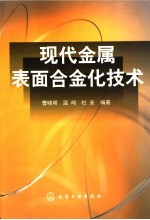
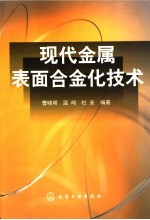
现代金属表面合金化技术PDF电子书下载
- 电子书积分:13 积分如何计算积分?
- 作 者:曹晓明,温鸣,杜安编著
- 出 版 社:北京:化学工业出版社
- 出版年份:2007
- ISBN:7502598812
- 页数:372 页
第1章 绪论 1
1.1 概述 1
1.2 金属表面合金化分类 2
1.3 金属表面合金化的功能 3
参考文献 4
第2章 金属表面合金化 5
2.1 固体表面 5
2.1.1 理想的固体表面 5
2.1.2 实际晶体表面 6
2.2 金属表面原子扩散 10
2.2.1 微观扩散的扩散系数 11
2.2.2 宏观扩散的扩散系数 12
2.2.3 表面向体内的扩散 13
2.3 金属磨损理论 14
2.3.1 磨损的分类 15
2.3.2 磨损特征及一般规律 17
2.4 金属腐蚀理论 19
2.4.1 金属腐蚀的分类 20
2.4.2 金属的常见腐蚀形态及防护措施 21
2.4.3 电化学腐蚀热力学 27
2.4.4 电化学腐蚀动力学 29
参考文献 33
第3章 热渗镀 34
3.1 热渗镀技术的基本原理 34
3.1.1 渗层形成的基本条件 34
3.1.2 渗层的形成机理 36
3.1.3 渗层的组织特征 37
3.1.4 渗层形成速度的影响因素 38
3.2 热渗镀工艺的分类 39
3.2.1 气态热渗镀工艺 40
3.2.2 液态热渗镀工艺 41
3.2.3 固态热渗镀工艺 46
3.2.4 等离子体热渗镀工艺 47
3.2.5 热渗镀的发展 51
3.3 渗碳 51
3.3.1 渗碳原理 51
3.3.2 气态渗碳 53
3.3.3 液体渗碳 63
3.3.4 固体渗碳 67
3.3.5 膏剂渗碳 70
3.3.6 离子渗碳及其他渗碳方法简介 71
3.3.7 常用渗碳钢的性能及应用 73
3.4 渗氮 75
3.4.1 渗氮的原理 75
3.4.2 气体渗氮 78
3.4.3 离子渗氮 83
3.4.4 其他渗氮方法 91
3.5 渗硼 93
3.5.1 渗硼方法 93
3.5.2 固体法渗硼 94
3.5.3 液体渗硼 99
3.5.4 气体渗硼 101
3.5.5 渗硼的前处理和后处理 102
3.5.6 渗硼钢的组织与性能 103
3.5.7 渗硼钢的用途 106
3.6 渗硅 108
3.6.1 固体渗硅 109
3.6.2 液体渗硅 112
3.6.3 气体渗硅 113
3.6.4 离子渗硅 115
3.6.5 有色金属渗硅 115
3.6.6 渗硅的影响因素 116
3.6.7 渗硅层的性能及应用 117
3.7 渗锌 119
3.7.1 固体粉末渗锌 120
3.7.2 热浸镀锌 124
3.8 渗铝 140
3.8.1 渗铝层的形成 142
3.8.2 固体渗铝 143
3.8.3 热浸镀铝 145
3.8.4 其他渗铝方法 156
3.8.5 渗铝层的性能 159
3.9.1 渗铬 163
3.9 渗其他金属 163
3.9.2 渗钛 172
3.9.3 渗钒 175
3.9.4 渗锰、渗锡、渗铌、渗钼、渗钽、渗镉 177
3.10 多元共渗和复合渗 180
3.10.1 碳氮共渗 181
3.10.2 硼铝共渗 192
3.10.3 硼铬共渗 195
3.10.4 硼硅共渗 197
3.10.5 硼锆共渗 198
3.10.6 硼碳氮三元共渗 198
3.10.7 铬铝共渗 199
3.10.9 钛铝共渗 201
3.10.8 铬钒共渗 201
3.10.10 铝硅共渗 202
3.10.11 铝与稀土元素共渗 203
3.10.12 碳硼复合渗 203
3.10.13 氮硼复合渗 204
参考文献 206
4.1 概述 207
4.1.1 堆焊的特点 207
第4章 堆焊 207
4.1.2 堆焊的分类 208
4.1.3 堆焊的用途 209
4.1.4 堆焊的应用现状及前景 210
4.2 手工电弧堆焊 211
4.2.1 手工电弧堆焊的特点 211
4.2.2 手工电弧堆焊的原理 212
4.2.3 手工电弧堆焊设备 215
4.2.4 手工电弧堆焊工艺 218
4.2.5 手工电弧堆焊应用实例 222
4.3.2 氧-乙炔火焰堆焊装置 224
4.3.1 氧-乙炔火焰堆焊的特点 224
4.3 氧-乙炔火焰堆焊方法及工艺 224
4.3.3 氧-乙炔火焰堆焊应用实例 225
4.4 等离子弧堆焊 227
4.4.1 等离子弧堆焊的特点 227
4.4.2 等离子弧堆焊原理 228
4.4.3 等离子弧堆焊工艺 229
4.4.4 等离子弧堆焊实例 230
4.5 振动电弧堆焊 232
4.5.1 振动电弧堆焊特点 232
4.5.2 振动电弧堆焊的原理 232
4.5.3 振动电弧堆焊的设备 233
4.5.4 振动电弧堆焊实例 234
4.6 埋弧自动堆焊 235
4.6.1 埋弧自动堆焊的特点 236
4.6.2 埋弧自动堆焊的设备 236
4.6.3 埋弧自动堆焊工艺参数 238
4.6.4 埋弧自动堆焊实例 240
4.7 气体保护堆焊 241
4.7.1 气体保护堆焊原理 241
4.7.2 气体保护堆焊的种类 242
4.8.1 电渣堆焊的特点 245
4.8 电渣堆焊 245
4.8.3 电渣堆焊工艺 246
4.8.2 电渣堆焊的设备与材料 246
4.8.4 电渣堆焊的应用与实例 247
参考文献 249
第5章 气相沉积技术 250
5.1 薄膜技术基础 251
5.1.1 薄膜的定义和基本性质 251
5.1.2 薄膜的形成过程 252
5.1.3 薄膜的种类和应用 253
5.1.4 薄膜的制备方法 255
5.2.1 真空蒸镀 256
5.2 物理气相沉积 256
5.2.2 溅射镀膜 266
5.2.3 离子镀膜 279
5.3 化学气相沉积 296
5.3.1 化学气相沉积原理 296
5.3.2 CVD设备及工艺 298
5.3.3 化学气相沉积技术 303
5.3.4 化学气相沉积的应用 312
参考文献 315
6.1.1 高能束技术 316
第6章 高能束技术 316
6.1 高能束技术基础 316
6.1.2 高能束与金属材料的交互作用 317
6.1.3 高能束处理技术的特点 325
6.2 激光表面合金化与激光熔覆 327
6.2.1 激光表面处理简介 327
6.2.2 激光表面合金化 329
6.2.3 激光表面熔覆 345
6.3 离子注入 350
6.3.1 离子注入原理与特点 350
6.3.2 离子注入工艺 353
6.3.3 离子注入的应用 357
6.3.4 离子注入技术发展动向 360
6.4 电子束技术 361
6.4.1 电子束表面改性原理及特点 361
6.4.2 电子束表面改性工艺及应用 363
6.5 聚焦光束表面改性 367
6.5.1 概述 367
6.5.2 聚焦光束表面改性技术及应用 369
参考文献 372
- 《有色金属冶金新工艺与新技术》俞娟,王斌,方钊,崔雅茹,袁艳 2019
- 《过渡金属氧化物在环境保护中的应用》贾瑛,许国根,侯立安 2016
- 《蔬菜重金属控制原理与方法》徐卫红著 2019
- 《有色金属冶金学实验教程》李继东编著 2019
- 《铸造手册大全 金属铸造工艺、冶金技术和设计 第6册 熔炼·造型·铸造·凝固》John Campbell主编 2018
- 《金属类催化剂的密度泛函理论研究实例》任翠霞责任编辑;任瑞鹏 2019
- 《果园土壤重金属镉污染与植物修复》林立金,廖明安主编 2019
- 《金属有机骨架材料制备及其应用》葛金龙主编 2019
- 《中国近海重金属环境质量现状与污染风险评价》暨卫东,陈泓哲 2019
- 《高比表面积碳化硅》郭向云编著 2019
- 《市政工程基础》杨岚编著 2009
- 《家畜百宝 猪、牛、羊、鸡的综合利用》山西省商业厅组织技术处编著 1959
- 《《道德经》200句》崇贤书院编著 2018
- 《高级英语阅读与听说教程》刘秀梅编著 2019
- 《计算机网络与通信基础》谢雨飞,田启川编著 2019
- 《看图自学吉他弹唱教程》陈飞编著 2019
- 《法语词汇认知联想记忆法》刘莲编著 2020
- 《培智学校义务教育实验教科书教师教学用书 生活适应 二年级 上》人民教育出版社,课程教材研究所,特殊教育课程教材研究中心编著 2019
- 《国家社科基金项目申报规范 技巧与案例 第3版 2020》文传浩,夏宇编著 2019
- 《流体力学》张扬军,彭杰,诸葛伟林编著 2019