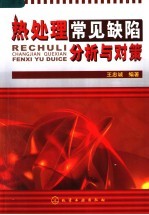
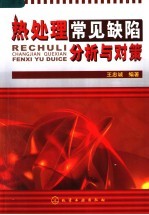
热处理常见缺陷分析与对策PDF电子书下载
- 电子书积分:12 积分如何计算积分?
- 作 者:王忠诚编著
- 出 版 社:北京:化学工业出版社
- 出版年份:2008
- ISBN:9787122011459
- 页数:338 页
第1章 常见热处理缺陷的类型及分析方法 1
1.1 热处理常见的缺陷类型 2
1.1.1 热处理裂纹 5
1.1.2 热处理变形 7
1.1.3 热处理性能不合格 7
1.2 缺陷分析的步骤和方法 7
1.3 热处理缺陷的对策方略 13
第2章 加热过程中产生的缺陷及其对策 17
2.1 氧化与脱碳 17
2.1.1 氧化和脱碳的机理 17
2.1.2 零件加热常用介质的作用和防止氧化和脱碳的措施 24
2.1.3 其他影响零件氧化和脱碳的因素 59
2.1.4 钢铁零件的表面腐蚀 63
2.1.5 零件表面氧化和脱碳的后续处理 64
2.2 过热和过烧 65
2.2.1 过热 65
2.2.2 过烧 69
2.2.3 防止零件过热和过烧的措施 71
2.3 氧化和脱碳实例分析 72
2.3.1 钢板弹簧的氧化和脱碳 72
2.3.2 螺栓的表面脱碳 73
2.3.3 汽车连杆的脱碳 76
2.3.4 热锻40Cr连杆螺栓的局部过烧造成断裂 77
第3章 淬火过程中产生的缺陷及其对策 79
3.1 概述 79
3.2 淬火应力分析 84
3.2.1 热应力 85
3.2.2 组织应力 87
3.3 淬火裂纹 89
3.3.1 淬火裂纹的特征 89
3.3.2 淬火开裂原因和形式 90
3.3.3 淬火裂纹的一般特点 97
3.3.4 影响零件开裂的因素和防止措施 99
3.3.5 其他裂纹 118
3.3.6 导致淬火零件裂纹的淬火加工 129
3.4 淬火变形 130
3.4.1 热处理变形的机理 130
3.4.2 影响零件变形的因素 133
3.4.3 零件热处理变形的规律 152
3.4.4 减小变形的热处理工艺的选择 157
3.4.5 其他防止零件变形的方法 158
3.4.6 工件热处理变形的校直方法 160
3.5 淬火后硬度不均匀、硬度不够 181
3.5.1 淬火后硬度不均匀 182
3.5.2 淬火后硬度不足 183
3.6 工具钢的淬火缺陷 187
3.6.1 碳素工具钢和合金工具钢常见热处理质量缺陷 188
3.6.2 高合金钢和高速工具钢常见热处理质量缺陷 194
3.6.3 工具钢热处理时的基本思路 213
3.7 实例分析 217
3.7.1 圆板牙的热处理及变形的控制 217
3.7.2 65Mn金刚石圆锯片基体的热处理和变形的控制 221
3.7.3 高速钢拉刀热处理变形的控制 223
3.7.4 塞规淬火裂纹及其控制 227
3.7.5 柴油机摆臂轴淬火剥落裂纹和防止措施 228
第4章 回火过程中产生的缺陷及其对策 230
4.1 硬度不足 230
4.1.1 加热温度和保温时间的影响 230
4.1.2 回火温度的影响 231
4.1.3 冷却速度、冷却介质以及化学成分的影响 232
4.1.4 零件表面脱碳 233
4.2 硬度偏高 233
4.3 回火裂纹 235
4.4 回火脆性 237
4.5 实例分析 240
第5章 表面淬火缺陷及其对策 242
5.1 高频淬火缺陷 243
5.1.1 感应淬火的意义和作用 243
5.1.2 感应加热表面质量的检查 245
5.1.3 常见的高频表面淬火缺陷 247
5.1.4 提高高频淬火件性能的措施和要求 259
5.2 电接触加热表面淬火缺陷 260
5.3 火焰加热表面淬火缺陷 262
5.3.1 火焰加热表面淬火的意义和应用 262
5.3.2 火焰加热表面淬火常见缺陷和防止措施 263
5.3.3 影响火焰淬火表面质量的因素 267
5.4 实例分析 268
5.4.1 齿轮的表面淬火开裂 268
5.4.2 60钢轴的高频淬火出现螺旋状软带 269
5.4.3 感应淬火时孔洞的边缘出现淬火裂纹 271
第6章 化学热处理缺陷及其对策 273
6.1 渗碳 273
6.1.1 渗碳的作用 273
6.1.2 渗碳零件的热处理 275
6.1.3 零件渗碳后常见的热处理缺陷和预防措施 281
6.1.4 渗碳零件的变形 286
6.1.5 渗碳零件裂纹形成原因和采取的措施 294
6.1.6 零件渗碳后的机械加工 298
6.2 渗氮 299
6.2.1 对渗氮零件的技术要求 301
6.2.2 零件渗氮的缺陷和防止措施 305
6.3 氮碳共渗 311
6.3.1 气体氮碳共渗 312
6.3.2 液体氮碳共渗 315
6.4 气体碳氮共渗 317
6.5 实例分析 323
6.5.1 齿轮的渗碳畸变 323
6.5.2 渗碳齿轮的磨削裂纹 326
6.5.3 气门液体软氮化后表面腐蚀和粗糙度超差 328
参考文献 336
- 《大数据Hadoop 3.X分布式处理实战》吴章勇,杨强 2020
- 《烧结法处理非常规含铁资源研究》王哲著 2018
- 《无机元素原子光谱分析样品预处理技术》吴瑶庆 2019
- 《农村生活污水处理工艺与技术应用》李灵娜著 2019
- 《中国人民大学研究报告系列 中国水处理行业可持续发展战略研究报告 膜工业卷 3》(中国)郑祥,魏源送,王志伟 2019
- 《工业废水处理工艺与设计》高永编著 2019
- 《常见病百家百方丛书 咳嗽百家百方 第2版》黄庆田 2018
- 《常见病舌象辨证与中医治疗》周幸来主编 2019
- 《工业水处理技术》(中国)赵文玉,林华,许立巍 2019
- 《常见病百家百方丛书 乙肝百家百方 第2版》冯磊,张超 2018
- 《市政工程基础》杨岚编著 2009
- 《家畜百宝 猪、牛、羊、鸡的综合利用》山西省商业厅组织技术处编著 1959
- 《《道德经》200句》崇贤书院编著 2018
- 《高级英语阅读与听说教程》刘秀梅编著 2019
- 《计算机网络与通信基础》谢雨飞,田启川编著 2019
- 《看图自学吉他弹唱教程》陈飞编著 2019
- 《法语词汇认知联想记忆法》刘莲编著 2020
- 《培智学校义务教育实验教科书教师教学用书 生活适应 二年级 上》人民教育出版社,课程教材研究所,特殊教育课程教材研究中心编著 2019
- 《国家社科基金项目申报规范 技巧与案例 第3版 2020》文传浩,夏宇编著 2019
- 《流体力学》张扬军,彭杰,诸葛伟林编著 2019