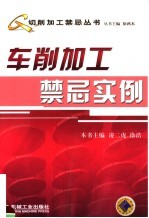
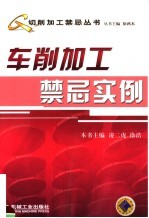
车削加工禁忌实例PDF电子书下载
- 电子书积分:15 积分如何计算积分?
- 作 者:凌二虎,徐浩主编
- 出 版 社:北京:机械工业出版社
- 出版年份:2005
- ISBN:7111160878
- 页数:451 页
第1章 切削过程中的禁忌 1
1.1 车削加工中不宜形成挤裂或单元切屑 1
1.2 精车时不允许存在积屑瘤 2
1.3 切削力不宜过大 3
1.4 切削温度不宜过高 6
1.5 不允许车刀出现过度磨损 8
1.6 切削液的正确使用,不可忽视 14
1.7 材料可切削性对车削生产率的重要影响,不可忽视 18
1.8 化学元素对钢的可切削性影响,不可忽视 19
1.9 钢的金相组织对可切削性的影响,不可忽视 20
1.10 造成车削表面粗糙度值增加的两大因素,不可忽视 20
2.2 各种刀具材料性能的差别,不可忽视 23
2.1 刀具材料必须具备的性能,不可忽视 23
第2章 车刀材料、车刀角度、车削用量选择的禁忌 23
2.3 通用型、高性能高速钢性能与用途的差异,不可忽视 25
2.4普通硬质合金、新型硬质合金和涂层硬质合金性能、用途的异同,不可忽视 27
2.5 陶瓷车刀不宜在低速、冲击负荷下车削 34
2.6 金刚石车刀不宜车削黑色金属工件,切削温度不宜过高 35
2.7 立方氮化硼车刀不宜车削软材料及在低速、冲击载荷大的条件下切削 36
2.8 选择车刀前角(γo)时,工件材料、刀具材料及加工条件的变化,不可忽视 37
2.9 选择车刀前面形状及刃区参数时,工件、刀具材料性质及切削的特点,不可忽视 39
2.10 切削塑性材料的断屑问题,不可忽视 41
2.11 选择车刀后角(αo)时,工件材料及加工条件的变化,不可忽视 43
2.12 选择车刀主偏角(kr)时,工艺系统的刚性及工件形状,不可忽视 44
2.13 选择车刀副偏角(k?)时,工艺系统刚性及加工条件,不可忽视 45
2.14 车刀切削刃上最薄弱部位形状的选择,不可忽视 45
2.15 选择车刀刃倾角(λs)时,工件材料及加工条件,不可忽视 46
2.16 车削用量三要素选择的顺序,不能颠倒 48
2.17 选择背吃刀量αp时,余量大小与车削条件,不可忽视 49
2.18 选择进给量f时,表面粗糙度要求与切削力的大小,不可忽视 50
2.19 选择车削速度vc,刀具耐用度的保证与切削条件的变化,不可忽视 55
第3章 车削工艺中的禁忌 64
3.1 车床使用中的禁忌 64
3.1.1 选择在车床上加工工件,不应背离车削加工的工艺特点 64
3.1.2 车床传动系统图的重要作用,不可忽视 71
3.1.3 识读车床传动系统图时两个关键问题,不可忽视 73
3.1.4 车床精度及调整对加工质量的影响,不可忽视 79
3.1.5 高精度工件车削、强力车削前,车床的调整,不可忽视 94
3.1.6 车床的定期保养,不可忽视 96
3.1.7 车床的维护保养,各部件的合理润滑,不可忽视 97
3.1.8 操作车床,不得违反切削加工通用工艺守则 99
3.1.9 操作车床,不得违反车削加工通用工艺守则 101
3.1.10 操作车床,不允许违反安全操作规程 103
3.2 车刀选用、刃磨、安装中的禁忌 104
3.2.1 选用车刀,不可背离不同结构车刀的使用特点 104
3.2.2 可转位刀片的厚度和精度,不可任意选择 133
3.2.3 使用可转位车刀,不允许出现打刀等不正常现象 135
3.2.4 夹紧可转位车刀刀片,要有防崩刃措施 136
3.2.5 可转位车刀刀杆上刀片槽的两个定位面间的角度,不能大于或等于刀片的实际角度 136
3.2.6 硬质合金可转位车刀刀片的法后角,不可任意选择 136
3.2.7 刃磨车刀时,砂轮的选择不能有误 137
3.2.8 手工刃磨车刀时,不能违背刃磨合理的顺序与安全操作 138
3.2.9 车刀在刀架上的正确安装,不可忽视 142
3.2.10 车刀安装位置对车刀前角、后角的影响,不可忽视 144
3.2.11 车刀安装位置对车刀主、副偏角的影响,不可忽视 146
3.2.12 进给运动对车刀工作角度的影响,不可忽视 146
3.3 轴类零件车削的禁忌 148
3.3.1 车端面时,刀具及进给方向的选择,不可忽视 148
3.3.2 车削外圆表面,工艺与设备的选择,不可忽视 150
3.3.3 在车床两顶尖间装夹工件车削外圆柱面时,两顶尖轴线不应错位 151
3.3.4 中心孔类型的选择,不可忽视 152
3.3.5 工件中心孔的加工质量,不可忽视 155
3.3.6 在车床上钻中心孔,钻头折断的原因,不可忽视 156
3.3.7 车削棒材毛坯的轴、盘、套类零件,棒材各 157
部位加工余量,不可任意确定 157
3.3.8 车削轴类零件,工序余量与车削步骤的选择,不可忽视 163
3.3.9 切断刀的安装质量,不可忽视 174
3.3.10 切断刀刀刃宽度及刀头长度,不可任意确定 175
3.3.11 切断时,切断刀折断的问题不可不防 175
3.3.12 影响车削质量的共同因素及改善途径,不可忽视 177
3.3.13 轴类零件检测时,检测量具与检验方法不可有误 201
3.4 盘套类零件车削的禁忌 209
3.4.1 选择盘套类零件车削的工艺方法,其技术要求与结构特点,不可忽视 209
3.4.2 盘套类零件孔加工的工序间余量,不可任意选择 215
3.4.3 钻孔、扩孔、铰孔和镗孔的切削用量,不可任意选择 221
3.4.4 刃磨麻花钻头常见的疵病,不可忽视 234
3.4.5 车床上钻孔自动进给方式的应用,不可忽视 235
3.4.6 钻孔时的操作调整,不可有误 237
3.4.7 标准麻花钻结构的缺点及修磨方法,不可忽视 238
3.4.9 同一直径尺寸的扩孔钻,其应用上的区别,不可忽视 242
3.4.8 钻削不同材料的工件孔时,钻头的几何角度不应一成不变 242
3.4.10 铰孔完毕时,铰刀退出工件的方式,不可忽视 243
3.4.11 铰孔时,铰刀刀齿崩刃,不可忽视 243
3.4.12 铰不连续孔铰刀结构的选择,不可忽视 245
3.4.13 铰刀直径尺寸的极限偏差值,不可任意选择 245
3.4.14 车内孔时,内孔车刀结构的选择,不可忽视 248
3.4.15 车削盘套类零件,保证内、外圆位置精度的方法,不可忽视 249
3.4.16 在三爪自定心卡盘上装夹工件进行粗车或精车时,其悬伸部分不宜过长 256
3.4.17 三爪自定心卡盘上安装大直径工件时,不宜用正爪装夹 256
3.4.18 用四爪单动卡盘装夹工件,校正工作,不可忽视 257
3.4.19 钻孔时孔径扩大或偏小,不可忽视 258
3.4.20 钻孔时孔的轴线歪斜,不可忽视 260
3.4.21 钻孔时产生振动或孔不圆的现象,不可不防 260
3.4.24 扩孔钻扩孔时,孔表面粗糙,不可忽视 261
3.4.25 多刃铰刀铰孔时,孔径增大问题,不可忽视 261
3.4.22 钻孔时孔壁表面粗糙问题,不可忽视 261
3.4.23 扩孔钻扩孔时,孔径增大问题,不可忽视 261
3.4.26 多刃铰刀铰孔时,孔径小的问题,不可忽视 262
3.4.27 多刃铰刀铰孔时,不允许铰出的内孔不圆 263
3.4.28 多刃铰刀铰孔时,不允许孔表面有明显的棱面 263
3.4.29 多刃铰刀铰孔时,孔表面粗糙,不可忽视 264
3.4.30 铰孔后不允许孔的轴线不直 265
3.4.31 车削内孔时,孔的尺寸精度未达要求,不可忽视 265
3.4.32 车削内孔时,不允许内孔的锥度超差 267
3.4.33 车削内孔时,孔壁粗糙,不可忽视 267
3.4.34 盘套类零件的精度检验,不可忽视 267
3.4.35 车削轴、盘套类零件,提高生产率的途径,不可忽视 274
3.4.36 提高钻孔生产率的途径,不可忽视 278
3.4.37 提高铰孔质量与生产率的途径,不可忽视 289
3.5 圆锥面车削的禁忌 291
3.5.1 圆锥面加工方法的正确选择,不可忽视 291
3.5.2 用转动小刀架法车削内、外圆锥面时,小刀架转动的角度不可不经换算 296
3.5.3 车削配套圆锥面,不允许变动小刀架的角度 298
3.5.4 车削对称圆锥孔,不允许变动小刀架的角度 299
3.5.5 车削圆锥面时,不可不防废品的出现 299
3.5.6 圆锥面精度的检验,不可忽视 302
3.6 螺纹车削的禁忌 306
3.6.1 螺纹车刀的安装方法不能有误 306
3.6.2 车螺纹的三种进刀方式各具特点,不可混淆、误用 307
3.6.3 选择螺纹车削方法,螺纹形状的特点,不可忽视 311
3.6.4 车螺纹时扎刀、打刀不可不防 311
3.6.5 车螺纹时不允许螺距超差 312
3.6.6 车螺纹时,不允许螺距周期性误差超差 313
3.6.7 车螺纹时,螺距积累误差超差,不可忽视 313
3.6.8 螺纹车削时,螺纹牙形角不能超差 314
3.6.9 车螺纹时,不能使螺纹中径几何形状超差 314
3.6.10 车螺纹不应不防螺纹乱扣 315
3.6.11 车削螺纹牙形,表面粗糙度值不允许超差 315
3.6.12 机用丝锥攻螺纹时,丝锥崩刃、折断,不可忽视(一) 316
3.6.13 机用丝锥攻螺纹时,丝锥崩刃、折断,不可忽视(二) 319
3.6.14 机用丝锥攻螺纹时,丝锥崩刃、折断,不可忽视(三) 320
3.6.15 攻锥螺纹的底孔尺寸与切削速度,不可任意选择 322
3.6.16 使用特种丝锥,其结构特点和使用范围,不可忽视 323
3.6.17 机用丝锥攻螺纹,不允许螺纹中径过大 323
3.6.19 用板牙套螺纹时,毛坯准备、工具校正与切削速度的选择,不可忽视 325
3.6.18 机用丝锥攻螺纹,不允许螺纹中径过小 325
3.6.20 用螺纹切头切螺纹,梳刀崩齿问题,不可忽视 326
3.6.21 用螺纹切头切螺纹,切头张开不灵、梳刀卡住工件不可不防 327
3.6.22 用螺纹切头切螺纹,不能让螺纹乱扣 328
3.6.23 用螺纹切头切螺纹,不允许螺纹中径椭圆 328
3.6.24 用螺纹切头切螺纹,不允许螺纹中径超差 328
3.6.25 用螺纹切头切螺纹,螺纹表面有波纹,不可忽视 328
3.6.26 滚压螺纹的优点,不可忽视 328
3.6.27 滚压螺纹的坯件材料硬度不能太高 330
3.6.28 滚压螺纹前,坯件不能不倒角 330
3.6.29 滚压头滚压螺纹时,滚轮张开量不足、工件退不出,不可忽视 331
3.6.30 滚压头滚压螺纹,滚轮寿命低,不可忽视 331
3.6.31 滚压头滚压螺纹,滚轮崩齿、碎裂不可不防 331
3.6.32 滚压头滚压螺纹,不允许螺纹乱扣 332
3.6.33 滚压头滚压螺纹,中径尺寸已小于下限,但过端环规仍通不过,不可忽视 333
3.6.34 滚压头滚压螺纹,不允许出现螺纹不圆、三棱形或一边牙尖、一边牙平现象 333
3.6.35 滚压头滚压螺纹,坯件不易进入滚压头,端部产生飞边或毛刺问题,不可忽视 333
3.6.36 滚压头滚压螺纹,螺纹表面粗糙度值不应太大 334
3.6.37 滚压头滚压螺纹时,不允许螺纹出现裂纹 334
3.6.38 滚压头滚压螺纹时,不允许螺纹牙顶、牙侧产生毛刺、碎屑 334
3.6.39 螺纹的检验,不可有误 335
3.6.40 提高螺纹加工生产率的途径,不可忽视 339
3.7 成形面车削的禁忌 342
3.7.1 选择成形表面的车削方法,不应忽视工件结构、生产批量与加工要求 342
3.7.2 用靠模法车削凸轮成形面,靠模表面圆弧半径不能任意选择 350
3.7.3 顶尖式和卡盘式仿形车床加工型面的范围不能混淆 351
3.7.4 仿形车削的型面与允许角度,不能任意选择 353
3.7.5 仿形车削的工件型面与车刀工作主、副偏角,不能任意选择 354
3.7.6 内仿形车削的型面与允许角度,不能任意选择 355
3.7.7 内仿形车削的工件型面与车刀工作主、副偏角,不能任意选择 356
3.7.8 仿形车削时,不允许外圆锥度超差 357
3.7.9 仿形车削阶梯轴,较大直径的外圆尺寸扩大,以及内仿形车削阶梯孔,较大孔径的尺寸缩小,不可忽视 357
3.7.10 仿形车削时,工件轴向尺寸忽长忽短,不可不防 357
3.7.11 仿形车削时,倒角忽大忽小,不可忽视 357
3.7.12 仿形车削时,圆弧半径扩大,不可忽视 357
3.8 滚花、绕弹簧的禁忌 358
3.8.1 表面滚花,滚花刀的选择和乱纹的防止不可忽视 358
3.8.2 车床上绕制弹簧时,其心轴直径,不可忽视 361
3.9 定位基准选择的禁忌 363
3.9.1 工件车削时,定位粗基准的选择,不可忽视 363
3.9.2 工件车削时,定位精基准的选择,不可忽视 365
3.9.3 选择定位基准,不应使定位基准与测量基准不一致 368
3.9.4 工件不能超定位 368
3.10 车削零件结构的禁忌 369
第4章 复杂、精密零件车削的禁忌 376
4.1 车削细长轴,对其结构及工艺特点,不可忽视 376
4.2 高速车削细长轴,不宜采用双支承跟刀架 376
4.3 车削细长轴时不宜采用自右向左的进给方向 377
4.4 车细长轴粗车刀主偏角不宜太小 377
4.5 车削细长轴,工件弯曲问题,不可忽视 378
4.6 用跟刀架车削细长轴时,出现竹节形误差不可不防 380
4.7 车削细长轴,棱圆形(多边形)、麻花形误差不可不防 381
4.8 车削细长轴时,出现锥度误差,不可忽视 382
4.9 车削细长轴,工件出现腰鼓形误差,不可忽视 382
4.10 车削细长轴时,表面粗糙度值大,不可忽视 383
4.11 采用跟刀架车削细长轴,不允许存在超定位现象 385
4.12 车削偏心零件,工件的结构、批量及加工要求的不同,不可忽视 386
4.13 不同零件偏心距的测量方法,不可忽视 392
4.14 大型薄壁件车削时,装夹变形问题,不可忽视 394
4.15 环状薄壁件、薄片圆盘工件加工时,装夹变形问题,不可忽视 395
4.16 微调刀头在精密孔加工中的应用,不可忽视 396
4.17 金刚石铰刀加工精密孔的优越性,不可忽视 397
4.18 深孔加工,其工艺上难点及相应的技术措施,不可忽视 397
4.19 丝杠车削,其结构特点及保证质量的措施,不可忽视 404
4.20 车削多头蜗杆,螺纹加工质量与分头误差的防止,不可忽视 406
4.21 车削环面蜗杆,工件和刀具的安装不能偏离正确位置 411
4.22 车削环面蜗杆齿形前,不可缺少蜗杆圆弧面的精车工序 412
5.1 车削难加工材料,材料特性与切削特点的关系,不可忽视 413
第5章 难加工材料车削的禁忌 413
5.2 车削高强度钢、超高强度钢,刀具材料、几何角度与切削用量的选择,不可忽视 414
5.3 车削高锰钢,其加工硬化严重、精度不易保证等特点,不可忽视 416
5.4 用硬质合金群钻、可转位浅孔钻钻削高锰钢工件,防止崩刃和“闷车”,不可忽视 419
5.5 车削淬硬钢、冷硬铸铁及耐磨合金铸铁,刀具磨损剧烈及崩刃问题,不可不防 420
5.6 车削不锈钢、高温合金,保证加工质量的措施,不可忽视 423
5.7 不锈钢、高温合金工件在钻孔时的断屑问题,不可忽视 429
5.8 不锈钢、高温合金铰孔时,保证孔的质量,不可忽视 432
5.9 车削工程塑料,材料回弹性等对加工质量的影响,不可忽视 435
5.10 钻削热塑性塑料、热固性塑料钻头的材料与几何参数的区别,不可忽视 438
附录 441
附录一 切削加工用硬质合金的应用范围分类和用途分组 441
附录二 三针测量螺纹中径时的M值 443
参考文献 451
- 《激光加工实训技能指导理实一体化教程 下》王秀军,徐永红主编;刘波,刘克生副主编 2017
- 《先进激光加工技能实训》肖海兵主编 2019
- 《CINEMA 4D新手快速进阶实例教学 商迪》商迪 2020
- 《AutoCAD机械设计实例精解 2019中文版》北京兆迪科技有限公司编著 2019
- 《犯罪痕迹师 谋杀禁忌 2 尸偶》黑眼圈著 2020
- 《菜籽油加工技术》罗质主编 2019
- 《蔬菜腌制加工技术》闫广金著 2019
- 《Dreamweaver CC 2018标准实例教程 中文版》杨雪静,胡仁喜编著 2019
- 《高分子材料与加工实验教程》刘昕责任编辑;(中国)胡扬剑,舒友,罗琼林 2019
- 《Adobe Photoshop 新手快速进阶实例教学》王楠 2019
- 《指向核心素养 北京十一学校名师教学设计 英语 七年级 上 配人教版》周志英总主编 2019
- 《北京生态环境保护》《北京环境保护丛书》编委会编著 2018
- 《高等教育双机械基础课程系列教材 高等学校教材 机械设计课程设计手册 第5版》吴宗泽,罗圣国,高志,李威 2018
- 《指向核心素养 北京十一学校名师教学设计 英语 九年级 上 配人教版》周志英总主编 2019
- 《高等院校旅游专业系列教材 旅游企业岗位培训系列教材 新编北京导游英语》杨昆,鄢莉,谭明华 2019
- 《中国十大出版家》王震,贺越明著 1991
- 《近代民营出版机构的英语函授教育 以“商务、中华、开明”函授学校为个案 1915年-1946年版》丁伟 2017
- 《新工业时代 世界级工业家张毓强和他的“新石头记”》秦朔 2019
- 《智能制造高技能人才培养规划丛书 ABB工业机器人虚拟仿真教程》(中国)工控帮教研组 2019
- 《AutoCAD机械设计实例精解 2019中文版》北京兆迪科技有限公司编著 2019