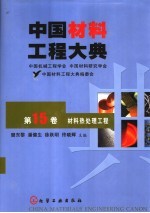
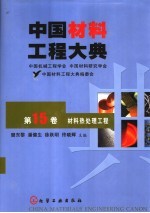
中国材料工程大典 第15卷 材料热处理工程PDF电子书下载
- 电子书积分:24 积分如何计算积分?
- 作 者:樊东黎,潘建生,徐跃明,佟晓辉主编
- 出 版 社:北京:化学工业出版社
- 出版年份:2006
- ISBN:7502573178
- 页数:923 页
第1篇 概论 1
1.4 形变热处理 3
1.3 化学热处理 3
第1章 材料热处理在现代制造业中的地位和作用 3
1 热处理工艺种类 3
1.1 整体热处理 3
1.2 表面热处理 3
2.1 提高材料的各种力学性能 4
2 提高和发挥材料性能的潜力 4
1.5 等离子热处理 4
1.6 表面沉积技术 4
1.7 镀层复合热处理 4
2.4 提高材料的工艺性能 5
2.3 提高材料的化学性能 5
2.2 提高材料的物理性能 5
3 热处理与相邻加工工艺的关系 6
1 中国古代的热处理 7
第2章 材料热处理技术发展史 7
2 中国近代热处理进展 9
2.2 科研、开发和新技术应用成果 10
2.1 热处理行业现状 10
2.3 热处理标准化的进展 12
2.4 热处理行业、学术团体 13
2.1 可持续发展战略 14
2 热处理的总体发展战略 14
第3章 热处理技术展望 14
1 历史的回顾 14
3.1 少无污染 15
3 先进热处理技术的发展方向 15
2.2 产品质量的不断提高 15
2.3 能源的有效利用 15
2.4 精确的生产过程 15
2.5 高效的生产技术 15
3.2 少无畸变 17
3.4 少无浪费(能源) 19
3.3 少无(质量)分散 19
3.5 少无氧化 21
4 热处理生产技术改造的途径 26
3.8 少无人工 26
3.6 少无脱碳 26
3.7 少无废品 26
4.3 不断提高新技术开发能力 27
4.2 知识和技能的再教育 27
4.1 设备更新 27
参考文献 28
第2篇 材料热处理技术基础 29
5 常用热处理工艺代号 31
4 多工序热处理工艺代号 31
第1章 金属热处理工艺分类和代号 31
1 基础分类 31
2 附加分类 31
3 热处理工艺代号 31
6 技术要求在零件图样上的表示方法 32
1.1 总类 38
1 金属热处理工艺术语 38
第2章 材料热处理术语 38
1.2 退火类 39
1.3 淬火类 40
1.6 渗碳类 41
1.5 固溶热处理类 41
1.4 回火类 41
1.10 表面处理及复合热处理类 42
1.9 共渗类 42
1.7 渗氮类 42
1.8 渗其他非金属及渗金属类 42
1.12 组织类 43
1.11 沉积类 43
2.1 一般术语 44
2 热处理设备术语 44
1.13 热处理缺陷类 44
2.2 热处理炉通用术语 45
2.3 热处理电热设备 46
2.6 淬火冷却装置 47
2.5 热处理燃料炉 47
2.4 热处理炉通用配套设备 47
3.3 热处理盐浴用盐类 48
3.2 热处理常用气氛类 48
2.7 清洗与清理设备 48
2.8 其他辅助设备 48
3 热处理工艺材料术语 48
3.1 总类 48
3.6 热处理保护涂料类 49
3.5 淬火冷却介质类 49
3.4 渗其他非金属剂与渗金属剂及其共渗剂类 49
1 Fe-Fe3C合金相图及其应用 51
第3章 合金相图与金属热处理的关系 51
2.1 Fe-C合金相图与热处理温度的关系 53
2 合金元素对钢铁组织和性能的影响 53
2.2 合金元素的影响 54
3 其他金属合金相图 58
1.2 铁素体-珠光体向奥氏体的等温转变 82
1.1 珠光体-奥氏体转变 82
第4章 材料热处理的加热 82
1 钢在加热过程中的转变 82
1.3 连续加热时的奥氏体形成过程 83
1.5 钢的晶粒度对性能的影响 85
1.4 钢加热时的奥氏体晶粒长大 85
1.7 过热和过烧 86
1.6 奥氏体晶粒度的显示和测定 86
1.8 氧化和脱碳 87
2 钢在CO-CO2气氛中的氧化和脱碳 89
3 钢在H2-H2O气氛中的氧化和脱碳 91
4 含硫气体对钢的作用 92
5.2 加热计算公式及常用图表 93
5.1 加热介质分类 93
5 加热介质和加热计算 93
6.2 制备方法 96
6.1 分类及用途 96
6 可控气氛 96
6.3 炉气控制原理 113
6.4 炉气检测方法 115
7.1 加热熔盐的成分及用途 119
7 加热熔盐和流态床 119
7.2 盐浴的脱氧及脱氧剂 122
7.4 流态床加热的特点 123
7.3 长效盐 123
8.1 金属在真空中加热时的行为 127
8 真空中的加热 127
8.2 金属在真空中的加热速度 128
1.1 过冷奥氏体等温转变图 129
1 钢的过冷奥氏体转变 129
第5章 材料热处理的冷却 129
1.3 钢的淬透性和奥氏体连续冷却转变图的关系 130
1.2 奥氏体连续冷却转变图 130
2.1 马氏体转变的本质 131
2 钢在冷却过程中的马氏体转变 131
3.2 金属在液态介质中冷却的特征 132
3.1 淬火冷却曲线 132
2.2 马氏体转变量和转变温度范围 132
2.3 马氏体形态 132
3 金属热处理的冷却过程 132
4.2 Grossmann的淬透性概念 133
4.1 概述 133
4 钢的淬透性 133
4.3 钢淬透性测定方法 134
5 淬火冷却方式和淬火介质 135
5.1 埋入淬火 136
5.2 喷射冷却 149
5.3 熔盐等温淬火 150
5.4 流态床淬火 152
5.5 气冷淬火 153
5.6 强烈淬火 154
5.7 淬火介质性能测试方法 155
5.8 淬火冷却的畸变与开裂 156
1 概述 159
第6章 热处理工艺材料 159
2.2 热处理加热用盐 160
2.1 制备气氛的原料气 160
2 热处理的加热介质 160
3 热处理淬冷介质 163
2.4 回火油 163
2.3 流动粒子 163
3.1 淬火油 164
3.2 聚合物淬火剂 167
4.2 碳氮共渗剂 172
4.1 渗碳剂 172
4 热处理渗剂 172
7 防渗涂料 173
6 不锈钢箔 173
4.3 渗硼剂 173
4.4 渗金属剂 173
5 防氧化脱碳涂料 173
9.2 防锈剂 174
9.1 清洗剂 174
8 表面处理剂 174
9 辅助材料 174
9.4 催化剂 175
9.3 干燥剂和吸收剂 175
1.2 热处理工艺性在机械制造工艺过程中的作用和意义 176
1.1 零件热处理工艺性的基本概念 176
第7章 零件热处理工艺性 176
1 概述 176
2.1 零件结构 177
2 零件热处理工艺性的内容和影响因素 177
1.3 零件热处理工艺性的特点 177
2.2 零件的材料 178
2.3 热处理工艺因素 189
2.4 影响零件热处理工艺性的其他因素 191
3 改善零件热处理工艺的根本途径 192
1 概述 194
第8章 材料热处理缺陷、预防和修正 194
2.2 加热不当形成的裂纹 196
2.1 热处理裂纹形成的机理 196
2 热处理裂纹 196
2.3 淬火裂纹 197
2.4 淬火裂纹的预防方法 200
2.5 其他热处理裂纹 207
3.1 热处理畸变类型及形成原因 208
3 热处理畸变 208
3.2 淬火畸变 209
3.3 化学热处理畸变 214
3.4 热处理变形的校正 216
4.1 热处理内应力 217
4 残余内应力 217
4.2 残余应力对力学性能的影响 220
4.3 残余应力的调整和消除 222
5 组织不合格 223
5.1 氧化与脱碳 224
5.2 过热与过烧 225
5.4 渗碳组织缺陷 227
5.3 低、中碳钢预备热处理球化体级别不合格 227
5.5 渗氮组织缺陷 229
5.6 渗硼组织缺陷 230
6.1 硬度不合格 231
6 力学性能不合格 231
6.2 拉伸性能不合格 232
6.3 持久蠕变性能不合格 233
6.4 非铁金属合金力学性能不合格 234
6.6 耐腐蚀性能不良 235
6.5 疲劳性能不良 235
7 脆性 236
7.1 回火脆性 237
7.2 低温脆性 239
7.3 氢脆性 240
7.5 渗层脆性 243
7.4 σ脆性 243
8.1 化学热处理和表面热处理特殊缺陷 244
8 其他热处理缺陷 244
8.2 真空热处理和加热保护热处理缺陷 245
8.3 非铁金属合金热处理缺陷 247
1.1 关于热处理的国际标准和国外先进标准 251
1 概述 251
第9章 材料热处理标准 251
2 热处理标准体系表 252
1.2 关于全国热处理标准化技术委员会 252
2.3 体系表的特点 253
2.2 体系表结构及内容 253
2.1 制、修订概况 253
2.4 热处理专业标准体系明细表 254
3 材料热处理标准 258
参考文献 263
第3篇 材料热处理工艺 265
1.1 钢的退火与正火 267
1 钢的热处理 267
第1章 材料和零件的整体热处理 267
1.2 钢的淬火 270
1.3 钢的回火 279
2.1 铸铁的分类和应用 284
2 铸铁的热处理 284
2.2 铸铁热处理基础 285
2.3 白口铸铁的热处理 290
2.4 灰铸铁的热处理 291
2.5 球墨铸铁的热处理 294
2.6 可锻铸铁的热处理 300
1.1 钢在快速加热时的组织转变 306
1 表面热处理原理 306
第2章 表面热处理 306
1.2 钢快速加热对冷却转变的影响 308
1.4 表面淬火时的残余应力 309
1.3 快速循环加热淬火法制备超细化晶粒 309
2.1 火焰加热表面淬火原理及优缺点 311
2 火焰加热表面淬火 311
2.3 火焰淬火喷嘴 312
2.2 火焰的结构及其特征 312
2.5 火焰淬火前的准备工作及操作 313
2.4 火焰淬火工艺 313
2.6 火焰加热表面淬火的应用 314
3.1 感应加热的原理 315
3 感应加热表面热处理 315
3.2 感应器 318
3.3 感应加热工艺 320
3.4 感应加热淬火的应用 324
3.5 感应加热表面淬火后的组织和性能 328
4.1 激光的产生及其特点 329
4 激光加热表面热处理 329
4.2 激光加热表面淬火的表面预处理 332
4.5 激光淬火对显微组织结构及性能的影响 333
4.4 激光淬火工艺参数选择 333
4.3 激光淬火工艺的特点 333
4.6 激光淬火层性能 335
4.8 激光淬火技术的应用 336
4.7 激光淬火加其他强化方法的复合处理工艺 336
5.1 电子束加热装置原理 337
5 电子束加热表面热处理 337
4.9 激光表面重熔 337
5.2 电子束和材料的交互作用 338
5.3 电子束表面处理的特点 339
5.4 电子束表面处理工艺 340
1.2 碳在钢中的扩散 342
1.1 基本规律 342
第3章 化学热处理 342
1 原子扩散 342
1.3 氮在钢中的扩散 343
2.1 气体渗氮 344
2 钢的低温化学热处理 344
2.2 离子渗氮 349
2.3 气体氮碳共渗 351
2.4 盐浴硫氮碳共渗 354
2.5 渗锌 356
2.6 低温化学热处理的渗层组织和性能 357
3.1 渗碳和碳氮共渗 358
3 钢的高温化学热处理 358
3.2 渗硼 367
3.3 渗金属 369
3.4 钢铁热浸铝和渗铝 372
1.3 形变热处理的工业应用 377
1.2 形变热处理的基本原理 377
第4章 形变热处理 377
1 概述 377
1.1 形变热处理的发展沿革 377
1.4 形变热处理的方法分类 378
2.1 低温形变热处理工艺 379
2 低温形变热处理 379
2.3 钢低温形变热处理后的力学性能 383
2.2 钢低温形变热处理后的组织 383
2.4 低温形变淬火强化机理 389
3.1 工艺参数对高温形变淬火效果的影响 391
3 高温形变热处理 391
3.2 高温形变淬火钢的组织 394
3.3 钢高温形变热处理后的力学性能 396
3.4 高温形变淬火强化机理 401
3.5 钢的锻热淬火 402
3.6 控制轧制 404
3.7 非调质钢 405
4.1 形变诱发马氏体相变 406
4 马氏体相变过程中的形变 406
4.2 变塑现象和变塑钢 407
5.1 马氏体形变强化的特点 408
5 马氏体相变后的形变 408
5.3 淬火马氏体的形变时效 409
5.2 马氏体形变强化的原因 409
5.4 回火马氏体的形变时效 410
6.1 应力与形变对过冷奥氏体分解过程的影响 411
6 形变与扩散型相变相结合的形变热处理 411
5.5 大形变量的马氏体形变时效 411
6.2 在扩散型相变前进行形变 412
6.3 在扩散型相变中进行形变(等温形变淬火) 414
6.4 在扩散型相变后进行形变 416
7.1 利用强化效果遗传性的形变热处理 418
7 其他形变热处理方法 418
7.2 预先形变热处理 419
7.3 多边化强化 420
7.4 表面形变热处理 421
7.5 形变化学热处理 423
8.2 铜合金的形变热处理 425
8.1 铝合金的形变热处理 425
7.6 晶粒超细化处理 425
7.7 复合形变热处理 425
8 非铁金属的形变热处理 425
1.2 低压气体放电 426
1.1 等离子体 426
第5章 等离子体热处理 426
1 等离子体热处理基础 426
2.1 等离子体化学热处理的基本原理 431
2 等离子体化学热处理 431
2.2 等离子体化学热处理设备 434
2.3 等离子体化学热处理工艺 435
3.1 等离子体物理气相沉积 440
3 离子沉积技术 440
3.2 等离子体化学气相沉积 446
4.2 等离子体基离子注入技术的工作模式 448
4.1 等离子体基离子注入技术的基本原理 448
4 等离子体基离子注入技术 448
4.4 离子注入技术改善表面性能的机理 449
4.3 等离子体基离子注入技术的特点 449
4.5 等离子体基离子注入技术的应用 450
1.1 硬质涂层气相沉积技术的进展 451
1 硬质涂层 451
第6章 化学气相沉积和物理气相沉积 451
1.3 硬质涂层对工业发展的贡献 452
1.2 常用硬质涂层材料种类 452
2.3 高温化学气相沉积技术 453
2.2 化学气相沉积技术分类 453
2 化学气相沉积 453
2.1 化学气相沉积概述 453
2.4 中温化学气相沉积(MT-CVD)技术 460
2.5 低温化学气相沉积技术 463
3.3 物理气相沉积的物理基础简介 465
3.2 物理气相沉积分类 465
3 物理气相沉积 465
3.1 物理气相沉积概述 465
3.4 各种物理气相沉积技术 468
4.2 金刚石涂层的沉积技术 482
4.1 非金属化合物超硬涂层种类 482
4 非金属化合物超硬涂层气相沉积技术 482
5.1 复合超硬涂层材料沉积技术的提出 483
5 复合超硬涂层材料沉积技术 483
4.3 立方氮化硼(CBN)涂层的沉积技术 483
4.4 氮化碳(β-C3N4)涂层沉积技术 483
6.2 硬质涂层工具、模具应用举例 484
6.1 硬质涂层的应用技术 484
5.2 复合超硬涂层沉积技术 484
6 硬质涂层工具、模具应用技术及举例 484
7.1 硬质涂层的性能测试 486
7 硬质涂层质量检测 486
7.2 硬质涂层微观结构的测试 487
参考文献 490
第4篇 热处理设备 495
2 热处理冷却设备 497
1 热处理加热设备 497
第1章 热处理设备分类 497
4 热处理辅助设备 498
3 热处理清洗和清理设备 498
6 热处理环境保护设备 499
5 热处理质量检测设备 499
第2章 真空热处理设备 500
1 气冷真空炉 501
2 油冷真空炉 504
4 多用途真空炉 505
3 水冷真空炉 505
8 真空烧结炉 506
7 真空钎焊炉 506
5 真空回火炉 506
6 真空渗碳炉 506
10 等离子热处理炉 507
9 台车式真空炉 507
2 普通型箱式电阻炉 510
1 热处理电阻炉结构 510
第3章 热处理电阻炉 510
3 台车式电阻炉 512
4 井式电阻炉 513
5 钟罩式炉 515
6 密封箱式炉 516
8 推杆式炉 518
7 转筒式炉 518
9 输送带式炉及其生产线 520
10 振底式炉 522
13 滚筒式炉(鼓形炉) 524
12 转底式炉 524
11 辊底式炉 524
15 牵引式炉 525
14 步进式和摆动步进式炉 525
16 自动化热处理设备 526
1 浴炉的分类 528
第4章 浴炉及流态粒子炉 528
3 外部电加热中温浴炉 529
2 低温浴炉 529
4 燃料加热中温浴炉 530
6 埋入式电极浴炉 531
5 插入式电极盐浴炉 531
7 流态粒子炉 532
2 燃料炉炉型选择 535
1 常用燃料炉分类 535
第5章 热处理燃料炉 535
3 燃料炉附属设备 536
4 燃油烧嘴 539
5 燃煤机 541
6 预热器 543
1 电子管式高频变频装置 545
第6章 热处理感应加热及火焰加热装置 545
3 晶体管(IGBT)式超音频变频装置 546
2 晶体管式高频变频装置 546
4 机式中频变频装置 547
5 晶闸管式中频变频装置 548
7 感应加热用热处理设备 549
6 工频感应加热装置 549
8 火焰表面加热装置 552
1 激光表面热处理装置 553
第7章 表面热处理设备 553
3 气相沉积装置 554
2 电子束表面改性装置 554
2 淬火槽 556
1 淬火冷却设备分类 556
第8章 热处理冷却设备 556
5 淬火介质冷却 557
4 淬火槽加热装置 557
3 淬火介质搅拌 557
6 淬火槽输送机械 558
9 冷处理设备 559
8 淬火机床 559
7 冷却过程的控制装置 559
1.1 吸热式气氛发生装置 561
1 可控气氛发生装置 561
第9章 热处理辅助设备 561
1.2 放热式气氛发生装置 563
2 工业氮制备装置 564
4 清洗设备 566
3 氨分解气氛发生装置 566
5 清理及强化设备 568
6 矫直(校直)设备 569
7 起重运输设备 570
参考文献 572
第5篇 材料热处理 573
1.1 钢的分类及编号原则 575
1 概述 575
第1章 钢铁材料热处理 575
1.2 常用合金元素 577
2.2 渗碳钢 584
2.1 低碳马氏体钢 584
2 淬火低温回火合金结构钢及其热处理 584
2.3 滚动轴承钢 588
3.3 弹簧钢的品种 590
3.2 成分特点 590
3 弹簧钢及其热处理工艺 590
3.1 性能要求 590
3.5 特殊性能弹簧用钢和弹性合金 591
3.4 热处理工艺 591
4.4 调质钢零件的表面强化 594
4.3 调质钢的热处理 594
4 调质钢及其热处理工艺 594
4.1 调质钢的性能要求 594
4.2 调质钢的成分特点 594
4.5 调质钢热处理技术的进展 598
5.2 刃具用钢 600
5.1 概述 600
5 工具钢及其热处理工艺 600
5.3 低合金刃具钢 601
5.4 高速钢 602
5.5 模具用钢 606
6.1 不锈钢 610
6 特殊钢及其热处理工艺 610
6.2 耐热钢 616
6.3 易切削钢和冷塑性成型用钢 619
1.1 铝及铝合金 622
1 铝及铝合金的热处理 622
第2章 非铁金属的热处理 622
1.2 变形铝合金的退火 625
1.3 变形铝合金的固溶 626
1.4 变形铝合金的时效 627
1.6 变形铝合金加工及热处理状态标记 630
1.5 变形铝合金的其他热处理 630
1.7 铸造铝合金的热处理 631
2.1 铜及铜合金 633
2 铜及铜合金的热处理 633
1.8 铝合金的热处理缺陷 633
2.4 青铜的热处理 638
2.3 黄铜的热处理 638
2.2 工业纯铜的热处理 638
3.1 钛及钛合金 641
3 钛及钛合金的热处理 641
2.5 白铜的热处理 641
2.6 铜及铜合金热处理应注意的问题 641
3.2 钛合金的退火 644
3.5 钛合金热处理应注意的问题 646
3.4 钛合金的形变热处理 646
3.3 钛合金的固溶和时效 646
4.1 镁及镁合金 647
4 镁合金的热处理 647
4.3 镁合金的固溶处理和时效 648
4.2 镁合金的退火热处理 648
5.1 镍和镍合金的热处理 649
5 其他非铁金属的热处理 649
5.2 钨、钼热处理 650
1.2 铁基粉末冶金件的应用 651
1.1 铁基粉末冶金材料的分类 651
第3章 粉末冶金材料和零件的热处理 651
1 铁基粉末冶金件的热处理 651
1.3 铁基粉末冶金件的热处理 653
2.1 钢结硬质合金的特点、牌号、性能和用途 658
2 钢结硬质合金的热处理 658
2.2 钢结硬质合金的热处理 660
2.3 钢结碳质合金的组织与性能 661
3.1 粉末高速钢类别和性能 662
3 粉末高速钢的热处理 662
4.1 硬质合金的分类和用途 663
4 硬质合金的热处理 663
3.2 热等静压和热挤压粉末高速钢 663
4.2 硬质合金的热处理 664
1.1 金属磁性的物理基础 667
1 磁性合金的热处理 667
第4章 功能合金的热处理 667
1.2 软磁合金的热处理 669
1.3 永磁合金的热处理 680
2.1 金属的热膨胀特性 692
2 膨胀合金的热处理 692
2.2 低膨胀合金的热处理 693
2.3 铁磁性定膨胀合金的热处理 698
2.4 无磁性定膨胀合金的热处理 704
2.5 高膨胀合金的热处理 707
3.1 金属的弹性性能 709
3 弹性合金的热处理 709
3.2 高弹性合金的热处理 711
3.3 恒弹性合金的热处理 728
4.1 合金的超弹性和形状记忆效应 734
4 形状记忆合金及其热处理 734
4.2 钛镍形状记忆合金 737
4.3 铜基形状记忆合金 744
4.4 形状记忆合金的应用 749
1.2 传质机理 754
1.1 烧结驱动力 754
第5章 陶瓷和硅酸盐材料的热处理 754
1 陶瓷材料的烧结 754
2.2 ZrO2陶瓷中的t-m相变 755
2.1 ZrO2陶瓷中的c-t相变 755
1.3 气氛对烧结的影响 755
2 温度对陶瓷相变的影响 755
3 熔体和玻璃体与温度的关系 756
3.2 玻璃的形成 757
3.1 熔体结构的形成 757
1.1 铝基复合材料的强化热处理 758
1 金属基复合材料的强化热处理 758
第6章 复合材料的热处理 758
1.2 镁合金基复合材料的强化热处理 762
1.3 钛合金基复合材料的强化热处理 763
2.1 概述 766
2 金属基复合材料尺寸稳定化热处理 766
2.2 铝合金基复合材料的冷热循环尺寸稳定化处理 767
2.3 铝合金基复合材料的深冷尺寸稳定化处理 768
参考文献 770
第6篇 热处理CAD/CAM/CAE 771
1.4 生产经验信息化处理 773
1.3 热处理专家系统 773
第1章 概述 773
1 热处理计算机辅助工程分析和工艺编制 773
1.1 知识重用 773
1.2 热处理数据库 773
4 热处理设备智能CAD技术 774
3 热处理智能控制技术 774
2 热处理数学建模与计算机模拟 774
5.3 面向绿色制造的CAD/CAE技术 775
5.2 产品制造全过程的CAE/CAPP 775
4.1 热处理设备的知识重用技术 775
4.2 热处理设备的科学计算 775
4.3 热处理设备研究开发的决策系统 775
5 热处理CAD/CAE/CAM与计算机集成制造 775
5.1 轻量化高可靠产品的设计制造 775
4 热处理计算机模拟技术的局限性 776
3 热处理的数值模拟与实验研究的关系 776
第2章 热处理计算机模拟的主要特点 776
1 理论知识和定量科学计算直接应用于热处理生产 776
2 计算机模拟使热处理向多学科交叉的综合性科学技术的方向发展 776
3 有限差分法 777
2 求解偏微分方程的方法 777
第3章 热处理计算机模拟的基本方法 777
1 描述热处理过程的偏微分方程 777
4.1 单元划分 779
4 用有限元法求解瞬态温度场 779
4.2 用加权余值法进行有限元分析 780
5.1 相变的计算 782
5 瞬态温度场与相变的耦合 782
4.3 三维瞬态导热的有限元分析 782
5.4 相变超塑性 784
5.3 应力对相变动力学的影响 784
5.2 马氏体转变的计算 784
6 界面换热系数的测定与计算 785
1.2 热弹塑性本构关系 787
1.1 热弹性本构方程 787
第4章 热处理过程中应力场的数值计算 787
1 热弹塑性应力场分析的基本原理 787
1.4 组织转变对应力场的影响 788
1.3 温度对应力场的影响 788
1.5 热弹塑性应力场分析的主要算法 789
2.2 热弹性有限元分析的方程 790
2.1 虚功原理和最小位能原理 790
2 热弹塑性应力场的有限元计算 790
2.4 淬火应力场分析中总应变的处理 791
2.3 热弹塑性应力应变关系 791
3 淬火应力场的求解及边界条件 792
2 流场动力学模拟 793
1 化学热处理瞬态浓度场的数值模拟 793
第5章 瞬态浓度场模拟与流场动力学模拟 793
1.2 优化加热工艺的CAD技术 795
1.1 三维温度场计算机模拟的实验验证 795
第6章 应用实例 795
1 阶梯轴加热CAE 795
2 高硬冷轧辊淬火工艺CAE 796
3 复杂形状零件淬火操作CAE/CAPP 798
5 气体渗碳CAE/CAPP/CAM 799
4 曲轴渗氮畸变控制CAE 799
6 气体渗碳CAE/CAM 800
8 热处理设备的智能CAD 802
7 基于计算机模拟的动态可控渗氮技术 802
参考文献 804
第7篇 热处理清洁生产和安全 805
1.5 电磁辐射 807
1.4 废渣 807
第1章 热处理的清洁生产 807
1 热处理生产的污染源 807
1.1 引起大气污染的主要根源 807
1.2 对水质的污染 807
1.3 噪声污染 807
2 环境的控制和治理 808
3.2 废水排放 809
3.1 废气及烟尘排放 809
3 热处理三废的排放 809
4.2 JB/T 5073—1991规定的热处理车间空气中有害物质的最高允许浓度 810
4.1 先进工业国家规定的空气中有害物质的限值 810
3.3 固体废物 810
4 空气中有害物质的限值 810
5.1 国外情况 811
5 热处理盐浴有害固体废物污染的管理 811
5.2 JB/T 9052—1999关于热处理盐浴有害废弃物的规定 812
6.2 盐浴固体废物及其毒性试验方法 813
6.1 国内外情况 813
6 热处理盐浴有害固体废物无害化处理方法 813
6.3 盐浴废渣的无害化处理 814
7.2 分析方法 815
7.1 与本标准有关的国内外标准概况 815
7 热处理盐浴有害固体废物的分析 815
2.1 易燃物质 817
2 热处理生产中的危险因素 817
第2章 热处理的安全生产 817
1 生产过程安全卫生的重要性 817
2.2 易爆物质 819
2.3 毒性物质 820
2.4 高压电 821
3.1 热辐射 822
3 热处理生产中的有害因素 822
2.5 炽热物体及腐蚀性物质 822
2.6 致冷剂 822
2.7 坠落物体或迸出物 822
3.3 噪声 823
3.2 电磁辐射 823
3.5 有害气体 824
3.4 粉尘 824
5.1 生产物料 826
5 生产物料和剩余物料 826
4 热处理生产作业环境 826
4.1 定义 826
4.2 车间卫生 826
4.3 作业场地空气中有害物质的最高允许浓度 826
4.4 噪声控制 826
4.5 照度标准及应急照明 826
4.6 设备间的距离 826
4.7 车间通道、安全标志和报警装置 826
6.1 电阻炉 827
6 生产装置 827
5.2 剩余物料 827
6.2 燃烧炉 828
6.3 盐浴炉和流动粒子炉 830
6.6 激光和电子束的热处理装置 831
6.5 离子化学热处理设备 831
6.4 感应加热装置 831
6.8 火焰加热淬火装置 832
6.7 淬火及回火油槽 832
6.9 可控气氛的制备和可控气氛炉 833
6.13 酸浸设备 835
6.12 喷砂、喷丸和高压水清理设备 835
6.10 冷处理设备 835
6.11 清洗设备 835
7.1 一般要求 836
7 热处理工艺作业 836
6.14 校直机 836
6.15 炉用构件、料盘和夹具 836
7.4 盐浴热处理 837
7.3 化学热处理 837
7.2 表面热处理 837
8.1 基本要求 838
8 安全、卫生防护技术措施 838
7.5 真空热处理 838
8.2 “四防” 839
参考文献 840
第8篇 热处理质量控制与无损检测 841
2 热处理质量控制体系 843
1 热处理质量管理的目的及主要内容 843
第1章 热处理生产的质量管理 843
4.2 工艺文件编制 844
4.1 工艺试验 844
3 产品设计中的热处理质量控制 844
4 工艺设计中的质量控制 844
5.2 零件材料的化学成分分析 848
5.1 原材料控制的主要内容 848
5 原材料质量控制 848
1 热处理设备质量控制 856
第2章 热处理工序的过程质量控制 856
2 热处理质量检验控制 859
4 热处理质量控制中常用的统计技术 860
3 操作者技能和责任质量控制 860
1.3 硫、磷元素的偏析 862
1.2 低倍检验的一般方法 862
第3章 热处理件的宏观和微观组织检验 862
1 原材料缺陷的低倍检验 862
1.1 常见的低倍缺陷特征 862
2.3 常用的断口分析方法 863
2.2 断口样品的切取和制备 863
2 断口分析 863
2.1 断口分析的用途 863
2.4 典型断口形貌特征 864
3.1 光学显微镜分析方法 865
3 显微组织检验 865
3.2 定量金相分析方法 868
3.3 晶粒度测定方法 870
3.5 电子显微镜分析方法 872
3.4 高温和低温金相分析方法 872
3.6 钢铁零件典型热处理显微组织与缺陷的金相特征 873
1.1 布氏硬度 875
1 硬度 875
第4章 力学性能试验 875
1.2 洛氏硬度 877
1.3 维氏硬度和显微硬度 878
1.5 硬度与强度及各种硬度之间的换算 882
1.4 肖氏硬度和里氏硬度 882
1.6 典型硬度计简介 886
2.2 性能指标的计算 888
2.1 试样 888
2 拉伸 888
4 弯曲 889
3 压缩 889
2.3 缺口拉伸与缺口偏拉伸 889
2.4 高温拉伸和低温拉伸 889
6 冲击 890
5 扭转 890
7 疲劳 891
8 断裂韧度 892
2 X射线法 894
1 应力释放法 894
第5章 残余应力测定 894
5 深层应力分布测量 896
4 超声波法 896
3 磁性法 896
1.1 磁化方法 897
1 磁粉探伤 897
第6章 热处理质量的无损检测方法 897
1.2 磁化规范 899
1.5 磁粉探伤的操作 900
1.4 磁粉探伤设备 900
1.3 磁粉与磁悬液 900
1.6 磁痕分析 901
2 涡流探伤 902
3 渗透法探伤 903
4.2 超声波探伤仪 908
4.1 超声波探伤方法的种类 908
4 超声波探伤 908
4.4 探头 909
4.3 试块 909
4.5 检测 910
5 X射线探伤 912
5.1 X射线探伤设备 913
5.2 X射线照相 916
5.4 射线CT技术 917
5.3 X射线电视探伤 917
4 点腐蚀 919
3 均匀腐蚀试验 919
第7章 耐腐蚀性能测试 919
1 工程上常见的腐蚀类型 919
2 腐蚀速率评定方法 919
5 晶间腐蚀 920
8 大气腐蚀与高温氧化 921
7 应力腐蚀开裂 921
6 缝隙腐蚀 921
参考文献 923
- 《市政工程基础》杨岚编著 2009
- 《工程静力学》王科盛主编 2019
- 《中央财政支持提升专业服务产业发展能力项目水利工程专业课程建设成果 设施农业工程技术》赵英编 2018
- 《化学反应工程》许志美主编 2019
- 《绿色过程工程与清洁生产技术 张懿院士论文集精选 上》《绿色过程工程与清洁生产技术》编写组编 2019
- 《软件工程》齐治昌,谭庆平,宁洪编著 2019
- 《大数据Hadoop 3.X分布式处理实战》吴章勇,杨强 2020
- 《材料导论》张会主编 2019
- 《化学工程与工艺专业实验指导》郭跃萍主编 2019
- 《华乐大典 琵琶卷 乐曲篇 下》中国民族管弦乐学会 2016
- 《海明威书信集:1917-1961 下》(美)海明威(Ernest Hemingway)著;潘小松译 2019
- 《旅伴文库 白衣女人》潘华凌译;(英)威尔基·柯林斯 2019
- 《南方快车》朱卫净,潘丽萍责编;吴娴敏译者;(智利)路易斯·塞普尔维达 2019
- 《流体力学与传热学》潘小勇编著 2019
- 《京剧音乐基础教程》杨晓辉,何群,齐欢编著 2018
- 《面向工程教育的本科计算机类专业系列教材 普通高等教育“十一五”国家级规划教材 计算机网络 第3版》胡亮,徐高潮,魏晓辉,车喜龙编 2018
- 《虚拟现实与人工智能技术的综合应用》潘晓霞著 2018
- 《海明威书信集:1917-1961 上》(美)海明威(Ernest Hemingway)著;潘小松译 2019
- 《中国城市发展报告 No.12 大国治业之城市经济转型》潘家华,单菁菁主编 2019
- 《威慑赛博战 加强赛博空间的战略稳定性》况晓辉,李响,曹华阳,林哲超 2019