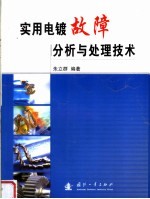
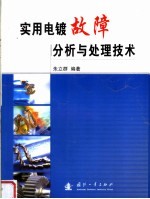
实用电镀故障分析与处理技术PDF电子书下载
- 电子书积分:9 积分如何计算积分?
- 作 者:朱立群编著
- 出 版 社:北京:国防工业出版社
- 出版年份:2007
- ISBN:7118051675
- 页数:184 页
第1章 常见电镀故障及处理电镀故障的基本原则与方法 1
1.1 电镀故障 1
1.1.1 零件表面电镀处理的重要性 1
1.1.2 电镀故障 1
1.1.3 电镀新工艺应用与电镀故障 3
1.1.4 电镀故障的处理思路与原则 4
1.2 影响电镀出现故障的主要因素 9
1.2.1 零件镀覆前的质量控制 9
1.2.2 镀覆中的质量控制 15
1.2.3 水与电镀故障 15
1.2.4 其他方面的质量控制 16
1.3 查找电镀故障起源的实用方法 16
1.3.1 跳越试验 17
1.3.2 对比试验 17
1.3.3 改变零件装挂位置试验 17
1.3.4 小型镀槽试验 20
1.4 电镀故障的预防和控制 26
1.4.1 生产中电镀故障的预防 26
1.4.2 识别电镀故障中的假象 27
第2章 镀锌工艺中的故障分析与处理 30
2.1 锌酸盐镀锌常见故障现象及可能原因 30
2.1.1 镀层起泡发脆、结合力差 30
2.1.2 镀层结晶粗糙 31
2.1.3 镀层沉积速率慢 31
2.1.4 镀层光亮不均匀 31
2.1.5 镀层花斑发雾 31
2.1.6 镀层发暗或钝化无光泽 31
2.1.7 镀锌阳极出现钝化发黑 31
2.1.8 镀液的分散能力差 31
2.1.9 镀液的深镀(覆盖)能力差 31
2.2 锌酸盐镀锌常见故障现象分析 32
2.2.1 零件制造工序的影响 32
2.2.2 锌酸盐镀锌各工序的影响 33
2.2.3 锌酸盐镀锌液成分及工艺参数的影响 34
2.2.4 镀后钝化与除氢 35
2.3 锌酸盐镀锌工艺的故障原因与处理方法 35
2.3.1 低电流密度区出现黑色或灰色镀层 35
2.3.2 铸铁零件较难沉积上镀锌层 36
2.3.3 镀层呈海绵状 37
2.3.4 镀层结合力差的原因及解决方法 37
2.3.5 沉积速度慢的原因及解决方法 38
2.3.6 镀液中锌含量过快积累和阳极钝化的原因及解决方法 38
2.3.7 镀锌层出现粗糙或粗糙发暗的原因及解决方法 39
2.3.8 镀层钝化膜质量故障(发花、变色、变暗等) 39
2.3.9 锌酸盐镀锌层起泡故障的分析与处理实例 40
2.3.10 锌酸盐镀锌中阳极板引起的故障实例 42
2.4 氯化物镀锌故障原因分析与处理措施 43
2.4.1 零件制造工序的控制 44
2.4.2 镀锌前处理的控制 44
2.4.3 氯化物镀锌工序的控制 45
2.4.4 氯化物镀锌后处理的控制 48
2.5 氯化物镀锌常见故障处理 49
2.5.1 镀层发花或起泡,结合力差 49
2.5.2 镀层光亮度差 49
2.5.3 镀层易烧焦,电流密度开不大 49
2.5.4 镀层粗糙有麻点 49
2.5.5 镀层覆盖能力差,孔内及凹处无镀层 49
2.5.6 镀层灰暗 50
2.5.7 镀层有白雾、黑点 50
2.5.8 光亮剂消耗量增大 50
2.5.9 镀层有条纹 50
2.5.10 综合因素引起的氯化物镀锌故障及处理实例 50
2.5.11 氯化物镀锌液中铬杂质的影响实例 53
2.5.12 电镀钝化后出现的故障和镀锌零件储存期间出现的故障实例 53
第3章 镀铜工艺中的故障分析与处理 55
3.1 硫酸盐镀铜液故障的处理 55
3.1.1 溶液成分的影响 55
3.1.2 水质的影响 58
3.1.3 含磷铜阳极 59
3.1.4 整流电源 59
3.2 光亮酸性镀铜常见故障分析和排除 60
3.2.1 镀层发花或发雾 60
3.2.2 电镀铜时阴极电流下降,电压升高 60
3.2.3 低电流密度区镀层不亮 61
3.2.4 镀层粗糙 62
3.2.5 镀铜层上有麻点 63
3.2.6 镀铜层上有条纹 65
3.2.7 镀层光亮整平性不足 65
3.2.8 杂质的影响和去除 66
3.3 焦磷酸盐镀铜故障的处理 68
3.3.1 镀层粗糙 68
3.3.2 镀层结合力不好 69
3.3.3 镀层上有细麻点或针孔 69
3.3.4 电流密度范围缩小,镀层易烧焦 70
3.3.5 阴极电流效率低,沉积速度慢 71
3.3.6 低电流密度区走位差 71
3.3.7 镀层光泽度差 72
3.3.8 杂质的影响和去除 73
第4章 电镀镍与化学镀镍工艺中的故障处理 75
4.1 电镀镍工艺的故障影响与分析 75
4.1.1 电镀镍故障种类和特点 75
4.1.2 电镀镍故障的影响与原因分析 76
4.2 印制板(PCB)电镀镍工艺中的故障原因与排除 86
4.2.1 麻坑(针孔) 86
4.2.2 粗糙(毛刺) 86
4.2.3 结合力低 86
4.2.4 镀层脆、可焊性差 87
4.2.5 镀层发暗和色泽不均匀 87
4.2.6 镀层烧伤 87
4.2.7 沉积速率低 87
4.2.8 镀层起泡或起皮 87
4.2.9 阳极钝化 87
4.3 化学镀镍溶液故障分析与影响 87
4.3.1 化学镀镍的故障种类 88
4.3.2 化学镀镍常见故障及排除 90
4.4 电镀镍镀液中杂质的影响和去除 90
4.4.1 铜杂质的影响和去除 91
4.4.2 锌杂质的影响和去除 91
4.4.3 铁杂质的影响和去除 92
4.4.4 六价铬的影响和去除 92
4.4.5 硝酸根的影响和去除 92
4.4.6 有机杂质的影响和去除 93
4.4.7 油类杂质的影响和去除 93
第5章 电镀铬常见故障及处理方法 94
5.1 镀铬溶液及工艺参数的影响 94
5.1.1 镀液成分的影响 95
5.1.2 镀铬工艺参数及挂具、电源的影响 97
5.2 电镀装饰铬常见故障及其处理方法 99
5.2.1 电镀铬层发花、呈灰色 99
5.2.2 镀铬后表面有圆圈状不良现象 99
5.2.3 镀铬低电流密度区出现彩虹色和黄色斑渍 100
5.2.4 挂具上层与下层零件烧焦 100
5.2.5 镀铬层粗糙、毛刺或结瘤 100
5.2.6 镀层裂纹 100
5.2.7 镀铬层结合力差 101
5.2.8 硬铬镀层出现针孔 103
5.2.9 镀铬层光亮性差 103
5.2.10 镀铬槽电压偏高 104
5.3 三价铬电镀的常见故障和处理 104
5.3.1 镀液沉淀 104
5.3.2 高电流密度区漏镀和镀层色泽暗、绒毛状条纹 105
5.3.3 低电流密度区镀铬层出现白渍 105
5.3.4 镀层出现棕黑色条纹 105
5.3.5 低电流密度区镀铬出现白斑,高电流密度区镀层剥落 106
5.4 铜/镍/铬多层电镀故障分析与处理 106
5.4.1 铜/镍/铬多层电镀层间脱皮故障原因分析 106
5.4.2 铜/镍/铬多层电镀表面铬层发灰原因分析 108
5.4.3 铜/镍/铬多层电镀毛刺、麻点等故障原因分析 108
第6章 电镀锡工艺故障处理 111
6.1 光亮酸性镀锡常见故障分析和排除 112
6.1.1 镀锡层光亮不够,发雾 112
6.1.2 镀锡层粗糙、不细致、有气流状条纹或有针孔 112
6.1.3 镀锡液浑浊 112
6.1.4 零件小电流处镀层发白发花 113
6.1.5 镀锡层发黄 113
6.1.6 镀锡件出现圈状发黑 113
6.1.7 镀锡层长锡须 113
6.2 酸性光亮镀锡液杂质的影响和去除 114
6.3 碱性镀锡常见故障与排除 115
6.3.1 低电流密度区无镀层 115
6.3.2 镀锡层灰暗,边缘粗糙呈海绵状 116
6.3.3 阳极发黑,析氧严重 116
6.4 实际零件光亮酸性镀锡故障举例 116
6.4.1 镀件下部弯折处发黄、发白、水印 116
6.4.2 零件表面镀层边缘烧焦 116
6.4.3 镀层亮度不均 117
6.4.4 镀层在后加工时发生起皮脱落 117
6.4.5 零件冲孔周围镀层呈白点 118
第7章 合金电镀故障分析与处理 119
7.1 碱性锌镍合金电镀故障分析与处理 119
7.2 锌铁合金电镀故障分析与处理 120
7.2.1 氯化钾光亮锌铁合金电镀故障 120
7.2.2 碱性光亮锌铁合金电镀故障 122
7.3 电镀锡钴合金故障分析与处理 124
7.3.1 零件镀层在高电流密度区云状发雾,低电流密度区露底 124
7.3.2 镀件高电流密度区(尖端或者边缘部位)出现黑块状 125
7.3.3 镀层色泽偏黑,不呈铬色 125
7.3.4 镀液浑浊 125
7.3.5 镀层变色 125
7.4 电镀镍铁合金工艺故障的处理 125
7.4.1 常见故障的分析和纠正 126
7.4.2 镀液成分失调的影响和纠正 129
7.4.3 镀液中杂质的影响和去除 129
7.5 电镀锡铈的故障分析与处理 130
第8章 难镀基体材料电镀故障分析与处理 132
8.1 难镀基体 132
8.1.1 难镀基体分类 132
8.1.2 难镀原因 133
8.1.3 解决措施 134
8.2 锌合金基体材料电镀故障及处理 136
8.2.1 锌合金镀前处理的故障分析 136
8.2.2 锌合金零件酸性光亮镀铜故障分析 141
8.2.3 锌合金零件电镀光亮镍故障分析 141
8.2.4 锌合金零件镀铬、仿金及镀枪色 142
8.2.5 锌合金零件电镀故障实例 142
8.3 塑料电镀故障的处理 143
8.3.1 前处理工序的故障分析与处理 144
8.3.2 化学镀铜、化学镀镍溶液故障分析 146
8.3.3 塑料镀常见故障分析和处理 147
8.3.4 塑料零件故障实例 151
8.4 铝合金零件电镀故障分析与处理 152
8.4.1 影响镀层结合性能的铝合金零件因素 153
8.4.2 镀前预处理对镀层结合性能的影响 153
8.4.3 铝合金零件浸锌的影响 154
8.4.4 预镀铜或者预镀镍的影响 156
第9章 金属零件表面转化膜处理技术故障分析 157
9.1 铝及铝合金硫酸阳极氧化工艺故障分析与处理 157
9.1.1 故障现象与排除措施 157
9.1.2 氧化膜染色不均匀故障的预防措施 161
9.2 钢铁零件磷化工艺故障与排除措施 164
9.2.1 磷化溶液成分的一般控制 165
9.2.2 磷化缺陷及处理措施 165
9.3 钢铁零件氧化的故障分析与处理 167
9.3.1 高温氧化膜层无膜、脱膜 167
9.3.2 零件表面高温氧化膜层出现黄色挂霜或者红色挂灰 167
9.3.3 高温氧化膜层出白斑或在存放时挂白霜 168
9.3.4 高温氧化溶液中NaOH与NaNO2的比例失调 168
9.3.5 钢铁常温氧化膜层发花 168
9.3.6 常温发黑时膜层疏松 168
9.3.7 常温发黑膜层颜色浅 169
第10章 印制电路板孔化电镀故障分析与处理 170
10.1 钻孔工序对印制电路板电镀质量的影响 171
10.1.1 孔口毛刺的产生及去除 171
10.1.2 孔壁粗糙、基材凹坑对镀层质量的影响 172
10.1.3 环氧树脂腻污的成因 172
10.2 避免板钻孔缺陷,提高钻孔质量的途径 172
10.2.1 钻头的质量控制 172
10.2.2 钻头的形状选择 173
10.2.3 钻头排沟槽的长度 173
10.2.4 控制钻孔的工艺参数 173
10.2.5 钻头的寿命控制 173
10.2.6 上盖板、下垫板的使用 173
10.2.7 钻头进入下垫板的深度控制 174
10.3 多层板层压工序的影响 174
10.3.1 层压材料固化作用应完全 174
10.3.2 优化层压工艺,减少粉红圈现象的产生 174
10.3.3 提高黑化层与基材的结合力 175
10.3.4 提高黑化层耐腐蚀能力 175
10.4 印制板孔化电镀工艺的影响 175
10.5 电镀过程中常见的孔化电镀故障分析与处理 176
10.5.1 化学镀铜层结合不牢,在图形转移前擦板导致分层(起皮) 176
10.5.2 化学沉铜一次镀铜加厚后板面有水印 177
10.5.3 化学沉铜后一次镀铜层粗糙 177
10.5.4 孔壁镀铜层出现空洞——“眼镜圈” 177
10.5.5 图形电镀导线高低不平呈台阶状 178
10.5.6 碱性蚀刻后两线条间或图形上有环状或半圆形镀铜层 178
10.5.7 碱性蚀刻后线条上有针孔、凹坑、断线、缺口等现象 178
10.5.8 两线条之间被点状铜层连在一起,产生短路(“碰点”)现象 179
10.5.9 图形镀铜中孔口及大面积铜层表面发白或颜色不均 179
10.5.10 镀铜层烧焦 179
10.5.11 镀铜厚度分布不均匀 179
10.5.12 板面孔口角出现裂缝 180
10.5.13 孔壁镀铜层发花 180
10.5.14 孔内镀层出现节瘤、粗糙现象 180
10.5.15 镀层结合力差,在胶带试验时出现沾铜或“脱壳”现象 180
10.5.16 孔壁镀铜层有破洞露点 181
10.5.17 图形线条上某一点或某一小部位镀层厚度较薄 181
10.5.18 气泡造成的金属化孔镀层空洞 181
参考文献 183
- 《水面舰艇编队作战运筹分析》谭安胜著 2009
- 《分析化学》陈怀侠主编 2019
- 《影响葡萄和葡萄酒中酚类特征的因素分析》朱磊 2019
- 《仪器分析技术 第2版》曹国庆 2018
- 《全国普通高等中医药院校药学类专业十三五规划教材 第二轮规划教材 分析化学实验 第2版》池玉梅 2018
- 《大数据Hadoop 3.X分布式处理实战》吴章勇,杨强 2020
- 《Power BI数据清洗与可视化交互式分析》陈剑 2020
- 《行测资料分析》李永新主编 2019
- 《药物分析》贡济宇主编 2017
- 《土壤环境监测前沿分析测试方法研究》中国环境监测总站编著 2018
- 《市政工程基础》杨岚编著 2009
- 《家畜百宝 猪、牛、羊、鸡的综合利用》山西省商业厅组织技术处编著 1959
- 《《道德经》200句》崇贤书院编著 2018
- 《高级英语阅读与听说教程》刘秀梅编著 2019
- 《计算机网络与通信基础》谢雨飞,田启川编著 2019
- 《看图自学吉他弹唱教程》陈飞编著 2019
- 《法语词汇认知联想记忆法》刘莲编著 2020
- 《培智学校义务教育实验教科书教师教学用书 生活适应 二年级 上》人民教育出版社,课程教材研究所,特殊教育课程教材研究中心编著 2019
- 《国家社科基金项目申报规范 技巧与案例 第3版 2020》文传浩,夏宇编著 2019
- 《流体力学》张扬军,彭杰,诸葛伟林编著 2019
- 《指向核心素养 北京十一学校名师教学设计 英语 七年级 上 配人教版》周志英总主编 2019
- 《北京生态环境保护》《北京环境保护丛书》编委会编著 2018
- 《指向核心素养 北京十一学校名师教学设计 英语 九年级 上 配人教版》周志英总主编 2019
- 《抗战三部曲 国防诗歌集》蒲风著 1937
- 《高等院校旅游专业系列教材 旅游企业岗位培训系列教材 新编北京导游英语》杨昆,鄢莉,谭明华 2019
- 《中国十大出版家》王震,贺越明著 1991
- 《近代民营出版机构的英语函授教育 以“商务、中华、开明”函授学校为个案 1915年-1946年版》丁伟 2017
- 《新工业时代 世界级工业家张毓强和他的“新石头记”》秦朔 2019
- 《智能制造高技能人才培养规划丛书 ABB工业机器人虚拟仿真教程》(中国)工控帮教研组 2019
- 《陶瓷工业节能减排技术丛书 陶瓷工业节能减排与污染综合治理》罗民华著 2017