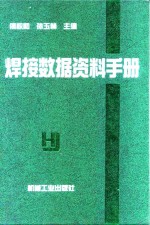
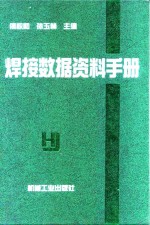
焊接数据资料手册PDF电子书下载
- 电子书积分:23 积分如何计算积分?
- 作 者:傅积和,孙玉林主编
- 出 版 社:北京:机械工业出版社
- 出版年份:1994
- ISBN:7111038622
- 页数:878 页
第一章概述 1
1焊接方法的发明年代及国别 1
2焊接方法的分类及特点 1
2.1基本焊接方法及分类 1
目 录 1
2.2常用焊接方法的适用范围 2
2.3常用金属材料适用的焊接方法 3
2.4常用焊接热源的特性 4
2.5常用焊接方法的热效率 4
2.6常用电弧焊方法的熔深系数 4
2.7常用电弧焊方法的有效功率因数 5
2.8不同焊接方法焊缝金属中的扩散氢含量 5
2.9常用焊接热源的能量密度和热量消耗 5
2.10常用焊接热源的焊接热输入比较 5
3.1电弧焊方法的比较 6
3焊接方法的比较及选择 6
3.2 MIG焊、CO2气体保护电弧焊、TIG焊的比较 7
3.3 MIG焊、TIG焊焊接性能比较 8
3.4 CO2气体保护电弧焊和手工电弧焊熔敷速度的比较 9
3.5TIG焊和等离子弧焊焊接速度的比较 9
3.6等离子弧和钨极电弧的比较 9
3.7电子束焊、等离子弧焊、TIG焊的焊缝断面形状比较 10
3.8 TIG焊、MIG焊和等离子弧焊焊接成本的比较 10
3.9 CO2气体保护电弧焊和埋弧焊抗锈能力的比较 10
3.10几种气体保护焊接方法的应用及特点 11
参考文献 11
1.2.3碳当量公式(CEN) 12
1.2.2碳当量公式(Pcm) 12
1.2.1碳当量公式(CE、Ceq) 12
1.2钢的碳当量公式 12
1.1焊接性试验方法分类 12
1金属焊接性 12
第二章焊接冶金 12
1.2.4各种碳当量公式及其相关系数 13
1.2.5常用低合金高强度钢的碳当量及允许的最大硬度(Hmax) 13
1.2.6不同强度级别钢种的限界Pcm值 14
1.3主要焊接性试验方法 14
1.3.1斜y形坡口焊接裂纹试验 14
1.3.2刚性固定对接裂纹试验 16
1.3.3十字接头裂纹试验 16
1.3.4 T形接头焊接裂纹试验 18
1.3.5搭接接头(CTS)焊接裂纹试验 19
1.3.6窗形拘束裂纹试验 22
1.3.7压板对接(FISCO)焊接裂纹试验 22
1.3.8拉伸拘束裂纹试验 24
1.3.9刚性拘束裂纹试验 25
1.3.10插销试验 27
1.3.11可变拘束裂纹试验 30
1.3.12再热裂纹敏感性试验 31
(1)铁研式自拘束试验 31
(2)插销试验 31
1.3.13层状撕裂敏感性试验 33
(1)Z向拉伸层状撕裂敏感性试验 33
(2)Granfild层状撕裂试验 33
1.3.14焊接热影响区(HAZ)最高硬度试验 34
1.3.15焊接热影响区(HAZ)最高硬度计算公式 35
2焊接热影响区(HAZ)的组织分布及连续冷却组织转变图 36
2.1焊接热影响区的组织分布 36
2.1.1焊接热影响区内不同温度范围的各区划分 36
2.1.5不同焊接方法的热影响区平均尺寸 37
2.1.4 16Mn钢的焊接热影响区 37
2.1.2距离焊缝各点的焊接热循环 37
2.1.3低碳钢热影响区的组织分布特征及性能 37
2.1.6不同钢种的焊接热影响区 38
2.2连续冷却组织转变图 38
2.2.1低合金钢的模拟焊接CCT图 38
2.2.2某些高强度钢的临界冷却时间(t8/5) 39
2.2.3 16MnR钢的焊接CCT图 40
2.2.4 15MnVN钢的焊接CCT图 41
2.2.5 18 MnMoNb钢的焊接CCT图 42
2.2.6 14MnMoNbB钢的焊接CCT图 43
2.2.7 15 MnMoVNRE钢的焊接CCT图 44
2.2.8 21/4Cr-1Mo钢的焊接CCT图 45
2.2.9 12Ni2CrMoV钢的焊接CCT图 46
2.3焊接冷却时间(一) 47
2.3.1计算公式(日本稻垣公式) 47
2.2.11美国T-1钢的焊接CCT图 47
2.2.10 日本HW 36钢的焊接CCT图 47
2.3.2不同焊接方法计算冷却时间的各系数值 48
2.3.3手弧焊t8/5(a)和t8/3(b)冷却时间线算图 48
2.3.4 CO2气体保护电弧焊t8/5(a)和t8/3(b)冷却时间线算图 49
2.3.5埋弧焊t8/5(a)和t8/3(b)冷却时间线算图 49
2.3.6 t8/5与线能量(E)和板厚(δ)的关系 50
2.4焊接冷却时间(二) 50
2.4.1传热理论计算公式 50
2.4.2临界厚度计算公式 51
2.4.3临界厚度的线算图 51
2.4.4求t8/5的作图法 51
3低合金结构钢焊缝的组织 53
3.2低合金结构钢焊缝组织的形态 54
3.1合金结构钢中合金元素的作用 54
3.3低合金结构钢焊缝的组织转变图及韧化途径 55
4焊接裂纹 56
4.1焊接裂纹的分布特征 56
4.2焊接裂纹分类表 56
4.3热裂纹 57
4.3.1结晶裂纹产生的原因 57
4.3.2铁二元和镍二元共晶成分及共晶温度 57
4.3.3合金元素对结晶裂纹的影响 57
(1)临界应变增长率(简称CST) 57
(2)热裂纹敏感系数(简称HCS) 57
4.4冷裂纹 58
4.4.2氢在不同钢中的扩散系数 58
4.4.1碳当量与临界含氢量的关系 58
4.3.5结晶裂纹的防止措施 58
4.3.4不锈钢焊缝中合金元素对结晶裂纹的影响 58
4.4.3拘束应力的分类 59
4.4.4一些钢的相变温度及所引起的应变 59
4.4.5拘束度R及其计算公式 60
4.4.6实际结构焊接接头拘束度的有关数据 60
4.4.7一般常用钢的临界拘束度Rcr 61
4.4.8拘束应力公式 61
4.4.9拘束系数计算公式 61
4.4.10临界拘束应力的经验公式 61
4.4.11防止冷裂纹的预热温度经验公式 62
4.4.12 Pcm及板厚与预热温度的关系 62
4.4.13Pw与预热温度的关系 63
4.4.14根据Pw及板厚δ确定的局部预热温度 63
4.5再热裂纹 64
4.4.17采用后热对预热温度的影响 64
4.5.1判断再热裂纹的经验公式 64
4.4.16避免裂纹所需的后热温度和后热时间 64
4.4.15后热温度的经验公式 64
4.5.2防止再热裂纹的预热及后热 65
4.6层状撕裂 65
4.6.1层状撕裂敏感性评定公式 65
4.6.2层状撕裂敏感性指数Pl与(σz)cr的关系 65
4.6.3防止层状撕裂的措施 65
参考文献 65
第三章电弧焊 67
1手工电弧焊 67
1.1焊条 67
1.1.1焊条的型号 67
(1)焊条型号的分类及代号 67
(2)焊条长度的规定 67
(4)低合金钢焊条型号的编制方法 68
(3)碳钢焊条型号的编制方法 68
(5)不锈钢焊条型号的编制方法 70
(6)铸铁焊条型号的编制方法 70
1.1.2焊条牌号的分类及表示方法 71
(1)焊条牌号的类别及符号 71
(2)焊条型号大类与焊条牌号大类对照表 71
(7)不锈钢焊条牌号的表示方法 72
(6)低温钢焊条牌号的表示方法 72
(5)铬和铬钼耐热钢焊条牌号的表示方法 72
(4)结构钢焊条牌号的表示方法 72
(3)焊条牌号的药皮类型及焊接电源的表示方法 72
(8)堆焊焊条牌号的表示方法 73
(9)铸铁焊条牌号的表示方法 73
(10)镍及镍合金焊条牌号的表示方法 73
(11)铜及铜合金焊条牌号的表示方法 73
(12)铝及铝合金焊条牌号的表示方法 73
(14)结构钢焊条的牌号、型号及主要用途 74
(13)特殊用途焊条牌号的表示方法 74
(15)铬及铬钼耐热钢焊条的牌号、型号及主要用途 77
(16)低温钢焊条的牌号、型号及主要用途 78
(17)不锈钢焊条的牌号、型号及主要用途 78
(18)堆焊焊条的牌号、各国标准型号及堆焊层硬度 82
(19)铸铁焊条的型号、牌号及主要用途 84
(20)镍及镍合金焊条的牌号及焊缝主要成分 84
(21)铜及铜合金焊条的牌号、型号及焊缝主要成分 84
(22)铝及铝合金焊条的牌号、型号及焊缝主要成分 85
(23)特殊用途焊条的牌号及主要用途 85
1.1.3药皮 85
(1)国产焊条药皮类型及特点 85
(2)常用药皮原材料的组成与作用 86
(3)焊条药皮矿物类原材料的成分及作用 86
(5)焊条药皮中铁合金和金属粉的成分及作用 88
(4)焊条药皮中有机物原材料的成分及作用 88
(6)焊条药皮中化工产品类的成分及作用 89
(7)焊条药皮组成物用量范围 90
(8)焊条药皮成分组成范围 90
(9)焊条药皮粉剂的颗粒度(目数) 91
(10)几种筛号及规格 91
(11)不同类型焊条药皮对钠水玻璃模数及密度的要求 91
(12)常用粘塑剂及其适用范围 92
(13)几种焊条保护气氛的组成 92
(14)几种铁合金的焙烧钝化规范 92
(15)焊条熔渣凝固温度范围实测值 93
1.1.4焊条性能 93
(1)几种焊条工艺性能一览表 93
(2)几种焊条冶金性能一览表 94
(6)不锈钢焊条药皮表面的温升曲线 95
(5)焊接时沿焊条长度药皮表面上的温度分布 95
(4)焊芯的温度与熔化时间的关系 95
(3)焊条的熔化速度 95
1.1.5焊条的烘干 96
(1)焊条的烘干脱水曲线 96
(2)焊条的烘干参数 96
(3)焊条的再烘干参数 96
(4)连续烘干时间对焊条的影响 96
(5)烘干次数对焊条的影响 97
(6)焊条烘干温度与焊缝中扩散氢含量的关系 97
1.2操作及工艺参数 98
1.2.1定位焊尺寸 98
1.2.2对接装配的错边量允许值 98
1.2.3电弧长度对焊接质量的影响 98
1.2.4焊接电流对气孔的影响 98
1.2.7角焊焊条角度 99
1.2.8焊接磁场对磁偏吹的影响 99
1.2.6对接平焊的焊条角度 99
1.2.5焊接电流对焊缝金属化学成分的影响 99
1.3焊接电源 100
1.3.1各类弧焊电源的特点及适用范围 100
1.3.2各种外特性的形状及适用范围 100
1.3.3常用弧焊变压器的类型及用途 100
1.3.4弧焊整流器的类型及用途 101
1.3.5直流弧焊发电机的类型及用途 101
1.3.6负载持续率对焊接电源效率的影响 102
1.3.7弧焊电源的类型及其适用范围 102
1.3.8焊接电缆截面与焊接电流、电缆长度的关系 103
1.3.9交流弧焊机电缆不同放置情况的电能损失 103
1.3.10常用焊钳的型号及规格 103
1.3.11护目玻璃选用表 103
1.3.13直流弧焊整流器的常见故障及检修方法 104
1.3.12交流弧焊机的常见故障及检修方法 104
2埋弧焊 105
2.1焊剂 106
2.1.1熔炼焊剂和非熔炼焊剂的特点 106
2.1.2硅酸锰焊剂的典型成分 106
2.1.3 MnO-SiO2系统相图 106
2.1.4 国产埋弧焊剂的成分和用途 107
(1)熔炼焊剂的分类及成分 107
(2)烧结焊剂的分类及成分 107
2.1.5国产熔炼焊剂的牌号表示方法 108
2.1.6国产烧结焊剂的牌号表示方法 108
2.1.7常用埋弧焊剂的用途及其配用焊丝 109
2.1.8 日本的埋弧焊剂标准 110
2.1.9焊剂中SiO2含量与硅过渡量[△Si]的关系 110
2.1.10焊剂中MnO含量与锰过渡量[△Mn]的关系 110
2.1.13电弧电压对硅和锰过渡量的影响 111
2.1.11焊剂氧化性对合金元素过渡量的影响 111
2.1.12焊接电流对硅和锰过渡量的影响 111
2.1.14焊剂中CaF2含量对焊缝气孔的影响 112
2.1.15焊剂产生CO2气体数量对焊缝金属含氢量[H]的影响 112
2.1.16温度对焊剂粘度与电阻的影响 112
2.1.17熔炼焊剂的吸湿曲线 112
2.1.18非熔炼焊剂的吸湿曲线 113
2.1.19焊剂的烘干温度 113
2.1.20焊剂粒度及筛子度量表 113
2.1.21焊剂粒度及其适用的焊接电流范围 114
2.2焊丝 114
2.2.1常用结构钢埋弧焊焊接材料的选用 114
2.2.2同种焊丝配合不同焊剂时焊缝金属的化学成分 115
2.2.3日本焊丝的种类及成分 115
2.3.1埋弧焊的经验公式 116
2.3焊接工艺参数 116
2.2.4美国埋弧焊用焊丝的分类及成分 116
2.2.5焊丝各部位及焊缝金属的锰硅含量 116
2.3.2焊接电流 117
(1)焊丝直径与适用的焊接电流范围 117
(2)焊接电流对熔深的影响 117
(3)焊接电流对焊道形状的影响 117
(4)焊接电流对焊丝熔化速度的影响 118
(5)焊接电流与焊接速度的关系 118
2.3.3电弧电压 118
(1)电弧电压对熔深的影响 118
(2)电弧电压和焊缝形状的关系 118
(3)电弧电压对焊剂熔化速度的影响 118
2.3.5焊接电流、电弧电压、焊接速度对熔深的综合影响 119
(1)焊丝直径对熔化速度的影响 119
2.3.6焊丝直径 119
(1)焊接速度对熔深的影响 119
(2)焊接速度对焊道形状的影响 119
2.3.4焊接速度 119
(2)焊丝直径对焊缝表面宽度及熔深的影响 120
2.3.7焊丝伸出长度和电流密度对焊丝熔化速度的综合影响 120
2.3.8埋弧焊实际焊接电流和电弧电压的关系 120
2.3.9熔剂层厚度对埋弧焊表面成形及熔透程度的影响 121
2.3.10焊道截面积的计算 121
2.3.11焊丝倾角对焊道形状的影响 122
2.3.12母材倾角对焊道形状的影响 122
2.3.13对接接头坡口形状 122
(1)中厚板 122
(2)留间隙双面焊的焊接工艺参数 123
(1)单面焊双面成形的焊接工艺参数 123
(2)厚板双Y形坡口的尺寸 123
2.3.14埋弧焊工艺举例 123
(3)开坡口双面焊的焊接工艺参数 124
(4)船形焊的焊接工艺参数 124
(5)横角焊的焊接工艺参数 124
(6)薄板的焊接工艺参数 125
2.3.15筒体环缝埋弧焊 125
(1)偏心距离 125
(2)筒体直径和最大焊接电流 125
2.3.16埋弧焊缺陷产生的原因及防止措施 126
(1)钨极氩(氦)弧的特性 127
(3)焊接不同金属时钨极电弧的特性 127
(2)氦、氩、氢混合气体的电弧特性 127
3.1 TIG焊电弧 127
3 TIG焊接 127
3.1.1 TIG焊电弧的静特性 127
3.1.5TIG焊电弧的弧柱温度分布 128
3.2.1国产电极的种类和成分 128
3.1.6 TIG焊电弧中阳极、阴极和气体的热量分布 128
3.2电极 128
3.1.4 TIG焊电弧的极性特点 128
3.1.3 TIG焊电弧电压和气体压力的关系 128
3.1.2 TIG焊电弧电压和弧长的关系 128
3.2.2日本电极的种类和成分 129
3.2.3美国电极的种类和成分 129
3.2.4常用电极材料的电子发射性能 129
3.2.5不同电极和不同材料所需的空载电压 130
3.2.6电极的端头形状 130
3.2.7电极的不同端头形状与电弧燃烧稳定性及焊缝成形的关系 130
3.2.9电极伸出长度和最大允许焊接电流的关系 131
3.2.10不同电极的最大允许焊接电流比较 131
3.2.8电极顶角对熔宽和熔深的影响 131
3.2.11不同极性纯钨电极的最大允许焊接电流 132
3.2.12引弧时钨极的损耗 132
3.2.13电极沿长度方向的温度分布 132
3.3保护气体 132
3.3.1国产焊接用氩气的成分 132
3.3.2日本焊接用氩气标准 133
3.3.3氩、氦保护气体的特性 133
3.3.4各种材料适用的保护气体及特点 133
3.3.5不同材质所使用的氩气纯度 134
3.3.6 Ar、He、H2、N2气体的热导率与温度的关系 134
3.4 TIG焊工艺及参数 134
3.4.1材料种类和TIG焊极性 134
3.4.2保护气体流量和风速的关系 134
3.4.5焊接电流和喷嘴直径、气体流量的关系 135
3.4.3氩气流量与保护效果的关系 135
3.4.4气体流量和风对保护效果的影响 135
3.4.6焊缝表面色泽与气体保护效果 136
3.4.7焊接电流、焊接速度和焊道形状的关系 136
3.4.8焊接速度对熔深、焊道形状的影响 136
3.4.9奥氏体不锈钢薄板手工TIG焊的焊接工艺参数 136
3.4.10钛及钛合金手工TIG焊的焊接工艺参数 137
3.4.11管子TIG打底焊的焊接工艺参数 137
3.4.12管子手工TIG焊的焊接工艺参数(V形坡口) 138
3.4.13管子手工TIG焊的焊接工艺参数(U形坡口) 139
3.4.14管子TIG自动焊的焊接工艺参数(悬空焊) 140
3.4.15自动TIG焊的焊接工艺参数(平焊位置、带铜垫夹具) 140
3.5 TIG焊操作 140
3.5.1焊丝添加方法 140
3.5.4水平搭接角焊时焊炬、焊丝的角度 141
3.5.3横角焊时焊炬、焊丝的角度 141
3.5.2平焊时焊炬、焊丝的角度 141
3.6脉冲TIG焊 142
3.6.1各种材料脉冲TIG焊时脉冲电流参数的选择 142
3.6.2常用脉冲TIG焊脉冲频率的选择 142
3.6.3脉冲电流和基值电流的组合对焊缝成形的影响 142
3.6.4不同板厚的焊缝咬边与脉冲幅比和脉冲宽比的关系 142
3.6.5脉冲幅比与脉冲频率的关系 142
3.6.6不锈钢薄板脉冲TIG焊的焊接工艺参数 142
3.6.7不同材料的管子全位置脉冲TIG焊的焊接工艺参数 143
3.7 TIG点焊 143
3.7.1TIG点焊程序 143
3.7.2 TIG点焊时间对焊核直径和强度的影响 143
4 MIG焊 144
4.1.1焊接用保护气体的特征 144
4.1保护气体 144
3.7.4 1 Cr 18 Ni 9 Ti钢TIG点焊的焊接工艺参数 144
3.7.3焊接电流对焊核直径和强度的影响 144
4.1.2保护气体的分类 145
4.1.3焊接黑色金属时保护气体的分类 145
4.1.4保护气体分类的三元图 146
4.1.5 MIG焊适用的保护气体 146
4.1.6常用富Ar混合气体的特点及应用范围 147
4.1.7国产焊接用气体的容器涂色标记 148
4.1.8焊接用气体的技术要求 148
4.1.9德国焊接用保护气体 148
4.2熔滴过渡 149
4.2.1熔滴过渡的种类及特点(直流反接) 149
4.2.2焊接电流对熔滴过渡频率及熔滴体积的影响 149
4.2.3德国标准DIN 1910,Blatt4关于电弧形式的分类及熔滴过渡特征 149
4.3临界电流 149
4.3.4 Ar、CO2、O2二元成分及三元成分保护气体的临界电流区 150
4.3.3气体混合比对临界电流的影响 150
4.3.1各种焊丝的临界电流 150
4.3.2焊丝直径对临界电流的影响 150
4.4 MIG焊工艺及参数 151
4.4.1气体混合比 151
(1)Ar-CO2气体混合比对短路过渡频率的影响 151
(2)短路过渡时气体混合比对飞溅率的影响 151
(3)Ar-He气体混合比焊铝时对焊道形状的影响 152
(4)Ar-CO2气体混合比对焊缝金属含氧量的影响 152
(8)Ar-O2气体混合比对焊丝熔化速度的影响 153
(9)Ar-CO2气体混合比对空间焊缝成形的影响 153
(10)Ar-CO2气体混合比对焊接工艺的影响 153
(7)Ar-CO2气体混合比对焊丝熔化*速度的影响 153
(6)Ar-CO2气体混合比对焊缝冲击吸收功的影响 153
(5)Ar-CO2气体混合比对合金元素过渡率的影响 153
(11)保护气体成分对18-8 Ti钢焊缝化学成分和抗晶间腐蚀性能的影响 154
(12)保护气体中含氮量对不锈钢焊缝中铁素体含量和热裂纹倾向的影响 155
4.4.2焊接电流 155
(1)焊接电流对焊道形状的影响 155
(2)焊接电流和电弧电压的关系 155
(3)焊接电流和送丝速度的关系 156
(4)MIG焊使用的焊接电流范围(碳钢) 156
4.4.3焊接速度对焊道形状的影响 156
4.4.4焊丝伸出长度 157
(1)焊丝伸出长度对焊道形状的影响 157
(2)焊丝伸出长度对熔化速度的影响 157
4.4.5焊道形状、熔敷速度的调整方法 157
5.2.1 CO2饱和气体的性能 158
5.2 CO2气体 158
5.2.2 CO2分解度与温度的关系 158
5.1.1 CO2电弧的熔化特性 158
5.1 CO2电弧 158
5CO2气体保护电弧焊 158
5.2.3 CO2露点与焊缝金属含氢量的关系 159
5.2.4 CO2气体湿度与焊缝金属含氢量的关系 159
5.2.5 CO2气体中的水分与瓶中压力的关系 159
5.2.6日本焊接用CO2气体标准 159
5.3焊丝 160
5.3.1国产CO2焊常用焊丝的化学成分和用途 160
5.3.2 日本CO2焊丝的化学成分及熔敷金属的力学性能 160
5.3.3美国CO2焊丝的种类及性能 161
5.3.4不同牌号焊丝焊缝金属的化学成分及力学性能 161
5.3.5采用H 08Mn 2 SiA焊丝的焊缝及接头力学性能 161
5.3.6 CO2焊丝的最低含Mn、Si量 162
5.3.7焊丝含氢量对焊缝金属含氢量的影响 162
(2)药芯焊丝的截面形状 163
(1)药芯焊丝和实心焊丝的比较 163
5.3.8药芯焊丝 163
(3)国产药芯焊丝的药芯成分 164
(4)常用药芯焊丝的规格及适用的焊接方法 164
5.4 CO2焊焊接工艺及参数 164
5.4.1不同极性的应用范围及特点 164
5.4.2焊接电流 164
(1)焊接电流对焊缝形状的影响 164
(2)焊接电流、电弧电压对气孔的影响 164
(4)焊接电流对飞溅率的影响 165
(3)焊接电流对熔敷速度的影响 165
(5)焊接电流对熔滴过渡频率的影响 166
(6)焊接电流和熔滴体积的关系 166
5.4.3电弧电压 166
(1)电弧电压对焊道形状的影响 166
(2)电弧电压对短路频率的影响 166
(1)CO2气体流量和风速的关系 167
5.4.5气体流量 167
(4)电弧电压变化对焊缝含N2量及气孔的影响 167
(3)电弧电压对飞溅率的影响 167
5.4.4焊接速度对焊道形状的影响 167
(2)CO2气体流量的选择 168
(3)CO2气体流量和喷嘴高度的关系 168
5.4.6焊丝直径 168
(1)焊丝直径对焊缝熔深的影响 168
(2)焊丝直径与焊丝熔化速度的关系 168
(3)不同直径焊丝颗粒过渡的焊接电流下限值及电弧电压范围 168
(4)各种直径焊丝的适用范围 169
5.4.7导电嘴与母材的距离 169
(1)导电嘴与母材的距离对焊丝熔化速度的影响 169
(2)导电嘴与母材的距离对焊接电流和熔深的影响 169
5.4.8典型的焊接工艺参数 170
(2)不同直径焊丝焊接12 mm钢板时的焊接电流和电弧电压范围 170
(1)常用焊接电流和电弧电压的范围 170
(4)焊丝伸出长度对焊接过程的影响 170
(3)焊丝伸出长度与喷嘴内径的关系 170
(3)细丝CO2半自动焊工艺参数 171
(4)细丝CO2自动焊工艺参数 171
(5)粗丝CO2焊工艺参数 172
(6)CO2-O2半自动焊工艺参数 173
(7)CO2电弧点焊工艺参数 174
(8)采用药芯焊丝各种位置焊接的焊接电流范围 175
(9)药芯焊丝对接平焊工艺 175
5.4.9 CO2半自动焊焊接缺陷产生的原因及防止措施 176
5.5 CO2焊的操作方法 177
5.5.1 CO2半自动焊运条法 177
(1)前进法的特点 177
(2)后退法的特点 177
5.5.6水平旋转管焊接时焊炬的位置与焊道成形的关系 178
5.5.5焊道的接头要领 178
5.5.3横角焊时的焊炬角度 178
5.5.2平焊时的焊炬角度 178
5.5.4横焊时的焊炬角度 178
5.6 CO2焊机 179
5.6.1 CO2焊机的组成 179
5.6.2不同焊丝直径时焊接回路的电感值 179
5.6.3 CO2焊常用喷嘴的结构及特点 179
5.6.4不同焊丝直径选用的导丝管孔径 180
5.6.5常用导电嘴的结构形式 180
参考文献 180
(1)电阻焊的简要分类 182
(1)各种金属材料电阻焊的焊接性指数 182
1.1.2金属材料电阻焊的焊接性 182
(2)主要电阻焊方法示意图 182
1.1.1电阻焊类型 182
1.1电阻焊 182
1压焊 182
第四章其它焊接方法 182
(2)各种合金相互间电阻焊的焊接性 184
1.1.3电阻焊的电极材料 184
(1)美国电阻焊机制造业协会(R.W.M.A)的电极材料标准 184
(2)日本电阻焊的电极材料 186
(3)国内电阻焊的电极材料 186
1.1.4点焊 187
(1)点焊电极 187
(2)点焊时电极材料的选择 187
(3)点焊工件与电极的各种配置方式 189
(4)点焊接头的搭接宽度 189
(5)焊点的最小焊点距 189
(7)点焊接头质量等级 190
(6)低碳钢串联点焊时板厚、焊点距与分流的关系 190
(8)低碳钢点焊的焊接工艺参数 191
(9)可淬硬碳钢点焊的焊接工艺参数 192
(10)镀锌钢板点焊的焊接工艺参数 193
(11)不锈钢点焊的焊接工艺参数 194
(12)铝合金点焊的焊接工艺参数 195
(13)焊点直径和强度 197
(14)焊点表面缺陷及其产生原因 199
1.1.5缝焊 200
(1)低碳钢缝焊的焊接工艺参数 200
(2)奥氏体不锈钢缝焊的焊接工艺参数 201
(1)凸起的形状及尺寸 202
1.1.6凸焊 202
(3)铝合金缝焊的焊接工艺参数 202
(2)低碳钢凸焊的焊接工艺参数 203
(3)不锈钢凸焊的焊接工艺参数 204
(4)铝合金凸焊的焊接工艺参数 205
(5)低碳钢线材交叉凸焊的焊接工艺参数 205
1.1.7电阻对焊时的电流密度和压力 205
1.1.8闪光对焊 206
(1)闪光焊接头的预加工 206
(2)闪光焊接头最大板宽与板厚的关系 206
(3)闪光焊接头最大管径与管壁厚度的关系 206
(4)管、棒、板材闪光焊时伸出长度和总收缩量及烧化时间的关系 207
1.2.2扩散焊机 208
(2)扩散焊接头的四种组合类型 208
(1)杠杆加压式真空高频感应扩散焊机 208
(1)扩散焊分类 208
1.2.1扩散焊分类及接头类型 208
1.2扩散焊 208
(2)液压电阻加热的卧式真空扩散焊机 209
1.2.3真空扩散焊焊接工艺流程 209
1.2.4扩散焊焊接工艺参数的选择 209
(1)扩散规律 209
(2)扩散焊焊接温度和熔化温度的关系 209
(3)接头强度与焊接温度的关系 210
(4)接头强度与压力的关系 210
(5)接头强度与保温时间的关系 210
1.2.5扩散焊焊接工艺 210
(1)扩散焊的焊接接头 210
(2)扩散焊的焊接工艺参数 210
(1)超声波焊接的基本类型 212
1.3.1超声波焊分类 212
1.3超声波焊 212
(2)超声波焊接振动能量的导入方式 213
1.3.2超声波焊接的材料范围 214
1.3.3超声波焊接的双金属种类 214
1.3.4超声波焊机的结构及类型 215
(1)超声波点焊机的典型结构 215
(2)超声波焊机的类型 215
(3)超声波点焊机功率与几种金属熔深的关系 215
1.3.5超声波焊焊接工艺参数的选择 216
(1)各种功率超声波焊机中静压力的范围 216
(2)静压力与功率的关系曲线 216
(3)静压力与焊点抗剪力的关系 216
(4)静压力的大小对形成最高接头强度所需时间的影响 217
(5)频率谐振条件与接头抗剪力的关系 217
(6)振幅与焊点抗剪力的关系 217
1.3.7超声波焊焊接接头的性能 218
(1)超声波点焊和电阻点焊的疲劳试验结果比较 218
(3)钛及钛合金超声波焊的焊接工艺参数及焊点强度 218
(2)室温下超声波点焊和电阻点焊的剪切试验比较 218
(7)焊接时间与焊点抗剪力的关系 218
(2)铜T2超声波焊的焊接工艺参数及焊点强度 218
(1)铝及铝合金超声波焊的焊接工艺参数及焊点强度 218
1.3.6各种金属超声波焊的焊接工艺参数 218
(3)几种金属超声波点焊焊点的平均抗剪力 219
(4)几种耐高温材料的焊点强度 219
1.3.8超声波焊在半导体器件生产中的应用 219
1.4摩擦焊 220
1.4.1摩擦焊类型 220
(1)摩擦焊分类 220
(2)两种常用摩擦焊机的基本形式 220
1.4.2金属摩擦焊的焊接性 220
(1)连续驱动摩擦焊的焊接性 221
(2)储能摩擦焊的焊接性 222
1.4.3摩擦焊焊接材料表面的温度 222
1.4.4摩擦焊焊机 223
(1)摩擦焊焊机的几种形式 223
(2)几种典型摩擦焊焊机的技术数据 223
1.4.5摩擦焊焊接工艺参数 224
(1)摩擦焊的接头形式 224
(2)典型材料的摩擦焊焊接工艺参数 224
(3)典型产品的摩擦焊焊接工艺参数 225
(4)铝铜摩擦焊的焊接工艺参数 225
(1)铝铜摩擦焊焊接接头的力学性能 226
1.4.6摩擦焊的焊接接头性能 226
(2)石油钻杆摩擦焊焊接接头热处理后的力学性能 226
(5)高速钢与45钢摩擦焊的焊接工艺参数 226
(6)石油钻杆(35 CrMo钢与40Mn2钢)摩擦焊的焊接工艺参数 226
1.4.7摩擦焊焊接的典型产品 227
1.5爆炸焊 227
1.5.1爆炸焊原理 227
1.5.2能进行爆炸焊的金属组合 229
1.5.3爆炸焊的装配方式 229
(1)平行放置爆炸焊 229
(2)倾斜放置爆炸焊 230
(3)管塞与管板的爆炸焊装置 230
1.5.7不锈钢管与锆合金管(覆管)爆炸焊的焊接工艺参数 231
(1)爆炸复合材料的验收标准 231
1.5.8爆炸焊的焊接接头性能 231
1.5.6几种爆炸材料中的声速 231
1.5.5几种爆炸焊炸药的性能 231
1.5.4几种金属过渡接头的爆炸焊 231
(2)爆炸复合材料的抗剪强度和结合强度 232
1.6冷压焊 232
1.6.1冷压焊类型 232
1.6.2冷压焊焊接工艺参数的选择 232
(1)焊接压力 232
(2)变形程度 233
1.6.3对接用尖形复合钳口 234
1.6.4搭接用冷压点焊形式 234
1.6.5压坑深度 234
1.6.6冷压焊应用实例 234
1.7旋弧焊 235
1.7.1旋弧焊形式 235
(3)焊接旋弧时间对接头性能的影响 236
(2)焊接电流 236
(5)顶锻压力对接头性能的影响 236
(4)对口间隙对接头性能的影响 236
1.7.3旋弧焊焊接工艺参数的选择 236
1.7.2旋弧焊机的典型结构 236
(1)旋弧速度 236
(6)旋弧焊的典型焊接工艺参数 237
1.7.4几种对焊方法焊接钢管的焊接工艺参数比较 237
1.8高频焊 238
1.8.1高频焊的两种形式 238
1.8.2电流透入深度与频率的关系 239
1.8.3不同高频电源功率时,管子焊接速度与壁厚的关系 239
1.8.4国内高频直缝焊管机组举例 239
1.8.5高频焊的其它应用 239
2高能焊 240
2.1等离于弧焊 240
2.1.1等离子弧焊的分类 240
(2)等离子弧的伏-安特性 241
2.1.2等离子弧 241
(1)等离子弧的形式 241
(3)等离子弧的温度与挺度 242
(4)等离子弧焰流速度 243
(5)三种形式等离子弧的能量分配 243
(6)双弧现象 243
2.1.3等离子弧焊喷嘴和应用气体的选择 245
(1)喷嘴种类 245
(2)典型喷嘴的结构参数 245
(3)等离子弧焊(大电流)焊接用保护气体的选择 246
(4)等离子弧焊(小电流)焊接用保护气体的选择 246
2.1.4小孔法等离子弧焊接 246
(1)等离子弧的穿透性 246
(2)焊接电流 247
(4)等离子气体流量和焊接速度的关系 248
(3)电弧电压 248
(5)材质对可焊接区域的影响 249
(6)可能焊接的最大背面焊缝宽度与板厚的关系 249
(7)焊接工艺参数的调节范围 249
(8)典型的焊接工艺参数 252
2.1.5微束等离子弧焊 252
(1)微束等离子弧焊(板厚小于0.8 mm)的接头设计和装配要求 252
(2)不锈钢薄板激束等离子弧焊的焊接工艺参数 253
(3)不锈钢薄板、细丝微束等离子弧焊的焊接工艺参数 253
2.2电子束焊 254
2.2.1电子束焊分类 254
2.2.2电子束焊机 254
(1)真空电子束焊机的组成 254
(2)电子束焊机的类型及特点 254
(1)板厚相差较小的对接接头 255
(2)板厚相差较大的对接接头 255
(4)ZD-7.5-1型电子束焊机的技术数据 255
2.2.3接头形式 255
(3)部分国产电子束焊机的型号及规格 255
(3)异种材料的对接接头 256
(4)圆柱体的对接接头 256
(5)几种特殊的对接接头 256
(6)塔接接头 256
(7)T形接头 257
2.2.4坡口装配精度 257
(1)坡口装配精度要求 257
(2)装配间隙对电子束焊缝强度的影响 258
2.2.5电子束焊接工艺参数的选择 258
(1)穿透深度与加速电压的关系 258
(2)工作距离、加速电压对功率密度的影响 258
(6)焦点位置对焊缝形状的影响 259
(5)焊接工艺参数与熔深和输入能量的关系 259
(3)焦点工作距离对焊缝熔深、熔宽的影响 259
(4)加速电压对焊缝熔深、熔宽的影响 259
(7)焦点位置对焊缝断面的影响 260
2.2.6几种金属电子束焊的焊接工艺参数 260
(1)难熔金属电子束焊的焊接工艺参数 260
(2)钛及钛合金电子束焊的焊接工艺参数 261
(3)铝及铝合金电子束焊的焊接工艺参数 261
(4)合金钢电子束焊的焊接工艺参数 261
(5)紫铜电子束焊的焊接工艺参数 261
2.2.7电子束焊的焊接缺陷及产生原因 262
2.2.8电子束焊的部分应用实例 262
2.3.2焊接用激光器 263
(1)接头形式 263
2.3.3脉冲微型激光焊 263
2.3.1激光焊分类 263
2.3激光焊 263
(2)金属丝激光焊的焊接工艺参数 264
(3)焊接实例 264
2.3.4连续激光焊 265
(1)接头形式 265
(2)工件边缘的处理方法 266
(3)允许的装配误差 266
(4)热导焊 266
(5)深熔焊 267
3电渣焊 270
3.1电渣焊的特点及应用 270
3.1.1电渣焊的焊接过程 270
(3)电渣焊和埋弧焊熔池结晶的对比 271
(1)熔渣温度与电导的关系 271
(2)渣池和金属熔池的温度分布 271
3.1.2电渣焊的类型 271
3.1.3电渣焊的热源及焊缝结晶 271
3.1.4电渣焊焊缝断面形状和接头形式 272
(1)电渣焊焊缝断面形状 272
(2)电渣焊的接头形式 272
3.1.5电渣焊焊接接头的力学性能与热处理的关系 272
3.1.6电渣焊的焊接材料 272
(1)焊丝的选用 272
(2)焊剂的选用 273
3.2丝极电渣焊 273
3.2.1丝极电渣焊的形式 273
3.2.2丝极电渣焊的焊接工艺参数 273
(1)焊缝成形系数与焊缝金属含碳量的关系 273
(4)焊接电流对母材熔深的影响 274
(5)焊丝末端与熔池间距离对母材熔深的影响 274
(3)焊接时应采用的渣池深度 274
(2)焊接电压、送丝速度与母材含碳量的推荐数值 274
(6)渣池深度对母材熔深的影响 275
(7)焊件厚度不同时,宜采用的焊丝根数 275
(8)不同δ/n时的送丝速度与金属熔池深度的关系 275
(9)金属熔池宽度与焊接电流、焊接电压、渣池深度及间隙宽度之间的关系 275
(10)渣池深度与vj/δ/n的关系 276
(11)多丝摆动时焊丝的位置 276
(12)焊缝宽度与焊丝摆动速度的关系 276
(13)焊接工艺参数对焊缝形状的影响 276
3.2.3丝极电渣焊焊接碳素钢和低合金钢的焊接工艺参数 277
3.2.4丝极电渣焊焊接前的准备 277
(1)工件装配要求 277
(2)水冷成形滑块(整体式) 277
3.3.3熔嘴电渣焊的焊接工艺参数 278
(2)熔嘴排列方式 278
(2)焊丝送给速度的计算公式 278
(1)焊接速度 278
(1)熔嘴构造 278
3.3.2熔嘴构造和排列方式 278
3.3.1熔嘴电渣焊示意图 278
3.3熔嘴电渣焊 278
(3)熔嘴电渣焊焊接工艺参数举例 279
3.3.4熔嘴电渣焊的焊接应用举例 279
3.3.5结构钢熔嘴电渣焊时焊缝金属的力学性能 280
3.3.6碳钢和合金钢熔嘴电渣焊时焊缝金属的力学性能 280
3.4管状焊条熔嘴电渣焊 280
3.4.1管状焊条熔嘴电渣焊示意图 280
3.4.2管状焊条 280
(1)管状焊条药皮成分 280
(2)焊接不同母材时,管状焊条药皮中铁合金的加入量 280
(3)管极电渣焊焊丝的熔化速度与焊接电流、电压的关系 281
(2)管极钢管截面积与其承受电流的范围 281
(1)管极电渣焊焊接电流与电压的选择 281
3.4.3管极电渣焊焊接工艺参数的选择 281
(4)管极电渣焊熔化深度与焊接电流、电压的关系 282
3.4.4 I形接头管极电渣焊对接焊的焊接工艺参数 282
3.4.5 T形接头管极电渣焊角接焊的焊接工艺参数 282
3.5板极电渣焊 284
3.5.1大断面板极电渣焊 284
3.5.2板极电渣焊的焊接工艺参数 284
3.5.3板极电渣焊的焊前准备 284
(1)利用引弧槽造渣 284
(2)板极绝缘装置 285
3.6 电渣焊焊缝中缺陷的形成原因及消除措施 285
4气焊 286
4.1可燃气体的种类和性质 286
4.1.1常用燃气的性能 286
4.1.4几种燃气燃烧时产生同等热量的气体耗量比较 287
4.1.3常用燃气与氧混合比不同时的燃烧速度 287
4.1.2主要混合燃气的化学和物理性能 287
4.1.5电石(CaC2)的分级和技术要求 288
4.1.6乙炔的反应式和发热量 288
4.1.7乙炔(未净化)中的杂质含量 288
4.1.8乙炔净化剂的成分(重量%)和用量 288
4.1.9乙炔爆炸分解的压力与温度之间的关系 288
4.1.10乙炔爆炸分解时临界压力与管子直径的关系 289
4.1.11乙炔在丙酮中的溶解度(g/kg溶剂) 289
4.1.12乙炔在二甲基甲酰胺[HCON(CH3)2]中的溶解度(g/kg溶剂) 289
4.2氧-燃气火焰的种类和应用 289
4.2.1氧-乙炔焰的燃烧反应 289
4.2.2氧-石油气火焰的燃烧反应 289
(1)氧-丙烷火焰 289
(2)氧-丙烯火焰 289
4.2.3各种氧-燃气火焰的回火区域 289
4.2.4氧-乙炔火焰的回火、稳定燃烧和脱火范围 290
4.2.5氧-乙炔火焰中燃烧产物的成分 291
4.2.6氧-丙烷火焰中燃烧产物的成分 291
4.2.7几种氧-燃气火焰的加工性能比较 291
4.2.8氧-乙炔中性焰的构成和温度分布 292
4.2气焊时火焰的选择 292
(1)氧-乙炔火焰的种类、焊接特性及应用举例 292
(2)气焊时氧-乙炔火焰的选用 292
(3)氧-丙烷火焰的焊接特性及应用 293
4.3气焊用器具 293
4.3.1中压乙炔发生器的型号和主要技术参数 293
4.3.2常用乙炔钢瓶的规格和技术数据 293
4.3.3溶解乙炔装瓶条件及最大充装量的规定 294
4.3.4乙炔瓶内剩余乙炔量的估算 294
4.3.5乙炔管路管径的确定 294
(2)气焊和焊补铸铁用焊丝 295
(1)气焊各种钢材用焊丝 295
4.3.6射吸式焊炬的主要技术数据 295
4.4气焊用焊丝和熔剂及其选用 295
4.4.1焊丝及其选用 295
(3)气焊Cr5Mo钢管用焊丝 296
(4)气焊电热丝用焊丝 296
(5)气焊铝及铝合金用焊丝及其选用 296
(6)气焊铜及铜合金用焊丝 298
4.4.2气焊用熔剂 298
(1)定型熔剂 298
(2)自配熔剂 299
4.5气焊工艺 299
4.5.1低碳钢管对接的气焊工艺参数 299
4.5.2低合金珠光体耐热钢管对接的气焊工艺参数 300
4.5.3奥氏体不锈钢的气焊工艺参数 300
4.5.4铸铁气焊焊补的工艺要点 300
4.5.7铝-钢的气焊工艺参数 301
4.5.8铜-铝的气焊工艺要点 301
4.5.5铝及铝合金的气焊工艺及操作要点 301
4.5.6铜及铜合金的气焊工艺要点 301
5钎焊 302
5.1钎焊方法的种类及其特性 302
5.1.1钎焊方法分类 302
5.1.2各种钎焊方法的特点及应用 302
5.1.3各种材料的钎焊性 303
5.2钎焊接头 305
5.2.1各种钎焊接头形式 305
5.2.2钎料的放置方法 306
5.2.3钎焊接头的定位方法 306
(1)硬钎料 307
5.3.2常用钎料的成分、性能及用途 307
5.3.1钎料牌号的表示方法 307
5.2.4各种金属钎焊接头的合适间隙 307
5.3钎料 307
(2)软钎料 312
5.3.3钎料的选用原则及供应状态 316
5.3.4根据母材的种类选择钎料 316
5.4钎剂(熔剂) 317
5.4.1钎剂牌号的编制方法 317
5.4.2软钎料用钎剂 317
5.4.3硬钎料用钎剂 319
5.4.4铝、银钎焊用钎剂 319
(1)铝钎焊用钎剂 319
(2)银钎焊用钎剂 320
5.4.5根据母材及钎料选择钎剂 320
(1)钎焊前工件表面的准备 321
(2)钎焊用还原性气氛的组成及用途 321
5.5.1炉中钎焊 321
5.5钎焊工艺方法 321
(3)炉中钎焊各种发热体在不同气氛中的最高使用温度 322
(4)各种材料真空钎焊时的真空度与润湿性的关系 322
5.5.2感应钎焊 322
(1)感应钎焊不同材料的加热厚度与电流频率的关系 322
(2)感应圈的形式 323
5.5.3电接触钎焊 323
(1)电接触钎焊机的型号与技术数据 323
(2)电接触钎焊用电极材料的性能 324
(3)电接触钎焊的电极组合 324
(4)电接触钎焊的电极及钎料的放置 324
5.5.4浸沾钎焊 324
(1)钎焊接头浸蚀液的成分 324
(4)钢、铜、镍及其合金钎焊的盐浴成分 325
(2)盐浴电阻炉的型号与技术数据 325
(3)铝及铝合金钎焊的盐浴成分 325
5.5.5各种钎焊工艺方法优缺点的比较 326
5.6各种金属钎焊接头的强度 326
5.6.1低碳钢用软钎料钎焊的接头强度 326
5.6.2低碳钢与40Cr钢用硬钎料钎焊的接头强度 326
5.6.3 1Cr18Ni9Ti用软钎料钎焊的接头强度 326
5.6.4银钎料钎焊1Cr18Ni9Ti的接头强度 327
5.6.5铜基钎料钎焊硬质合金的接头强度 327
5.6.6软钎料钎焊铜及黄铜的接头强度 327
5.6.7硬钎料钎焊铜及黄铜的接头强度 328
5.6.8铝及铝合金钎焊的接头强度 328
5.6.9银基钎料钎焊钛合金的接头强度 328
5.7钎焊接头的质量检验 329
5.7.1钎焊接头的缺陷及其产生原因 329
5.6.11钎焊1Cr13不锈钢的接头强度 329
5.6.10银基钎料钎焊钛及钛与钢的接头强度 329
5.7.2钎焊接头缺陷的检验方法及特点 330
5.8国外钎料规格 330
5.8.1美国焊接学会钎料规格 330
5.8.2原苏联国家标准规定的钎料规格 332
(1)硬钎料 332
(2)软钎料 332
5.8.3 日本工业规定的钎料规格 333
(1)硬钎料 333
(2)软钎料 335
5.8.4德国国家标准规定的钎料规格 336
(1)硬钎料 336
(1)硬钎料 337
5.8.5英国国家标准规定的钎料规格 337
(2)软钎料 337
(2)软钎料 339
考文献 340
五章热切割工艺和设备 342
1热切割方法的种类及其特性 342
1.1热切割方法的类型、定义及其适用范围 342
1.2主要热切割方法的能量密度 342
1.3主要热切割方法的切割性能综合比较 343
1.4主要热切割方法的实用切割速度比较 343
2气割 344
2.1金属的气割性 344
2.1.1各种金属的熔点、氧化物的熔点和金属的气割性 344
2.1.2各种元素对钢材气割性的影响 344
2.1.5钢材气割面的温度分布 345
2.1.6气割厚25mm碳钢时的热平衡 345
2.1.4铁-氧燃烧反应时的单位放热量 345
2.1.3各种金属燃烧时生成的氧化物及其放热量 345
2.2切割速度 346
2.2.1各种厚度的热态钢材在不同温度下的切割速度 346
2.2.2氧气纯度对钢材切割速度的影响 346
2.2.3氧气中的杂质气体对切割速度的影响 346
2.2.4氧气中水蒸气含量(露点)对切割速度的影响 346
2.2.5车间底漆类型和膜厚对钢材切割速度的影响 347
2.2.6氧气纯度对气割时间和氧气消耗量的影响 347
2.2.7钢材的温度和含碳量对热态时的实用切割速度和切断速度的影响 348
2.3气割(气焊)用气体及其器具 348
2.3.1工业用氧纯度 348
2.3.2常用氧气瓶的尺寸和装气量 348
(1)移动式液氧容器的规格和主要技术参数 349
2.3 5液氧贮罐的规格和主要技术参数 349
(2)固定式液氧贮槽的规格和主要技术参数 349
23.4液态氧的优点和供应方式 349
2.3.3气瓶内剩余氧气量的估算 349
2.3.6液态氧和气态氧的换算 350
2.3.7气瓶用减压器的主要技术数据 350
2.3.8减压器常见故障及防止措施 350
2.4气割工具和设备 351
2.4.1常用及新型割嘴的类型和用途 351
2.4.2快速割嘴(扩散形)切割氧孔道设计资料 351
(1)切割氧孔道(即拉伐尔喷管)设计的基本公式 351
(2)不同进口压力时的dl/dc值和M值 352
(3)切割氧流量计算式(标准状态下) 352
2.4.3快速割嘴与普通割嘴的切割性能比较 352
2.4.4大厚度切割用F411-600~1500外混式割嘴的结构参数 352
(2)等压式割炬 353
(1)射吸式割炬 353
2.4.5手工割炬的型号及主要技术参数 353
2.4.6氧-丙烷割炬的主要技术性能 354
2.4.7常用切割机的类型、工作原理和用途 354
2.5气割工艺 354
2.5.1氧-乙炔预热焰乙块流量与切割钢材厚度的关系 354
2.5.2单位切割长度耗氧量与切割钢材厚度的关系 355
2.5.3普通等压式割嘴机械切割低碳钢的工艺参数 355
2.5.4快速割嘴(扩散形)机械切割低碳钢的工艺参数 355
2.5.5氧气屏割嘴机械切割低碳钢的工艺参数 356
2.5.6大厚度碳钢和低合金钢的气割工艺参数 356
(1)国内常用手工切割工艺参数 356
(2)低压大流量氧手工切割工艺参数 356
(3)外混式割嘴机械切割钢材的工艺参数 357
2.5.7成叠(多层)钢板氧-乙炔气割的工艺参数 357
2.5.8薄钢板机械切割的工艺与参数 357
(1)双Y形坡口切割时割嘴的配置和工艺参数 358
2.5.9焊接坡口多割炬一次切割的工艺与参数 358
(2)Y形和倒Y(?)形坡口切割时割嘴的配置 359
2.5.10 U形坡口气割的工艺和参数 359
2.5.11火焰气刨的工艺参数 361
2.5.12高碳钢和合金钢气割时的预热和割后热处理条件 361
2.5.13常见切割面缺陷及其产生原因 361
2.6切割面的质量和特性 362
2.6.1切割面质量的评定和分等 362
(1)ZBJ 59002.3—88切割面质量的分等 362
(2)CB 3136—83切割面粗糙度和缺口的规定 363
2.6.2气割零件尺寸偏差标准 364
(1)ZBJ 59002.3-88工件尺寸偏差允许值(mm) 364
(2)CB 3136—83船体零件气割尺寸公差 364
2.6.3钢材气割的热影响区宽度 364
(1)普通割嘴气割的热影响区宽度 364
2.6.4钢材气割时切割面和热影响区的增碳和合金元素的变化 365
(2)快速割嘴气割的热影响区宽度 365
2.6.5钢材切割面附近的硬度 366
(1)不同含碳量的碳钢其切割面附近的硬度 366
(2)SM50钢(类似于我国16Mn钢)切割面附近的硬度 366
(3)中碳钢和某些合金钢切割面(氧-丙烷气割)的硬度 367
2.6.6气割对钢材力学性能的影响 367
(1)气割对钢材冷弯性能的影响 367
(2)各种切割面的冲击弯曲试验结果 368
(3)自动切割面的疲劳试验结果 368
2.7特殊气割和熔割法 369
2.7.1氧-熔剂气割法 369
(1)熔剂 369
(2)不锈钢的切割工艺参数 369
(3)铸铁的切割工艺参数 369
(1)穿孔孔径与氧矛(钢管)直径 370
2.7.2氧矛穿孔 370
(5)混凝土板氧-熔剂(铁粉)切割工艺参数 370
(4)有色金属及合金的切割工艺参数 370
(2)混凝土和岩石的穿孔工艺参数 371
2.7.3混凝土板氧-丙烷火焰熔割开孔的工艺参数 371
3电弧切割 371
3.1碳弧气刨 371
3.1.1碳弧气刨用碳棒的型号和规格 371
3.1.2碳弧气刨的工艺参数 372
(1)碳弧气刨时极性的选择 372
(2)钢板碳弧气刨的工艺参数 372
(3)矩形碳棒的电流值 372
(4)18-8型不锈钢板喷水碳弧气刨工艺参数 372
3.1.3碳弧气刨对钢的组织和性能的影响 372
(1)碳弧气刨的热影响区宽度及对组织和硬度的影响 372
3.1.4碳弧气刨对18-8型不锈钢焊接接头耐晶间腐蚀性能的影响 373
(3)碳弧气刨对焊接接头力学性能的影响 373
(2)刨槽表面层的增碳 373
3.2水下切割 374
3.2.1氧弧切割的原理和适用范围 374
3.2.2氧弧水下割条和切割工艺参数 374
3.3熔化极电弧切割 374
3.3.1 MIG电弧切割工艺 374
3.3.2喷水式熔化极电弧切割工艺 374
(1)水下切割工艺参数 375
(2)喷水式熔化极电弧切割18-8型不锈钢的工艺参数 375
3.3.3熔化极空气电弧刨槽工艺 376
4等离子弧切割与工艺 376
4.1等离子弧切割的基本原理 376
4.1.1等离子弧的类型及其主要应用 376
4.1.2氩等离子弧和氮等离子弧的最高温度与平均温度 376
4.1.5等离子弧切割的种类及其主要用途 377
4.1.3等离子弧的流速 377
4.1.4等离子弧切割原理及典型的热分布与热消耗 377
4.2等离子弧切割用的气体和电极材料 378
4.2.1等离子弧切割用气体的纯度要求 378
4.2.2氩、氮、氢和空气的重量和体积对照表 378
4.2.3电极材料及适用气体 378
4.2.4电极金属及其氧化物的熔点 379
4.3等离子弧切割工艺 379
4.3.1各种等离子弧的切割特性比较 379
4.3.2氩-氢和氮等离子弧切割工艺 380
(1)切割不锈钢和铝时工作气体的选用 380
(2)喷嘴孔径同切割厚度和切割电流的关系 380
(3)产生串列电弧(双弧)的临界电流 380
(4)喷嘴至工件的距离(喷嘴高度)对切割速度v、电弧电压U和割缝宽度B的关系 380
(5)电极内缩量(钨极尖端至喷嘴内端面的距离) 380
4.3.3空气等离子弧切割工艺 381
(1)LG 8-25型小电流空气等离子弧切割的工艺参数 381
(6)不锈钢的切割工艺参数 381
(8)铜的切割工艺参数 381
(7)铝的切割工艺参数 381
(2)大电流空气等离子弧切割的工艺参数 382
4.3.4氧等离子弧切割的工艺参数 382
(1)小电流氧等离子弧切割的工艺参数 382
(2)大电流(150A)氧等离子弧切割的工艺参数 383
(3)V形坡口的氧等离子弧切割 383
4.3.5水再压缩等离子弧切割的工艺参数 384
(1)水再压缩等离子弧切割有色金属的工艺参数 384
(2)水再压缩等离子弧切割碳钢的工艺参数 384
(3)大电流氧等离子弧切割时铪电极的使用寿命 385
(1)普通等离子弧切割时钨极的引弧次数与电极消耗量的关系 385
(2)小电流空气等离子弧切割时的电极消耗深度 385
4.3.6水下等离子弧切割的工艺参数 385
4.3.7电极和喷嘴的使用寿命 385
(4)喷嘴的使用寿命 386
4.4等离子弧切割面的质量评定和特性 386
4.4.1 ZBJ 59002.4—88等离子弧切割面质量评定标准 386
(1)平面度u的分级取值范围(mm) 386
(2)割纹深度h分级取值范围(μm) 386
4.4.2实际切割面的割纹深度 386
4.4.3切割面的切口角和切口宽度 387
4.4.4等离子弧切割的热影响区深度 387
4.4.5等离子弧切割面的硬度 387
4.4.6空气及空气加碳化氢混合气体等离子弧切割不锈钢边缘的耐蚀性比较 389
4.4.7等离子弧切割18-8型不锈钢手弧焊焊接接头的力学性能和抗晶间腐蚀性能 389
5激光切割 389
5.1激光切割的原理 389
5.3辅助气体的种类对激光切割不锈钢能力和速度的影响 390
5.2各种材料的激光(CO2激光器)切割性 390
5.4氧气压力和纯度对切割速度的影响 391
5.5切割用激光器的种类和主要技术参数 391
5.6 CO2激光切割碳钢时切割厚度和极限切割速度同输出功率的关系 392
5.7激光切割不同材料时的切割条件 392
参考文献 392
第六章各种材料的焊接 394
1 概述 394
1.1各种金属材料焊接难易程度一览表 394
1.2各种金属材料的焊接性 395
1.3焊接裂纹的类型 397
1.3.1裂纹的分类 397
1.3.2各种金属材料及其可能发生焊接裂纹的类型 397
(3)含碳量引起Ms点下降和马氏体形状变化 398
(4)含碳量与脆性转变曲线的关系 398
(2)含碳量与物理性能的关系 398
(5)含碳量与所形成马氏体量对碳钢硬度的影响 398
2.1一般性能 398
(1)含碳量与静力学性能的关系 398
2.1.2含碳量对钢性能的影响 398
2.1.1碳素钢按含碳量分类 398
2碳素结构钢的焊接 398
2.1.3碳素结构钢的化学成分和力学性能(GB 700—88) 399
(1)钢的牌号及其表示方法 399
(2)新旧GB 700标准牌号对照 400
(3)化学成分 400
(4)力学性能 401
2.1.4优质碳素结构钢热轧厚钢板和宽钢带的化学成分和力学性能(GB 711—88) 402
(1)化学成分 402
(2)力学性能 403
(2)化学成分 404
(1)分类和代号 404
2.1.5船体用结构钢的化学成分和力学性能(GB 712—88) 404
(3)交货状态 405
(4)力学性能 405
(5)检验项目和试验方法 406
2.1.6锅炉用碳素钢和低合金钢板的化学成分和力学性能 406
(GB 713—86) 406
(1)化学成分 406
(2)力学性能 407
(3)检验项目和试验方法 408
2.1.7锅炉用碳素钢及低合金钢厚钢板的化学成分和力学性能[YB(T)41—87] 408
(1)化学成分 408
(2)力学性能 408
(3)高温性能 409
(2)力学性能 410
(1)化学成分 410
(4)检验项目和试验方法 410
2.1.8压力容器用碳素钢和低合金钢厚钢板的化学成分和力学性能(GB6654—86) 410
(3)检验项目和试验方法 411
2.1.9多层压力容器低合金钢钢板的化学成分和力学性能(GB6655—86) 411
(1)化学成分 411
(2)力学性能 411
(3)检验项目和试验方法 411
2.1.10压力容器用碳素钢和低合金钢厚钢板的化学成分和力学性能[YB(T)40—87] 412
(1)化学成分 412
(2)力学性能 412
(3)高温性能 413
(4)检验项目和试验方法 413
(1)化学成分 414
(2)力学性能 414
2.1.11焊接气瓶用钢板的化学成分和力学性能(GB 6479—86) 414
(3)检验项目和试验方法 415
2.1.12碳素结构钢的焊接性能 415
(1)碳当量和硬度、焊道下裂纹敏感性和带缺口焊缝金属弯曲角度的关系 415
(2)手工电弧焊时,母材含碳量和厚度对预热和层间温度的影响 416
(3)焊缝区最高硬度与预热层间温度的关系 416
(4)母材厚度和含碳量对碳钢焊后消除应力热处理必要性的影响 416
2.2低碳钢的焊接工艺 416
2.2.1低碳钢焊接材料的选用 417
2.2.2低碳钢在低温下焊接的预热温度 417
2.2.3焊条和焊剂的烘干 417
(1)低氢型焊条扩散氢含量的规定值(GB 3965—83) 417
(2)焊条烘干温度对焊缝含氢量Ho的影响 418
(3)焊条烘干条件和烘干后放置时间t对药皮吸潮性的影响 418
(4)焊接材料的吸湿临界值和标准烘干规范 418
2.2.4低碳钢、低合金钢手工电弧焊的焊接工艺参数 419
2.3.1中、高碳钢焊接及补焊用焊条 422
2.3.2中碳钢焊接时,预热和消除应力热处理温度 422
3低合金高强度钢的焊接 422
3.1一般性能 422
3.1.1低、中合金结构钢的类型 422
2.3中、高碳钢的焊接工艺 422
3.1.2几种热轧和正火钢的化学成分和力学性能 423
3.1.3几种低碳调质钢的化学成分 424
3.1.4几种低碳调质钢的热处理工艺参数及组织 424
3.15几种低碳调质钢的力学性能 424
3.1.6几种中碳调质钢的化学成分 425
3.1.7几种中碳调质钢的力学性能 426
3.1.8淬火回火钢热影响区硬度的分布 426
3.2.3各种合金元素对钢的淬透性的影响 427
3.2.4一些低合金结构钢的碳当量Ceq值 427
3.2低合金高强度钢的焊接性能 427
3.2.2 16Mn钢及低碳钢的连续冷却曲线 427
3.2.1低合金高强度钢的焊接特点 427
3.2.5几种日本焊接结构用高强度钢的热影响区最高硬度允许值 428
3.2.6碳当量与热影响区最高硬度的关系 428
3.2.7焊缝中C、Mn、S含量对角焊缝热裂纹的影响 428
3.2.8热影响区液化裂纹与C、Mn/S之间的关系 429
3.2.9焊接线能量E对15 MnVN和15 MnTi钢过热区-40℃冲击韧度的影响 429
3.3热轧和正火高强度钢的焊接工艺 430
3.3.1热轧和正火高强度钢常用的焊接材料 430
3.3.2热轧和正火高强度钢的焊前预热和焊后热处理工艺参数 430
(1)几种热轧及正火钢的预热和焊后热处理工艺参数 430
3.4.1低碳调质钢的焊接特点 431
3.4低碳调质钢的焊接工艺 431
3.4.2几种低碳调质钢焊接材料的选择 431
(2)按焊接裂纹敏感性指数Pw确定焊前预热温度To 431
3.3.3不同环境温度下焊接16 Mn钢的预热温度 431
3.43几种低碳调质钢的最低预热温度与层间温度 432
3.4.4 T-1钢对接焊的最大线能量 432
3.4.5 HY-80和HY100钢焊接的最大线能量 433
3.4.6 HY-130钢焊接的最大线能量 433
35中碳调质钢的焊接工艺 433
3.5.1中碳调质钢的焊接特点 433
3.5.2中碳调质钢焊接材料选用实例 433
4珠光体耐热钢的焊接 434
4.1一般性能 434
4.1.1几种低、中合金耐热钢的化学成分 434
4.1.2几种低、中合金耐热钢的力学性能 435
4.1.3不同工业部门中各种金属材料的使用温度范围 435
4.2.2常用珠光体耐热钢焊条的选择 436
4.2.3常用珠光体耐热钢焊丝和焊剂的选择 436
4.2.1珠光体耐热钢的焊接特点 436
4.2珠光体耐热钢的焊接工艺 436
4.2.4常用珠光体耐热钢焊接的预热温度和焊后热处理温度 437
5低温钢的焊接 437
5.1一般性能 437
5.1.1低温钢类型及其使用温度范围 437
5.1.2几种低温钢的主要化学成分 438
5.1.3对低温钢的力学性能要求 438
5.1.4低温压力容器用低合金钢厚板的化学成分和力学性能(GB 3531—83) 438
(1)化学成分 438
(2)力学性能 439
(3)检验项目和试验方法 439
(4)超声波探伤检查数量 439
5.2.2低温钢的焊接工艺参数 440
5.2.1低温钢的焊接材料 440
5.2低温钢的焊接工艺 440
5.1.5低温钢的焊接特点 440
6不锈钢及耐热钢的焊接 441
6.1一般性能 441
6.1.1不锈钢的分类系统 441
(1)我国不锈钢的分类系统 441
(2)美国不锈钢的分类系统 442
6.1.2各类不锈钢在退火状态下的典型物理性能 443
6.1.3冷轧不锈钢板(GB3280—84) 443
(1)类别与牌号 443
(2)化学成分 444
(3)力学性能 447
(4)
- 《SQL与关系数据库理论》(美)戴特(C.J.Date) 2019
- 《Maya 2018完全实战技术手册》来阳编著 2019
- 《数据库技术与应用 Access 2010 微课版 第2版》刘卫国主编 2020
- 《大数据Hadoop 3.X分布式处理实战》吴章勇,杨强 2020
- 《Power BI数据清洗与可视化交互式分析》陈剑 2020
- 《高等教育双机械基础课程系列教材 高等学校教材 机械设计课程设计手册 第5版》吴宗泽,罗圣国,高志,李威 2018
- 《慢性呼吸系统疾病物理治疗工作手册》(荷)瑞克·考斯林克(RikGosselink) 2020
- 《数据失控》(美)约翰·切尼-利波尔德(John Cheney-Lippold)著 2019
- 《战略情报 情报人员、管理者和用户手册》(澳)唐·麦克道尔(Don McDowell)著 2019
- 《中国生态系统定位观测与研究数据集 森林生态系统卷 云南西双版纳》邓晓保·唐建维 2010
- 《指向核心素养 北京十一学校名师教学设计 英语 七年级 上 配人教版》周志英总主编 2019
- 《北京生态环境保护》《北京环境保护丛书》编委会编著 2018
- 《高等教育双机械基础课程系列教材 高等学校教材 机械设计课程设计手册 第5版》吴宗泽,罗圣国,高志,李威 2018
- 《指向核心素养 北京十一学校名师教学设计 英语 九年级 上 配人教版》周志英总主编 2019
- 《高等院校旅游专业系列教材 旅游企业岗位培训系列教材 新编北京导游英语》杨昆,鄢莉,谭明华 2019
- 《中国十大出版家》王震,贺越明著 1991
- 《近代民营出版机构的英语函授教育 以“商务、中华、开明”函授学校为个案 1915年-1946年版》丁伟 2017
- 《新工业时代 世界级工业家张毓强和他的“新石头记”》秦朔 2019
- 《智能制造高技能人才培养规划丛书 ABB工业机器人虚拟仿真教程》(中国)工控帮教研组 2019
- 《AutoCAD机械设计实例精解 2019中文版》北京兆迪科技有限公司编著 2019