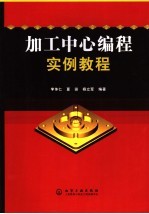
第1章 加工中心基础知识 1
1.1 加工中心的分类及特点 1
1.1.1 加工中心的分类 1
1.1.2 加工中心的主要特点 4
1.2 加工中心的工作原理 6
1.2.1 数控机床的工作原理与工作方式 6
1.2.2 控制方式 7
1.3.2 自动编程 9
1.3.1 手工编程 9
1.3 数控编程的类型及发展 9
第2章 数控加工基础 12
2.1 数控加工程序及加工功能 12
2.1.1 数控程序中的字、代码与字符 12
2.1.2 数控程序中字的功能 13
2.1.3 数控程序的结构与格式 17
2.2 数控机床的坐标系统 18
2.2.1 机床坐标系的有关规定 18
2.2.2 机床坐标系的定义 18
2.2.3 机床原点与机床参考点 21
2.2.4 工件坐标系 22
2.2.5 绝对坐标系与增量(相对)坐标系 25
2.3 数控程序的编制 26
2.3.1 数控程序编制的内容及步骤 26
2.3.2 加工中心编程的特点 29
2.4 数控加工中的刀具补偿 30
2.4.1 刀具长度补偿 30
2.4.2 刀具半径补偿 33
2.5.1 加工中心中嵌刀片的使用 40
2.5 数控加工的刀具系统 40
2.5.2 车削刀具的编码及选择 44
2.5.3 铣削刀具的类型及选择 47
2.5.4 刀具测量 50
2.6 加工中心的工作方式 53
第3章 加工流程 54
3.1 数控加工工作流程 54
3.2 偏心套加工实例 55
3.2.1 偏心套零件的加工工艺分析 55
3.2.2 工序5的数控加工 58
3.2.3 工序7的数控加工 62
3.2.4 工序10的数控加工 64
第4章 车削加工中心及编程 66
4.1 车削中心换刀系统 66
4.2 车削加工的编程特点 66
4.3 车削中心数控功能简介 68
4.3.1 进给功能F 68
4.3.2 主轴功能S 68
4.3.3 刀具功能T 70
4.3.4 准备功能G 71
4.3.5 辅助功能M 71
4.4 工件坐标系设定(G50) 74
4.5 车削加工常用编程指令 75
4.6 螺纹加工指令 80
4.6.1 基本螺纹切削指令G32 80
4.6.2 螺纹切削循环指令G92 83
4.6.3 螺纹切削复合循环指令G76 85
4.7.1 单一形状固定循环 87
4.7 车削加工循环指令 87
4.7.2 复合车削循环 91
4.8 倒角、倒圆编程 100
4.9 车削加工编程实例 102
4.9.1 轴类零件加工编程实例 102
4.9.2 盘类零件加工编程实例 104
第5章 铣削加工中心及其数控编程 108
5.1 加工中心的组成 108
5.2 加工中心的换刀类型 108
5.4 刀具在主轴和刀库的固定方式 109
5.4.1 刀具在机床主轴上的固定方式 109
5.3 加工中心的刀库类型 109
5.3.2 链式刀库 109
5.3.1 盘形刀库 109
5.4.2 刀具在刀库中的固定方式 111
5.5 机械手的换刀形式 111
5.5.1 主轴上的刀具交换 111
5.7 换刀时间 113
5.6.2 任意选择方式 113
5.6.1 顺序选择方式 113
5.5.2 刀库的取刀和装刀 113
5.6 选刀方式 113
5.8 台湾高明精机KM-3000SD龙门式加工中心换刀系统 114
5.9 台湾高明精机KM-3000SD龙门式加工中心上新型刀座的使用 115
5.10 日本牧野公司MAKINO 1210A卧式加工中心 116
5.10.1 刀库取刀 116
5.10.2 主轴换刀 117
5.10.3 刀库装刀 118
5.12.1 自动原点复归 119
5.11 牧野加工中心换刀过程的讨论 119
5.12 刀具交换的编程 119
5.12.2 刀具交换(ATC)条件 120
5.12.3 刀具交换指令 120
5.12.4 刀具交换编程 120
5.13 交换工作台 122
5.14 托盘自动交换的类型 123
5.15 编程指令 124
5.16.1 变量 126
5.16 用户宏程序 126
5.16.2 运算 127
5.16.3 系统变量 128
5.16.4 转移和循环 131
5.16.5 宏程序调用 132
第6章 加工程序实例 136
6.1 机床坐标系和工件坐标系的区别 136
6.2 G92与G54~G59之间的区别 136
6.3 工件坐标系中子坐标系的使用(G52) 137
6.4 工件坐标系建立的原则 138
6.5 在加工中心上,使用机床坐标系选择(G53),指定换刀位置 140
6.6 立卧加工中心的刀长度补偿与数控车刀偏补偿的区别 141
6.7 数控车刀尖半径补偿 142
6.8 在G18平面使用刀具半径补偿加工外形轮廓 142
6.9 使用子程序调用,加工工件外形(一) 144
6.10 使用子程序调用,加工工件外形(二) 145
6.11 刀具半径偏置中预读(缓冲)功能的使用 145
6.12 缩放比例(G50、G51) 148
6.13.2 分度工作台(B)轴 150
6.13.1 分度轴和旋转轴的区别 150
6.13 卧式加工中心的分度轴和旋转轴 150
6.14 坐标系旋转(G68、G69) 152
6.15 可编程镜像 154
6.16 大平面的多次铣削 155
6.17 圆弧插补的进给率 157
6.18 加工中心刀具长度补偿的三种方法 158
6.19 工件外形和内腔轮廓的铣削 160
6.20.1 螺栓孔圆周分布模式 162
6.20 圆周分布孔的加工 162
6.20.2 螺栓圆周分布孔的计算公式 163
6.20.3 用极坐标加工螺栓圆周分布孔 165
6.20.4 用坐标旋转加工螺栓圆周分布孔 167
6.20.5 用宏程序加工螺栓圆周分布孔 168
6.21 沉孔的底面加工 168
6.22 背镗孔 169
6.22.1 主轴定向 169
6.22.2 背镗孔 169
6.24 浮动攻螺纹加工 172
6.23 用T形槽铣刀在孔中切槽加工 172
6.25 精度检验编程 173
6.26 使用啄式钻孔循环(G83),加工孔 175
6.27 使用啄式钻孔循环(G73),加工孔 176
6.28 综合实例(一) 176
6.29 综合实例(二),板类零件的加工 188
第7章 自动编程 196
7.1 自动编程过程 196
7.2.1 MasterCAM编程系统概述 197
7.2 MasterCAM编程系统 197
7.2.2 MasterCAM Mill9.0铣削加工的刀具路径 198
7.2.3 二维数控加工实例 199
7.2.4 三维数控加工实例 220
附录 236
附表1 FANUC 0i MC数控铣床G功能代码-M代码 236
附表2 FANUC 0i MC数控铣床编码字符的意义 237
附表3 FANUC 0i MC数控系统的准备功能M代码及其功能 237
附表4 FANUC 0i MC数控铣床G功能代码 238
参考文献 243
- 《激光加工实训技能指导理实一体化教程 下》王秀军,徐永红主编;刘波,刘克生副主编 2017
- 《程序逻辑及C语言编程》卢卫中,杨丽芳主编 2019
- 《先进激光加工技能实训》肖海兵主编 2019
- 《每个人的故乡都是宇宙中心》许石林著 2019
- 《CINEMA 4D新手快速进阶实例教学 商迪》商迪 2020
- 《AutoCAD机械设计实例精解 2019中文版》北京兆迪科技有限公司编著 2019
- 《全国职业院校工业机器人技术专业规划教材 工业机器人现场编程》(中国)项万明 2019
- 《菜籽油加工技术》罗质主编 2019
- 《编程超有趣 奇妙Python轻松学 第1辑》HelloCode人工智能国际研究组 2018
- 《蔬菜腌制加工技术》闫广金著 2019