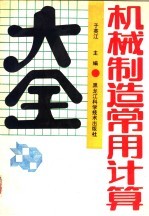
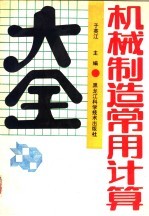
机械制造常用计算大全PDF电子书下载
- 电子书积分:13 积分如何计算积分?
- 作 者:于英江主编
- 出 版 社:哈尔滨:黑龙江科学技术出版社
- 出版年份:1992
- ISBN:7538817727
- 页数:399 页
(三)切断、成形车削和车刀副偏角φ 1
19.蜗杆螺牙沿分度圆柱上法向齿厚?n 1
18.蜗杆螺牙沿分度圆柱上轴向齿厚Sx 1
(一)切削速度计算(车刀的副偏角φ 1
五、米制锥螺纹尺寸(GB1415—78) 3
关系 3
螺纹厚度偏差a与螺纹中径偏差b的 3
11.工作极限负荷下的高度或长度H 3
七、30°锯齿形螺纹(JB923—66)牙形尺寸 3
六、梯形螺纹(GB784—65)牙形尺寸 3
三、55°圆锥管螺纹尺寸 3
四、60°圆锥螺纹尺寸 3
二、55°圆柱管螺纹尺寸 3
一、普通螺纹计算公式 3
第一章 螺纹计算 3
第一篇 机械零件设计计算 3
目录 3
1.轴向载荷 4
(一)单个螺检的计算 4
螺纹联接的计算 4
第二章 螺纹联接计算 4
2.横向载荷 7
(二)螺栓组的受力分析 7
1.载荷垂直于联结的接合面,其合力通过接合面的形心 7
2.载荷作用在联接的接合面内,并通过螺栓组的形心 7
3.联接的载荷作用在联接接合面内的转矩T 7
4.联接的载荷倾复力矩M 7
2.半圆键 8
4.切向键 8
3.楔键 8
一、键联接的强度校核公式 8
1.平键 8
第三章 键、花键、销及过盈联接的计算 8
二、花键联接的强度校核 9
三、销联接的强度校核 9
1.圆柱销 9
四、圆柱面过盈联接的计算 9
2.圆锥销 9
1.传递负荷所需的最小压力Pmin计算公式 9
2.零件不产生塑性变形所容许的最大压力Pmax的计算公式 10
3.传递负荷所需要的最小过盈的计算公式 11
4.零件不产生塑性变形所容许的最大过盈δmax计算公式 12
5.选择配合种类的计算公式 12
6.装拆力Fy计算公式 13
7.装配温度tr或tl计算公式 13
8.包容件外径增大量△d2计算公式 18
9.被包容件内径减小量△d1计算公式 18
五、圆锥面过盈联接的计算(液压装拆) 18
六、螺母压紧的圆锥面过盈联接计算 19
七、弹性环联接的轴向压紧力Fy和内环与轴的配合面间的压力P的计算 19
1.单剪 20
2.挤压强度 20
1.剪切强度 20
2.双剪 20
三、铆钉数量Z的计算公式 20
2.构件受压 20
1.构件受拉 20
一、被铆件的横剖面面积A(mz)计算公式 20
第四章 铆接计算 20
二、铆钉直径d,(m)计算公式 20
五、受拉(或压)的不对称剖面的填角侧焊缝计算公式 21
九、受转矩作用的填角焊缝计算公式 21
八、受弯矩作用的填角焊缝计算公式 21
七、受弯矩作用的填角侧焊缝计算公式 21
六、受拉(或压)的填角组合焊缝的计算公式 21
四、受拉(或压)的填角侧焊缝计算公式 21
三、受拉(或压)的填角端焊缝计算公式 21
二、受弯矩作用的对接焊缝计算公式 21
一、受拉(或压)的对接焊缝计算公式 21
第五章 焊接计算 21
第六章 机械传动计算 22
一、传动运动和动力计算中的几个常用公式 22
1.效率计算公式 22
2.传动比计算公式 22
3.转矩计算公式 22
4.圆周力计算公式 22
6.初定中心距ao 23
7.初算胶带长度Lo 23
5.带速v 23
8.实际中心距a 23
9.小带轮包角a1 23
4.大带轮计算直径d2 23
3.小带轮计算直径d1 23
2.确定胶带型号 23
1.功率P计算公式 23
二、三角胶带传动的设计计算 23
10.单根胱带传递的功率Po 25
11.单根胶带传递功率的增量△Po 25
12.三角胶带根数Z 25
13.单根胶带初张力Fo 25
14.对轴的作用力Q 25
15.带轮的结构和尺寸 26
三、平型传动胶带的设计计算 26
1.小带轮直径d1 26
2.大带轮直径d2 26
4.中心距a 27
3.带速v 27
5.胶带长度L 28
6.小带轮包角a1 28
7.曲挠次数u 28
8.带厚δ 28
9.带的截面积A 28
10.带宽b 28
11.作用在轴上的力Q 28
四、同步齿形带传动设计计算 28
1.计算功率Pc 28
2.模数m 29
3.小带轮齿数Z1 29
6.大带轮节圆直径d2 30
7.带速v 30
5.大带轮齿数Z2 30
4.小带轮节圆直径d1 30
9.带长Lo及其齿数Z 30
8.初定中心距ao 30
五、同步齿形带带轮的计算公式 31
4.顶圆直径da 31
3.节圆直径d 31
2.节距p 31
1.齿形角α 31
14.作用在轴上的力Q 31
13.带宽b 31
12.单位带宽的离心拉力Fc 31
11.小带轮啮合齿数Zn 31
10.实际中心距a 31
14.轮齿宽B 32
13.齿顶圆角半径ra 32
12.齿根圆角半径rf 32
11.根圆齿槽宽wf 32
10.根圆直径df 32
9.齿槽深h 32
8.顶圆齿槽宽wa 32
7.径向间隙C 32
6.齿侧间隙j 32
5.顶圆齿距po 32
第七章 套筒滚子链传动的计算 33
一、v≥0.6m/s时链传动的设计步骤和方法 33
1.小链轮齿数Z1 33
2.传动比i 33
4.张紧轮或多轴传动中任一从动链轮齿数Zi 33
5.初定中心距αo 33
6.计算功率Pc 33
7.链节距P 33
8.验算小链轮轴孔最大直径dhmax 33
3.大链轮齿数Z2 33
9.作用在轴上的压力Q 34
10.链条节数Lp 34
11.链条长度L 35
12.中心距a 35
13.链速v 36
二、v<0.6m/s的低速链设计计算方法 36
三、套筒滚子链链轮 36
1.滚子链链轮主要尺寸 36
3.简化端面齿形 39
四、链传动的张紧 39
2.以张紧装置张紧 39
1.调整中心距张紧 39
一、外啮合标准直齿、斜齿(人字齿)圆柱齿轮传动几何尺寸及侧隙检验尺寸计算公式 40
第八章 渐开线圆柱齿轮传动的计算 40
9.中心距a 40
8.齿根圆直径df 40
7.齿顶圆直径da 40
6.齿全高h 40
5.齿根高hf 40
4.齿顶高ha 40
3.分度圆直径d 40
2.压力角α或αx 40
1.模数m(或mn) 40
(一)几何尺寸计算 40
5.公法线跨齿数R 41
6.公法线长度Wk或Wkn 41
4.固定弦齿高?c或?cx 41
直齿轮 41
(一)直齿轮主要几何参数的计算 41
二、外啮合变位直齿斜齿(人字齿)圆柱齿轮几何尺寸计算公式 41
2.分度圆弦齿高?a或? 41
1.分度圆弦齿厚?或?n 41
10.齿数比u 41
(二)侧隙检验尺寸计算 41
3.固定弦齿厚?c或?ca 41
1.已知Z1、Z2、m、a′求x∑及△y′ 49
7.全齿高h 53
1.已知Z1、Z2、ma(mt)、β、α′,求x?∑及△yn 53
(一)斜齿(人字齿)轮主要几何参数的计算 53
斜齿(人字齿)轮 53
(三)直齿轮侧隙检验尺寸(选用一组) 53
9.齿根圆直径df 53
8.齿顶圆直径da 53
4.节圆直径d′ 53
6.齿根高hf 53
5.齿顶高ha 53
3.分度圆直径d 53
2.齿数比u 53
1.模数m 53
(二)直齿轮主要几何尺寸计算公式 53
2.已知Z1、Z2、m、x∑求a′及△y 53
2.已知Z1、Z2、mn(mt)、β、xn∑(xt∑),求a′及△yn 56
6.齿根高hf 57
7.全齿高h 57
5.齿顶高ha 57
8.齿顶圆直径da 57
9.齿根圆直径df 57
(三)斜齿(人字齿)轮侧隙检验尺寸(选用一组) 57
4.节圆直径d′ 57
3.分度圆直径d 57
1.模数mn 57
(二)斜齿(人字齿)轮主要几何尺寸计算公式 57
2.齿数比u 57
(一)直齿轮主要几何参数的计算 58
8.齿顶高ha 58
7.全齿高h 58
6.齿根圆直径df1、df2 58
5.齿顶圆直径da1、da2 58
三、内啮合圆柱齿轮(标准与变位、直齿与斜齿)几何尺寸计算公式 58
直齿轮 58
4.节圆直径d′ 58
1.已知Z1、Z2、m、α′求x∑及△y 58
2.已知Z1、Z2、m、x∑求α′及△y 58
(二)直齿轮主要几何尺寸计算公式 58
1.模数m 58
2.齿数比u 58
3.分度圆直径d 58
(三)直齿轮侧隙检验尺寸(选用一 59
组) 59
斜齿(人字齿)轮 59
(一)斜齿(人字齿)轮主要几何参数的计算 59
1.已知Z1、Z2、mx(mt)、β、α′,求x?∑及△yn 59
2.已知Z1、Z2、mn(mt)、β、xn∑(xt∑),求d′及△yn 60
6.齿根圆直径dt1、df2 61
7.全齿高h 61
5.齿顶圆直径da1、da2 61
8.齿顶高ha 61
(三)斜齿(人字齿)轮侧隙检验尺寸(选用一组) 61
2.齿数比u 61
4.节圆直径d′ 61
3.分度圆直径d 61
1.模数mn 61
(二)斜齿(人字齿)轮主要几何尺寸计算公式 61
2.齿数Z 62
1.齿数比u 62
(二)圆柱齿轮主要参数的选择 62
5.转矩T 62
4.轴向力F′x 62
3.径向力F′r 62
2.节圆上的圆周力F′t 62
1.分度圆上的圆周力Ft 62
(一)圆柱齿轮的作用力计算 62
四、圆柱齿轮传动的设计计算 62
3.模数m 63
4.螺旋角β 63
5.齿宽系数φ 63
(三)圆柱齿轮主要尺寸的初步确定 63
八、锯齿形螺纹公差(根据JB923— 66
(四)圆柱齿轮齿面接触疲劳强度与齿根弯曲疲劳强度校核计算 66
1.计算公式 66
2.计算中的有关数据及各系数的确定 72
(五)圆柱齿轮开式齿轮传动的特点 73
8.变位系数x 76
17.节锥顶点到轮冠距离AK 76
16.齿顶圆直径da 76
15.齿根圆锥角δf 76
14.齿顶圆锥角δa 76
13.齿顶角θn 76
12.齿根角θf 76
11.齿顶间隙C 76
10.齿根高hf 76
9.齿顶高ha 76
2.链轮端面齿形(根据GB1244— 76
7.周节p 76
6.齿宽b 76
5.锥距R 76
4.节锥角δ 76
3.大端模数m 76
2.齿数Z 76
1.分度圆直径d 76
(一)标准及高变位直齿圆锥齿轮传动几何尺寸计算 76
一、圆锥齿轮传动的几何尺寸计算 76
第九章 圆锥齿轮传动的计算 76
4.节锥角δ 77
3.大端模数m 77
2.齿数Z 77
1.分度圆直径d 77
(二)孤齿圆锥齿轮传动的几何尺寸计算(∑=90°,α=20°) 77
21.齿角(供刨齿用) 77
20.分度圆弦齿高?a 77
19.分度圆弦齿厚? 77
18.大端分度圆弧齿厚S 77
5.锥距R 78
6.齿宽b 78
7.周节P 78
8.工作齿高h′、全齿高h 78
9.齿顶高ha 78
二、圆锥齿轮传动的设计计算 79
19.齿侧间隙jn 79
18.大端分度圆弧齿厚S 79
17.节锥顶点到轮冠的距离At 79
15.齿根圆锥角δf 79
(一)圆锥齿轮的作用力计算 79
14.齿顶圆锥角δa1 79
13.齿顶角θa 79
12.齿根角θf 79
11.齿顶间隙C 79
10.齿根高hf 79
16.齿顶圆直径da 79
1.平均分度圆上的圆周力 79
2.径向力 79
3.轴向力 82
(二)初步确定主要尺寸 82
1.直齿及零度齿 82
2.βm=30°~35°的孤齿 82
(三)圆锥齿轮传动疲劳强度校核 83
2.齿根弯曲疲劳强度 84
1.齿面接触疲劳强度 84
3.公法线长度Wk 86
2.公法线跨齿数R 86
1.弦齿深? 86
(二)测量尺寸计算 86
11.全齿高h 86
10.齿根圆直径df 86
9.齿顶圆直径da 86
7.重合度ε 86
8.分度圆直径d 86
5.齿宽b 86
4.螺旋角β 86
3.端面模数mt 86
2.法面模数ma 86
1.中心距a 86
(一)单圆弧齿轮几何尺寸计算 86
一、单圆弧齿轮的几何计算 86
第十章 圆弧齿轮传动的计算 86
6.轴向齿距Px 86
二、单圆弧齿轮传动的强度计算 87
(一)主要尺寸的初步确定 87
5.螺旋线波度的波长I 87
4.齿根圆斜径Li 87
(二)齿面接触疲劳强度与齿根弯曲疲劳强度的校核计算 88
1.计算公式 88
2.式中各符号的意义 88
5.齿根圆直径df 90
4.齿顶圆直径da 90
3.分度圆直径d 90
2.螺旋角β 90
1.齿数Z 90
(四)双圆弧齿轮传动几何尺寸计算 90
3.多对齿啮合系数计算公式 90
1.同一工作齿面上两接触点间距离qTA2.多点啮合系数计算公式 90
(三)双圆弧齿轮的啮合特点 90
4.最小齿宽计算公式 90
6.轴向齿距Px 91
7.齿宽(人字齿轮半齿宽)b 91
6.变位系数x 92
13.蜗杆节圆直径d′1 92
12.蜗杆分度圆直径d1 92
10.蜗杆齿根高hf 92
9.蜗杆齿顶高ha 92
8.圆弧齿蜗杆轴截面齿廓圆弧半径p 92
7.蜗杆轴截面齿形角a 92
11.径向间隙c 92
4.蜗杆的直径系数q 92
3.蜗杆齿数Z2 92
2.蜗杆头数Z1 92
1.中心距a′ 92
一、圆柱蜗杆传动的几何尺寸计算 92
第十一章 蜗杆传动的计算 92
5.蜗轮端面模数mt 92
24.蜗轮顶圆直径da2 93
2.普通圆柱蜗杆传动强度计算 93
1.齿上力的分析 93
二、圆柱蜗杆传动承载能力的计算 93
28.蜗轮齿根圆弧半径Rf2 93
27.蜗轮齿顶圆弧半径Ra2 93
26.蜗轮轮缘宽度b 93
25.蜗轮最大外圆直径dw2 93
20.蜗杆齿厚测量高度?a 93
23.蜗轮根圆直径df2 93
22.蜗轮节圆直径d′2 93
21.蜗轮分度圆直径d2 93
17.蜗杆螺旋长度L 93
16.蜗杆分度圆螺旋导角γ 93
15.蜗杆齿根圆直径df1 93
14.蜗杆齿顶圆直径da1 93
3.圆弧齿圆柱蜗杆传动接触强度计算公式 94
4.蜗杆传动的效率及散热计算 94
4.蜗杆头数Z1 96
1.中心距a 96
3.蜗轮齿数Z2 96
2.传动比i 96
(一)圆弧面蜗杆传动几何尺寸计算 96
三、圆弧面蜗杆传动 96
11.齿根高hf 97
21.蜗杆工作包角之半φw 97
5.蜗轮齿顶圆直径da2 97
6.蜗轮宽度b 97
7.形成圆直径db 97
8.蜗轮端面模数mt 97
9.径向间隙和根部圆角半径C=γ 97
10.齿顶高hx 97
12.蜗轮分度圆直径dt2 97
13.蜗轮齿根圆直径df2 97
14.蜗杆分度圆直径d1 97
15.蜗杆喉部齿顶圆直径da1 97
16.蜗杆喉部齿根圆直径df1 97
17.蜗杆齿顶圆弧半径Ra1 97
18.蜗杆齿根圆弧半径Rf1 97
19.周节角τ 97
20.蜗杆包容蜗轮齿数Z′ 97
27.蜗杆喉部螺旋导角γm 98
23.蜗杆最大根径dj1max 98
24蜗杆最大外径da1max 98
25.蜗轮最大外径da1max 98
26.蜗轮顶部圆弧半径Ra2 98
28.分度圆压力角α 98
29.蜗轮法面弦齿厚?n2 98
30.蜗轮弦齿高?a2 98
31.蜗杆喉部法面弦齿厚?n1 98
32.蜗杆螺牙入口修正量△f 98
33.蜗杆弦齿高?a1 98
22.蜗杆工作部分长度Lw 98
8.人口修缘时中心距再增加量△′? 99
6.蜗杆螺牙入口修缘量△′f 99
7.修缘长度对应角度值φf 99
5.变参数修形形成圆直径dbo 99
9.入口修缘时蜗杆轴向偏移量△x 99
(三)圆弧面蜗杆传动承载能力计算 99
(二)直线圆弧面蜗杆变参数修形计算 99
4.变参数修形中心距ao 99
3.传动比增量系数Ki 99
2.变参数修形传动比io 99
1.蜗杆螺旋人口修形量△f 99
34.肩带宽度t 99
4.NN型 101
3.WW型 101
2.NW型 101
1.NGW型 101
一、常用的行星传动型式及其主要特点 101
第十二章 行星传动的计算 101
5.N型 102
6.NGWN型 102
7.两级NGW型 102
二、NGW型行星传动的设计 103
1.齿数的选择 103
2.行星传动齿轮的计算要点 103
三、摆线针轮行星传动几何尺寸计算 103
四、摆线轮齿面接触强度计算 103
六、输出机构圆柱销的强度计算 104
2.三支点的针齿计算 104
1.二支点的针齿计算 104
五、针齿销的弯曲强度和刚度计算 104
1.齿轮减速器箱壳尺寸 109
二、齿轮、蜗杆减速器结构尺寸 109
一、两级圆柱齿轮减速器 109
第十三章 减速器的计算 109
2.蜗杆减速器箱壳尺寸 111
3.普通圆柱蜗杆减速器蜗轮轴计算转矩 112
4.选用NGW型行星减速器时,应根 113
据使用条件计算 113
第十四章 螺旋传动的计算 120
一、滑动螺旋传动的设计计算 120
1.耐磨性 120
3.螺杆强度 120
2.验算自锁 120
5.螺母体强度 121
6.螺杆的稳定性 121
7.螺杆的刚度 121
4.螺牙强度 121
8.驱动力矩Ta 122
9.效率η 122
二、滚动螺旋传动的设计计算 122
1.用载荷和角速度计算平均载荷Fm 122
2.用载荷计算和角速度计算 122
6.稳定性验算一校核临界载荷Fcr 125
9.效率η 125
8.驱动力矩Ta 125
7.螺杆系统的刚度验算δs/s 125
5.螺杆强度计算σc 125
4.按静载荷计算Coa 125
3.寿命计算 125
三、滚动螺旋副的主要几何尺寸 126
1.螺纹滚道 126
2.螺杆 126
3.螺母 126
第十五章 轴的计算 127
一、轴径的初步估算 127
二、精确校核计算 127
三、轴的刚度计算 129
1.轴的扭转刚度计算 129
2.轴的弯曲刚度计算 135
第十六章 滚动轴承的计算 137
一、滚动轴承的选择计算 137
1.滚动轴承的寿命计算 137
二、滚动轴承的极限转速 139
三、推力轴承和推力向心轴承的最小轴向负荷 139
1.推力球轴承 139
2.滚动轴承静负荷计算 139
2.推力向心球轴承 140
3.推力滚子轴承 140
(二)径向滑动轴承的pv值的验算 141
2.pv值验算 141
(四)平面推力轴承的计算 141
(三)径向滑动轴承润滑方式的选择 141
1.比压p的验算 141
(一)径向滑动轴承的压强p的验算 141
一、非液体摩擦轴承 141
第十七章 滑动轴承的计算 141
二、液体动压轴承 148
(一)径向轴承 148
1.性能计算 148
2.参数选择 152
(二)推力轴承 153
1.固定瓦推力轴承 153
2.摆动瓦推力轴承 154
三、液体静压轴承 155
(一)单腔平面油垫计算 155
1.单腔平面油垫的流量和液阻 155
2.各种节流器的流量和液阻计算 155
1.毛细管节流静压轴承计算 156
(二)对油垫计算 156
3.单腔平面油垫承载能力 156
4.单腔平面油垫刚度(以毛细管节流为例) 156
2.小孔节流静压轴承计算 158
3.双面薄膜反馈静压轴承计算 159
4.滑阀反馈静压轴承计算 160
2.油进出口间的最高温升(近似计算) 161
1.功耗 161
(三)功耗及温升 161
1.计算转矩Tc 162
第十八章 联轴器的计算 162
2.CLZ型联轴器允许径向位移值αmax 162
3.联轴器强度的检验 162
联轴器的选择 162
1.公式计算法 163
一、压缩、拉伸弹簧的设计与计算 163
第十九章 弹簧的计算 163
2.已知弹簧直径D2(或D、D1)时的设计方法 163
(一)设计计算 163
3.查表法 166
(二)几何尺寸计算 166
1.材料直径d 166
2.弹簧中径D2 168
3.弹簧内径D1 168
4.弹簧外径D 168
5.有效圈数n 168
6.总圈数n1 168
7.节距p 168
8.自由高度或长度H0 168
10.工作高度或长度H 169
2.弹簧的疲劳强度验算 169
3.弹簧的共振验算 169
1.拉伸弹簧钩环强度验算 169
(三)验算 169
15.螺旋导角γ 169
14.弹簧展开长度L 169
13.间距δ 169
9.压缩弹簧高径比b 169
12.压缩弹簧压拼高度Hb 169
1.A型的计算公式 170
3.刚度RT 170
2.有效圈数n 170
1.材料直径d 170
(四)扭转弹簧设计公式 170
5.间距δ 170
6.节距p 170
7.自由长度H0 170
8.螺旋导角γ 170
9.弹簧展开长度L 170
二、碟形弹簧 170
(一)单片碟簧的计算公式 170
4.工作中弹簧的内径D′1 170
(二)许用应力 172
1.静载荷的许用应力 172
2.变载荷的许用应力 172
2.B型应用A型公式注意事项 172
第二十章 起重零件的计算 174
一、起重机构运转持续率 174
二、起重机钢丝绳直径选择 174
三、滑轮的最小许用名义直径的确定 174
1.卷筒名义直径 180
4.绳槽节距t 180
5.卷筒上有螺旋槽部分长L0 180
3.绳槽深度h 180
2.绳槽半径R 180
7.卷筒壁厚δ 180
(二)链轮节圆直径d′计算公式 180
(一)焊接链的选择 180
五、起重焊接链 180
6.卷筒长度 180
四、卷筒几何尺寸计算 180
六、吊钩组与滑轮组 181
(一)带式制动器的计算 182
3.棘爪的强度计算 182
八、制动器 182
4.棘爪轴的强度计算 182
2.棘轮齿的强度计算 182
1.棘爪下滑的条件 182
七、棘轮停止器 182
1.特点 183
2.缺点 183
(二)瓦块式制动器 183
(三)惯性负载的计算公式 186
(一)计算液压缸有效面积A 186
二、确定液压系统的工作压力 186
三、计算液压缸的有效面积或液压马达的排量 186
(一)外负载的计算公式 186
一、计算液压执行器的外负载 186
第二十一章 液压件的计算 186
(二)摩擦负载的计算公式 186
(二)液压泵的流量Qp 187
(一)阀的规格 187
七、选择控制阀 187
六、确定泵的驱动功率N 187
(三)液压泵的规格 187
五、确定液压泵的规格 187
(一)液压泵的工作压力Pp 187
(二)马达的流量 187
(一)缸的流量 187
四、计算执行器所需流量 187
(二)计算液压马达排量q 187
(二)阀的型式 188
八、非标准液压件的设计 188
九、管件及其它辅助装置的选择 188
十、液压系统的验算 188
(一)管路系统压力损失的计算 188
1.液流的类型 188
2.沿程压力损失 188
3.局部压力损失 188
4.管路系统总压力损失及压力效率 190
(二)发热温升的验算 190
1.系统发热的计算 191
2.系统散热的计算 191
3.热平衡条件 193
(三)液压冲击的验算 193
(四)管路系统容积损失和容积效率的计算 196
1.油流经平行平面间隙的泄漏量 196
3.油流径细长小孔或小直径沟槽的泄漏量(一般指L/d>4,层流) 197
4.油流经薄壁小孔的泄漏量(索流状态下) 197
2.油流经环形间隙的泄漏量 197
第二十二章 液压泵及液压马达的计算 198
1.液压泵与液压马达主要参数计算公式 198
2.理论排量计算公式 198
3.液压泵的技术性能 198
第二十三章 液压缸的计算 200
液压缸的设计计算 200
(一)液压缸设计计算步骤 200
(二)液压缸的作用能力、作用时间及储油量的计算 200
(三)液压缸壁厚计算 200
1.一般按薄壁筒公式计算 200
2.按厚壁筒公式计算 200
3.纵向弯曲强度验算 201
1.缸体和缸底的焊缝强度计算 201
(五)液压缸零件的连接计算 201
2.缸体与缸盖螺纹连接计算 201
2.纵向弯曲极限力计算 201
1.按强度条件验算活塞杆直径d(1≤10d时) 201
(四)活塞杆的计算 201
4.活塞与活塞杆螺纹连接计算 202
5.活塞杆与活塞肩部压应力验算 202
3.缸体与缸盖用法兰连接的螺栓计算 202
二、金属管管子壁厚δ的计算 210
一、管子内径的计算 210
第二十四章 管件的计算 210
2.油的加热及加热器 211
1.油箱的容量 211
二、油箱及油的加热和冷却 211
3.吸收冲击容积计算公式 211
2.吸收泵的脉动容积计算公式 211
1.作辅助动力源容积计算公式 211
一、蓄能器 211
第二十五章 其它辅助装置的计算 211
1.风冷翅片管式冷却器散热面积 212
三、油的冷却及冷却器 212
2.水冷式冷却器散热面积 212
第二十六章 气压传动的计算 214
一、空气的湿度 214
(一)绝对湿度x 214
(二)饱和绝对湿度xb 214
(三)相对湿度ψ 214
数)λ 215
(三)比热容C与导热率(导热系 215
(二)粘度 215
2.重度Y 215
1.密度ρ 215
(一)密度ρ与重度γ 215
二、空气的基本物理性质 215
(四)湿含量d 215
(二)理想气体状态变化的基本过程四、气体动力学的有关计算 216
(四)音速a、马赫数M对气流压缩性的影响 216
1.音速a 216
2.马赫数M 216
三、空气的状态变化 216
五、气体系统供气量与管道直径计算 216
(一)气体系统供气量计算 216
(一)理想气体状态方程及其修正 216
(二)压缩空气管道和压力降计算 218
1.管道内径计算 218
2.压降验算 218
第二十七章 气缸的计算 220
气缸的有关计算 220
(一)活塞杆上作用力和气缸直径的计算 220
(二)缸筒壁厚的计算 220
(三)活塞杆的计算 220
1.按强度条件计算活塞杆直径d(L≤10d) 220
2.按纵向弯曲极限力计算 220
(四)缓冲计算 220
(五)耗气量的计算 221
(六)冲击气缸 221
(一)明确设计依据 224
第二十八章 气动系统设计的计算 224
一、气动系统设计的基本内容及一般步骤 224
1.工艺动作要求 224
2.工作环境与结构条件 224
(二)设计气动回路 224
(三)选择设计执行元件 224
(四)选择控制元件 224
(五)气动辅件选用 224
(六)管道直径的确定、系统压降验算 224
(七)空压机选择 224
二、气动系统设计的几个注意问题 225
(二)用靠模板车锥体 229
(三)大头直径D计算公式 229
(四)小头直径d计算公式 229
二、车锥体的方法 229
(一)转动小刀架车锥体 229
(三)移动尾座车锥体 229
第二篇 机械切削计算 229
第二十九章 车工计算 229
一、锥体各部分尺寸的计算公式 229
(一)斜度M计算公式 229
(二)锥度K计算公式 229
3.用钢球测量圆锥孔的斜角 230
2.用块规和圆柱测量 230
4.用圆柱测量圆锥体的小端直径 230
(四)应用钢丝展开法车削圆锥体的计算 230
1.用正弦规测量圆锥体的斜角 230
(六)圆锥体表面的测量计算 230
计算 230
(五)车削圆锥表面时切削深度的 230
5.用钢球测量圆锥孔的大端直径 231
三、车螺纹 231
(一)车螺纹的刀尖宽度尺寸 231
1.车梯形螺纹的刀尖宽度尺寸 231
2.车模数蜗杆的刀尖宽度尺寸 231
3.车径节蜗杆的刀尖宽度尺寸 231
(二)挂轮计算 231
1.公制车床车公制螺纹 231
2.公制车床车时制螺纹 231
3.英制车床车公制螺纹 231
4.英制车床车时制螺纹 231
7.车多头螺纹 232
8.有走刀箱车床的挂轮计算 232
四、乱扣盘 232
5.用定数求各种丝杠的车床挂轮计算法 232
6.车蜗杆时的挂轮计算 232
五、冷绕弹簧心轴直径的计算 233
六、利用三爪卡盘车偏心 233
七、金属切削过程的计算 233
(一)切削用量的计算 233
1.切削深度计算公式 233
2.走刀量计算公式 233
3.切削速度计算公式 233
4.切削厚度计算公式 233
5.切削宽度计算公式 233
6.切削横截面积计算公式 233
7.机动时间计算公式 233
8.利用刻度盘控制切削深度 233
(二)切削力的计算 233
(三)车床功率的计算 234
(四)车床扭矩的计算 234
(五)刀具角度的计算 234
1.纵向前角和横向前角的计算 234
2.带圆弧形前面车刀的前角计算 234
3.切断刀的宽度计算 234
4.标准麻花钻前角的近似计算 234
5.圆形样板刀的计算 234
7.走刀运动与车刀角度变化关系的计算 235
八、车圆柱体和圆柱孔时的计算 235
(一)正多边形外接圆直径的计算公式 235
(二)圆弧直径的计算公式 235
(三)用圆柱(或钢球)测量圆柱体直径的计算 235
(四)用内卡钳测量圆柱孔直径时摆动距的计算 235
(五)用两个钢球测量圆柱孔直径时的计算 235
6.车刀安装位置与角度变化关系的计算 235
(一)车床所配备的配换齿轮 236
(六)小圆柱孔的测量计算 236
(七)尺寸链换算 236
九、车床的配换齿轮计算 236
1.无走刀箱车床 236
2.有走刀箱车床 236
(二)车床配换齿轮的啮合规则和调整 236
(三)无走刀箱车床的配换齿轮计算 236
1.公制车床的配换齿轮计算 236
2.铭牌上只有公制螺距和每英寸牙数,需加工工件是模数或径节螺纹时的配换齿轮计算 237
1.车特殊规格工件时的配换齿轮计算 237
(四)有走刀箱车床的配换齿轮计算 237
2.英制车床的配换齿轮计算 237
(五)在C618型车床上车削螺纹时的调整计算 238
(六)车削球面螺纹时的配换齿轮计算 238
第三十章 铣工计算 239
一、分度头的各种分度法 239
(一)单式分度 239
1.单式分度计算公式 239
2.单式分度表(分度头定数40) 239
(二)复式分度 239
(二)铣螺旋齿轮时的挂轮计算 240
(一)选择铣刀号数用假想齿数的计算公式 240
(四)差动分度 240
二、铣四方和铣六方 240
(一)铣四方计算公式 240
(二)铣六方计算公式 240
三、铣螺旋齿轮 240
(三)近似分度 240
四、铣伞齿轮 241
(一)铣刀号数的选择 241
1.计算法 241
2.铣伞齿轮用铣刀号数表 241
(二)伞齿轮的铣削方法 241
1.分度头不带转盘的铣削方法 241
(三)分度头法 242
(二)分度盘法 242
(一)刻度盘法 242
1.Z1装在分度头主轴上的挂轮计算 242
公式 242
2.分度头转盘的铣削方法 242
六、铣齿条 242
(二)飞刀主要尺寸及角度的计算 242
(一)挂轮计算 242
五、铣蜗轮 242
九、键槽的加工 243
(一)深度的计算 243
1.键槽深度 243
八、燕尾槽的测量与计算 243
2.键槽侧面深度 243
(二)对刀计算 243
七、铣圆球 243
(二)加工带柄圆球 243
(一)加工整球 243
算公式 243
2.Z1装在分度头挂轮轴上的挂轮计 243
(三)加工内球 243
1.用单角铣刀加工 244
(三)用双角铣刀铣螺旋齿刀槽 244
2.用双角铣刀加工 244
1.用单角铣刀加工 244
(二)铣前角不等于零的刀齿 244
2.用双角铣刀加工 244
十一、铣刀与铰刀的开齿计算 244
(一)铣前角为零的刀齿 244
扳角度铣削法 244
垂直铣削法 244
(二)铣凸轮的方法及有关计算 244
(一)凸轮曲线导程的计算 244
十、铣凸轮 244
(五)铣端面齿 245
4.用双角铣刀铣γ=0的刀齿 245
3.用单角铣刀铣γ=0的刀齿 245
(六)铣锥面齿 245
2.用双角铣刀铣前角γ>0的刀齿 245
1.用单角铣刀铣前角γ>0的刀齿 245
(四)刀齿齿底带有圆角时的开齿计算 245
(二)铣梯形齿和等边尖齿离合器 245
(一)铣直齿离合器 245
(三)铣锯齿形尖齿离合器 245
十二、齿式离合器的铣削加工与计算 245
十三、滚铣齿轮 246
(一)分齿挂轮计算公式 246
(二)走刀挂轮计算公式 246
(三)差动挂轮计算公式 246
(四)滚铣大质数齿轮(以Y38为例)1.滚铣大质数正齿轮时各组挂轮计算 246
2.滚铣大质数螺旋齿轮时各组挂轮计算 246
第三十一章 磨工计算 247
第三十二章 拉削计算 248
一、拉削力 248
二、拉削功率 248
二、攻丝前钻孔用钻头直径 250
(五)切削宽度 250
(四)切削厚度 250
1.公制螺纹 250
2.英制螺纹 250
三、钣金工展开图画法——射线法 250
(三)吃刀深度 250
(二)走刀量 250
(一)切削速度 250
一、钻削名词解释与计算公式 250
第三十三章 钳工计算 250
(十七)不锈钢板弯曲 252
(十六)无缝钢管弯曲 252
(十五)方钢弯曲 252
(十四)圆钢弯曲 252
(十三)扁钢弯曲 252
(十二)碳钢板弯曲 252
(十一)钢槽以Y0—Y0轴内弯 252
(十)槽钢以Y0—Y0轴外弯 252
(九)槽钢以X0—X0轴弯曲 252
(八)工字钢以W0—X0轴弯曲 252
(七)工字钢以Y0—Y0轴弯曲 252
(六)不等边角钢大边内弯 252
(五)不等边角钢小边内弯 252
(四)不等边角钢大边外弯 252
(三)不等边角钢小边外弯 252
(二)等边角钢内弯 252
(一)等边角钢外弯 252
一、型材、管材最小弯曲半径R的计算公式 252
第三十四章 弯曲与铆接计算 252
三、铆钉杆的长度计算 253
(十八)不锈圆钢弯曲 253
(十九)不锈耐酸钢管弯曲 253
二、弯曲前毛坯长度的计算 253
1.确定齿轮加热时的等效面积S 257
(一)加热功率的确定 257
(二)淬火加热时间的估算 257
2.加热功率的估算 257
电热规范的选择 257
第三篇 热处理计算 257
第三十五章 感应加热全齿淬火的计算 257
第三十六章 弹簧热处理计算 258
一、弹簧片正应力最大值计算 258
二、卷簧最大切应力值计算 258
第三十七章 轧辊的热处理计算 259
一、轧锟在水中停留的时间T 259
二、轧锟淬火加热移动速度计算 259
二、吃刀运动 263
四、切削速度对耐用度的影响 263
三、走刀运动 263
第三十八章 切削用量的确定 263
一、主运动 263
第四篇 专用机床设计与制造计算 263
五、吃刀深度和走刀量对耐用度的影响 264
六、切削速度的计算 264
七、机床功率的校验公式 264
3.计算法 265
1.类比法 265
2.实验确定法 265
一、机床功率的确定 265
第三十九章 机床主传动功率的确定 265
二、切削力的确定 266
(一)采用切削测力仪测定 266
(二)测机床电动机功率计算 266
第四十章 机床生产率的计算 267
一、单件工时的计算 267
二、机床生产率的计算 267
二、进给系统中快速移动功率的计算 268
一、圆柱齿轮传动的简易计算方法 268
第四十一章 零部件设计计算 268
第四十二章 丝杠螺母传动的计算 269
一、载荷不大、精度较高的螺旋磨损 269
计算 269
二、高精度机床丝杠的刚度验算 269
三、螺杆的稳定性验算 269
第四十三章 轮轮机构的设计 270
第四十四章 滚动导轨的计算 271
一、滚动导轨的摩擦力计算 271
二、滚动导轨的计算 271
(二)接触刚度计算 271
(一)接触强度的计算 271
第四十五章 手腕运动的驱动力计算 272
一、摩擦阻力矩M摩的计算 272
二、偏置力矩M偏的计算 272
三、惯性力矩M惯的计算 272
第四十六章 手臂的驱动力计算 273
一、手臂水平伸缩时 273
二、手臂升降时 273
三、手臂水平左右摆动时 273
第五篇 材料力学计算 277
第四十七章 轴向拉伸和压缩计算 277
一、拉杆横截面上正应力σ计算公式 277
二、虎克定律 277
三、杆内变形能 277
四、材料在拉伸(压缩)时的许用应力 277
三、铆钉的拉伸强度计算 279
二、铆钉的挤压强度计算 279
四、材料的剪切虎克定律 279
第四十八章 剪切计算 279
一、铆钉的剪切强度计算 279
(四)综合考虑几何、物理、静力学三方面的结果 280
1.强度条件 280
二、等直圆杆在扭转时的变形和杆内的变形能计算公式 280
(五)当ρ等于横截面半径r时,剪应力达到的最大值 280
三、圆杆在扭转时的强度条件、刚度条件 280
(三)静力学方面 280
(二)物理方面 280
(一)几何方面 280
一、等直圆杆在扭转时的应力 280
第四十九章 扭转计算 280
2.刚度条件 281
四、密圈螺旋弹簧计算 281
1.簧杆内的应力 281
2.弹簧的变形 281
3.簧杆的强度条件 281
五、组合截面的主形心惯性矩的计算 281
第五十章 梁的内力一剪力与弯矩 282
一、基本概念 282
二、剪力与弯矩的计算 282
四、梁的剪应力强度校核 283
第五十一章 梁的应力 283
一、纯弯曲时的梁的正应力 283
二、纯弯曲时正应力的强度条件 283
三、梁的剪应力 283
第五十二章 应力状态理论基础计算 284
一、复杂应力状态下一点处的最大应力 284
二、在复杂应力状态下一点处的主应变广义虎克定律 284
三、在复杂应力状态下一点处的比能 284
第五十三章 强度理论 285
一、最大拉应力理论 285
二、最大伸长线应变理论 285
三、最大剪应力理论 285
四、形状改变比能理论 285
弹性模量 286
1.弹性模量 286
2.剪切弹性模量 286
3.体积弹性模量 286
4.泊松比 286
第五十四章 弹性计算 286
第六篇 机械制造工艺理论计算 289
第五十五章 机械加工精度计算 289
一、主轴平均静刚度K,计算公式 289
二、刻度盘转过几格,刀具移动△L?两者间的关系式 289
2.在机械加工中,从加工精度观点出发,工艺系统刚度的概念 290
3.动刚度Ko 290
二、接触刚度 290
一、工艺系统的刚度 290
第十六章 工艺系统刚度及受力变形计算 290
1.刚度的一般概念 290
三、在加工过程中,刀具(或工件)一般温升估算公式 291
五、板类工件单面加工时的热变形计算 291
四、长圆柱体类工件加工时的热变形计算 291
六、热膨胀引起的测量误差公式 291
二、工艺系统中刀具(或工件)的散热能力估算公式 291
一、车削时切削热Q的计算公式 291
第五十七章 工艺系统的热变形计算 291
第五十八章 机械加工表面质量计算 292
一、微观不平度+点高度R计算公式 292
二、磨削区的总发热量计算公式 292
第五十九章 接合表面的发热计算 293
一、机械传动的发热计算 293
二、轴承的发热计算 293
第六十章 技术经济与价值分析计算 294
一、产品设计的成本估算 294
1.费用的组成 294
2.产品制造费用H的估算 294
二、工艺成本的计算 295
1.一种零件(或一道工序)的全年工艺成本计算 295
2.工艺方案所需的单位产品的工艺成本Cm?计算 295
第七篇 机械制造企业生产 299
组织计算 299
第六十一章 企业生产过程计算 299
一、工序的大量系数计算公式 299
二、顺序移动方式加工一批零件加工周期的计算 299
三、平行移动方式加工一批零件加工周期的计算 299
四、平行顺序移动方式加工一批零件加工周期的计算 299
五、装配线的时间损失率计算 299
六、流水线生产节拍r的计算 299
七、单一对象流水线组织设计和有关的计算 299
八、多对象流水线的组织设计和有关计算 301
十、网络计划技术时间值的确定 302
九、成组零件批的加工周期TG.T计算 302
第六十二章 企业生产技术准备计算 304
一、设计方案的机器成本计算 304
二、设计方案的经济效果分析 304
三、工艺装备的设计计算 304
四、工艺方案的经济效果分析 305
第六十三章 价值工程的应用计算 306
一、成本系数的计算 306
二、价值系数的计算 306
三、活动成果的评价 306
第六十四章 生产技术计划的计算 307
一、准备工作周期的计算 307
二、决定生产能力的基本因素计算 307
三、生产能力的计算 307
四、在制品结存量的计算 309
三、指数平滑法 310
二、加权移动平均法 310
第六十五章 产品短期需要量预测的计算 310
一、简单平均法 310
第六十六章 机械制造业的均衡生产的计算 311
一、一种产品均衡率 311
第六十八章 设备管理与工具管理的计算 311
二、多种产品的均衡率 311
1.节拍 312
一、大量生产期量标准的制定 312
2.在制品占用量定额 312
二、成批生产期量标准的制定 312
1.批量和生产间隔期 312
第六十七章 期量标准的计算 312
4.在制品占用量 313
2.生产周期 313
3.生产提前期 313
二、设备最小年平均寿命周期费用法 314
三、修理工作定额 314
1.修理周期 314
一、有关设备状况及利用指标的计算 314
2.一级保养间隔期和二级保养间隔期 315
3.修理复杂系数 315
四、储备量定额 316
1.备件制造(或订购)经济批量 316
2.最小储备量、订货点、最大储备量计算 316
五、工具需要量计算 316
六、工具周转储备量计算 316
三、误差的计算 319
五、应用对数计算选配机床挂轮的几种实例 319
(一)普通车床的挂轮计算 319
1.缺少127牙齿轮时的挂轮计算 319
1.挂轮的啮合条件 319
四.选配机床挂轮的一般知识 319
2.解决所选挂轮组不能啮合的方法 319
二、对数的运算法则 319
2.复式轮系 319
1.单式轮系 319
一、速比的计算 319
第六十九章 挂轮的常用计算 319
第八篇 挂轮计算 319
2.调整挂轮比抵消热处理后的伸长变形 320
(二)万能铲齿车床螺距、差动挂轮的计算 320
(三)万能铣床铣削螺旋齿轮的挂轮计算 321
(四)插齿机插削质数齿轮分齿挂轮的计算 321
(五)滚齿机差动挂轮的计算 321
(六)齿轮磨床滚切挂轮的计算 321
1.磨正齿轮滚切挂轮的计算 321
2.磨螺旋齿轮滚切挂轮的计算 321
(七)刨齿机滚切挂轮的计算 321
(八)螺纹磨床挂轮的计算 321
第九篇 机械加工工艺计算 325
第七十章 常用计算 325
一、车螺纹、蜗杆时的挂轮计算 325
二、分度头的分度计算 325
三、直齿圆柱齿轮及斜齿圆柱齿轮尺寸计算 325
四、周节、模数、径节的计算公式和互换 325
五、直齿圆锥齿轮尺寸计算 326
六、蜗杆、蜗轮尺寸的计算 326
二、锥度心轴的计算 327
三、常用夹紧型式所需夹紧力的计算 327
6.由于定位销与孔之间的配合间隙引起工件或顶板等有回转一角度的可能,由此所形成的定位误差计算公式 327
4.菱形销上圆孤部分宽度计算公式 327
5.定位销宽度计算公式 327
第七十一章 定位夹紧方面的计算 327
一、定位销误差的计算 327
1.定位销与工件最小配合间隙计算公式 327
2.由于中心距离的公差,孔对于定位销的可能移动量计算公式 327
3.菱形销圆孤部分与孔壁间最小间隙计算公式 327
3.三角形螺纹 328
2.梯形螺纹 328
2.行程比is计算公式 328
四、常用斜楔夹紧机构的计算 328
1.扩力比ip计算公式 328
3.夹紧力W 328
五、螺旋夹紧型式夹紧力的计算 328
1.方牙螺纹 328
七、铰链夹紧机构的计算 329
2.偏心的夹紧行程 329
六、圆偏心夹紧力及夹紧行程计算 329
1.偏心的夹紧力 329
2.液性塑料夹紧用套筒 330
1.弹簧夹头 330
八、常用弹性夹紧元件夹紧力的计算 330
>0°) 331
一、车削 331
第七十二章 切削用量计算 331
(二)切削力计算公式(车刀的副偏角φ1>0°) 332
式 332
=0°时车削速度和切削力计算公 332
三、钻削 333
二、刨削 333
(一)切削速度的计算公式 333
(二)轴向力P、扭矩M及动力N的计算公式 334
四、铣削 335
(一)硬质合金铣刀 335
(二)高速钢W18Cr4V铣刀 336
五、螺纹加工 338
(一)车螺纹的切削速度计算公式 338
(二)车螺纹的切削速度计算公式 338
(三)车螺纹的动力计算公式 338
(四)旋风切削螺纹的进给量及切削速度计算公式 339
(五)切削速度计算公式 339
(六)丝锥攻丝的切削速度计算公式 339
(七)铰螺纹的切削速度计算公式 340
(八)铣螺纹的切削速度计算公式 340
七、磨削 341
(一)外圆磨的切削用量计算公式 341
六、齿轮、花键加工 341
(五)磨内圆的切削用量计算 342
(四)切入式无心磨的切削动力计算 342
(六)磨平面的切削用量计算 342
(三)无心外圆磨切削用量的计算 342
(二)磨外圆的切削动力计算 342
第七十三章 机动时间的计算 347
一、钻削 347
二、车削 350
三、刨削、插削 351
四、螺纹加工 351
五、齿轮加工 353
六、磨削 357
1.外圆磨 357
2.无心磨 358
3.内圆磨 358
5.平面磨 359
6.珩磨 359
4.内圆无心磨 359
一、零件的静平衡和动平衡计算 360
第七十四章 装配工艺的计算 360
三、不可拆连接装配的计算 361
二、可拆连接装配的计算 361
四、滚动轴承的装配计算 362
第七十五章 零件表面冷压加工的计算 363
一、滚轮滚压加工的滚压压力计算 363
二、螺纹滚轧的计算 363
1.滚轧螺纹工件的毛坯直径的计算 363
2.螺纹滚轧工具的计算 363
3.滚轧工具的螺纹形状的计算 364
第七十六章 机械加工车间和装配车间的设计计算 365
一、折合系数K的计算 365
二、设备数量的计算 365
六、各种毛坯、半成品或中间仓库的面积计算 366
(一)机械加工车间主要数据和技术经济指标 366
七、车间技术经济指标 366
1.主要数据 366
五、装配车间所需的生产工人数的计算 366
四、机械加工车间所需的生产工人数的计算 366
三、工作位置的计算 366
1.主要数据 367
(二)装配车间主要数据和技术经济指标 367
2.技术经济指标 367
2.技术经济指标 367
(二)拉刀直径和砂轮直径之间的关系式 371
(三)齿距及同时工作齿数的计算 371
3.多边形拉刀加工时拉削余量的确定 371
2.花键拉刀加工时拉削余量的确定 371
(四)容屑槽的有关计算 371
1.容屑槽各个参数与齿距t之间的大致关系 371
2.容屑槽的容屑系数计算 371
1.圆孔拉刀加工时拉削余量的确定 371
(一)拉削余量的确定 371
一、拉刀切削部分的设计计算 371
第七十七章 拉削刀具的计算 371
第十篇 复杂刀具设计计算 371
(一)前角及后角 372
(二)齿距及齿形 372
(三)齿数 372
3.最小槽深hmin 372
4.最大齿升量Sxmax 372
(五)拉刀的分屑 372
(六)切削部分的长度 372
二、拉刀校准部分的设计计算 372
(三)前导部 373
(二)颈部及过渡锥 373
(四)后导部 373
(五)支托部及压光环尾部 373
(一)柄部 373
三、拉刀光滑部分的设计计算 373
(四)校准部分的直径及长度 373
(二)拉刀强度校核 374
(一)拉削力可用下式计算 374
(三)拉床拉刀验算 374
五、拉削力的计算及拉刀强度校核 374
四、拉刀的总长度及成套拉刀的设计计算 374
第七十八章 普通式圆孔拉刀的计算 375
第七十九章 小模数齿轮滚刀设计计算 382
一、小模数齿轮滚刀设计步骤与计算 382
二、小模数齿轮滚刀主要技术条件 383
第八十章 直齿锥齿轮定装滚刀 387
一、直齿锥齿轮定装滚刀设计计算 387
二、直齿锥齿轮定装滚刀的主要技术条件 389
第八十一章 链轮滚刀设计计算(加工非渐开线齿轮形的刀具) 392
一、链轮滚刀设计计算步骤 392
二、链轮滚刀的主要技术条件 394
第八十二章 行星摆线齿轮铣刀设计计算一、摆线齿轮铣刀设计计算 395
二、行星摆线齿轮铣刀的主要技术条件 395
第八十三章 钟表齿轮齿形尺寸的计算 397
主要参考文献 399
4.推力向心球面滚子轴承 1440
- 《计算机网络与通信基础》谢雨飞,田启川编著 2019
- 《大学计算机实验指导及习题解答》曹成志,宋长龙 2019
- 《中国制造业绿色供应链发展研究报告》中国电子信息产业发展研究院 2019
- 《计算机辅助平面设计》吴轶博主编 2019
- 《计算机组成原理解题参考 第7版》张基温 2017
- 《云计算节能与资源调度》彭俊杰主编 2019
- 《Helmholtz方程的步进计算方法研究》李鹏著 2019
- 《高等教育双机械基础课程系列教材 高等学校教材 机械设计课程设计手册 第5版》吴宗泽,罗圣国,高志,李威 2018
- 《超强大·英语10000+常考单词+常用搭配,随身带随时用》朱晓琴 2019
- 《智能制造高技能人才培养规划丛书 ABB工业机器人虚拟仿真教程》(中国)工控帮教研组 2019
- 《钒产业技术及应用》高峰,彭清静,华骏主编 2019
- 《现代水泥技术发展与应用论文集》天津水泥工业设计研究院有限公司编 2019
- 《异质性条件下技术创新最优市场结构研究 以中国高技术产业为例》千慧雄 2019
- 《Prometheus技术秘笈》百里燊 2019
- 《中央财政支持提升专业服务产业发展能力项目水利工程专业课程建设成果 设施农业工程技术》赵英编 2018
- 《药剂学实验操作技术》刘芳,高森主编 2019
- 《林下养蜂技术》罗文华,黄勇,刘佳霖主编 2017
- 《脱硝运行技术1000问》朱国宇编 2019
- 《催化剂制备过程技术》韩勇责任编辑;(中国)张继光 2019
- 《信息系统安全技术管理策略 信息安全经济学视角》赵柳榕著 2020