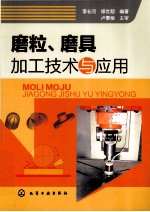
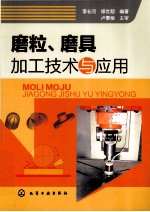
磨粒、磨具加工技术与应用PDF电子书下载
- 电子书积分:12 积分如何计算积分?
- 作 者:李长河,修世超编著
- 出 版 社:北京:化学工业出版社
- 出版年份:2012
- ISBN:9787122150196
- 页数:309 页
第1章 磨粒加工的历史及发展趋势 1
1.1 磨粒加工及其历史 1
1.1.1 磨粒加工的定义及在国民经济中的重要地位 1
1.1.2 磨粒加工的历史 2
1.2 磨削加工的特点和磨削过程 6
1.2.1 磨削加工的特点 6
1.2.2 磨削加工的分类 7
1.2.3 磨削加工的基本参数 8
1.2.4 磨削过程 9
1.3 磨削加工的力和热 10
1.3.1 磨削力 10
1.3.2 磨削热和磨削温度 11
1.4 磨削加工的发展趋势 12
1.4.1 磨削加工机理研究的发展趋势 12
1.4.2 磨削加工向数控化、自动化、智能化及虚拟化方向发展 13
1.4.3 磨削加工新工艺的发展 13
1.4.4 硬脆材料磨削技术的发展 15
1.4.5 磨料、磨具的研究和开发 16
1.5 磨削是否会被硬切削替代 17
1.5.1 硬切削工艺 17
1.5.2 硬切削会取代磨削加工吗 18
1.6 国家科技重大专项在磨削方面解决的重点问题和相关的研究进展 19
1.6.1 解决的重点问题 19
1.6.2 研究进展 20
第2章 磨料与磨具 21
2.1 普通磨料 21
2.1.1 普通磨料品种及代号 21
2.1.2 普通磨料粒度、粒度组成及标记 21
2.1.3 刚玉系磨料 26
2.1.4 陶瓷微晶刚玉磨料 27
2.1.5 碳化物系磨料 28
2.2 超硬磨料 28
2.2.1 超硬磨料品种及代号 28
2.2.2 超硬磨料的应用特点 30
2.3 固结磨具 31
2.3.1 普通磨料磨具 31
2.3.2 超硬磨料磨具 42
2.4 涂附磨具 58
2.5 磨具特性参数的选择 59
2.5.1 磨具的构成及特性 59
2.5.2 选择磨具特性参数的一般性原则 59
2.5.3 磨具特性参数选择方法的不足与发展趋势 61
第3章 砂轮的整形与修锐 63
3.1 砂轮磨损的形式及原因 63
3.1.1 砂轮磨损形式 63
3.1.2 砂轮磨损原因 64
3.1.3 砂轮磨损的表征 66
3.2 砂轮磨损的测量方法 66
3.2.1 用台阶法测量砂轮磨损量 67
3.2.2 用仿形法测量砂轮磨损量 67
3.2.3 用空气量规传感器测量砂轮磨损量 67
3.2.4 用砂轮周围空气流特征测量砂轮磨损量 68
3.2.5 用随机过程分析法测量砂轮磨损量 68
3.3 砂轮地貌的测量方法 68
3.3.1 轮廓测量仪法 68
3.3.2 复印法 69
3.3.3 光截法 70
3.3.4 激光功率谱法 71
3.3.5 电镜观察法 71
3.3.6 测力计法和热电偶法 72
3.3.7 光反射法 72
3.4 普通磨料砂轮的修整 73
3.4.1 砂轮修整的作用 73
3.4.2 车削修整法 73
3.4.3 滚压修整法 74
3.4.4 磨削修整法 74
3.5 超硬磨料砂轮的修整 76
3.5.1 电解在线修锐法 76
3.5.2 电火花放电修锐法 78
3.5.3 激光修锐法 78
3.5.4 软弹性修锐法 79
3.5.5 超声波振动修锐法 79
3.5.6 研磨修锐法 80
3.5.7 游离磨粒修锐法 80
3.6 砂轮的平衡 81
3.6.1 砂轮的静态平衡 81
3.6.2 砂轮的动态平衡 83
3.6.3 砂轮的动平衡 85
第4章 磨削液及供液方法 86
4.1 磨削液的作用、要求和种类 86
4.1.1 磨削液的作用 86
4.1.2 磨削液的种类及性能 87
4.1.3 磨削液添加剂的种类及作用 90
4.1.4 磨削液的要求 91
4.2 磨削液的动压作用与影响 92
4.2.1 流体动压润滑的基本理论 92
4.2.2 磨削液的动压作用与影响 92
4.3 磨削砂轮气流场及对磨削液的影响 92
4.3.1 磨削砂轮气流场的产生 92
4.3.2 磨削砂轮气流场的影响 93
4.4 磨削液的供液方法 93
4.5 磨削液射流特性及有效注入技术 96
4.5.1 磨削液射流速度分布场研究 97
4.5.2 磨削区气流场对有效磨削液的影响 98
4.5.3 有效磨削液的计算与分析 98
4.5.4 提高有效磨削液比例的途径 99
4.6 磨削液的过滤 102
第5章 磨削加工表面质量 104
5.1 表面质量概念 104
5.2 磨削表面质量对零件使用性能的影响 104
5.3 磨削表面粗糙度与波纹度 105
5.3.1 表面粗糙度 105
5.3.2 波纹度 111
5.4 磨削表面和次表面的金相组织变化 112
5.4.1 磨削表面金相组织特点 112
5.4.2 磨削烧伤的概念及分类 113
5.4.3 磨削烧伤对零件工作性能的影响 114
5.4.4 避免烧伤的措施 114
5.4.5 磨削表层烧伤的测量方法 115
5.5 表面加工硬化和表面残余应力 115
5.5.1 表面加工硬化 115
5.5.2 表面残余应力 116
5.6 磨削表面裂纹和预应力磨削 120
5.6.1 磨削表面裂纹 120
5.6.2 预应力磨削 121
5.7 残余应力与裂纹的测量 122
5.8 其他磨削表面缺陷 122
5.9 磨削表面完整性指标综合作用及评价 122
第6章 磨削加工精度 124
6.1 磨削误差的来源 124
6.2 工艺系统受力变形对加工精度的影响 125
6.2.1 工艺系统受力变形对加工精度的影响机理 125
6.2.2 减少工艺系统受力变形的措施 125
6.3 磨削温度及工艺系统受热变形对加工精度的影响 126
6.3.1 磨削温度及工艺系统受热变形对加工精度的影响机理 126
6.3.2 控制磨削温度和工艺系统受热变形的措施 126
6.4 工件和砂轮工作状态对加工精度的影响 127
6.5 工艺系统几何精度对加工精度的影响 127
6.5.1 机床成形运动误差的影响 127
6.5.2 机床传动链误差的影响 128
第7章 磨削加工过程的控制 129
7.1 磨削加工循环及其控制 129
7.1.1 磨削加工的自动化特点 129
7.1.2 磨削加工自动循环过程 129
7.1.3 自动切入过程的控制 130
7.2 磨削过程参数优化 130
7.2.1 磨削过程优化的概念 130
7.2.2 磨削过程特点与目标函数的设置 131
7.3 磨削过程虚拟与仿真 132
7.3.1 系统仿真的概念 132
7.3.2 磨削加工仿真流程 133
7.3.3 磨削仿真数据输入流程 133
7.3.4 磨削模型 133
7.3.5 磨削加工的虚拟与仿真 135
7.4 磨削过程智能控制 136
7.5 磨削过程监测与控制 136
7.5.1 磨削过程信息监测 137
7.5.2 磨削过程信息智能监控技术 138
7.6 磨削尺寸自动测量 138
7.7 数控磨削 139
7.7.1 数控磨床概述 139
7.7.2 数控磨削加工工艺 140
7.8 机器人磨削 141
第8章 常用磨削加工方法 142
8.1 平面磨削 142
8.1.1 平面磨床的类型 142
8.1.2 平面磨削形式及特点 143
8.1.3 平面磨削常用方法 144
8.1.4 平面磨削常见的缺陷与消除措施 145
8.1.5 平面磨削加工实例 146
8.2 外圆磨削 147
8.2.1 外圆磨削的形式 148
8.2.2 外圆磨削砂轮的选择 148
8.2.3 工件的装夹 149
8.2.4 外圆磨削的方法 151
8.2.5 外圆磨削常见的缺陷与消除措施 153
8.2.6 轴类零件磨削加工实例 155
8.3 内圆磨削 157
8.3.1 内圆磨削的特点 157
8.3.2 内圆磨削的形式 158
8.3.3 砂轮的选择 158
8.3.4 工件的装夹 159
8.3.5 内圆磨削的方法 161
8.3.6 内圆磨削常见的缺陷与消除措施 162
8.3.7 磨削加工实例 163
8.4 无心磨削 165
8.4.1 无心磨削的特点 165
8.4.2 导轮倾角、转速与工件转速的关系 165
8.4.3 无心外圆磨削的成圆分析 166
8.4.4 无心磨削的方法 167
8.4.5 无心磨削的用量 171
8.4.6 无心外圆磨床的调整 171
8.4.7 无心磨削常见的缺陷及消除措施 173
8.4.8 无心外圆磨削加工实例 175
8.5 齿轮磨削 175
8.5.1 齿轮磨削方法和特点 175
8.5.2 砂轮的选择和平衡 176
8.5.3 磨削余量的确定 177
8.5.4 磨齿误差产生原因与消除方法 177
8.5.5 加工实例 178
8.6 成形磨削 180
8.6.1 成形砂轮磨削法 180
8.6.2 仿形磨削法(靠模法) 180
8.6.3 成形夹具磨削法 180
8.6.4 成形展成磨削法 181
8.6.5 数控加工方法 181
8.6.6 成形砂轮的修整 181
8.6.7 磨削加工实例 182
8.7 刀具磨削 183
8.7.1 刃磨刀具的基本原则 183
8.7.2 刃磨刀具常用机床附件 183
8.7.3 刃磨刀具砂轮的选择 184
8.7.4 刃磨刀具的缺陷及消除措施 185
8.7.5 加工实例 185
8.8 花键轴磨削 188
8.8.1 磨削矩形花键的方法 188
8.8.2 花键轴磨削时砂轮的选择 188
8.8.3 花键轴磨削时的注意事项 189
8.8.4 花键轴磨削常见的质量问题及防止措施 189
8.8.5 花键轴磨削加工实例 190
8.9 螺纹磨削 191
8.9.1 螺纹磨削方法 191
8.9.2 砂轮的选择与修整 192
8.9.3 螺纹磨削产生的误差及消除方法 194
8.9.4 加工实例 195
第9章 高效率磨削 198
9.1 高效率磨削基本原理 198
9.2 重负荷磨削 198
9.3 高速强力外圆磨削 199
9.3.1 高速强力外圆磨削的原理及特点 199
9.3.2 高速强力外圆磨削设备及关键技术 199
9.4 缓进给磨削 199
9.4.1 缓进给磨削原理 199
9.4.2 缓进给磨削的技术特点 200
9.4.3 缓进给磨削设备及关键技术 200
9.5 高效深切磨削 201
9.5.1 高效深切磨削的原理及应用特点 201
9.5.2 高效深切磨削对机床的技术要求 202
9.6 高速与超高速磨削 202
9.6.1 高速与超高速磨削的原理及特点 202
9.6.2 高速和超高速磨削的关键技术 203
9.6.3 超高速磨削在高效率磨削中的应用 207
9.6.4 超高速磨削在难加工材料磨削加工中的应用 207
9.7 快速点磨削 209
9.7.1 快速点磨削相关技术与机床特点 209
9.7.2 快速点磨削的材料去除机理 212
9.7.3 快速点磨削的应用特点 212
9.8 砂带磨削 213
9.8.1 砂带磨削的特点 214
9.8.2 砂带磨削的应用 214
9.8.3 砂带磨削方式 215
9.8.4 砂带磨削的关键技术及参数选择 216
9.8.5 强力砂带磨削 220
9.9 超硬磨料砂带磨削 222
9.9.1 超硬磨料砂带结构与特性 222
9.9.2 超硬磨料砂带的分类 223
9.9.3 金刚石砂带磨削的应用 223
9.9.4 CBN砂带磨削的应用 223
9.9.5 超硬磨料砂带的发展趋势 223
第10章 精密超精密磨粒加工 224
10.1 精密超精密磨粒加工技术的内涵 224
10.1.1 精密超精密磨粒加工技术的界定 224
10.1.2 几个重要概念 224
10.1.3 精密超精密磨粒加工特点 225
10.1.4 精密超精密磨粒加工方法及其分类 225
10.2 精密磨削加工 225
10.2.1 精密磨削加工机理 225
10.2.2 精密磨削加工影响因素 225
10.2.3 精密磨削的工艺参数 226
10.3 超精密磨削加工 227
10.3.1 超精密磨削加工机理 227
10.3.2 超精密磨削加工影响因素 227
10.3.3 超精密磨削的工艺参数 228
10.4 镜面磨削 228
10.4.1 镜面磨削的定义 228
10.4.2 镜面磨削表面的形成机理 228
10.4.3 实现镜面磨削的工艺方法 229
10.4.4 实现镜面磨削磨床应具备的条件 229
10.4.5 镜面磨削的工艺参数 229
10.5 在线电解修锐超精密镜面磨削技术 230
10.5.1 在线电解修锐镜面磨削的特点 230
10.5.2 在线电解修锐镜面磨削实现条件 231
10.5.3 在线电解修锐镜面磨削效果 232
10.6 双端面精密磨削技术 232
10.6.1 双端面精密磨削加工机理 232
10.6.2 双端面精密磨削加工装置 232
10.7 珩磨 233
10.7.1 珩磨的工作原理 233
10.7.2 珩磨头 233
10.7.3 珩磨油石的选择 234
10.7.4 珩磨工艺参数的选择 235
10.7.5 珩磨常见的工件缺陷、产生原因及解决方法 237
10.8 研磨 239
10.8.1 研磨的加工机理 239
10.8.2 研磨加工的特点 240
10.8.3 研磨加工的分类 240
10.8.4 研磨加工的实现条件 240
10.8.5 研磨工艺参数 242
10.8.6 研磨时常见的缺陷及产生原因 242
10.9 抛光 242
10.9.1 抛光的加工原理 243
10.9.2 抛光加工实现的条件 243
第11章 特种磨粒加工方法 245
11.1 特种磨粒加工技术概述 245
11.1.1 特种磨粒加工的定义 245
11.1.2 特种磨粒加工的特点 245
11.2 磁力研磨 245
11.2.1 磁力研磨的工作原理 245
11.2.2 磁力研磨加工的特点 247
11.2.3 磁力研磨加工的应用 247
11.2.4 五自由度并联机器人磁力研磨加工实例 247
11.2.5 磁力研磨加工关键技术 250
11.3 磁力悬浮研磨 251
11.3.1 磁力悬浮研磨的原理 251
11.3.2 磁力悬浮研磨的特点 252
11.3.3 加工实例——磁力悬浮研磨加工陶瓷球 252
11.3.4 磁力悬浮研磨关键技术 253
11.4 磁性流体研磨 253
11.4.1 磁性流体研磨的工作原理 253
11.4.2 磁性流体研磨的特点 253
11.4.3 磁性流体研磨的应用 253
11.5 磁流变抛光 253
11.5.1 磁流变抛光的原理 253
11.5.2 磁流变抛光的特点 254
11.5.3 磁流变抛光的应用 254
11.5.4 磁流液的组成成分 254
11.5.5 磁流变抛光关键技术 255
11.6 磨料流加工 255
11.6.1 磨料流加工的原理 255
11.6.2 磨料流加工的特点 255
11.6.3 磨料流加工的应用 255
11.6.4 磨料流加工去除速度和精度 256
11.6.5 磨料流加工关键技术 256
11.7 弹性发射加工 256
11.7.1 弹性发射加工的原理 256
11.7.2 弹性发射加工的特点 257
11.7.3 弹性发射加工的效果 257
11.8 浮动抛光 257
11.8.1 浮动抛光的工作原理 257
11.8.2 浮动抛光材料去除机理 258
11.8.3 浮动抛光速度 258
11.8.4 浮动抛光的应用 258
11.9 动压浮起平面研磨 259
11.9.1 动压浮起平面研磨的原理 259
11.9.2 动压浮起平面研磨的特点 259
11.9.3 动压浮起平面研磨的应用 259
11.10 水合抛光 259
11.10.1 水合抛光的工作原理 259
11.10.2 水合抛光的特点 260
11.10.3 水合抛光的应用 260
11.11 化学机械抛光 260
11.11.1 化学机械抛光材料去除机理 260
11.11.2 化学机械抛光的特点 261
11.11.3 化学机械抛光的应用 261
11.11.4 化学机械抛光关键技术 261
11.11.5 化学机械抛光加工装置 261
11.12 砂轮约束磨粒喷射加工 262
11.12.1 砂轮约束磨粒喷射加工的原理 262
11.12.2 砂轮约束磨粒喷射加工的特点 263
11.12.3 砂轮约束磨粒喷射加工的应用 263
11.12.4 砂轮约束磨粒喷射加工关键技术 263
11.12.5 砂轮约束磨粒喷射加工实例 263
11.13 磨粒喷射加工 265
11.13.1 工作原理 265
11.13.2 加工装置 265
11.13.3 磨粒喷射加工的分类 265
11.13.4 磨粒喷射加工的特点 266
11.13.5 磨粒喷射加工的应用 266
11.13.6 主要工艺参数 267
11.13.7 磨粒喷射加工关键技术及发展方向 267
11.14 电解磨削 267
11.14.1 电解磨削的工作原理 267
11.14.2 电解磨削加工的特点 268
11.14.3 电解磨削的应用 268
11.15超声波加工 268
11.15.1 工作原理 268
11.15.2 超声波加工的特点及应用 268
11.16电泳磨削技术 269
11.17精密超精密特种磨粒加工技术研究热点 270
第12章 难磨削加工材料的磨削加工 271
12.1 难磨削加工材料的类型及磨削加工特点 271
12.1.1 难磨削加工材料的类型 271
12.1.2 难磨削加工材料磨削加工的特点 272
12.1.3 改善难磨削加工材料磨削性能的措施 272
12.2 不锈钢的磨削加工 272
12.2.1 不锈钢的种类 272
12.2.2 不锈钢磨削的特点 273
12.2.3 不锈钢磨削的参数选择 273
12.2.4 不锈钢磨削加工实例 278
12.3 钛合金的磨削加工 279
12.3.1 钛合金的种类 279
12.3.2 钛合金磨削的特点 280
12.3.3 钛合金磨削的参数选择 280
12.3.4 钛合金磨削加工实例 283
12.4 高温合金的磨削加工 284
12.4.1 高温合金的种类 284
12.4.2 高温合金磨削的特点 285
12.4.3 高温合金磨削的参数选择 286
12.4.4 高温合金磨削加工实例 288
12.5 工程陶瓷的磨削加工 291
12.5.1 工程陶瓷的性能和特点 291
12.5.2 陶瓷磨削的参数选择 293
12.5.3 陶瓷磨削加工实例 295
12.6 玻璃的磨削加工 300
12.6.1 熔融石英玻璃的磨削 300
12.6.2 光学玻璃的磨削 301
12.7 玛瑙的磨削 301
12.8 新高速钢的磨削加工 301
12.8.1 新高速钢磨削加工的特点 302
12.8.2 新高速钢磨削加工时砂轮的选择 303
12.8.3 新高速钢磨削加工时磨削用量和磨削液的选择 304
12.9 钢结硬质合金的磨削加工 304
12.9.1 钢结硬质合金的性能及其磨削加工的特点 304
12.9.2 钢结硬质合金磨削加工时砂轮的选择 305
12.9.3 钢结硬质合金磨削加工时的磨削用量和磨削液 305
12.10 球墨铸铁的磨削加工 305
12.10.1 球墨铸铁材料及其磨削加工的特点 305
12.10.2 球墨铸铁磨削加工时砂轮的选择 305
12.10.3 球墨铸铁磨削加工的工艺条件 306
12.11 铜、铝合金的磨削加工 306
12.11.1 铜、铝合金磨削的特点 306
12.11.2 铜、铝合金磨削时砂轮的选择 307
12.11.3 铜、铝合金磨削加工的工艺条件 307
参考文献 308
- 《钒产业技术及应用》高峰,彭清静,华骏主编 2019
- 《现代水泥技术发展与应用论文集》天津水泥工业设计研究院有限公司编 2019
- 《激光加工实训技能指导理实一体化教程 下》王秀军,徐永红主编;刘波,刘克生副主编 2017
- 《英汉翻译理论的多维阐释及应用剖析》常瑞娟著 2019
- 《数据库技术与应用 Access 2010 微课版 第2版》刘卫国主编 2020
- 《区块链DAPP开发入门、代码实现、场景应用》李万胜著 2019
- 《虚拟流域环境理论技术研究与应用》冶运涛蒋云钟梁犁丽曹引等编著 2019
- 《当代翻译美学的理论诠释与应用解读》宁建庚著 2019
- 《第一性原理方法及应用》李青坤著 2019
- 《先进激光加工技能实训》肖海兵主编 2019
- 《市政工程基础》杨岚编著 2009
- 《家畜百宝 猪、牛、羊、鸡的综合利用》山西省商业厅组织技术处编著 1959
- 《《道德经》200句》崇贤书院编著 2018
- 《高级英语阅读与听说教程》刘秀梅编著 2019
- 《计算机网络与通信基础》谢雨飞,田启川编著 2019
- 《看图自学吉他弹唱教程》陈飞编著 2019
- 《法语词汇认知联想记忆法》刘莲编著 2020
- 《培智学校义务教育实验教科书教师教学用书 生活适应 二年级 上》人民教育出版社,课程教材研究所,特殊教育课程教材研究中心编著 2019
- 《国家社科基金项目申报规范 技巧与案例 第3版 2020》文传浩,夏宇编著 2019
- 《流体力学》张扬军,彭杰,诸葛伟林编著 2019