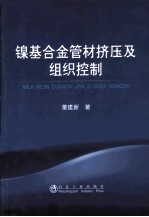
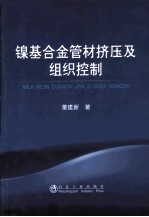
镍基合金管材挤压及组织控制PDF电子书下载
- 电子书积分:14 积分如何计算积分?
- 作 者:董建新著
- 出 版 社:北京:冶金工业出版社
- 出版年份:2014
- ISBN:9787502464318
- 页数:417 页
1镍基合金的挤压特点 1
1.1挤压成型技术 1
1.1.1挤压成型技术的分类 2
1.1.2挤压加工的特点 3
1.2镁合金管材的挤压成型 4
1.3铝合金的挤压成型 5
1.4钢铁材料的挤压成型 6
1.4.1冷挤压 6
1.4.2温挤压 6
1.4.3热挤压 7
1.4.4无缝钢管的热挤压技术 8
1.5镍基合金管材的生产工艺 8
1.5.1感应加热扩孔 10
1.5.2热挤压 11
1.5.3冷轧/冷拔+热处理 12
1.6典型镍基合金的特点 13
1.6.1蒸汽发生器传热管690合金 13
1.6.2油井管G3合金 15
1.7镍基合金管材制备过程中存在的问题 18
1.7.1成材率 18
1.7.2荒管内表面橘皮状缺陷 18
1.7.3冷轧管和成品管内表面丝状皱折 19
1.7.4成品管内壁细晶层及晶粒尺寸不均匀性 21
1.7.5油井管G3合金荒管开裂 22
1.7.6坯料温升引起的热塑性降低 23
参考文献 24
2镍基合金690的热变形行为 26
2.1流变应力的影响规律 26
2.1.1热变形行为的研究方案 26
2.1.2流变应力曲线 28
2.2本构关系的构建及验证 32
2.3再结晶组织的影响规律 38
2.3.1热变形参数对再结晶组织的影响 39
2.3.2初始晶粒尺寸对热变形特性的影响 48
2.3.3再结晶图 53
2.4加工图的建立及应用分析 56
2.4.1加工图的建立 56
2.4.2加工图的分析 61
2.4.3管材热挤压的控制原则 64
2.5热变形组织演变模型及挤压组织控制 66
2.5.1热变形过程中的组织演变及模型构建 67
2.5.2动态再结晶 71
2.5.3亚动态再结晶 77
2.5.4晶粒长大 83
参考文献 86
3镍基合金G3的热变形行为 87
3.1 G3合金的本构方程建立 87
3.1.1真应力-真应变曲线 87
3.1.2峰值应力的表征 89
3.1.3 G3合金的本构方程 91
3.2变形参数对微观组织的影响 94
3.2.1变形温度以及应变速率的影响 94
3.2.2应变量的影响 97
3.3动态再结晶行为 102
3.3.1真应力-真应变曲线 103
3.3.2显微组织特征 105
3.3.3动态再结晶动力学方程 109
3.4 G3合金亚动态(静态)再结晶行为 114
3.4.1双道次热压缩后G3合金的热变形特性 116
3.4.2 G3合金的亚动态再结晶组织演化规律 121
3.4.3热变形参数对G3合金亚动态再结晶行为的影响 125
3.4.4亚动态再结晶动力学方程 127
3.5 G3合金再结晶晶粒长大方程 130
3.5.1 G3合金晶粒长大阶段的组织演化规律 131
3.5.2晶粒长大模型验证 134
参考文献 136
4镍基合金GH536和825的热变形行为 137
4.1 GH536合金 137
4.1.1 GH536的相组成及析出规律 138
4.1.2 GH536合金热加工性 138
4.1.3 GH536合金的焊接性 139
4.1.4 GH536合金的其他性能 140
4.2 825合金 140
4.2.1 825合金的热加工性 141
4.2.2 825合金的焊接性 141
4.2.3 825合金的耐腐蚀性 142
4.3两种合金的组织特征 142
4.3.1热力学模拟方法 143
4.3.2 GH536合金的热力学平衡相 143
4.3.3 GH536合金凝固过程中的元素再分配规律 144
4.3.4合金元素对GH536平衡析出相的影响规律 145
4.3.5合金元素对825合金平衡析出相的影响规律 148
4.3.6 GH536合金相组成及相析出规律 149
4.3.7 825合金的相组成及相析出规律 151
4.4两种合金的热变形特征 157
4.4.1两种合金的应力-应变曲线 157
4.4.2两种合金的流变应力本构方程 160
4.4.3两种合金热加工过程中的动态再结晶行为 163
参考文献 172
5 C-276和800H镍基合金及热变形行为 173
5.1 C-276合金及其性能 173
5.1.1 C-276合金生产过程 175
5.1.2 C-276合金的性能 176
5.2 C-276合金的组织特征 184
5.3 C-276合金锭均匀化 189
5.3.1均匀化理论分析 190
5.3.2合金铸锭的组织分析 192
5.3.3均匀化制度 195
5.3.4均匀化效果 196
5.4热加工塑性 198
5.5热变形行为 203
5.5.1变形参数对组织特征的影响 204
5.5.2热压缩流变曲线特征 208
5.5.3高温压缩的本构关系 209
5.6 800H合金及热变形行为 210
5.6.1 800H合金及性能 210
5.6.2 800H合金的热变形行为 212
5.6.3 800H合金的热加工图 215
参考文献 222
6镍基合金管材基于工艺优化的模拟 223
6.1金属热变形的数值模拟技术研究现状 223
6.1.1金属塑性加工主要的数值模拟技术 223
6.1.2有限元法在金属塑性加工中的应用 224
6.2 GH4169合金管材正挤压的有限元模拟 229
6.2.1有限元模型的建立 229
6.2.2挤压参数调整对结果的影响 231
6.3 G3合金的管材挤压工艺优化有限元模拟 239
6.3.1有限元模型的建立 239
6.3.2材料特性与边界条件的定义 239
6.3.3基准参数选择与参数调整方案 241
6.3.4基准参数下挤压模拟结果分析 242
6.3.5挤压参数调整对结果的影响 246
6.4 690合金管材挤压的有限元模拟与正交试验优化 255
6.4.1有限元模型的建立 255
6.4.2材料特性与边界条件的定义 255
6.4.3正交试验的设计 258
6.4.4适宜参数组合的确定 262
6.5合金特征对挤压工艺的关联影响性 266
6.6 GH625和825合金管材挤压过程数值模拟 268
6.6.1 GH536合金管材挤压模拟 269
6.6.2 825合金管材挤压模拟 273
参考文献 278
7热挤压工艺与磨损和润滑 280
7.1热挤压模具磨损研究现状 281
7.2玻璃润滑热挤压工艺研究现状 283
7.2.1玻璃润滑热挤压工艺介绍 283
7.2.2玻璃润滑剂的研究现状 285
7.2.3玻璃润滑剂的组成 286
7.3 G3合金热挤压模具磨损行为 287
7.3.1模具磨损计算模型 288
7.3.2模具磨损特点 291
7.3.3模具-坯料界面状态对模具磨损的影响 293
7.4 G3合金热挤压过程中的润滑行为及与工艺的关系 298
7.4.1玻璃润滑膜厚度计算公式 299
7.4.2基于润滑特征的G3合金热挤压工艺参数的制定 304
7.4.3 G3合金热挤压工艺对润滑用玻璃粉的黏度要求 322
7.4.4 G3合金热挤压润滑用玻璃粉的组成设计 328
7.5模具磨损和润滑对G3合金热挤压工艺的作用规律 336
7.5.1润滑良好的模具磨损行为 336
7.5.2基于模具最高工作温度的热挤压工艺参数选择 340
7.5.3润滑效果对热挤压工艺的影响规律 342
参考文献 344
8热挤压工艺与组织控制 346
8.1 G3合金组织演变模型的验证 347
8.2热挤压工艺参数对G3合金管材内部晶粒的影响 351
8.2.1坯料预热温度 351
8.2.2挤压速度 353
8.2.3圆角半径和模具预热温度 354
8.2.4初始晶粒尺寸 355
8.3 G3合金管材热挤压工艺参数选择 357
8.3.1热挤压工艺参数选择准则 357
8.3.2 G3合金热挤压工艺参数选择 359
8.4 690合金热变形过程组织演变模型验证 361
8.4.1 690合金热压缩实验条件下的验证 361
8.4.2模型外推验证 364
8.4.3热挤压过程组织演变模拟的可行性 364
8.4.4用户定义子程序的开发 366
8.4.5热挤压变形的有限元模型 368
8.4.6热挤压组织预测可行性分析 370
8.5热挤压工艺参数对荒管晶粒组织的影响 372
8.5.1操作工艺参数 372
8.5.2模具尺寸因素 376
8.5.3摩擦润滑工艺条件 377
8.5.4其他因素 378
参考文献 381
9 690合金冷轧退火组织控制及管材组织可控性 382
9.1冷轧及退火处理工艺组织演变研究方案 382
9.2冷加工对组织和硬度的影响规律 386
9.2.1冷加工对显微组织的影响 387
9.2.2冷加工对硬度的影响 388
9.3退火处理工艺对组织和硬度的影响规律 388
9.3.1退火处理工艺对晶粒尺寸的影响 389
9.3.2退火处理工艺对碳化物回溶的影响 393
9.3.3退火处理工艺对硬度的影响 394
9.3.4退火再结晶晶粒长大模型 395
9.4基于组织均匀性的冷轧退火处理工艺优化 398
9.4.1组织均匀性研究方法 399
9.4.2单道次冷轧退火后的组织均匀性 401
9.4.3双道次冷轧退火后的组织均匀性 404
9.5组织可控传热管关键生产工艺优化 410
9.5.1组织可控的热挤压工艺参数优化 411
9.5.2组织可控的冷轧退火处理工艺参数优化 414
参考文献 417
- 《高含硫气藏开发腐蚀控制技术与实践》唐永帆,张强 2018
- 《钢铁行业污染特征与全过程控制技术研究》周长波等 2019
- 《组织学与胚胎学习题集 第3版》周忠光主编;刘黎青,汪涛,李健副主编 2019
- 《生活垃圾焚烧飞灰中典型污染物控制技术》朱芬芬等编著 2019
- 《钢铁烧结烟气多污染物过程控制原理与新技术》甘敏,范晓慧著 2019
- 《形态学实验 组织学与胚胎学分册》郝利铭,邓香群 2018
- 《真菌毒素控制集成解决方案 第二届MycoKey国际真菌毒素大会论文集》冯洁 2018
- 《动物解剖学及组织胚胎学》陈耀星,崔燕主编 2018
- 《医疗机构内新型冠状病毒感染预防与控制相关流程》河南省卫生健康委员会编写 2020
- 《静电纺纳米纤维与组织再生》莫秀梅主编 2019
- 《极简社交》王励新著 2020
- 《数学家画传 吴文俊》蔡天新著 2019
- 《精进思维》柏从新著 2019
- 《没有凋谢的玫瑰》何礼新著 2019
- 《所有遗憾,都是对未来的成全》小新著 2019
- 《孔子的智慧 何新讲《论语》》何新著 2019
- 《柔弱胜刚强 何新讲《老子》》何新著 2019
- 《旗人老舍的文化解析》关纪新著 2019
- 《26城记》蔡天新著 2019
- 《钢琴调律与维修技术=GANGQIN TIAOLU YU WEIXIU JISHU》董建华编著 2019
- 《指向核心素养 北京十一学校名师教学设计 英语 七年级 上 配人教版》周志英总主编 2019
- 《北京生态环境保护》《北京环境保护丛书》编委会编著 2018
- 《指向核心素养 北京十一学校名师教学设计 英语 九年级 上 配人教版》周志英总主编 2019
- 《高等院校旅游专业系列教材 旅游企业岗位培训系列教材 新编北京导游英语》杨昆,鄢莉,谭明华 2019
- 《中国十大出版家》王震,贺越明著 1991
- 《近代民营出版机构的英语函授教育 以“商务、中华、开明”函授学校为个案 1915年-1946年版》丁伟 2017
- 《新工业时代 世界级工业家张毓强和他的“新石头记”》秦朔 2019
- 《智能制造高技能人才培养规划丛书 ABB工业机器人虚拟仿真教程》(中国)工控帮教研组 2019
- 《陶瓷工业节能减排技术丛书 陶瓷工业节能减排与污染综合治理》罗民华著 2017
- 《全国职业院校工业机器人技术专业规划教材 工业机器人现场编程》(中国)项万明 2019