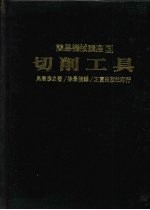
1切削加工所使用之切削工具 1
1.1切削工具的发展 1
1.2切削工具的分类 2
(a)依据切削工具作用於工作件之运动而分类 2
(b)依据使用机械及加工内容而分类 3
2切削的现象 4
2.1切削的出现方式 4
2.1.1刀具的作用 4
2.1.2剪断角φ 4
2.1.3切削的出现方式 5
(a)流出形 6
(b)剪断形 6
(c)撕裂形 6
(d)龟裂形 6
2.2胶附层 7
2.3加工面的粗度 9
2.3.1加工面的状态 9
2.3.2理想的加工面粗度 9
2.3.3加工面粗度 11
(a)切屑与胶附层的影响 11
(b)工作机械、工具及工作件的振动 12
2.4切削抵抗 12
2.4.1切削抵抗的状态 12
2.4.2影响切削抵抗的要素 13
(a)工作件 13
(b)切削面积 13
(c)刀具的後斜角与刀尖的形状 14
(d)切削速度 14
(e)切削油剂 14
(f)进入角 14
2.4.3切削抵抗的测定 16
2.5切削温度 16
2.6材料的被削性 17
(a)钢 18
(b)铸铁 18
(c)铝合金 19
(d)钢合金 19
2.7 切削中之振动 19
(a)工作机械 19
(b)工作件 20
(c)刀具 20
(d)切削条件 20
2.8切削油剂 20
2.8.1切削油剂对於切削的作用 20
2.8.2切削油剂必备的性质 21
2.8.3切削油剂的种类及用途 21
(a)不水溶性切削油 21
(b)水溶性切削油 22
2.8.4切削油剂的选择 23
3切削工具的要素与切削条件 25
3.1切削工具的材料 25
3.1.1 切削工具材质的特性 25
3.1.2合金工具钢 26
3.1.3高速度钢 26
(a)钨高速度钢 26
(b)钴高速度钢 26
(c)低碳素高钴高速度钢 26
(d)钼高速度钢 27
3.1.4烧结碳化物 27
(a)烧结碳化物的材种 27
(b)烧结碳化物的使用选择基准 29
3.1.5陶磁工具 30
3.1.6其他的切削工具材料 35
(a)铸造合金 35
(b)时效硬化合金 36
(c)金刚石 37
3.2切削工具的刀锋形状 37
3.3切削工具的寿命 37
3.3.1切削工具寿命的判定 38
(a)由加工面所生之白辉带来判定 38
(b)刀尖之一定量的摩耗 38
(c)所定的加工尺寸能保持的时间 38
(d)切削抵抗的变化 39
3.3.2切削工具寿命与其他要素之关系 39
3.4切削条件 41
3.4.1切削速度 41
(a)影响切削速度的要素 41
(b)切削速度的实用式 42
(c)切削时之切削速度 43
3.4.2进给与切削深度 44
(a)进给 44
(b)切削深度 44
4车削用刀具 45
4.1车刀的构成要素 45
4.2车刀的形状与角度 46
4.2.1车刀的形状 46
(a)构造上的分类 46
(b)由形状之分类 47
(c)由用途或机能分类 48
(d)由刀部材质分类 52
(e)车刀的称呼 52
4.2.2车刀的刀尖角度 52
(a)斜角度 53
(b)让角 54
(c)隙角 55
(d)侧锋角 55
(e)前锋角 55
(f)刀尖角 55
(g)後斜度 55
4.2.3车刀的有效角 56
(a)安装角 56
(b)进入角 56
(c)刀具角 56
(d)有效後斜角及有效让角 57
(e)有效前锋角 57
(f)切削角 57
4.2.4车刀的刀尖形状表示 57
4.3切削条件 58
4.4切削力与动力 60
4.4.1切削力 60
4.4.2切削动力 60
4.5碳化物车刀 61
4.5.1碳化物车刀的切削需考虑之点 61
4.5.2车刀的形状、尺寸、材种的选择 65
4.5.3刀尖的形状与角度 65
(a)刀尖的形状 65
(b)刀尖的角度 65
4.5.4刀片的安装方法 66
(a)碳化物刀片的硬焊 66
(b)碳化物刀片的机械性夹持方法 68
4.5.5断屑器 70
(a)磨槽形 70
(b)夹紧形 71
4.5.6刚性与振动 71
4.6车刀的摩耗与研磨 72
4.6.1车刀的摩耗 72
(a)刀腹的异常摩耗 73
(b)斜角面的异常摩耗 73
(c)缺口,微剥 73
(d)硬焊裂痕 74
4.6.2车刀的再研磨与更换之时期 74
4.6.3车刀的再研磨 75
(a)适当之磨轮 75
(b)磨床 76
(c)研磨作业 76
(d)研磨裂痕的防止 78
4.7利用碳化物车刀的高能率切削 78
4.7.1高速切削 78
4.7.2高温切削 79
(a)高温切削之优点、缺点 79
(b)加热的方法 81
4.7.3高进给切削 82
(a)可雷索夫车刀 82
(b) SWC车刀 83
4.7.4碳化钛车刀的切削 84
4.7.5陶磁刀具的切削 84
5平铇削、形铇削与插削用刀具 87
5.1加工的状态 87
5.2铇刀的构成要素与形状 88
5.2.1铇刀的构成要素 88
5.2.2铇刀的形状 88
(a)铇刀的种类 88
(b)刀柄 88
(c)铇刀的刀尖角度 89
5.3切削条件 89
6钻头与搪孔刀具 91
6.1钻头与搪孔刀具的加工状态 91
6.2钻头的构成要素与形状 92
6.2.1钻头的构成要素 92
6.2.2钻孔刀具的种类 93
(a)钻头的分类 93
(b)特殊钻头 93
6.2.3钻头的形状 95
(a)钻头的切边 95
(b)钻头的间隙 95
(c)钻头的角度 95
(d)钻头切边的切削状况 96
6.3钻头的切削条件 97
(a)切削速度 97
(b)进给 99
(c)切削深度 99
(d)切削油剂 99
(e)加工面的粗度与精度 99
6.4钻头的切削力与动力 100
6.4.1切削力 100
6.4.2动力 101
6.5搪孔切削工具构成要素与形状 101
6.5.1搪孔用刀具 101
(a)构成要素 101
(b)搪孔刀具的形状 101
(c)刀尖角度 102
(d)切削条件 103
6.5.2鱼眼坑用刀具 103
(a)构成要素 103
(b)鱼眼坑刀具的形状 104
(c)鱼眼坑刀具的刀尖形状 104
6.6钻头的摩耗及研磨 104
6.6.1钻头的摩耗 104
6.6.2钻头的研磨 105
(a)圆锥面研磨法 105
(b)十字形研磨法 106
(c)蜗旋静点研磨法 107
(d)西洛研磨法 107
(e)断屑器 108
(f)再研磨 108
6.7碳化物钻头 109
7铰刀 111
7.1铰刀的加工状态 111
7.2铰刀的构成要素与形状 111
7.2.1铰刀的构成要素与各部名称 111
7.2.2铰刀的形状 111
(a)铰刀的分类 112
(b)铰刀刀锋的形状 115
(c) 刃数及分度方法 116
(d)螺旋刀锋 116
(e)刀锋的角度 116
7.3切削条件 117
7.4铰刀的摩耗与再研磨 118
7.5碳化物铰刀 118
8 铣刀 120
8.1铣刀的加工状态 120
8.1.1上铣法与下铣法 121
(a)上铣法 121
(b)下铣法 121
(c)正面铣削 122
8.2铣刀的构成要素与形状 122
8.2.1铣刀的构成要素与各部之名称 122
8.2.2铣刀的分类 123
(a)从构造上分类 123
(b)从形状上分类 123
(c)从形状详细的分类 123
(d)材质上的分类 127
8.2.3铣刀的形状 128
(a)铣刀的直径 128
(b)铣刀的刃形 128
(c)铣刀的刃数 130
(d)铣刀的螺旋角 130
(e)铣刀刀锋的角度 130
(f)铣刀的有效角 133
8.3切削条件 134
8.3.1切削速度 134
8.3.2切削深度 134
8.3.3进给 135
8.4 切削力与动力 136
8.4.1切削量 136
8.4.2切削力 137
8.4.3动力 138
8.5铣刀的加工面 138
8.6用碳化物铣刀的高能率切削 139
8.6.1碳化物铣刀 139
(a)碳化物铣刀的种类 139
(b)从形状分类 140
8.6.2高能率切削 140
8.7铣刀的摩耗与再研磨 143
9拉刀 146
9.1拉刀的加工状态 146
9.2拉刀的构成要素与形状 147
9.2.1拉刀的构成要素与各部名称 147
9.2.2拉刀的分类 147
(a)依使用机械的驱动方法而分类 147
(b)由作业内容而分类 147
(c)从构造上分类 148
(d)依加工零件的形状而分类 148
9.2.3拉刀的形状 148
(a)安装部 148
(b)前端导引部 149
(c)从端导引部及保持部 149
(d)刀尖的形状 149
(e)刀锋数 150
(f)刀槽 150
(g)刀锋的角度 151
(h)刀背(land) 152
(i)断屑器 152
9.2.4切削方法与切削条件 152
(a)切削方法 152
(b)切削条件 152
9.2.5切削力与动力 153
9.2.6拉刀的摩耗与再研磨 153
10切齿用切削工具 155
10.1齿轮的要素 155
10.1.1齿轮的各部名称 155
10.1.2渐开线齿形 157
10.1.3齿轮齿形的清角与移位齿轮 157
10.1.4齿轮的种类 158
10.2齿轮的切齿原理与其状态 158
10.2.1成形切齿法 158
10.2.2创成切齿法 160
(a)用齿条形铣刀创成切齿 160
(b)滚齿刀的创成切齿 161
(c)小齿轮铣刀的创成切齿 161
(d)直形伞齿轮的创成切齿 162
10.3成形刀具 163
(a)渐开线铣刀 163
(b)端铣刀 163
10.4创成刀具 164
10.4.1齿条铣刀 164
(a)齿条铣刀的种类 164
(b)齿条铣刀的形状 165
10.4.2滚齿刀 166
(a)滚齿刀的各部名称 166
(b)滚齿刀的种类 166
(c)滚齿刀的齿形 169
(d)滚齿刀的条数 170
(e)刀槽 170
(f)後斜角与让角 171
(g)外径及孔径 171
(h)切削条件 171
10.4.3小齿轮铣刀 172
(a)小齿轮铣刀的种类 172
(b)小齿轮铣刀的齿形 173
(c)刀锋的角度、後斜角、侧让角以及前让角 173
(d)齿形的整形 173
(e)铣刀的齿数 174
(f)切削条件 174
10.4.4伞齿轮用铣刀 175
(a)直刃伞齿用G形铣刀 175
(b)其他伞齿轮用铣刀 175
10.5剃削刀具 175
10.5.1剃削作用 176
10.5.2剃削铣刀的种类 178
10.5.3剃削铣刀的形状 178
(a)齿数 178
(b)铣刀的宽度 178
(c)锯齿 178
(d)齿形的修正 178
10.5.4切削条件 179
10.6切齿用切削工具的摩耗与再研磨 179
11螺纹之切削工具 182
11.1螺纹的要素 182
11.2螺纹的切削作用 183
(a)车刀之切削作用 184
(b)螺丝攻的切削作业 184
11.3切削螺纹用之刀具 185
(a)单锋牙刀 185
(b)多锋牙刀 185
11.4螺纹加工用铣刀 186
(a)单锋铣刀 186
(b)多锋螺纹铣刀 187
(c)切削条件 187
11.5螺模头螺纹刀 187
(a)径向形 188
(b)切线形 188
(c)圆形 190
11.6螺丝攻 190
11.6.1螺丝攻的种类 190
(a)等径手螺丝攻 190
(b)增径手螺丝攻 191
(c)枪管螺丝攻 191
(d)机械螺丝攻 191
(e)管用螺丝攻 191
(f)无槽螺丝攻 192
(g)其他 192
11.6.2螺丝攻的形状及各部名称 193
11.6.3螺丝攻的导孔 193
11.7螺模 193
11.7.1螺模的种类 194
(a)螺丝切削用圆螺模 194
(b)固定螺模 194
(c)分件螺模 194
(d)其他 194
11.7.2螺模的形状与各部名称 195
12研磨磨轮 196
12.1磨轮的构成 196
12.1.1磨轮的构成 196
12.1.2研磨作用 197
(a)磨粒切削深度 197
(b)研磨的现象 198
(c)研磨抵抗 199
12.2磨轮的要素 200
12.2.1磨粒的种类 200
12.2.2磨粒的粒度 202
12.2.3结合剂的种类 202
12.2.4结合度 204
12.2.5组织 204
12.3磨轮的形状与尺寸以及表示 205
12.3.1磨轮的形状与尺寸 205
12.3.2磨轮的表示 205
12.4金刚石磨轮 208
12.4.1结合剂的种类 208
(a)金属结合剂 208
(b)树脂结合剂 208
(c)熔合结合剂 208
12.4.2金刚石磨轮的表示方法 208
12.4.3磨轮的形状与使用条件 209
12.5磨轮的选择 209
12.5.1依据工作件、作业条件选择磨轮 209
(a)研磨材的选择要领 209
(b)粒度、结合度以及组织的选择要领 210
12.5.2以JIS为基准的研磨磨轮选择标准 211
(a)对於切削工具(碳化物)的选择标准 211
(b)对切削工具(工具钢)的选择标准 214
(c)对於一般金属材料的选择标准 214
12.6加工状态与研磨加工 214
12.6.1各种研磨加工 214
(a)圆柱研磨 214
(b)内面研磨 214
(c)平面研磨 215
(d)无心研磨 216
12.6.2研磨条件 217
(a)磨轮的圆周速度 217
(b)工作件的圆周速度 217
(c)进给 218
(d)研磨裕度与切削深度 219
(e)研磨油剂 220
12.7研磨面的粗度 220
12.7.1加工面粗度 220
12.7.2研磨面的缺陷 221
(a)研磨裂痕与研磨烧焦 221
(b)颤纹 221
(c)进给痕迹 222
12.8磨轮的安装及修整 222
12.8.1磨轮的安装 222
(a)磨轮的检查 222
(b)磨轮的安装 222
(c)磨轮的平衡 222
12.8.2磨轮的修整 223
- 《管理者的思维工具》(美)詹姆斯.曼特罗(JamesManktelow)朱利安·伯金肖(JulianBirkins 2019
- 《万物探索 交通工具》焦庆锋主编 2018
- 《常用工具软件立体化教程》谭桂华,王伟,彭凯 2019
- 《近代文科工具书 25》王强主编 2015
- 《工具,还是武器?=TOOLS AND WEAPONS THE PROMISE AND THE PERIL OF THE DIGITAL AGE》(美)布拉德·史密斯 2020
- 《设计工具与表现》(日)清水吉治著 2019
- 《高等学校“十三五”规划教材 软件测试技术与工具应用》(中国)王妍 2019
- 《书法篆刻工具书系列 常用鸟虫篆书法字典》樊中岳,陈大英 2019
- 《国外科技文献检索工具简介国外标准文献》王骏初等编 1983
- 《普通高等教育规划教材 创新创业实用管理工具与方法》(中国)康桂花,姚松 2019
- 《海明威书信集:1917-1961 下》(美)海明威(Ernest Hemingway)著;潘小松译 2019
- 《激光加工实训技能指导理实一体化教程 下》王秀军,徐永红主编;刘波,刘克生副主编 2017
- 《羊脂球 莫泊桑短篇小说选》(法)莫泊桑著;张英伦译 2010
- 《公主小姐不想吃饭》(法)克里斯汀·诺曼·维拉蒙著(法)玛丽安娜·巴尔西隆绘苏迪译 2019
- 《风涛》(日)井上靖著;覃思远译 2019
- 《凯恩斯文集 第13卷 社会、政治和文学论集》严忠志译 2018
- 《危险化学品经营单位主要负责人和安全生产管理人员安全培训教材》李隆庭,徐一星主编 2012
- 《商务英语口译教程 第3版》朱佩芬,徐东风编著 2017
- 《钢渣梯级利用技术》徐国平,黄毅,程慧高,万迎峰,林路 2016
- 《弗里达·卡罗》(加)苏珊娜·巴贝扎特著;朱一凡,玩静雯,李梦幻译 2020
- 《中国十大出版家》王震,贺越明著 1991
- 《近代民营出版机构的英语函授教育 以“商务、中华、开明”函授学校为个案 1915年-1946年版》丁伟 2017
- 《国之重器出版工程 云化虚拟现实技术与应用》熊华平 2019
- 《新闻出版博物馆 总第33期》新闻出版博物馆 2018
- 《哈佛出版史》董唯责编;李广良,张琛译者;(美)马克斯·豪尔 2019
- 《新时代期刊编辑出版的理论与实践》吴厚庆 2019
- 《上海市订购苏联情报出版物联合目录与索引 1983》上海科学技术情报研究所 1983
- 《中国骨干旅游高职院校教材编写出版项目 中国饮食文化》邵万宽 2016
- 《出版词典》《出版词典》(修订本)编委会编 2014
- 《晚明士人与商业出版》何朝晖著 2019