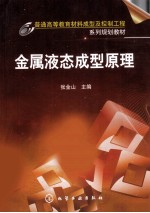
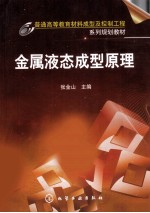
金属液态成型原理PDF电子书下载
- 电子书积分:10 积分如何计算积分?
- 作 者:张金山主编
- 出 版 社:北京:化学工业出版社
- 出版年份:2011
- ISBN:9787122099303
- 页数:235 页
0 绪论 1
0.1 金属的液态成形与凝固的关系 1
0.2 凝固过程研究的对象 1
0.3 凝固理论的研究进展 2
第1章 液态金属的结构和性质 4
1.1 固体金属的加热、熔化 4
1.1.1 晶体的定义与结构 4
1.1.2 金属的加热膨胀 4
1.1.3 金属的熔化 6
1.2 液态金属的结构 6
1.2.1 液态金属的热物理性质 7
1.2.1.1 体积和熵值的变化 7
1.2.1.2 熔化潜热与汽化潜热 7
1.2.2 X射线结构分析 7
1.2.3 液态金属的结构 8
1.2.3.1 纯金属液态结构 8
1.2.3.2 实际金属液态结构 9
1.2.4 液态金属理论结构模型-钢球模型与P-Y理论 10
1.3 液态金属的性质 12
1.3.1 液态金属的黏滞性 12
1.3.1.1 液态金属黏滞性的基本概念 13
1.3.1.2 黏滞性(黏度)在材料成形过程中的意义 14
1.3.2 液态金属的表面张力 15
1.3.2.1 表面张力的基本概念和实质 15
1.3.2.2 影响表面张力的因素 17
1.3.2.3 毛细现象及表面张力引起的附加压力 19
1.3.2.4 表面张力在材料成形中的意义 20
1.4 液态金属的充型能力 21
1.4.1 液态金属充型能力的基本概念 21
1.4.1.1 充型能力的定义及其他相关名词 21
1.4.1.2 液态金属流动性测试方法 22
1.4.2 液态金属停止流动的机理与充型能力 22
1.4.2.1 液态金属停止流动的机理 22
1.4.2.2 液态金属的充型能力 24
1.4.3 影响充型能力的因素 27
1.4.3.1 金属性质方面的因素 27
1.4.3.2 铸型性质方面的因素 29
1.4.3.3 浇注条件方面的因素 30
1.4.3.4 铸件结构方面的因素 31
1.5 液体金属中的流动 31
1.5.1 自然对流和强迫对流 31
1.5.2 凝固过程液相区液态金属的流动 32
1.5.3 液态金属对流对凝固组织的影响 33
习题与思考题 34
第2章 金属凝固过程的传热 35
2.1 概述 35
2.1.1 热量传递的基本方式 35
2.1.2 铸造过程中的热交换 35
2.2 导热基本定律 36
2.2.1 温度场 36
2.2.1.1 概念 36
2.2.1.2 等温面及等温线 36
2.2.2 傅里叶定律 36
2.2.3 导热微分方程 37
2.3 凝固温度场的求解方法 39
2.3.1 方法介绍 39
2.3.2 铸件凝固温度场的解析解法 39
2.3.3 半无限大物体的非稳态导热解析法 41
2.3.4 测温法 43
2.3.5 影响铸件温度场的因素 43
2.3.5.1 金属性质的影响 43
2.3.5.2 铸型性质的影响 43
2.3.5.3 浇注条件t浇 44
2.3.5.4 铸件结构的影响 44
2.4 不同界面热阻条件下温度场 46
2.4.1 概述 46
2.4.1.1 热阻 46
2.4.1.2 多层板的热阻 46
2.4.2 铸件在非金属型中凝固 48
2.4.3 金属型铸造凝固 48
2.5 铸件的凝固方式及其对铸件质量的影响 49
2.5.1 凝固动态曲线 49
2.5.2 凝固区域及其结构 49
2.5.3 铸件的凝固方式及其影响因素 51
2.5.3.1 凝固方式 51
2.5.3.2 影响凝固方式的因素 52
2.6 合金凝固方式与铸件质量的关系 52
2.6.1 窄结晶温度范围的合金 52
2.6.2 宽结晶温度范围的合金 53
2.6.3 中等结晶温度范围的合金 54
2.7 无限大平板铸件的凝固时间计算 54
2.7.1 理论计算法 54
2.7.2 经验公式法 55
习题与思考题 56
第3章 液态金属凝固热力学及动力学 57
3.1 凝固热力学 57
3.1.1 液固相变驱动力 57
3.1.2 曲率、压力对金属平衡结晶温度的影响 59
3.1.2.1 曲率对金属平衡结晶温度的影响 59
3.1.2.2 压力对物质熔点的影响 59
3.2 自发形核过程 60
3.2.1 液态金属的结晶过程 60
3.2.2 自发形核形核功 61
3.2.3 自发形核形核率 62
3.3 非自发形核过程 64
3.3.1 非自发形核形核功 64
3.3.2 非自发形核的形核条件 66
3.4 晶核的生长 67
3.4.1 液-固界面的结构及其影响因素 68
3.4.2 粗糙界面与光滑界面 69
3.5 晶体的生长方式及生长速度 70
3.5.1 晶体的生长方式 70
3.5.2 晶体的生长速度 70
3.5.2.1 连续生长 71
3.5.2.2 二维生核生长 72
3.5.2.3 沿螺型位错生长 72
3.5.3 晶体的生长方向和生长表面 73
习题与思考题 74
第4章 单相及多相合金的结晶 75
4.1 凝固过程中的质量传输 75
4.1.1 溶质分配方程 75
4.1.1.1 扩散第一定律 75
4.1.1.2 扩散第二定律 75
4.1.2 凝固传质过程的有关物理量 76
4.1.2.1 扩散系数D 76
4.1.2.2 溶质平衡分配系数k0 76
4.1.2.3 液相线斜率mL 77
4.1.2.4 液相温度梯度GL 77
4.1.3 稳定态扩散(溶质传输)过程的一般性质 77
4.1.3.1 稳定态定向凝固特征微分方程的通解 78
4.1.3.2 固液界面处的溶质平衡 78
4.1.3.3 远离固-液界面的液体成分 78
4.2 单相合金的凝固 79
4.2.1 溶质再分配现象的产生 79
4.2.2 平衡凝固时的溶质再分配 80
4.2.3 非平衡凝固时的溶质再分配 81
4.2.3.1 固相无扩散,液相充分扩散时的溶质再分配 81
4.2.3.2 固相无扩散,液相只有有限扩散的溶质再分配 83
4.2.3.3 固相无扩散、液相存在部分混合时的溶质再分配 85
4.3 成分过冷的产生 87
4.3.1 溶质富集引起界面前方熔体凝固温度的变化 87
4.3.2 热过冷与成分过冷 88
4.3.3 成分过冷判据 88
4.4 界面前方过冷状态对凝固过程的影响 90
4.4.1 热过冷对纯金属结晶过程的影响 90
4.4.2 成分过冷对一般单相合金结晶过程的影响 91
4.4.3 凝固参数和微观组织形态之间的关系 96
4.5 多相合金的凝固 97
4.5.1 共晶合金的凝固 97
4.5.1.1 共晶组织的分类与特点 97
4.5.1.2 规则共晶的凝固 99
4.5.1.3 非小平面-小平面共晶合金的结晶 102
4.5.1.4 离异生长及离异共晶 105
4.5.2 偏晶合金的凝同 106
4.5.2.1 偏晶合金大体积的凝固 106
4.5.2.2 偏晶合金的单向凝固 106
4.5.3 包晶合金的凝固 107
4.5.3.1 平衡凝固 107
4.5.3.2 非平衡凝固 107
习题与思考题 109
第5章 金属凝固组织的形成与控制 111
5.1 铸件宏观凝固组织的形成及其影响因素 111
5.1.1 铸件宏观凝固组织的特征 111
5.1.2 晶粒游离的产生 111
5.1.2.1 液态金属流动对结晶中晶粒游离过程的作用 111
5.1.2.2 铸件结晶中的晶粒游离 112
5.1.3 表面细晶粒区的形成 114
5.1.4 柱状晶区的形成 115
5.1.5 内部等轴晶区的形成 116
5.1.5.1 关于等轴晶晶核的来源 116
5.1.5.2 关于等轴晶区的形成过程 116
5.2 铸件宏观凝固组织的控制 117
5.2.1 铸件凝固组织对铸件质量和性能的影响 117
5.2.2 等轴晶组织的获得和细化 118
5.2.2.1 合理控制热学条件 118
5.2.2.2 孕育处理与变质处理 120
5.2.2.3 动态晶粒细化 124
5.2.2.4 等轴晶枝晶间距的控制 125
习题与思考题 125
第6章 凝固新技术 126
6.1 定向凝固 126
6.1.1 定向凝固的理论基础 126
6.1.1.1 定向凝固技术的工艺参数 126
6.1.1.2 成分过冷理论与界面稳定性理论 127
6.1.2 非平衡条件下的定向凝同 128
6.1.2.1 非平衡凝固时的溶质分配系数 128
6.1.2.2 非平衡定向凝固的界面形态选择 128
6.1.3 定向凝固技术及其应用 130
6.1.3.1 传统的定向凝固技术 130
6.1.3.2 新型定向凝固技术 132
6.1.3.3 定向凝固技术的应用 133
6.2 快速凝固 135
6.2.1 快速凝固技术简介 135
6.2.1.1 急冷凝固技术 136
6.2.1.2 深过冷法 137
6.2.2 快速凝固方法 137
6.2.2.1 急冷快速凝固方法 137
6.2.2.2 深过冷快速凝固方法 138
6.2.2.3 表面快速熔凝技术 140
6.2.2.4 喷射成型技术 141
6.2.2.5 表面沉积技术 141
6.2.3 快速凝固显微组织 141
6.2.4 金属玻璃 146
6.2.4.1 金属玻璃的基本概念 146
6.2.4.2 容易形成金属玻璃的合金系 147
6.2.4.3 金属玻璃的性能特点 147
6.3 超常凝固 147
6.3.1 微重力下的凝固 148
6.3.2 微重力实验环境的获得 148
6.3.3 声悬浮下的凝固 149
6.3.3.1 声悬浮技术简介 150
6.3.3.2 声悬浮理论 151
6.3.3.3 声悬浮凝固组织 152
6.3.4 高压凝固 153
6.3.4.1 压力对凝固参数的影响 153
6.3.4.2 高压下的非晶形成 155
6.3.4.3 高压下的纳米晶的形成 155
6.4 物理场作用下的凝固 156
6.4.1 电脉冲作用下的凝固 156
6.4.1.1 液相线以上电脉冲处理机理 156
6.4.1.2 液固两相区内电脉冲处理机理探讨 156
6.4.1.3 电脉冲作用下的凝固组织 157
6.4.2 电场作用下的凝固 157
6.4.2.1 连续电流作用下合金熔体凝固组织研究结果 157
6.4.2.2 连续电流对凝固组织的作用机制 158
6.4.3 超声波作用下的凝固 159
6.4.3.1 超声波对液体的作用机理 159
6.4.3.2 超声波对金属凝固组织的作用 160
6.5 半固态金属的凝固 161
6.5.1 半固态凝固技术简介 161
6.5.2 半固态金属的特性及形成机理 161
6.5.2.1 半固态金属的特性 161
6.5.2.2 半固态金属的形成机理 162
6.5.3 半固态铸造 162
6.5.3.1 半固态金属原料的制备 162
6.5.3.2 半固态金属铸造的特点及方法 163
习题与思考题 165
第7章 合金中的成分偏析 166
7.1 微观偏析 166
7.1.1 晶内偏析 167
7.1.1.1 晶内偏析的影响因素 167
7.1.1.2 晶内偏析的预防与消除 169
7.1.2 晶界偏析 170
7.2 宏观偏析 171
7.2.1 正常偏析 172
7.2.2 逆偏析 173
7.2.3 V型和逆V型偏析 173
7.2.4 带状偏析 174
7.2.5 重力偏析 174
习题与思考题 175
第8章 气孔和夹杂 176
8.1 气孔 176
8.1.1 金属中气体的来源及种类 176
8.1.1.1 金属中气体的来源 176
8.1.1.2 铁和钢中的气体 177
8.1.1.3 铝及铝合金中的气体 177
8.1.1.4 镁及镁合金中的气体 177
8.1.1.5 铜及铜合金中的气体 177
8.1.2 铸件中气孔的分类及特征 177
8.1.2.1 反应性气孔 177
8.1.2.2 侵入性气孔 178
8.1.2.3 析出性气孔 178
8.1.3 气孔的形成过程 179
8.1.3.1 经典形核理论 179
8.1.3.2 非经典形核理论 182
8.1.4 防止气孔形成的措施 186
8.1.4.1 防止侵入气孔的措施 186
8.1.4.2 防止析出气孔的措施 186
8.1.4.3 防止反应气孔的措施 187
8.1.4.4 防止卷入气孔的措施 187
8.2 夹杂 187
8.2.1 夹杂物的来源及分类 188
8.2.1.1 夹杂物的来源 188
8.2.1.2 夹杂物的分类 188
8.2.2 非金属夹杂物的形成过程 189
8.2.2.1 非金属夹杂物形成的热力学条件 189
8.2.2.2 初生夹杂物的形成过程 191
8.2.2.3 二次氧化夹杂物的形成过程 196
8.2.2.4 次生夹杂物的形成过程 197
8.2.3 非金属夹杂物的去除 197
8.2.3.1 气体搅拌 197
8.2.3.2 电磁净化 198
8.2.3.3 氯盐精炼法 199
8.2.3.4 熔剂净化法 199
8.2.3.5 化学法 199
8.2.3.6 过滤器 199
习题与思考题 199
第9章 缩孔和缩松 200
9.1 金属收缩的概念 200
9.1.1 液态收缩 201
9.1.2 凝固收缩 201
9.1.3 固态收缩 203
9.1.4 铸件的收缩 205
9.2 缩孔与缩松的形成机理 206
9.2.1 缩孔 207
9.2.1.1 缩孔的形成 207
9.2.1.2 缩孔的容积 207
9.2.1.3 缩孔位置的确定 209
9.2.2 缩松 210
9.2.2.1 缩松的形成 211
9.2.2.2 缩孔和缩松的相互转化 214
9.2.3 灰铸铁和球墨铸铁铸件的缩孔和缩松 215
9.3 防止铸件产生缩孔和缩松的途径 217
9.3.1 顺序凝固和同时凝固 217
9.3.1.1 顺序凝固 217
9.3.1.2 同时凝固 219
9.3.2 浇注系统的引入位置及浇注工艺 220
9.3.3 冒口、补贴和冷铁的应用 221
9.3.4 加压补缩 221
习题与思考题 221
第10章 铸造应力、变形和裂纹 222
10.1 概述 222
10.2 铸造应力 223
10.2.1 铸造应力的分类 223
10.2.2 应力的形成 223
10.2.2.1 热应力的形成 223
10.2.2.2 相变应力的形成 224
10.2.2.3 机械阻碍应力的形成 225
10.2.3 控制应力的措施 225
10.2.3.1 形成铸造应力的影响因素 225
10.2.3.2 减小应力的途径 225
10.2.3.3 消除残余应力的方法 226
10.3 变形 226
10.3.1 变形的种类 227
10.3.2 控制变形的措施 227
10.4 铸造中的裂纹 228
10.4.1 铸造中的热裂纹的形成与控制 228
10.4.1.1 热裂纹的分类及特征 228
10.4.1.2 热裂纹的形成机理 228
10.4.1.3 热裂纹的影响因素 231
10.4.1.4 合金因素的影响 231
10.4.1.5 工艺因素对热裂纹的影响 232
10.4.1.6 防止热裂纹的措施 232
10.4.2 冷裂纹 232
习题与思考题 234
参考文献 235
- 《第一性原理方法及应用》李青坤著 2019
- 《计算机组成原理解题参考 第7版》张基温 2017
- 《高等院校保险学专业系列教材 保险学原理与实务》林佳依责任编辑;(中国)牟晓伟,李彤宇 2019
- 《刑法归责原理的规范化展开》陈璇著 2019
- 《教师教育系列教材 心理学原理与应用 第2版 视频版》郑红,倪嘉波,刘亨荣编;陈冬梅责编 2020
- 《单片机原理及应用》庄友谊 2020
- 《通信电子电路原理及仿真设计》叶建芳 2019
- 《计算机组成原理 第2版》任国林 2018
- 《化工原理课程设计》刘建周主编 2018
- 《会计学原理》邵瑞庆主编 2019