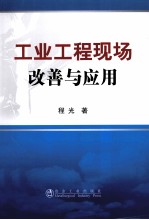
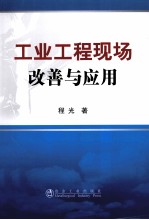
工业工程现场改善与应用PDF电子书下载
- 电子书积分:9 积分如何计算积分?
- 作 者:程光著
- 出 版 社:北京:冶金工业出版社
- 出版年份:2013
- ISBN:9787502462574
- 页数:178 页
1工业工程概述 1
1.1工业工程定义 1
1.2传统与现代工业工程 2
1.2.1 传统工业工程 2
1.2.2现代工业工程 3
1.3工业工程基本职能 5
1.4工业工程主要技术方法 10
1.5工业工程应用 12
1.5.1 工业工程的作用 12
1.5.2工业工程的特点 12
1.5.3 工业工程的主要范围领域 13
1.5.4代表性成果和贡献 13
2基础工业工程的现场应用 14
2.1程序分析方法 14
2.1.1程序分析概述 14
2.1.2 5W1H与ECRS 15
2.1.3工艺程序分析 18
2.1.4流程程序分析 21
2.1.5线路图分析 21
2.2动作效率分析与改善 27
2.2.1 动素分析 27
2.2.2动作经济原则 31
2.3作业测定 32
2.3.1作业测定概述 33
2.3.2时间研究 33
2.3.3预定时间标准 39
2.3.4工作抽样 47
3现场物流设施布局规划 52
3.1物流相关概念 52
3.1.1 物流的产生及发展 52
3.1.2物流的研究对象及行业组成 54
3.1.3物流的基本概念 57
3.1.4物流系统 59
3.2物流系统分析方法 63
3.2.1物流系统分析 64
3.2.2企业物流系统分析内容 64
3.2.3企业物流系统分析方法 64
3.3工厂车间设备布局 67
3.3.1 车间设备布置的原则和基本类型 67
3.3.2 典型车间布置原则 70
3.3.3 系统设施布置规划方法(SLP法) 71
4精益生产与现代工业工程的应用 74
4.1精益生产 74
4.1.1 精益生产方式的产生与发展 74
4.1.2精益生产方式在国内外应用现状 75
4.1.3丰田生产方式 76
4.1.4现场改善 83
4.2生产线平衡 84
4.2.1 生产线平衡概述 84
4.2.2生产线平衡方法 86
5现场管理“5S”概述 88
5.1 “5S”的起源和发展 88
5.2 “5S”的含义和作用原理 89
5.2.1 “5S”的含义 89
5.2.2 “5S”活动作用原理 90
5.3 “5S”活动采用的主要方法 91
5.3.1 目视管理 91
5.3.2标准作业管理 91
5.3.3 PDCA管理循环 91
5.4 “5S”在企业管理活动中的地位 92
5.5 “5S”活动的作用 93
5.6 “5S”活动实施方案 95
5.6.1 “5S”活动的准备阶段 95
5.6.2 “5S”活动方案的实施 98
5.6.3 “5S”活动的标准化管理 103
5.6.4 “5S”活动改善与延伸 106
5.6.5 “5S”活动实施效果预测 108
5.6.6 “5S”推行活动中的认识误区 109
5.6.7企业成功实施“5S”的建议 110
6 目视管理与防错技术 112
6.1 目视管理 112
6.1.1 目视管理的含义及原理 112
6.1.2 目视管理的作用 112
6.1.3 目视管理的工具和方法 114
6.1.4 目视管理要注意的问题 116
6.2防错技术 116
6.2.1 异常管理定义 116
6.2.2异常管理的步骤 116
6.2.3防错法定义 122
6.2.4防错法作用 123
6.2.5防错法原则 124
6.2.6防错法思路 124
6.2.7防错法原理方法 125
7现场改善实例分析 127
7.1某汽车公司及其生产线概况 127
7.1.1 冲压工艺 127
7.1.2涂装工艺 128
7.1.3焊装工艺 129
7.1.4 总装工艺 130
7.2装焊车间生产线的基础效率改善 131
7.2.1 作业时间充实度测定 132
7.2.2程序分析 136
7.2.3 改进结果 148
7.2.4焊装工人的动作分析改善 149
7.3喷涂车间生产线平衡的研究应用 156
7.3.1 喷涂生产线的现状分析 156
7.3.2现状分析 165
7.3.3设定操作人数和标准时间 166
7.3.4改善方案 167
7.4总装车间的现场问题分析与改善 170
参考文献 178
- 《市政工程基础》杨岚编著 2009
- 《钒产业技术及应用》高峰,彭清静,华骏主编 2019
- 《现代水泥技术发展与应用论文集》天津水泥工业设计研究院有限公司编 2019
- 《工程静力学》王科盛主编 2019
- 《英汉翻译理论的多维阐释及应用剖析》常瑞娟著 2019
- 《中央财政支持提升专业服务产业发展能力项目水利工程专业课程建设成果 设施农业工程技术》赵英编 2018
- 《数据库技术与应用 Access 2010 微课版 第2版》刘卫国主编 2020
- 《区块链DAPP开发入门、代码实现、场景应用》李万胜著 2019
- 《化学反应工程》许志美主编 2019
- 《虚拟流域环境理论技术研究与应用》冶运涛蒋云钟梁犁丽曹引等编著 2019
- 《中风偏瘫 脑萎缩 痴呆 最新治疗原则与方法》孙作东著 2004
- 《水面舰艇编队作战运筹分析》谭安胜著 2009
- 《王蒙文集 新版 35 评点《红楼梦》 上》王蒙著 2020
- 《TED说话的力量 世界优秀演讲者的口才秘诀》(坦桑)阿卡什·P.卡里亚著 2019
- 《燕堂夜话》蒋忠和著 2019
- 《经久》静水边著 2019
- 《魔法销售台词》(美)埃尔默·惠勒著 2019
- 《微表情密码》(波)卡西亚·韦佐夫斯基,(波)帕特里克·韦佐夫斯基著 2019
- 《看书琐记与作文秘诀》鲁迅著 2019
- 《酒国》莫言著 2019
- 《指向核心素养 北京十一学校名师教学设计 英语 七年级 上 配人教版》周志英总主编 2019
- 《北京生态环境保护》《北京环境保护丛书》编委会编著 2018
- 《指向核心素养 北京十一学校名师教学设计 英语 九年级 上 配人教版》周志英总主编 2019
- 《高等院校旅游专业系列教材 旅游企业岗位培训系列教材 新编北京导游英语》杨昆,鄢莉,谭明华 2019
- 《中国十大出版家》王震,贺越明著 1991
- 《近代民营出版机构的英语函授教育 以“商务、中华、开明”函授学校为个案 1915年-1946年版》丁伟 2017
- 《新工业时代 世界级工业家张毓强和他的“新石头记”》秦朔 2019
- 《智能制造高技能人才培养规划丛书 ABB工业机器人虚拟仿真教程》(中国)工控帮教研组 2019
- 《陶瓷工业节能减排技术丛书 陶瓷工业节能减排与污染综合治理》罗民华著 2017
- 《全国职业院校工业机器人技术专业规划教材 工业机器人现场编程》(中国)项万明 2019