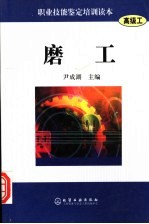
第1章 磨削基础 1
1.1 磨削技术概述 1
1.1.1 磨削技术概况 1
1.1.2 磨削方法 3
1.1.3 磨削工艺系统 3
1.2 磨削原理 5
1.2.1 磨削运动和磨削用量 6
1.2.2 磨削过程 9
1.2.3 磨削要素 11
1.2.5 磨削热和磨削温度 15
1.2.4 磨削力与磨削功率 15
1.2.6 磨削液 17
第2章 磨床 26
2.1 磨床概述 26
2.1.1 磨床的类型及型号 26
2.1.2 磨床品种的组成 29
2.1.3 磨床的精度 32
2.2 磨床的传动 35
2.2.1 磨床的布局和用途 35
2.2.2 磨床的机械传动 38
2.2.3 磨床液压传动系统 41
2.3 磨床的主要结构 48
2.3.1 砂轮架及其轴承 48
2.2.4 磨床伺服系统 48
2.3.2 内圆磨具及其支架 50
2.3.3 头架 51
2.3.4 尾架 53
2.3.5 横进给机构 54
2.3.6 滚动导轨和滚珠丝杠 57
2.4 磨床电气控制 61
2.4.1 常用低压电器 61
2.4.2 异步电动机的电气控制 71
2.4.3 直流电动机的电气控制 78
2.4.4 M1432A型万能外圆磨床的电气控制 83
2.5.1 平面磨床 87
2.5 其他磨床 87
2.5.2 内圆磨床 88
2.5.3 无心磨床 89
2.5.4 半自动磨床及数控磨床 89
2.6 磨床的维护保养 93
2.6.1 磨床的保养 93
2.6.2 磨床常见的故障与排除 96
第3章 磨料磨具 102
3.1 普通磨料磨具的结构和性能 102
3.1.1 磨料磨具的结构 102
3.1.2 磨料磨具的特性 102
3.2.2 磨具的形状尺寸选择 111
3.2.1 磨料选择 111
3.2 普通磨料磨具的选用 111
3.1.3 磨具的标记 111
3.2.3 粒度 112
3.2.4 结合剂、硬度和组织选择 112
3.3 砂轮的磨损与修整 113
3.3.1 砂轮的堵塞 113
3.3.2 砂轮磨损 113
3.3.3 磨具的修整 115
3.4 超硬磨料磨具 116
3.4.1 超硬磨料磨具的应用特点及品种 116
3.4.2 超硬磨料的性能 119
3.5 金刚石修整笔 133
3.6 超硬磨料砂轮的修整 138
3.6.1 超硬磨料砂轮的整形方法 139
3.6.2 超硬磨料砂轮修锐方法 142
3.6.3 超硬磨料砂轮修整技术新进展 143
3.7 涂附磨具 148
3.7.1 涂附磨具的类型及特性 148
3.7.2 涂附磨具制造 150
3.7.3 砂带 151
3.8 珩磨、研磨、抛光磨料磨具 154
3.8.1 珩磨具及珩磨剂 154
3.8.2 研具及研磨剂 154
3.8.3 抛光轮及抛光剂 154
4.1.1 外圆磨削 157
第4章 磨削工艺 157
4.1 典型表面磨削 157
4.1.2 内圆磨削 166
4.1.3 平面磨削 169
4.1.4 螺纹磨削 176
4.2 高效强力磨削 181
4.2.1 高速磨削 181
4.2.2 缓进给磨削 190
4.2.3 砂带磨削 199
4.2.4 恒压力磨削 209
4.3 精密、超精密和镜面磨削 213
4.3.1 精密、超精密加工的概念 214
4.3.2 精密、超精密磨削原理 218
4.3.3 精密、超精密磨削砂轮 219
4.3.4 砂轮的修整 221
4.3.5 精密、超精密磨削的磨削用量 223
4.3.6 精密、超精密磨削对机床的要求 224
4.3.7 镜面磨削的缺陷及改进措施 227
4.4 珩磨与超精加工 228
4.4.1 珩磨 228
4.4.2 超精加工 244
4.4.3 轮式超精磨 249
4.5 游离磨粒加工技术 251
4.5.1 研磨 251
4.5.2 抛光 266
4.5.3 磁性研磨 273
4.5.4 喷射加工 274
4.5.5 磨料流动加工 277
4.6 特殊材料磨削技术 279
4.6.1 硬质合金磨削 279
4.6.2 不锈钢磨削 280
4.6.3 钛合金磨削 281
4.6.4 工程陶瓷磨削 282
第5章 磨削加工工艺规程 285
5.1 工艺规程基本知识 285
5.1.1 生产过程和工艺过程 285
5.1.2 机械加工工艺过程的组成 285
5.1.3 生产纲领与生产类型 287
5.2 工艺规程的作用和格式 289
5.2.1 机械加工工艺规程的作用 289
5.2.2 机械加工工艺规程的格式 290
5.3 机械加工工艺规程的制订 293
5.3.1 制订机械加工工艺规程的原则和步骤 293
5.3.2 零件分析 294
5.3.3 毛坯的选择 294
5.3.4 定位基准的选择 295
5.3.5 机械加工工艺路线的拟定 299
5.4 加工余量及工序尺寸和公差的确定 309
5.4.1 加工余量的确定 309
5.4.2 工序尺寸和公差的确定 311
5.5.1 工艺过程的生产率 315
5.5 工艺过程的生产率和工艺成本 315
5.5.2 工艺成本 317
第6章 磨床夹具 319
6.1 夹具概述 319
6.1.1 夹具的功能和作用 319
6.1.2 夹具的组成 319
6.1.3 夹具的类型 320
6.2 工件在夹具中的定位 322
6.2.1 工件定位的概念 322
6.2.2 定位方式与定位元件 323
6.3.1 加工误差产生的原因 326
6.3 定位误差 326
6.3.2 定位误差的组成 327
6.3.3 定位误差的分析计算 327
6.4 夹紧装置 329
6.4.1 夹紧装置的基本要求 329
6.4.2 夹紧力确定 330
6.4.3 常用夹紧机构 331
6.5 组合夹具 336
6.5.1 组合夹具的特点 336
6.5.2 组合夹具的元件及其作用 336
6.5.3 组合夹具的组装 339
7.1.1 机械加工精度的基本知识 347
7.1 磨削加工精度 347
第7章 磨削质量与检测仪器 347
7.1.2 工艺系统几何误差对加工精度的影响 348
7.1.3 工艺系统受力变形对加工精度的影响 350
7.1.4 工艺系统的受热变形对加工精度的影响 351
7.2 磨削加工表面质量 351
7.2.1 磨削加工表面质量的含义及其对使用性能的影响 351
7.2.2 影响磨削加工表面粗糙度的因素 353
7.2.3 磨削表面层物理力学性能 353
7.2.4 磨削表面完整性参数综合影响及改善措施 359
7.3 常用量具 361
7.3.1 长度测量 361
7.3.2 角度测量 367
7.4 精密量仪 372
7.4.1 电动测量与气动测量 372
7.4.2 圆度仪 376
7.4.3 万能工具显微镜 381
7.4.4 电动轮廓仪 387
7.5 其他测量技术 389
7.5.1 磨削表面层显微硬度的测量方法 389
7.5.2 磨削烧伤的判别与检测 391
7.5.3 磨削残余应力的检测 396
第8章 典型工件磨削加工 400
8.1 精密主轴磨削 400
8.1.1 螺纹磨床主轴零件分析 400
8.1.2 螺纹磨床主轴加工的定位基准选择 402
8.1.3 机械加工工艺路线 403
8.1.4 表面的加工余量和工序尺寸 404
8.1.5 其他工艺分析 404
8.2 深孔磨削 405
8.2.1 深孔磨削的装夹方法 406
8.2.2 提高砂轮接长轴的刚性 407
8.2.3 磨削深孔的技术措施 409
8.2.4 磨削实例 409
8.3 刀具的刃磨 415
8.3.1 三面刃铣刀的刃磨 415
8.3.2 磨削实例 417
8.4.1 精密丝杠螺母传动的要求 418
8.4 精密丝杠磨削 418
8.4.2 精密丝杠的工艺分析 419
8.4.3 温度控制措施 422
8.4.4 精密丝杠的检测与质量分析 424
8.4.5 质量分析 424
8.4.6 磨削实例 428
8.5 畸形精密件磨削 434
8.5.1 凸轮的磨削 434
8.5.2 铲磨凸轮实例 435
8.5.3 精密样板的磨削 437
附录 高级磨工模拟测试题及参考答案 448
主要参考文献 466
- 《翦伯赞全集 第10卷 中外历史年表 主编》翦伯赞著 2008
- 《磨工 高级 考前辅导》郭玲梅;郑柳;于子立 2013
- 《磨工 高级》刘风军主编 2016
- 《公路工程造价员》陈楠主编 2013
- 《农网配电营业技师培训教材》王金笙主编 2010
- 《动物故事 70则中国原生态童话作品》何承伟本册主编 2013
- 《天使与女神》韦伶主编 2013
- 《安装工程造价员》周胜主编 2013
- 《模拟电子技术基础 第2版 学习指导与解题指南》杨拴科,赵进全主编 2012
- 《中华人民共和国老年人权益保障法释义及适用指南》何永坚主编 2013