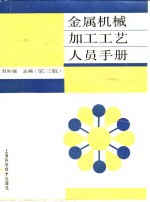
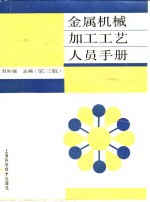
金属机械加工工艺人员手册 第3版PDF电子书下载
- 电子书积分:31 积分如何计算积分?
- 作 者:赵如福主编
- 出 版 社:上海:上海科学技术出版社
- 出版年份:1990
- ISBN:7532313840
- 页数:1274 页
各种单位和换算表 2
国际单位制的基本单位和辅助单位(表1-1) 2
有专用名称的国际单位制导出单位(表1-2) 2
第一章 常用基本资料 2
国际单位制用的十进词头(表1-3) 3
不同单位制的基本单位和力学单位(表1-4) 3
分数英寸、小数英寸与毫米对照(表1-5) 4
面积和地积单位换算(表1-7) 5
容积单位换算(表1-8) 5
长度单位换算(表1-6) 5
重量单位换算(表1-9) 6
线速度单位换算(表1-10) 6
角速度单位换算(表1-11) 6
力单位换算(表1-12) 7
力矩和转矩单位换算(表1-13) 7
密度单位换算表(表1-14) 7
压力和应力单位换算(表1-15) 8
功、能和热量单位换算(表1-16) 9
功率单位换算(表1-17) 9
钢铁硬度与强度对照(表1-18) 10
黄铜维氏、洛氏、布氏硬度对照(表1-20) 14
钢铁洛氏与肖氏硬度对照(表1-19) 14
度、分、秒与弧度对照(表1-21) 15
弧度与度对照(表1-22) 15
分、秒与小数度对照(表1-23) 15
常用数学资料 16
常用数学符号(表1-24) 16
1~20的阶乘值及其倒数、对数(表1-25) 17
圆的内切、外接多边形的几何尺寸(表1-26) 17
外接圆直径D与内切圆直径d的关系(表1-27) 18
圆周等分长度计算(表1-28) 18
面积计算(表1-29) 19
各种几何体的表面及体积的计算(表1-30) 20
圆的弓形尺寸系数表(表1-31) 21
常用数学公式 23
等式变形(表1-32) 23
连分数及其应用(表1-33) 23
三角函数的定义(表1-34) 25
三角函数值随角度α的变化及符号规律(表1-35) 26
特殊角的三角函数值(表1-36) 26
用同角某三角函数表示其他三角函数(表1-37) 26
用α的三角函数表示(n·?±α)的三角函数(表1-38) 27
三角恒等式(表1-39) 27
斜三角形解法(表1-42) 29
反三角函数的定义、记号和主值区间(表1-40) 29
斜三角形的边角关系(表1-41) 29
三角形的面积和有关线段长度的计算公式(表1-43) 30
矢量基本公式(表1-44) 31
矢量的和、差与数乘(表1-45) 31
字母、化学符号和物理系数 32
常用希腊字母(表1-46) 32
主要元素的化学符号、原子量和密度(表1-47) 32
固体线膨胀系数(表1-48) 33
摩擦系数(表1-49) 33
固体材料的密度(表1-50) 34
材料重量计算 34
方钢、六角钢、圆钢重量表(表1-51) 35
金属板料重量表(表1-52) 36
机械制图 37
图纸幅面尺寸(表1-53) 37
图线(表1-54) 38
比例(表1-55) 38
尺寸注法(表1-56) 39
尺寸简化画法(表1-57) 41
各种孔的标准注法(表1-58) 43
尺寸公差注法(表1-59) 44
表面粗糙度代号及其注法(表1-60) 46
表面粗糙度的注法(表1-61) 47
螺纹及螺纹紧固件画法(表1-62) 48
螺纹的标注方法(表1-63) 50
滚动轴承的简化画法和示意画法的尺寸比例(表1-64) 51
零件结构要素 52
中心孔(表1-65) 52
滚花(表1-66) 53
砂轮越程槽(表1-67) 54
倒角及倒圆半径系列(表1-68) 54
轴与套的倒角(表1-70) 55
倒角及倒圆半径配合尺寸(表1-69) 55
轴与套的倒圆半径(表1-71) 56
球面半径(表1-72) 56
外螺纹紧固件的末端型式与尺寸(表1-73) 57
普通外螺纹收尾(表1-74) 58
普通内螺纹收尾(表1-75) 59
米制锥螺纹收尾(表1-76) 60
圆柱管螺纹收尾(表1-77) 61
牙形角55°圆锥管螺纹收尾(表1-78) 62
牙形角60°圆锥管螺纹收尾(表1-79) 63
普通螺纹的螺纹余留长度、钻孔深度及螺栓突出螺母末端的收尾长度(表1-80) 64
单线梯形外螺纹与内螺纹的退刀槽与倒角(表1-81) 65
粗牙螺栓、螺钉的拧入深度(表1-82) 66
紧固件沉头座及通孔尺寸(表1-83) 67
挂轮及分度计算 69
车螺纹、蜗杆时的挂轮计算(表1-84) 69
分度头的分度计算 69
挂轮计算中的近似分式(表1-85) 70
复式分度表(表1-86) 71
渐开线圆柱齿轮计算 72
基准齿形(表1-87) 72
外啮合标准圆柱齿轮传动几何计算(表1-89) 73
齿轮模数(表1-88) 73
螺旋齿轮传动几何计算特点(表1-90) 74
标准圆柱内齿轮的几何计算公式(表1-91) 75
圆弧齿轮几何尺寸计算(表1-92) 76
直齿圆锥齿轮传动的主要几何尺寸及参数(表1-93) 77
圆柱蜗杆传动基本几何尺寸计算公式(表1-94) 78
切削液 80
切削液的选择(表1-95) 80
市场供应的切削液品种(表1-96) 81
切削液的配方(表1-97) 82
术语与定义 84
尺寸公差与配合 84
第二章 公差与配合 84
标准公差的等级与配合代号 86
新旧国标的公差带对照(尺寸1~500mm) 86
基孔制配合的轴公差带代号(表2-1) 86
基轴制配合的孔公差带代号(表2-2) 87
尺寸公差与配合数表 87
尺寸至500mm轴的极限偏差(表2-3) 88
尺寸至500mm孔的极限偏差(表2-4) 99
标准公差数值(表2-5) 109
尺寸至500mm基孔制与基轴制优先、常用配合极限间隙或极限过盈(表2-6) 110
尺寸〉500~3150mm轴的极限偏差(表2-7) 116
尺寸〉500~3150mm孔的极限偏差(表2-8) 119
未注公差尺寸的极限偏差(表2-9) 121
形状和位置公差 122
形状和位置公差的项目及其公差带定义 122
形位公差基本项目与其符号(表2-10) 122
形位公差其他项目与其符号(表2-11) 122
形状和位置公差带的定义和示例说明(表2-12) 123
形状和位置公差值 136
直线度、平面度公差(表2-13) 136
圆度、圆柱度公差(表2-14) 136
同轴度、对称度、圆跳动和全跳动公差(表2-16) 137
平行度、垂直度、倾斜度公差(表2-15) 137
形状和位置未注公差值 138
未注直线度、平面度公差值(表2-17) 138
未注同轴度、对称度公差值(表2-18) 138
螺纹联结的公差与配合 138
普通螺纹 138
公制螺纹基本牙型 138
直径1~355mm普通螺纹的公差与配合 139
直径与螺距(表2-19) 140
直径1~600mm普通螺纹的基本尺寸(表2-20) 142
螺纹中径公差(表2-21) 143
螺纹的基本偏差和小径、大径公差(表2-22) 145
螺纹旋合长度(表2-23) 146
普通内螺纹选用的公差带(表2-24) 147
普通外螺纹选用的公差带(表2-25) 147
螺纹标记 147
英制螺纹基本牙型 148
英制螺纹的尺寸和公差(表2-26) 148
梯形螺纹 149
基本牙型 149
梯形螺纹的直径与螺距系列(表2-27) 149
梯形螺纹基本尺寸 150
梯形螺纹公差带位置和基本偏差 151
梯形螺纹基本尺寸表(表2-28) 151
梯形螺纹公差带和公差等级 152
梯形螺纹中径基本偏差和大小径公差TD1、Td(表2-29) 152
梯形螺纹中径公差、旋合长度(表2-30) 153
梯形螺纹外螺纹小径公差Td3(表2-31) 154
梯形螺纹内、外螺纹选用公差带(表2-32) 155
多线螺纹 155
螺纹标记 155
管螺纹 155
基本牙型与螺纹公差带 155
非螺纹密封的管螺纹(表2-33) 156
用螺纹密封的管螺纹的基本牙型与术语示图 157
用螺纹密封的管螺纹的基本尺寸和公差(表2-34) 158
布氏圆锥形管螺纹的基本尺寸(表2-35) 159
圆锥形、布氏圆锥形管螺纹的尺寸公差(表2-36) 160
锯齿形螺纹 160
直径与螺距(表2-37) 160
锯齿形螺纹牙形(表2-38) 161
锯齿形螺纹的基本尺寸(表2-39) 161
锯齿形螺纹公差及旋合长度(表2-40) 162
平键 163
平键和键槽的剖面尺寸(表2-41) 163
键与花键的公差与配合 163
薄形平键 164
薄形平键和键槽的剖面尺寸(表2-42) 164
半圆键 165
半圆键和键槽的剖面尺寸(表2-43) 165
楔键 166
楔键和楗槽的剖面尺寸(表2-44) 166
矩形花键 167
矩形花键的规格和尺寸(表2-45) 167
矩形花键的公差与配合(表2-46) 167
齿槽宽和齿厚的总公差(T+λ)(表2-47) 168
圆柱直齿渐开线花键 168
齿距累积公差Fp(表2-48) 169
齿形公差?f(表2-49) 170
齿向公差Fβ(表2-50) 171
内花键小径D?极限偏差和外花键大径Dee公差(表2-51) 171
齿轮公差 171
渐开线圆柱齿轮精度 171
公差组的划分(表2-52) 171
误差定义和代号(表2-53) 172
新旧标准的误差及偏差名称、代号对照(表2-54) 179
齿距累积公差Fp及K个齿距累积公差Fpk值(表2-55) 180
齿圈径向跳动公差、径向综合公差(表2-56) 181
齿形公差、一齿径向综合公差(表2-57) 182
齿距极限偏差、基节极限偏差(表2-58) 183
中心距极限偏差±?a(表2-59) 184
公法线长度变动公差Fω值(表2-60) 184
齿向公差Fβ值(表2-61) 185
齿厚极限偏差(表2-62) 185
齿坯公差(表2-63) 185
齿坯基准面径向和端面跳动公差(表2-64) 185
公差与偏差应用示例(表2-66) 186
接解斑点(表2-65) 186
锥齿轮精度 187
误差及侧隙的定义和代号(表2-67) 187
齿轮和齿轮副公差组(表2-68) 192
齿轮副的最小法向侧隙 192
齿轮精度标注示例 192
齿距累积公差Fp和K个齿距积累公差Fpk值(表2-69) 193
周期误差的公差fzj′值(表2-70) 193
齿距极限偏差±fpt值、齿形相对误差的公差fo值(表2-71) 194
最小法向测隙jnmin值(表2-72) 195
侧隙变动公差Fv?值(表2-73) 196
齿轮副齿频周期误差fzzo′值(表2-74) 196
齿圈跳动公差F?、齿轮副轴交角公差FiΣc″、齿轮副相邻齿轴交角综合公差f?Σc″值(表2-75) 197
齿厚公差T?值(表2-77) 198
齿厚上偏差E?值(表2-76) 198
安装距极限偏差±fАм值(表2-78) 199
轴间距极限偏差±fɑ值(表2-79) 200
轴交角极限偏差±EΣ值(表2-80) 200
齿坯尺寸公差(表2-81) 201
齿坯顶锥母线跳动和基准端面跳动公差(表2-82) 201
接触斑点大小与精度对应关系(表2-84) 202
锥齿轮精度应用示例(表2-85) 202
齿坯轮冠距和顶锥角极限偏差(表2-83) 202
圆柱蜗杆蜗轮精度 203
误差的定义和代号(表2-86) 203
蜗杆、蜗轮和蜗杆传动的精度等级及公差组 209
蜗杆的公差和极限偏差fh、fhi、fpx、fpxi、f?1值(表2-87) 210
蜗杆齿槽径向跳动公差f?值(表2-88) 211
蜗轮齿距累积公差Fp及K个齿距累积公差Fpk值(表2-89) 211
蜗轮Fr、Fi″值(表2-90) 212
蜗轮fi″、±fpt、ff2值(表2-91) 212
传动中间平面极限偏移值(表2-94) 213
传动轴交角极限偏差值(表2-95) 213
传动接触斑点的要求(表2-92) 213
传动中心距极限偏差值(表2-93) 213
蜗杆齿厚公差T?1值(表2-96) 214
蜗杆副传动的最小法向侧隙jnmin值(表2-97) 214
蜗轮齿厚公差T?2值(表2-98) 214
蜗杆齿厚上偏差中的误差补偿部分Es△值(表2-99) 215
蜗杆、蜗轮齿坯尺寸和形状公差(表2-100) 216
蜗杆、蜗轮齿坯基准面径向和端面跳动公差(表2-101) 216
蜗杆、蜗轮和蜗杆传动精度应用示例(表2-102) 216
角度公差 217
标准锥度(表2-103) 217
自由角度公差(表2-105) 218
锥度公差(表2-104) 218
第三章 材料 220
热处理及有关概念简介 220
钢的组织及特性(表3-1) 220
常用热处理名词、方法、特点、代号及应用(表3-2) 221
常用表面处理、化学处理方法、特点、代号和应用(表3-3) 223
金属材料机械性能代号及名词解释(表3-4) 226
常用硬度试验方法的原理及使用范围(表3-5) 227
钢 228
钢号表示法 228
钢的名称及其代号表示(表3-6) 229
碳素结构钢新旧牌号对照(表3-7) 229
钢铁牌号表示方法举例(表3-8) 230
钢的机械性能和代学成分 232
碳素结构钢机械性能(表3-9) 232
碳素结构钢化学成分(表3-10) 233
优质碳素结构钢的化学成分和机械性能(表3-11) 233
低合金结构钢(表3-12) 234
合金结构钢化学成分(表3-13) 236
合金结构钢机械性能(表3-14) 238
冷拉钢机械性能(表3-15) 240
冷拉钢的硬度(表3-16) 240
不锈钢(表3-17) 242
耐热钢(表3-18) 244
弹簧钢化学成分(表3-19) 245
弹簧钢硬度(表3-20) 246
弹簧钢机械性能(表3-21) 246
冷顶锻钢机械性能及硬度(表3-22) 247
易切削钢(表3-23) 247
碳素工具钢(表3-24) 247
合金工具钢(表3-25) 248
高速工具钢化学成分(表3-26) 249
高速工具钢硬度(表3-27) 249
高速工具钢的使用性能及用途(表3-28) 249
硬质合金(表3-29) 250
常用钢热处理后的机械性能(表3-30) 251
铸钢 259
碳素铸钢的机械性能(表3-31) 259
合金结构铸钢(表3-32) 259
特殊性能高合金铸钢(表3-33) 260
不锈、耐酸钢铸件(表3-34) 260
铸铁 261
灰口铸铁(表3-35) 261
黑心可锻铸铁和珠光体可锻铸铁的机械性能(表3-36) 262
白心可锻铸铁的机械性能(表3-37) 262
有色金属及合金产品代号表示方法(表3-39) 263
有色金属 263
球墨铸铁(表3-38) 263
有色金属产品状态名称及其代号(表3-40) 264
压力加工用黄铜(表3-41) 264
铸造铜合金之一(黄铜)(表3-42) 265
压力加工用青铜(表3-43) 266
铸造铜合金之二(青铜)(表3-44) 267
压力加工用铝及铝合金(表3-45) 269
铸造铝合金(表3-46) 270
压力加工用锌合金(表3-47) 270
压铸锌合金(表3-48) 270
常用粉末冶金基体材料的选择(表3-51) 271
粉末冶金材料 271
锌基耐磨合金(表3-49) 271
轴承合金(表3-50) 271
常用粉末冶金摩擦材料的成分和性能(表3-52) 272
工程塑料 273
工程塑料的分类及其产品(表3-53) 273
常用工程塑料的特性与用途(表3-54) 273
常用工程塑料的物理、机械性能(表3-55) 275
材料消耗定额 277
各种加工方法的表面粗糙度Ra和表面缺陷深度Ta值(表3-56) 278
车床加工工件夹头部分长度(表3-57) 278
确定加工余量实例(表3-58) 279
焊枪气割切口余量(表3-61) 280
下料利用率和下料残料率 280
端头修正损耗量(表3-62) 280
下料损耗 280
自动车床切口宽度(表3-60) 280
锯床、铣床切口宽度(表3-59) 280
各种型材按除去锯耗、残料、歪斜计算的下料利用率K1(表3-63) 281
各种型材按除去缺陷长度、料头长度计算的下料利用率K1(表3-64) 282
各种型材按缺陷、锯耗、残料计算的下料残料率K2(表3-65) 282
材料消耗定额的制定 283
材料消耗定额制定实例(表3-66) 283
基本概念 286
第四章 工艺规程的编制 286
工艺规程的编制 287
工艺文件 288
定位夹紧符号(表4-1) 289
定位夹紧装置、夹具标注示例(表4-2) 290
机械加工过程卡(表4-3~4-4) 293
机械加工工艺卡(表4-5) 295
机械加工工序卡(表4-6~4-7) 296
多轴自动车床工序卡(表4-8) 298
单轴六角自动车床工序卡(表4-9) 300
单轴纵切自动车床工序卡(表4-10) 302
技术检查卡(表4-11) 304
尺寸偏差的经济精度 305
孔加工精度(表4-12) 305
圆柱形深孔加工精度(表4-13) 306
圆锥形孔加工精度(表4-14) 306
多边形孔中工精度(表4-15) 306
花键孔加工精度(表4-16) 306
圆柱形外表面的加工精度(表4-17) 306
平面加工精度(表4-21) 307
成形铣刀加工精度(表4-20) 307
平行表面的加工精度(表4-19) 307
端面加工精度(表4-18) 307
公制螺纹加工精度(表4-22) 308
花键制造的经济精度(表4-23) 308
齿轮加工精度(表4-24) 309
表面粗糙度 310
基本概念 310
轮廓算术平均偏差Ra的数值(表4-25) 312
微观不平度十点高度Rz,轮廓最大高度Ry的数值(表4-26) 312
轮郭微观不平度的平均间距Sm,轮廓的单峰平均间距S的数值(表4-28) 313
轮廓支承长度率tp的数值(表4-29) 313
取样长度的数值(表4-27) 313
表面粗糙度(光洁度)代号与参数数值对照(表4-30) 314
表面粗糙度Ra数值与原表面光洁度符号对照(表4-31) 316
各种机械加工方法所能够达到的零件表面粗糙度(表4-32) 317
表面粗糙度与加工精度和配合之间的关系 319
轴的表面粗糙度与加工精度和配合之间的关系(表4-33) 319
孔的表面粗糙度与加工精度和配合之间的关系(表4-34) 320
各种连接表面的粗糙度 321
动连接接合表面的粗糙度(表4-35) 321
静连接接合表面的粗糙度(表4-36) 321
齿轮、蜗轮和蜗杆的工作表面粗糙度(表4-39) 322
螺纹连接的工作表面粗糙度(表4-38) 322
丝杠传动接合表面的粗糙度(表4-37) 322
车床加工 323
车床加工示例(表4-40) 323
车床装夹方法及装夹精度(表4-41) 326
仿型车床加工(表4-42) 329
多刀车床加工(表4-43) 330
转塔车床加工(表4-44) 332
自动车床加工(表4-45) 341
多轴立式半自动车床加工(表4-46) 349
镗床加工示例(表4-47) 354
镗床加工 354
镗床加工的基准面及较准方法(表4-48) 358
镗床工作的测量方法及测量精度(表4-49) 360
刨、铣床加工 362
刨、铣床加工示例(表4-50) 362
外圆磨床加工 365
螺纹加工 365
丝锥与板牙组合加工 365
螺纹铣 366
螺纹滚轧 367
螺纹滚轧方法及其应用(表4-51) 367
用滚轧方法可获得的螺纹精度与表面粗糙度(表4-52) 368
螺纹滚轧工具 369
滚轧工具的螺纹形状公差(表4-53) 370
滚轧螺纹的基本(工艺)时间(表4-54) 371
齿轮加工 372
圆柱齿轮加工 372
齿轮加工示例(表4-55) 372
齿轮冷滚轧 373
第五章 光整加工 376
光整磨削 376
光整磨削对机床的要求 376
光整磨削磨轮的选择(表5-1) 377
光整磨削工艺参数的选择(表5-2~5-5) 379
研磨 380
研磨的精度水平(表5-6) 380
研磨剂(表5-7~5-12) 381
研具 382
研磨用量(表5-13~5-14) 382
平面研磨 383
珩磨 383
珩磨头 384
珩磨尺寸的控制 386
珩磨磨条的选用(表5-15~5-17) 387
磨块的选用(表5-18~5-24) 388
超精加工 391
超精加工示例(表5-25) 391
超精加工用磨块(表5-26~5-28) 392
超精加工余量和磨块的选择(表5-29) 392
超精加工工艺参数的选择(表5-30~5-31) 392
滚轮珩磨 396
滚轮珩磨的特点 396
滚轮珩磨工具结构 397
滚轮珩磨磨轮的选择(表5-32) 397
滚轮珩磨工艺参数的选择(表5-33~5-34) 398
零件表面冷压加工 399
概述(表5-35) 399
滚轮滚压加工(表5-36~5-41) 405
滚珠滚压加工(表5-42~5-44) 414
孔的挤压加工(表5-45) 417
液体抛光 420
麻料粒度和表面粗糙度(表5-46) 423
各种原始表面状态和加工后表面粗糙度(表5-47) 423
抛光轮的速度(表5-51) 424
磨料的选择(表5-49) 424
抛光时选用的磨料粒度(表5-50) 424
用弹性抛光轮抛光 424
抛光 424
磨料粒度、加工次数和加工表面粗糙度(表5-48) 424
用砂纸抛光 425
用钢丝轮抛光(表5-52) 425
第六章 成组技术 428
基本概念 428
机床的布置 428
零件的相似性 428
零件分类编码系统的要求 429
零件分类编码系统 429
零件分类编码系统的分类 430
OPITZ分类编码系统 430
JCBM-1分类编码系统 448
成组技术的工艺设计 449
相似性工艺设计的工艺准备工作 449
零件分类的基本方法 450
每组零件的成组工艺规程的编制 453
成组加工设备布置形式的确定 457
指导性资料的编制 459
CAPP举例 460
计算机辅助工艺规程设计(CAPP) 460
相似性工艺设计 460
第七章 金属的特种加工 464
概述 464
金属特种加工方法的综合比较(表7-1) 464
电火花加工 464
电火花加工设备(表7-2~7-3) 464
电火花加工的工艺规律(表7-4~7-6) 466
电火花加工工艺(表7-7~7-11) 469
加工实例(表7-12~7-16) 473
电火花磨削(表7-17~7-19) 475
电火花线切削加工(表7-20~7-23) 476
电解加工 479
电解加工设备(表7-24~7-26) 479
电解液(表7-27~7-31) 482
电解加工基本工艺参数(表7-32~7-36) 484
非加工部分的涂覆(表7-37) 486
电化学抛光 486
除油除锈方法(表7-38) 487
电抛光用的电解液成分及使用条件(表7-39) 487
电抛光工艺参数(表7-40) 488
电解磨削 489
电解磨床特点及电解液(表7-41~7-43) 489
电解磨削的工艺参数(表7-45) 491
导电磨轮(表7-44) 491
阳极机械切割(表7-46~7-48) 492
超声波加工(表7-49~7-50) 493
激光加工(表7-51~7-59) 495
电子束加工(表7-60~7-61) 500
离子束加工(表7-62~7-63) 502
等离子加工 503
等离子体的稳定方法(表7-64) 503
高速流体加工(表7-65~7-67) 504
化学加工 505
化学铣切腐蚀溶液配方(表7-68) 506
通用机床型号 508
第八章 金属切削机床 508
金属切削机床型号编制方法 508
机床类别代号(表8-1) 509
机床通用特性代号(表8-2) 510
金属切削机床类、组、型划分表(表8-3) 511
各类机床主参数名称及折算系数(表8-4) 519
我国旧的金属切削机床类、组划分表(表8-5) 520
专用机床型号 521
组合机床级其自动线的型号 521
组合机床及其自动线的分类代号(表8-6) 521
单轴六角自动车床(表8-8) 522
常用金属切削机床的技术性能 522
单轴纵切自动车床(表8-7) 522
TB型单轴自动车床(表8-9) 523
卧式多轴自动车床(表8-10) 524
六角车床(表8-11) 525
半自动、组合式转塔车床(表8-12) 526
立式车床(一)(表8-13) 527
立式车床(二)(表8-14) 528
立式车床(三)(表8-15) 529
普通车床(一)(表8-16) 530
普通车床(二)(表8-17) 532
数控车床(表8-18) 533
马鞍车床(表8-19) 534
落地车床(表8-20) 535
半自动液压仿形车床(表8-21) 536
多刀半自动车床(表8-22) 537
铲齿车床(表8-23) 538
台式钻床(表8-24) 539
播臂钻床(表8-25) 540
立式钻床(表8-26) 541
坐标镗床(表8-27) 542
镗床(表8-28) 543
数控龙门镗铣床(表8-30) 545
落地镗铣床(表8-29) 545
自动换刀镗铣床(表8-31) 546
无心磨床(表8-32) 547
外圆磨床(表8-33) 548
内圆磨床(表8-34) 550
卧轴矩台平面磨床(表8-35) 551
立轴矩台平面麻床(表8-36) 553
卧轴圆台平面磨床(表8-37) 553
立轴圆台平面磨床(表8-38) 554
卧轴双端面磨床(表8-39) 554
弧齿锥齿轮铣齿机(表8-40) 555
弧齿锥齿轮拉齿机(表8-42) 556
锥齿轮刨齿机(表8-41) 556
滚齿机(表8-43) 557
大型滚齿机(表8-44) 559
插齿机(表8-45) 560
剃齿机(表8-46) 560
珩齿机(表8-47) 561
锥形砂轮磨齿机(表8-48) 561
大平面砂轮磨齿机(表8-49) 562
双砂轮磨齿机(表8-50) 562
半自动齿轮倒角机(表8-51) 562
螺纹磨床(表8-52) 563
龙门铣床(表8-54) 564
柔性加工单元(表8-53) 564
铣床(立式、卧式、万能)(表8-55) 565
双立轴圆工作台铣床(表8-56) 567
龙门刨床(一)(表8-57) 568
龙门刨床(二)(表8-58) 570
牛头刨床(表8-59) 572
插床(表8-60) 573
拉床(表8-61) 574
电加工机床(表8-62~8-68) 575
各种机床工作精度(表8-69) 580
机床工作精度 580
组合机床通用部件 584
多轴箱箱体尺寸(表8-71) 584
支架尺寸(表8-72) 585
回转工作台用多边形中间底座尺寸(表8-73) 585
滑台尺寸(表8-74) 586
动力箱尺寸(表8-75) 587
组合机床的加工精度(表8-70) 588
滑台侧底座尺寸(表8-76) 589
中间底座和立柱尺寸(表8-77) 590
立柱尺寸(表8-78) 591
立柱侧底座尺寸(表8-79) 592
滑套进给式钻削头(表8-80) 593
具有换刀用可调滑座的滑套进给式钻削头(表8-81) 594
单轴钻削头(表8-82) 595
单轴铣削头(表8-83) 596
单轴镗削与车端面头(表8-84) 597
有导轨立柱尺寸(表8-85) 598
落地式有导轨立柱尺寸(表8-86) 599
组合机床的动力部件 599
液压动力滑台(表8-88) 600
动力滑台和自驱式动力头的对比(表8-87) 600
液压自驱式动力头(表8-89) 601
JT机械动力滑台(表8-90) 602
JT机械动力头(表8-91) 603
铣头(表8-92) 604
液压镗孔车端面头(表8-93) 604
精镗头(表8-94) 605
主轴可调头(表8-95) 606
小型机械钻孔动力头(表8-96) 607
回转工作台(表8-97) 608
组合机床配置型式(表8-99) 609
组合机床的配置(表8-98) 609
组合机床的型式和配置 609
几种典型的自动工作循环(表8-100) 611
转塔动力头的几种型式(表8-101) 612
自动更换主轴箱机床示例(表8-102) 614
柔性制造系统 614
柔性制造系统的原理 614
柔性制造系统的生产与经济效益 616
采用柔性制造系统的条件 617
柔性制造系统的组成部分 617
工作工位内容、用途及要求(表8-103) 617
缓冲存贮区 618
控制系统的软件 618
物料运贮系统 618
常用的物料运贮装置(表8-104) 618
刀、夹、量具及其他辅具等 619
刀、夹、量具等内容及要求(表8-105) 619
加工中心布局 619
三种加工中心的外形尺寸(表8-106) 621
三种加工中心的主要性能(表8-107) 623
FMS实例 623
FMS实例简介(表8-108) 623
FMS的实施步骤 626
FMS的实施步骤汇总表(表8-109) 627
第九章 夹具及机床附件 630
概述 630
夹具的种类 630
夹具的组成 630
平具的设计 631
定位夹紧机构 633
定位机构 633
常用定位件的类型(表9-1) 633
浮动定位机构(表9-2) 634
拨动定位机构(表9-3) 635
辅助支承类型(表9-4) 637
典型的对刀装置(表9-5) 640
几种典型的镗杆引导装置(表9-6) 641
分度定位机构 642
分度定位机构(表9-7) 642
分度定位机构的应用实例(表9-8) 646
夹紧机构 647
斜楔夹紧机构的几种类型(表9-9) 647
几种典型的螺旋夹紧机构(表9-10) 649
几种典型的偏心夹紧机构(表9-11) 651
几种典型的凸轮夹紧机构(表9-12) 652
几种典型的械杆、铰链夹紧机构(表9-13) 653
几种典型的联动机构(表9-14) 654
几种典型的多件夹紧机构(表9-15) 655
几种典型的定心夹紧机构(表9-16) 657
定位夹紧方面的计算 659
常见的定位形式和定位误差(表9-17) 659
钻模的钻孔精度计算(表9-18) 661
定位销的设计计算(表9-19) 662
锥度心轴的尺寸计算(表9-20) 663
弹簧夹头各部分尺寸计算公式(表9-21) 664
直齿轮定位时定位滚柱直径及外公切圆直径计算(表9-22) 665
钻斜孔钻模导向件与工艺基准间位置尺寸的计算(表9-23) 666
几种夹紧型式所需夹紧力的计算(表9-24) 667
几种刚性夹紧机构型式及主要特性(表9-25) 669
斜楔夹紧机构计算公式及数据(表9-26) 670
螺旋夹紧机构夹紧力的计算(表9-27) 673
螺母的夹紧力(表9-28) 674
圆偏心夹紧力及夹紧行程的计算(表9-29) 675
各种铰链夹紧机构主要参数的计算式(表9-30) 676
常用弹性夹紧元件型式及其主要特性(表9-31) 678
常用弹性元件夹紧力的计算(表9-32) 679
转动压板(表9-33) 680
常用夹具零件的通用标准 680
转动弯压板(表9-34) 681
移动压板(表9-35) 682
移动弯压板(表9-36) 683
偏心轮用压板(表9-37) 684
双向压板(表9-38) 685
铰链压板(表9-39) 686
槽面压块(表9-40) 687
弧形压块(表9-41) 688
钩形压板(表9-42) 689
套简(表9-43) 690
切向夹紧套(表9-44) 691
圆偏心轮(表9-45) 692
叉形偏心轮(表9-46) 693
单面偏心轮(表9-47) 694
双面偏心轮(表9-48) 694
固定式定位销(表9-49) 695
可换定位销(表9-50) 696
定位衬套(表9-51) 697
V形块和固定V形块(表9-52) 698
调整V形块和活动V形块(表9-53) 699
支承钉(表9-54) 700
六角头支承(表9-55) 701
球头支承(表9-56) 702
支承板(表9-57) 703
压紧螺钉(表9-58) 704
对刀块(表9-59) 705
钻套用衬套(表9-60) 706
固定钻套(表9-61) 707
可换钻套(表9-62) 708
快换钻套(表9-63) 709
铰链支座(表9-64) 710
铰链叉座(表9-65) 711
螺钉支座(表9-66) 712
星形把手(表9-67) 713
塑料夹具用柱塞(表9-68) 713
塑料夹具用六角头螺钉(表9-69) 714
塑料夹具用内六角螺钉(表9-70) 715
夹具的传动部件 715
气动夹紧给气装置的组成 715
气动传动部件的结构形式 716
气缸、气室的计算数据(表9-71) 716
几种气动传动部件 717
气缸(表9-72~9-74) 717
方向控制阀(表9-75~9-76) 719
气阀 719
流量控制阀(表9-77) 724
气动三联件(表9-78~9-80) 725
液压夹紧的控制回路 728
几种液压传动部件 730
油缸(表9-81~9-84) 730
液压增压器(表9-85~9-86) 732
组合夹具 735
组合夹具可达到的加工精度(表9-87) 735
组合夹具元件分类和编号(表9-88) 736
组合夹具组装使用实例(表9-89) 745
成组夹具 747
成组夹具的特点、设计及经济效益 747
成组夹具示例 748
通用夹具 755
顶尖 755
几种常用固定顶尖的参数(表9-90) 755
几种常用回转顶尖的参数(表9-91) 755
外拨顶尖尺寸(表9-92) 756
内拨顶尖尺寸(表9-93) 757
支持式内拨顶尖尺寸(表9-94) 757
支持式内锥孔顶尖尺寸(表9-96) 758
内锥孔顶尖尺寸(表9-95) 758
几种非标准顶尖(表9-97) 759
拨盘和鸡心卡头 760
各种拨盘和鸡心卡头夹紧工件的尺寸范围(表9-98) 760
拨盘形式之一的尺寸(表9-99) 761
拨盘形式之二的尺寸(表9-100) 761
鸣心卡头尺寸(表9-101) 762
自动夹紧拨动装置的结构型式(表9-102) 763
花盘(表9-103) 764
卡盘 765
三爪自定心卡盘(表9-104~9-106) 765
四爪单动卡盘(表9-107~9-110) 766
动力卡盘(表9-111) 769
电动卡盘(表9-112) 769
夹板(表9-113) 770
快换卡头 770
车床用快换卡头(表9-114) 770
磨床用快换卜头(表9-115) 771
钻夹头及丝锥夹头 771
扳手夹紧式三爪钻夹头参数(表9-116) 771
快换钻夹头(表9-117) 772
自紧式钻夹头(表9-118) 772
机用平口钳 773
综合式丝锥夹头(表9-119) 773
摩擦片丝锥夹头参数和性能(表9-120) 773
平口钳的型式和主参数(表9-121) 774
机用平口钳的基本参数和尺寸(表9-122) 774
回转工作台 775
立轴式回转工作台(表9-123) 775
具有分度和螺旋锁紧的回转工作台 776
万能回转工作台 776
双工位回转工作台 776
卧轴式偏心锁紧回转工作台 779
双柱式分度台 779
万能分度头主要规格(表9-124) 781
分度头 781
等分分度头主要规格(表9-125) 782
电磁吸盘 782
XD250A强力电磁吸盘性能(表9-126) 782
XJ150矩形永磁吸盘性能(表9-127) 782
电磁吸盘规格(表9-128) 783
正弦电磁吸盘规格(表9-129) 783
机床附加装置 783
车床附加装置 783
快速更换刀架 783
车球面刀架 784
车偏心弹簧夹头 784
车端面凸轮装置 786
车锥螺纹刀架 786
车曲面装置 786
车台阶轴仿形装置 788
螺纹切削头 789
深孔钻具 789
磨轮架 790
超精加工头 790
移动角铁(表9-130) 790
双轴立铣头(表9-131) 791
铣床附加装置 791
单边双轴卧铣头 792
仿形装置 792
离合器自动铣齿装置 793
刨床附加装置 796
多刀刀架 796
返回切削刀架 796
回转刀架 796
内孔不通槽铣头 797
镗床附加装置 797
刨镶条斜面装置 797
磨头 797
铣花键装置 798
短锥孔镗头 798
深锥孔镗头 798
立铣头 798
内孔超精加工附件 799
大型角铁及支承梁(表9-132、9-133) 799
第十章 刀具 802
刀具选择的主要因素 802
切刀 802
切刀的各部分名称 802
高速钢车刀条尺寸(表10-1) 803
硬质合金焊接车刀片(表10-2) 803
切刀的选择 803
切刀刀片 803
硬质合金焊接刀片(表10-3) 804
切削刀具用可转位刀片型号表示规则(表10-4) 808
断屑槽的参考尺寸(表10-5) 811
圆孔硬质合金可转位刀片(表10-6) 812
沉孔硬质合金可转位刀片(表10-7) 815
无孔硬质合金可转位刀片(表10-8) 817
铣削刀具用硬质合金可转位刀片(表10-9) 818
普通车刀及其尺寸(表10-10) 819
切刀的类型及尺寸 819
可转位车刀型号表示规则(表10-11) 820
可转位车刀型式尺寸(表10-12) 823
机械夹固式可转位车刀(表10-13) 824
机械夹固式重磨车刀(表10-14) 825
六角车床用切刀(表10-15) 826
镗刀(表10-16) 827
微调镗刀的结构及主要尺寸(表10-17) 828
刨刀(表10-18) 829
插刀(表10-19) 830
先进车刀、刨刀(表10-20) 830
中心钻的类型及尺寸(表10-21) 833
中心钻 833
钻头 834
钻头的各部名称 834
钻头的选择 834
钻头的类型及尺寸 835
麻花钻(表10-22) 835
各种钻头及应用范围(表10-23) 845
先进钻头(表10-24) 846
硬质合金喷吸钻头(表10-25) 848
扩孔钻的选择 849
扩孔钻 849
扩孔钻的各部分名称 849
扩孔钻的类型及尺寸 850
标准扩孔钻(表10-26) 850
镗刀片(表10-27) 852
硬质合金可调节浮动镗刀(表10-28) 853
各类扩孔钻及应用范围(表10-29) 854
锪钻 855
锪钻的选择 855
锪钻的类型及尺寸 856
锪钻(表10-30) 856
锪钻的类型及应用范围(表10-31) 858
铰刀 859
铰刀的各部分名称 859
铰刀的选择 859
铰刀的类型及尺寸 860
铰刀(表10-32) 860
圆锥铰刀(表10-33) 864
硬质合金可调节浮动铰刀(表10-34) 867
各种饺刀及应用范围(表10-35) 868
先进铰刀(表10-36) 869
铣刀的选择 870
铣刀的各部分名称 870
铣刀 870
各种类型铣刀的应用范围(表10-37) 871
铣刀直径的选择(表10-38) 872
铣刀的类型及尺寸 872
标准铣刀(表10-39) 872
可转位铣刀(表10-40) 881
先进铣刀(表10-41) 886
拉刀的各部分名称 888
拉刀及推刀的基本类型 888
拉刀及推刀的定义 888
拉刀 888
拉刀的紧固部分 891
拉刀长度 891
圆孔拉刀(表10-42) 891
键槽拉刀(表10-43) 892
矩形齿花键拉刀(表10-44) 893
矩形齿综合花键拉刀(表10-45) 894
矩形齿花键推刀(表10-46) 895
圆孔推刀(表10-47) 896
丝锥(表10-48~10-54) 897
螺纹刀具的类型及尺寸 897
螺纹刀具的各部分名称 897
螺纹刀具的选择 897
螺纹刀具 897
圆板牙(表10-55) 906
滚丝轮(表10-56) 908
搓丝板(表10-57) 910
先进螺纹刀具(表10-58) 911
齿轮刀具 912
齿轮刀具的各部分名称 912
齿轮铣刀、齿轮刨刀、斜齿齿条形刨齿刀 912
齿轮刀具的选择 913
插齿刀、盘形剃齿刀、螺旋锥齿轮铣刀 913
齿轮刀具的类型及尺寸 914
盘形齿轮铣刀(表10-59) 914
渐开线齿形的单线齿轮滚刀(表10-60) 915
齿轮刀具(表10-61) 915
磨具 918
磨具的选择 918
磨料的选择(表10-61~10-64) 918
结合剂的选择(表10-65~10-66) 919
粒度的选择(表10-67~10-70) 920
硬度的选择(表10-71) 922
浓度的选择(表10-73) 923
组织的选择(表10-72) 923
磨具的形状及尺寸选择(表10-74~10-76) 924
各类磨具的用途及尺寸 925
砂轮(表10-77) 925
平形砂轮(表10-78) 928
磨头、砂瓦(表10-79) 931
磨具安全规则(表10-80) 933
工具的紧固部分(表10-81~10-91) 934
计量与计量学 946
各种测量方法的定义与用途(表11-1) 946
测量方法 946
检验 946
测量 946
基本概念 946
概述 946
第十一章 几何量测量技术 946
测量器具 947
测量器具的基本度量指标(表11-2) 947
长度计量的量值传递系统 947
量块 948
量块和线纹尺 948
测量误差产生原因 948
测量误差分类 948
没量误差 948
测量误差 948
量块尺寸系列(表11-3) 949
按制造精度分级的量块长度极限偏差(表11-4) 950
量块测量面的平面度(表11-5) 951
按检定精度分等的量块极限误差与偏差(表11-6) 951
线纹尺 952
基准和标准金属线纹尺的精度及用途(表11-7) 952
标准钢卷尺的精度及用途(表11-10) 953
钢直尺的精度(表11-11) 953
三等标准金属线纹尺的极限偏差(表11-9) 953
一、二等标准玻璃线纹尺的精度及用途(表11-8) 953
钢卷尺的精度(表11-12) 954
通用量具和量仪 955
游标量具(表11-13) 955
测微量具(表11-14) 956
外径千分尺的允许误差(表11-15) 956
内径千分尺的允许误差(表11-16) 957
深度千分尺的允许误差(表11-17) 957
机械量仪(表11-18) 957
千分表允许示值误差(表11-20) 959
扭簧比较仪允许示值误差(表11-19) 959
百分表允许示值误差(表11-21) 960
内径百分表的测量范围及允许示值误差(表11-22) 960
光学计的测量范围及测量误差(表11-23) 960
测长仪及测长机的测量范围及示值误差(表11-24) 961
工具显微镜(表11-25) 961
投影仪(表11-26) 962
气动量仪(表11-27) 962
电感测量头(表11-28) 962
常用孔径测量方法性能比较(表11-29) 963
长度测量 963
大尺寸间接测量的原理及计算公式(表11-30) 964
大尺寸测量方法的极限测量误差参考值(表11-31) 965
角度和锥度的测量 965
常用的角度量具及量仪 965
成套角度块工作角的标称值及其块数(表11-32) 965
90°角尺的结构和尺寸(表11-33) 966
90°角尺的技术要求(表11-34) 967
正弦规 967
正弦规的尺寸精度、形位公差及综合误差(表11-35) 968
使用正弦规测量角度的极限误差(表11-36) 968
游标读数2’的万能角度尺的测量误差(表11-39) 969
万能角度尺的允许示值误差(表11-38) 969
多面棱体的主要技术要求(表11-37) 969
水平仪的主要技术要求(表11-40) 970
合像水平仪的主要技术要求(表11-41) 970
自准直仪及平行光管(表11-42) 970
经纬仪(表11-43) 970
光学分度头(表11-44) 971
角度测量示例(表11-45) 972
锥度测量示例(表11-46) 974
平台测量 977
铸铁平板的规格与精度要求(表11-47) 978
岩石平板的规格与精度要求(表11-48) 979
检验平尺的规格和精度等级(表11-49) 980
刀口尺的精度要求(表11-50) 981
方形平尺的精度要求(表11-51) 981
Ⅰ字、Ⅱ字形和桥形平尺的精度要求(表11-52) 982
检验方箱和弯板的精度要求(表11-53) 983
形状和位置误差测量 983
直线度误差的常用测量方法(表11-55) 985
平面度误差的常用测量方法(表11-56) 985
圆度误差的常用测量方法(表11-57) 986
平行度误差测量举例(表11-58) 987
检验圆柱形表面之间或圆柱形表面与端平面之间的垂直度示例(表11-59) 988
检验孔的同轴度示例(表11-60) 988
形位误差的检测原则(表11-54) 988
表面粗糙度测量 989
样板比较法 989
轮廓仪触针法 989
光切法 989
显微干涉法 989
表面粗糙度各种测量方法的测量对象和范围(表11-61) 989
6JA干涉显微镜(表11-64) 990
常用轮廓仪的规格(表11-62) 990
JSG型光切显微镜(表11-63) 990
螺纹测量 991
螺纹的单项量法 991
螺纹千分尺的测量范围和所备插头副(表11-65) 991
螺纹千分尺示值误差(表11-66) 992
螺纹量针直径(表11-67) 993
螺纹量柱直径(表11-68) 995
普通螺纹三针测量值(表11-69) 995
三针量法测量外螺纹中径的精度(表11-70) 996
光学量法测量螺纹参数的精度(表11-71) 996
丝杠静态测量方法和测量精度(表11-72) 997
丝杠测量 997
齿轮测量 998
齿轮公差组与检验组合(表11-73) 998
部分国产齿轮量具量仪的主要技术数据(表11-74) 999
圆柱齿轮的检验方法 1001
量规 1003
最规的种类 1003
光滑极限量规 1004
光滑极限量规的代号(表11-75) 1004
推荐的量规形式和应用尺寸范围(表11-76) 1004
螺纹量规 1004
螺纹量规的名称、代号、功能、特征及使用规则(表11-77) 1006
新技术在几何量测量中的应用 1007
计量光栅 1007
激光测长 1008
第十二章 毛坯的机械加工余量 1010
毛坯的选择 1010
毛坯的加工余量 1010
各种毛坯的表面层厚度(表12-1) 1011
铸铁件机械加工余量 1011
铸件机械加工余量(表12-2) 1012
铸件机械加工余量等级的选择(表12-3) 1012
合格铸件允许重量偏差(表12-6) 1013
铸件尺寸公差(表12-4) 1013
铸件尺寸精度等级选择(表12-5) 1013
铸钢件的机械加工余量 1014
铸钢件重量偏差(表12-7) 1014
1级精度铸钢件的机械加工余量(表12-8) 1014
1级精度铸钢件尺寸偏差(表12-9) 1015
2级精度铸钢件的机械加工余量(表12-10) 1015
2级精度铸钢件尺寸偏差(表12-11) 1015
3级精度铸钢件的机械加工余量(表12-12) 1016
3级精度铸钢尺寸偏差(表12-13) 1016
铸铁件及铸钢件机械加工余量(金属模)(表12-14) 1016
锡青铜铸件的机械加工余量(手工制模)(表12-16) 1017
铸钢件在用气割切除浇口后的残余留量(表12-15) 1017
有色金属铸件的机械加工余量 1017
青铜棒状铸件的机械加工余量(表12-17) 1018
青铜轴套铸件的机械加工余量(表12-18) 1018
铝铸件的机械加工余量(手工制模)(表12-19) 1019
棒状铝铸件的机械加工余量(表12-20) 1019
铝轴套铸件的机械加工余量(表12-21) 1020
有色金属的机械加工余量(金属模)(表12-22) 1020
有色金属的机械加工余量(压力浇注)(表12-23) 1020
缎件的机械加工余量 1020
台阶和凹档的锻出条件(表12-24) 1021
端部法兰或中间法兰的最小锻出宽度(表12-25) 1023
光轴类和多台阶轴类的机械加工余量及公差(表12-26) 1024
方轴类和有台阶长方形类锻件的机械加工余量及公差(表12-27) 1025
凸肩椭圆形及凸肩长方形类锻件的机械加工余量及公差(表12-28) 1026
凸肩齿轮及凸肩法兰类锻件的机械加工余量及公差(表12-29) 1027
空心类锻件的机械加工余量及公差(表12-30) 1028
短方柱、方块、带孔方盘类锻件的机械加工余量及公差(表12-31) 1028
圆环类锻件的机械加工余量及公差(表12-32) 1029
短圆柱、圆盘、带孔圆盘类锻件的机械加工余量及公差(表12-33) 1029
六方螺母类锻件的机械加工余量及公差(表12-34) 1030
六方螺钉类锻件的机械加工余量及公差(表12-35) 1031
锤上模锻件机械加工余量及公差(表12-36) 1032
钢冲压件的机械加工余量 1033
在锻锤下垫模中制出的冲压件(表12-37) 1033
钢冲件的尺寸公差(表12-38) 1034
轧制材料轴类的机械加工余量 1034
热轧钢轴类外圆的选用(表12-39) 1034
易切削钢轴类外圆的选用--车后不磨(表12-40) 1035
易切削钢轴类外圆的选用--车后须淬火及磨(表12-41) 1035
气割毛坯的加工余量(表12-42) 1036
气割毛坯的加工余量 1036
第十三章 工序间的加工余量 1038
工序间的加工余量 1038
选择工序间加工余量的主要原则 1038
轴加工余量 1038
切断余量(表13-1) 1038
轴的加工方法(表13-2) 1039
轴的折算长度(确定精车及磨削加工余量用)(表13-3) 1039
轴在粗车外圆后,精车外圆的加工余量(表13-4) 1039
轴磨削的加工余量(表13-5) 1040
用金刚石细车轴外圆的加工余量(表13-8) 1041
研磨的加工余量(表13-6) 1041
抛光的加工余量(表13-7) 1041
精车端面的加工余量(表13-9) 1042
磨端面的加工余量(表13-10) 1042
切除渗碳层的加工余量(表13-11) 1043
孔加工余量 1044
在钻床上用钻模加工孔(孔的长度为直径的五倍)(表13-12) 1044
在自动车床、六角车床、车床或另一些机床上加工孔(孔长是直径的三倍)(表13-13) 1044
按照基孔制7级公差(H7)加工孔(表13-14) 1045
按照基孔制9级公差(H9)加工孔(表13-15) 1045
环孔钻加工余量(表13-17) 1046
单面钻削深孔的加工余量(表13-18) 1046
按照7级与9级公差加工预先铸出或热冲出的孔(表13-16) 1046
拉孔的加工余量(表13-19) 1047
拉正方形及多边形孔的加工余量(表13-20) 1047
拉键槽的加工余量(表13-21) 1047
磨孔的加工余量(表13-22) 1048
金刚石细镗孔的加工余量(表13-23) 1049
珩磨孔的加工余量(表13-24) 1049
研磨孔的加工余量(表13-25) 1049
平面的刨、铣、磨、刮加工余量(表13-27) 1050
刮孔的加工余量(表13-26) 1050
平面加工余量 1050
平面的研磨余量(表13-28) 1051
齿轮精加工的余量 1051
精滚齿或精插齿的加工余量(表13-29) 1051
剃齿的加工余量(表13-30) 1051
磨齿的加工余量(表13-31) 1051
直径大于400mm渗碳齿轮的磨齿加工余量(表13-32) 1051
花键精加工的余量 1052
蜗杆的精加工余量(表13-36) 1052
磨花键的加工余量(表13-38) 1052
精铣花键的加工余量(表13-37) 1052
蜗轮的精加工余量(表13-35) 1052
圆锥齿轮的精加工余量(表13-34) 1052
螺旋齿轮及双曲线螺旋齿轮精加工的余量(表13-33) 1052
攻螺纹及装配前的钻孔直径 1053
攻螺纹及装配前的钻孔直径(表13-39) 1053
第十四章 切削用量 1056
车削 1056
切削速度计算公式(表14-1) 1056
切削力计算公式(表14-2) 1058
切削部分的几何形状(表14-3) 1059
刀具磨损限度的参考值(表14-4) 1060
硬质合金的应用范围分类和用途分组(表14-5) 1061
粗车外圆进给量(表14-6) 1062
粗镗孔进给量及最大切削深度(表14-7) 1063
按表面粗糙度选择给量(表14-8) 1064
成形车削结构碳钢的进给量(表14-9) 1065
切断及车槽的进给量(表14-10) 1066
瓷刀车削的进给量(表14-11) 1066
高速钢车刀纵车削外圆的切削速度υ(表14-12) 1067
硬质合金车刀纵车削外圆的切削速度υ(表14-13) 1068
硬质合金车刀纵车削淬火钢的切削速度υ(表14-14) 1069
硬质合金车刀外圆纵车削的切削速度υ(表14-15) 1069
瓷刀纵车削钢外圆的切削速度υ(表14-16) 1070
切断、车槽及成形车削的切削速度υ(表14-17) 1070
使用条件变换时的修正系数(表14-18) 1071
刨、插加工切削速度和切削力计算公式(表14-19) 1075
刨削 1075
切削部分的几何形状(表14-20) 1076
龙门刨床刨平面、刨槽、切断的进给量及粗刨平面最大切削深度(表14-21) 1077
牛头刨床刨平面、刨槽及切断和插床插平面及槽的进给量(表14-22) 1078
龙门刨床刨平面的切削速度υ(表14-23) 1079
牛头刨床平面的切削速度υ(表14-24) 1080
刨槽及切断的切削速度υ(表14-25) 1081
插平面的切削速度υ(表14-26) 1081
使用条件变换时的修正系数(表14-28) 1082
高速钢刀具W18Cr4V插槽的切削速度υ(表14-27) 1082
钻、扩、铰 1084
钻削速度的计算公式(表14-29) 1084
轴向力N、扭矩M及功率P的计算公式(表14-30) 1084
切削部分允许的中等磨耗量(表14-31) 1085
工具钢钻头切削部分的几何参数(表14-32) 1086
手动进给钻孔的进给量(表14-33) 1087
工具钢钻头钻孔的进给量(表14-34) 1088
钻孔径0.25~1mm的钻头的几何参数及切削用量(表14-35) 1089
高速钢钻头钻孔的切削速度υ(表14-36) 1090
高速钢钻头扩钻的切削速度υ(表14-38) 1091
高速钢钻头扩钻的进给量f(表14-37) 1091
扩孔钻切削部分的几何参数(表14-39) 1092
工具钢扩孔钻扩孔的进给量(表14-40) 1092
高速钢扩孔钻扩孔的切削速度υ(表14-41) 1093
使用条件变换时的切削速度修正系数(表14-42) 1094
工具钢铰刀铰圆柱孔的进给量(表14-43) 1096
机铰刀切削部分的几何参数(表14-44) 1096
高速钢铰刀铰孔的切削速度(钢件)(表14-45) 1097
高速钢铰刀铰孔的切削速度(灰口铸铁)(表14-46) 1098
高速钢铰刀铰锥孔的进给量及切削速度(表14-47) 1099
高速钢刀具锪端面的进给量及切削速度(表14-48) 1099
钻中心孔及在热处理后修整中心孔的时间(表14-49) 1100
深孔加工的切削用量(表14-50) 1101
镗刀加工孔的进给量及切削速度(表14-51) 1102
镶硬质合金刀片钻头切削部分的几何参数(表14-52) 1102
钻孔的进给量(表14-53) 1103
扩钻的进给量(表14-54) 1103
硬质合金钻头YG8钻孔、扩钻的切削速度υ(表14-55) 1104
硬质合金麻花钻钻淬火钢及白口铸铁的切削用量(表14-56) 1104
镶硬质合金刀片扩孔钻切削部分的几何参数(表14-57) 1105
硬质合金扩孔钻扩孔的进给量(表14-58) 1105
硬质合金扩孔钻扩孔的切削速度υ(表14-59) 1106
镶硬质合金刀片机用铰刀切削部分的几何参数、进给量及切削用量(表14-60) 1106
加工碳钢及合金钢使用条件变换时的切削速度修正系数(表14-61) 1107
加工灰口铸铁及可锻铸铁使用条件变换时切削速度的修正系数(表14-62) 1108
铣削 1109
高速钢铣刀切削部分的几何参数(表14-63) 1109
硬质合金铣刀切削部分的几何参数(表14-64) 1110
镶陶瓷刀片的铣刀切削部分的几何参数(表14-65) 1112
铣刀切削部分后刃面允许的磨耗量(表14-66) 1112
铣削用量计算公式(表14-67) 1112
进给量及铣平面最大切削深度(表14-68) 1116
铣削进给量(表14-69) 1117
硬质合金套式面铣刀切削速度υ(表14-70) 1122
高速钢套式面铣刀切削速度υ(表14-71) 1123
精铣平面的切削速度υ(表14-72) 1124
陶瓷套式面铣刀切削速度υ(表14-73) 1124
硬质合金圆柱铣刀切削速度(表14-74) 1125
硬质合金三面丸圆盘铣刀的切削速度(表14-75) 1125
高速钢圆柱铣刀的切削速度(表14-76) 1126
高速钢三面刃圆盘铣刀铣平面及凸台的切削速度(表14-77) 1127
高速钢三面刃圆盘铣刀铣槽的切削速度(表14-78) 1128
硬质合金立铣刀铣平面及凸台的切削速度(表14-79) 1129
高速钢立铣刀铣平面的切削速度(表14-80) 1130
高速钢立铣刀铣槽的切削速度(表14-81) 1132
高速钢槽(花键)铣刀切削速度(表14-82) 1133
高速钢切断铣刀切断的切削速度(表14-83) 1134
高速钢样板铣刀、角度铣刀的切削速度(表14-84) 1135
高速钢键槽铣刀铣槽的切削用量(表14-85) 1136
高速钢T形槽铣刀的切削用量(表14-86) 1136
高速钢燕尾槽铣刀的切削用量(表14-87) 1136
面铣刀、圆盘铣刀铣铝合金的切削用量(表14-88) 1137
使用条件变换时的切削速度修正系数(表14-89) 1137
螺纹加工 1142
螺纹加工的切削速度计算公式(表14-90) 1142
车螺纹的切削用量(表14-91) 1144
按螺距和螺纹精度确定车螺纹精行程次数(表14-93) 1145
车螺纹的切削速度(表14-92) 1145
攻螺纹的切削用量(表14-94) 1146
旋风切削螺纹的切削用量(表14-95) 1147
板牙铰螺纹的切削速度(表14-96) 1147
铣螺纹的圆周进给量(表14-97) 1148
高速钢梳形铣刀铣螺纹的切削速度(表14-98) 1148
高速钢梳形铣刀钎灰口铸铁HB140~180螺纹的切削速度(表14-99) 1148
磨螺纹的切削用量(表14-100) 1149
齿轮、花键加工 1149
滚齿、插齿、滚花键的切削速度及功率的计算公式(表14-101) 1149
滚齿的进给量(表14-102) 1150
滚刀滚齿的切削速度(钢)(表14-103) 1151
滚刀滚齿的切削速度(灰口铸铁)(表14-104) 1152
滚刀滚蜗轮的切削用量(表14-105) 1153
模数片铣刀粗铣齿的切削用量(表14-106) 1154
滚刀滚直花键轴的进给量(表14-107) 1154
直齿花键轴滚刀滚花键的切削速度(钢)(表14-108) 1155
圆盘插齿刀插齿的进给量(表14-109) 1156
圆盘插齿刀插齿的切削速度(表14-110) 1157
圆盘剃齿刀剃齿的切削用量(表14-111) 1158
锥齿轮加工的切削速度(表14-112) 1158
磨齿的磨轮选择(表14-113) 1159
双盘形砂轮磨齿的切削用量(表14-114) 1160
锥形砂轮磨齿的切削用量(表14-115) 1161
磨淬火钢花键的切削用量(表14-116) 1162
拉削 1163
制造拉刀的材料和拉刀齿的几何参数(表14-117) 1163
拉削的进给量(单面的齿升)(表14-118) 1163
拉削速度分组(表14-119) 1164
拉削速度(表14-120) 1165
拉刀切削刃在单位长度上的切削力(表14-121) 1165
磨轮的选择(表14-122) 1166
磨削 1166
切削用量的计算公式(表14-123) 1167
磨轮耐用度(表14-124) 1168
无心磨通磨的粗磨切削用量(表14-125) 1169
无心磨通磨的精磨切削用量(表14-126) 1170
切入式无心磨的切削用量(表14-127) 1171
纵进给磨外圆的切削用量(表14-128) 1172
磨内圆的切削用量(表14-129) 1174
用磨轮圆周粗磨平面的切削用量--矩形工作台平面磨(表14-130) 1177
用磨轮圆周精磨平面的切削用量--矩形工作台平面磨(表14-131) 1178
用磨轮圆周粗磨平面的切削用量--圆形工作台平画磨(表14-132) 1179
用磨轮圆周精磨平面的切削用量--圆形工作台平面磨(表14-133) 1180
用磨轮端面磨平面的切削用量--矩形工作台平面磨(表14-134) 1181
用磨轮端面磨平面的切削用量--圆形工作台平面磨(表14-135) 1182
用磨轮端面磨平面深磨法的切削用量--圆形工作台平面磨(表14-136) 1183
用磨轮端面磨平面的切削动力--圆形工作台平面磨 1184
第十五章 机动时间计算方法 1186
车削工作 1186
刨削、插削工作 1187
车刀及镗刀切入及超出长度(表15-1) 1188
龙门刨床工作台的超出长度(表15-2) 1189
牛头刨床及插床上切刀的超出长度(表15-3) 1189
钻削工作 1190
试刀的附加长度l3(表15-4) 1190
加工计算长度(表15-5) 1192
在实体材料上钻孔单刃磨钻头的切入及超出长度(表15-6) 1192
双重刃磨的钻头钻孔和扩孔的切入及超出长度(表15-7) 1193
单刃磨钻头扩钻时的切入及超出长度(表15-8) 1193
扩孔的切入及超出长度(表15-9) 1194
铰孔的切入及超出长度(表15-10) 1194
与清除切屑有关的钻头退出及引入的次数(表15-11) 1195
铣削工作 1196
圆柱形铣刀、三面刃铣刀、槽铣刀及样板铣刀的切入及超出长度(表15-12) 1198
圆柱形铣刀、三面刃铣刀铣削圆形表面的切入及超出长度(表15-13) 1199
面铣刀对称铣削的切入及超出长度(表15-14) 1200
面铣刀不对称铣削的切入及超出长度(1)(表15-15) 1201
面铣刀不对称铣削的切入及超出长度(2)(表15-16) 1201
立铣刀切入及超出长度(表15-17) 1202
螺纹加工 1203
齿轮加工 1205
在插齿机上用梳形插齿刀加工时的计算齿数(表15-18) 1208
用盘形模数铣刀铣圆柱齿轮的切入及超出长度(表15-19) 1208
用滚刀滚齿时的切入及超出长度(表15-20) 1209
分度转换时间(锥形砂轮磨齿)(表15-24) 1210
半精磨及精磨分度转换的时间(双砂轮范成法磨齿)(表15-23) 1210
刨齿机的切入及超出长度(表15-22) 1210
插齿机的切入及超出长度(表15-21) 1210
工作行程长度(锥形砂轮磨齿)(表15-25) 1211
拉削工作 1211
由零件长度所决定的拉刀齿距(表15-26) 1212
磨削工作 1213
外圆磨的系数K(表15-27) 1213
光整时间τ(表15-28) 1214
光整时间的修正系数(表15-29) 1214
平面磨的系数K(表15-30) 1216
尺寸链和装配方法 1218
概述 1218
第十六章 装配工艺 1218
装配方法及应用范围(表16-1) 1219
装配的组织形式 1219
装配的组织形式(表16-2) 1219
装配过程中的钳工修配工作 1220
钳工修配工作的主要类型、用途和机械化措施(表16-3) 1220
用涂色法检验平面的接触精度(表16-4) 1221
气动砂轮的技术规格(表16-5) 1221
电动砂轮机的技术规格(表16-6) 1222
气钻的技术规格(表16-7) 1222
装配零件的尺寸检验方法(表16-9) 1223
装配零件的尺寸检验 1223
电钻的技术规格(表16-8) 1223
零件和部件的密封性及强度试验 1226
回转零件的平衡 1227
推荐选用的水平导轨宽度b(表16-10) 1228
通用卧式动平衡机技术规格(表16-11) 1229
刚性转子的平衡精度等级(表16-12) 1229
零件的清洗 1231
零件的清洗方法(表16-13) 1231
可拆连接的装配 1232
螺纹连接 1232
螺纹的拧紧力矩(表16-14) 1232
气动扳手的技术规格(表16-15) 1233
电动板手的技术规格(表16-16) 1234
气动螺钉旋具的技术规格(表16-17) 1234
电动螺钉旋具的技术规格(表16-18) 1234
键、花键和圆锥面连接 1235
不可拆连接的装配 1235
具有一定过盈的连接 1235
具有一定过盈不可拆连接的装配方法(表16-19) 1235
压合时的摩擦系数f的数值(表16-20) 1236
滚口及卷边连接 1238
胶接连接 1239
气动铆钉机的技术规格(表16-21) 1239
铆钉连接 1239
焊接连接 1239
- 《激光加工实训技能指导理实一体化教程 下》王秀军,徐永红主编;刘波,刘克生副主编 2017
- 《Maya 2018完全实战技术手册》来阳编著 2019
- 《先进激光加工技能实训》肖海兵主编 2019
- 《高等教育双机械基础课程系列教材 高等学校教材 机械设计课程设计手册 第5版》吴宗泽,罗圣国,高志,李威 2018
- 《慢性呼吸系统疾病物理治疗工作手册》(荷)瑞克·考斯林克(RikGosselink) 2020
- 《金甲虫》(美)爱伦·坡著,焦菊隐;文楚安等译 2019
- 《战略情报 情报人员、管理者和用户手册》(澳)唐·麦克道尔(Don McDowell)著 2019
- 《实用内科手册》黄清,阮浩航主编 2016
- 《集成曲谱金集 卷7 卷8》黄天骥总主编;王季烈,刘富梁辑 2018
- 《基层医疗卫生机构安全用药手册》黎月玲,熊慧瑜 2019
- 《钒产业技术及应用》高峰,彭清静,华骏主编 2019
- 《现代水泥技术发展与应用论文集》天津水泥工业设计研究院有限公司编 2019
- 《异质性条件下技术创新最优市场结构研究 以中国高技术产业为例》千慧雄 2019
- 《Prometheus技术秘笈》百里燊 2019
- 《中央财政支持提升专业服务产业发展能力项目水利工程专业课程建设成果 设施农业工程技术》赵英编 2018
- 《药剂学实验操作技术》刘芳,高森主编 2019
- 《林下养蜂技术》罗文华,黄勇,刘佳霖主编 2017
- 《脱硝运行技术1000问》朱国宇编 2019
- 《催化剂制备过程技术》韩勇责任编辑;(中国)张继光 2019
- 《信息系统安全技术管理策略 信息安全经济学视角》赵柳榕著 2020