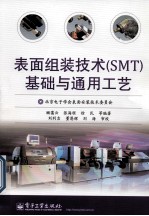
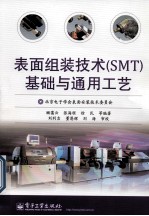
表面组装技术(SMT)基础及通用工艺PDF电子书下载
- 电子书积分:14 积分如何计算积分?
- 作 者:顾霭云等编著
- 出 版 社:北京:电子工业出版社
- 出版年份:2014
- ISBN:9787121219689
- 页数:429 页
上篇 表面组装技术(SMT)基础与可制造性设计(DFM) 3
第1章 表面组装元器件(SMC/SMD) 3
1.1 对SMC/SMD的基本要求及无铅焊接对元器件的要求 3
1.2 SMC的封装命名及标称 4
1.3 SMD的封装命名 5
1.4 SMC/SMD的焊端结构 6
1.5 SMC/SMD的包装类型 7
1.6 SMC/SMD与静电敏感元器件(SSD)的运输、存储、使用要求 8
1.7 湿度敏感器件(MSD)的管理、存储、使用要求 9
1.8 SMC/SMD方向发展 10
思考题 12
第2章 表面组装印制电路板(SMB) 14
2.1 印制电路板 14
2.1.1 印制电路板的定义和作用 14
2.1.2 常用印制电路板的基板材料 14
2.1.3 评估PCB基材质量的相关参数 15
2.2 SMT对表面组装印制电路的一些要求 16
2.2.1 SMT对印制电路板的总体要求 16
2.2.2 表面组装PCB材料的选择 17
2.2.3 无铅焊接用FR-4特性 17
2.3 PCB焊盘表面涂(镀)层及无铅PCB焊盘涂镀层的选择 17
2.3.1 PCB焊盘表面涂(镀)层 17
2.3.2 无铅PCB焊盘涂镀层的选择 19
2.4 当前国际先进印制电路板及其制造技术的发展动向 21
思考题 22
第3章 表面组装工艺材料 23
3.1 锡铅焊料合金 24
3.1.1 锡的基本物理和化学特性 24
3.1.2 铅的基本物理和化学特性 26
3.1.3 63Sn-37Pb锡铅共晶合金的基本特性 26
3.1.4 铅在焊料中的作用 27
3.1.5 锡铅合金中的杂质及其影响 27
3.2 无铅焊料合金 28
3.2.1 对无铅焊料合金的要求 28
3.2.2 目前最有可能替代Sn-Pb焊料的合金材料 29
3.2.3 目前应用最多的无铅焊料合金 32
3.2.4 Sn-Ag-Cu系焊料的最佳成分 33
3.2.5 继续研究更理想的无铅焊料 33
3.3 助焊剂 33
3.3.1 对助焊剂物理和化学特性的要求 33
3.3.2 助焊剂的分类和组成 34
3.3.3 助焊剂的作用 36
3.3.4 四类常用助焊剂 37
3.3.5 助焊剂的选择 38
3.3.6 无铅助焊剂的特点、问题与对策 39
3.4 焊膏 39
3.4.1 焊膏的技术要求 39
3.4.2 焊膏的分类 40
3.4.3 焊膏的组成 40
3.4.4 影响焊膏特性的主要参数 42
3.4.5 焊膏的选择 44
3.4.6 焊膏的检测与评估 45
3.4.7 焊膏的发展动态 46
3.5 焊料棒和丝状焊料 46
3.6 贴片胶(粘结剂) 47
3.6.1 常用贴片胶 47
3.6.2 贴片胶的选择方法 47
3.6.3 贴片胶的存储、使用工艺要求 48
3.7 清洗剂 48
3.7.1 对清洗剂的要求 48
3.7.2 清洗剂的种类 49
3.7.3 有机溶剂清洗剂的性能要求 49
3.7.4 清洗效果的评价方法与标准 49
思考题 50
第4章 SMT生产线及主要设备 51
4.1 SMT生产线 51
4.2 印刷机 52
4.3 点胶机 54
4.4 贴装机 55
4.4.1 贴装机的分类 55
4.4.2 贴装机的基本结构 57
4.4.3 贴装头 58
4.4.4 X、 Y与Z/θ的传动定位(伺服)系统 60
4.4.5 贴装机对中定位系统 61
4.4.6 传感器 63
4.4.7 送料器 64
4.4.8 吸嘴 66
4.4.9 贴装机的主要易损件 66
4.4.10 贴装机的主要技术指标 67
4.4.11 贴装机的发展方向 68
4.5 再流焊炉 69
4.5.1 再流焊炉的分类 69
4.5.2 全热风再流焊炉的基本结构与性能 70
4.5.3 再流焊炉的主要技术指标 72
4.5.4 再流焊炉的发展方向 73
4.5.5 气相再流焊(VPS)炉的新发展 73
4.6 波峰焊机 74
4.6.1 波峰焊机的种类 74
4.6.2 双波峰焊机的基本结构 74
4.6.3 波峰焊机的主要技术参数 76
4.6.4 波峰焊机的发展方向及无铅焊接对波峰焊设备的要求 77
4.6.5 选择性波峰焊机 77
4.7 检测设备 79
4.7.1 自动光学检查设备(AOI) 80
4.7.2 自动X射线检查设备(AXI) 82
4.7.3 在线测试设备 84
4.7.4 功能测试设备 85
4.7.5 锡膏检查设备(SPI) 85
4.7.6 三次元影像测量仪 86
4.8 手工焊接与返修设备 87
4.8.1 电烙铁 87
4.8.2 焊接机器人和非接触式焊接机器人 90
4.8.3 SMD返修系统 90
4.8.4 手工贴片工具 92
4.9 清洗设备 93
4.9.1 超声清洗设备 93
4.9.2 气相清洗设备 93
4.9.3 水清洗设备 94
4.10 选择性涂覆设备 94
4.11 其他辅助设备 95
思考题 95
第5章 SMT印制电路板的可制造性设计(DFM) 97
5.1 不良设计在SMT生产中的危害 97
5.2 国内SMT印制电路板设计中普遍存在的问题及解决措施 98
5.2.1 SMT印制电路板设计中的常见问题举例 98
5.2.2 消除不良设计、实现DFM的措施 101
5.3 编制本企业可制造性设计规范文件 101
5.4 PCB设计包含的内容及可制造性设计实施程序 101
5.5 SMT工艺对设计的要求 105
5.5.1 表面贴装元器件(SMC/SMD)焊盘设计 106
5.5.2 通孔插装元器件(THC)焊盘设计 126
5.5.3 布线设计 128
5.5.4 焊盘与印制导线连接的设置 129
5.5.5 导通孔的设置 130
5.5.6 测试孔和测试盘设计——可测试性设计DFT (Design for Testability) 131
5.5.7 阻焊、丝网的设置 133
5.5.8 元器件整体布局设置 133
5.5.9 再流焊与波峰焊贴片元件的排列方向设计 135
5.5.10 元器件最小间距设计 137
5.5.11 模板设计 137
5.6 SMT设备对设计的要求 140
5.6.1 PCB外形、尺寸设计 140
5.6.2 PCB定位孔和夹持边的设置 141
5.6.3 基准标志(Mark)设计 142
5.6.4 拼板设计 143
5.6.5 PCB设计的输出文件 144
5.7 印制电路板可靠性设计 145
5.7.1 散热设计简介 145
5.7.2 电磁兼容性(高频及抗电磁干扰)设计简介 146
5.8 无铅产品PCB设计 148
5.9 PCB可加工性设计 149
5.10 SMT产品设计评审和印制电路板可制造性设计审核 149
5.10.1 SMT产品设计评审 149
5.10.2 SMT印制电路板可制造性设计审核 150
5.11 IPC-7351《表面贴装设计和焊盘图形标准通用要求》简介 154
思考题 158
下篇 表面组装技术(SM)通用工艺 161
第6章 表面组装工艺条件 161
6.1 厂房承重能力、振动、噪声及防火防爆要求 161
6.2 电源、气源、排风、烟气排放及废弃物处理、照明、工作环境 161
6.3 SMT制造中的静电防护技术 162
6.3.1 防静电基础知识 163
6.3.2 国际静电防护协会推荐的6个原则 170
6.3.3 高密度组装对防静电的新要求 170
6.3.4 IPC推荐的电子组装件操作的习惯做法 170
6.3.5 手工焊接中防静电的一般要求和防静电措施 171
6.4 对SMT生产线设备、仪器、工具的要求 172
6.5 SMT制造中的工艺控制与质量管理 173
6.5.1 SMT制造中的工艺控制 173
6.5.2 SMT制造中的质量管理 176
6.5.3 SPC和六西格玛质量管理理念简介 177
思考题 178
第7章 典型表面组装方式及其工艺流程 179
7.1 典型表面组装方式 179
7.2 纯表面组装工艺流程 180
7.3 表面组装和插装混装工艺流程 180
7.4 工艺流程的设计原则 181
7.5 选择表面组装工艺流程应考虑的因素 181
7.6 表面组装工艺的发展 181
思考题 182
第8章 施加焊膏通用工艺 183
8.1 施加焊膏技术要求 183
8.2 焊膏的选择和正确使用 184
8.3 施加焊膏的方法 184
8.4 印刷焊膏的原理 185
8.5 印刷机金属模板印刷焊膏工艺 186
8.6 影响印刷质量的主要因素 189
8.7 印刷焊膏的主要缺陷与不良品的判定和调整方法 194
8.8 印刷机安全操作规程及设备维护 195
8.9 手动滴涂焊膏工艺介绍 195
8.10 SMT不锈钢激光模板制作外协程序及工艺要求 196
思考题 199
第9章 施加贴片胶通用工艺 200
9.1 施加贴片胶的技术要求 200
9.2 施加贴片胶的方法和工艺参数的控制 201
9.2.1 针式转印法 201
9.2.2 印刷法 201
9.2.3 压力注射法 203
9.3 施加贴片胶的工艺流程 206
9.4 贴片胶固化 206
9.4.1 热固化 206
9.4.2 光固化 207
9.5 施加贴片胶检验、清洗、返修 207
9.6 点胶中常见的缺陷与解决方法 208
思考题 209
第10章 自动贴装机贴片通用工艺 210
10.1 贴装元器件的工艺要求 210
10.2 全自动贴装机贴片工艺流程 212
10.3 贴装前准备 213
10.4 开机 213
10.5 编程 213
10.5.1 离线编程 215
10.5.2 在线编程 217
10.6 安装供料器 219
10.7 做基准标志(Mark)和元器件的视觉图像 219
10.8 首件试贴并检验 221
10.9 根据首件试贴和检验结果调整程序或重做视觉图像 221
10.10 连续贴装生产 222
10.11 检验 222
10.12 转再流焊工序 223
10.13 提高自动贴装机的贴装效率 223
10.14 生产线多台贴片机的任务平衡 223
10.15 贴片故障分析及排除方法 224
10.16 贴装机的设备维护和安全操作规程 227
10.17 手工贴装工艺介绍 230
思考题 231
第11章 再流焊通用工艺 232
11.1 再流焊的工艺目的和原理 232
11.2 再流焊的工艺要求 233
11.3 再流焊的工艺流程 233
11.4 焊接前准备 234
11.5 开炉 234
11.6 编程(设置温度、速度等参数)或调程序 234
11.7 测试实时温度曲线 235
11.7.1 温度曲线测量、分析系统 235
11.7.2 实时温度曲线的测试方法和步骤 236
11.7.3 BGA/CSP、QFN实时温度曲线的测试方法 237
11.8 正确设置、分析与优化再流焊温度曲线 238
11.8.1 设置最佳(理想)的温度曲线 238
11.8.2 正确分析与优化再流焊温度曲线 238
11.9 首件表面组装板焊接与检测 240
11.10 连续焊接 240
11.11 检测 241
11.12 停炉 241
11.13 注意事项与紧急情况处理 241
11.14 再流焊炉的安全操作规程 242
11.15 双面再流焊工艺控制 242
11.16 双面贴装BGA工艺 243
11.17 常见再流焊焊接缺陷、原因分析及预防和解决措施 244
11.17.1 再流焊的工艺特点 244
11.17.2 影响再流焊质量的原因分析 244
11.17.3 SMT再流焊中常见的焊接缺陷分析与预防对策 246
11.18 再流焊炉的设备维护 254
思考题 254
第12章 通孔插装元件再流焊工艺(PIHR)介绍 256
12.1 通孔插装元件再流焊工艺的优点及应用 256
12.2 通孔插装元件再流焊工艺对设备的特殊要求 257
12.3 通孔插装元件再流焊工艺对元件的要求 257
12.4 通孔插装元件焊膏量的计算 257
12.5 通孔插装元件的焊盘设计 258
12.6 通孔插装元件的模板设计 258
12.7 施加焊膏工艺 259
12.8 插装工艺 263
12.9 再流焊工艺 263
12.10 焊点检测 264
思考题 264
第13章 波峰焊通用工艺 265
13.1 波峰焊原理 265
13.2 波峰焊工艺对元器件和印制板的基本要求 268
13.3 波峰焊的设备、工具及工艺材料 269
13.3.1 设备、工具 269
13.3.2 工艺材料 269
13.4 波峰焊的工艺流程和操作步骤 270
13.5 波峰焊工艺参数控制要点 272
13.6 无铅波峰焊工艺控制 275
13.7 无铅波峰焊必须预防和控制Pb污染 277
13.8 波峰焊机安全技术操作规程 277
13.9 影响波峰焊质量的因素与波峰焊常见焊接缺陷分析及预防对策 278
13.9.1 影响波峰焊质量的因素 278
13.9.2 波峰焊常见焊接缺陷的原因分析及预防对策 279
思考题 287
第14章 手工焊、修板和返修工艺 288
14.1 手工焊接基础知识 288
14.2 表面贴装元器件(SMC/SMD)手工焊工艺 291
14.2.1 两个端头无引线片式元件的手工焊接方法 292
14.2.2 翼形引脚元件的手工焊接方法 293
14.2.3 J形引脚元件的手工焊接方法 294
14.3 表面贴装元器件修板与返修工艺 294
14.3.1 虚焊、桥接、拉尖、不润湿、焊料量少、焊膏未熔化等焊点缺陷的修整 295
14.3.2 Chip元件立碑、元件移位的修整 295
14.3.3 三焊端的电位器、SOT、 SOP、 SOJ移位的返修 296
14.3.4 QFP和PLCC表面组装器件移位的返修 297
14.3.5 BGA的返修和置球工艺 297
14.4 无铅手工焊接和返修技术 302
14.5 手工焊接、返修质量的评估和缺陷的判断 303
思考题 303
第15章 表面组装板焊后清洗工艺 304
15.1 清洗机理 305
15.2 表面组装板焊后有机溶剂清洗工艺 306
15.2.1 超声波清洗 306
15.2.2 气相清洗 308
15.3 非ODS清洗介绍 309
15.3.1 免清洗技术 309
15.3.2 有机溶剂清洗 311
15.3.3 水洗技术 311
15.3.4 半水清洗技术 311
15.4 水清洗和半水清洗的清洗过程 311
15.5 无铅焊后清洗 312
15.6 清洗后的检验 312
思考题 313
第16章 表面组装检验(检测)工艺 314
16.1 组装前的检验(或称来料检测) 314
16.1.1 表面组装元器件(SMC/SMD)检验 315
16.1.2 印制电路板(PCB)检验 315
16.1.3 工艺材料检验 315
16.2 工序检验(检测) 316
16.2.1 印刷焊膏工序检验 316
16.2.2 贴装工序检验(包括机器贴装和手工贴装) 317
16.2.3 再流焊工序检验(焊后检验) 317
16.2.4 清洗工序检验 318
16.3 表面组装板检验 318
16.4 自动光学检测(AOI) 319
16.4.1 AOI在SMT中的作用 319
16.4.2 AOI编程 320
16.5 自动X射线检测(AXI) 320
16.5.1 X射线评估和判断BGA、 CSP焊点缺陷的标准 320
16.5.2 X射线检测BGA、 CSP焊点图像的评估和判断及其他应用 321
16.6 美国电子装联协会《电子组装件验收标准IPC-A-610E》简介 323
16.6.1 IPC-A-610概述 324
16.6.2 IPC-A-610E简介 325
思考题 326
第17章 电子组装件三防涂覆工艺 327
17.1 环境对电子设备的影响 327
17.2 三防设计的基本概念 327
17.3 三防涂覆材料 328
17.4 电子组装件新型防护技术——选择性涂覆工艺 330
17.4.1 工艺流程 330
17.4.2 选择性涂覆工艺 331
17.4.3 印制电路板和组装件敷形涂覆的质量检测 333
思考题 335
第18章 运用焊接理论正确设置无铅再流焊温度曲线 336
18.1 概述 336
18.2 锡焊(钎焊)机理 337
18.2.1 钎焊过程中助焊剂与金属表面(母材)、熔融焊料之间的相互作用 337
18.2.2 熔融焊料与焊件(母材)表面之间的反应 338
18.2.3 钎缝的金相组织 343
18.3 焊点强度、连接可靠性分析 344
18.4 如何获得理想的界面组织 345
18.5 无铅焊接机理 345
18.6 Sn-Ag-Cu焊料与不同材料的金属焊接时的界面反应和钎缝组织 347
18.6.1 无铅焊料合金、元器件焊端镀层材料、PCB焊盘表面镀层三要素 347
18.6.2 焊料合金元素与各种金属电极焊接后在界面形成的化合物 348
18.6.3 Sn系焊料与Ni/Au (ENIG)焊盘焊接的界面反应和钎缝组织 348
18.6.4 Sn系焊料与42号合金钢(Fe-42Ni合金)焊接的界面反应和钎缝组织 349
18.7 运用焊接理论正确设置无铅再流焊温度曲线 350
18.7.1 以焊接理论为指导、分析再流焊的焊接机理 350
18.7.2 影响钎缝(金属间结合层)质量与厚度的因素 351
18.7.3 运用焊接理论正确设置无铅再流焊温度曲线 353
18.7.4 几种典型的温度曲线 357
思考题 359
第19章 无铅焊接可靠性讨论及无铅再流焊工艺控制 360
19.1 无铅焊接可靠性讨论 360
19.2 无铅再流焊的特点及对策 364
19.3 如何正确实施无铅工艺 365
19.4 无铅再流焊工艺控制 371
19.4.1 三种无铅再流焊温度曲线 372
19.4.2 无铅再流焊工艺控制 372
思考题 376
第20章 有铅、无铅混装再流焊工艺控制 377
20.1 有铅、无铅混装制程分析 377
20.1.1 再流焊工艺中无铅焊料与有铅元件混装 377
20.1.2 再流焊工艺中有铅焊料与无铅元件混装 380
20.1.3 再流焊工艺中有铅焊料焊接有铅和无铅元器件的混装工艺 381
20.2 有铅焊料与有铅、无铅元件混装工艺必须考虑相容性问题 382
20.2.1 材料相容性 382
20.2.2 工艺相容性 383
20.2.3 设计相容性 383
20.3 有铅焊料与有铅、无铅元件混装工艺质量控制方案的建议 384
思考题 387
第21章 其他工艺和新技术介绍 388
21.1 0201、 01005的印刷与贴装技术 388
21.1.1 0201、 01005的焊膏印刷技术 388
21.1.2 0201、01005的贴装技术 389
21.2 PQFN的印刷、贴装与返修工艺 391
21.2.1 PQFN的印刷和贴装 391
21.2.2 PQFN的返修工艺 393
21.3 COB技术 393
21.4 倒装芯片FC (Flip Chip)与晶圆级CSP (WL-CSP)、WLP (Wafer Level Processing)的组装技术 396
21.5 倒装芯片(Flip Chip)、晶圆级CSP和CSP底部填充工艺 400
21.6 三维堆叠POP (Package On Package)技术 404
21.7 ACA、 ACF与ESC技术 408
21.7.1 ACA、ACF技术 408
21.7.2 ESC技术 410
21.8 FPC的应用与发展 410
21.9 LED应用的迅速发展 412
21.10 PCBA无焊压入式连接技术 413
21.11 无焊料电子装配工艺——Occam倒序互连工艺介绍 418
思考题 420
附录A SMT常用缩略语、术语、金属元素中英文名称及物理性能表 421
参考文献 428
- 《葡萄酒工艺与鉴赏 第3版》廖祖宋 2019
- 《化学工程与工艺专业实验指导》郭跃萍主编 2019
- 《美物之道 日本手工艺》(日)柳宗悦著 2019
- 《新课标初中英语词汇同步速记 八年级 上 通用版》蔡波主编 2018
- 《通用安装工程消耗量定额 TY02-31-2015 第4册 电气设备安装工程》中华人民共和国住房和城乡建设部 2015
- 《小荧星艺术学校通用教程 流行舞初级教程》沈莹 2019
- 《有色金属冶金新工艺与新技术》俞娟,王斌,方钊,崔雅茹,袁艳 2019
- 《洗涤剂生产工艺与技术》宋小平,韩长日主编 2019
- 《皮革用化学品生产工艺与技术》宋小平,韩长日著 2018
- 《玉米淀粉绿色精益制造 新工艺、新设备、新理念》佟毅 2018
- 《市政工程基础》杨岚编著 2009
- 《家畜百宝 猪、牛、羊、鸡的综合利用》山西省商业厅组织技术处编著 1959
- 《《道德经》200句》崇贤书院编著 2018
- 《高级英语阅读与听说教程》刘秀梅编著 2019
- 《计算机网络与通信基础》谢雨飞,田启川编著 2019
- 《看图自学吉他弹唱教程》陈飞编著 2019
- 《法语词汇认知联想记忆法》刘莲编著 2020
- 《培智学校义务教育实验教科书教师教学用书 生活适应 二年级 上》人民教育出版社,课程教材研究所,特殊教育课程教材研究中心编著 2019
- 《国家社科基金项目申报规范 技巧与案例 第3版 2020》文传浩,夏宇编著 2019
- 《流体力学》张扬军,彭杰,诸葛伟林编著 2019
- 《电子测量与仪器》人力资源和社会保障部教材办公室组织编写 2009
- 《少儿电子琴入门教程 双色图解版》灌木文化 2019
- 《指向核心素养 北京十一学校名师教学设计 英语 七年级 上 配人教版》周志英总主编 2019
- 《北京生态环境保护》《北京环境保护丛书》编委会编著 2018
- 《指向核心素养 北京十一学校名师教学设计 英语 九年级 上 配人教版》周志英总主编 2019
- 《通信电子电路原理及仿真设计》叶建芳 2019
- 《高等院校旅游专业系列教材 旅游企业岗位培训系列教材 新编北京导游英语》杨昆,鄢莉,谭明华 2019
- 《电子应用技术项目教程 第3版》王彰云 2019
- 《中国十大出版家》王震,贺越明著 1991
- 《近代民营出版机构的英语函授教育 以“商务、中华、开明”函授学校为个案 1915年-1946年版》丁伟 2017