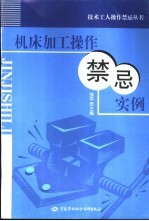
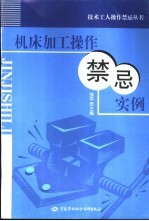
机床加工操作禁忌实例PDF电子书下载
- 电子书积分:12 积分如何计算积分?
- 作 者:徐平田主编
- 出 版 社:北京:中国劳动社会保障出版社
- 出版年份:2003
- ISBN:7504537063
- 页数:320 页
2.在夹具随主轴一起转动的机床上加工大批量小型工件时,不宜采用组合夹具 1
3.夹具使用保养四不准 1
第一章 机床加工操作基础 1
一、机床夹具 1
1.单件或小批量工件不宜制作专用夹具 1
5.选择定位方式不可忽视夹具制造成本 2
4.定位和夹紧的概念不可混淆 2
6.重复定位一般是不允许的 3
9.安装刚性较差的工件时,不可忽视辅助支承的应用 5
8.定位支承点之间的距离不能太小 5
7.欠定位是绝对不允许的 5
11.选择粗基准的四不能 6
10.辅助支承不应消除工件的自由度 6
13.选择定位基准一般不宜违反基准重合原则 7
12.选择定位基准时不宜违反基准统一原则 7
14.确定夹紧力的禁忌六则 10
18.采用螺旋压板机构时,不可忽视杠杆原理 11
17.采用单个螺旋夹紧机构时,不宜直接用螺钉头部压紧工件 11
15.切削力大或批量大的工件不宜直接用斜楔夹紧 11
16.斜楔的升角不宜太大或太小 11
20.不宜随便选取圆偏心夹紧机构的工作段 12
19.被夹压表面尺寸变化大的工件及振动较大的场合,不宜采用圆偏心夹紧机构 12
21.平行式多件夹紧机构不宜采用刚性压板 13
24.一夹一顶安装轴类零件时,卡盘夹持部分不能过长 14
23.小锥度心轴应用三不宜 14
22.连续式多件夹紧机构不宜装夹过多的工件 14
26.V形铁两工作面之间的夹角不宜过大或过小 15
25.端面与内孔垂直度较差的套类零件不宜采用普通圆柱心轴安装 15
1.选择量具时不可忽视量具精度与工件精度的适应性 16
二、量具、量仪的使用与保养 16
3.量具、量仪维护保养十不准 18
2.不可忽视环境温度对测量精度的影响 18
4.钢直尺使用保养五忌 19
7.用内卡钳测量孔径时,摆动距不能过大或过小 20
6.内卡钳在千分尺上取尺寸时,卡钳脚与千分尺测量面的接触不能过松或过紧 20
5.卡钳调整三忌 20
9.用游标卡尺测量时,不能用力推挤尺框 21
8.游标卡尺维护保养三不准 21
12.千分尺没校对零位不宜使用 22
11.用深度游标卡尺或深度千分尺测量时,测量基准面不能凹凸不平 22
10.用游标卡尺测量时,两测量爪对应点的连线不应与被测尺寸方向相倾斜 22
16.外径千分尺维护保养六不准 23
15.用外径千分尺测量时,不能拧动微分筒上的滚花部分 23
13.使用千分尺时,测微螺杆轴线不应与被测尺寸方向相倾斜 23
14.不宜用手握住千分尺的尺架进行测量 23
18.内测千分尺使用与保养三不准 24
17.内径千分尺使用与保养五项禁忌 24
20.公法线千分尺应用三不能 25
19.螺纹千分尺应用四项禁忌 25
22.不能忽视百分表与被测表面的位置关系 26
21.百分表维护保养五项禁忌 26
25.极限量规使用与保养六项禁忌 27
24.扭簧比较仪维护保养三不准 27
23.内径百分表使用与保养四项禁忌 27
27.量块维护保养七不要 28
26.使用量块组时量块数量不宜过多 28
29.用三针法测量螺纹中径时,量针直径不可任意选取 29
28.正弦规维护保养三不准 29
31.用三针法测量螺纹升角大于4°的螺纹中径时,测量值不可不进行修正 30
30.用三针法对螺纹中径进行精确测量时,量针直径不宜偏离最佳值 30
32.牙数很少的螺纹不宜采用三针测量 31
33.用单针法测量螺纹中径时,不应忽视螺纹大径误差对测量结果的影响 32
34.万能角度尺应用禁忌五则 33
3.为降低切削温度,不可随意选择切削用量 34
2.刀具角度对切削力的影响不可忽视 34
三、切削加工的基本理论与常识 34
1.刀具材料对切削力的影响不可忽视 34
5.刀具产生磨粒磨损的原因不可不究 35
4.刀具几何参数对切削温度的影响不可忽视 35
8.切削速度对刀具寿命的影响不可忽视 36
7.刀具产生相变磨损的原因不可不究 36
6.刀具产生扩散磨损的原因不可不究 36
10.不可忽视刀具安装对工作角度的影响 37
9.切削加工中不宜产生带状及粒状切屑 37
11.不能忽略进给运动对刀具角度的影响 38
12.为获得良好的断屑效果,不可随意选择切削用量 40
13.精加工时不宜产生积屑瘤 41
14.抑制积屑瘤生成的六不宜 42
15.减轻加工硬化的四不宜 43
17.减小工件表面粗糙度的十不宜 44
16.减小工件残余应力的禁忌三则 44
18.高速切削的概念不应模糊 45
19.零件表面的加工顺序不能随意安排 46
21.不可忽视工件的热变形 47
20.不能将工件的某一表面粗、精加工全部完成再加工其他表面 47
23.不可忽视自激振动对切削加工的影响 48
22.不可忽视强迫振动对切削加工的影响 48
24.对光滑工件进行尺寸检验时,不应按图样标注的极限尺寸作为验收界限 49
25.不应在工件温度较高时进行测量 50
1.高速钢刀具不可用于高速切削 51
四、刀具材料、刀具几何参数与刀具刃磨 51
26.加工批量大、形状复杂的工件时,不应采用工序集中原则 51
27.加工批量小、重量大及各表面相互位置精度高的工件时,不宜采用工序分散原则 51
4.加工铸铁等脆性金属不宜使用YT类硬质合金刀具,加工碳素钢不宜使用YG类硬质合金刀具 52
3.YG类与YT类硬质合金刀具牌号中的数字含义不应模糊 52
2.硬质合金刀具不宜用于低速切削 52
8.金刚石刀具不宜切削含碳的黑色金属材料 53
7.不宜用含钛的刀具加工含钛的金属材料 53
5.粗加工及带有冲击性的场合不宜采用含硬质相多的硬质合金刀具,精加工不宜采用含硬质相少的硬质合金刀具 53
6.陶瓷刀具不宜用于粗加工或带有冲击性的切削 53
12.刀具后角一般不应取负值 54
11.刀具前、后角的大小对刀具耐用度及加工质量的影响不可忽视 54
9.金刚石刀具的工作温度不宜过高 54
10.刀尖角的概念不应模糊 54
16.加工塑性金属时刀具的前、后角不宜过小,加工脆性金属时刀具的前、后角不宜过大 55
15.粗加工时刀具的前、后角不宜过大,精加工时刀具的前、后角不宜过小 55
13.高速钢刀具不宜取负值前角 55
14.硬质合金及陶瓷刀具的前、后角不宜过大 55
19.刀具刃倾角对实际前角的影响不可忽视 56
18.带有冲击性的切削不宜采用较大的刀具前角和后角 56
17.加工强度和硬度高的材料时刀具的前、后角不宜过大,加工塑性大和硬度低的材料时刀具的前、后角不宜过小 56
23.不可忽视刃倾角对断屑的影响 57
22.工件刚性较差时,刀具刃倾角不宜取负值 57
20.粗加工、强力切削、断续切削及加工硬度高的材料时,刀具不宜取正值刃倾角 57
21.精加工时刀具不宜取负值刃倾角 57
25.断屑槽的反屑角不可过大或过小 58
24.刀具断屑槽的宽度不可过大或过小 58
28.为延长刀具寿命,主、副偏角不宜过大 59
27.为取得良好的断屑效果,刀具的主偏角不宜取小值 59
26.圆弧形断屑槽的圆弧半径和槽深不可过大或过小 59
33.刃磨刀具时,不宜随便选用砂轮磨料和砂轮硬度 60
32.刀具严重磨损时不可继续使用 60
29.工件刚性较差时,刀具的主、副偏角不宜过小 60
30.加工刚性差的工件时刀尖圆弧不宜过大 60
31.一般刀具的刀尖都不宜过尖 60
34.手工刃磨刀具八不准 61
35.鐾刀六不宜 62
1.切削液对切削加工的影响不可忽视 63
五、切削液 63
4.乳化液的浓度不宜过高或过低 64
3.切削液使用四不宜 64
2.选择切削液时,不能忽视切削液的特性 64
9.不宜用亚硝酸钠作为添加剂 65
8.使用含油性添加剂的切削液时,切削温度不宜超过200% 65
5.无机盐溶液中,碳酸钠的质量分数不应超过1/100 65
6.用含氯极压添加剂的切削液加工钢料时,切削温度不宜超过350℃ 65
7.不宜用含硫的切削液加工有色金属 65
13.切削液对孔类零件尺寸精度的影响不可忽视 66
12.断续切削及有振动的场合不宜选用低浓度的切削液 66
10.粗加工脆性材料时,一般不宜使用切削液 66
11.用硬质合金刀具切削时,不能断续浇注切削液 66
14.不宜用油基切削液进行冷却 67
1.不宜随意选择中心孔类型 68
一、轴类零件的车削 68
第二章 车削加工 68
2.钻削中心孔的六则禁忌 69
3.防止中心钻折断的五忌 70
5.采用后顶尖支顶时,忌尾座套筒紧固不牢 71
4.在两顶尖间装夹工件的四则禁忌 71
8.安装外圆车刀的五则禁忌 72
7.精度要求较高的工件不宜采用活顶尖支顶 72
6.用碳钢死顶尖安装工件时,工件转速不能过高 72
11.车削铸造毛坯零件时,切削深度不宜过小 74
10.用高速钢精车刀精车外圆时,切削速度不宜过高 74
9.用硬质合金车刀精车外圆时,精车余量不宜过大或过小 74
12.使用中心架安装工件的四则禁忌 75
14.跟刀架的支承爪不宜采用平面型 76
13.跟刀架支承爪对工件的压力不宜过大或过小 76
16.车削细长轴时,后顶尖不宜采用死顶尖 77
15.车削细长轴时,不宜采用两个支承爪的跟刀架 77
18.精加工后的细长轴不宜水平放置 78
17.车削细长轴时,选择刀具几何参数的四则禁忌 78
21.关于外圆产生锥度的五忌 79
20.细长轴毛坯料的弯曲度不宜过大 79
19.车削细长轴时,不宜采用自右向左的进给方式 79
22.外圆产生圆度误差的三项禁忌 80
2.直径大于30mm的孔不宜一次钻削完成 81
1.钻孔前,工件端面不宜有凸台 81
23.关于外圆表面粗糙度过大的六忌 81
二、套类零件的车削 81
6.钻孔伊始时进给量不宜过大 82
5.钻头在钻削过程中不宜停车 82
3.用麻花钻扩孔时进给量不宜过大 82
4.钻孔时尾座套筒轴线不应偏离主轴轴线 82
9.内孔车刀的刀杆截面尺寸不宜过小 83
8.安装内孔车刀的三则禁忌 83
7.钻削小孔时主轴转速不宜过低 83
12.使用中心架车削圆柱孔时,支承爪不可将工件支偏 84
11.车削平底孔的三则禁忌 84
10.内孔车刀的后角不宜过大 84
14.车削内孔的四项禁忌 85
13.车削通孔时车刀不宜采用负值刃倾角 85
15.安装内沟槽车刀的四项禁忌 86
17.装夹薄壁套类零件的三则禁忌 87
16.加工后的薄壁套类零件不宜平放 87
19.在车床上铰孔时的六则禁忌 88
18.车削薄壁套类零件的三则禁忌 88
20.在车床上铰孔时,尾座套筒轴线不应偏离主轴轴线 89
1.选择切断刀几何形状的七忌 90
三、切断、切槽与车端面 90
21.铰削不通孔时不宜选用正值刃倾角铰刀 90
2.切断刀安装四忌 91
3.切断的五项禁忌 92
6.平面切槽刀的两个副后面不可都磨成平面形 93
5.不可在没有保险装置的卡盘上使用反切刀 93
4.切断时,防止断面凹凸不平的四忌 93
9.使用右偏刀车削端面时的二项禁忌 94
8.车削端面时,刀尖不宜高于或低于工件回转中心 94
7.车削端面沟槽的二忌 94
1.采用倒顺车法车削螺纹时的三忌 95
四、螺纹和蜗杆的车削 95
3.采用直进法车削三角螺纹时,切削深度不宜过大 96
2.车削铸铁螺纹的三项禁忌 96
5.高速车削三角形外螺纹的六项禁忌 97
4.用高速钢车刀精车大螺距螺纹时,不宜采用直进法 97
8.精车铜螺纹时刀刃不宜太锋利 98
7.车削锯齿形螺纹的二项禁忌 98
6.安装螺纹车刀的三忌 98
11.刃磨小螺距方形螺纹车刀的二项禁忌 99
10.车削扩大导程螺纹时,不可任意选择主轴转速 99
9.重新安装的螺纹车刀不可在工件反转时对刀 99
13.用径向前角大于0°的车刀车削螺纹时,中滑板丝杠与丝母的间隙不能过大 100
12.用厚样板检查径向前角不为0°的螺纹车刀角度时,样板相对于水平面不应倾斜 100
14.车削内螺纹的八项禁忌 101
15.使用小滑板分头三忌 102
18.安装挂轮的四项禁忌 103
17.在车床上套丝的三忌 103
16.车削多头螺纹的三项禁忌 103
20.粗车梯形螺纹或蜗杆的四项禁忌 104
19.安装大模数轴向直廓蜗杆车刀时,不宜采用角度样板进行校正 104
1.用转动小滑板法车削圆锥时,小滑板镶条间隙不宜过大或过小 105
五、圆锥面的车削 105
5.车削圆锥表面时,刀尖不可高于或低于工件的回转中心 106
4.精加工以后的圆锥表面不宜有接刀 106
2.转动小滑板车削圆锥时,初调角度不宜小于圆锥半角 106
3.粗车第一件圆锥面时,切削深度不宜过大 106
6.宽刃车刀车削圆锥的六项禁忌 108
8.精车圆锥面时不宜盲目进刀 109
7.偏移尾座车削圆锥的四项禁忌 109
9.铰削圆锥孔的四项禁忌 110
10.用锥度量规检验锥度时,量规的转动量不宜超过半周 111
1.使用成形车刀的三忌 112
六、成形面车削及表面修饰加工 112
11.检验锥度的四项禁忌 112
3.摆动式靠模车削成形面三忌 113
2.靠模法车凸轮三忌 113
5.滚花加工七忌 114
4.靠板靠模应用二忌 114
8.锉刀修光成形表面的七忌 115
7.无法用后顶尖支顶的工件,滚花时伸出部分不宜过长 115
6.带滚花的薄壁零件不宜最后滚花 115
9.用砂布抛光的三项禁忌 116
12.用样板检验成形面时,样板的方向与工件轴线方向不宜歪斜 117
11.在车床上研磨工件时,研具与研磨表面之间的间隙不宜过大或过小 117
10.在车床上研磨工件时,选用研具材料的三不宜 117
2.偏心距较大的工件不宜采用双重卡盘安装 118
1.在三爪自定心卡盘上车削偏心工件时的三项禁忌 118
七、复杂零件的车削 118
5.偏心工件划线时的三项禁忌 119
4.车削偏心工件时,主轴转速不宜过高 119
3.车削偏心工件时,不能从最低点开始上刀 119
8.花盘端面不可外凸 120
7.花盘的垂直度误差不宜过大 120
6.在花盘上安装工件不可有偏重现象 120
11.车削曲轴的五项禁忌 121
10.用间接测量法确定偏心距时,不可按基准轴和偏心轴的标注尺寸计算 121
9.在花盘上加工工件时的三项禁忌 121
1.车削淬火钢时选择刀具几何参数的五不宜 122
八、难加工材料的车削 122
2.用硬质合金车刀切削淬火钢时,切削速度不宜过低 123
4.车削高锰钢时,选择刀具几何角度的三不宜 124
3.车削冷硬铸铁时,刀具的几何角度不宜过大 124
7.车削高强度钢时选择刀具几何角度的四不宜 125
6.不宜使用陶瓷刀具车削高强度钢 125
5.车削高锰钢时,选择切削用量的二项禁忌 125
8.车削不锈钢时,选择刀具几何参数四不宜 126
10.车削钛合金时,选择刀具几何角度的三项禁忌 127
9.车削不锈钢时选择切削用量的二忌 127
13.不宜使用硬质合金车刀车削纯镍 128
12.车削纯铜时,选择刀具几何角度的二不宜 128
11.加工钛合金时不宜干切削 128
16.不宜使用高速钢或硬质合金刀具车削玻璃钢 129
15.车削高温合金时,选择切削用量二忌 129
14.车削高温合金时,选择刀具几何角度的二项禁忌 129
18.车削橡胶零件的车刀,前角和后角不宜过小 130
17.车削工业塑料时的四忌 130
2.用压板装夹工件时的六项禁忌 131
1.工件在机用虎钳上安装时的四项禁忌 131
第三章 铣削加工 131
一、平面、连接面、斜面的铣削 131
4.圆柱铣刀安装时的几点禁忌 132
3.用圆柱铣刀铣平面时,选择铣刀的三不宜 132
7.用端面铣刀铣平面不宜采用顺铣 133
6.铣削平面时,不能忽视试铣削 133
5.在铣削过程中,不能中途停止工作台的进给运动 133
10.用硬质合金铣刀进行高速铣削时的三项禁忌 134
9.端面铣刀铣平面时,铣刀回转轴线与进给方向的垂直度误差不宜过大 134
8.端面铣刀的对称铣削法不适宜铣削窄长或较薄的工件 134
14.转动立铣头铣斜面时不可忽视的问题 135
13.用角度铣刀铣斜面时,不宜采用较大的进给量 135
11.铣削脆性材料时,防止铣削表面的边缘出现折角崩裂的禁忌 135
12.对表面有硬皮的毛坯件,不宜采用顺铣 135
15.角度铣刀不适宜加工较大的斜面 136
2.采用组合铣刀铣削T形阶台时,两把铣刀间距不应等于工件凸形宽度 137
1.采用三面刃铣刀铣阶台时,铣刀直径不宜过大 137
二、阶台、沟槽的铣削和切断 137
5.用盘形铣刀铣直角沟槽时的四忌 138
4.铣阶台时,不能忽视夹具与工件的校正 138
3.当阶台凸起部分尺寸精度要求较高时,不宜将工作台一次调整到位 138
7.键槽铣刀用钝后,不宜刃磨圆柱面上刀刃 139
6.成批加工轴件键槽时,如工件未经精加工,不宜采用虎钳装夹 139
10.铣键槽时,防止键槽上宽下窄的禁忌 140
9.防止键槽两侧面表面粗糙度过大的禁忌 140
8.用键槽铣刀钻进刀孔时,进给量不宜过大 140
13.防止锯片铣刀折断的五项禁忌 141
12.切断薄板料时,切开部位不宜在工作台T形槽的上方 141
11.采用机用虎钳装夹切断工件时,工件的伸出长度不宜太长 141
16.在铣床上切断时不容忽视的问题 142
15.切断刀的厚度不能随意选择 142
14.切断铣刀的直径不宜选得过大 142
18.防止T形槽铣刀折断的三项禁忌 143
17.铣削螺钉起口槽时,不能将工件螺纹夹伤 143
1.铣削直齿圆柱齿轮时,齿轮铣刀不能随意选择 144
三、螺旋槽及齿面的铣削 144
19.单件T形槽的铣削,不宜采用三面刃铣刀 144
20.用立铣刀铣削T形槽时,铣削深度不宜过大 144
3.铣齿轮时,不能忽视分度头的检查与校正 145
2.铣削直齿圆柱齿轮前,不能忽视对齿轮坯的检查 145
4.铣削直齿圆柱齿轮时,铣刀与齿轮坯中心位置不应偏斜 146
7.铣斜齿条时,工件倾斜装夹方法不适于铣削螺旋角较大的长齿条 147
6.横向移距法不适于铣削较长的齿条 147
5.铣削短齿条时,选择移距方法时不能忽视移距误差 147
9.铣斜齿圆柱齿轮时的三项禁忌 148
8.铣斜齿圆柱齿轮时,不能按实际齿数选择铣刀 148
13.用盘形铣刀在万能铣床上铣削螺旋槽时,铣刀与所铣齿槽不得产生干涉 149
12.铣直齿圆柱齿轮时,防止齿厚不等、齿距误差过大的三则禁忌 149
10.铣削齿轮时,调整分度头手柄不能随意摇动 149
11.铣直齿圆柱齿轮时,防止表面粗糙度过大的禁忌 149
15.采用指状齿轮铣刀铣削螺旋齿轮不可忽视的问题 150
14.对螺旋角较大的螺旋齿轮不宜采用扳转工作台的方法铣削 150
16.铣削圆锥齿轮时,不宜采用切痕对刀法 151
20.不宜采用圆柱齿轮铣刀代替圆锥齿轮铣刀铣削精度较高的圆锥齿轮 152
19.铣圆锥齿轮时,防止齿面表面粗糙度过大的禁忌 152
17.铣削圆锥齿轮时,防止齿厚尺寸超差的禁忌 152
18.铣削圆锥齿轮时,防止齿圈径向跳动超差的禁忌 152
23.高精度蜗杆不宜在铣床上加工 153
22.铣削圆锥齿轮时不宜从小端向大端铣削 153
21.用圆柱齿轮铣刀代替圆锥齿轮铣刀铣锥齿轮时,其小端模数不能超过2 153
25.铣蜗轮时,铣刀直径不能小于蜗杆直径 154
24.指状铣刀不宜加工小模数蜗杆 154
27.断续分齿飞刀展成法不宜加工精度较高或螺旋角较大的蜗轮 155
26.配偶蜗杆头数大于2的蜗轮不宜采用盘形铣刀加工 155
30.用飞刀加工蜗轮不宜采用径向进给 156
29.高精度齿轮不应在铣床上采用成形法加工 156
28.在卧铣上用连续分齿飞刀展成法铣削蜗轮时,分度头主轴转速不宜过高 156
31.铣削矩形牙嵌离合器时,铣刀宽度不宜过大或过小 157
33.铣削尖齿离合器时,双角铣刀的刀尖不得高于或低于主轴中心 158
32.铣削矩形齿离合器时,获得齿侧间隙的方法不可随意选用 158
35.铣削齿数较少的梯形收缩齿离合器时,不宜采用试切法对刀 159
34.铣削直径较小的偶数齿离合器,不宜采用盘形铣刀 159
37.防止一对离合器接触齿数太少或无法嵌入的五项禁忌 160
36.防止牙嵌式离合器齿侧工作面表面粗糙度过大的禁忌 160
1.用双角铣刀对前角γ0=0°的圆柱面直齿铣刀开齿时,其调整方法不应与单角铣刀相同 161
四、刀具的开齿 161
4.铣削圆柱刀齿螺旋槽时,铣刀切削方向不可随意选择 162
3.用双角铣刀铣削螺旋齿槽时,铣刀的小角度δ不宜过大 162
2.铣削圆柱螺旋齿槽不宜采用单角铣刀 162
5.铣削螺旋角较大的圆柱螺旋齿时,工作台旋转角度不应与被开齿铣刀的螺旋角相同 163
6.铣错齿三面刃铣刀螺旋齿槽时不可忽视的问题 164
8.对直齿端面齿刀具开齿时,铣刀的外径不宜过大 165
7.铣削滚刀螺旋槽时的禁忌三则 165
10.圆锥螺旋齿刀具开齿时,不宜将螺旋角选为定值 166
9.刀具端面齿开齿时,调整分度头倾角不能忽视刀具端面齿副偏角的影响 166
12.铣削直齿铰刀时,防止棱边尺寸偏差过大的五忌 167
11.铣削直齿铰刀的三项禁忌 167
16.铣削三面刃铣刀时,防止端面齿棱边宽度内外不一致的有关禁忌 168
15.铣削圆柱铣刀时,防止分齿不均的三则禁忌 168
13.铣削直齿铰刀时,防止前角偏差过大的四则禁忌 168
14.加工圆柱铣刀时,防止螺旋齿槽槽形误差过大的禁忌 168
19.铣削麻花钻齿槽时不可忽略的问题 169
18.铣削圆锥铣刀时,防止棱边宽度不一致的禁忌 169
17.铣削三面刃铣刀时,防止前刀面连接不光滑的禁忌 169
3.铣削直线螺旋面端面凸轮时,不可盲目对中心 170
2.用垂直法铣圆盘凸轮时,对刀位置不能忽视从动件位置的影响 170
五、成形面及难加工材料的铣削 170
1.用垂直法铣削凸轮时,铣刀的直径不能随意选择 170
6.铣削凸轮时,进刀和退刀不宜在加工状态下进行 172
5.铣削圆盘凸轮刀具的螺旋角不宜太小 172
4.铣削等速圆盘凸轮时,不应出现夹紧变形 172
9.对导程是大质数或带小数值的凸轮,不宜采用垂直法加工 173
8.凸轮上有几条不同导程的曲线时,不宜采用垂直法铣削 173
7.铣削等速圆盘凸轮时,不应出现顺铣 173
11.铣削凸轮时,防止凸轮升高量不正确的几项禁忌 174
10.凸轮从动件为摆动的圆柱滚子时,不能按理论曲线夹角计算有关参数 174
15.在圆转台上铣削曲线外形时,不能忽视曲线型面各部分的连接 175
14.铣削曲线外形时,不宜加注切削液 175
12.铣削凸轮时,防止凸轮工作型面形状误差过大的几则禁忌 175
13.铣削曲线外形时,不能忽视铣刀的选择 175
17.在用靠模铣削曲线外形时,靠模和滚轮之间的压力不宜过大或过小 176
16.用圆转台铣曲线外形时,校正中不能忽视圆转台和工作台的间隙方向 176
21.铣削球面时,铣刀轴线与工件轴线不应为异面直线 177
20.用立铣刀铣削内球面时,刀尖回转直径不能过大或过小 177
18.按划线手动进给铣曲线外形时,不能忽视模拟铣削 177
19.用附加靠模装置铣削曲线外形时,铣刀直径不能任选 177
22.铣削内球面时,铣刀刀尖运动轨迹不能偏离工件端面中心 178
25.在立式铣床上镗椭圆孔,不能用主轴套筒做伸缩来进行加工 179
24.铣削大质数直齿锥齿轮,不宜采用近似分度法进行分齿 179
23.铣削球面时,铣刀刀尖回转直径dc调整误差不宜过大 179
28.铣削高温合金类材料时,不宜选择硬质合金类刀具 180
27.铣削高锰奥氏体钢材料时,不宜选用钨钛钴类(YT)硬质合金铣刀 180
26.铣削不锈钢材料时,不宜采用逆铣 180
2.影响磨削厚度的因素不可忽视 181
1.磨削热对加工的影响不可忽视 181
第四章 磨削加工 181
一、磨削的基本知识 181
4.影响砂轮与工件接触弧的因素不可忽视 182
3.砂轮与工件的接触弧对加工的影响不可忽视 182
6.防止零件表面烧伤的五项禁忌 183
5.表面烧伤对零件使用寿命的影响不容忽视 183
9.选择工件圆周速度的八不宜 184
8.选择砂轮圆周速度的五不宜 184
7.光磨的行程次数不宜过多 184
10.选择进给速度的三不宜 185
12.不可忽视磨削用量对工件表面粗糙度的影响 186
11.选择磨削深度的五不宜 186
13.磨削余量不可过大或过小 187
3.砂轮硬度不应选得过高或过低 188
2.砂轮硬度与磨料硬度的概念不应混淆 188
二、砂轮及其使用 188
1.不能忽视砂轮磨料与工件材料的适应性 188
6.磨削导热性差的材料及散热体积小的工件时,不宜选择硬度高的砂轮 189
5.成形磨削时不宜选择硬度低的砂轮 189
4.选择砂轮硬度时不可忽视加工性质和磨削方式 189
9.选择砂轮硬度时不可忽视磨削用量 190
8.选择砂轮硬度时不应忽视砂轮与工件的接触弧长 190
7.选择砂轮硬度时,不应忽视工件材料硬度 190
11.选择砂轮组织的七不宜 191
10.断续磨削时不宜选用硬度低的砂轮,干磨时不宜选用硬度高的砂轮 191
14.树脂结合剂砂轮不宜在浓度较高的碱性切削液下使用 192
13.陶瓷结合剂砂轮不宜用于强烈振动的场合 192
12.选择砂轮粒度的六不宜 192
17.砂轮磨粒被磨钝后不宜继续使用 193
16.金刚石砂轮使用禁忌五则 193
15.橡胶结合剂砂轮不宜用于一般性的粗加工,不宜用油进行冷却 193
20.用金刚钻修整砂轮时,金刚石不宜过大或过小 194
19.砂轮外形失真后不宜继续使用 194
18.砂轮表面被堵塞后不宜继续使用 194
24.金刚钻的安装高度不应高于或等于砂轮中心 195
23.不能随意确定金刚钻的安装角度 195
21.焊接不牢的金刚钻不宜使用 195
22.金刚钻的安装位置不宜与磨削工件时的位置相差过多,刀杆不宜伸出过长 195
25.修整砂轮时不宜随便选择进给量 196
29.砂轮内孔与法兰盘的配合间隙不能过大或过小 197
28.未经检验的砂轮不能安装使用 197
26.用金刚钻修整砂轮时不能间断地浇注冷却液 197
27.修整砂轮时切去砂轮表面的厚度不宜太大或太小 197
32.紧固砂轮法兰盘时,不能将螺母依次拧紧 198
31.用法兰盘安装砂轮时,两个法兰盘的直径不能大小不等 198
30.用法兰盘装夹砂轮时,法兰盘的端面不宜直接与砂轮平面接触 198
34.新砂轮不能只进行一次平衡 199
33.直径较大的砂轮未经平衡不准使用 199
1.工件经热处理后,中心孔未经修研不宜进行磨削 200
三、外圆磨削 200
35.砂轮保管六忌 200
3.用两顶尖安装工件的八项禁忌 201
2.对要求特殊的工件不宜采用普通结构的中心孔 201
7.用纵磨法磨削时,砂轮超越工件端面的距离不能过长或过短 202
6.磨削高精度工件时不可忽视试磨 202
4.在磨床上不能使用活顶尖 202
5.前后顶尖连线与工作台运动方向之间的平行度误差不能过大 202
11.磨削光滑轴时不宜在轴的中间接刀 203
9.磨削刚性差的工件不宜采用切入法 203
8.用纵磨法磨削带台肩的外圆时,砂轮行至台肩时不宜立即换向 203
四、内圆磨削 204
1.内圆砂轮直径不宜太大或太小 204
13.防止外圆产生螺旋形痕迹的五项禁忌 204
12.用砂轮端面磨削轴肩时,进给量不能过大 204
2.内圆砂轮宽度不宜太宽或太窄 205
3.内圆砂轮的硬度不可过高或过低 205
6.在接长轴上安装砂轮的四项禁忌 206
5.使用接长轴的五不能 206
4.内圆磨削时不宜选择粒度细、组织紧密的砂轮 206
7.用黏结剂黏结内圆砂轮时的六项禁忌 207
8.用金刚钻修整内圆砂轮时的四项禁忌 208
9.不能随便选择内圆砂轮与工件的接触位置 208
11.用纵磨法磨内孔时,砂轮端面超出孔口的距离不能过长或过短 209
12.磨削间断表面内孔时的三项禁忌 209
10.用卡盘和中心架安装工件时,中心架支承爪不可将工件支偏 209
13.小直径深孔磨削五忌 210
14.磨削阶台孔时,工件调头安装的次数不宜过多 210
3.不宜用转动砂轮架的方法磨削大批量圆锥面 211
4.不宜用转动砂轮架的方法磨削圆锥母线较长的圆锥面 211
2.不能只依靠工作台(或头架)刻度来调整工件锥度 211
五、圆锥及细长轴磨削 211
1.不能用转动工作台的方法磨削圆锥角太大的圆锥面 211
6.试磨内圆锥时,工作台(或头架)最初的回转角度不宜小于圆锥半角 212
7.磨内圆锥时砂轮直径不能过大 212
5.磨削成批工件时,不宜用固定横向进给刻度的方法来控制圆锥尺寸 212
9.精磨内圆锥时的工作状态不能与调整锥度时的工作状态相差太多 213
10.磨削直径小且较长的内圆锥时,砂轮不宜过宽 213
8.转动砂轮架磨削内圆锥时,砂轮宽度不能小于圆锥母线长度 213
13.磨削细长轴时尾架顶尖不能顶得过紧 214
14.磨削高精度细长轴时,不宜采用单拨杆夹头装夹工件 214
12.细长轴经车削后,未经校直和消除应力处理不宜进行磨削 214
11.磨削细长轴时选择砂轮的四不宜 214
16.中心架对细长轴的压力不宜过大或过小 215
17.磨削细长轴时,使用中心架的数目不宜为偶数 215
15.细长轴在两顶尖上安装的时间不宜过长 215
1.精度要求高的平面不宜采用端面磨削方式 216
2.用倾斜磨头的方法磨削平面时,磨头倾斜角度不宜过大 216
六、平面及无心外圆磨削 216
18.磨削细长轴时工件转速不宜过高,磨削深度不宜过大 216
19.磨削细长轴时切削液流量不能太急 216
3.圆周磨削方式不适于大批量平面的粗磨 217
4.不宜专门为小批量工件修整阶梯砂轮 217
8.在电磁吸盘上安装定位基准面小且较高的工件时,不可忽视补牢措施 218
7.工件定位基准面横跨电磁盘导磁条的数目不宜太少 218
6.不能用力将工件从电磁吸盘上拖下来 218
5.较薄的工件不宜采用深度磨削法 218
9.平面磨削时,防止平面度和平行度超差的禁忌三则 219
11.无心外圆磨削采用纵磨法时,导轮的倾角不能过大或过小 220
12.无心外圆磨削时,调整托板位置的三项禁忌 220
10.无心外圆磨削时工件中心不能和磨削轮与导轮中心连线等高 220
13.用纵磨法磨削时,托板不能伸出磨削区太长 221
14.无心外圆磨削时,不允许将导板装偏 221
1.用展成法磨削球面时,砂轮中心不能高于或低于工件中心 222
2.修整成形砂轮时的禁忌三则 222
七、复杂工件磨削 222
5.磨齿余量不宜过大或过小 223
10.应用深度磨削法时,砂轮外圆表面形状不宜采取普通型 223
4.磨削齿轮时调整机床的三忌 223
3.磨削花键时,避免齿形误差过大的三忌 223
9.磨削长丝杠时,减少工件弯曲变形的五不宜 224
8.磨削精密丝杠时,不可忽视磨削热对螺距精度的影响 224
6.精度要求较高的螺纹不宜用多线砂轮磨削 224
7.磨削螺纹时不可忽视对线 224
12.用低熔点材料粘固薄片工件的三项禁忌 225
11.磨削薄片工件时,减少变形的措施不可忽视 225
10.小尺寸环形薄片工件不宜直接用电磁吸盘安装 225
14.刀具刃磨五不宜 226
13.磨削大型薄壁套时不宜采用普通冷却方式 226
16.刃磨滚刀时不可违反的三项原则 227
15.刃磨螺旋槽滚刀前面时的禁忌三则 227
18.偏心距较大的偏心工件不宜在四爪单动卡盘上磨削 228
17.刃磨拉刀前面时,砂轮半径不能大于拉刀前面锥形的曲率半径 228
3.插刀的前角和后角不宜过大 229
2.刃磨较小的插刀头时,不宜用手直接握住刃磨 229
第五章 刨削、插削加工 229
一、插削与刨削的基本知识 229
1.插削时,切削用量不宜过大 229
6.插削相同尺寸的铸铁和钢件键槽时,成形刀宽度尺寸不应相同 230
5.插削时,不宜选用整体式插刀 230
4.安装插刀时的四项禁忌 230
9.插削方孔时,不能按划线直接将方孔插至尺寸 231
8.采用斜垫铁装夹法插削倾斜面时,楔角不宜过大 231
7.插削工件两端面时,平行度超差的原因不可忽视 231
12.插削内齿轮的四项禁忌 232
11.插削双键槽时,相互位置不能偏移 232
10.插削时,产生振动与啃刀的原因不可不究 232
16.刨削时滑枕换向有冲击声不可不究 233
15.刨削时滑枕在长行程时有震荡声响的原因不可不究 233
13.刨削时,切削速度不宜过高 233
14.刨削时滑枕温度过高的原因不可不究 233
17.刨床上用压板搭压工件时的四项禁忌 234
2.刨平面时,防止吃刀一端形成倾斜倒棱面的禁忌四则 235
1.刨平面时,产生小沟纹或小阶台的原因不可忽视 235
18.刨削时,不宜用提高切削速度的方法来提高生产率 235
二、平面、垂直面、斜面及燕尾槽的刨削 235
4.刨削薄板或壳类工件的平面时,夹紧力不能过大 236
3.刨削平面时,避免平面局部凹陷的禁忌三则 236
6.精刨平面时,防止表面产生鱼鳞纹的四项禁忌 237
5.刨平面时,防止表面产生有规律直纹的五项禁忌 237
9.刨削平行度较高的工件时,不宜用平口钳直接装夹 238
8.不应忽视薄壁工件的安装刚性 238
7.精刨平面时,产生交叉纹的原因不可忽视 238
11.刨垂直面时,在平口钳上装夹工件的二项禁忌 239
10.平行面及互成直角关联面产生相互位置误差的原因不容忽视 239
13.垂直面与水平面不垂直的原因不可忽视 240
12.用偏刀进行粗刨和精刨垂直面时,刀杆偏斜角度不宜过大或过小 240
16.刨阶台工件时,内连接面不清根或清根过量的原因不可忽视 241
15.刨削较薄的工件端面时,不宜将工件平放在工作台上用垂直走刀方式来刨削 241
14.刨削时,垂直面与两侧面不垂直的原因不可忽视 241
19.刨削精度较高的斜面,不宜采用倾斜刀架法 242
18.精刨内斜面时切削速度不宜过高,进给量不宜过大 242
17.阶台与工件基准面不平行的原因不可忽视 242
23.刨削宽薄斜铁的五项禁忌 243
22.倾斜刀架法刨斜面时的四项禁忌 243
20.斜度较大的工件不宜采用斜垫铁安装 243
21.采用样板刀刨斜面时,切削用量不能过大 243
24.刨削较长的斜铁时,所需的垫铁和挤铁不能小于工件长度 244
28.燕尾形零件不宜用卡尺直接测量 245
27.刨削较小的燕尾形工件和大型燕尾形工件时,加工工艺不应相同 245
25.刨削斜面时,角度产生误差的原因不容忽视 245
26.刨削燕尾形工件时,粗、精刨刀的刀尖角不能相同 245
3.在刨床上切断时,工件安装的三项禁忌 246
2.在刨床上安装切断刀时的三项禁忌 246
三、切断、刨槽及刨削内表面 246
1.在刨床上切断不同刚性的工件,刀头宽度不应相同 246
5.在刨床上切断时,断面与相邻面不垂直的原因不可忽视 247
4.在刨床上切断工件时的五项禁忌 247
8.刨T形槽时,选择弯切刀几何尺寸的四项禁忌 248
7.在轴上刨削键槽时,不宜直接用平口钳装夹工件 248
6.宽度和精度要求不同的直沟槽刨削方法不应相同 248
10.刨T形槽时,弯切刀不应同其他刨槽刀的安装方法相同 249
9.刨T形槽时的三项禁忌 249
12.采用组合式弯头刀杆刨削内孔时,垂直刀杆的截面不宜过小,伸出不宜过长 250
11.刨T形槽时,产生误差的原因不可不究 250
15.刨削孔内键槽时,键槽宽度尺寸不合格的原因不可忽视 251
14.刨内孔键槽时,不能开动机床来调整刀具、工件及机床间的相对位置 251
13.用直刀杆刨削孔内表面时不宜采用刀头向下的安装方式 251
2.确定强力刨刀几何参数的六不宜 252
1.在刨床上不能用提高切削速度的方法来实现强力刨削 252
16.刨孔内槽时,表面粗糙度过大的原因不可忽视 252
四、强力刨、精刨及特种材料的刨削 252
4.强力刨削时,不应忽视切削用量对刀具耐用度的影响 253
3.采用强力刨削时的五项禁忌 253
6.用宽刃刀精刨平面时,不容忽视刨刀的对刀方法 254
5.强力刨削时,关于工艺系统刚性的四忌 254
10.刚性不同的刨床和工件,所用精刨刀的宽度不应相同 255
9.精刨铸铁工件时,严禁机油滴洒在加工表面上 255
7.未经研磨的刨刀,不宜用来精刨平面 255
8.精刨平面时,不允许中间停车或换刀 255
13.刨削不锈钢时的刀具材料及几何角度不应与普通刨刀相同 256
14.刨削不锈钢工件的四不宜 256
11.精刨精度很高的工件,不宜单靠刀架刻度来控制上刀量 256
12.精刨时,切削深度不能过大 256
17.刨削紫铜时,不应忽视刀具材料与刀具几何参数对工件材料的适应性 257
16.刨削淬火钢时,切削用量的选择不可不议 257
15.刨削淬火钢的刀具材料及几何角度不应与普通刨刀相同 257
3.形状复杂且尺寸较大的曲面不宜用成形刀刨削 258
2.用成形刀刨曲面时,进给量不能过大,切削速度不能过高 258
18.刨削铝合金工件的四项禁忌 258
五、复杂零件的刨削 258
1.刨曲面时,圆头刨刀的圆弧半径不能随意选择 258
8.装夹薄板工件时,不能用手锤敲打的方法来校正工件 259
7.装夹薄板工件时,夹紧力不能太大 259
4.修磨成形刀时,不能随便修磨刀具的后面 259
5.刨削大圆弧曲面时,不宜采用普通刨曲面的方法 259
6.刨削薄板工件的刨刀不应与普通平面刨刀相同 259
11.装夹大型薄板时,不能忽视辅助压板的应用 260
10.装夹薄板时,工件的侧面不应是毛坯表面 260
9.刨削薄板工件时,不宜采用普通装夹方法 260
14.检验键槽深度时,不宜用深度尺测量 261
13.刨细长轴键槽时,用压板压紧工件的先后顺序不容忽视 261
12.刨削细长轴键槽时,工件产生弯曲变形的原因不可忽视 261
17.刨削斜镶条时,产生废品的原因不可忽视 262
16.未经热处理的坯料不能用来制作大型斜镶条 262
15.装夹大型斜镶条时的禁忌四则 262
20.刨斜齿条时,齿条节线直线度及节线与齿条基面平行度超差的原因不可忽视 263
19.刨斜齿条时,齿厚产生误差的原因不可忽视 263
18.刨削大型斜齿条时,不宜采用展成法加工 263
2.刃磨普通麻花钻时,钻头转动和摆动不能过大 264
1.刃磨普通麻花钻时,切削刃不能低于砂轮中心 264
第六章 钻削、镗削加工 264
一、钻孔、扩孔、铰孔及攻丝 264
5.麻花钻的横刃不宜修磨得过长或过短 265
4.刃磨钻头时,不应忽视常见疵病 265
3.刃磨钻头时,横刃斜角不宜过小 265
7.钻削时,大、小直径的钻头进给量不应相同 266
6.修磨分屑槽的禁忌二则 266
9.刃磨群钻时不能忽视常见疵病 267
8.刃磨钻头时,后角不宜过大 267
13.刃磨群钻时,外缘后角不宜过大或过小 268
12.刃磨群钻时,月牙圆弧槽不宜过浅,半径不宜过大 268
10.刃磨群钻时,钻尖不宜过高、内刃顶角不宜过小 268
11.刃磨群钻时,不应将刃瓣磨去过多 268
14.孔即将钻穿时进给量不能过大 269
18.钻深孔时的三项禁忌 270
17.钻削时,起钻的进给量不宜过大,转速不宜过低 270
15.钻小孔时的禁忌二则 270
16.不宜在不平整的表面上用麻花钻直接钻孔 270
19.在小工件上钻孔或钻孔直径超过8mm时,不得用手握住工件加工 271
22.不能忽视铸件缩孔对钻削的影响 272
21.不宜用刃带已严重磨损的钻头钻孔 272
20.不宜用普通麻花钻钻薄板 272
24.钻孔时产生振动的原因不可不究 273
23.钻缺圆孔时的二项禁忌 273
28.扩孔时孔的位置精度超差的原因不可不究 274
27.扩孔时孔径增大的原因不可不究 274
25.采用导向套钻孔时的三不宜 274
26.采用模钻钻多孔时,孔距尺寸超差的原因不可忽视 274
33.铰削通孔、盲孔及有键槽的孔时,所选用的铰刀不应相同 275
32.铰削锥度较大的圆锥孔时,不宜在直孔上直接铰削 275
29.铰削余量不宜太大或太小 275
30.铰孔时铰刀不能倒转 275
31.机铰时进给量不能太大或太小 275
36.铰孔时,孔的位置精度超差的原因不可不究 276
35.铰孔时防止轴线不直的四则禁忌 276
34.铰孔时,防止铰刀崩齿的禁忌四则 276
39.铰孔后孔径减小不容忽视 277
38.铰孔后表面粗糙度过大的原因不可不究 277
37.铰孔时,防止内孔不圆的禁忌四则 277
42.机用丝锥攻螺纹时,防止丝锥折断的五项禁忌 278
41.不宜用增多铰刀齿数的方法来提高孔的铰削精度 278
40.铰孔时,孔径扩大不容忽视 278
3.粗镗工件时,不宜使用双刃镗刀 279
2.在镗床上,不能用主轴箱做微量下降移动来精找正工件 279
43.攻丝时,丝锥崩齿的原因不容忽视 279
二、镗床的基本加工方法 279
1.安装镗刀时,刀尖不宜低于工件中心 279
5.使用浮动镗刀的四项禁忌 280
4.未倒角的孔不宜用浮动镗刀做精镗加工 280
8.悬伸镗削的二项禁忌 281
7.悬伸镗削时,工作台进给对加工的影响不可忽视 281
6.精镗较长的孔时,不宜采用主轴进给 281
10.镗床工作台回转定位精度较差时,不宜采用调头镗削 282
9.采用悬伸镗削法不应忽视导向支承套的使用 282
13.精镗盲孔时,长度尺寸控制二不宜 283
12.采用平旋盘镗大孔时的二项禁忌 283
11.镗削较长的小孔时,防止产生锥度的三不宜 283
16.锪削孔的端面时,镗刀杆的刚性不容忽视 284
15.镗削缺圆孔三不宜 284
14.镗盲孔时,较大的孔底平面不宜用主轴装刀刮削 284
19.镗床产生强迫振动的原因不可不究 285
18.振动对镗削加工的影响不容忽视 285
17.反锪削孔的端面时,进给量不宜过大 285
2.精镗前后阶台端孔时,同轴度超差的原因不可忽视 286
1.镗孔时,防止圆柱度误差的五忌 286
三、镗床的孔系加工 286
4.采用试切法镗平行孔系时,除第一孔以外其他孔不能一次镗削至尺寸 287
3.采用坐标法镗平行孔系时,游标尺的精度不容忽视 287
6.采用回转法镗削垂直孔系时,工作台的回转精度不应忽视 288
5.用镗模镗平行孔系时,镗模的精度和刚度不能过低 288
8.采用回转台在圆柱面上镗削圆周孔系时的三不能 289
7.在弯板上镗削平面圆周孔系时的三项禁忌 289
11.镗床上采用滚压加工时的七项禁忌 290
10.精镗深孔时,单刃宽刀不应与普通单刃宽刀相同 290
9.镗削孔径较小的深孔时,不宜采用正向进给方式 290
12.不应忽视镗床主轴旋转精度对孔圆度的影响 291
16.为防止产生振动,镗削速度不宜随意选择 292
15.采用工作台进给及导向套镗孔时,圆度超差的原因不容忽视 292
13.镗杆受力变形对圆度误差的影响不应忽视 292
14.精镗时,夹紧变形、铸造内应力及热变形对圆度误差的影响不容忽视 292
1.不容忽视镗床铣削加工对镗床精度的影响 293
四、镗床的扩大利用 293
17.不应忽视进给量与切削深度对振动的影响 293
18.不应忽视刀具热变形对加工精度的影响 293
5.铣刀杆锥柄与镗床主轴锥孔之间的连接刚性不容忽视 294
4.在镗床主轴上装铣刀进行铣削时,主轴伸出不宜过长 294
2.在镗床上铣削时,不应忽视铣刀的安装与使用 294
3.钝化的铣刀不宜在镗床上继续切削 294
7.在镗床上铣削较大平面时,不宜将铣刀盘直接装在主轴锥孔内 295
6.采用主轴装铣刀进行铣削时,不能忽视增强主轴刚度的措施 295
11.镗床上铣削时,两平面垂直度超差的原因不容忽视 296
10.在镗床上铣平面时,平面度超差的原因不可忽视 296
8.镗床上连续铣削和断续铣削时,切削用量的选择不应相同 296
9.镗床上铣槽时,铣刀直径不宜与槽宽等同 296
13.在镗床上车削时,装夹工件及刀具的三不能 297
12.在镗床上铣削工件时,防止表面粗糙度过大的四项禁忌 297
16.在镗床上车外圆时,外圆镗刀装夹不容忽视 298
15.在镗床上不宜车削较长的外圆柱面 298
14.利用平旋盘车外圆时的二不宜 298
18.在镗床上不宜利用主轴镗削外螺纹 299
17.在镗床上车削螺纹时,不宜选用硬质合金刀具 299
4.不可忽视电极材料对电火花加工精度的影响 300
3.不可忽视极性效应对电火花加工的影响 300
第七章 切削加工新技术 300
一、电加工 300
1.不可忽视放电间隙对电火花加工的影响 300
2.不可忽视工作液对电火花加工的影响 300
9.不可忽视排气孔在型腔电火花加工中的重要性 301
8.型腔加工时,工具电极的冲油孔不宜开得过多、过大 301
5.“二次放电”对电火花加工精度的影响不可不防 301
6.电火花加工速度对工具电极损耗速度的影响不容忽视 301
7.不宜采用“单电极平动法”加工须清棱、清角的型腔 301
15.利用电火花进行铲磨加工时,严禁使用煤油作为工作液 302
14.深小孔电火花加工时,不可忽视导向装置的使用 302
10.小孔电火花加工中,工具电极的材料不可随意选用 302
11.电火花加工时,不可忽视预加工对加工效率的影响 302
12.不可忽视排屑环境对电火花加工效率的影响 302
13.不可忽视振动头在小孔电火花加工中的作用 302
19.不可忽视脉冲宽度对切割速度的影响 303
18.不可忽视电源空载电压对线切割速度的影响 303
16.利用电火花加工高阻抗材料时,不可忽视电参数的设置 303
17.采用电火花线切割机床进行加工时,不可盲目缩短脉冲周期来提高切割速度 303
24.电火花线切割加工时,不可忽视线电极张力对加工平面度的影响 304
23.不可忽视工作液压力对线切割速度的影响 304
20.不可忽视脉冲间隔t0对切割速度的影响 304
21.不可忽视供电部位的接触电阻对切割速度的影响 304
22.不可忽视线极丝振动过大对线切割加工速度的影响 304
27.不可忽视工件厚度对线切割加工精度的影响 305
26.线切割加工时,不可忽视工件残余应力对加工精度的影响 305
25.线切割加工时,不可忽视工件安装位置对加工平面度的影响 305
32.电火花线切割加工中,初始加工时的参数不宜过大 306
31.在线切割机床上进行校正端面、中心或线电极垂直校正时,电容的影响不容忽视 306
28.利用线切割进行精加工时,工作液的压力不宜过大 306
29.线切割精加工时,不可忽视工作液上、下喷嘴与工件之间距离对加工精度的影响 306
30.线切割加工时,不可忽视小余量、大工件的安装方法 306
34.电火花线切割加工时,不可忽视加工路线的选择 307
33.利用线切割加工孔类零件时,不可忽视“二次切割法” 307
3.数控加工中,对刀点的确定不容忽视 308
2.数控加工时不宜随意选择夹具 308
二、数控机床加工 308
1.不宜单纯追求高精度数控加工 308
8.数控加工时不可忽视跳步指令的正确运用 309
7.手工编程时,不可忽视G00指令的运动特征 309
4.编制程序时,不可忽视换刀点的确定 309
5.手工编程时,不可忽视顺序号的应用 309
6.准备功能字在不同设备上的功能差异不容忽视 309
12.数控加工中,不可忽视孔系加工路线的确定 310
11.数控加工中,不可忽视加工路线的确定 310
9.不可忽视暂停指令G04在数控加工中的作用 310
10.不可忽视数控加工工序与普通加工工序的衔接 310
14.在数控铣床上铣外表面轮廓时,切入和切出的程序设计不容忽视 311
13.在数控车床上加工螺纹时,不可忽视引入距离δ1与超越距离δ2值的确定 311
17.在数控机床上加工直纹曲面时,不可忽视加工方法的选择 312
16.在数控铣床上铣削凹槽时,不可忽视加工方法的选择 312
15.在数控铣床上铣削内轮廓表面时,不可忽视刀具切入、切出点的选择 312
20.用数控车床加工工件时,不可忽视主轴最高速度的限定 313
19.不可忽视数控加工中的在线测量 313
18.加工具有拐角的轮廓件时,其“超程”现象不容忽视 313
24.数控编程时,工件原点的确定不容忽视 314
23.应用刀具补偿时,不同方向的刀具补偿指令不可直接重复使用 314
21.在数控车床上使用G96指令时,不可忽视工件坐标系的设定 314
22.使用数控车床加工零件时,不可忽视刀具的补偿 314
27.利用数控铣床加工工件时,不可忽视G53指令的应用条件 315
26.数控车床编程时,不取消刀具补偿不准使用G27指令 315
25.编制数控车床程序时,G20、G21指令不可同时出现在同一程序内 315
31.利用加工中心加工工件时,加工余量的确定不容忽视 316
30.用加工中心加工刚性较差的零件时,不可忽视暂停指令的使用 316
28.在数控铣床上同时加工多个相同零件时,不同程序原点的设置不容忽视 316
29.利用加工中心加工工件时,应尽可能避免在同一工序中同时完成粗、精加工 316
35.在数控外圆磨床上执行圆弧插补指令G02、G03时,切入方向的编程不容忽视 317
34.修整数控磨床的砂轮时,不容忽视圆弧插补方向的判别 317
32.不可忽视自动换刀时重复定位误差对加工的影响 317
33.数控外圆磨床编程时,编程点的确定不容忽视 317
参考文献 319
- 《激光加工实训技能指导理实一体化教程 下》王秀军,徐永红主编;刘波,刘克生副主编 2017
- 《先进激光加工技能实训》肖海兵主编 2019
- 《CINEMA 4D新手快速进阶实例教学 商迪》商迪 2020
- 《AutoCAD机械设计实例精解 2019中文版》北京兆迪科技有限公司编著 2019
- 《犯罪痕迹师 谋杀禁忌 2 尸偶》黑眼圈著 2020
- 《菜籽油加工技术》罗质主编 2019
- 《蔬菜腌制加工技术》闫广金著 2019
- 《Dreamweaver CC 2018标准实例教程 中文版》杨雪静,胡仁喜编著 2019
- 《高分子材料与加工实验教程》刘昕责任编辑;(中国)胡扬剑,舒友,罗琼林 2019
- 《Adobe Photoshop 新手快速进阶实例教学》王楠 2019
- 《红色旅游的社会效应研究》吴春焕著 2019
- 《中国当代乡土小说文库 本乡本土》(中国)刘玉堂 2019
- 《社会学与人类生活 社会问题解析 第11版》(美)James M. Henslin(詹姆斯·M. 汉斯林) 2019
- 《异质性条件下技术创新最优市场结构研究 以中国高技术产业为例》千慧雄 2019
- 《中国铁路人 第三届现实主义网络文学征文大赛一等奖》恒传录著 2019
- 《莼江曲谱 2 中国昆曲博物馆藏稀见昆剧手抄曲谱汇编之一》郭腊梅主编;孙伊婷副主编;孙文明,孙伊婷编委;中国昆曲博物馆编 2018
- 《中国制造业绿色供应链发展研究报告》中国电子信息产业发展研究院 2019
- 《中国陈设艺术史》赵囡囡著 2019
- 《指向核心素养 北京十一学校名师教学设计 英语 七年级 上 配人教版》周志英总主编 2019
- 《《走近科学》精选丛书 中国UFO悬案调查》郭之文 2019