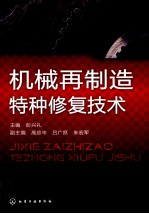
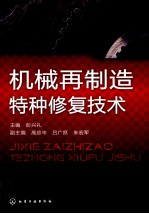
机械再制造特种修复技术PDF电子书下载
- 电子书积分:11 积分如何计算积分?
- 作 者:彭兴礼编著
- 出 版 社:北京:化学工业出版社
- 出版年份:2011
- ISBN:7122115652
- 页数:288 页
第一章 概论 1
第一节 发展机械再制造的重要意义 1
第二节 国外机械再制造发展概况 2
第三节 我国机械再制造发展概况 3
第四节 机械再制造特种修复技术的选择 3
第二章 机械制造基础 5
第一节 工程材料概述 5
一、钢铁材料分类 6
二、钢的编号表示法 7
三、钢材的成分、性能和用途 8
四、铸铁及其用途 11
五、有色合金 15
六、陶瓷材料 16
七、高分子材料 16
八、复合材料 17
第二节 工程材料的性能 18
一、工程材料的力学性能 18
二、材料物理性能 27
三、材料化学性能 28
四、材料工艺性能 28
第三节 钢铁材料微观组织与性能 28
一、金属的晶体结构 28
二、金属结晶 30
三、合金的结构 31
四、Fe-Fe3C相图 32
五、碳含量对铁碳合金组织及性能的影响 36
六、钢中杂质 37
七、合金元素在钢中的作用 38
第四节 金属材料强化与改性 38
一、钢的加热 39
二、奥氏体在冷却时的转变 41
三、常规热处理工艺 42
四、钢的表面淬火 47
五、化学热处理 48
六、表面处理 50
第五节 金属材料成形 53
一、铸造 53
二、锻压 56
三、焊接 59
四、粘接成形工艺 64
五、切削成形 64
第六节 材料质量检验与零件失效分析 69
一、材质检验在机械制造中的作用 69
二、材料及工艺质量标准体系 71
三、材料质量检验规程 72
四、材质检验技术 74
五、零件失效分析 76
附:新旧标准金属材料强度、塑性指标有关名词及符号对照表 79
第三章 电刷镀修复技术 80
第一节 电刷镀修复技术的基本原理、特点及电源设备 80
一、电刷镀修复技术的基本原理 80
二、电刷镀修复技术的特点 81
三、电刷镀修复技术的电源设备 82
四、电刷镀镀笔 83
第二节 电刷镀镀液 85
一、电刷镀镀液的分类及特点 85
二、表面准备溶液 85
三、刷镀溶液 87
第三节 电刷镀修复技术的操作工艺 97
一、电刷镀工艺中的一般问题 97
二、电刷镀镀层的结构及结构设计 100
第四节 常用金属材料的电刷镀工艺 102
一、低碳钢类材料电刷镀工艺 102
二、中、高碳钢类材料的电刷镀工艺 103
三、铸铁和铸钢类材料的电刷镀工艺 103
四、镍、镍不锈钢、热强钢类材料的电刷镀工艺 104
五、铬、铬不锈钢类材料的电刷镀工艺 104
六、铜及铜合金电刷镀工艺 105
七、锌、锡、铅、镉、钴等金属材料电刷镀工艺 105
八、铝及铝合金材料的电刷镀工艺 105
九、铁-铜复合表面的电刷镀工艺 106
第五节 电刷镀质量控制与质量检测 107
一、电刷镀的质量问题及其解决对策 107
二、电刷镀镀层质量检验 108
第四章 微脉冲电阻熔焊及高频熔焊修复技术 112
第一节 微脉冲电阻熔焊修复技术 112
一、微脉冲电阻熔焊的工作原理 112
二、微脉冲电阻熔焊修复工艺及其冷焊特征 113
三、熔焊微区的性状及金相组织 114
四、微脉冲电阻熔焊修补机的应用及操作工艺 115
五、微脉冲电阻熔焊的修补材料 118
六、待修零部件微脉冲电阻熔焊修复前的处理 118
七、不同金属材料电阻熔焊修复工艺方法的选择 118
第二节 高频熔焊多金属材料缺陷修复技术 120
一、高频熔焊多金属缺陷修复技术的工作原理 120
二、高频熔焊多金属缺陷修复技术的特点 120
三、高频熔焊多金属修补机的应用范围 121
四、高频熔焊多金属材料缺陷修补机对铝合金零部件修复的应用 121
附:高频熔焊多金属缺陷修补机及其焊枪使用操作说明 122
第五章 胶粘修复技术 125
第一节 胶粘技术的基本原理 125
一、被粘物表面的特征 125
二、胶粘作用的形成 125
三、几种胶粘理论简介 127
第二节 胶粘修复技术的特点、发展与应用 128
一、胶粘技术的特点与发展 128
二、胶粘技术在机械制造及再制造中的应用 130
第三节 胶黏剂的组成、种类与性能 131
一、胶黏剂的组成 131
二、胶黏剂的种类和性能 137
第四节 胶粘技术中被粘材料表面的处理 144
一、金属材料的胶粘及其表面的处理 144
二、塑料胶粘及其表面的处理 150
三、橡胶胶粘及其表面的处理 158
四、其它材料粘接及其表面处理 164
第五节 胶粘接头的设计与胶粘结构的强化 166
一、胶粘接头及其受力状况 166
二、胶粘接头形式的选择原则 167
三、胶粘接头的类型 168
四、常用胶粘接头的分析与评价 170
五、胶粘结构与强化 170
第六节 胶粘技术的工艺方法 173
一、确定部位 174
二、表面处理 174
三、配胶 185
四、涂胶 186
五、晾置 187
六、胶合 188
七、清理与防粘连 188
八、固化 189
九、检验 192
十、整修 193
第七节 胶粘质量的控制 193
一、影响胶粘质量的因素 193
二、胶粘的质量缺陷及处理 198
三、确保胶粘质量的措施 199
四、常用胶黏剂使用应注意的事项 200
第八节 胶粘强度及影响胶粘强度的因素 202
一、胶粘强度的基本概念 203
二、胶粘的破坏类型 207
三、胶粘强度的影响因素 208
第九节 胶粘强度的测试方法 211
一、剪切强度的测定方法 211
二、拉伸强度的测定方法 213
三、不均匀扯离强度的测定方法 214
四、剥离强度的测定方法 215
五、冲击强度的测定方法 219
六、胶粘强度的无损检验 220
第十节 胶黏剂选用的基本原则 220
一、考虑被粘物的种类和性质 220
二、考虑胶黏剂的性能 221
三、考虑胶粘的目的和用途 221
四、考虑胶粘件的受力情况 221
五、考虑胶粘件的使用环境 221
六、考虑工艺上的可行性 222
第六章 热喷涂修复技术 223
第一节 热喷涂修复技术的基本概念 223
第二节 热喷涂工艺技术分类 224
一、熔体喷涂 224
二、普通热喷涂 225
三、粉末火焰喷涂 226
四、超音速火焰喷涂 226
五、爆炸喷涂 227
六、电弧喷涂 227
七、等离子喷涂 228
八、激光喷涂 231
第三节 热喷涂涂层形成过程和结合机理 231
一、热喷涂涂层形成过程 231
二、涂层结构及结合机理 231
第四节 不同热喷涂工艺技术与工艺参数的关系 232
一、不同热喷涂工艺技术热源温度与喷涂粒子速度的关系 232
二、热喷涂工艺技术与温度的关系 233
三、热喷涂工艺技术与粒子速度关系 233
四、热喷涂工艺技术与喷涂材料关系 233
五、热喷涂工艺技术与涂层性能的关系 233
六、不同喷涂方法有关技术经济参数的比较 235
第五节 热喷涂修复技术的操作程序及注意事项 235
一、零部件检查 236
二、零部件修复表面预加工 236
三、待修复表面毛化处理 236
四、对零部件进行保护与预热 236
五、选择喷涂工艺和喷涂材料 236
六、涂层结构设计 238
七、喷涂自粘接底涂层 239
八、喷涂工作涂层 239
九、涂层的封孔处理 239
十、保温 241
十一、涂层机加工 241
十二、清理与修整 241
第七章 激光修复技术 242
第一节 激光修复技术工作原理及特性 242
一、激光修复技术工作原理 242
二、激光修复技术的特性 243
第二节 激光修复技术的成套设备 243
第三节 激光修复工艺技术 244
一、激光修复工艺 244
二、激光修复工艺参数对修复层形状、稀释率的影响 246
三、激光修复的专用材料 249
第四节 激光修复层裂纹、气孔的产生与控制 250
一、激光修复层应力状态 250
二、激光修复层裂纹的产生与控制 253
三、激光修复层气孔的产生与控制 256
第八章 机械再制造特种修复技术实际应用案例 258
第一节 设备铸造件缺陷的修复与再制造 258
一、航天设备大型不锈钢铸件缺陷的修复 258
二、汽车大型铸钢(铸铁)覆盖件模具损伤的修复 259
三、不锈钢齿轮铸件砂眼缺陷的修复及再制造 260
四、PET瓶制造模具裂纹的修复 260
第二节 机械零部件断裂的修复及再制造 261
一、汽车凸轮轴支座断裂的修复 261
二、汽车发动机缸体裂纹及缸套之间断裂的修复 262
三、联合收割机铝合金变速箱断裂及裂纹的修复 262
四、铝型材轧机主动辊断裂的修复 262
五、航空材料研究院特种压力机主轴及凸轮键槽部位断裂的修复 263
六、汽车后桥半轴法兰断裂的修复 263
七、空压机机体裂缝的修复 264
八、平板印刷机压印滚筒轴断裂的修复 265
第三节 机械零部件表面磨损、划伤、剥落及腐蚀的修复与再制造 266
一、地铁工程盾构掘进机驱动外壳密封位严重磨损的修复与再制造 266
二、万吨水压机进口充液阀提升柱塞的再制造 267
三、数控凸轮磨床静压导轨磨损的修复和再制造 269
四、船载打桩机变幅油缸及活塞损伤的修复 270
五、百万吨远洋货轮主发动机机体及曲轴严重磨损的现场不解体修复 274
六、宽幅压缩板成型机组热压辊筒磨损及腐蚀的不解体修复 274
七、2500吨压床大型齿轮磨损的修复 275
八、设备机体、箱体轴承孔磨损的修复 275
九、设备液压油缸磨损与划伤的修复 276
十、车床尾座滑板磨损的修复 277
第四节 压力容器泄漏的修复及再制造 277
一、“十五”重点工程“飞机模拟实验台的大型风洞”冷却塔渗漏修复 277
二、锅炉贮水箱泄漏的修复 278
三、大型煤气贮气罐及贮油罐泄漏的修复 278
第五节 激光修复技术在重要机械零部件表面损伤的修复和再制造中的应用 278
一、激光修复技术在航空发动机叶片损伤修复及再制造中的应用 278
二、激光修复技术在汽轮机叶片损伤修复及再制造中的应用 279
三、激光修复技术在注塑(橡)机螺杆损伤及表面强化中的应用 281
四、激光修复技术在石化系统的碱过滤器中的应用 285
参考文献 288
- 《钒产业技术及应用》高峰,彭清静,华骏主编 2019
- 《现代水泥技术发展与应用论文集》天津水泥工业设计研究院有限公司编 2019
- 《异质性条件下技术创新最优市场结构研究 以中国高技术产业为例》千慧雄 2019
- 《Prometheus技术秘笈》百里燊 2019
- 《中国制造业绿色供应链发展研究报告》中国电子信息产业发展研究院 2019
- 《中央财政支持提升专业服务产业发展能力项目水利工程专业课程建设成果 设施农业工程技术》赵英编 2018
- 《药剂学实验操作技术》刘芳,高森主编 2019
- 《林下养蜂技术》罗文华,黄勇,刘佳霖主编 2017
- 《脱硝运行技术1000问》朱国宇编 2019
- 《催化剂制备过程技术》韩勇责任编辑;(中国)张继光 2019
- 《市政工程基础》杨岚编著 2009
- 《家畜百宝 猪、牛、羊、鸡的综合利用》山西省商业厅组织技术处编著 1959
- 《《道德经》200句》崇贤书院编著 2018
- 《高级英语阅读与听说教程》刘秀梅编著 2019
- 《计算机网络与通信基础》谢雨飞,田启川编著 2019
- 《看图自学吉他弹唱教程》陈飞编著 2019
- 《法语词汇认知联想记忆法》刘莲编著 2020
- 《培智学校义务教育实验教科书教师教学用书 生活适应 二年级 上》人民教育出版社,课程教材研究所,特殊教育课程教材研究中心编著 2019
- 《国家社科基金项目申报规范 技巧与案例 第3版 2020》文传浩,夏宇编著 2019
- 《流体力学》张扬军,彭杰,诸葛伟林编著 2019