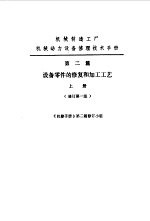
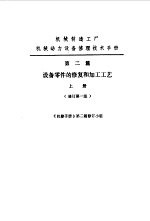
机修手册 第2篇 设备零件的修复和加工工艺 上下PDF电子书下载
- 电子书积分:6 积分如何计算积分?
- 作 者:中国机械工程学会第一机械工业部著编
- 出 版 社:北京:机械工业出版社
- 出版年份:1979
- ISBN:
- 页数:23 页
第十三章橡胶密封件的制造 1
(一)生产的特点 1
(二)合理选择工艺 1
第十二章锻压设备主要零件加工工艺 1
一、锻压设备主要零件的特性 1
二、对毛坯及材料质量的要求 1
(一)毛坯的选择及要求 1
(一)金属喷涂的优缺点 1
一、金属喷涂的特点及其在机修中的应用 1
第五章金属喷涂 1
一、零件加工工艺的特点 1
一、常用的橡胶密封件 1
(一)橡胶密封件的种类及其特点 1
第八章导轨淬火 1
(一)工程塑料的特性 1
一、工程塑料的特性及其在修理中的应用 1
第四章工程塑料在修理中的应用 1
第十四章双金属套的制造 1
一、内层为铜合金的离心浇注 1
(一)铬镀层的特性及其使用范围 1
一、镀铬 1
第三章磨损零件的电镀修复 1
一、分度蜗轮副的测量 1
(一)基本原理 1
(二)电石墨棒式电极的手工操作 1
(一)概述 1
一、铸铁裂损件的电弧冷焊修复 1
第七章焊接修复 1
目次 1
第九章研磨技术 1
一、研磨原理 1
第十章分度蜗轮副的修复 1
第十一章金属切削机床主要零件加工工艺 1
(一)分度蜗轮副的综合测量 1
1.用试切样品齿轮来估计分度蜗轮副的运动精度 1
3.胶粘剂粘接法 1
2.溶剂粘接法 1
1.热熔粘接法 1
(一)粘接方法 1
一、粘接方法和粘接剂的选择 1
第六章粘接修复 1
目次 1
一、机床导轨电接触加热自冷淬火 1
第一章零件修复工艺的选择 1
一、概述 1
(一)强固扣合法 1
一、修复大型铸件的金属扣合法 1
第二章金属扣合和塑性变形修复法 1
1.波形键制造 1
(一)加热炉加热钢套的离心浇注 2
(二)用自制奥氏体和铸铁焊条修复 2
二、零件的磨损极限和修换的一般规定 2
(一)零件的磨损极限 2
(二)金属喷涂在机修及其他方面的应用 2
2.外壳的准备 2
2.超声波探伤 2
1.磁力探伤 2
1.双金属套的材料 2
1.焊条选择 2
(二)材料缺陷的检查 2
(一)工序间的加工余量 2
二、加工工艺的一般技术通则 2
(三)合理选择毛坯 2
1.对机床精度的影响 2
二、材料的可加工性与研磨余量 2
(一)研磨与工件材料的关系 2
2.低压降压器的制造 2
1.电极 2
5.对零件强度的影响 3
(二)橡胶密封件的结构和尺寸 3
2.波形槽加工 3
2.对完成预定使用功能的影响 3
3.对机床性能和操作的影响 3
4.对机床生产率的影响 3
(三)研磨对预加工的要求及研磨余量 3
(二)研磨在修理中的应用 3
1.工件毛糙处理设备 3
3.操作方法 3
4.处理后工件表面情况 3
(二)镀铬工艺 3
二、不对称交流-直流低温镀铁 3
(一)不对称交流-直流镀铁的特点及性能 3
三、主要零件加工工艺 3
2.焊接工艺 3
(一)金属喷涂设备 3
二、金属喷涂设备及喷涂工艺 3
(一)曲轴(偏心轴)加工工艺 3
1.曲轴(偏心轴)的技术条件 3
2.常用材料及热处理 3
3.铆击工艺 4
(一)研磨粉 4
2.主轴及轴瓦 4
2.蜗轮副分度精度的静态综合测量法 4
1.床身、箱体等主要铸件 4
(二)零件修换的一般规定 4
6.对磨损条件恶化的影响 4
三、研磨剂 4
3.偏心轴颈的加工方法 4
1.研磨粉的性能及应用 4
2.用扩张法修复滚轮1 4
5.影响淬火质量因素 4
(二)镀铁工艺 4
1.准备工作 4
3.花键轴 5
4.光杠 5
5.一般轴类零件与轴套 5
2.镀铁规范 5
2.电喷涂设备 5
4.提高轴颈表面光洁度和耐磨性的方法 6
(三)滚轮式电极及机械化操作 6
1.铜滚轮电极几个主要参数 6
6.丝杠、闸瓦、丝杠螺母 6
7.齿轮 6
(二)强密扣合法 6
3.研磨粉的研磨性能 6
3.铜料的准备 6
2.研磨粉的粒度及其选择 6
4.装料 6
5.加热熔化 7
8.蜗轮与蜗杆 7
9.离合器 7
10.皮带轮 7
11.液压元件 7
(三)优级扣合法 7
(二)粘接剂的选择 7
1.加强件的形式 7
6.离心浇注 7
(三)电解液 7
1.电解液的选用 7
2.电解液的配制 7
4.电解液的维护 8
(二)研磨膏 8
1.行星差动传动淬火机 8
(一)修复工艺的分类 8
三、修复工艺的选择 8
2.冷却方式对淬火效果的影响 8
2.加强件的加工 8
5.曲轴(偏心轴)加工应注意的问题 8
(四)电接触淬火设备 8
12.其它零件 8
3.电解液的处理 8
二、设备修理常用粘接剂及其应用 9
1.热扣合件的形状 9
1.环氧树脂的牌号和规格 9
3.蜗轮副分度精度的动态综合测量法 9
(四)热扣合法 9
2.环氧胶粘剂的辅助材料 9
(一)环氧树脂胶粘剂 9
2.热扣合件的计算 9
(二)常用材料的热处理与切削加工性、表面光洁度的关系 9
(二)高频率电流加热钢套的离心浇注 9
(三)研磨液 9
(四)低温镀铁的电源设备 9
1.单相双半波电路 9
3.修复实例 9
1.蜗轮周节差和周节累积误差的测量及计算方法 10
二、塑性变形修复法 10
(二)修复工艺的选择 10
1.选择工艺时应考虑的因素 10
3.气喷涂设备 10
(二)分度蜗轮单个要素的测量 10
四、研磨工具的材料 10
2.可移式自动往复淬火机 10
(一)手工研磨工具 11
1.平面研磨工具 11
五、研磨工具 11
(一)镦粗法 11
3.内圆柱表面研磨工具 11
6.曲轴加工主要工艺路线 11
7.零件加工工艺实例 11
1.镦粗法简介 11
2.用镦粗法改制报废的轴承滚柱 11
2.外圆研磨工具 11
(二)在设备修理及改装时工程塑料的选用 11
2.单相桥式电路 11
(三)电弧加热钢套的离心浇注 12
2.电源设备 12
1.局部电镀槽 12
(一)局部电镀槽和电源设备 12
3.无级变速淬火机 12
三、大件局部镀孔 12
2.用挤压法修复滚动轴承外圈 12
1.冷挤压简介 12
(二)挤压法 12
(三)常用橡胶的性能 12
2.典型零件修复工艺的选择 12
1.扩张法简介 13
(三)扩张法 13
4.简易机械化淬火 13
二、橡胶密封件模具的设计 13
(二)大件局部镀孔的工艺过程 13
1.电解液的配方 13
(一)模具设计的基本要求 13
(二)模具结构及各部位尺寸 13
1.各种密封件模具的结构形式 13
2.模具各部尺寸 13
(三)细长零件热处理吊挂形式 13
2.工艺过程 13
1.双金属套的质量检查 14
3.用扩张法修复滚动轴承内圈 14
3.模具的定位方法 14
二、铸型尼龙零件的制造 14
(五)淬火过程中应注意的几个问题 14
(四)双金属套的质量检查及其分析 14
2.复合材料制件的收缩率 15
3.形状复杂零件 15
1.收缩率变化条件 15
(四)收缩率 15
3.耐油胶制件的收缩率 15
(三)模具材料及技术要求 15
(六)电接触表面淬火工艺的扩大应用 15
1.轴类零件 15
2.长薄零件 15
(四)轴类零件的热校直 15
1.热校直简介 15
1.一般浇注成型 15
(三)镀液的维护与调整 15
(一)铸型尼龙的制备方法 15
(四)带孔主轴和套筒类零件镶堵头及芯轴的几种形式 16
(二)设备及工艺装备 16
1.加热设备 16
2.离心浇注聚合成型 16
4.收缩率的应用计算方法 16
(五)模具设计实例 16
1.骨架油封压模设计 16
2.L形密封环压模 16
(一)概论 16
二、机床导轨表面高频感应淬火 16
(一)无电镀镍的原理及其性能 16
四、无电镀镍 16
2.轴的热校直举例 16
2.双金属套的质量分析 16
2.工艺流程 17
1.工件清洗和毛糙处理 17
(二)金属喷涂工艺 17
二、内层为铜合金的固定浇注 17
2.淬火装置 17
3.感应器 17
3.O形圈压模设计 17
(二)无电镀镍的工艺过程 17
1.镀液的配方 17
1.铸型尼龙的热处理 18
2.添加填充料改性 18
(一)轻便槽电镀法 18
五、长轴的局部镀铬 18
(一)橡胶密封件的工艺过程 18
(六)模具高度的系列化 18
三、压制工艺 18
(二)铸型尼龙的改性 18
三、内层为巴氏合金的离心浇注 18
(一)沸腾熔敷法 19
(二)喷液电镀法 19
(五)中心孔加工 19
(二)硫化条件 19
三、塑料涂敷 19
1.刷镀的原理 20
2.刷镀的特点 20
3.环氧树脂胶粘剂常用的配方 20
(一)刷镀的原理与特点 20
(三)工艺参数 20
六、刷镀 20
(二)火焰喷涂法 21
(三)硫化设备及其特点 21
(四)修边工艺 21
(四)减小导轨淬火变形的措施 21
2.刷镀的工艺装备 21
1.刷镀工艺流程 21
(二)刷镀的工艺流程及工艺装备 21
四、内层为巴氏合金的固定浇注 22
2.半瓦合并加工的方法 22
4.环氧树脂粘接在设备修理中的应用举例 22
1.轴瓦常用材料及毛坯 22
(二)轴瓦加工工艺 22
(五)橡胶密封件常见的缺陷原因和防止措施 22
(一)主轴加工工艺 23
1.主轴技术条件 23
3.轴瓦加工中应注意的问题 23
(三)热熔敷法 23
2.电喷涂 23
三、主要零件加工工艺 23
(三)用普低钢焊条修复 24
2.填充聚四氟乙烯的性能 24
4.圆锥体研磨工具 24
1.聚四氟乙烯的性能 24
(一)聚四氟乙烯及填充聚四氟乙烯的性能 24
四、聚四氟乙烯及填充聚四氟乙烯在机修中的应用 24
2.焊接工艺 25
6.螺纹研磨工具 25
5.球面研磨工具 25
4.零件加工工艺实例 25
1.焊条选择 25
1.氟-4及填充氟-4在机械密封上的应用 26
(二)聚四氟乙烯及填充聚四氟乙烯在机修中的应用 26
2.蜗轮齿圈径向跳动的测量 26
(二)酚醛-缩醛类粘合剂 26
1.酚醛-缩丁醛胶粘剂 26
2.酚醛-缩甲醛胶粘剂 26
(三)酚醛-橡胶胶粘剂 27
1.酚醛-丁腈胶粘剂 27
3.接触斑点的检验 27
(三)滑块、连杆及球头螺杆加工工艺 27
(二)机械研磨工具 27
1.单盘研磨机和双盘研磨机 27
1.常用材料及毛坯 27
2.滑块加工及定位基面的选择 27
2.填充氟-4活塞环及导向环 27
3.连杆加工 28
4.蜗轮齿厚的测量 28
3.气喷涂 28
3.填充聚四氟乙烯塑料轴承 28
4.齿轮研磨机 29
3.钢球研磨机 29
(三)蜗杆的测量 29
2.内圆研磨机 29
2.主轴常用的材料及热处理 30
4.主要加工工艺路线 30
5.零件加工实例 30
2.酚醛-氯丁胶粘剂 30
(一)磨损状态分析 31
二、蜗轮修复方案的选择 31
(四)丙烯酸酯类粘合剂 31
六、研磨方法 31
3.修复实例 31
1.氰基丙烯酸酯类粘合剂 31
2.氰基丙烯酸酯在修理中的应用举例 32
(二)修复方案的选择 32
(五)厌氧性(嫌气性)密封粘合剂 32
1.厌氧性(嫌气性)密封粘合剂的性能与使用 32
(一)平面研磨 32
(三)保证接触斑点及啮合侧隙的方法 33
1.涂层的比重 33
2.涂层的硬度 33
3.涂层材料的抗拉强度 33
(二)外圆研磨 33
(三)金属喷涂层的性质和检验 33
1.影响接触斑点的因素 33
(四)制动键和键套加工工艺 34
1.常用材料与热处理 34
2.制动键偏心轴颈的加工方法 34
4.涂层的平行收缩 34
5.涂层与基体的结合力 34
3.键套半圆孔的加工方法 35
(三)内孔研磨 35
3.主轴加工应注意的问题 35
2.喷枪的安全技术 35
(四)金属喷涂的安全技术 35
1.喷涂时的金属蒸发气体和粉末 35
2.保证接触斑点的工艺方法 35
2.厌氧性(嫌气性)密封粘合剂的使用实例 36
(六)聚氨酯粘合剂 36
1.聚氨酯粘合剂的性能 36
5.零件加工实例 36
三、喷涂使用实例 36
4.典型工艺路线 36
(四)锥体研磨 36
(一)曲轴喷钢 36
(一)概述 37
二、机床导轨划伤或研伤的焊接修复 37
3.保证啮合侧隙的加工方法 37
4.不同材料、不同要求的主轴主要工艺路线 37
5.零件加工工艺实例 37
(六)螺纹研磨 37
(五)球面研磨 37
4.安装调整中应注意的问题 38
2.聚氨酯粘合剂的使用实例 38
(七)GPS-1有机硅胶粘剂 38
(八)F-2含氟材料用胶 38
(二)电弧冷焊修复导轨研伤 39
1.液态密封胶的特点 39
1.两种焊条混合电弧冷焊法 39
(九)高分子液态密封胶 39
5.侧隙的检查和调整方法 39
(二)机床导轨喷钢 39
(七)齿轮研磨 40
2.液态密封胶的分类和选择 40
3.液态密封胶的使用方法 40
3.防止加工中的变形 41
(五)离合器摩擦片加工工艺 41
1.常用材料及毛坯 41
2.齿形加工 41
七、影响研磨精度的因素 41
5.摩擦片加工主要工艺路线 42
4.石棉铜板与摩擦片的装配 42
(四)内孔喷涂 42
1.精滚齿面 42
2.用φ2.5或φ3.2铸308或铸508焊条冷焊 42
(三)松动的电动机端盖轴承壳喷钼压配 42
(一)修复齿形的加工方法 42
三、分度蜗轮的修复方法 42
1.无机粘结剂的调制 43
(十)无机粘结剂 43
(五)内燃机主体、汽缸盖碎缝的修补 43
2.无机粘结剂的特点 43
1.无槽化学镀铜钎焊工艺 43
3.无机粘结剂的使用方法 43
6.零件工艺实例 43
(三)钎焊修复导轨研伤 43
4.无机粘结剂的使用举例 44
2.锡铋合金钎焊导轨划伤 44
1.概述 45
(一)钢制精密淬火零件的电焊修复 45
3.锡基轴承合金钎焊修复导轨研伤 45
三、钢制零件的电焊修复 45
(六)锤杆、锤头及锤杆活塞加工工艺 45
1.锤杆及锤杆活塞技术条件 45
2.剃削齿面 46
2.材料及热处理 46
3.加工中应注意的问题 47
2.焊条制造 47
4.零件加工工艺实例 48
3.焊接工艺 48
3.滚剃齿面 48
4.珩磨齿面 49
4.修复实例 52
1.钻床、镗床主轴与轴套技术条件实例 53
(二)钻、镗床主轴与轴套加工工艺 53
5.焊接修复时应注意的问题 53
(七)活塞环加工工艺 54
1.活塞环技术条件 54
(二)钢制精密轴型零件的电焊修复 54
1.概述 54
2.HB248以下的45号钢精密轴型零件的堆焊修复 55
2.材料与热处理 55
3.承受冲击负荷的45号钢大型轴型零件的焊接修复 57
3.活塞环加工余量的计算 57
2.材料与热处理 58
4.活塞环加工常用夹具 58
(二)刮研修复法 58
5.活塞环加工中应注意的问题 59
3.钻、镗床主轴与主轴套加工应注意的问题 59
7.活塞环主要工艺路线 60
6.活塞环的压缩加工法 60
(一)引起运动误差的因素 61
1.几何偏心引起的周节累积误差规律 61
四、提高蜗轮副运动精度的方法 61
4.大型轴型零件精密表面损伤的焊接修复 61
8.零件加工工艺实例 62
5.机床主轴裂纹的焊接修复 62
4.零件加工工艺实例 62
2.运动偏心引起的周节累积误差规律 63
(一)概述 64
四、细焊丝二氧化碳气体保护电磁振动电弧堆焊 64
(二)细焊丝堆焊设备的工作原理 65
(三)细焊丝堆焊设备的主要装置 66
3.两种偏心误差的抵消方法 67
(二)误差抵消法的应用 69
1.运动偏心eh的大小及方向的确定 70
(四)细焊丝堆焊主要参数的选择 70
2.误差抵消法在加工及装配中的应用 72
(五)细焊丝堆焊的应用范围 72
1.主轴滑动轴承技术条件 73
(三)主轴滑动轴承加工工艺 73
3.易位法及其应用 74
2.主轴滑动轴承常用材料与热处理 74
3.主轴滑动轴承加工应注意的问题 76
4.零件加工工艺实例 78
1.花键轴技术条件(包括花键孔) 83
(四)花键轴加工工艺 83
2.花键轴加工应注意的问题 85
3.零件加工工艺实例 89
2.传动光杆加工应注意的问题 92
1.传动光杆常用材料和原材料的选用 92
(五)传动光杆加工工艺 92
3.零件加工工艺实例 94
1.长丝杠与螺母技术条件 97
(六)长丝杠与螺母加工工艺 97
2.丝杠与螺母常用材料及热处理 98
3.长丝杠与螺母加工应注意的问题 102
4.长丝杠的测量 115
5.不同材料,不同精度和不同热处理要求的丝杠的典型工艺路线 115
6.零件加工工艺实例 117
(七)齿轮加工工艺 127
1.齿轮的技术条件 127
2.齿轮常用材料及热处理 131
3.齿形加工方法 134
4.花键孔的加工 142
5.齿轮定位基面的选择和轮坯的安装 144
7.零件加工工艺实例 149
6.根据不同材料、不同热处理要求的齿轮加工主要工艺路线 149
(八)蜗轮蜗杆加工工艺 167
1.蜗轮蜗杆技术条件 167
2.蜗轮蜗杆常用材料及热处理 169
3.蜗轮蜗杆齿形的加工方法 171
4.蜗轮蜗杆加工中应注意的问题 176
5.提高蜗轮加工精度的方法 181
6.蜗轮蜗杆加工典型工艺路线 181
7.零件加工工艺实例 182
(九)摩擦片加工工艺 195
1.摩擦片技术条件 195
2.摩擦片常用材料及热处理 195
3.摩擦片加工应注意的问题 196
4.零件加工工艺实例 197
- 《市政工程基础》杨岚编著 2009
- 《工程静力学》王科盛主编 2019
- 《中央财政支持提升专业服务产业发展能力项目水利工程专业课程建设成果 设施农业工程技术》赵英编 2018
- 《化学反应工程》许志美主编 2019
- 《绿色过程工程与清洁生产技术 张懿院士论文集精选 上》《绿色过程工程与清洁生产技术》编写组编 2019
- 《软件工程》齐治昌,谭庆平,宁洪编著 2019
- 《高等教育双机械基础课程系列教材 高等学校教材 机械设计课程设计手册 第5版》吴宗泽,罗圣国,高志,李威 2018
- 《化学工程与工艺专业实验指导》郭跃萍主编 2019
- 《天水师范学院60周年校庆文库 新工科视域下的工程基础与应用研究》《天水师范学院60周年校庆文库》编委会编 2019
- 《高等工程教育改革探析》李瀛心,吴价宝著 1997
- 《国学经典诵读》(中国)严琼燕 2019
- 《思维导图 超好用英语单词书》(中国)王若琳 2019
- 《东北民歌文化研究及艺术探析》(中国)杨清波 2019
- 《中国当代乡土小说文库 本乡本土》(中国)刘玉堂 2019
- 《两京烟云》陈诗泳,赖秀俞责任编辑;(中国)千慧 2019
- 《HTML5从入门到精通 第3版》(中国)明日科技 2019
- 《MBA大师.2020年MBAMPAMPAcc管理类联考专用辅导教材 数学考点精讲》(中国)董璞 2019
- 《莼江曲谱 2 中国昆曲博物馆藏稀见昆剧手抄曲谱汇编之一》郭腊梅主编;孙伊婷副主编;孙文明,孙伊婷编委;中国昆曲博物馆编 2018
- 《中国制造业绿色供应链发展研究报告》中国电子信息产业发展研究院 2019
- 《2013数学奥林匹克试题集锦 走向IMO》2013年IMO中国国家集训队教练组编 2013
- 《指向核心素养 北京十一学校名师教学设计 英语 七年级 上 配人教版》周志英总主编 2019
- 《北京生态环境保护》《北京环境保护丛书》编委会编著 2018
- 《高等教育双机械基础课程系列教材 高等学校教材 机械设计课程设计手册 第5版》吴宗泽,罗圣国,高志,李威 2018
- 《指向核心素养 北京十一学校名师教学设计 英语 九年级 上 配人教版》周志英总主编 2019
- 《高等院校旅游专业系列教材 旅游企业岗位培训系列教材 新编北京导游英语》杨昆,鄢莉,谭明华 2019
- 《中国十大出版家》王震,贺越明著 1991
- 《近代民营出版机构的英语函授教育 以“商务、中华、开明”函授学校为个案 1915年-1946年版》丁伟 2017
- 《新工业时代 世界级工业家张毓强和他的“新石头记”》秦朔 2019
- 《智能制造高技能人才培养规划丛书 ABB工业机器人虚拟仿真教程》(中国)工控帮教研组 2019
- 《AutoCAD机械设计实例精解 2019中文版》北京兆迪科技有限公司编著 2019