559
2持久强度试验机 560
1.4计算公式 560
1.2持久塑性 560
1.3持久缺口敏感性 560
3.1试样 561
3持久强度试验操作要点 561
3.3.1试验前的测定工作及计算 563
3.3试验操作过程 563
3.2试验参数的确定 563
4持久强度试验的注意事项 564
3.3.5试样断裂后的测量工作 564
3.3.2装样 564
3.3.3升温及加载 564
3.3.4试验过程的管理 564
5.2.1等温线法 565
5.2持久强度外推公式 565
5持久强度试验数据处理与外推 565
5.1关于持久强度的外推 565
5.3.1最小二乘法 566
5.3数据处理与计算方法 566
5.2.2时间-温度参数(T.T.P)法 566
5.3.2回归分析法 567
5.5持久断裂数据的统计分布规律 569
5.4等温线法、时间-温度参数(T.T.P)法的适用性 569
5.6.1加速寿命试验及短期试验区域分布参数的估计 570
5.6统计分布外推法 570
5.6.2持久强度外推统计模型 571
6持久强度的工程应用及试验实例 572
5.6.3外推值的置信区间计算 572
1概述 573
第4章蠕变裂纹扩展试验 573
2.2?(t)参量 574
2.1试样及其制备 574
2试样与?(t)参量定义 574
3.2裂纹长度的测量——直流电位法 575
3.1加载点位移的测量 575
3蠕变裂纹扩展试验的测试装置 575
3.3操作要点 577
1.1.1全息照相的原理和特点 578
3.4.2试验结果的分析 578
3.4数据处理与试验结果分析 578
3.4.1数据处理的方法 578
3.4.3有效性判断 579
1.1蠕变疲劳交互作用的工程应用 580
第5章蠕变疲劳复合试验 580
1概述 580
1.2蠕变疲劳复合性能测试原理 581
2.1.1符号及定义 583
2蠕变疲劳复合试验方法 583
2.1周期持久试验 583
2.1.2试样及制备 584
2.1.4试验过程及试验结果处理 585
2.1.3试验仪器及试验条件 585
2.1.6几种常用工程材料的试验结果 586
2.1.5试验记录及报告 586
2.2.2蠕变疲劳复合寿命预测 589
2.2时间相关蠕变疲劳复合试验 589
2.2.1基本原理及应用 589
2.2.3时间相关蠕变疲劳复合试验实例 590
2.3蠕变疲劳裂纹扩展试验 591
2.4GH169蠕变疲劳裂纹扩展试验实例 597
3.1蠕变疲劳复合损伤 599
3蠕变疲劳复合试验结果的评定 599
4.1拉压保时对蠕变疲劳复合损伤的影响 601
3.2延性耗竭理论 601
3.3蠕变疲劳复合裂纹扩展的断裂力学评定 601
4蠕变疲劳复合试验的影响因素 601
4.3保持时间对蠕变疲劳复合寿命的影响 602
4.2平均应力σm与应力幅σa对寿命的影响 602
4.4.2力学过程的影响 603
4.4几种因素对蠕变疲劳裂纹扩展的影响 603
4.4.1温度的影响 603
4.4.4其他因素的影响 604
4.4.3环境的影响 604
2拉伸应力松弛试验 605
第6章应力松弛试验 605
1概述 605
2.1.1试样的制备 606
2.1试样制备与检验 606
2.2.2拉伸松弛试验设备 607
2.1.2试样的检验 607
2.2技术要求及测试仪器 607
2.2.1拉伸松弛试验技术要求 607
3 弯曲应力松弛试验 608
2.3试验及操作要点 608
2.3.1试验环境和条件 608
2.3.2试样及热电偶的安装要求 608
2.3.3引伸计的安装原则 608
2.3.4升保温及加载方法 608
2.3.5测量与记录 608
2.3.6拉伸松弛试验程序 608
3.1.1试样的制备 609
3.1试样制备与检验 609
3.2.3设备性能 610
3.1.2试样检验要求 610
3.2测试设备及技术要求 610
3.2.1技术要求 610
3.2.2测试设备 610
3.3.4压痕距离的测量及剩余应力的计算 611
3.3试验及操作要点 611
3.3.1试验机的工作环境 611
3.3.2试样及热电偶的安装要求 611
3.3.3初应力的选择及施加方法 611
4.3外推评定 612
4数据处理与评定 612
4.1数据处理与取舍 612
4.2松弛曲线的建立与外推 612
5.4初应力的影响 613
5影响因素 613
5.1试验方法的影响 613
5.2试样尺寸与形状的影响 613
5.3试样制备方法的影响 613
参考文献 614
5.5重复加载的影响 614
1试验原理 619
第7篇金属工艺性能试验 619
第1章概论 619
1工艺性能试验的特点 619
2 工艺性能试验的分类 619
第2章金属弯曲试验 619
3试验设备 620
2试样制备 620
2.1样坯的切取 620
2.2试样形状和尺寸 620
2.3试样的制备 620
4试验方法 622
3试验设备 623
5结果评定 623
6注意事项 623
第3章金属杯突试验 623
1试验原理 623
2试样制备 623
6注意事项 624
4试验方法 624
5结果评定 624
5结果评定 625
第4章金属线材扭转试验 625
1试验原理 625
2试样制备 625
3试验设备 625
4试验方法 625
5注意事项 627
第5章金属顶锻试验 627
1试验原理 627
2试样制备 627
3试验方法 627
3.1冷顶锻试验 627
3.2热顶锻试验 627
4结果评定 627
6注意事项 628
第6章金属反复弯曲试验 628
1试验原理 628
2试样制备 628
3试验设备 628
4试验方法 628
5结果评定 628
4试验方法 630
第7章金属线材缠绕试验 630
1试验原理 630
2试样制备 630
3试验设备 630
1.2试样 631
5结果评定 631
6注意事项 631
第8章金属管工艺性能试验 631
1金属管液压试验 631
1.1试验原理 631
2.2试验设备 632
1.3试验设备 632
1.4试验方法 632
1.5结果评定 632
2金属管扩口试验 632
2.1试样制备 632
3.3试验方法 633
2.3试验方法 633
2.4结果评定 633
3 金属管缩口试验 633
3.1试样制备 633
3.2试验设备 633
5金属管卷边试验 634
3.4结果评定 634
4 金属管弯曲试验 634
4.1试样制备 634
4.2试验设备 634
4.3试验方法 634
4.4结果评定 634
6金属管压扁试验 635
5.1试样制备 635
5.2试验设备 635
5.3试验方法 635
5.4结果评定 635
6.3试验方法 636
6.1试样制备 636
6.2试验设备 636
参考文献 637
6.4结果评定 637
3光测法 641
第8篇实验应力分析 641
第1章概论 641
1概述 641
2电测法 641
2.1电阻应变计的工作特征 642
第2章电测力学 642
1概述 642
2电阻应变计 642
2.2.1电阻应变计的特性 644
2.2电阻应变计的特性、试验条件及质量 644
2.3.2检验 645
2.2.2电阻应变计的试验条件 645
2.2.3电阻应变计的质量 645
2.3电阻应变计的粘贴、检验与防护 645
2.3.1粘贴 645
3.1应变电桥 647
2.3.3防护 647
3电阻应变仪 647
3.1.2等臂对称电桥特性 648
3.1.1加减特性 648
3.1.4应变电桥的实用接法 649
3.1.3电桥的灵敏度 649
3.2.2动态应变仪 651
3.1.5电桥的平衡及电阻和电容平衡 651
3.2电阻应变仪的工作过程 651
3.2.1静态电阻应变仪 651
3.2.3以微机为中心的应变仪 652
4.6动应力的测量 653
4 应力测量 653
4.1简单受力状态的测量 653
4.2复杂受力状态下的单向应力测量 653
4.3剪力的测量 653
4.4平面应力状态下的应力测量 653
4.5多点测量及其自动检测 653
4.7应力测量中若干注意的问题 654
5.1疲劳片与断裂片 655
5特殊要求的应力测量 655
5.2温度条件下的测量 656
5.3高压下的测量 657
5.4旋转体的测量 659
5.5非金属材料的测量 661
2.1.1光的性质、自然光和偏振光 662
第3章光弹性法 662
1概述 662
2光弹性学的原理 662
2.1光学基础知识 662
2.1.2琼斯(Jones)偏振光矢量光强和光的干涉 663
2.1.3折射率、双折射和相对光程差 664
2.3光弹仪及其使用 665
2.3.1光弹仪的光路配置 665
2.2应力-光定律 666
2.3.2光弹仪的构造及其部件 666
2.4.1光弹仪屏上光强分布 667
2.3.3光弹仪的使用、调整和误差 667
2.4等差线和等倾线 667
2.4.2等差线(等色线) 668
2.4.4等倾线消除 669
2.4.3等倾线 669
2.4.5非整数级等差线条纹级数的精确确定 670
3二维和三维光弹性应力分析 671
3.1.2等差线识别和等倾线描绘 672
3.1二维光弹性 672
3.1.1光弹性法解平面应力问题 672
3.1.3主应力迹线 673
3.1.4光弹性平板材料的制作和材料条纹值的标定 674
3.2.1材料的冻结性能及其应力冻结机理 675
3.2三维光弹性冻结切片法 675
3.2.3三维应力分析方法 676
3.2.2三维光弹性效应及其应力-光定律 676
1.1全息照相 678
3.3光弹性散光法 678
第4章现代光测力学 678
1全息干涉法 678
1.2.2特点 679
1.2.1定义 679
1.1.2全息照相分类 679
1.2全息干涉法的定义、特点和方法 679
1.3实验装置与技术要点 680
1.2.3基本方法 680
1.4全息干涉条纹的解释技术 682
1.5.1ZF法作位移矢定量分析的基本方程 683
1.5全息干涉法位移定量分析的基本方程 683
2散斑法 684
1.6.4瞬态变形及应力波传播的测量 684
1.5.2FC法作位移矢定量分析的基本方程 684
1.6全息干涉法在机械工程材料测试方面的应用 684
1.6.1位移分析 684
1.6.2材料无损检测 684
1.6.3振动分析 684
2.2.2双曝光散斑图的分析 685
2.2.1双曝光散斑图与变形的关系 685
2.1激光散斑效应 685
2.1.1激光散斑的形成 685
2.1.2散斑的记录 685
2.1.3散斑的大小 685
2.2 散斑照相(单光束散斑干涉法) 685
2.3.1散斑场的叠加 686
2.3散斑干涉(双光束散斑干涉法) 686
2.2.3散斑照相应用 686
2.3.4电子散斑干涉仪(ESPI) 687
2.3.3双散斑场的干涉 687
2.3.2参考光与散斑干涉 687
2.4.2波前分割剪切干涉法 688
2.4.1振幅分割散斑剪切干涉 688
2.4散斑错位(剪切)干涉 688
2.6.1散斑照相条纹图的图像处理 689
2.6散斑方法中的数字图像处理技术 689
2.5白光散斑照相 689
3.1云纹条纹形成 690
3 云纹图 690
2.6.2散斑图的数字图像相关技术 690
3.2云纹条纹与位移关系 691
3.4干涉云纹法 692
3.3云纹条纹与应变关系 692
3.5影像云纹法 693
4.2.1测试仪器 694
4.2测试方法 694
4 红外应力图分析法 694
4.1基本原理 694
4.1.1热幅射基础 694
4.1.2热弹性效应 694
4.1.3应力变化和红外辐射变化的关系 694
4.3.1铝圆板试件的应力分析 695
4.3应用实例 695
4.2.2测试过程 695
4.4方法的优点和目前的局限性 696
4.3.5应力集中系数的计算 696
4.3.2裂纹扩展时应力波的传播 696
4.3.3裂纹尖端特征区和应力强度因子KI的确定 696
4.3.4塑性区范围的确定 696
5.2.2基本处理技术 697
5.2.1特点 697
5光测图像信息的采集与处理 697
5.1光测图像的特点 697
5.2数字图像处理的特点及基本技术 697
5.3.1光弹性条纹图的自动处理与分析 698
5.3应用实例 698
参考文献 699
5.3.2全息干涉法三维位移的自动处理分析 699
2塑料的力学性能 703
1概述 703
第9篇塑料力学性能试验 703
第1章概论 703
3.1试样的制备 705
3影响因素 705
1概述 706
第2章拉伸试验 706
3.2试样的状态调节及试验的标准环境 706
3.3加载速度的影响 706
3试样的标准型式 707
2.2夹持系统 707
2试验机及夹持系统 707
2.1试验机 707
4应力-应变曲线 709
7影响试验结果的主要因素 711
6结果的计算与表示 711
5试验方法 711
1概述 712
第3章压缩试验 712
5结果的计算 713
4试验方法 713
2试验机及压缩加载器 713
3试样的标准型式 713
6影响试验结果的主要因素 714
4试验条件 715
3试样 715
第4章弯曲试验 715
1概述 715
2试验原理 715
6.3弯曲弹性模量 716
6.2弯曲强度 716
5试验装置 716
6性能指标的测定 716
6.1挠度值的测定 716
7.3上压头半径对弯曲强度的影响 717
7.2跨厚比对弯曲强度的影响 717
7影响因素 717
7.1试验速度对弯曲强度的影响 717
2.1试验原理 718
2简支梁冲击试验 718
7.4试验温度对弯曲强度的影响 718
第5章冲击试验 718
1概述 718
2.3试验设备 719
2.2试样 719
2.5试验结果处理 720
2.4试验方法 720
3.3试验设备 721
3.2试样 721
3悬臂梁冲击试验 721
3.1试验原理 721
4.2试样 722
4.1试验原理 722
3.4试验方法 722
3.5试验结果处理 722
4落锤冲击试验 722
4.4试验方法 723
4.3试验设备 723
1概述 725
第6章硬度试验 725
5 影响冲击强度的因素 725
2.3试验方法 726
2.2试样 726
2洛氏硬度 726
2.1试验原理 726
3球压痕硬度 727
2.5洛氏α硬度 727
2.4试验结果表示 727
4邵氏硬度 728
1概述 729
第7章剪切试验 729
5影响试验结果的主要因素 729
2.3试验结果处理 730
2.2试验方法 730
2穿孔剪切试验 730
2.1试验原理 730
2.4影响因素 731
3.3单面压缩剪切试验 732
3.2双面压缩剪切试验 732
3 剪切试验的其他方法 732
3.1胶粘剂拉伸剪切强度试验 732
参考文献 733
2复合材料力学性能的特点 737
1概述 737
第10篇复合材料力学性能试验 737
第1章概论 737
3复合材料力学性能试验的重要性 738
2基体性能的测试 739
1概述 739
4复合材料力学性能试验的发展及其应用 739
第2章基体、纤维及界面的力学性能测定 739
2.2树脂浇铸体拉伸试验 740
2.1树脂浇铸体力学性能试验总则 740
2.3树脂浇铸体的压缩试验 741
2.4树脂浇铸体的弯曲试验 742
2.5树脂浇铸体的剪切性能试验 743
2.6树脂浇铸体性能简介 745
3.1纤维纱线的拉伸性能测定 746
3纤维性能的测试 746
3.2玻璃纤维机织物性能的测定及纤维性能的其他测试方法 749
3.3几种纤维的基体性能 750
4.1纤维拔出试验 751
4界面性能的测定 751
4.2纤维埋置试验 752
4.5改善界面性能的一些方法 753
4.4微压入试验 753
4.3微粘接试验 753
2.2试样状态调节和试验环境条件 754
2.1试样 754
第3章复合材料基本力学性能试验 754
1概述 754
2复合材料性能试验方法总则 754
3.1板状试样的拉伸 755
3 拉伸性能的测试 755
2.3试验设备 755
2.4试验结果 755
3.2环状试样的拉伸 760
3.3管状试样的拉伸 761
4.1柱状试样的压缩 762
4 压缩性能的测试 762
4.2板状试样的压缩 763
5弯曲性能的测试 765
4.3管状试样的压缩 765
5.1板条形试样的弯曲 766
5.2环形试样的弯曲试验 767
6剪切性能的测试 768
6.1层间剪切试验 768
6.2面内剪切试验 771
第4章复合材料特殊力学性能测试 772
1概述 772
2疲劳性能试验 772
2.1基本概念 772
2.2试验原理及步骤 773
3蠕变和持久强度试验 774
3.1基本概念 774
3.2试验原理及步骤 775
4冲击性能试验 776
4.1基本概念 776
4.2试验原理 777
4.3试样制备 777
4.4特点与限制 778
参考文献 778
2.1实际使用试验 783
2橡胶性能试验 783
2.2成品试验 783
2.3实验室试验 783
1概述 783
第1章概论 783
第11篇橡胶力学性能试验 783
1概述 784
2常温拉伸性能 784
第2章拉伸性能 784
2.1裁刀 785
2.5加载速度 786
2.4环境温度 786
2.6打磨 786
3高温拉伸性能 786
2.3压延方向 786
2.2试样尺寸 786
4伸长疲劳 787
5拉伸耐寒系数 787
第3章压缩性能 788
1概述 788
6弹性模量 788
2恒定形变压缩永久变形 789
3静压缩 790
4压缩疲劳 790
第4章硬度 791
1概述 791
5压缩耐寒系数 791
2.1影响因素 792
2.2硬度计校正 792
2邵尔硬度 792
3橡胶国际硬度 793
4赵氏硬度和邵坡尔硬度 793
1概述 794
第5章撕裂性能 794
2直角形撕裂 794
6硬质橡胶硬度 794
5海绵硬度 794
4裤形撕裂 795
5小试样撕裂(德尔夫特试样) 795
3新月形撕裂 795
第6章粘接性能 796
1概述 796
2拉伸粘合强度 797
3剥离粘合强度 798
4剪切粘合强度 799
5抽出粘合强度 800
参考文献 802
附录 803
附录一Monte-Carlo法模拟随机载荷时间历程的BASIC程序 803
附录二常用物理量法定计量单位换算关系表 805
附录三kgf·mm-2换算成N·mm-2(MPa)对照表 809
- 《市政工程基础》杨岚编著 2009
- 《激光加工实训技能指导理实一体化教程 下》王秀军,徐永红主编;刘波,刘克生副主编 2017
- 《工程静力学》王科盛主编 2019
- 《中央财政支持提升专业服务产业发展能力项目水利工程专业课程建设成果 设施农业工程技术》赵英编 2018
- 《化学反应工程》许志美主编 2019
- 《绿色过程工程与清洁生产技术 张懿院士论文集精选 上》《绿色过程工程与清洁生产技术》编写组编 2019
- 《软件工程》齐治昌,谭庆平,宁洪编著 2019
- 《高等教育双机械基础课程系列教材 高等学校教材 机械设计课程设计手册 第5版》吴宗泽,罗圣国,高志,李威 2018
- 《化学工程与工艺专业实验指导》郭跃萍主编 2019
- 《天水师范学院60周年校庆文库 新工科视域下的工程基础与应用研究》《天水师范学院60周年校庆文库》编委会编 2019
- 《钒产业技术及应用》高峰,彭清静,华骏主编 2019
- 《现代水泥技术发展与应用论文集》天津水泥工业设计研究院有限公司编 2019
- 《异质性条件下技术创新最优市场结构研究 以中国高技术产业为例》千慧雄 2019
- 《Prometheus技术秘笈》百里燊 2019
- 《中央财政支持提升专业服务产业发展能力项目水利工程专业课程建设成果 设施农业工程技术》赵英编 2018
- 《药剂学实验操作技术》刘芳,高森主编 2019
- 《林下养蜂技术》罗文华,黄勇,刘佳霖主编 2017
- 《脱硝运行技术1000问》朱国宇编 2019
- 《催化剂制备过程技术》韩勇责任编辑;(中国)张继光 2019
- 《信息系统安全技术管理策略 信息安全经济学视角》赵柳榕著 2020