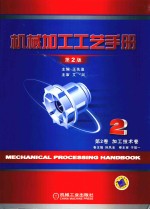
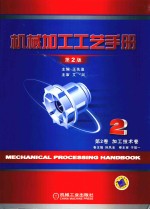
机械加工工艺手册 第2卷 加工技术卷 第2版PDF电子书下载
- 电子书积分:46 积分如何计算积分?
- 作 者:王先逵主编;艾兴主审;孙凤池卷主编;王龙山卷副主编;于骏一卷主审
- 出 版 社:北京:机械工业出版社
- 出版年份:2014
- ISBN:9787111205647
- 页数:2021 页
第1章 车削、镗削加工 3
1.1 车削 3
1.1.1 车床及其技术参数 3
1.卧式车床的型号与技术参数 3
2.立式车床的型号与技术参数 5
3.转塔车床的型号与技术参数 6
4.多刀半自动车床的型号与技术参数 6
5.仿形车床的型号与技术参数 7
6.自动车床的型号与技术参数 11
7.卧式数控车床及车削中心的型号与技术参数 12
1.1.2 典型机床精度验收标准 15
1.普通标准卧式车床 15
2.数控卧式车床 15
1.1.3 车床夹具 20
1.车床夹具技术要求 20
2.车床夹具的装配基准与联系尺寸 22
3.车床夹具典型结构 24
1.1.4 车刀及其辅具 32
1.车刀的分类 32
2.车刀结构 32
3.车刀几何参数的选用 33
4.焊接式车刀 37
5.机夹车刀 38
(1)可转位车刀的夹紧形式及特点 38
(2)可转位车刀刀片的型号 38
(3)可转位车刀的型号 41
6.机夹切断刀(切槽刀) 42
7.机夹螺纹车刀 43
8.成形车刀 44
9.车刀辅具 44
1.1.5 车削用量选择与车削参数计算 44
1.车削用量选择 44
2.车削参数的计算与修正 48
(1)车削速度的计算及修正 48
(2)车削力与车削功率的计算及修正 51
1.1.6 典型车削工艺 53
1.卧式车床加工 53
2.立式车床加工 69
(1)加工表面 69
(2)工件的装夹、定位和测量 71
(3)立式车床典型零件加工 71
(4)立式车床常见加工质量问题与解决措施 75
3.其他车削加工 75
(1)转塔车床加工 75
(2)仿形车床加工 77
(3)多刀车床加工 82
(4)自动车床加工 82
1.1.7 数控车床加工 82
1.数控车床用途 82
2.数控车床分类 82
3.数控车床选用 83
(1)床身和导轨 83
(2)主轴箱 84
(3)液压夹盘 85
(4)刀架系统 85
(5)进给传动系统 86
(6)尾座 87
(7)对刀装置 87
4.数控车削的加工工艺与工装 87
(1)数控车床加工的主要对象 87
(2)数控车削加工的工艺分析 87
(3)夹具的选择、工件装夹方法的确定 88
5.车削用量的选择 88
6.对刀点、换刀点的确定 89
7.数控车削程序的编制 89
(1)运动指令中的坐标轴说明 89
(2)编程注意事项 89
(3)坐标系的设定 89
(4)数控车床基本编程指令 90
8.数控车削加工实例 98
(1)数控车床的操作 98
(2)数控车削实例 99
9.数控车床的发展 104
1.2 镗削 104
1.2.1 镗床类型及技术参数 104
1.卧式镗床的类型和技术参数 104
2.坐标镗床的类型和技术参数 108
3.金刚镗床的类型和技术参数 111
1.2.2 镗床附件 112
1.基本附件 112
2.支承类附件 112
3.回转工作台 114
1.2.3 镗刀及其辅具 118
1.镗刀分类 118
2.刀杆与镗杆 120
1.2.4 镗床夹具 123
1.镗模导向装置的形式和特点 123
2.镗套与衬套 124
3.镗床夹具典型结构 131
1.2.5 镗削用量 132
1.卧式镗床的镗削用量 132
2.金刚镗床的精密镗削用量 133
3坐标镗床镗削用量和加工精度 134
1.2.6 镗削加工工艺 135
1.卧式镗床加工 135
(1)卧式镗床基本工作范围 135
(2)卧式镗床上工件的定位方法和定位精度 135
(3)卧式镗床加工中工件的夹紧 140
(4)卧式镗床加工中的测量 140
(5)卧式镗床镗孔调刀与对刀方法 140
(6)卧式镗床镗孔方法及加工精度 142
2.金刚镗床加工 144
3.坐标镗床加工 147
1.2.7 影响镗削加工质量的因素与解决措施 149
1.常见影响镗削加工质量的因素与解决措施 149
2.提高镗孔质量的途径和方法 156
3.防止和消除振动的措施 156
参考文献 157
第2章 铣削、锯削加工 3
2.1 铣削 3
2.1.1 铣床 3
1.铣床的型号与技术参数 3
(1)升降台铣床 3
(2)工具铣床 3
(3)龙门铣床 3
(4)数控铣床 3
2.铣床主轴端部圆锥与工作台T形槽尺寸 13
(1)铣床主轴端部圆锥和端面键 13
(2)工作台T形槽尺寸 13
3.铣床附件 15
(1)平口台虎钳 15
(2)回转工作台 15
(3)万能分度头 15
(4)万能铣头 15
(5)立铣头 15
(6)铣床插头 19
2.1.2 铣削夹具 20
1.铣床夹具的基本要求 20
2.铣床夹具的技术条件 20
3.通用可调铣床夹具 24
(1)V形钳口自定心台虎钳 24
(2)三向台虎钳 24
(3)卧轴空心分度台 24
(4)气动夹紧立轴分度台 24
(5)多件装夹夹具 24
(6)铣阿基米德平板凸轮用的夹具 24
4.铣床夹具的典型结构 28
(1)直线进给铣床夹具 28
(2)圆周进给铣床夹具 30
(3)靠模仿形铣床夹具 30
2.1.3 铣刀及其辅具 35
1.铣刀类型、几何参数与规格 35
(1)铣刀的类型与用途 35
(2)铣刀的几何参数 35
(3)铣刀的规格 35
2.硬质合金可转位铣刀与刀片 51
(1)可转位铣刀刀片的夹紧形式 51
(2)可转位铣刀的种类与规格 51
(3)可转位铣刀刀片 51
3.其他铣刀 57
(1)硬质合金可转位密齿铣刀 57
(2)硬质合金螺旋齿玉米铣刀 57
(3)可转位螺旋立铣刀 58
(4)硬质合金可转位阶梯面铣刀 58
4.铣刀直径和角度的选择 59
(1)铣刀直径的选择 59
(2)铣刀角度的选择 59
5.铣刀的安装与铣刀辅具 59
(1)铣刀的安装 59
(2)铣刀辅具 59
6.铣刀的刃磨 66
(1)后刀面的刃磨 66
(2)前刀面的刃磨 68
2.1.4 铣削用量 82
1.铣削要素 82
2.铣削进给量的选择 82
(1)高速钢铣刀的进给量 82
(2)硬质合金铣刀的进给量 82
3.铣削速度、铣削力、铣削功率的计算及修正系数 82
(1)铣刀的磨钝标准及寿命 82
(2)铣削速度计算公式 86
(3)铣削力、扭矩和铣削功率计算 88
(4)铣削条件改变时的修正系数 89
4.确定铣削用量及功率的常用表格 89
(1)硬质合金面铣刀的铣削用量 89
(2)高速钢和硬质合金圆柱铣刀的铣削用量 89
(3)高速钢及硬质合金圆盘铣刀的铣削用量 104
(4)高速钢和硬质合金立铣刀的铣削用量 108
(5)涂层硬质合金及金刚石铣刀的铣削用量 120
5.铣削切削时间的计算 122
(1)切削时间计算公式 122
(2)切入行程长度和切出行程长度 124
6.铣削用量选择举例 125
2.1.5 铣削工艺 126
1.铣削特点、铣削方式与铣削加工的应用 126
2.分度头的分度计算与分度头的应用 130
(1)分度头的结构和参数 130
(2)分度头的分度方法与计算 130
(3)分度头的应用 133
3.精铣平面 134
(1)精铣平面对铣床提出的要求 134
(2)精铣平面对铣刀提出的要求和采取的措施 135
(3)精铣平面的铣削用量 135
(4)提高工艺系统的刚度和精度 135
(5)铝合金的精铣 135
4.型面铣削 136
(1)成形面的铣削 136
(2)凸轮的铣削 137
(3)端面齿离合器的铣削 137
(4)曲面铣削 144
5.多刀铣削及铣刀的安装调整 144
2.1.6 典型应用 147
1.曲轴的铣削 147
(1)立铣刀铣削 147
(2)圆盘铣刀铣削 147
2.气缸体顶面的精铣 150
3.锁块平面的铣削 150
4.分离叉圆弧面的铣削 151
5.球面的铣削 151
2.1.7 常见问题及解决对策 153
2.2 锯削 154
2.2.1 锯床 154
1.锯床的特点和适用范围 154
2.锯床类型与技术参数 154
(1)带锯床型号与技术参数 154
(2)圆锯床型号与技术参数 154
(3)弓锯床型号与技术参数 154
2.2.2 锯削刀具 158
1.弓锯锯条齿形型式和几何形状 158
(1)锯齿分齿 158
(2)齿距与工件材料的关系 158
(3)齿形几何形状 158
2.圆锯锯片 159
(1)圆锯片结构型式与特征 159
(2)圆锯片齿形的几何形状 159
(3)圆锯片齿距的选用 160
(4)锯片的刃磨 160
3.带锯锯带 160
(1)锯带宽度和厚度的选用 160
(2)齿距的选用 161
(3)锯带齿形的几何形状 161
2.2.3 锯削用量 161
1.弓锯锯削用量 161
2.圆锯锯削用量 161
3.带锯床加工各种材料的锯削速度和材料切除率 161
2.2.4 锯削工艺 165
1.弓锯床加工 165
(1)坯料装夹固定方法 165
(2)加工方法 165
(3)切削液选用 165
2.圆锯床加工 165
3.带锯床加工 165
2.2.5 常见问题及对策 166
1.弓锯锯削常见问题与解决方法 166
2.圆锯锯削常见问题与解决方法 166
3.带锯锯削常见问题与解决方法 166
参考文献 169
第3章 钻削、扩削、铰削加工 3
3.1 钻床的类型、技术参数与联系尺寸 3
3.1.1 台式钻床 3
3.1.2 立式钻床 3
3.1.3 摇臂钻床 5
3.1.4 排式钻床 7
3.1.5 铣端面、打中心孔机床 7
3.1.6 数控立式钻床 8
3.1.7 钻削中心 9
3.1.8 深孔钻床 10
3.2 钻床夹具 10
3.2.1 通用钻床夹具 10
1.滑柱钻模 10
(1)常用滑柱钻模的结构 10
(2)滑柱钻模的特点 10
2.自定心装置 11
(1)自定心装置的常用结构 11
(2)自定心装置的特点 14
3.分度转台 14
(1)分度转台的常用结构 14
(2)分度转台的特点 18
4通用多轴头 18
(1)通用多轴头的常用结构 18
(2)通用多轴头的特点 18
3.2.2 专用钻床夹具 18
1.固定式钻模 18
(1)固定式钻模示例 18
(2)固定式钻模的特点及用途 19
2.移动式钻模 19
(1)移动式钻模示例 19
(2)移动式钻模的特点及用途 19
3回转式钻模 19
(1)回转式钻模示例 19
(2)回转式钻模的特点及用途 20
4.翻转式钻模 20
(1)翻转式钻模示例 20
(2)翻转式钻模的特点及用途 22
5.摆动式钻模 22
(1)摆动式钻模示例 22
(2)摆动式钻模的特点及用途 23
6.固定钻模板式钻模组合式结构 23
(1)固定钻模板式钻模组合式结构示例 23
(2)固定钻模板式钻模组合式结构的特点及用途 23
7.铰链钻模板式钻模 23
(1)铰链钻模板式钻模示例 23
(2)铰链钻模板式钻模的特点及用途 23
8.可卸钻模板式钻模 23
(1)可卸钻模板式钻模示例 23
(2)可卸钻模板式钻模的特点及用途 23
9.升降钻模板式钻模 23
10.悬挂钻模板式钻模 23
(1)悬挂钻模板式钻模示例 23
(2)悬挂钻模板式钻模的特点及用途 23
11.专用多轴头 27
12.组合式钻模 27
(1)组合式钻模示例 27
(2)组合式钻模的特点及用途 27
3.2.3 钻套 31
1.钻套的类型及用途 31
(1)常用钻套 31
(2)特殊钻套 31
2.钻套与被加工孔的尺寸关系 32
3.标准钻套、衬套的常用规格 32
3.2.4 钻床夹具的技术要求 36
3.3 刀具及其辅具 37
3.3.1 中心钻 37
1.打中心孔用的中心钻 37
2.钻孔定中心用的中心钻 37
3.3.2 麻花钻 39
1.高速钢麻花钻 39
2.硬质合金麻花钻 53
3.3.3 硬质合金浅孔钻 59
3.3.4 深孔钻 63
1.深孔钻的类型及用途 63
2.钻实心料孔的深孔钻 63
3.深孔套料钻 64
(1)套料钻的结构 64
(2)深孔套料钻的导向问题 64
3.3.5 扩孔钻 78
1.高速钢扩孔钻 78
2.硬质合金扩孔钻 78
3.3.6 锪钻 82
1.锪钻类型和尺寸 82
2.硬质合金可转位锪钻 82
3.3.7 铰刀 89
1.铰刀的类型及用途 89
2.铰刀的结构要素和几何参数 89
(1)铰刀的结构要素和几何参数 89
(2)铰刀直径 91
(3)铰刀的齿数 91
3.铰刀的导向形式 91
4.常用铰刀的型式和主要规格尺寸 91
5.其他铰刀 91
3.3.8 孔加工复合刀具 114
3.3.9 辅具 118
1.扳手三爪钻夹头 118
2.卡头 118
3.套筒 118
4.刀杆 118
3.3.10 标准麻花钻的缺点和改进方法 128
1.修磨横刃 128
2.修磨前刀面 129
3.修磨分屑槽 129
4.开断屑槽 129
5.修磨锋角 130
6.圆弧刃钻头 130
7.修磨棱边 130
3.3.11 钻头、扩孔钻、铰刀刃磨方式与刃磨夹具 131
1.麻花钻的刃磨 131
2.扩孔钻的刃磨 132
3.铰刀的刃磨 132
3.4 钻、扩、铰孔切削用量及参数计算 133
3.4.1 钻、扩、铰孔进给量的选择 133
1.钻孔的进给量 133
2.扩孔的进给量 136
3.铰孔的进给量 136
3.4.2 钻、扩、铰孔时切削速度、轴向力、转矩、切削功率的计算公式及修正系数 137
1.钻头、扩孔钻和铰刀的磨钝标准及刀具寿命 137
2.钻、扩、铰孔时切削速度的计算公式 137
3.钻孔时轴向力、转矩及功率的计算公式 145
4.群钻加工时轴向力及转矩的计算公式 146
3.4.3 确定钻、扩、铰孔时切削用量、轴向力、转矩及切削功率的常用表格 147
1.钻孔 147
2.钻深孔及套料 163
3.扩孔的切削用量 170
4.铰孔的切削用量 174
3.4.4 钻、扩、铰孔切削用量选择举例 179
1.钻孔 179
(1)钻头 179
(2)确定钻削用量 179
2.扩孔 180
(1)扩孔钻 180
(2)确定扩孔切削用量 180
3.铰孔 180
(1)铰刀 180
(2)确定铰孔切削用量 180
4.各工序实际切削用量 180
3.5 钻、扩、铰孔加工机动时间的计算 182
3.6 钻、扩、铰孔加工工艺 182
3.6.1 一般孔的钻、扩、铰加工工艺 182
1.钻、扩、铰工艺的加工精度 182
2.加工实例 182
3.6.2 小孔、微孔钻削工艺 186
1.小孔、微孔的加工特点 186
2.小孔加工需采用的工艺措施 186
3.微孔加工需采用的工艺措施 186
4.小孔、微孔加工实例 187
3.6.3 数控钻削工艺 187
1.数控钻削的工艺范围 187
2.数控钻削程序编制步骤 187
3.数控钻削实例 187
(1)钻孔加工 187
(2)深孔加工 188
(3)螺纹孔加工 188
3.6.4 深孔钻削工艺 188
1.深孔钻削方法 188
2.深孔钻削的工作要点 189
3.深孔钻削的加工精度、表面粗糙度和适用范围 189
4.深孔加工举例 190
3.7 加工中常见问题的原因和解决办法 190
3.7.1 标准麻花钻加工中常见问题的产生原因和解决办法 190
3.7.2 枪钻钻孔中常见问题的原因和解决办法 192
3.7.3 内排屑深孔钻钻孔中常见问题的原因和解决办法 193
3.7.4 扩孔钻扩孔中常见问题的原因和解决办法 194
3.7.5 多刃铰刀铰孔中常见问题的原因和解决办法 195
参考文献 197
第4章 拉削、刨削、插削加工 3
4.1 拉削加工 3
4.1.1 拉削加工分类与拉削方式 3
1.拉削加工分类 3
2.拉削方式 7
3.拉削前对工件的工艺要求 8
4.1.2 拉床 8
1.立式拉床 8
2.卧式拉床 10
3.连续拉床 10
4.专用拉床 10
4.1.3 拉削装置 11
1.拉削夹具 11
(1)拉床用球面支座 11
(2)键槽拉削装置 11
(3)强制导向推孔装置 18
(4)连续拉床随行夹紧装置 18
2.拉削辅具 18
(1)内拉刀用拉削辅具 18
(2)外拉刀用拉削辅具 21
4.1.4 拉刀 22
1.拉刀的类型 22
2.常用拉刀的结构特点 22
(1)圆孔拉刀 22
(2)螺旋齿圆拉刀 23
(3)矩形花键拉刀 24
(4)渐开线花键拉刀 25
(5)三角齿花键拉刀 26
(6)键槽拉刀 27
(7)推刀 31
(8)挤压推刀 32
3.拉刀设计常用参数的选择 32
(1)拉刀齿升量 32
(2)拉刀刀齿主要几何参数 33
(3)拉刀容屑槽、齿距与同时工作齿数 34
(4)拉刀的分屑槽 37
(5)拉削时孔的扩张量或收缩量 40
(6)拉刀校准齿齿数 40
(7)拉刀前导部、后导部形状与尺寸 40
(8)拉刀柄部尺寸 42
(9)拉刀允许设计长度 49
(10)单位拉削力 49
4.拉刀技术条件 51
(1)拉刀材料与热处理硬度 51
(2)拉刀各部位表面粗糙度的规定 51
(3)拉刀制造精度 51
5.拉刀设计举例 53
(1)圆拉刀设计 53
(2)综合轮切式圆拉刀设计举例 55
4.1.5 拉削余量、拉削用量与拉削切削液 58
1.拉削余量 58
(1)孔拉削余量 58
(2)键槽拉削余量 58
2.拉削用量 59
(1)拉削速度的选用 59
(2)拉削速度分组 59
(3)高速拉削常用工艺参数 61
(4)拉削的进给量 61
3.拉削切削液 61
4.1.6 生产应用实例 61
1.汽车发动机轴瓦内圆表面拉削 61
2.汽车循环球转向机螺母滚道的螺旋拉削 61
3.齿条拉削 62
4.汽车套管叉花键孔拉削 62
4.1.7 拉削加工常见问题及对策 66
4.2 刨削加工 68
4.2.1 刨床 68
1.刨床的型号与技术参数 68
2.刨床工作精度 73
3.刨床的允许载荷 74
4.2.2 刨刀 74
1.刨刀的种类及用途 74
2.刨刀的合理几何参数 77
4.2.3 刨削用量 77
1.进给量及背吃刀量 77
2.切削速度、切削力及切削功率 81
4.2.4 刨削加工生产应用实例 90
1.刨削薄形工件 90
2.槽类工件的刨削与切断 90
3.精刨 93
(1)精刨的类型 93
(2)精刨的要点 95
4.2.5 刨削加工中常见问题及对策 98
1.刨平面常见质量问题产生的原因与解决方法 98
2.刨垂直面及台阶常见质量问题产生的原因与解决方法 99
3.刨斜面、V形槽及镶条常见质量问题产生的原因和解决方法 100
4.切断、刨直槽及T形槽常见质量问题产生原因与解决方法 100
4.3 插削加工 101
4.3.1 插床 101
1.插床的类型及技术参数 101
2.插床的工作精度 103
4.3.2 插刀及插刀杆 103
1.插刀的种类及用途 103
2.插刀的合理几何参数 103
3.插刀杆种类及用途 103
4.3.3 插削用量和切削液选用 104
1.插削用量 104
2.切削液的选用 107
4.3.4 插削加工工艺 107
1.插方孔和键槽 107
2.插花键孔 109
3.插螺旋花键孔 109
4.3.5 插键槽常见质量问题产生原因 109
参考文献 110
第5章 磨削加工 3
5.1 磨削原理 3
5.1.1 磨削加工方法与分类 3
5.1.2 磨削加工的特点与切屑形成 3
1.磨削加工的特点 3
2.切屑的形成 4
5.1.3 磨削基本参数 4
5.1.4 磨削力和磨削功率 5
1.磨削力 5
2.磨削功率 6
5.1.5 磨削热与磨削温度 8
1.磨削温度 8
2.降低磨削温度的途径 8
5.1.6 砂轮的磨损 8
1.砂轮磨损的形态 8
2.砂轮磨损的原因 8
5.2 磨削液 9
5.2.1 磨削液的性能要求 9
5.2.2 磨削液的种类和组成 9
1.油基磨削液 10
(1)矿物油 10
(2)极压油 10
2.水基磨削液 11
(1)乳化液及极压乳化液 11
(2)无机盐水溶液 11
(3)化学合成水溶液 11
5.2.3 磨削液的选用 11
5.2.4 磨削液的供给方法 16
1.浇注法 16
2.喷射法 16
3.内冷却供液方式 19
4.喷雾法 19
5.浸渍砂轮法 19
5.2.5 磨削液的过滤方法 19
1.涡旋分离器 20
2.纸质过滤装置 21
5.3 磨床与磨床夹具 21
5.3.1 磨床的技术参数及加工精度 21
1.外圆磨床 21
2.无心磨床 24
3.内圆磨床 25
4.平面磨床 26
5.中心孔磨床 28
6.坐标磨床 29
7.导轨磨床 29
8.珩磨机床 30
9.外圆砂带磨床 32
10.研磨机床 33
11.数控磨床 34
5.3.2 磨床夹具 37
1.磨床通用夹具 38
(1)顶尖和鸡心夹头 38
(2)心轴 38
(3)中心孔柱塞 44
(4)弹簧夹头 44
(5)卡盘及花盘 44
(6)磁力吸盘及磁力过渡垫块 44
(7)精密平口虎钳 45
(8)磨直角用夹具、直角块和多角形块 45
2.典型专用磨床夹具 46
(1)专用矩形电磁吸盘 46
(2)真空吸盘 47
(3)真空夹头 47
(4)轴承外圈内圆磨削液压夹具 47
(5)锥齿轮端面及内圆磨削夹具 47
(6)圆柱齿轮内圆磨削夹具 47
(7)齿轮轴内孔磨削夹具 47
(8)专用气动内圆磨削夹具 47
(9)异形工件专用磨削夹具 49
(10)磨扁方夹具 49
5.4 磨料磨具 50
5.4.1 普通磨料磨具及其选择 50
1.普通磨料及其选择 50
(1)普通磨料的品种、代号、特性及其应用范围 50
(2)选择磨料应注意的问题 51
2.普通磨料的粒度及其选择 52
3.普通磨具的硬度及其选择 53
4.普通磨具的结合剂及其选择 54
5.普通磨具的强度及其选择 55
6.普通磨具的组织及其选择 55
7.普通磨具形状和尺寸的选择 56
8.普通磨具的标志 61
5.4.2 超硬磨料磨具及其选择 61
1.超硬磨料及其选择 61
2.超硬磨料粒度及其选择 62
3.超硬磨具结合剂及其选择 64
4.超硬磨具浓度及其选择 64
5.超硬磨具形状和尺寸的选择 64
(1)超硬磨具的形状 65
(2)超硬磨具尺寸代号 71
6.超硬磨具的标志 71
7.金刚石磨具中外对照 72
5.4.3 涂覆磨具 74
1.涂覆磨具的特点 74
2.涂覆磨具产品 75
3.砂带的选择 77
4.标记示例 79
5.4.4 砂轮的平衡与修整 79
1.砂轮的平衡 79
(1)砂轮静平衡的工具与方法 79
(2)砂轮的动态平衡装置 80
(3)砂轮的动平衡 81
2.砂轮的修整 82
(1)车削法修整 82
(2)滚压法修整 86
(3)磨削法修整 91
5.5 磨削加工工艺 94
5.5.1 固结磨具普通磨削 94
1.固结磨具普通磨削用量选择 94
2.外圆磨削 96
(1)外圆磨削的方法 96
(2)外圆磨削用量 96
(3)外圆磨削的中心孔 102
(4)外圆磨削实例 102
3.内圆磨削 105
(1)内圆磨削的常用方法 105
(2)内圆磨削用量 105
(3)内圆磨头 112
(4)内圆磨削砂轮接长轴及砂轮尺寸的选择 112
(5)内圆磨削实例 117
4.平面磨削 119
(1)平面磨削的常用方法 120
(2)平面磨削用量 126
(3)薄片工件平面磨削的装夹 130
(4)平面磨削实例 130
5.无心磨削 133
(1)无心磨削的常用方法 133
(2)无心磨削用量 139
(3)无心磨削实例 139
6.成形磨削 139
(1)成形磨削的主要方式 139
(2)成形砂轮磨削 139
(3)成形夹具磨削 146
(4)仿形磨削 151
5.5.2 高效磨削 152
1.高速磨削 152
2.缓进给磨削 158
3.高效深切磨削 165
4.宽砂轮与多砂轮磨削 166
5.恒压力磨削 168
6.高速重负荷磨削 170
5.5.3 砂带磨削 175
1.砂带磨削的机理、特点、适用范围及分类 175
2.砂带磨削磨头(架) 180
(1)磨头结构 180
(2)磨头的主要尺寸及参数 183
(3)接触轮 183
(4)张紧轮和主动轮 184
(5)张紧机构和调偏机构 186
(6)磨头各轮的动平衡 188
(7)磨头电动机功率的选择 188
(8)砂带基体种类及适用范围 190
(9)砂带粘结剂 190
3.砂带磨削工艺参数选择 190
4.砂带寿命及提高寿命的措施 194
5.砂带磨削实例 195
(1)外圆砂带磨削 195
(2)内圆砂带磨削 196
(3)平面砂带磨削 196
5.5.4 数控磨削 197
1.数控外圆磨削 197
2.数控坐标磨削 202
(1)数控坐标磨削的基本方法 202
(2)数控坐标磨削机床的附件和通用夹具 205
(3)数控坐标磨削砂轮 205
(4)数控坐标磨削的加工工艺参数 205
(5)数控坐标磨削加工实例 205
5.6 磨削加工中常见缺陷及其解决办法 207
5.6.1 通用磨削中产生缺陷的主要原因 207
5.6.2 磨削缺陷产生原因的综合分析 216
参考文献 219
第6章 齿轮、蜗轮蜗杆、花键加工 3
符号表 3
6.1 圆柱齿轮加工 8
6.1.1 概述 8
1.加工方法简介 8
2.几何参数计算 10
(1)渐开线圆柱齿轮标准基本齿条齿廓 10
(2)渐开线圆柱齿轮模数 10
(3)渐开线圆柱齿轮图样上应注明尺寸 11
(4)标准圆柱齿轮传动几何参数计算 11
(5)变位圆柱齿轮传动几何参数计算 16
3.典型齿轮加工工艺 25
6.1.2 铣齿 28
1.成形铣刀铣直齿轮 28
2.成形铣刀铣斜齿轮 29
3.铣齿条 30
6.1.3 滚齿 31
1.滚齿原理 31
2.滚齿方法 32
3.滚齿机及加工精度 35
4.滚齿夹具 38
5.滚刀 39
(1)整体齿轮滚刀 39
(2)镶片滚刀 40
(3)滚刀的精度 43
(4)滚刀的刃磨 49
6.滚齿工艺 50
(1)切削用量的选择 50
(2)机动时间的计算 52
(3)切削液选用 52
(4)滚齿调整 54
(5)硬齿面滚齿 57
(6)高速干式切削滚齿技术 58
7.常见问题及对策 59
6.1.4 插齿 61
1.插齿原理 61
(1)插齿基本原理 61
(2)直齿圆柱齿轮的插削 61
(3)斜齿圆柱齿轮的插削 62
(4)插削内齿轮 62
(5)插削齿条 65
(6)插削端面齿盘 65
2.插齿机及加工精度 65
3.插齿夹具 70
4.插齿刀 71
(1)Ⅰ型——盘形直齿插齿刀 73
(2)Ⅱ型——碗形直齿插齿刀 75
(3)Ⅲ型——锥柄直齿插齿刀 77
(4)直齿插齿刀的技术要求 77
(5)斜齿插齿刀 82
(6)插齿刀的磨损及刃磨方法 85
5.插齿工艺 86
(1)切削用量及其选择 86
(2)机动时间的计算 89
(3)切削力和切削功率的计算 89
(4)插齿的调整 89
6.常见问题及对策 90
6.1.5 剃齿 92
1.剃齿原理和方法 92
2.剃齿机及精度 94
3.剃齿夹具 102
4.剃齿刀 102
(1)剃齿刀的重磨 102
(2)剃齿刀的齿形修正 104
5.剃齿工艺 105
(1)切削用量及其选择 105
(2)机动时间的计算 106
(3)切削液的选用 106
(4)剃齿调整 106
(5)加工实例 108
(6)径向剃齿 109
6.常见问题及对策 110
6.1.6 挤齿 111
1.挤齿原理和设备 111
(1)挤齿原理 111
(2)挤齿机 113
2.挤轮 114
3.挤齿工艺 117
(1)工艺参数的选择与计算 117
(2)机动时间的计算 118
(3)切削液的选用 118
(4)挤齿的其他问题 118
4.挤齿误差产生原因与消除方法 119
6.1.7 珩齿 119
1.珩齿原理与方法 120
2.珩齿机 123
3.珩齿夹具 126
4.珩磨轮 127
5.珩齿工艺 128
(1)珩削方法和珩齿条件的选用 128
(2)外啮合齿轮形珩轮珩齿机和蜗杆形珩轮珩齿机的调整 131
(3)内啮合珩齿机的调整 131
(4)磨削液的选择 132
6.珩齿常见问题及解决办法 132
6.1.8 磨齿 134
1.磨齿原理和方法 134
2.磨齿机 136
(1)圆柱齿轮磨齿机类型 136
(2)磨齿机的性能比较 137
(3)国产和进口磨齿机产品及主要技术参数 138
3.磨齿夹具 138
4.磨齿砂轮 138
(1)对磨齿机使用砂轮的要求 138
(2)磨齿砂轮的选用 143
(3)砂轮的平衡 144
(4)立方氮化硼(CBN)砂轮 144
(5)砂轮的修形 144
5.磨齿工艺 145
(1)磨齿工艺参数的选择 145
(2)磨削烧伤 146
(3)磨齿生产率的计算 147
(4)磨削液的选择 148
6.常见磨齿误差和纠正方法 148
6.1.9 圆柱齿轮检测 151
1.精度标准与公差项目的选择 151
(1)偏差的定义和代号 152
(2)齿轮精度允许值 152
(3)齿轮公差项目的选择 152
2.齿距偏差的测量 172
(1)相对测量法 172
(2)绝对测量法 174
3.齿廓误差的测量 174
4.螺旋线偏差的测量 178
5.齿圈径向跳动的测量 178
6.公法线长度的测量 180
7.齿厚的测量 181
8.切向综合偏差的测量 182
9.径向综合偏差的测量 182
6.2 直齿锥齿轮加工 183
6.2.1 概述 183
6.2.2 直齿锥齿轮传动的几何计算 185
6.2.3 直齿锥齿轮成形铣刀铣齿 188
1.加工原理 188
2.直齿锥齿轮成形铣刀及其刀号的选择 188
3.直齿锥齿轮铣齿方法及调整计算 189
6.2.4 直齿锥齿轮刨齿 191
1.刨齿原理及设备 191
(1)按平顶产形轮刨齿的原理 191
(2)按平面产形轮刨齿的原理 192
(3)直齿锥齿轮刨齿机 192
2.刨齿夹具及刀具 197
(1)刨刀的结构型式和类型 197
(2)刨刀主要参数的确定和选用 200
(3)刨刀的技术条件 201
3.刨齿工艺 201
(1)刨齿机调整计算 201
(2)粗刨 201
(3)刨鼓形齿 203
(4)刨齿工艺参数的选择 204
4.常见问题及对策 204
6.2.5 双刀盘滚切法铣齿 209
1.双刀盘滚切法铣齿原理及机床 209
(1)双刀盘滚切法铣齿原理及特点 209
(2)双刀盘铣齿机型号和技术参数 209
2.双刀盘滚切法铣齿刀具 209
6.2.6 圆拉法加工 210
1.加工原理及设备 210
(1)加工原理 210
(2)圆拉法加工机床 211
2.圆盘拉刀 211
(1)圆拉刀盘 212
(2)圆拉法加工直齿锥齿轮的运动规律 212
3.圆拉法加工的齿轮 212
(1)圆拉法加工的齿轮及应用 212
(2)圆拉法加工直齿锥齿轮的应用 212
4.常见问题及对策 213
6.3 螺旋锥齿轮加工 214
6.3.1 概述 214
1.螺旋锥齿轮分类 214
2.典型加工工艺流程 214
3.铣齿加工方法和特点 214
(1)铣齿加工方法 214
(2)铣齿加工特点 217
6.3.2 螺旋锥齿轮铣齿 217
1.铣齿加工原理 217
(1)平面产形齿轮加工原理 217
(2)平顶产形齿轮加工原理 219
(3)锥面产形齿轮加工原理 219
2.铣齿加工机床 219
(1)弧齿锥齿轮铣齿机 220
(2)长幅外摆线锥齿轮铣齿机 220
(3)数控螺旋锥齿轮铣齿机 220
3.铣齿刀具 225
(1)弧齿锥齿轮加工刀具 225
(2)长幅外摆线锥齿轮加工刀具 244
4.铣齿夹具 253
(1)铣齿基准面选择的基本原则 253
(2)心轴 253
(3)夹具典型结构 254
5.螺旋锥齿轮铣齿工艺 255
(1)弧齿锥齿轮铣齿加工工艺 255
(2)长幅外摆线锥齿轮铣齿加工工艺 266
6.螺旋锥齿轮计算 269
(1)弧齿锥齿轮计算 269
(2)长幅外摆线锥齿轮计算 296
6.3.3 螺旋锥齿轮研齿加工 299
1.研齿原理 299
2.研齿机床 300
3.研齿工艺 301
(1)“O”位调整 301
(2)研齿循环 302
(3)研齿其他工艺要素 302
(4)研齿的一般性规则 302
(5)长幅外摆线锥齿轮研齿特点 303
6.3.4 螺旋锥齿轮磨齿加工 303
1.螺旋锥齿轮磨齿加工原理 303
2.磨齿机床 304
3.磨齿工艺特点 305
6.3.5 螺旋锥齿轮刮削 306
1.弧齿锥齿轮刮削 306
2.长幅外摆线齿轮刮削 306
6.3.6 螺旋锥齿轮检验 306
1.螺旋锥齿轮精度标准 306
(1)轮齿精度标准 306
(2)齿坯精度标准 306
2.螺旋锥齿轮几何检测 308
(1)螺旋锥齿轮公差项目的选择 308
(2)轮齿几何测量 309
(3)齿面粗糙度的测量 311
3.螺旋锥齿轮副的综合测量 311
(1)传动误差产生的原因 311
(2)传动误差测量 311
(3)齿轮的噪声测量 312
4.螺旋锥齿轮接触区检验 313
(1)EPG检验的概念 313
(2)EPG检验的作用 313
(3)检验机床 313
(4)检验机的校准 315
(5)EPG检验 315
(6)轮齿接触区调整 318
(7)侧隙检查 318
(8)修缘检查 318
6.4 蜗轮蜗杆加工 318
6.4.1 概述 318
1.蜗轮蜗杆传动的特点和分类 318
2.普通圆柱蜗杆传动和几何尺寸计算 319
3.其他蜗杆传动简介 321
(1)圆弧圆柱蜗杆(ZC蜗杆)传动 321
(2)直廓环面蜗杆传动 323
(3)包络环面蜗杆传动 324
(4)锥蜗杆传动 324
6.4.2 普通圆柱蜗杆、蜗轮加工 324
1.普通圆柱蜗杆加工 324
(1)车削加工 324
(2)铣削加工 327
(3)磨削加工 328
(4)蜗杆加工用机床 328
(5)蜗杆加工工艺 333
2.普通圆柱蜗轮加工 336
(1)滚齿加工 336
(2)飞刀加工 339
(3)剃齿加工 343
(4)蜗轮加工误差分析及消除方法 344
6.4.3 其他蜗杆蜗轮加工介绍 346
1.圆弧圆柱蜗杆、蜗轮加工 346
(1)圆弧圆柱蜗杆的加工 346
(2)圆弧圆柱蜗轮的加工 346
(3)加工圆弧圆柱蜗杆副要注意的问题 347
2.直廓环面蜗杆、蜗轮加工 348
(1)环面蜗杆加工 348
(2)环面蜗轮加工 351
3.平面包络环面蜗杆、蜗轮加工 352
6.4.4 蜗杆蜗轮检测 354
1.蜗杆的测量 354
(1)蜗杆螺旋线误差的测量 354
(2)蜗杆齿形误差的测量 355
(3)蜗杆轴向齿距偏差的测量 356
(4)蜗杆齿槽径向圆跳动的测量 357
(5)蜗杆齿厚偏差的测量 357
2.蜗轮的测量 359
3.蜗杆副和蜗杆传动的测量 360
6.5 花键加工 361
6.5.1 概述 361
1.花键的定心方式 361
2.花键的加工过程和方法 361
6.5.2 花键轴的成形铣削 364
1.成形铣削的种类和方法 364
(1)三面刃铣刀和锯片铣刀加工花键轴 364
(2)用组合铣刀加工花键轴 366
(3)用成形铣刀铣削花键轴 367
2.机床、夹具及辅具 368
3.刀具 371
(1)圆盘铣刀和锯片铣刀 371
(2)成形铣刀 371
(3)铣刀的磨损 371
4.成形铣削工艺 376
(1)切削用量的选择 376
(2)切削力、切削功率的计算 383
(3)铣削机动时间的计算 384
(4)切削液 385
5.常见问题及对策 385
6.5.3 花键轴的展成铣削 386
1.加工原理和设备 386
2.刀具 387
(1)渐开线花键滚刀 387
(2)矩形花键滚刀 394
(3)滚刀的磨损及刃磨 399
3.展成铣削工艺 399
(1)切削用量及其选择 399
(2)切削功率的计算 399
(3)机动时间的计算 401
(4)切削液的选择 401
(5)加工花键轴的调整步骤 401
4.常见问题及对策 402
6.5.4 花键轴的磨削 402
1.磨削方法和设备 402
2.砂轮 404
(1)砂轮的选择 404
(2)砂轮的修整及修整工具 404
3.磨削工艺 406
(1)加工余量及公差 406
(2)磨削用量及其选择 408
(3)机动时间的计算 408
(4)切削液的选择 409
(5)磨削加工举例 410
4.常见问题及对策 410
6.5.5 花键孔的加工 411
1.插齿刀加工渐开线花键孔 411
2.插齿刀加工矩形花键孔 414
6.5.6 花键轴的无屑加工 416
1.无屑加工方法 416
(1)滚轧花键轴 416
(2)冷轧花键轴 416
(3)冷挤花键轴 418
2.无屑加工的要求、工艺参数及有关计算 418
(1)滚轧(冷打)加工 419
(2)冷轧加工的工艺要求 421
(3)冷挤压加工的工艺要求 422
3.挤压加工举例 422
6.5.7 花键检测 424
1.花键的精度要求 424
2.花键检验方法的选择 424
(1)渐开线花键检验方法的选择 424
(2)矩形花键检验方法的选择 425
3.渐开线花键的检测 425
4.矩形花键的检测 425
(1)综合检测 425
(2)单项误差测量 427
参考文献 429
第7章 螺纹加工 3
7.1 车削螺纹 3
7.1.1 车削螺纹的加工方法、特点和应用 3
1.螺纹车削方法 3
2.车削螺纹的特点和应用范围 5
7.1.2 加工机床 5
1.专用螺纹车床的型号与技术参数 5
2.在卧式车床上车削螺纹时交换齿轮的计算与调整 5
7.1.3 螺纹车刀 6
1.螺纹车刀的分类、结构特点和应用 6
2.螺纹车刀几何参数 7
(1)平体螺纹车刀的几何参数 7
(2)棱体、圆体螺纹车刀的几何参数 8
3.螺纹车刀的安装 8
4.机夹螺纹车刀 9
5.可转位螺纹车刀 12
7.1.4 工艺参数的选择与机动时间的计算 15
1.切削用量的选择 15
2.切削力与切削功率的计算 17
3.机动时间的计算 18
7.1.5 车螺纹切削液的选用 18
7.1.6 丝杠及特殊螺纹的车削 18
1.丝杠的车削 18
(1)车削丝杠螺纹的工艺要求 18
(2)车削丝杠的切削用量 18
(3)刀具几何参数选择 18
2.平面螺纹的车削 18
3.锥螺纹的车削 19
7.1.7 车削螺纹的数控编程 19
1.单行程螺纹切削G32 19
2.变导程螺纹切削G34 19
3.螺纹切削循环G92 19
4.螺纹切削复合循环G76 20
5.编制螺纹加工程序应注意的几个问题 20
(1)螺纹加工的切入与切出距离 20
(2)螺纹加工走刀次数与切削余量确定 20
6.数控车削螺纹编程实例 21
(1)用G32指令加工圆柱螺纹程序示例 21
(2)用G32指令加工圆锥螺纹程序示例 21
(3)用G92指令加工圆柱螺纹程序示例 21
(4)用G92指令加工圆锥螺纹程序示例 23
(5)用G76复合固定循环指令加工圆柱螺纹程序示例 23
7.1.8 车削螺纹常见问题和解决方法 23
7.2 丝锥攻螺纹 25
7.2.1 丝锥攻螺纹的方法、特点及应用 25
7.2.2 攻丝机的类型与技术参数 26
7.2.3 用普通螺纹丝锥攻螺纹 28
1.普通螺纹丝锥 28
(1)普通螺纹丝锥的结构 28
(2)普通螺纹丝锥的规格尺寸 28
(3)普通螺纹丝锥几何参数的选择 31
(4)被加工的内螺纹公差与丝锥制造公差的关系 33
(5)丝锥的磨钝标准 33
2.丝锥辅具的特点与选择 33
3.攻螺纹工艺参数的确定和机动时间的计算 33
(1)攻螺纹前钻孔直径的确定 33
(2)切削速度的计算和选择 36
(3)攻螺纹扭矩的计算 38
(4)攻螺纹机动时间的计算 39
4.机用丝锥攻螺纹切削液的选择 39
5.机用丝锥攻螺纹中常发生问题的解决方法 39
7.2.4 螺母丝锥攻螺母螺纹 40
1.螺母丝锥 40
(1)螺母丝锥的型式 40
(2)螺母丝锥的规格尺寸 40
2.螺母丝锥攻螺纹辅具的选择 45
3.攻螺母螺纹工艺参数的选择与生产率计算 46
(1)攻螺纹前对底孔的要求 46
(2)攻螺母螺纹切削速度的选择 46
(3)自动螺母攻丝机生产率的计算 46
4.弯柄螺母丝锥攻螺纹中常发生的问题、产生原因与解决方法 46
7.2.5 锥形丝锥攻锥螺纹 47
1.锥形螺纹丝锥 47
2.攻锥形螺纹工艺参数的选择 47
(1)攻锥形螺纹前底孔的加工 47
(2)攻锥形螺纹切削速度的选择 47
7.2.6 挤压丝锥挤压螺纹 50
1.挤压丝锥的特点和种类 50
2.挤压螺纹工艺参数的选择与计算 50
(1)挤压螺纹前底孔的确定 50
(2)挤压螺纹速度的选择 50
(3)挤压螺纹扭矩的计算 50
7.2.7 特种丝锥的应用 51
7.3 板牙套螺纹 52
7.3.1 板牙 52
1.板牙的种类和应用范围 52
2.各种圆板牙的尺寸规格 52
3.圆板牙的几何参数 57
7.3.2 圆板牙套螺纹切削用量的选择 58
7.4 螺纹切头加工螺纹 58
7.4.1 螺纹切头加工螺纹的特点及应用 58
7.4.2 圆梳刀外螺纹切头加工螺纹 58
1.螺纹切头的规格与选用 58
2.螺纹切头的安装 60
3.圆梳刀几何参数的选择 61
4.工艺参数的选择与机动时间的计算 62
(1)毛坯尺寸与公差的确定 62
(2)切削速度的计算与选择 62
(3)扭矩、切削功率的计算 62
(4)切螺纹机动时间的计算 62
5.切削液的选择 62
6.圆梳刀螺纹切头加工螺纹常发生的问题、产生原因与解决方法 62
7.4.3 径向平梳刀外螺纹切头加工螺纹 66
1.螺纹切头的规格与选用 66
2.径向平梳刀几何参数的选择 66
3.工艺参数的选择 66
(1)毛坯外径尺寸与公差的选择 66
(2)切削速度的选择 66
4.平梳刀螺纹切头加工外螺纹常见的问题、产生原因与解决方法 68
7.4.4 径向平梳刀内螺纹切头加工螺纹 69
1.螺纹切头的规格与选用 69
2.平梳刀的规格与几何参数 69
3.工艺参数的选择 70
(1)加工前的螺纹底孔尺寸与公差的选择 71
(2)切削速度的选择 71
7.4.5 圆梳刀内螺纹切头加工螺纹 71
7.5 铣螺纹 72
7.5.1 铣螺纹的方式、特点及应用 72
1.铣螺纹的方式与使用范围 72
2.铣螺纹的特点 72
7.5.2 螺纹铣床 72
7.5.3 螺纹铣刀 73
1.螺纹铣刀的结构和尺寸 73
2.螺纹铣刀的几何参数 74
7.5.4 铣削用量的选择与机动时间的计算 74
1.切削速度的选择 74
2.铣螺纹机动时间的计算 75
7.5.5 旋风铣削螺纹 75
1.旋风铣削螺纹的方式 75
2.刀头的几何参数、材料及刀头数 76
3.切削用量及切削功率的计算 76
(1)圆周进给量的选择 76
(2)刀头寿命的选择 76
(3)旋风铣削螺纹切削速度 76
(4)切头转速与工件转速 78
(5)旋风铣削螺纹切削功率 78
7.5.6 数控铣削螺纹 78
7.6 滚压螺纹 79
7.6.1 滚压螺纹的特点与应用 79
7.6.2 滚压螺纹的坯件制备 82
1.滚压螺纹对材料性能的要求 82
2.滚压螺纹的坯件直径与公差的确定 82
3.滚压前坯件倒角要求 85
7.6.3 滚丝轮滚压螺纹 85
1.滚丝机床的主要技术参数 85
2.普通螺纹滚丝轮的型式及规格尺寸 85
3.工艺参数的选择与计算 90
(1)滚压速度的选择 90
(2)滚丝轮进给速度的选择 90
(3)滚压时间的确定 90
(4)滚压力的计算 90
4.滚丝轮的寿命 91
5.锥形螺纹滚丝轮 92
7.6.4 搓丝板滚压螺纹 94
1.搓丝机的型号与技术参数 94
2.普通螺纹用搓丝板型式及规格尺寸 94
3.工艺参数的选择 97
(1)滚压速度选择 97
(2)滚压力计算 97
7.6.5 螺纹滚压头滚压螺纹 97
1.螺纹滚压头的结构与规格 97
2.滚压头速度和切削液的选择 98
3.滚压螺纹时滚轮寿命 98
4.螺纹滚压头加工的典型工件和滚压头在机床上的安装示例 98
5.叉式滚压头 98
7.6.6 滚压螺纹常见问题的解决方法 100
1.滚丝轮滚压螺纹的常见问题、产生原因与解决方法 100
2.搓丝板搓螺纹过程中的常见问题、产生原因与解决方法 102
3.螺纹滚压头滚压螺纹的常见问题、产生原因与解决方法 103
7.7 磨削螺纹 106
7.7.1 磨削螺纹的方法、特点及应用 106
7.7.2 螺纹磨床 107
7.7.3 砂轮 109
7.7.4 磨削用量的选择与机动时间的计算 110
1.磨削用量的选择 110
2.机动时间的计算 111
7.7.5 切削液的选择 111
7.7.6 磨螺纹常见问题、产生原因与解决方法 111
7.8 螺纹测量 116
7.8.1 螺纹的综合测量 116
7.8.2 外螺纹单项参数测量 116
1.用量针法测量单一中径 116
2.在工具显微镜上测量外螺纹参数 119
(1)测量方法 119
(2)测量外螺纹中径 119
(3)外螺纹螺距测量 120
(4)外螺纹牙型半角的测量 120
7.8.3 内螺纹单项参数测量 120
参考文献 122
第8章 特种加工 3
8.1概述 3
8.1.1 特种加工的定义及特点 3
8.1.2 特种加工的分类 3
8.1.3 几种常用特种加工方法性能和用途的对比 4
8.2 电火花穿孔、成形加工 5
8.2.1 电火花穿孔、成形加工的原理 5
8.2.2 电火花穿孔、成形加工机床 5
1.我国电火花穿孔、成形加工机床的型号和标准 5
2.电火花成形加工机床主要型号与技术参数 5
8.2.3 电火花加工用的脉冲电源 7
1.基本的脉冲波形及其主回路 7
2.各种派生的电火花加工用的脉冲电源 8
8.2.4 电火花加工的工具进给调节系统 9
1.工具电极自动进给调节系统的类型 9
2.自动进给调节系统的基本组成部分 9
3.步进电动机自动进给调节系统 9
4.直流、交流伺服电动机自动进给调节系统 10
8.2.5 电火花加工的工具电极和工作液系统 10
1.电火花加工用工具电极材料 10
2.电火花加工用工具电极的设计及制造 10
(1)加工冲模的穿孔电极工具设计 10
(2)加工型腔的电极工具设计 12
3.电火花加工用的工作液系统 12
8.2.6 电火花加工的基本工艺规律 12
1.电火花加工的工艺指标 12
2.电火花加工的电规准 12
3.电火花加工工艺规律及电火花加工工艺曲线图表 14
8.2.7 电火花加工时正确选择电规准的方法 22
8.2.8 电火花加工时工具电极的安装、调整和找正 22
1.工具电极的安装、调整和找正的要求 22
2.工具电极的安装、调整和找正的装置 22
8.2.9 电火花加工机床的一般故障和加工中的不正常现象 24
1.液压主轴头常见的故障、原因及解决办法 24
2.伺服电动机主轴头常见的故障及原因 25
3.电火花加工中的不正常现象的故障和原因以及解决办法 25
8.3 电火花加工小孔 26
8.3.1 小孔的电火花加工 26
8.3.2 小深(斜)孔的电火花加工 27
8.3.3 异形小孔的电火花加工 27
1.喷丝板异形小孔的电火花加工 27
2.精密筛网多个小方孔的电火花加工 28
8.3.4 微孔电火花加工 29
1.微小轴(工具电极)的制作 29
2.高深径比微小孔的加工 29
8.4 电火花成形加工的数控技术 29
8.4.1 数控电火花加工机床的类型 29
8.4.2 电火花数控摇动加工 30
1.电火花数控摇动加工的特点 30
2.电火花数控摇动加工的代码和轨迹 30
3.数控摇动的伺服方式 30
8.5 电火花加工的其他工艺形式及应用 32
8.5.1 电火花磨削 32
1.电火花小孔磨削 32
2.电火花刃磨和切割 33
8.5.2 共轭回转电火花加工及双轴回转电火花加工 33
1.电火花共轭同步回转加工精密内外螺纹 33
2.电火花共轭倍角同步回转加工 33
3.双轴回转展成法电火花加工精密凹凸球面、平面 34
8.5.3 电火花表面强化及刻字 35
1.电火花表面强化 35
2.电火花刻字 36
8.5.4 混粉电火花镜面加工技术 37
1.混粉电火花加工原理及特点 37
2.混粉电火花镜面加工工艺要点 37
3.混粉电火花加工装置及设备 37
4.混粉电火花镜面加工应用实例 37
8.5.5 半导体和非导体电火花加工技术 37
1.半导体和高阻抗材料的电火花加工 37
2.非导体的电火花加工 37
8.5.6 气体介质中电火花加工 39
8.5.7 电火花铣削加工技术 39
8.5.8 微细电火花加工技术 39
1.微细电火花加工的关键技术 39
(1)微细电火花加工脉冲电源 39
(2)微细工具电极的制造与安装 40
(3)高精度、高灵敏度的工具电极伺服进给主轴 40
2.微细电火花加工的应用举例 40
8.6 电火花线切割加工 40
8.6.1 电火花线切割加工原理和特点 40
8.6.2 高、低速走丝电火花线切割加工比较 41
8.6.3 电火花线切割机床 42
1.电火花线切割机床的分类及型号 42
2.电火花线切割机床标准 43
3.我国生产的高速走丝电火花线切割机床 43
4.国内外生产的低速走丝电火花线切割机床 43
8.6.4 导轮部件及电极丝保持器 47
1.导轮部件 47
2.电极丝保持器 48
8.6.5 电火花线切割机床夹具和加工工件装夹方法 48
1.电火花线切割机床夹具 48
2.电火花线切割加工工件的装夹方法 48
8.6.6 常用电火花线切割电源 51
1.常用电火花线切割电源的波形、电参数及性能 51
2.电火花线切割电源波形和电参数对工艺指标的影响 52
(1)矩形波电源的影响 52
(2)分组波电源的影响 53
8.6.7 电火花线切割工艺效果分析 53
1.高速走丝速度vs对切割速度vwi的影响 53
2.电极丝材料及直径对线切割工艺效果的影响 53
3.工件厚度h对切割速度vwi的影响 54
4.电极丝往复运动引起的黑白条纹和斜度 54
5.不同工作液对工艺参数的影响 54
6.不同电参数对线切割表面熔化层的影响 55
7.低速走丝电火花线切割工艺效果 56
8.6.8 线切割引起断丝的原因 58
8.6.9 线切割加工中工件产生的变形和裂纹 58
1.产生变形和裂纹的规律 58
2.减小变形和裂纹的措施 59
8.6.10 线切割机床的扩展运用 59
1.用普通线切割机床加工带斜度凹模的简易方法 59
2.用两轴控制加工三维曲面 60
8.6.11 编制简单零件线切割加工程序的方法 62
1.程序格式 62
(1)3B格式 62
(2)ISO格式 64
2.零件编程实例 65
3.有公差编程尺寸的计算法 66
4.间隙补偿值f 66
(1)间隙补偿值f的确定方法 66
(2)考虑间隙补偿值f的编程实例 67
8.6.12 线切割自动编程 69
1.人机对话式自动编程 69
2.语言式自动编程 69
3.图形交互式自动编程 70
8.7 电化学加工 71
8.7.1 电化学加工原理及设备组成 71
1.电化学加工原理 71
2.电化学加工用电源 73
3.电化学加工的分类 74
8.7.2 电解加工 74
1.电解加工的特点及其应用 74
2.电解加工的设备 76
(1)电解加工机床 76
(2)电解液供给系统 77
3.电解加工的基本规律 79
4.电解加工的阴极设计 82
5.电解加工的电解液 84
(1)电解液的种类及特性 84
(2)常用的电解液配方 85
6.混气电解加工 88
(1)气液混合比 88
(2)气液混合腔的结构类型 89
7.脉冲电解加工 89
8.小孔束流电解加工 90
9.数控展成电解加工 90
10.电解加工的应用 90
11.电解加工常见疵病及消除方法 95
8.7.3 电化学抛光 95
1.影响电化学抛光的主要因素 95
2.金属的电化学抛光工艺及应用 96
8.7.4 电解磨削 99
1.电解磨削的加工原理 99
2.电解磨削用的电解液 99
3.电解磨床及改装 100
4.电解磨削的工艺参数 101
5.电解研磨 101
8.7.5 在线电解修锐镜面磨削(ELID) 101
1.ELID磨削技术的优点 102
2.ELID磨削装置 102
8.8 超声加工 103
8.8.1 超声加工的原理及特点 103
8.8.2 超声加工的设备组成 103
1.超声加工设备的规格与技术性能 103
2.振幅变幅杆(扩大棒)的设计、计算和工具长度的确定 104
(1)振幅变幅杆的设计与计算 104
(2)工具长度的确定 106
8.8.3 超声加工的基本工艺规律 107
1.超声加工的加工速度 107
2.超声加工的加工精度 108
3.超声加工的表面粗糙度 108
8.8.4 超声加工的应用 109
1.打孔、套料与切断 109
2.超声回转加工 109
3.超声清洗加工 110
8.9 高能束加工 111
8.9.1 激光加工 111
1.激光加工的原理及特点 111
2.激光加工的设备组成 112
(1)固体激光加工设备 112
(2)CO2气体激光加工设备 113
3.激光切割的工艺参数 113
8.9.2 电子束加工 115
1.电子束加工的原理及特点 115
2.电子束加工的工艺规律 116
3.电子束加工的应用 116
8.9.3 离子束加工 117
1.离子束加工及其特点 117
2.离子束加工的应用 118
8.10 化学加工 119
8.10.1 化学铣切加工 119
(1)化学铣切的特点 119
(2)化学铣切的缺点 119
(3)化学铣切的应用范围 119
(4)化学铣切的主要过程 120
8.10.2 光化学腐蚀加工 121
8.10.3 化学抛光 121
8.11 水喷射切割 121
1.水喷射切割加工的基本原理及特点 121
2.水喷射切割加工的基本工艺规律 121
3.水喷射切割加工的应用 122
8.12 磨料喷射加工 122
8.12.1 磨料喷射加工的基本原理 122
8.12.2 磨料喷射加工的基本工艺规律 123
8.12.3 磨料喷射加工的应用 124
8.13 复合加工 124
8.13.1 复合加工的一般概念 124
8.13.2 超声-电火花复合加工 124
1.超声-电火花复合加工的原理 124
2.超声-电火花复合加工影响因素分析 124
3.超声-电火花复合加工的应用举例 125
8.13.3 电解-电火花复合加工 125
8.13.4 超声-电解复合加工 125
参考文献 126
第9章 精密加工和纳米加工 3
9.1 概述 3
9.1.1 精密加工与纳米加工的概念、范畴、特点和分类 3
1.精密加工与纳米加工的概念 3
(1)尺度加工 3
(2)精密加工和超精密加工 3
(3)纳米加工 3
(4)微细加工和超微细加工 3
(5)光整加工和精整加工 3
2.精密加工和超精密加工的特点 3
3.精密加工和超精密加工方法及其分类 4
9.1.2 精密加工和超精密加工原理 7
1.进化加工原理 7
2.微量加工原理 7
(1)微量切除 7
(2)材料缺陷与破坏方式 7
(3)加工能量 8
9.1.3 精密加工和纳米加工的工艺系统 8
1.影响精密加工和超精密加工的工艺因素 8
2.精密加工和超精密加工的工艺系统结构 8
9.1.4 精密加工和纳米加工技术的地位、作用和发展 8
1.精密加工和纳米加工技术的地位和作用 8
2.精密加工和纳米加工技术的发展 9
9.2金刚石刀具超精密切削加工 9
9.2.1 金刚石刀具超精密切削机理 9
1.金刚石刀具超精密切削的切屑形成 9
2.加工表面的形成及其加工质量 9
3.表面破坏层及应力状态 9
9.2.2 金刚石刀具的设计和刃磨 10
1.金刚石的性能和结构 10
2.金刚石刀具的设计 12
(1)金刚石的晶体定向 12
(2)金刚石的剖分 13
(3)金刚石刀具的结构 13
(4)金刚石刀具的刃磨 14
9.2.3 金刚石刀具超精密切削的工艺规律 18
1.影响金刚石刀具超精密切削的因素 18
2.金刚石刀具超精密切削工艺 18
(1)金刚石刀具超精密切削参数选择 18
(2)金刚石刀具的刀刃锋锐度 19
(3)金刚石刀具的磨损和破损 19
9.2.4 金刚石刀具超精密切削的应用和发展 20
9.3 精密和超精密磨削加工 21
9.3.1 精密磨削加工 21
1.普通砂轮精密磨削机理 21
2.普通砂轮精密磨削砂轮选择 21
3.精密磨床的选择 22
4.普通砂轮精密磨削时的砂轮修整 22
5.普通砂轮精密磨削时的磨削用量 23
9.3.2 超硬磨料砂轮精密磨削 23
1.超硬磨料砂轮精密磨削特点及应用 23
2.超硬磨料砂轮精密磨削机理 23
3.超硬磨料砂轮精密磨削用量选择 23
4.超硬磨料砂轮磨削时的磨削液选择 23
5.超硬磨料砂轮修整 24
(1)超硬磨料砂轮修整过程 24
(2)超硬磨料砂轮的修整方法 24
9.3.3 超精密磨削加工 25
1.超精密磨削的概念、机理、特点及其应用 25
(1)超精密磨削的概念 25
(2)超精密磨削机理 25
(3)超精密磨削的特点及其应用 26
2.超硬磨料微粉砂轮 26
3.超精密磨床 26
4.超精密磨削工艺 26
9.3.4 精密砂带磨削 28
1.精密砂带磨削方式、特点和应用范围 28
2.精密砂带磨削机理 28
3.精密砂带磨床和砂带磨削头架(装置) 28
4.精密砂带磨削工艺 28
9.4 精密光整加工 29
9.4.1 研磨加工 29
1.传统研磨加工的概念、分类、特点及应用范围 29
2.研磨机理和加工要素 30
3.精密和超精密研磨方法 31
9.4.2 抛光加工 32
1.抛光加工机理和加工要素 32
2.抛光和研磨复合加工 32
3.精密和超精密抛光方法 32
9.4.3 珩磨 36
1.珩磨加工原理、特点和应用范围 36
2.珩磨头 37
3.珩磨工艺要素选择 37
4.新型珩磨加工方法 38
9.4.4 超精加工 38
1.超精加工的原理、特点及其应用范围 38
2.超精加工头 39
3.超精加工工艺要素选择 39
4.超精研抛 40
9.4.5 挤压研抛 40
1.挤压研抛原理及应用 40
2.挤压研抛的工作要素 40
9.4.6 砂带振动研抛 40
1.砂带振动研抛原理 40
2.砂带振动研抛运动轨迹 41
9.4.7 喷射加工 41
1.喷射加工的原理和类型 41
2.喷射加工的工艺因素 41
3.喷射加工的应用 42
9.4.8
- 《激光加工实训技能指导理实一体化教程 下》王秀军,徐永红主编;刘波,刘克生副主编 2017
- 《先进激光加工技能实训》肖海兵主编 2019
- 《三毛传 你松开手我便落入茫茫宇宙》(中国)程碧 2019
- 《高等教育双机械基础课程系列教材 高等学校教材 机械设计课程设计手册 第5版》吴宗泽,罗圣国,高志,李威 2018
- 《AutoCAD机械设计实例精解 2019中文版》北京兆迪科技有限公司编著 2019
- 《菜籽油加工技术》罗质主编 2019
- 《蔬菜腌制加工技术》闫广金著 2019
- 《食品工厂机械装备》方祖成,李冬生,汪超 2017
- 《高分子材料与加工实验教程》刘昕责任编辑;(中国)胡扬剑,舒友,罗琼林 2019
- 《“十一五”国家级规划教材 工程材料与机械制造基础 下 第3版》(中国)李爱菊 2019
- 《指向核心素养 北京十一学校名师教学设计 英语 七年级 上 配人教版》周志英总主编 2019
- 《北京生态环境保护》《北京环境保护丛书》编委会编著 2018
- 《高等教育双机械基础课程系列教材 高等学校教材 机械设计课程设计手册 第5版》吴宗泽,罗圣国,高志,李威 2018
- 《指向核心素养 北京十一学校名师教学设计 英语 九年级 上 配人教版》周志英总主编 2019
- 《高等院校旅游专业系列教材 旅游企业岗位培训系列教材 新编北京导游英语》杨昆,鄢莉,谭明华 2019
- 《中国十大出版家》王震,贺越明著 1991
- 《近代民营出版机构的英语函授教育 以“商务、中华、开明”函授学校为个案 1915年-1946年版》丁伟 2017
- 《新工业时代 世界级工业家张毓强和他的“新石头记”》秦朔 2019
- 《智能制造高技能人才培养规划丛书 ABB工业机器人虚拟仿真教程》(中国)工控帮教研组 2019
- 《AutoCAD机械设计实例精解 2019中文版》北京兆迪科技有限公司编著 2019