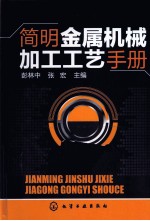
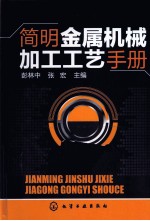
简明金属机械加工工艺手册PDF电子书下载
- 电子书积分:18 积分如何计算积分?
- 作 者:彭林中,张宏主编
- 出 版 社:北京:化学工业出版社
- 出版年份:2012
- ISBN:9787122116383
- 页数:629 页
第1章 金属切削基本知识 1
1.1 切削运动与切削用量 1
1.1.1切削运动和工件表面 1
1.1.2切削用量 2
1.1.3切削用量的选择原则 4
1.2刀具几何参数 5
1.2.1刀具切削部分的组成 5
1.2.2确定刀具几何角度的参考系 6
1.2.3刀具几何角度的定义 7
1.2.4刀具合理几何参数的选择 7
1.3刀具材料 12
1.3.1刀具材料应具备的性能 12
1.3.2各类刀具材料的主要性能比较 13
1.3.3高速钢的分类、性能及用途 14
1.3.4硬质合金 16
1.4金属切削过程及其物理现象 20
1.4.1切削过程及切屑种类 20
1.4.2积屑瘤 22
1.4.3切削力与切削功率 23
1.4.4切削热与切削温度 25
1.4.5刀具磨损及刀具寿命 27
1.4.6切削液 30
1.4.7工件材料的切削加工性 34
1.5金属切削机床型号编制方法 36
1.5.1通用机床的型号 37
1.5.2专用机床的型号 44
1.5.3机床自动线的型号 45
第2章 毛坯及余量 46
2.1毛坯的加工余量 46
2.1.1加工余量的基本概念 46
2.1.2毛坯的表面层厚度 48
2.2轧制件 48
2.2.1轴类零件采用精轧圆棒料时毛坯直径 48
2.2.2轧制圆棒料切断和端面加工余量 50
2.2.3易切削钢轴类外圆的选用(车后不磨) 50
2.2.4易切削钢轴类外圆的选用(车后需淬火及磨) 51
2.3铸件 52
2.3.1铸件的尺寸公差 52
2.3.2铸件尺寸公差等级的选用 54
2.3.3铸件的机械加工余量 54
2.4锻件 56
2.4.1自由锻件的机械加工余量 56
2.4.2模锻件的机械加工余量 58
2.5工序间加工余量 59
2.5.1影响工序间加工余量的因素 59
2.5.2轴的加工余量 60
2.5.3孔的加工余量 65
2.5.4平面加工余量 70
2.5.5切除渗碳层的加工余量 73
2.5.6齿轮精加工余量 74
2.5.7花键精加工余量 76
2.5.8有色金属及其合金的加工余量 77
第3章 机械加工质量和精度检验 82
3.1机械加工精度 82
3.1.1机械加工精度的概念 82
3.1.2影响加工精度的因素及改善措施 84
3.1.3经济加工精度 89
3.2机械加工表面质量 97
3.2.1已加工表面质量的概念 97
3.2.2表面粗糙度 98
3.2.3工件表面层的加工硬化 106
3.2.4表面层金相组织的变化与磨削烧伤 107
3.2.5表面层残余应力 109
3.3常用检测方法 110
3.3.1圆弧的测量计算 110
3.3.2锥度的常用测量方法 110
3.3.3 V形块的常用测量方法 114
3.3.4燕尾与燕尾槽的常用测量方法 114
3.3.5直线度误差的常用测量方法 115
3.3.6平面度误差的常用测量方法 120
3.3.7圆度误差的常用测量方法 125
3.3.8圆柱度误差的常用测量方法 127
3.3.9轮廓度误差的常用测量方法 129
3.3.10定向误差的常用测量方法 132
3.3.11定位误差的常用测量方法 141
3.3.12跳动误差的常用测量方法 150
第4章 机械加工工艺规程 153
4.1基本概念 153
4.1.1常用的机械制造工艺基本术语 153
4.1.2工艺过程及其组成 156
4.1.3生产纲领、生产类型及其工艺特征 159
4.1.4机械加工工艺规程的作用 162
4.1.5制订工艺规程的基本要求、主要依据和制订步骤 162
4.2工艺过程设计中应考虑的主要因素 163
4.2.1定位基准的选择 163
4.2.2零件表面加工方法的选择 164
4.2.3加工顺序的合理安排 167
4.3工艺文件格式及填写规则 169
4.3.1机械加工工艺过程卡片格式及填写规则 169
4.3.2机械加工工序卡片填写及格式规则 171
4.3.3标准零件(或典型零件)工艺过程卡片格式 173
4.4典型零件加工工艺过程 174
4.4.1轴类零件加工工艺过程分析 174
4.4.2圆柱齿轮加工工艺过程分析 184
4.4.3套筒类零件加工工艺过程分析 190
4.4.4箱体类零件加工工艺过程分析 193
第5章 机床夹具 201
5.1夹具概述 201
5.1.1机床夹具的概念 201
5.1.2机床夹具的分类 201
5.1.3机床夹具的组成 202
5.1.4机床夹具的作用 203
5.2工件定位原理 204
5.2.1六点定位 204
5.2.2限制工件自由度与加工要求的关系 205
5.2.3正确处理重复定位 206
5.2.4常见定位元件所限制的自由度 209
5.3夹紧装置简介 211
5.3.1夹紧装置的组成及基本要求 211
5.3.2夹紧力的确定 212
5.3.3几种基本夹紧机构 215
5.4夹具的对定 227
5.4.1夹具与机床的连接方式 227
5.4.2对刀和导引装置 229
5.4.3分度装置 239
5.5机床夹具常用标准零件 242
5.5.1定位件 242
5.5.2导向件 255
5.5.3支承件 265
5.5.4夹紧件 269
第6章 车削加工 281
6.1车刀 281
6.1.1车刀几何角度的参考值 281
6.1.2硬质合金焊接车刀 283
6.1.3可转位车刀 291
6.2车外圆 313
6.2.1车削用量的选择 313
6.2.2车外圆时产生废品的原因及预防措施 316
6.3车内孔 317
6.3.1不同精度内孔在车床上的加工方法 317
6.3.2内孔车刀 317
6.3.3车削用量的选择 318
6.3.4车内孔时产生废品的原因及预防措施 319
6.4切槽与切断 320
6.4.1常用切断刀的种类 320
6.4.2常用切断刀的几何参数 323
6.4.3切断及切槽的切削用量 324
6.4.4常用车槽方法和工具 326
6.4.5切槽及切断常见工件缺陷及预防措施 328
6.5车圆锥面 328
6.5.1圆锥面的车削方法 328
6.5.2车圆锥面时产生废品的原因及预防措施 332
6.6车球面 333
6.6.1车削外球面 333
6.6.2车削内球面 333
6.7车偏心 333
6.7.1用四爪卡盘车偏心工件 333
6.7.2用三爪卡盘车偏心工件 334
6.7.3用花盘车偏心工件 334
6.7.4用两顶尖车偏心工件 335
6.7.5用偏心卡盘车偏心工件 335
6.7.6用专用夹具车偏心工件 336
6.8车螺纹 337
6.8.1螺纹车刀角度及修正 337
6.8.2螺纹车刀的刀尖宽度尺寸 339
6.8.3螺纹车刀的对刀及安装 340
6.8.4螺纹车削方法 342
6.8.5螺纹车削用量 344
6.8.6车削多头螺纹的分度方法 346
6.8.7车削螺纹时挂轮的计算 348
6.8.8常用螺纹车刀 364
6.8.9螺纹车削实例 364
6.8.10攻螺纹前钻孔用钻头直径的确定 374
6.8.11螺纹的测量 378
6.9车细长轴工艺参数 387
6.9.1细长轴的加工特点 387
6.9.2车削细长轴常用装夹方法 388
6.9.3车削细长轴车刀的几何参数 390
6.9.4车削细长轴常用的切削用量和能达到的加工质量 392
6.9.5车细长轴实例 392
6.10车削薄壁工件的工艺参数 395
6.10.1薄壁工件的车削特点 395
6.10.2防止和减少薄壁工件变形的方法 395
6.10.3正确选择工件的装夹方法 396
6.10.4车削薄壁工件实例 398
第7章 铣削加工 400
7.1铣刀 400
7.1.1铣刀主要几何角度的代号和选择 400
7.1.2铣刀主要结构参数的选择 404
7.1.3常用标准铣刀的类型及规格 405
7.2铣削用量 419
7.2.1铣削用量的定义 419
7.2.2铣削用量的选择 421
7.3分度头 426
7.3.1分度头简介 426
7.3.2分度方法及计算 427
7.4铣离合器 438
7.4.1铣矩形齿离合器 438
7.4.2铣尖齿离合器 440
7.4.3铣锯齿形离合器 442
7.4.4铣梯形齿离合器 444
7.5铣球面 444
7.5.1铣整球 444
7.5.2铣带柄球面 445
7.5.3铣内球面 445
7.6铣花键轴 445
7.6.1用单刀铣削矩形齿花键轴 446
7.6.2用组合铣刀铣削矩形齿花键轴 448
7.6.3铣削花键轴时产生误差的原因及解决方法 449
7.7刀具开齿 450
7.7.1对前角γ。=0°的铣刀开齿 450
7.7.2对前角γ。>0°的铣刀开齿 451
7.7.3圆柱螺旋齿铣刀的开齿 452
7.7.4麻花钻的铣削 454
7.7.5端面齿的铣削 455
7.7.6锥面齿的铣削 455
7.7.7铰刀的开齿 456
7.8铣齿轮 458
7.8.1铣直齿圆柱齿轮 458
7.8.2铣齿条 459
7.8.3铣斜齿圆柱齿轮 460
7.8.4铣直齿锥齿轮 462
7.9铣凸轮 464
7.9.1凸轮传动的三要素 464
7.9.2等速圆盘凸轮的铣削 465
7.9.3等速圆柱凸轮的铣削 467
7.10精铣平面 467
7.10.1精铣平面对铣刀的要求 467
7.10.2精铣对工艺系统的要求 468
7.10.3精铣对铣床的要求 469
7.10.4精铣平面的铣削用量 469
7.10.5铝合金的精铣 470
第8章 刨削和插削加工 472
8.1刨刀 472
8.1.1常用刨刀的种类和用途 472
8.1.2刨刀几何参数的选择 474
8.1.3几种先进的刨刀 474
8.2装夹方法与刨削工具 479
8.2.1刨削时工件的常用装夹方法 479
8.2.2刨削工具 480
8.3典型零件的刨削 481
8.3.1刨削薄板工件 481
8.3.2槽类工件的刨削 483
8.3.3镶条的刨削 485
8.3.4精刨 486
8.4刨削加工中常见问题产生的原因及解决方法 488
8.4.1 刨平面常见问题产生的原因及解决方法 488
8.4.2刨垂直面和台阶常见问题产生的原因及解决方法 489
8.4.3刨斜面、V形槽及镶条常见问题产生的原因及解决方法 490
8.4.4切断、刨直槽及T形槽常见问题产生的原因及解决方法 491
8.5插削加工 492
8.5.1插刀的类型与用途 492
8.5.2插刀主要几何角度的选择 493
8.5.3典型表面的插削 493
8.5.4插削时产生废品的原因及解决方法 497
第9章 圆柱齿轮加工 498
9.1滚齿加工 498
9.1.1滚刀的类型及精度选择 498
9.1.2滚齿加工工艺参数的选择& 500
9.1.3挂轮的调整计算(以Y3150E型滚齿机为例) 500
9.1.4滚刀的对中 502
9.1.5滚刀芯轴及滚刀的安装要求 503
9.1.6滚刀安装角度的调整 504
9.1.7齿坯的安装 506
9.1.8滚切深度的调整 507
9.1.9滚切大质数齿轮(以Y3150E为例) 508
9.1.10滚齿加工常见缺陷及消除方法 512
9.2齿轮的测量 515
9.2.1 分度圆弦齿厚的测量 515
9.2.2固定弦齿厚的测量 517
9.2.3公法线长度的测量 518
9.3插齿加工 523
9.3.1插齿刀具及安装 523
9.3.2常用插齿机挂轮计算 525
9.3.3插齿用夹具及调整 526
9.3.4插直齿圆柱外齿轮(以Y54为例) 528
9.3.5插直齿圆柱内齿轮 529
9.3.6插齿加工常见缺陷及其产生原因 529
第10章 磨削加工 531
10.1普通磨料磨具 531
10.1.1普通磨料的类型、代号、特性和应用 531
10.1.2普通磨料粒度号及其选择 532
10.1.3普通磨具的硬度及其选择 533
10.1.4普通磨具的结合剂及其选择 534
10.1.5普通磨具的组织及其选择 535
10.1.6普通磨具的强度及其选择 535
10.1.7普通磨具的形状和尺寸的选择 536
10.1.8普通磨具的标志(GB/T2428—1994) 542
10.2超硬磨料磨具 542
10.2.1磨料的类型、代号及应用范围 542
10.2.2超硬磨料的粒度及其选择 543
10.2.3超硬磨料结合剂及其代号、性能和应用范围 544
10.2.4浓度代号及选择 545
10.2.5砂轮、磨石及磨头的尺寸代号及术语 546
10.2.6砂轮、磨石及磨头形状代号、主要用途 546
10.2.7超硬磨具的标记方法 548
10.3磨削液及磨削工艺 549
10.3.1磨削液 549
10.3.2砂轮的平衡与修整 551
10.3.3磨削用量的选择 553
10.4外圆磨削 554
10.4.1外圆磨削用量 554
10.4.2细长轴的磨削 557
10.4.3外圆磨削常见的工件缺陷及防止措施 564
10.5内圆磨削 566
10.5.1内圆磨削用量 566
10.5.2内圆磨削时砂轮直径选择 571
10.5.3薄壁工件的磨削 571
10.5.4内圆磨削常见的工件缺陷及防止措施 574
10.6平面磨削 575
10.6.1平面磨削用量 575
10.6.2薄片零件的平面磨削 582
10.6.3平面磨削中常见的工件缺陷及防止措施 584
10.7刀具刃磨 585
10.7.1刀具刃磨时砂轮的选择 585
10.7.2铣刀和拉刀的刃磨 587
10.7.3铰刀的刃磨 589
第11章 钻孔、铰孔加工 594
11.1钻孔 594
11.1.1麻花钻 594
11.1.2硬质合金麻花钻 598
11.1.3几种改进的钻头 601
11.1.4切削液的选择 607
11.1.5钻削不同孔距精度所用的加工方法 608
11.1.6几种特殊孔的钻削方法 608
11.1.7钻削切削用量的选择 610
11.1.8麻花钻钻孔中常见工件缺陷产生原因和解决办法 615
11.2铰削 618
11.2.1铰刀的结构要素和几何参数 618
11.2.2铰刀主要几何参数的选择 618
11.2.3常用铰刀类型、规格范围及标准代号 621
11.2.4铰孔切削用量及切削液的选择 623
11.2.5多刃铰刀铰孔中常见工件缺陷及解决方法 625
参考文献 629
- 《激光加工实训技能指导理实一体化教程 下》王秀军,徐永红主编;刘波,刘克生副主编 2017
- 《Maya 2018完全实战技术手册》来阳编著 2019
- 《先进激光加工技能实训》肖海兵主编 2019
- 《高等教育双机械基础课程系列教材 高等学校教材 机械设计课程设计手册 第5版》吴宗泽,罗圣国,高志,李威 2018
- 《慢性呼吸系统疾病物理治疗工作手册》(荷)瑞克·考斯林克(RikGosselink) 2020
- 《金甲虫》(美)爱伦·坡著,焦菊隐;文楚安等译 2019
- 《战略情报 情报人员、管理者和用户手册》(澳)唐·麦克道尔(Don McDowell)著 2019
- 《实用内科手册》黄清,阮浩航主编 2016
- 《集成曲谱金集 卷7 卷8》黄天骥总主编;王季烈,刘富梁辑 2018
- 《基层医疗卫生机构安全用药手册》黎月玲,熊慧瑜 2019