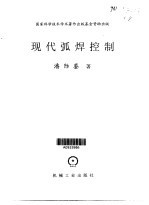
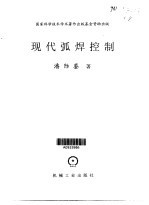
现代弧焊控制PDF电子书下载
- 电子书积分:15 积分如何计算积分?
- 作 者:潘际銮著(南昌大学)
- 出 版 社:北京:机械工业出版社
- 出版年份:2000
- ISBN:7111080874
- 页数:453 页
1.1 引言 3
1.2 等速送丝电弧控制系统 3
第1章 常用弧焊方法动态过程的理论分析 3
1.2.1 弧长自调节性能 6
1.2.2 系统主要参数对动态性能的影响 8
1.3 均匀调节电弧控制系统 9
1.3.1 送丝机构时间常数的影响 12
1.3.2 焊丝直径的影响 12
1.4 均匀调节和自发调节共同作用下的电弧控制系统 12
第2章 弧焊电源的动态特性及其测试方法 15
2.1 弧焊电源动特性的研究现况 15
2.1.1 解析法 15
2.1.2 直接测试法 17
2.2 描述和测试弧焊电源特性的可行性方法 19
2.3.1 简单下降特性电源传递函数的分析 20
2.3 弧焊电源传递函数的理论分析 20
2.3.2 旋转式直流弧焊发电机传递函数的分析 24
2.3.3 模拟型晶体管弧焊电源传递函数的理论分析 27
2.4 弧焊电源传递函数的测试 31
2.4.1 测试装置 31
2.4.2 电源特性的频域测试方法 32
2.4.3 测试结果及分析 32
2.5 弧焊电源传递函数对工艺性能的影响 36
2.6 小结 37
第3章 弧焊动态过程的实验研究 39
3.1 引言 39
3.2 co2焊接 39
3.2.1 电弧模拟器 39
3.2.2 利用电弧模拟器测试弧焊动态过程 42
3.2.3 焊接过程直接测试 44
3.3.1 MIG电弧模拟器的设计 50
3.3 MIG直流焊接 50
3.3.2 电弧模拟器的实验验证 52
3.3.3 MIG焊动态过程的研究 53
3.4 脉冲MIG焊接 55
3.4.1 脉冲MIG电弧模拟器的设计 56
3.4.2 脉冲MIG电弧模拟器的实验验证 57
3.4.3 脉冲MIG焊动态调节过程的研究 59
3.5 小结 59
第4章 QH-ARC101控制法 63
4.1 焊接电弧控制发展现状 63
4.2 QH-ARC101控制法原理 65
4.2.1 双阶梯形外特性 66
4.2.2 双阶梯外特性的组合 67
4.3 双阶梯外特性的实现 67
4.3.2 采用逻辑黾路选通控制电路进行特性之间的自动转换 68
4.3.1 实现双阶梯外特性的方案比较 68
4.3.3 利用反馈选通控制电路实现外特性之间的自动转换 70
4.4 双阶梯外特性的切换电路 73
4.4.1 切换两组控制电路 73
4.4.2 切换同一控制电路的给定值 73
4.5 静态精度和动态性能 74
4.5.1 静态精度与外特性切换的快速性之间的矛盾 75
4.5.2 主电路结构分析 76
4.5.3 QHT-80晶体管焊接电源的恒压特性斜率 81
4.5.4 QHT-80晶体管焊接电源恒流特性斜率 82
4.5.5 QHT-80晶体管焊接电源的动态性能 83
4.6 QHT-80电源电路框图 83
4.7 QH-ARC101控制法的工艺效果 84
4.7.1 不同控制方案的对比试验 84
4.7.2 焊接工艺规范范围 89
第5章 QH-ARC103控制法 91
5.1 引言 91
5.2.1 控制系统方框图 93
5.2 QH-ARC102控制法 93
5.2.2 弧长信号的采样 94
5.2.3 控制系统的特点 94
5.2.4 控制电路的工作原理 95
5.2.5 焊接试验结果 96
5.3 QH-ARC103控制法 96
5.3.1 QH-ARC103控制法原理 97
5.3.2 控制系统线路图 99
5.4 电弧工作点的运动规律和数学分析 108
5.4.1 电弧工作点在陡升电源外特性作用下的运动 108
5.4.2 电弧工作点在运动外特性作用下的运动 111
5.4.3 运动外特性对电弧的控制作用 116
5.5 MIG单面双面成形的闭环自动控制 122
5.5.1 概述 122
5.5.2 MIG焊熔透和控制的分析 123
5.5.3 闭环控制系统原理 124
5.5.4 工艺实验及生产应用 128
第6章 CO2焊接及交流MIG焊的控制 131
6.1 CO2焊接电弧简述 131
6.1.1 H-ARC CO2(A)焊接法工作原理 131
6.1.2 QH-ARC CO2(A)焊接的工艺效果 134
6.1.3 工艺参数及单旋钮操作 136
6.1.4 QH-ARC CO2(B)控制法 141
6.1.5 小结 142
6.2 交流MIG焊的提出 143
6.2.1 直流脉冲MIG焊 144
6.2.2 交流脉冲MIG焊接电弧控制法 148
6.2.3 交流脉冲MIG焊接电源 152
6.2.4 交流脉冲MIG焊工艺实验 162
6.2.5 小结 168
7.1 焊缝跟踪传感器的发展现状 171
7.1.1 接触式传感器 171
第7章 焊缝跟踪传感器 171
7.1.2 电磁传感器 172
7.1.3 光学传感器 172
7.1.4 附加式传感器的共同问题和电弧传感器的特点 173
7.2 电弧传感器的应用现状 174
7.2.1 摆动扫描式MIG/MAG焊接电弧传感器 174
7.2.2 摆动扫描式TIG焊 175
7.2.3 旋转扫描式MIG/MAG电弧传感器 175
7.3.1 电弧传感器基本原理 176
7.3 电弧传感器跟踪原理 176
7.3.2 跟踪系统工作原理 177
7.4 电弧扫描焊炬 179
7.4.1 旋转式扫描焊炬 181
7.4.2 旋转直径的调节 182
7.4.3 电弧扫描位置的检测方法 183
7.5 空心轴电驱动的电弧扫描焊炬RAG-Ⅱ 184
7.5.2 电弧扫描位置与转速测量方法 185
7.5.1 空心轴电动机 185
7.5.3 旋转焊炬调速电路 186
7.5.4 焊炬的设计参数与运转效果 187
第8章 电弧传感器的物理数学模型 189
8.1 静态物理数学模型 189
8.1.1 模型的理论推导 189
8.1.2 模型的实验研究 192
8.1.3 模型的分析 194
8.1.4 小结 196
8.2 动态物理数学模型 196
8.2.1 概述 197
8.2.2 模型的理论推导 197
8.2.3 实验方法与设备 201
8.2.4 实验研究结果与分析 204
8.2.5 小结 213
9.1.1 概述 215
9.1 理想电弧传感系统的信号分析 215
第9章 电弧传感器的信息处理 215
9.1.2 传感过程的数字仿真模型 216
9.1.3 仿真结果及其分析 220
9.2 传感信号特征分析 226
9.2.1 概述 226
9.2.2 变换空间的数学分析 226
9.2.3 传感系统输入信号特征分析 228
9.2.4 特征谐波检测法 231
9.2.5 特征谐波检测法在脉冲焊中的适用性 233
9.2.6 小结 237
9.3 电弧信号滤波处理 237
9.3.1 概述 237
9.3.2 数字滤波原理 238
9.3.3 CO2焊电弧信号滤波处理 242
9.3.4 脉冲焊电弧信号滤波处理 247
9.3.5 小结 249
9.4 焊接过程扫描电弧的信息处理 249
9.4.1 坡口扫描特征向量的正交处理 249
9.4.2 扫描电弧传感受信号处理 253
9.4.3 扫描坡口的偏差检测 255
9.4.4 脉冲焊接扫描电弧信号处理 259
9.4.5 小结 262
第10章 以电弧为传感器的自动跟踪焊机 263
10.1 引言 263
10.2 常规自动跟踪焊机 263
10.2.1 闭环跟踪系统构成 263
10.2.2 跟踪控制方法 267
10.2.3 软件系统功能及设计 268
10.2.4 闭环跟踪实验结果 269
10.2.5 工业应用实例 271
10.3.1 焊接小车 274
10.3 自由爬行式自动跟踪焊机 274
10.3.2 微机控制系统 283
10.3.3 焊车转弯实时模糊控制法原理 288
10.3.4 转变模糊控制系统的建立 291
10.3.5 模糊转弯控制系统的调试与实焊结果 295
第11章 焊接温度场图像比色检测法原理 301
11.1 引言 301
11.1.1 焊接温度场检测方法及研究现状 301
11.1.2 现有红外辐射测量焊接温度场方法中存的主要问题 304
11.2 图像比色测温系统的理论基础及分析 305
11.2.1 红外辐射在电磁波谱中的位置 305
11.2.2 黑体辐身几个基本定律 306
11.2.3 灰体辐射 309
11.2.4 两种辐射测温方案及比较 309
12.1 红外摄像装置 315
12.1.1 几种摄像装置的比较 315
第12章 图像比色测温法的实验论证 315
12.1.2 CCD摄像器件的光学响应特性 317
12.2 实验用比色测温传感器 317
12.2.1 滤光片的选择 317
12.2.2 传感器的结构 318
12.3 图像比色测温系统 320
12.3.1 系统的构成 320
12.3.2 图像比色检测温度场的基本过程 321
12.4 比色测温系统的数学方法标定 322
12.3.3 图像去噪声处理 322
12.5 系统数学方法标定结果的检验 323
12.5.1 Gleeble-1500热模拟装置简介 323
12.5.2 数学方法标定结果的检验及实验标定 324
12.5.3 实验标定结果的应用范围 327
12.6 新造图像比色测温系统的标定方法及步骤 327
12.7 材料、距离、表面状况对测温的影响 328
12.7.1 材料对测温结果的影响 328
12.7.2 距离对测温的影响 329
12.7.3 材料表面状况对测温结果的影响 330
第13章 图像比色测温系统的设计 331
13.1 引言 331
13.2 焊接热辐射成像系统 331
13.3 双色热图像测温法的理论分析 333
13.3.1 多色测温法 333
13.3.2 双色热图像测温法 336
13.4 焊接温度场的分区处理 337
13.4.1 ICCD的动态范围 337
13.4.2 温度场分区处理 338
13.4.3 动态范围对温度场分区的影响 340
13.5 波长的设计 341
13.5.1 双色热图像灰度比值响应模拟计算 341
13.5.2 双色波长的选择 343
13.6 传感器设计 348
13.6.1 结构选择 348
13.6.2 器件选择 349
13.6.3 双色盘及滤光片设计 350
13.6.4 双色热图像信号的获取及控制 351
13.7 各个系统因素对测温的影响 353
13.7.1 测量材料性质、表面状况对测温影响 353
13.7.2 测量距离对测温的影响 356
13.7.3 ICCD及透镜参数对测温的影响 357
13.8 传感系统的标定 359
13.8.1 离线标定 359
13.8.2 在线标定 360
13.8.3 小结 361
第14章 焊接温度场实时检测与应用 363
14.1 焊接温度场实时检测 363
14.1.1 焊接温度场实时采集 364
14.1.2 焊接温度场信息处理 365
14.1.3 各区域温度场连接 366
14.2.1 双椭圆高斯热源模型 367
14.2 利用检测结果建立焊接温度场理论模型 367
14.2.2 焊接温度场理论计算与实时检测的比较 372
14.3 不同焊接规范的温度场实时检测与理论计算 374
14.3.1 不同焊接电流时焊接温度场的分布 374
14.3.2 不同焊接速度时焊接温度场的的分布 375
14.4 焊接热循环参数提取 376
14.4.1 工件背面热循环参数获取 376
14.4.2 二维焊接温度场外推发布 378
14.5 三维焊接温度场分布 379
14.5.1 三维焊接温度场分布 379
14.5.2 三维焊接温度场分布校验 380
14.6 焊接熔透闭环控制 381
14.6.1 熔透闭环控制 381
14.6.2 控制系统的仿真分析 383
14.6.3 控制系统性能及工艺实验 386
14.7 小结 392
15.1 焊缝识别及机器人路径规划 395
第15章 弧焊机器人视沉系统及路径自动规划 395
15.1.1 弧焊机器人路径规划及相关技术的研究综述 396
15.1.2 焊缝二维图像识别 397
15.1.3 焊缝三维坐标的经典算法和神经网络算法 400
15.1.4 焊缝三维坐标算法——直线-点匹配法 404
15.1.5 机器人路径规划结果 408
15.2 自动规划路径的弧焊机器人 409
15.2.1 弧焊机器人的设计 409
15.2.2 弧焊自动跟踪用视觉系统 414
15.2.3 摄像机标定 417
15.2.4 机器人焊接与视觉系统的接口 428
15.2.5 实际焊接 431
15.2.6 小结 433
参考文献 434
索引 448
- 《大学计算机实验指导及习题解答》曹成志,宋长龙 2019
- 《大学生心理健康与人生发展》王琳责任编辑;(中国)肖宇 2019
- 《大学英语四级考试全真试题 标准模拟 四级》汪开虎主编 2012
- 《大学英语教学的跨文化交际视角研究与创新发展》许丽云,刘枫,尚利明著 2020
- 《复旦大学新闻学院教授学术丛书 新闻实务随想录》刘海贵 2019
- 《大学英语综合教程 1》王佃春,骆敏主编 2015
- 《高含硫气藏开发腐蚀控制技术与实践》唐永帆,张强 2018
- 《大学物理简明教程 下 第2版》施卫主编 2020
- 《大学化学实验》李爱勤,侯学会主编 2016
- 《中国综合性大学法语学科表征研究》田园著 2019
- 《高等数学试题与详解》西安电子科技大学高等数学教学团队 2019
- 《重庆市绿色建筑评价技术指南》重庆大学,重庆市建筑节能协会绿色建筑专业委员会主编 2018
- 《刘泽华全集 先秦政治思想史 下》刘泽华著;南开大学历史学院编 2019
- 《高等数学 上》东华大学应用数学系编 2019
- 《江苏中小企业生态环境评价报告》南京大学金陵学院企业生态研究中心 2019
- 《国学 第6集》四川师范大学中华传统文化学院四川省人民政府文史研究馆 2018
- 《西中有东》华大学国学院编;(美)包华石;王金凤译 2019
- 《江苏中小企业生态环境评价报告 2016》南京大学金陵学院企业生态研究中心 2017
- 《江苏中小企业生态环境评价报告 2017》南京大学金陵学院企业生态研究中心 2018
- 《闻声知道 古琴文化读本》厦门大学汉语国际推广南方基地,龙人古琴研究院 2018
- 《指向核心素养 北京十一学校名师教学设计 英语 七年级 上 配人教版》周志英总主编 2019
- 《北京生态环境保护》《北京环境保护丛书》编委会编著 2018
- 《高等教育双机械基础课程系列教材 高等学校教材 机械设计课程设计手册 第5版》吴宗泽,罗圣国,高志,李威 2018
- 《指向核心素养 北京十一学校名师教学设计 英语 九年级 上 配人教版》周志英总主编 2019
- 《高等院校旅游专业系列教材 旅游企业岗位培训系列教材 新编北京导游英语》杨昆,鄢莉,谭明华 2019
- 《中国十大出版家》王震,贺越明著 1991
- 《近代民营出版机构的英语函授教育 以“商务、中华、开明”函授学校为个案 1915年-1946年版》丁伟 2017
- 《新工业时代 世界级工业家张毓强和他的“新石头记”》秦朔 2019
- 《智能制造高技能人才培养规划丛书 ABB工业机器人虚拟仿真教程》(中国)工控帮教研组 2019
- 《AutoCAD机械设计实例精解 2019中文版》北京兆迪科技有限公司编著 2019