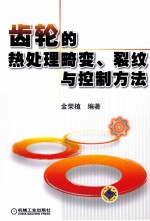
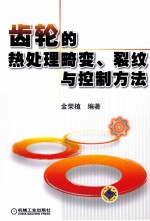
齿轮的热处理畸变、裂纹与控制方法PDF电子书下载
- 电子书积分:13 积分如何计算积分?
- 作 者:金荣植编著
- 出 版 社:北京:机械工业出版社
- 出版年份:2014
- ISBN:9787111445050
- 页数:364 页
第1章 热处理应力的概述 1
1.1 热处理应力及其分类 1
1.2 热处理残余应力 2
第2章 热处理畸变及其原因分析和规律 4
2.1 热处理畸变机理 4
2.2 热处理畸变的种类 4
2.3 外应力与热处理畸变 5
2.4 应力与热处理畸变 5
2.5 热处理畸变原因分析及畸变规律 6
第3章 齿轮的整体热处理畸变与控制 11
3.1 环套类齿轮的热处理畸变与控制 11
3.1.1 中碳钢环套类齿轮的热处理畸变与控制 11
3.1.2 中碳低合金钢环套类齿轮的热处理畸变与控制 12
3.2 轴类齿轮的热处理畸变与控制 14
3.2.1 轴类齿轮的热处理畸变 14
3.2.2 轴类齿轮的热处理畸变影响因素及其控制措施 14
3.2.3 中碳钢和中碳合金钢带键槽齿轮轴的热处理畸变与控制 17
第4章 齿轮的化学热处理畸变与控制 18
4.1 齿轮的渗碳热处理畸变与控制 18
4.1.1 齿轮的渗碳热处理畸变 19
4.1.2 齿轮的渗碳热处理畸变影响因素 23
4.1.3 控制与减小齿轮渗碳热处理畸变的措施 27
4.1.4 环形齿轮(盘形齿轮、齿圈)的渗碳热处理畸变与控制 41
4.1.5 带内花键齿轮的渗碳淬火畸变与控制 44
4.1.6 双联齿轮的渗碳淬火畸变与控制 57
4.1.7 齿轮轴的渗碳淬火畸变与控制 59
4.1.8 大型齿轮(轴)的渗碳淬火畸变与控制 60
4.1.9 大型焊接齿轮的渗碳淬火畸变与控制 72
4.1.10 齿轮的碳氮共渗热处理畸变与控制 72
4.2 齿轮的渗氮热处理畸变与控制 74
4.2.1 渗氮热处理及其特点 74
4.2.2 渗氮对齿轮热处理畸变的影响 75
4.2.3 齿轮的气体渗氮和离子渗氮畸变与控制 75
4.2.4 环套类齿轮的渗氮热处理畸变与控制 80
4.2.5 轴类齿轮的渗氮热处理畸变与控制 81
4.2.6 齿轮的氮碳共渗热处理畸变与控制 84
4.2.7 齿轮的低压真空氮碳共渗技术 86
4.2.8 齿轮的深层渗氮技术 87
4.2.9 齿轮的稀土催渗氮技术 88
第5章 齿轮的感应热处理畸变与控制 89
5.1 齿轮的感应热处理及其特点 89
5.2 齿轮的感应淬火畸变与控制 89
5.2.1 感应淬火的特点 90
5.2.2 感应淬火的畸变 91
5.2.3 减小与控制齿轮感应淬火畸变的措施 93
5.3 齿轮的高频感应淬火畸变与控制 99
5.3.1 齿轮的高频感应淬火畸变特点及其影响因素 99
5.3.2 不同高频感应淬火方法及其畸变特点 100
5.3.3 齿轮高频感应淬火后的畸变 101
5.4 齿轮的中频感应淬火畸变与控制 114
5.4.1 轴类齿轮的中频感应淬火畸变与控制 114
5.4.2 环套类齿轮的中频感应淬火畸变与控制 115
5.5 埋液感应淬火畸变控制技术 117
第6章 影响齿轮热处理畸变的(其他)因素 119
6.1 钢中含碳量对畸变的影响 121
6.2 钢中合金元素对畸变的影响 122
6.3 钢的淬透性对畸变的影响 123
6.4 齿轮形状、截面尺寸对畸变的影响 126
6.5 钢的原始组织对畸变的影响 128
6.5.1 钢的原始组织对热处理畸变的影响 128
6.5.2 连铸坯形对齿轮热处理畸变的影响 131
6.6 锻造对畸变的影响 132
6.7 毛坯预备热处理对畸变的影响 133
6.8 残余应力对畸变的影响 134
6.9 淬火加热过程对畸变的影响 136
6.10 淬火温度对畸变的影响 139
6.11 淬火冷却对畸变的影响 140
6.11.1 冷却速度与淬火冷却介质对畸变的影响 141
6.11.2 冷却不均匀引起的畸变 142
6.11.3 淬火冷却介质温度对畸变的影响 143
6.12 淬火操作对畸变的影响 144
6.12.1 齿轮装夹及支承方式对畸变的影响 144
6.12.2 淬火加热温度及加热均匀性对畸变的影响 148
6.12.3 重复淬火对畸变的影响 148
6.12.4 淬火冷却对畸变的影响 148
6.12.5 其他操作因素对畸变的影响 149
6.13 回火、冷处理及时效处理对畸变的影响 149
6.13.1 回火对畸变的影响 149
6.13.2 冷处理对畸变的影响 150
6.13.3 时效处理对畸变的影响 151
第7章 减小与控制齿轮热处理畸变的方法与措施 152
7.1 合理选材和正确设计 152
7.1.1 合理选材 152
7.1.2 正确设计齿轮结构 156
7.1.3 正确设计齿轮硬度 161
7.2 优化锻造 162
7.3 采用预备热处理 163
7.3.1 预备退火处理 163
7.3.2 齿轮半成品的预备热处理 164
7.3.3 铸钢齿轮的预备热处理 166
7.3.4 渗碳齿轮毛坯的预备热处理 170
7.3.5 渗碳齿轮毛坯的等温正火处理 171
7.3.6 预备调质处理 174
7.4 消除机械加工残余应力 177
7.4.1 合理选择切削用量 177
7.4.2 热处理前的残余应力消除 177
7.5 合理调整冷热加工工序 180
7.5.1 畸变试样及畸变试验 180
7.5.2 合理安排冷热加工工序 180
7.5.3 预留加工余量 182
7.5.4 进行预先修正 183
7.5.5 采用预先胀大花键孔方法 185
7.5.6 感应加热预先收缩内孔方法 186
7.5.7 采用“去渗碳层→二次加热淬火”方法 187
7.6 合理选择装炉及支承方式 187
7.7 减小热应力 189
7.7.1 选择合理的加热方法 189
7.7.2 选择适当的淬火加热温度、加热速度和保温时间 189
7.7.3 提高淬火油温度 193
7.7.4 采用分级淬火工艺 195
7.7.5 采用等温淬火工艺 199
7.7.6 采用亚温淬火(临界温度淬火)工艺 201
7.7.7 采用喷液淬火方法 203
7.7.8 合理选择淬火冷却介质及淬火方式 204
7.8 改进热处理工艺与材料 214
7.8.1 采用渗氮(或氮碳共渗)工艺代替渗碳淬火 214
7.8.2 采用“中碳钢调质+感应淬火”代替渗碳淬火 214
7.8.3 采用局部感应淬火代替整体加热淬火 216
7.8.4 采用盐浴快速加热淬火工艺 216
7.8.5 采用碳氮共渗代替渗碳淬火 217
7.8.6 采用“正火+回火”代替调质处理 218
7.8.7 改变齿轮材料 220
7.9 采用减小齿轮畸变的热处理工艺方法与装备 221
7.9.1 减小齿轮畸变的热处理工艺方法 222
7.9.2 减小细长齿轮轴、薄片盘形齿轮和薄壁齿套畸变的工艺方法 222
7.9.3 减小复杂齿轮体积畸变和翘曲畸变的工艺方法 223
7.9.4 减小齿轮时效畸变的工艺方法 225
7.9.5 采用压床淬火 226
7.10 采用先进的工艺和装备减小与控制齿轮热处理畸变 233
7.10.1 采用低压真空热处理炉与高压气淬设备及其工艺 233
7.10.2 采用激光热处理技术与装备 238
7.10.3 采用稀土渗碳(碳氮共渗)技术与BH催渗碳技术 241
7.10.4 采用双频感应淬火技术与装备 244
7.10.5 采用渗碳后感应淬火技术 245
7.10.6 采用新的模压式感应淬火技术 247
7.10.7 采用同步双频感应淬火技术 248
7.11 采用微小畸变钢材减小齿轮畸变 250
第8章 齿轮热处理畸变的校正 252
8.1 齿轮热处理畸变的校正方法 252
8.1.1 冷态校正方法 253
8.1.2 热态校正方法 254
8.1.3 淬火状态校正方法 255
8.1.4 回火校正方法 256
8.2 轴类齿轮热处理畸变的校直方法 256
8.2.1 冷态校直方法 256
8.2.2 热态校直方法 258
8.3 环套类齿轮热处理畸变的校正方法 260
8.3.1 收缩(内)孔方法 260
8.3.2 胀大(内)孔方法 266
8.3.3 使用胎具回火定型校正方法 266
8.3.4 采用回火校正花键孔方法 267
8.3.5 采取喷砂校正方法 268
8.3.6 环形齿轮圆度畸变的热点校正方法 268
8.3.7 采用淬火压床的校正方法 268
8.3.8 采用圆度校正机校正圆度畸变方法 269
8.3.9 采用翻面装夹方式校正畸变方法 270
8.3.10 齿轮花键孔的校正方法 271
8.3.11 齿轮的感应加热应力校正方法 271
8.3.12 齿轮的双液淬火收缩内孔方法 273
8.3.13 齿轮的淬火校正方法 273
8.3.14 缩孔齿轮的化学酸蚀挽救方法 274
8.3.15 渗碳齿轮的旋转校直方法 275
8.4 齿轮齿形的校正方法 275
8.4.1 齿部校正 275
8.4.2 硬齿面切削加工校正方法 276
第9章 齿轮的热处理裂纹原因分析与防止措施 278
9.1 淬火残余应力的类型、作用特点及裂纹的形成规律 278
9.1.1 淬火残余应力的类型 278
9.1.2 淬火残余应力的作用特点及裂纹的形成规律 279
9.1.3 淬火应力对工件裂纹的作用 279
9.2 热处理裂纹的分类 280
9.3 热处理裂纹的特征与类型 280
9.3.1 淬火裂纹的特征 281
9.3.2 热处理裂纹的类型 282
9.4 形成齿轮淬火裂纹的影响因素 287
9.4.1 钢的化学成分对淬火裂纹的影响 288
9.4.2 原材料缺陷对齿轮淬火时形成裂纹的影响 293
9.4.3 齿轮结构对形成裂纹的影响 296
9.4.4 淬火前的原始组织及应力状态对形成裂纹的影响 298
9.4.5 加热因素对形成淬火裂纹的影响 300
9.4.6 冷却因素对形成淬火裂纹的影响 302
9.4.7 齿轮表面脱碳对形成淬火裂纹的影响 303
9.4.8 回火对形成裂纹的影响 304
9.5 防止齿轮形成裂纹的方法与措施 304
9.5.1 合理设计齿轮结构与优选钢材 305
9.5.2 改善齿轮锻造质量 307
9.5.3 适当安排冷热加工工序及正确选择预备热处理 307
9.5.4 正确选择加热介质、加热温度及保温时间 308
9.5.5 消除齿轮的残余应力 310
9.5.6 合理选用淬火冷却介质和淬火方法 310
9.5.7 预防白点退火 316
9.5.8 防止淬火裂纹的其他方法 317
9.6 齿轮的感应淬火裂纹形成原因及其防止措施 320
9.6.1 齿轮结构或表面质量造成的淬火裂纹及其防止措施 323
9.6.2 齿轮材料因素造成的淬火裂纹及其防止措施 325
9.6.3 加热温度过高或加热不均造成的淬火裂纹及其防止措施 326
9.6.4 冷却条件不良造成的淬火裂纹及其防止措施 326
9.6.5 齿轮的喷液及浸液感应淬火 328
9.6.6 齿轮高频感应淬火裂纹特征及其形成原因和防止措施 329
9.6.7 齿轮中频感应淬火裂纹的形成原因及其防止措施 335
9.6.8 采用埋液感应淬火预防齿轮感应淬火裂纹 338
9.6.9 齿轮超音频感应淬火裂纹形成原因及其防止措施 338
9.7 齿轮的化学热处理裂纹形成原因及其防止措施 340
9.7.1 渗碳齿轮表面裂纹形成原因及其防止措施 340
9.7.2 渗氮齿轮表面裂纹形成原因及其防止措施 350
9.8 齿轮的喷丸处理形成裂纹原因及其防止措施 352
9.9 齿轮的磨削裂纹形成原因及其防止措施 352
9.9.1 齿轮磨削裂纹的特征 353
9.9.2 齿轮的磨齿裂纹 354
9.9.3 齿轮花键的磨削裂纹 354
9.9.4 齿轮磨削裂纹与淬火裂纹的区别 354
9.9.5 齿轮的磨削裂纹产生原因分析 354
9.9.6 防止齿轮磨削裂纹的措施 355
9.9.7 防止齿轮磨削裂纹的实例 358
9.10 调质齿轮淬火裂纹形成原因分析及其防止措施 359
参考文献 361
- 《大数据Hadoop 3.X分布式处理实战》吴章勇,杨强 2020
- 《烧结法处理非常规含铁资源研究》王哲著 2018
- 《无机元素原子光谱分析样品预处理技术》吴瑶庆 2019
- 《农村生活污水处理工艺与技术应用》李灵娜著 2019
- 《中国人民大学研究报告系列 中国水处理行业可持续发展战略研究报告 膜工业卷 3》(中国)郑祥,魏源送,王志伟 2019
- 《工业废水处理工艺与设计》高永编著 2019
- 《工业水处理技术》(中国)赵文玉,林华,许立巍 2019
- 《污水处理PPP项目实施方案编制实务》王雁然,方俊,朱立冬 2019
- 《图像处理与图形界面(GUI)设计案例教程》李娜,张丽君 2019
- 《辽河流域制药废水处理与资源化技术》曾萍,宋永会编著 2020
- 《市政工程基础》杨岚编著 2009
- 《家畜百宝 猪、牛、羊、鸡的综合利用》山西省商业厅组织技术处编著 1959
- 《《道德经》200句》崇贤书院编著 2018
- 《高级英语阅读与听说教程》刘秀梅编著 2019
- 《计算机网络与通信基础》谢雨飞,田启川编著 2019
- 《看图自学吉他弹唱教程》陈飞编著 2019
- 《法语词汇认知联想记忆法》刘莲编著 2020
- 《培智学校义务教育实验教科书教师教学用书 生活适应 二年级 上》人民教育出版社,课程教材研究所,特殊教育课程教材研究中心编著 2019
- 《国家社科基金项目申报规范 技巧与案例 第3版 2020》文传浩,夏宇编著 2019
- 《流体力学》张扬军,彭杰,诸葛伟林编著 2019
- 《指向核心素养 北京十一学校名师教学设计 英语 七年级 上 配人教版》周志英总主编 2019
- 《北京生态环境保护》《北京环境保护丛书》编委会编著 2018
- 《高等教育双机械基础课程系列教材 高等学校教材 机械设计课程设计手册 第5版》吴宗泽,罗圣国,高志,李威 2018
- 《指向核心素养 北京十一学校名师教学设计 英语 九年级 上 配人教版》周志英总主编 2019
- 《高等院校旅游专业系列教材 旅游企业岗位培训系列教材 新编北京导游英语》杨昆,鄢莉,谭明华 2019
- 《中国十大出版家》王震,贺越明著 1991
- 《近代民营出版机构的英语函授教育 以“商务、中华、开明”函授学校为个案 1915年-1946年版》丁伟 2017
- 《新工业时代 世界级工业家张毓强和他的“新石头记”》秦朔 2019
- 《智能制造高技能人才培养规划丛书 ABB工业机器人虚拟仿真教程》(中国)工控帮教研组 2019
- 《AutoCAD机械设计实例精解 2019中文版》北京兆迪科技有限公司编著 2019