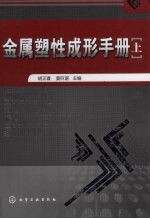
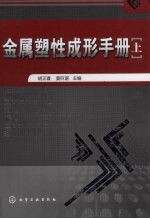
金属塑性成形手册 上PDF电子书下载
- 电子书积分:19 积分如何计算积分?
- 作 者:胡正寰,夏巨谌主编
- 出 版 社:北京:化学工业出版社
- 出版年份:2009
- ISBN:9787122053213
- 页数:686 页
第1篇 概论 1
1 材料塑性成形的特点 3
2 材料塑性成形在国民经济中的地位和作用 3
3 中国塑性成形加工技术发展概况及成就 4
3.1 古代塑性成形加工技术概况 4
3.2 建国以来前30余年的发展概况及成就 4
3.3 改革开放20余年的发展概况及成就 5
4 中国锻压技术与国外先进锻压技术的比较 9
5 21世纪材料塑性成形的发展趋势 11
6 加入WTO后材料塑性成形发展的机遇与应对挑战的策略及措施 12
6.1 加入WTO后材料塑性成形发展的机遇 12
6.2 材料塑性成形面临的挑战 12
6.3 应对挑战的策略与措施 13
参考文献 16
第2篇 锻造成形 17
第1章 自由锻造工艺及其装备 22
1 自由锻造工艺 22
1.1 自由锻造的基本工序 22
1.2 自由锻工艺过程的制订 27
2 锻造原材料及其加热 31
2.1 钢锭与钢材 31
2.2 算料与下料 33
2.3 坯料加热及加热规范 36
3 大型锻件的锻造特点 39
3.1大型锻件的生产特点 39
3.2 大型锻造的工艺特点 39
3.3 提高大型锻件质量的工艺措施 40
4 合金钢的锻造特点 41
4.1 高合金钢的锻造特点 41
4.2 莱氏体高合金工具钢的锻造 41
4.3 不锈钢的锻造 43
4.4 高温合金的锻造 44
5 有色金属及合金的锻造特点 45
5.1 铝合金锻造 45
5.2 镁合金锻造 47
5.3 铜合金锻造 48
5.4 钛合金锻造 49
6 锻件锻后的冷却和热处理 52
6.1 锻件的冷却 52
6.2 锻件的热处理 52
7 锻造工具的特点和应用 53
7.1 锻造工具的分类 53
7.2 锻造工装选用及设计原则 53
8 锻造设备的选用 53
8.1 选择主要锻压设备的原则 53
8.2 自由锻锤吨位的概略估算 53
8.3 自由锻造水压机的选定 53
9 自由锻造工艺举例 53
9.1 齿轮锻造工艺规程的制订 53
9.2 600MW汽轮机转子锻造工艺规程 54
第2章 胎模锻 58
1 胎模锻造特点及应用 58
1.1 胎模锻造特点 58
1.2 胎模锻的应用 58
2 胎膜锻件分类及胎模锻件图设计 59
2.1 胎模锻件分类 59
2.2 胎模锻件图的设计 60
3 胎模锻工艺 62
3.1 镦粗 62
3.2 拔长 63
3.3 摔形 64
3.4 扣形 64
3.5 冲孔与扩孔 65
3.6 弯曲 65
3.7 翻边 66
3.8 劈叉 66
3.9 挤压 66
3.10 焖形 67
3.11 冲切 68
4 胎模设计 69
4.1 制坯整形模 69
4.2 成形模 70
4.3 切边冲孔模 73
5 胎模锻设备的选用 74
5.1 设备能力的选择要点 74
5.2 设备吨位的计算 74
6 自由锻锤固定胎模锻造的特点 75
7 胎模锻实例 76
第3章 锤类设备上模锻 79
1 模锻锤上模锻特点及应用范围 79
2 锻件分类及模锻工步选择 79
3 模锻锤上模锻工艺规程的制订 81
3.1 锻件图的设计 81
3.2 选择模锻工艺 88
3.3 确定模锻锤吨位 89
3.4 坯料计算 89
4 终锻模膛设计 89
4.1 热锻件图的确定 89
4.2 飞边槽的确定 90
4.3 终锻模膛的绘制及尺寸标注 91
5 预锻模膛的设计 91
5.1 预锻模膛的采用原则 91
5.2 采用预锻模膛带来的不利因素 92
5.3 预锻模膛的设计原则 92
5.4 预锻模膛的尺寸标注 95
6 钳口 95
6.1 钳口的作用 95
6.2 钳口尺寸的确定 95
7 拔长模膛 96
7.1 拔长模膛的作用与型式 96
7.2 拔长模膛的结构 96
7.3 拔长模尺寸的确定 96
7.4 拔长平台的设计 97
8 滚压模膛设计 97
8.1 滚压模膛的作用与型式 97
8.2 滚压模膛的尺寸确定 98
9 压肩模膛设计 100
9.1 压肩模膛的型式 100
9.2 压肩模膛的尺寸设计 100
10 弯曲模膛 100
10.1 弯曲模膛纵向截面设计 100
10.2 弯曲模膛横截面形状的设计 101
10.3 坯料的定位 101
10.4 弯曲模膛宽度 101
10.5 弯曲模膛高度方向的位置 101
11 切断模膛 101
12 镦粗台与压扁台 102
12.1 镦粗台的作用与尺寸设计 102
12.2 镦粗台在模块上的位置 102
12.3 压扁台 103
13 锻模结构 103
13.1 模膛的排列 103
13.2 错移力的平衡与锁扣设计 105
13.3 模膛的壁厚 107
13.4 锻模承击面 108
14 模块尺寸的确定 108
15 锻模的一般要素 108
16 锻模的加工精度及粗糙度要求 109
17 锻模材料及热处理 110
18 典型锻件锤模锻示例 110
19 高速锤上闭式模锻 111
19.1 高速锤闭式模锻的特点及模锻工艺制定 111
19.2 高速锤模锻的典型锻件及其基本工艺参数 112
19.3 模具设计和制造特点 113
19.4 一些典型锻件的高速闭式模锻工艺 113
第4章 螺旋压力机上模锻 117
1 螺旋压力机模锻特点及应用范围 117
1.1 螺旋压力机模锻的特点 117
1.2 应用范围 117
2 锻件分类和锻件图设计 117
3 模锻工步的选择 119
4 开式锻模设计 120
4.1 飞边槽 120
4.2 模膛布置 121
4.3 模壁厚度的确定 121
5 闭式锻模设计 121
5.1 凸、凹模间隙的确定 121
5.2 凸模尺寸的确定 121
6 成组锻模的设计 122
7 锻模结构设计 123
8 螺旋压力机 124
8.1 螺旋压力机的种类及其性能特点 124
8.2 螺旋压力机的主要技术参数及吨位选择 126
9 实例 127
第5章 热模锻压力机上模锻 130
1 模锻特点与应用 130
1.1 模锻特点 130
1.2 应用范围 130
2 锻件分类与锻件图设计特点 130
2.1 锻件分类 130
2.2 锻件图设计特点 130
3 变形工步及工步图设计 130
3.1 变形工步 130
3.2 工步图设计 136
4 坯料选择 139
4.1 计算坯料体积Vm 139
4.2 计算坯料尺寸 139
4.3 坯料选定 139
5 模锻力计算及吨位的确定 139
5.1 开式模锻算力公式之一 139
5.2 开式模锻算力公式之二 139
5.3 挤压力 139
5.4 设备选择 139
6 锻模模架结构型式 140
6.1 模架的型式 140
6.2 模架结构 141
7 锻模结构与模膛设计 143
7.1 锻模结构 143
7.2 模膛设计 144
8 实例 150
8.1 转向节模锻 150
8.2 轮毂模锻 153
8.3 曲轴模锻 154
第6章 平锻机上模锻 162
1 模锻特点及应用范围 162
1.1 平锻机模锻过程 162
1.2 主要锻造工序和应用范围 162
1.3 平锻机的模锻特点 162
2 平锻件分类及其工艺特点 163
3 锻件图的绘制 164
3.1 确定分模面形式和位置 164
3.2 锻件的机械加工余量和公差 164
3.3 模锻斜度和圆角半径 164
3.4 锻件技术条件 165
4 镦锻力计算和平锻机规格选择 165
4.1 镦锻力的计算公式 165
4.2 平锻机的规格选择 166
4.3 举例 166
5 镦粗(聚集)规则 169
5.1 自由聚集规则 169
5.2 凹模内聚集规则 169
5.3 锥形模膛聚集规则 169
5.4 管料镦粗(聚集)规则 170
6 平锻工步设计 171
6.1 坯料直径选择及其长度确定 171
6.2 终锻工步设计 172
6.3 预锻工步设计 172
6.4 聚集工步设计 174
6.5 管料的聚集工步设计 174
7 平锻模结构 176
7.1 模具的总体结构 176
7.2 凸模夹持器的设计 176
7.3 凹模体 177
8 平锻模膛和凸模、凹模镶块 179
8.1 终锻凹模和凸模 179
8.2 预锻凸模和凹模 180
8.3 聚集凸模和凹模 180
8.4 夹紧模膛设计 181
8.5 卡细模膛设计 181
8.6 扩径模膛设计 181
8.7 穿孔凹模和凸模 182
8.8 切边模膛设计 184
8.9 切断模膛设计 184
8.10 管料聚集凹模和凸模 185
9 典型锻件的工艺及其模具设计 186
9.1 一般设计程序 186
9.2 转向摇臂轴平锻工艺及模具设计 186
9.3 轮毂轴管锻件平锻工艺及模具设计 187
10 平锻机热挤压工艺及模具设计 188
10.1 水平分模平锻机挤压工艺分析 188
10.2 挤压模结构及工作部分主要尺寸 188
10.3 热挤压举例 189
第7章 闭式模锻 192
1 闭式模锻的特点及应用 192
1.1 闭式模锻的特点 192
1.2 闭式模锻的应用 192
2 闭式模锻件的分类及表示锻件复杂程度的参数 193
2.1 锻件的分类 193
2.2 表示锻件复杂程度的参数 193
3 闭式模锻变形过程分析 195
3.1 镦粗式闭式模锻的变形过程 195
3.2 镦粗压入式闭式模锻变形过程 196
3.3 侧向挤压模锻 196
4 闭式模锻变形力的计算 197
4.1 影响闭式模锻力的主要因素 197
4.2 闭式模锻力的计算 199
5 闭式模锻工艺的制订 204
5.1 锻件的工艺性分析 204
5.2 锻件图的制订 204
5.3 模锻工序及锻坯的设计 205
5.4 主要的辅助工序及特点 206
6 闭式锻模设计 207
6.1 模具的类型 207
6.2 分流降压腔的设计 208
6.3 可分凹模模具设计要点及设计方法与步骤 212
7 闭式模锻设备 213
7.1 双动热模锻压力机 213
7.2 中小件专用多向闭式模锻压力机 215
8 闭式模锻实例 216
8.1 模锻锤上整体凹模闭式模锻 216
8.2 螺旋压力机上整体凹模闭式模锻 217
8.3 螺旋压力机上可分凹模模锻 219
8.4 热模锻压力机上闭式模锻 222
8.5 曲柄压力机用可分凹模模具设计及实例 225
8.6 双动压力机可分凹模模锻 229
8.7 高速锤闭式模锻 231
第8章 多向模锻 237
1 多向模锻的特点及应用范围 237
1.1 多向模锻的特点 237
1.2 多向模锻工艺的适用范围 237
2 多向模锻工艺及金属流动分析 238
2.1 多向模锻工艺 238
2.2 多向模锻中的金属流动分析 240
3 多向模锻力的计算 240
4 多向模锻件图设计 241
5 多向模锻模具设计 243
5.1 模具设计要点 243
5.2 模具结构设计 243
6 多向模锻压力机 246
7 多向模锻实例 248
第9章 精密模锻 250
1 精密模锻工艺的特点及应用 250
1.1 精密模锻工艺的特点 250
1.2 精密模锻工艺的应用 250
2 影响精密模锻件尺寸精度的主要因素 251
2.1 坯料体积的波动 251
2.2 模膛的尺寸精度和磨损 251
2.3 模具温度和锻件温度的波动 252
2.4 零件结构的工艺性 252
2.5 模具和锻件的弹性变形 253
2.6 锻件高度尺寸的变化同各种影响因素的关系 253
3 各类锻件的精密模锻工艺方案分析 253
3.1 齿轮类锻件 253
3.2 带有薄肋的锻件 254
3.3 带工字形断面复杂长轴类锻件 254
3.4 形状复杂的锻件 254
4 精密模锻模具设计特点 254
4.1 精密模锻模膛与精密模锻件的设计 254
4.2 模膛尺寸计算 255
4.3 模膛的尺寸公差和表面粗糙度 256
4.4 有深凹穴且形状复杂的模膛的布置 256
4.5 模具的导向装置 256
4.6 模具的推出装置 256
5 实例 256
6 冷精密模锻的特点与应用 257
6.1 传统冷精密模锻工艺的特点与应用 257
6.2 冷精密模锻工艺的新进展 258
7 温精密模锻的特点与应用 262
7.1 温锻时加热温度与尺寸精度的关系 263
7.2 温精密模锻的应用实例 263
8 多工序温冷复合精密模锻的特点及应用 265
9 多层杯筒形零件流动控制成形 267
10 闭式冷精密模锻模具及设备 269
10.1 闭式冷精密模锻模具 269
10.2 闭式冷精密模锻设备 269
参考文献 271
第3篇 板料冲压成形 273
第1章 冲压成形工艺基础 275
1 冲压成形工艺分类 275
2 冲压成形用原材料 276
2.1 冲压常用板料规格与力学性能 276
2.2 板料的冲压性能 287
2.3 常用板料的冲压性能 297
2.4 冲压用新材料及其性能 302
第2章 冲裁 305
1 冲裁机理 305
1.1 冲裁变形过程 305
1.2 冲裁力-行程曲线 305
1.3 变形区受力状况和应力状态 305
1.4 冲裁件断面特征 306
2 冲裁件的工艺性 306
2.1 冲裁件结构工艺性 306
2.2 冲裁件的精度与表面粗糙度和毛刺高度 307
3 冲裁间隙 308
3.1 间隙对冲裁过程的影响 308
3.2 冲裁间隙分类 310
3.3 确定冲裁间隙的方法 311
3.4 常用间隙表 311
4 冲裁凸、凹模工作部分尺寸设计 313
4.1 凸、凹模尺寸计算原则 313
4.2 凸、凹模分开加工时其尺寸与公差的确定 313
4.3 凸、凹模配合加工时其尺寸与公差的确定 314
4.4 数控线切割编程时凸、凹模尺寸的确定 314
5 冲裁力的计算 315
5.1 冲裁力的计算方法 315
5.2 减小冲裁力的方法 315
5.3 卸料力、推件力和顶件力计算 315
6 材料利用率 316
6.1 排样及材料的利用率 316
6.2 搭边 318
6.3 条料宽度及导尺间距离的确定 319
7 冲裁模分类及典型结构 320
7.1 落料模 320
7.2 冲孔模 321
7.3 切边模 321
7.4 剖切模、切口模 323
7.5 复合冲裁模典型结构 323
7.6 连续冲裁模典型结构 324
8 冲裁模主要零件的设计及标准的选用 327
8.1 凸模及其固定方法 327
8.2 凹模及其固定方法 329
8.3 模具定位零件及选用 332
8.4 卸料及出件装置 335
8.5 安装、夹持零件及标准模架的选择 337
9 提高冲裁件质量和精度的方法 339
10 精密冲裁 340
10.1 精冲机理 340
10.2 精冲力的计算 343
10.3 精冲件结构工艺性 343
10.4 精冲复合工艺 345
10.5 精冲件质量及影响因素 349
10.6 精冲材料及工艺润滑 353
10.7 精冲模具 354
10.8 精冲设备 364
第3章 弯曲 369
1 弯曲变形分析 369
1.1 弯曲变形过程和特点 369
1.2 弯曲变形时应力应变状态 370
2 弯曲件的工艺性 370
2.1 最小相对弯曲半径 370
2.2 材料的纤维方向 371
2.3 影响最小相对弯曲半径的因素 371
3 弯曲件展开尺寸计算 372
3.1 中性层位置 372
3.2 展开长度计算 374
4 弯曲件的回弹 378
4.1 回弹及影响回弹的因素 378
4.2 回弹值的确定 379
4.3 防止回弹的措施 381
5 弯曲模工作部分尺寸计算 383
5.1 凸、凹模的圆角半径 383
5.2 凹模的工作深度 384
5.3 凸、凹模的间隙 384
5.4 凹模工作部分尺寸计算及制造公差的确定 384
6 弯曲力的计算 385
6.1 自由弯曲时的弯曲力 385
6.2 校正弯曲时的弯曲力 385
6.3 顶件力和压料力 386
6.4 弯曲设备选择 386
7 弯曲模结构设计 386
7.1 弯曲模设计要点 386
7.2 常见弯曲模结构介绍 388
第4章 拉深 394
1 拉深基本原理 394
1.1 圆筒形件的拉深过程 394
1.2 拉深时毛坯的应力应变状态 395
1.3 凸缘变形区的应力分析 396
1.4 拉深起皱及防皱措施 397
1.5 拉断与极限拉深系数 399
2 拉深件的工艺性 400
3 圆筒形件的拉深工序计算 401
3.1 修边余量的确定 401
3.2 毛坯尺寸计算 401
3.3 拉深系数和拉深次数 414
4 带凸缘圆筒形件的拉深 418
4.1 拉深特点 418
4.2 拉深系数 418
4.3 拉深方法 419
5 回转体阶梯形件的拉深 421
5.1 阶梯形件拉深次数的确定 421
5.2 阶梯形件拉深原则 421
6 盒形件拉深 422
6.1 盒形件的拉深特点 422
6.2 盒形件首次拉深成形极限 423
6.3 盒形件毛坯尺寸计算 423
6.4 盒形件的工艺计算 425
6.5 盒形件拉深工序计算的新方法 430
7 其他拉深方法 433
7.1 反拉深 433
7.2 带料连续拉深 433
7.3 变薄拉深 438
8 拉深力和拉深功的计算 439
8.1 拉深力的计算 439
8.2 压床吨位的选择 441
8.3 拉深功的计算 442
9 拉深模工作部分尺寸的确定 442
9.1 拉深凸凹模间隙确定 442
9.2 拉深凸凹模圆角半径 443
9.3 拉深凸凹模工作部分结构形状及尺寸 444
10 拉深过程中的辅助工序 445
10.1 润滑 445
10.2 热处理 446
10.3 酸洗 446
11 拉深件废品类型、产生原因及防止措施 447
12 拉深零件工序安排实例 447
第5章 成形 452
1 胀形与翻边 452
1.1 胀形 452
1.2 翻边 454
2 曲面零件成形 463
2.1 半球形件成形 463
2.2 抛物形件成形 464
2.3 锥形件成形 465
3 汽车覆盖件的冲压成形 469
3.1 汽车覆盖件材料 469
3.2 汽车覆盖件的成形特点及分类 472
3.3 覆盖件冲压成形的变形特点 474
3.4 汽车覆盖件成形工艺 475
3.5 拉深成形工艺设计 482
3.6 汽车覆盖件成形模具的调试 490
4 厚板成形 493
4.1 厚板零件成形工艺 494
4.2 厚板零件热成形模具设计 499
4.3 缺陷的产生及防止 501
5 其他成形方法 505
5.1 缩口 505
5.2 扩口 507
5.3 充液拉深 508
第6章 冲压自动化与安全技术 511
1 冲压生产自动化 511
1.1 条料、卷料和板料送料装置 511
1.2 半成品送料装置 528
1.3 自动检测保护装置 549
1.4 冲压自动线 555
1.5 冲压生产线的输送机构 557
2 冲压安全技术 557
2.1 人身安全技术 557
2.2 冲压模具的安全技术要求 569
2.3 冲压生产中的噪声及其控制 572
参考文献 574
第4篇 板型管轧制成形 575
第1章 板带轧制成形 577
1 板带材的特点及分类 577
1.1 产品特点 577
1.2 技术要求 577
1.3 产品分类 578
2 板带轧制参数及产品几何参数 578
2.1 轧制过程基本参数 578
2.2 轧制过程的塑性变形 579
2.3 轧制压力与轧制力矩 580
2.4 板带的几何参数 581
2.5 板带产品的公差标准 584
3 板带轧机 585
3.1 轧机的结构及组成 585
3.2 板带轧机的分类 586
4 板带轧制生产工艺 587
4.1 中厚板 587
4.2 热轧薄板 590
4.3 冷轧薄板 593
5 板带轧制质量与性能控制 595
5.1 厚度控制 595
5.2 板形控制 598
5.3 温度和组织性能控制 603
第2章 型材轧制成形 607
1 型钢的品种及其生产工艺过程 607
1.1 型钢的品种和用途 607
1.2 热轧型钢轧制方法和特点 609
1.3 轨梁和大、中型型钢生产 611
1.4 小型型钢和线材生产 614
1.5 型钢生产发展趋势和轧制新技术 617
2 小型型钢和棒材连轧生产 620
2.1 小型型钢和棒材连轧生产的主要特点及其工艺过程 620
2.2 小型型钢和棒材连轧机的组成、类型及主要设备 621
3 高速线材生产 625
3.1 高速线材生产发展概况 625
3.2 高速线材生产工艺 625
3.3 高速线材轧机的组成、类型及主要设备 627
4 切分轧制技术 630
4.1 切分轧制技术的发展概况及其主要特点 630
4.2 切分轧制技术的基本方法 631
4.3 切分轧制技术在型钢轧机上的应用 633
5 H型钢生产 635
5.1 轧制H型钢的生产工艺 635
5.2 焊接H型钢的生产工艺 637
5.3 H型钢生产的新工艺和新设备 638
6 冷弯型钢 639
6.1 冷弯型钢产品的类型 639
6.2 冷弯型钢的材质要求 640
6.3 冷弯型钢的成形特点与成形过程 640
6.4 辊式冷弯成形生产工艺及其设备组成 641
第3章 管材轧制成形 643
1 管材的特点、分类及基本要求 643
1.1 管材的特点 643
1.2 钢管的分类 643
1.3 钢管的技术要求 643
1.4 钢管的轧制生产 644
2 管材的原料 645
2.1 管坯 645
2.2 管坯加热 646
3 管坯轧制穿孔 646
3.1 管坯斜轧穿孔 646
3.2 二辊斜轧穿孔变形过程 646
3.3 二辊斜轧穿孔过程运动学 647
3.4 二辊斜轧穿孔过程咬入条件 649
3.5 斜轧实心圆管坯的应力和变形状态——孔腔形成机理 650
3.6 二辊斜轧穿孔作用力与力矩 653
3.7 三辊斜轧穿孔 654
3.8 推轧穿孔机 656
3.9 导盘式二辊斜轧穿孔机——Diescher穿孔机 656
3.10 新型菌式(锥形辊)穿孔机 657
4 钢管在圆孔型中的纵轧 659
4.1 圆孔型中轧管的分类 659
4.2 圆孔型中轧管变形过程 661
4.3 圆孔型中轧管的变形区和孔型的几何参数 662
4.4 圆孔型中轧管的运动学 663
4.5 在圆孔型中轧管时的咬入条件 663
4.6 纵轧钢管的力参数计算 664
4.7 钢管空心轧制 666
4.8 连轧管机组 669
4.9 张力减径机组 675
5 钢管斜轧延伸 678
5.1 三辊斜轧管机轧管 678
5.2 狄塞尔轧管机轧管 679
5.3 Accu-Roll轧管机轧管 680
5.4 三辊行星轧机(PSW)轧管 680
6 钢管的周期轧制 682
6.1 周期式轧管变形过程和变形量 683
6.2 周期式轧管咬入 683
6.3 周期式轧管送进量的确定 684
6.4 周期式轧管滑移现象 684
6.5 周期式轧管轧制力的计算 685
参考文献 686
- 《Maya 2018完全实战技术手册》来阳编著 2019
- 《高等教育双机械基础课程系列教材 高等学校教材 机械设计课程设计手册 第5版》吴宗泽,罗圣国,高志,李威 2018
- 《慢性呼吸系统疾病物理治疗工作手册》(荷)瑞克·考斯林克(RikGosselink) 2020
- 《战略情报 情报人员、管理者和用户手册》(澳)唐·麦克道尔(Don McDowell)著 2019
- 《实用内科手册》黄清,阮浩航主编 2016
- 《基层医疗卫生机构安全用药手册》黎月玲,熊慧瑜 2019
- 《同仁眼科手册系列 同仁儿童眼病手册》付晶编 2018
- 《环境噪声监测实用手册》中国环境监测总站编 2018
- 《高度关注物质(SVHC)毒性手册 上》顾爱华主编 2019
- 《吉他宝典 吉他手超级手册 上》姜伟主编;汶麟,姚林,杜新春,赖康康,朱家明,克尔曼副主编 2018