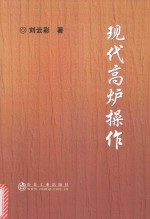
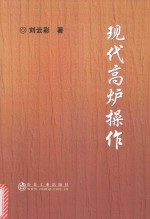
现代高炉操作PDF电子书下载
- 电子书积分:13 积分如何计算积分?
- 作 者:刘云彩著
- 出 版 社:北京:冶金工业出版社
- 出版年份:2016
- ISBN:9787502472337
- 页数:358 页
绪论——炼铁的过去和现在 1
0.1 炼铁的起源和发展 1
0.1.1 块炼铁——古老的炼铁方法 2
0.1.2 高炉的发明——炼铁生产的第一次革命 5
0.1.3 高炉起源于炼铜炉 5
0.2 高炉冶炼的发展 6
0.2.1 战国到西汉,高炉容积扩大期 6
0.2.2 强大的生产组织和质量管理 7
0.2.3 鼓风设备和椭圆高炉的发明 9
0.2.4 熔剂的使用 11
0.2.5 我国公元以前年代铁的化学成分 12
0.2.6 东汉到明朝——新技术创造期 14
0.3 我国古代炼铁和欧洲炼铁比较 18
0.3.1 我国高炉炼铁的重要创造 19
0.3.2 欧洲高炉发展 19
0.3.3 欧洲炼铁水平后来居上 21
0.3.4 高炉生产水平的变迁 22
0.3.5 高炉最早出现在中国的原因 24
0.4 直接还原——块炼铁的“复活” 24
0.4.1 直接还原铁生产的主要国家 24
0.4.2 直接还原铁生产的主要方法 25
0.4.3 转底炉法 27
0.5 熔融还原——炼铁二次革命 28
0.5.1 Corex法 28
0.5.2 Finex法 29
0.5.3 HIsmelt法 30
0.6 结语 31
参考文献 31
1 高炉生产概论 35
1.1 炼铁在钢铁企业中的地位 35
1.2 决定高炉生产水平的条件 35
1.3 高炉操作的任务 37
1.3.1 高炉顺行、稳定 37
1.3.2 合理使用炉料 38
1.4 高炉顺行、稳定的前提 38
参考文献 41
2 活跃炉缸 42
2.1 焦炭燃烧区与鼓风动能 43
2.1.1 焦炭燃烧区 43
2.1.2 鼓风动能与回旋区 45
2.1.3 鼓风动能与风速 47
2.2 下部调剂 47
2.2.1 风量水平 48
2.2.2 风速或鼓风动能的确定 49
2.2.3 风速、鼓风动能和冶炼强度的关系 50
2.2.4 回旋区长(深)度 51
2.2.5 回旋区的作用 54
2.2.6 风口长度 55
2.2.7 风口角度 56
2.2.8 堵风口操作 57
2.2.9 理论燃烧温度 57
2.3 合适风速(鼓风动能)的经验判断与调剂 58
2.4 风口烧损和预防 58
2.4.1 风口烧熔的原因 60
2.4.2 风口破损的处理 61
2.5 炉缸堆积和预防 62
2.5.1 炉缸堆积的征兆 62
2.5.2 炉缸堆积的主要原因 64
2.5.3 炉缸堆积的处理原则和方法 70
2.5.4 预防炉况失常的措施 76
参考文献 77
3 料柱结构与控制煤气分布 79
3.1 高炉料柱结构 80
3.1.1 炉料特征 80
3.1.2 高炉布料的作用 81
3.2 炉料分布和煤气分布 82
3.2.1 炉料分布和软熔带 82
3.2.2 软熔带高度 84
3.3 观察与判断煤气流分布 86
3.3.1 径向煤气流速和煤气温度 86
3.3.2 直接观察 88
3.3.3 仪表综合判断 89
3.3.4 由非正常炉况判断煤气分布 91
3.4 适应高炉冶炼条件的煤气分布 91
3.4.1 选择适应冶炼条件的煤气分布 91
3.4.2 确定相应的炉料分布 92
3.4.3 料线和批重 92
3.4.4 利用装料制度改善顺行 94
3.4.5 提高煤气利用率——由Ⅱ型煤气分布变Ⅲ型 95
3.5 炉料分布计算 99
3.5.1 布料落点计算公式 99
3.5.2 布料落点计算程序使用说明 100
3.6 边缘气流与中心气流调控 104
3.6.1 边缘煤气分布的危害 104
3.6.2 中心煤气流控制 105
3.6.3 取消中心加焦 107
3.7 渣皮脱落 108
3.7.1 渣皮脱落的特征 108
3.7.2 渣皮脱落与边缘管道 111
3.7.3 铜冷却壁与渣皮脱落 112
3.7.4 渣皮脱落的危害 112
3.8 上下部调剂相适应 113
参考文献 115
4 稳定炉温 117
4.1 铁水特性 117
4.1.1 铁水的熔点 117
4.1.2 温度对碳溶解度的影响 118
4.1.3 不同元素对碳溶解度的影响 118
4.1.4 现代高炉铁中含碳量 119
4.1.5 铁水中的微量元素 120
4.2 铁水在炉缸的状态 121
4.2.1 实测炉缸铁水状态 121
4.2.2 铁水成分波动 121
4.2.3 铁水成分波动幅度的确定 123
4.3 控制炉温 123
4.3.1 判断炉温的指标 123
4.3.2 炉温判断 124
4.3.3 影响炉温的主要参数 125
4.3.4 各参数的作用时间 127
4.3.5 炉温控制的方法 128
4.3.6 料速变化 129
4.4 喷煤操作 129
4.4.1 我国的喷煤 129
4.4.2 煤粉的作用 132
4.4.3 煤粉燃烧 133
4.4.4 喷煤对冶炼周期的影响 134
4.4.5 用煤粉调剂炉温 134
4.5 低硅铁冶炼 136
4.5.1 低硅铁生产 136
4.5.2 我国的实践 139
4.6 炉缸冻结及处理 139
4.6.1 炉缸冻结的原因及类型 140
4.6.2 称量错误导致的炉缸冻结 141
4.6.3 炉缸冻结的处理方法 145
4.6.4 净焦量 146
4.7 改铁操作 146
4.7.1 炼钢铁改铸造铁 146
4.7.2 铸造铁改炼钢铁 148
4.7.3 改铁总结 149
4.8 调剂炉温的专家系统 149
4.8.1 高炉过程自动控制的开发研究 149
4.8.2 高炉专家系统 152
参考文献 153
5 控制炉渣成分 155
5.1 铁水质量控制 156
5.1.1 铁中硫的危害 156
5.1.2 硫的分布及计算公式 156
5.1.3 炉渣碱度 160
5.1.4 硫分配系数的比较 161
5.2 稳定的炉渣和黏度 164
5.2.1 稳定的炉渣 164
5.2.2 MgO对炉渣黏度的影响 165
5.2.3 McCaffery黏度图分析 166
5.2.4 炉渣中Al2O3和MgO比例的确定 168
5.3 特殊功能炉渣 169
5.3.1 清理结瘤 170
5.3.2 利用炉渣排出碱金属 171
5.3.3 利用炉渣处理贫矿 174
参考文献 177
6 出铁出渣 179
6.1 高炉上推力 180
6.1.1 上推力的作用 180
6.1.2 保持高炉上推力稳定 180
6.2 出铁 181
6.2.1 铁水在炉缸的运动 181
6.2.2 出铁速度 182
6.2.3 铁水黏度 183
6.2.4 连续出铁 184
6.3 出渣 185
6.3.1 炉渣在炉芯带内的流动 185
6.3.2 不放上渣 185
6.3.3 稳定上推力 186
6.4 出铁过程排出的气体 188
6.5 深刻的教训 189
参考文献 190
7 高炉基本操作 191
7.1 炉料下降运动 192
7.2 直接观察和操作曲线识别 194
7.2.1 高炉工长的贡献和作用 195
7.2.2 合理追求,务实操作 195
7.2.3 把握时机,当机立断 198
7.3 管道 199
7.3.1 形成管道的原因 199
7.3.2 管道的处理 200
7.3.3 罕见的真实管道 200
7.3.4 管道的类别和特征 200
7.3.5 管道与偏尺 203
7.4 塌料与悬料 205
7.4.1 管道与塌料 205
7.4.2 悬料机理 207
7.4.3 料尺分类 209
7.4.4 悬料的处理与教训 210
7.4.5 难行状态下的加风 217
7.4.6 难行亏尺或坐料后亏尺的加料 218
7.5 操作教训 219
7.5.1 控制放风 219
7.5.2 坐料后的放风 219
7.5.3 低炉温时的坐料 219
7.6 高炉顺行指数 220
7.6.1 顺行的炉况 220
7.6.2 利用顺行指数比较本厂高炉的顺行水平 222
7.7 异常炉况的专家系统 223
参考文献 224
8 高炉烧穿的预防和处理 226
8.1 炉缸烧穿是一个过程 226
8.1.1 炉缸在哪里经常烧穿? 226
8.1.2 “突然”烧穿的原因 229
8.1.3 减少象脚型侵蚀 229
8.1.4 出铁速度 232
8.1.5 重点检测哪里? 232
8.2 炉缸烧穿及处理 233
8.2.1 炉缸烧穿前的征兆 233
8.2.2 侵蚀速度 234
8.2.3 减小烧穿损失 237
8.2.4 烧穿后的修复 238
8.3 炉底烧穿 240
8.3.1 事故经过 240
8.3.2 合理的炉底结构 242
8.3.3 铅渗透和炉底冷却装置的破坏 243
8.3.4 炉底冷却装置的检查 245
8.4 陶瓷杯结构 245
8.4.1 陶瓷杯的实践 246
8.4.2 我国专家对陶瓷杯结构的争议 249
8.4.3 陶瓷杯炉底炉缸结构的优势 251
8.5 补炉操作 252
8.5.1 对预防烧穿操作方法的评价 252
8.5.2 用含钛炉料补炉的历史 253
8.5.3 钛回收率 255
8.5.4 钛化物在炉缸的形成与沉积 256
8.5.5 为什么补炉后依然烧穿? 260
8.5.6 含钛炉料补炉效果 264
8.5.7 补炉操作的优点和缺点 264
8.6 炉体膨胀和炉皮开裂 265
8.6.1 炉皮开裂 265
8.6.2 开裂原因 266
8.6.3 避免开裂的措施 267
8.6.4 膨胀导致的炉皮开裂 267
8.7 灌浆、压入和喷涂造衬 267
8.7.1 灌浆 268
8.7.2 热面灌浆 268
8.7.3 硬质料压入造衬 269
8.7.4 喷涂造衬 269
8.8 预防炉体破损 271
8.8.1 高炉结构决定高炉寿命 271
8.8.2 炉衬材质 271
8.8.3 冷却系统 272
8.8.4 施工质量 272
8.8.5 控制有害元素入炉量 273
8.8.6 补炉操作 273
8.8.7 争取时间的临时措施 273
8.8.8 合理烘炉 274
8.8.9 完善、严格检测制度 274
参考文献 274
9 高炉结瘤 277
9.1 结瘤的征兆 278
9.1.1 结瘤部位的隔热 278
9.1.2 结瘤改变炉料分布 280
9.1.3 结瘤对炉缸的影响 283
9.1.4 结瘤后的操作特点 283
9.1.5 结瘤特征 284
9.2 炉瘤的组织结构和形成过程 285
9.2.1 炉瘤的组织结构 285
9.2.2 炉瘤的物理特性 286
9.2.3 炉瘤中粘结相的作用 286
9.2.4 炉瘤的形成 287
9.3 炉瘤位置的判断 288
9.3.1 探孔法 288
9.3.2 传热计算法 289
9.3.3 降料面观察法 289
9.4 结瘤的处理 289
9.4.1 高炉炉瘤是运动的,能增长,也能脱落 290
9.4.2 洗炉 291
9.4.3 降料面法处理炉墙结瘤 295
9.4.4 爆破除瘤 297
9.5 预防结瘤 301
参考文献 305
10 开炉操作 307
10.1 开炉前的准备工作 307
10.1.1 人员配备与培训 307
10.1.2 设备试车与验收 307
10.1.3 炉料和备品、备件准备 307
10.1.4 上下工序的状况调研 308
10.2 烘炉 308
10.2.1 热风炉烘炉 308
10.2.2 高炉本体烘炉准备 309
10.2.3 烘炉温度控制 311
10.2.4 烘炉结束与凉炉 312
10.2.5 严格操作,杜绝事故 313
10.3 开炉的冶炼指标和配料计算 313
10.3.1 开炉总焦比和开炉料的选择 313
10.3.2 计算方法 314
10.4 全焦开炉 315
10.5 含铁炉料的位置 317
10.6 装炉及测料面 318
10.6.1 装料前的工作 318
10.6.2 按计划安排次序加料 318
10.6.3 合理布料,应从开炉填料时开始 318
10.6.4 测量料面 320
10.7 点火与送风 320
10.7.1 点火烘料操作 320
10.7.2 风口参数选择 321
10.7.3 点火 323
10.7.4 加料 326
10.7.5 送气 328
10.8 出铁 328
10.8.1 出铁时间的确定 328
10.8.2 出第一次铁应考虑开铁口所需时间 330
10.8.3 有些厂在开炉出铁方面的创造 330
10.9 后续操作 330
10.9.1 改变装料 330
10.9.2 加负荷条件与加负荷 330
10.9.3 降铁水含硅量速度 330
10.9.4 加风速度 331
10.9.5 加风过程与装料制度相适应 331
参考文献 331
11 停风、封炉和停炉 332
11.1 短期停风 333
11.1.1 短期停风特点 333
11.1.2 短期停风操作程序 333
11.1.3 短期停风后送风程序 333
11.1.4 停送风注意事项 334
11.2 突然停风 334
11.2.1 突发事故的停风 335
11.2.2 紧急停水 335
11.2.3 鼓风机突然停风 336
11.2.4 紧急停电 336
11.3 长期停风 336
11.3.1 停风准备工作 337
11.3.2 停风程序(第一步) 337
11.3.3 炉顶点火 337
11.3.4 停风程序(第二步) 338
11.3.5 长期停风注意事项 339
11.4 降料面 339
11.4.1 停气降料面的缺点 339
11.4.2 全风降料面实践 340
11.5 封炉 341
11.5.1 封炉要点 341
11.5.2 封炉实例 342
11.5.3 经验教训 344
11.5.4 封炉小结 345
11.6 停炉 345
11.6.1 安全、快速降料面 345
11.6.2 利用煤气成分变化判定料面深度 345
11.6.3 控制煤气中H2、O2量,杜绝煤气爆震 346
11.6.4 放出全部残铁 348
参考文献 351
12 高炉爆炸 352
12.1 煤气爆炸 353
12.1.1 高炉煤气爆炸的必要条件 353
12.1.2 1号高炉炉内煤气爆炸的原因 353
12.1.3 混合形成爆炸煤气后发生的爆炸 354
12.1.4 预防煤气爆炸 355
12.1.5 炉内打水爆震和爆炸 356
12.2 铁水遇水发生爆炸 357
参考文献 358
- 《药剂学实验操作技术》刘芳,高森主编 2019
- 《细菌蛋白分泌系统研究方法与操作规程》(法)劳雷·詹来特,埃里克·卡斯卡莱斯编者;褚怡,崔改泵责编郑福英,宫晓炜,陈启伟,刘永生译者 2019
- 《云架构操作系统基础 Red Hat Enterprise Linux 7》李贺华 2018
- 《痘病毒学及痘苗病毒实验操作指南 2012》(美)斯图亚特·N.艾萨克斯 2019
- 《大气二次污染手工监测标准操作程序》袁鸾,岳玎利,郁建珍,钟流举 2019
- 《中国食品药品检验检测技术系列丛书 中国药品检验标准操作规范 2019版》中国食品药品检定研究院 2019
- 《中小学机器人 教学程序与操作指南 中》刘清明主编 2019
- 《家庭营养操作流程》王新颖,黄迎春主编 2019
- 《移空技术操作手册 一项本土化心身治疗技术》刘天君,(德)本哈德·特林克勒 2019
- 《生命科学实验室安全与操作规范》苏莉,曾小美,王珍主编 2019
- 《中风偏瘫 脑萎缩 痴呆 最新治疗原则与方法》孙作东著 2004
- 《水面舰艇编队作战运筹分析》谭安胜著 2009
- 《王蒙文集 新版 35 评点《红楼梦》 上》王蒙著 2020
- 《TED说话的力量 世界优秀演讲者的口才秘诀》(坦桑)阿卡什·P.卡里亚著 2019
- 《燕堂夜话》蒋忠和著 2019
- 《经久》静水边著 2019
- 《魔法销售台词》(美)埃尔默·惠勒著 2019
- 《微表情密码》(波)卡西亚·韦佐夫斯基,(波)帕特里克·韦佐夫斯基著 2019
- 《看书琐记与作文秘诀》鲁迅著 2019
- 《酒国》莫言著 2019
- 《指向核心素养 北京十一学校名师教学设计 英语 七年级 上 配人教版》周志英总主编 2019
- 《北京生态环境保护》《北京环境保护丛书》编委会编著 2018
- 《指向核心素养 北京十一学校名师教学设计 英语 九年级 上 配人教版》周志英总主编 2019
- 《高等院校旅游专业系列教材 旅游企业岗位培训系列教材 新编北京导游英语》杨昆,鄢莉,谭明华 2019
- 《中国十大出版家》王震,贺越明著 1991
- 《近代民营出版机构的英语函授教育 以“商务、中华、开明”函授学校为个案 1915年-1946年版》丁伟 2017
- 《新工业时代 世界级工业家张毓强和他的“新石头记”》秦朔 2019
- 《智能制造高技能人才培养规划丛书 ABB工业机器人虚拟仿真教程》(中国)工控帮教研组 2019
- 《陶瓷工业节能减排技术丛书 陶瓷工业节能减排与污染综合治理》罗民华著 2017
- 《全国职业院校工业机器人技术专业规划教材 工业机器人现场编程》(中国)项万明 2019