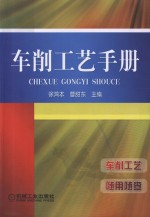
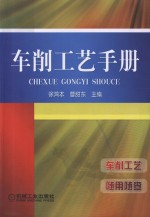
车削工艺手册PDF电子书下载
- 电子书积分:19 积分如何计算积分?
- 作 者:徐鸿本,曹甜东主编
- 出 版 社:北京:机械工业出版社
- 出版年份:2011
- ISBN:9787111352082
- 页数:676 页
第1章 车床 1
1.1金属切削机床型号编制方法 1
1.1.1通用机床型号表示方法 1
1.1.2机床的分类及类代号 1
1.1.3机床的特性代号 1
1.1.4机床的组、系代号 2
1.1.5机床的主参数 4
1.1.6机床的重大改进顺序号 4
1.1.7车床型号示例 4
1.2常用卧式车床型号与技术参数 4
1.3普通车床的结构与传动系统 6
1.3.1卧式车床主要组成部分的名称和用途 6
1.3.2车床传动系统图 7
1.主轴传动系统 7
2.进给传动系统 9
1.4车床加工的基本工艺特点、范围及经济精度 16
1.4.1车床加工的基本工艺特点及工艺范围 16
1.4.2车床加工的经济精度与表面粗糙度 17
1.5车床精度对工件加工质量的影响 21
1.5.1车床精度的项目与内容 21
1.5.2车床工作精度的检验 25
1.5.3车床精度对加工质量的影响及消除方法 25
1.6车床精度的调整 28
1.6.1车床主要部件的调整 28
1.6.2车削高精度工件车床的调整 31
1.6.3强力车削车床的调整 32
1.7车床的操纵与安全机构 32
1.7.1车床的操纵机构 32
1.7.2车床的安全机构 34
1.8车床的维护保养与合理润滑 36
1.8.1车床一级保养的内容 36
1.8.2车床的二级保养 37
1.8.3车床的合理润滑 37
1.9车床的安全操作 38
1.9.1切削加工通用工艺守则 38
1.9.2车削加工通用工艺守则 40
1.9.3车床的安全操作规程 40
第2章 车床常用刀具 42
2.1常用刀具材料 42
2.1.1刀具材料必须具备的性能 42
2.1.2常用刀具材料的性能及选用 42
1.高速钢 42
2.硬质合金 42
3.陶瓷 50
4.金刚石 50
5.立方氮化硼 52
2.2刀具几何角度及其选择 52
2.2.1刀具的几何角度 52
2.2.2刀具几何角度的选择 52
2.3车刀 59
2.3.1车刀的种类、用途与结构 59
1.车刀的种类与用途 59
2.车刀的结构 60
2.3.2高速钢车刀条 61
2.3.3焊接车刀 62
2.3.4机械夹固式车刀 81
1.硬质合金机械夹固式车刀的特点与夹压方式 81
2.机械夹固式切断车刀与螺纹车刀 81
2.3.5可转位车刀 87
1.可转位硬质合金刀片的标记方法 87
2.可转位硬质合金刀片的型号与基本参数 90
3.可转位陶瓷刀片的形状与基本参数 91
4.可转位硬质合金刀片的选择 117
5.可转位车刀刀片的夹紧方法 120
6.可转位车刀型号表示规则 120
7.优先选用的可转位车刀 124
8.可转位车刀使用中应注意的问题 149
2.3.6车刀实例 149
2.3.7车刀的刃磨与检测 152
1.砂轮的选择 152
2.车刀的刃磨 152
2.4麻花钻头 156
2.4.1麻花钻的组成与切削部分的结构 156
2.4.2高速钢麻花钻的类型、基本尺寸及标准代号 157
1.粗直柄小麻花钻 157
2.直柄短麻花钻和直柄麻花钻 157
3.直柄长麻花钻 157
4.直柄超长麻花钻 157
5.莫氏锥柄麻花钻 163
6.莫氏锥柄长麻花钻 163
7.莫氏锥柄加长麻花钻 163
8.莫氏锥柄超长麻花钻 163
2.4.3硬质合金麻花钻的类型、直径范围及标准代号 171
2.5群钻 172
2.5.1标准群钻 172
2.5.2铸铁群钻 173
2.5.3黄铜群钻 173
2.5.4纯铜群钻 173
2.5.5薄板群钻 173
2.5.6加工毛坯用扩孔群钻 176
2.6中心钻 176
2.6.1不带护锥中心钻(A型)的型式、基本尺寸及偏差 176
2.6.2带护锥中心钻(B型)的型式、基本尺寸及偏差 177
2.6.3弧形中心钻(R型)的型式、基本尺寸及偏差 177
2.7扩孔钻 178
2.7.1直柄扩孔钻 178
2.7.2锥柄扩孔钻 178
2.7.3套式扩孔钻 178
2.8锪钻 181
2.8.1 60°、 90°、 120°直柄锥面锪钻 181
2.8.2 60°、 90°、 120°锥柄锥面锪钻 182
2.8.3带导柱直柄平底锪钻 182
2.8.4带可换导柱锥柄平底锪钻 182
2.8.5带导柱直柄90°锥面锪钻 182
2.8.6带可换导柱锥柄90°锥面锪钻 182
2.9铰刀 184
2.9.1铰刀的主要几何参数 184
2.9.2常用机铰刀的形状与规格尺寸 184
1.直柄机用铰刀 184
2.莫氏锥柄机用铰刀 184
3.带刃倾角直柄机用铰刀 184
4.带刃倾角莫氏锥柄机用铰刀 184
5.套式机用铰刀 191
6.直柄硬质合金机用铰刀 191
7.莫氏锥柄硬质合金机用铰刀 191
8.硬质合金可调节浮动铰刀 191
9.直柄机用1:50锥度销子铰刀 191
10.莫氏锥柄机用1 : 50锥度销子铰刀 191
11.直柄莫氏圆锥铰刀及米制圆锥铰刀 191
12.锥柄莫氏圆锥铰刀及米制圆锥铰刀 191
2.10钻头、扩孔钻、铰刀的刃磨与使用 198
2.10.1麻花钻的刃磨 198
2.10.2麻花钻的修磨 198
2.10.3群钻的刃磨 201
2.10.4扩孔钻外径极限偏差的选择 204
2.10.5铰刀直径极限偏差的选择 204
2.10.6铰刀的刃磨与研磨 205
2.10.7铰削结构特殊孔铰刀的选择 207
2.11丝锥 207
2.11.1丝锥结构与几何参数 207
2.11.2常用丝锥的类型、规格与基本尺寸 209
1.粗柄机用和手用丝锥 209
2.粗柄带颈机用和手用丝锥 209
3.细柄机用和手用丝锥 209
4.细长柄机用丝锥 210
5.螺母丝锥 210
6.螺旋槽丝锥 210
7.55°非密封和55°密封管螺纹丝锥 210
2.11.3特种丝锥 219
2.12板牙 220
2.12.1圆板牙的结构与几何参数 220
2.12.2管螺纹板牙 220
2.12.3常用板牙的类型、规格与基本尺寸 220
1.圆板牙 220
2.55°非密封管螺纹圆板牙(G系列) 220
3.55°密封管螺纹圆板牙(R系列) 221
4.60°密封管螺纹圆板牙 221
第3章 车床夹具及辅具 228
3.1通用夹具 228
3.1.1顶尖 228
1.固定顶尖的型式及规格 228
2.回转顶尖的型式及规格 229
3.内拨顶尖的型式及规格 229
4.夹持式内拨顶尖的型式及规格 229
5.外拨顶尖的型式及规格 229
6.内锥孔顶尖的型式及规格 229
7.夹持式内锥孔顶尖的型式及规格 229
3.1.2夹头 233
1.鸡心夹头 233
2.卡环 233
3.夹板 234
4.车床用快换卡头 234
3.1.3卡盘 235
1.自定心卡盘 235
2.单动卡盘 235
3.过渡盘 238
3.1.4花盘 242
3.2专用夹具 243
3.2.1工件的定位 243
1.工件定位原理 243
2.常用定位元件限制的工件自由度及其应用 245
3.2.2工件的夹紧 250
1.对夹紧装置的基本要求 250
2.确定夹紧力的基本原则 250
3.车床夹具常用的夹紧装置 251
3.2.3典型车床夹具 253
3.3组合夹具 255
3.3.1槽系组合夹具元件 255
1.基础件 255
2.支承件 257
3.定位件 262
4.导向件 267
5.压紧件 269
6.紧固件 269
7.其他件 273
8.合件 273
3.3.2车转向节内孔组合夹具 277
3.4可调夹具 278
3.4.1通用可调夹具 278
3.4.2成组夹具 278
3.5车床辅具 281
3.5.1刀杆 281
1.弹性刀杆 281
2.多用刀杆 281
3.弹性转动刀杆 281
4.微调圆盘车刀刀杆及车刀安装尺寸 281
5.切断刀杆 283
6.90°车内孔方刀杆 283
7.45°车内孔方刀杆 283
8.90°车内孔圆刀杆 284
9.45°车内孔圆刀杆 284
3.5.2刀夹 285
1.方刀杆刀夹 285
2.圆刀杆刀夹 285
3.莫氏锥柄工具用夹持器 285
3.5.3加工螺纹用辅具 287
1.板牙夹套 287
2.丝锥夹套 287
3.切制螺纹夹头 287
第4章 常用量具与量仪 289
4.1游标类量具 289
4.1.1游标卡尺 289
4.1.2游标、带表和数显高度卡尺 293
4.1.3游标、带表和数显深度卡尺 294
4.1.4游标齿厚卡尺 294
4.2螺旋测微量具 295
4.2.1外径千分尺 295
4.2.2两点内径千分尺 297
4.2.3内测千分尺 298
4.2.4三爪内径千分尺 298
4.2.5板厚千分尺 299
4.2.6壁厚千分尺 299
4.2.7深度千分尺 300
4.2.8公法线千分尺 300
4.2.9螺纹千分尺 301
4.3机械式测微仪 302
4.3.1指示表 302
4.3.2杠杆指示表 302
4.3.3内径指示表 302
4.3.4大量程指示表 302
4.3.5钢球式内径指示表 304
4.3.6涨簧式内径指示表 304
4.3.7深度指示表 305
4.3.8指示表的结构原理与使用 305
4.4角度量具 308
4.4.1正弦规 308
4.4.2 90°角尺 310
4.4.3方形角尺 313
4.4.4万能角度尺 313
4.4.5刀口形直尺 314
4.4.6水平仪 314
1.条式水平仪 314
2.框式水平仪 315
3.合像水平仪 315
4.4.7角度量块 316
1.常用角度量块 316
2.特种角度量块 317
3.测量角度的判定 317
4.5量块、量针和量规 318
4.5.1量块 318
4.5.2量针 320
4.5.3量规 321
1.光滑极限量规 321
2.普通螺纹量规 324
3.梯形螺纹量规 329
4.工具圆锥量规 333
4.5.4塞尺 339
4.5.5半径样板 340
4.5.6螺纹样板 341
4.5.7中心规 342
4.6电动量仪 342
4.6.1圆度仪 342
4.6.2电动轮廓仪 343
4.7量具的选择 343
4.7.1根据测量内容和零件状况选择量具 343
4.7.2根据零件的生产批量选择量具 343
4.7.3根据零件精度选择量具 343
第5章 车削零件结构要素与结构工艺性 349
5.1车削零件的结构要素 349
5.1.1中心孔 349
1.60°中心孔 349
2.75°、 90°中心孔 350
5.1.2零件倒圆和倒角 352
5.1.3退刀槽 353
1.外圆退刀槽及相配件的倒角、倒圆 353
2.公称直径相同、具有不同配合的退刀槽 353
3.带槽孔的退刀槽 356
5.1.4滚花 356
5.1.5梯形螺纹 356
1.梯形螺纹的基本牙型与尺寸计算 356
2.梯形螺纹直径与螺距系列 357
3.梯形螺纹基本尺寸 357
4.梯形螺纹公差 361
5.梯形螺纹的收尾、退刀槽和倒角尺寸 365
5.1.6管螺纹 366
1.55°非密封管螺纹 366
2.55°密封管螺纹 369
3.60°密封管螺纹 371
4.米制锥螺纹 372
5.55°非密封管螺纹的收尾、退刀槽和倒角尺寸 375
5.1.7锯齿形(3°、 30°)螺纹 378
5.1.8寸制惠氏螺纹 385
5.1.9普通螺纹的收尾、肩距、退刀槽和倒角尺寸 389
5.1.10锥度、锥角和工具圆锥 393
1.锥度、锥角及其公差 393
2.机床和工具柄用自夹圆锥 398
5.2车削零件的结构工艺性 404
第6章 公差配合与表面粗糙度 407
6.1极限与配合 407
6.1.1术语和定义 407
6.1.2国家标准的基本规定 408
6.1.3孔、轴的极限偏差与配合 410
1.公称尺寸至500mm孔的极限偏差 410
2.公称尺寸至500mm轴的极限偏差 410
3.孔、轴的配合 410
6.1.4一般公差、未注公差的线性和角度尺寸的公差 410
6.2形状和位置公差 441
6.2.1形状和位置公差符号 441
6.2.2形状和位置公差的未注公差值 442
6.2.3图样上注出公差的规定 443
6.2.4形位误差的检测方法 447
1.直线度误差的常用测量方法 447
2.平面度误差的常用测量方法 447
3.圆度误差的常用测量方法 447
4.轮廓度误差的常用测量方法 447
5.定向误差的常用测量方法 447
6.定位误差的常用测量方法 447
7.跳动量的常用测量方法 454
6.3表面粗糙度 456
6.3.1表面粗糙度的评定参数 456
6.3.2表面粗糙度代(符)号 456
6.3.3各级表面粗糙度的表面特征、加工方法与应用举例 458
6.3.4各种加工方法所能达到的表面粗糙度 458
6.3.5表面粗糙度的检测 460
第7章 加工余量 461
7.1轧制材料轴的机械加工余量 461
7.2工序间加工余量 468
7.2.1工序余量的选择原则 468
7.2.2轴及槽的加工余量 468
1.轴的折算长度 468
2.粗车及半精车外圆加工余量及偏差 469
3.轴在粗车外圆后精车外圆的加工余量 469
4.粗车外圆、正火后精车外圆的加工余量 469
5.用金刚石细车轴外圆的加工余量 470
6.轴的粗车、半精车、精车、细车的加工余量 470
7.轴的端面及槽的加工余量 470
7.2.3孔的加工余量 473
1.基孔制7级精度(H7)孔的加工 473
2.基孔制8、 9级精度(H8、 H9)孔的加工 473
3.预先铸出或热冲出的H7至H9级精度孔的加工余量 473
4.金刚石镗刀细镗孔的加工余量 473
7.2.4攻螺纹前钻孔用麻花钻直径尺寸与套螺纹前圆杆直径尺寸的选择 478
7.2.5热处理(调质件)的加工余量 485
7.2.6有色金属及其合金零件的加工余量 485
7.3工序余量的校核计算 487
7.3.1尺寸链的定义、组成与特性 487
7.3.2尺寸链的计算方法 488
7.3.3工艺尺寸链用于余量校核实例 489
第8章 切削用量与切削液 491
8.1切削用量 491
8.1.1切削用量选择的原则 491
1.背吃刀量ap的选择 491
2.进给量f的选择 492
3.切削速度vc的选择 492
8.1.2车削用量的选择 492
1.硬质合金及高速钢车刀粗车外圆和端面时的进给量 492
2.硬质合金及高速钢车刀半精车与精车外圆和端面时的进给量 493
3.外圆车削的切削速度 494
4.车削加工的切削用量 495
5.用YT15硬质合金车刀车削碳钢、铬钢、镍铬钢及铸钢时的切削速度 495
6.用YG6硬质合金车刀车削灰铸铁时的切削速度 497
7.硬质合金及高速钢车刀粗车内孔的进给量 498
8.精密镗削内孔的切削用量 499
9.切断及切槽的进给量 499
10.切断及切槽的切削用量 500
11.高速切削细长轴的切削用量 500
12.硬质合金车刀精车薄壁工件的切削用量 500
13.涂层硬质合金车刀的切削用量 501
14.陶瓷车刀车削的进给量 501
15.陶瓷车刀的切削用量 501
16.立方氮化硼车刀的切削用量 504
17.金刚石车刀的切削用量 504
18.成形车削的进给量 506
19.用高速钢刀具车削螺纹的切削用量 506
20.用YT类(P类)硬质合金刀具车削螺纹的切削用量 507
21.用YG类(K类)硬质合金刀具车削螺纹的切削用量 507
22.高速钢及硬质合金车刀车削不同材料螺纹的切削用量 508
23.旋风切削螺纹的切削用量 509
8.1.3车削用量选择实例 509
8.1.4钻孔切削用量的选择 512
1.高速钢钻头钻孔时的切削速度 512
2.硬质合金钻头钻孔时的切削速度 512
3.高速钢钻头钻孔时的进给量 512
4.硬质合金YG8钻头钻灰铸铁时的进给量 514
5.硬质合金钻头钻削不同材料的切削用量 514
6.高速钢钻头钻削不同材料的切削用量 515
7.群钻加工钢时的切削用量 516
8.群钻加工铸铁时的切削用量 517
9.高速钢标准钻头钻削力及功率的计算公式 518
8.1.5扩孔的切削用量 518
1.高速钢及硬质合金扩孔钻的进给量 518
2.扩钻、扩孔的切削用量 519
3.高速钢扩孔钻在结构碳钢(Rm=650MPa)上扩孔时的切削速度 519
4.高速钢扩孔钻加工灰铸铁(190HBW)时的切削速度 520
5.硬质合金扩孔钻的切削速度 521
8.1.6铰削用量 523
1.高速钢及硬质合金机铰刀的进给量 523
2.高速钢铰刀加工不同材料的切削用量 523
3.高速钢铰刀铰削结构碳钢、铬钢、镍铬钢(Rm=650MPa)的切削速度 524
4.高速钢铰刀铰削灰铸铁(190HBW)的切削速度 525
5.硬质合金铰刀铰孔的切削用量 526
8.1.7钻、扩、铰切削用量选择实例 527
1.钻孔 527
2.扩孔 527
3.铰孔 527
8.2切削液 527
8.2.1切削液的作用 527
8.2.2切削液中的添加剂 528
8.2.3切削液的种类、选择与使用 528
第9章 零件车削工艺 531
9.1零件机械加工工艺过程的制订 531
9.1.1机械加工工艺过程的组成 531
9.1.2生产纲领与生产类型 531
9.1.3制定机械加工工艺过程的原则和内容 532
9.1.4基准及其选择 532
1.基准及其分类 532
2.定位基准的选择 533
3.工序基准的选择 536
4.基准不重合时的工艺尺寸计算示例 536
9.1.5机械加工工艺路线的拟定 539
1.表面加工方法的选择 539
2.加工阶段的划分 541
3.工序的集中与分散 542
4.工序顺序的安排 542
9.2改善零件车削质量的途径与方法 543
9.2.1尺寸精度及改善措施 543
9.2.2形状精度及改善措施 546
9.2.3位置精度及改善措施 551
9.2.4表面粗糙度 552
9.3轴类零件的车削加工 554
9.3.1车刀的安装 555
9.3.2工件的装夹与中心孔的加工 558
9.3.3阶梯轴的加工 561
9.3.4主轴的加工 562
9.3.5细长轴的加工 567
9.4盘套类零件的加工 572
9.4.1盘套类零件的结构与工艺特点 572
9.4.2车削盘套类零件,保证内、外圆位置精度的方法 573
9.4.3盘套类零件的安装及端面车削 575
9.4.4钻孔、扩孔、铰孔及车孔 578
1.钻孔 578
2.扩孔 580
3.铰孔 580
4.车孔 583
5.孔各种加工路线所达到的公差等级 584
9.4.5盘套类零件加工实例 585
9.5圆锥面的加工 588
9.5.1圆锥面的加工方法 588
9.5.2转动小刀架法车圆锥面的调整 590
9.5.3车圆锥面时加工精度的控制 592
9.5.4圆锥面精度的检验 594
9.6成形面的加工 595
9.6.1成形面车削方法及其选择 595
9.6.2用靠模法车削凸轮成形面,靠模表面圆弧半径不能任意选择 599
9.6.3车削成形面时产生废品的原因及预防措施 600
9.7滚花与绕弹簧 601
9.7.1表面滚花时,滚花刀的选择和乱纹的防止方法 601
9.7.2车床上绕制弹簧时,心轴直径的选择 603
9.8螺纹及蜗杆的加工 604
9.8.1螺纹车刀的安装方法 604
9.8.2车螺纹的三种进刀方式及其选用 604
9.8.3螺纹车削方法的选择 605
9.8.4螺纹车削质量的控制 605
9.8.5攻螺纹与套螺纹 610
1.攻螺纹 610
2.套螺纹 612
3.攻螺纹和套螺纹时常见质量问题的原因及预防方法 613
9.8.6旋风切削螺纹 613
9.8.7多头蜗杆的车削 615
9.8.8丝杠车削实例 617
9.8.9车螺纹及蜗杆常见质量问题的原因及预防方法 621
9.8.10螺纹及蜗杆的测量 623
1.螺纹的测量 623
2.蜗杆的测量 626
3.丝杠螺距的测量 627
9.9畸形件的车削 627
9.10深孔加工 631
9.10.1用外排屑枪钻钻深孔 631
9.10.2用内排屑深孔钻钻深孔 635
9.10.3用深孔套料钻钻深孔 638
9.10.4用深孔刀头镗削深孔 639
9.10.5深孔铰削 642
9.10.6深孔镗、铰削过程中的常见问题及原因 643
9.10.7深孔滚压加工 644
9.10.8深孔的镗、滚复合加工 645
9.10.9深孔零件加工实例 645
第10章 难切削材料的加工 648
10.1难切削材料及其工艺特点 648
10.1.1材料相对加工性等级 648
10.1.2难切削材料加工的工艺特点 648
10.2高强度钢、超高强度钢的切削 649
10.2.1刀具材料、几何参数与切削用量的选择 649
10.2.2车削高强度钢刀具实例 650
10.3高锰钢的切削加工 650
10.3.1刀具材料、几何参数与切削用量的选择 650
10.3.2高锰钢切削刀具实例 651
10.4淬硬钢的车削 652
10.4.1淬硬钢车削刀具及切削用量的选择 652
10.4.2车削淬硬钢刀具实例 653
10.5难切削铸件的加工 654
10.5.1冷硬、耐磨铸铁的车削 654
10.5.2冷铸轧辊车刀 655
10.6不锈钢的加工 656
10.6.1刀具及切削用量的选择 656
10.6.2不锈钢刀具实例 658
10.6.3不锈钢孔的钻削与铰削 659
10.7高温合金的加工 661
10.7.1刀具及切削用量的选择 661
10.7.2高温合金车刀实例 664
10.8钛合金的车削 665
10.8.1刀具及切削用量的选择 665
10.8.2钛合金车刀实例 665
10.9工程塑料的切削 666
10.9.1工程塑料的切削特点 666
10.9.2工程塑料的切削方式 666
10.9.3切削工程塑料的工艺参数及刀具 667
10.10橡胶的车削 669
附录 670
附录A切削加工用硬质合金的应用范围分类和用途分组 670
附录B三针测量螺纹中径时的M值 671
参考文献 676
- 《葡萄酒工艺与鉴赏 第3版》廖祖宋 2019
- 《Maya 2018完全实战技术手册》来阳编著 2019
- 《高等教育双机械基础课程系列教材 高等学校教材 机械设计课程设计手册 第5版》吴宗泽,罗圣国,高志,李威 2018
- 《化学工程与工艺专业实验指导》郭跃萍主编 2019
- 《慢性呼吸系统疾病物理治疗工作手册》(荷)瑞克·考斯林克(RikGosselink) 2020
- 《战略情报 情报人员、管理者和用户手册》(澳)唐·麦克道尔(Don McDowell)著 2019
- 《实用内科手册》黄清,阮浩航主编 2016
- 《美物之道 日本手工艺》(日)柳宗悦著 2019
- 《基层医疗卫生机构安全用药手册》黎月玲,熊慧瑜 2019
- 《同仁眼科手册系列 同仁儿童眼病手册》付晶编 2018
- 《东方杂志 第110册 第25卷 第一至四号 1928年1月-1928年2月》上海书店出版社编 2012
- 《清明 我们的节日》冯骥才编 2017
- 《现代水泥技术发展与应用论文集》天津水泥工业设计研究院有限公司编 2019
- 《甘肃省档案馆指南》甘肃省档案馆编 2018
- 《莼江曲谱 2 中国昆曲博物馆藏稀见昆剧手抄曲谱汇编之一》郭腊梅主编;孙伊婷副主编;孙文明,孙伊婷编委;中国昆曲博物馆编 2018
- 《花时间 我的第一堂花艺课 插花基础技法篇》(日)花时间编辑部编;陈洁责编;冯莹莹译 2020
- 《中央财政支持提升专业服务产业发展能力项目水利工程专业课程建设成果 设施农业工程技术》赵英编 2018
- 《东方杂志 第94册 第22卷 第四至七号 1925年2月-1925年4月》上海书店出版社编 2012
- 《远去的老调》经典文库编委会编 2019
- 《东方杂志 第13册 第四年 第一至三期 1907年3月-1907年5月》上海书店出版社编 2012
- 《指向核心素养 北京十一学校名师教学设计 英语 七年级 上 配人教版》周志英总主编 2019
- 《北京生态环境保护》《北京环境保护丛书》编委会编著 2018
- 《高等教育双机械基础课程系列教材 高等学校教材 机械设计课程设计手册 第5版》吴宗泽,罗圣国,高志,李威 2018
- 《指向核心素养 北京十一学校名师教学设计 英语 九年级 上 配人教版》周志英总主编 2019
- 《高等院校旅游专业系列教材 旅游企业岗位培训系列教材 新编北京导游英语》杨昆,鄢莉,谭明华 2019
- 《中国十大出版家》王震,贺越明著 1991
- 《近代民营出版机构的英语函授教育 以“商务、中华、开明”函授学校为个案 1915年-1946年版》丁伟 2017
- 《新工业时代 世界级工业家张毓强和他的“新石头记”》秦朔 2019
- 《智能制造高技能人才培养规划丛书 ABB工业机器人虚拟仿真教程》(中国)工控帮教研组 2019
- 《AutoCAD机械设计实例精解 2019中文版》北京兆迪科技有限公司编著 2019