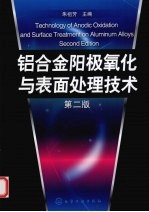
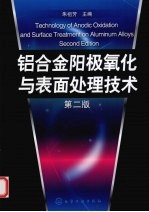
铝合金阳极氧化与表面处理技术 2版PDF电子书下载
- 电子书积分:13 积分如何计算积分?
- 作 者:朱祖芳编著
- 出 版 社:北京:化学工业出版社
- 出版年份:2010
- ISBN:9787122069856
- 页数:399 页
第1章 引论 1
1.1 铝的腐蚀性 2
1.2 铝的腐蚀形态 4
1.3 铝合金 5
1.3.1 铝合金系 5
1.3.2 典型铝合金的特性及应用 6
1.4 铝合金表面技术概述 7
1.5 铝的阳极氧化技术 8
1.5.1 铝阳极氧化膜的特性 8
1.5.2 铝合金与阳极氧化 9
1.5.3 铝的氧化膜 9
1.5.4 铝阳极氧化膜的应用 9
1.6 铝的其他表面处理技术 10
1.6.1 铝的化学转化技术 10
1.6.2 铝的涂装技术 10
1.6.3 铝的电镀 11
1.6.4 铝的珐琅和搪瓷涂层技术 11
参考文献 11
第2章 铝的表面机械预处理 13
2.1 磨光 13
2.1.1 磨光轮 14
2.1.2 磨料的选用 14
2.1.3 磨轮与磨料的黏结 15
2.1.4 磨光操作要求 15
2.2 抛光 16
2.2.1 抛光机理 16
2.2.2 抛光剂的类型 17
2.2.3 抛光剂的选择 18
2.2.4 抛光轮的种类、制作和功用 19
2.3 抛光机械及操作 20
2.3.1 抛光机械的主要部件、类型和功用 21
2.3.2 抛光操作 24
2.4 磨光、抛光常见问题及解决办法 25
2.5 其他机械处理方法 26
2.5.1 喷砂(丸) 26
2.5.2 刷光 27
2.5.3 滚光 27
2.5.4 磨痕装饰机械处理 27
参考文献 27
第3章 铝的化学预处理 29
3.1 概述 29
3.2 脱脂 30
3.2.1 酸性脱脂 30
3.2.2 碱性脱脂 31
3.2.3 有机溶剂脱脂 32
3.3 碱洗 33
3.3.1 碱洗原理 33
3.3.2 碱洗工艺 34
3.3.3 槽液回收及循环利用 35
3.3.4 长寿命添加剂碱洗工艺 36
3.3.5 碱洗缺陷及对策 38
3.4 除灰 40
3.4.1 硝酸除灰 41
3.4.2 硫酸除灰 41
3.5 氟化物砂面处理 43
3.5.1 典型工艺条件 43
3.5.2 槽液沉淀物处理方法 44
3.5.3 缺陷及对策 44
参考文献 45
第4章 铝的化学抛光和电化学抛光 46
4.1 概论 46
4.2 化学和电化学抛光历程与机理 49
4.2.1 化学抛光 49
4.2.2 电化学抛光 51
4.3 以磷酸为基的化学抛光工艺 52
4.3.1 磷酸-硫酸化学抛光 52
4.3.2 磷酸-硝酸化学抛光 53
4.3.3 磷酸-硫酸-硝酸化学抛光 54
4.3.4 磷酸乙酸-硝酸化学抛光 55
4.3.5 磷酸为基的化学抛光生产设备 56
4.3.6 含硝酸的磷酸基化学抛光液的工艺因素 56
4.4 硝酸-氟化物化学抛光工艺 58
4.4.1 硝酸-氢氟酸-阿拉伯胶化学抛光 58
4.4.2 硝酸-氢氟酸-芳香胺化学抛光 60
4.5 典型的电化学抛光工艺 60
4.5.1 碳酸钠磷酸三钠碱性电化学抛光 61
4.5.2 磷酸-铬酸-硫酸电化学抛光 63
4.5.3 氟硼酸电化学抛光 65
4.5.4 硫酸-铬酸电化学抛光 66
4.5.5 无铬酸电化学抛光 67
4.6 抛光缺陷及对策 68
4.6.1 化学抛光缺陷及对策 68
4.6.2 电化学抛光缺陷及对策 69
参考文献 70
第5章 铝的化学转化处理 71
5.1 化学转化处理的技术进展 71
5.2 化学氧化 73
5.2.1 化学氧化膜的用途 73
5.2.2 化学氧化膜的性能 73
5.2.3 化学氧化膜的生长 75
5.2.4 化学氧化膜的成分 75
5.3 铬酸盐处理 75
5.3.1 铬酸盐处理溶液 76
5.3.2 铬酸盐处理反应 77
5.3.3 铬化膜的性状 77
5.4 磷铬酸盐处理 78
5.4.1 磷铬酸盐处理溶液 78
5.4.2 磷铬化膜的生成 79
5.4.3 磷铬化膜的性状 79
5.5 磷酸盐处理 81
5.6 无铬化学转化处理 81
5.6.1 无铬化学转化处理 81
5.6.2 无铬化学转化膜的性状 83
5.7 无铬化学转化技术的研究动态 84
5.7.1 有机硅烷处理 84
5.7.2 稀土盐转化处理 84
5.7.3 有机酸转化处理 85
5.7.4 SAM处理 86
5.8 化学转化膜的鉴别 86
5.8.1 外观检验 86
5.8.2 膜厚检验 87
5.8.3 附着性检验 87
5.8.4 腐蚀试验 87
参考文献 87
第6章 铝阳极氧化与阳极氧化膜 89
6.1 铝阳极氧化的过程 90
6.1.1 铝阳极氧化按照电解溶液性质的分类 90
6.1.2 铝阳极氧化的反应过程 91
6.1.3 阳极氧化过程中铝合金合金化成分的影响 94
6.2 阳极氧化膜的结构与形貌 95
6.2.1 阳极氧化膜的多孔型结构与形貌的直接观测 95
6.2.2 阳极氧化膜的结构模型和结构参数 97
6.2.3 多孔型阳极氧化膜的微孔形成 98
6.3 多孔型阳极氧化膜的厚度、结构和成分 99
6.3.1 阻挡层的厚度 99
6.3.2 多孔层的厚度和结构 100
6.3.3 阻挡层的成分 102
6.3.4 多孔层的成分 103
6.4 结晶性阳极氧化膜的生长 105
6.5 阳极氧化膜的生成机理 107
6.5.1 壁垒型阳极氧化膜 107
6.5.2 多孔型阳极氧化膜 108
参考文献 110
第7章 阳极氧化工艺 111
7.1 硫酸阳极氧化工艺 111
7.1.1 硫酸阳极氧化工艺规范 112
7.1.2 阳极氧化工艺参数的影响 112
7.1.3 硫酸溶液中铝离子和杂质的影响 122
7.1.4 膜厚及其均匀性的控制 124
7.1.5 阳极氧化膜的缺陷及其防止方法 125
7.1.6 硫酸交流阳极氧化 125
7.2 其他酸阳极氧化工艺 125
7.2.1 铬酸阳极氧化工艺 127
7.2.2 草酸阳极氧化工艺 128
7.2.3 磷酸阳极氧化工艺 129
参考文献 131
第8章 铝的硬质阳极氧化 132
8.1 概述 132
8.2 硬质阳极氧化与铝合金材料的关系 133
8.3 硫酸溶液的硬质阳极氧化 135
8.4 硫酸硬质阳极氧化工艺参数的影响 137
8.5 非硫酸溶液或非单一硫酸溶液的硬质阳极氧化 139
8.5.1 草酸溶液的硬质阳极氧化 139
8.5.2 以硫酸为基础的混合酸硬质阳极氧化 139
8.5.3 其他混合有机酸硬质阳极氧化 140
8.5.4 硬质阳极氧化复合技术 141
8.6 硬质阳极氧化电源波形的改进和脉冲阳极氧化 142
8.6.1 直流脉冲硬质阳极氧化 143
8.6.2 交直流叠加硬质阳极氧化 145
8.6.3 电流反向法硬质阳极氧化 145
8.6.4 脉冲硬质阳极氧化膜的性能 146
8.7 铸造铝合金硬质阳极氧化 147
8.8 硬质阳极氧化膜的性能及检验 148
参考文献 153
第9章 铝及铝合金的微弧氧化 154
9.1 概述 154
9.2 微弧氧化现象及其特点 155
9.3 微弧氧化的基本设备 158
9.4 微弧氧化工艺 161
9.4.1 微弧氧化槽液成分 161
9.4.2 微弧氧化工艺 162
9.5 微弧氧化膜的主要性能 163
9.6 微弧氧化技术的应用 166
参考文献 170
第10章 铝阳极氧化膜的电解着色 171
10.1 概述 171
10.2 电解着色机理 173
10.2.1 电解着色阳极氧化膜 173
10.2.2 电解着色时金属离子和氢离子的放电 174
10.2.3 阻挡层及其散裂脱落 175
10.2.4 直流电解着色特点 175
10.2.5 电解着色的电源波形 176
10.2.6 电解着色的发色原理 176
10.3 锡盐电解着色 177
10.3.1 锡盐着色溶液的稳定方法 177
10.3.2 添加剂的开发现状 178
10.3.3 典型的锡盐电解着色工艺 181
10.3.4 锡盐电解着色工艺参数的影响 182
10.4 镍盐电解着色 185
10.4.1 镍盐电解着色的优缺点 185
10.4.2 交流镍盐电解着色 186
10.4.3 直流镍盐电解着色 187
10.4.4 镍盐电解着色的电化学研究 189
10.5 其他金属盐电解着色 191
10.5.1 锰酸盐电解着色 192
10.5.2 硒酸盐电解着色 192
10.6 干涉光效应着色的工业应用 193
10.6.1 多色化工艺的特点和发展 194
10.6.2 利用扩孔处理显色 194
10.6.3 利用调整阻挡层与孔底的显色 196
10.6.4 典型的多色化着色生产工艺 197
参考文献 198
第11章 铝阳极氧化膜的染色 199
11.1 染色对氧化膜的要求 199
11.2 染料染色机理 200
11.2.1 有机染料染色机理 200
11.2.2 无机染料染色机理 201
11.3 有机染料的选择 201
11.3.1 几种有机染料的特性 201
11.3.2 适用有机染料的色系分类 203
11.4 色彩的组合与调配 204
11.5 有机染料染色工艺 205
11.5.1 工艺流程 205
11.5.2 染色液的配制方法 205
11.5.3 有机染料染色工艺规范 206
11.5.4 染色液中杂质离子的影响及控制 209
11.5.5 操作注意事项 210
11.5.6 染色后的封孔处理 211
11.5.7 常用有机染料染色工艺实例 212
11.5.8 染色问题的产生原因及排除方法 212
11.5.9 不合格染色膜的褪色 212
11.5.10 染色废液的再生和处理 216
11.6 无机染料染色工艺 216
11.6.1 无机染色的化学反应 216
11.6.2 常用无机染色工艺规范 218
11.7 染色的特殊方法 219
11.7.1 双色染色工艺 219
11.7.2 渗透染色工艺 219
11.7.3 花样染色工艺 220
11.7.4 转移印花工艺 220
11.7.5 感光染色工艺 220
11.7.6 印染染色法 221
参考文献 221
第12章 铝阳极氧化膜的封孔 223
12.1 封孔技术的发展及分类 223
12.2 封孔质量的品质要求 224
12.3 热封孔工艺 225
12.3.1 热封孔机理 225
12.3.2 沸水封孔参数对封孔质量的影响 228
12.3.3 水中杂质的影响 229
12.3.4 封孔灰的防止措施 230
12.4 冷封孔工艺 231
12.4.1 冷封孔机理 231
12.4.2 冷封孔的溶液因素 232
12.4.3 冷封孔的工艺参数 233
12.4.4 冷封孔的后处理 234
12.4.5 冷封孔工艺的最佳控制 235
12.5 高温水蒸气封孔工艺 236
12.6 无机盐封孔工艺 237
12.6.1 铬酸盐封孔 237
12.6.2 硅酸盐封孔 238
12.6.3 乙酸镍封孔 239
12.7 新型中温封孔 240
12.7.1 无镍中温封孔 240
12.7.2 无重金属的中温封孔 241
12.7.3 “无金属”的中温封孔 242
12.8 有机物封孔技术 242
12.8.1 有机酸封孔 242
12.8.2 其他非水溶液的有机物封孔 243
12.9 封孔引起的阳极氧化膜缺陷 244
参考文献 245
第13章 铝阳极氧化膜的电泳涂漆 247
13.1 电泳涂漆与涂料 247
13.1.1 电泳涂漆 247
13.1.2 电泳涂料 248
13.2 铝合金阳极氧化膜电泳涂漆工艺 249
13.2.1 电泳涂漆原理 249
13.2.2 电泳涂漆的专用术语 252
13.2.3 铝及铝合金电泳涂漆工艺 253
13.2.4 铝材电泳涂漆的影响因素 254
13.2.5 电泳涂漆引起电解着色氧化膜褪色原因分析 257
13.3 电泳涂漆主要设备 258
13.3.1 电泳槽 258
13.3.2 阴极板 259
13.3.3 电源 260
13.3.4 精制系统 260
13.3.5 回收系统 261
13.3.6 加漆系统 261
13.3.7 固化炉 262
13.4 电泳涂漆产品的品质与缺陷 262
13.4.1 电泳涂漆产品的品质要求 262
13.4.2 电泳涂漆产品常见缺陷及防治措施 264
13.5 铝阳极氧化膜彩色及消光电泳涂漆 266
13.5.1 彩色及消光电泳简介 266
13.5.2 彩色电泳涂漆原理 267
13.5.3 阳极氧化与电泳膜复合色 268
参考文献 268
第14章 铝及铝合金的粉末喷涂 269
14.1 粉末涂装技术的发展 269
14.1.1 粉末涂装简介 269
14.1.2 粉末涂装特点 269
14.1.3 静电粉末涂装法 271
14.2 粉末静电喷涂工艺 274
14.2.1 粉末涂料的选择 274
14.2.2 粉末静电喷涂工艺流程 277
14.3 粉末静电喷涂设备 277
14.3.1 静电粉末喷枪 277
14.3.2 粉末喷涂的供粉装置 280
14.3.3 喷粉室 282
14.3.4 粉末涂料回收设备 282
14.3.5 固化炉 284
14.4 粉末静电喷涂的主要影响因素 284
14.5 粉末静电喷涂中的常见问题 287
14.6 铝材粉末静电涂装产品质量要求 290
14.7 粉末静电喷涂产品常见缺陷及防治措施 290
14.8 粉末静电涂装图纹处理技术 292
14.8.1 热转印用粉末涂料的组成 293
14.8.2 热转印图纹底粉喷涂质量的要求 293
14.8.3 热转印图纹生产工艺流程 294
14.9 粉末涂料与涂装的发展趋势 294
参考文献 295
第15章 铝及铝合金的液相静电喷涂 297
15.1 液相静电喷涂概述 297
15.1.1 液相喷涂方法简介 297
15.1.2 液相喷涂涂料简介 298
15.2 液相静电喷涂的原理 300
15.3 液相静电喷涂的特点 301
15.4 液相静电喷涂涂装主要设备 302
15.5 液相静电涂装的主要工艺参数 304
15.6 液相静电涂装的影响因素及工艺控制 306
15.7 铝材的氟碳喷涂工艺 308
15.8 氟碳涂层的相关指标和质量标准 312
15.9 液相喷涂产品常见缺陷及预防措施 313
15.10 液相喷涂涂膜综合性能的控制方法 315
参考文献 315
第16章 铝及铝合金的辊涂 317
16.1 辊涂概述 317
16.1.1 辊涂原理 317
16.1.2 常用涂料 318
16.2 铝卷材辊涂工艺 320
16.2.1 引入部分 320
16.2.2 前处理部分 321
16.2.3 化学预处理的品质控制 323
16.2.4 涂装部分 324
16.2.5 铝卷材的烘烤和冷却 326
16.2.6 引出部分 328
16.3 铝板材辊涂工艺 329
16.4 铝卷材辊涂质量的主要影响因素 330
16.4.1 铝卷材坯料质量的影响 330
16.4.2 涂料施工性能及黏度变化的影响 330
16.4.3 涂料中颜料粒度的影响 331
16.4.4 涂装辊材质及涂装辊质量的影响 332
16.5 铝卷材辊涂的标准及质量要求 333
16.5.1 性能指标 333
16.5.2 外观质量 334
16.5.3 涂装过程的质量控制 334
16.5.4 成品常见缺陷产生原因及控制措施 335
16.6 铝材辊涂的发展方向 337
参考文献 337
第17章 铝及铝合金的电镀 339
17.1 铝及其合金制件电镀的重要性 339
17.2 铝及其合金的化学物理特性 340
17.3 镀前预处理方法 340
17.3.1 预处理常规方法及工艺规范 340
17.3.2 预处理的特殊方法 341
17.4 预处理特殊方法的工艺规范及电镀实例 341
17.4.1 盐酸活化直接镀硬铬 341
17.4.2 直接镀锌或闪镀Zn-Fe合金预镀层 342
17.4.3 直接预镀镍后仿金镀 343
17.4.4 阳极氧化后电镀 343
17.4.5 表面条件化处理后电镀 344
17.4.6 浸锌处理后电镀 345
17.5 铝及其合金制件化学镀镍 348
17.5.1 一般概念 348
17.5.2 化学镀镍机理 348
17.5.3 化学镀前铝的预处理 348
17.5.4 化学镀Ni-P合金实例 348
17.5.5 Ni-P镀层的退除 351
17.6 氟硼酸盐浸镍锌(Ni-Zn)合金层电镀 351
17.6.1 工艺流程 352
17.6.2 工艺规范 352
17.6.3 氟硼酸盐浸镍锌(Ni-Zn)合金机理 352
17.6.4 浸Ni-Zn后电镀工艺 353
17.7 铝及其合金制件化学镀金 353
17.7.1 工艺流程 353
17.7.2 工艺规范 353
17.8 镀层质量的检验 354
17.8.1 外观检查 354
17.8.2 电镀层厚度的测量 354
17.8.3 镀层孔隙率的测定 354
17.8.4 结合力试验 354
17.8.5 镀层显微硬度的测定 354
17.8.6 镀层耐腐蚀性试验 355
17.8.7 镀层钎焊性的测试 355
17.8.8 镀层耐磨性能测试 355
参考文献 356
第18章 阳极氧化膜及高聚物涂层的性能与试验方法 358
18.1 概述 358
18.2 外观质量 359
18.3 颜色和色差 360
18.3.1 目视比色法 360
18.3.2 仪器检测法 360
18.4 阳极氧化膜及高聚物涂层厚度 361
18.4.1 显微镜测量横断面厚度 361
18.4.2 分光束显微镜测量透明膜厚度 362
18.4.3 质量损失法测量阳极氧化膜厚度 362
18.4.4 涡流法测量阳极氧化膜及高聚物涂层厚度 363
18.5 阳极氧化膜封孔质量 363
18.5.1 指印试验 364
18.5.2 酸处理后的染色斑点试验 364
18.5.3 磷铬酸试验 365
18.5.4 导纳试验 366
18.6 耐腐蚀性 366
18.6.1 盐雾腐蚀试验 367
18.6.2 含SO2潮湿大气腐蚀试验[即克氏(Kesternish)试验] 367
18.6.3 马丘(Machu)腐蚀试验 368
18.6.4 耐湿热腐蚀试验 368
18.6.5 滴碱腐蚀试验 368
18.7 耐化学稳定性 369
18.7.1 耐酸试验 369
18.7.2 耐碱试验 369
18.7.3 耐砂浆试验 370
18.7.4 耐洗涤剂试验 370
18.8 耐候性 370
18.8.1 自然曝露耐候试验 371
18.8.2 人工加速耐候试验 372
18.9 硬度 374
18.9.1 压痕硬度试验 374
18.9.2 铅笔硬度试验 375
18.9.3 显微硬度试验 375
18.10 耐磨性 376
18.10.1 喷磨试验仪检测耐磨性 376
18.10.2 轮式磨损试验仪检测耐磨性 376
18.10.3 落砂试验仪检测耐磨性 377
18.11 附着性 378
18.11.1 附着性划格试验 378
18.11.2 附着性仪器试验 379
18.12 耐冲击性 379
18.13 抗杯突性 379
18.14 抗弯曲性 380
18.15 涂层聚合作用性能 380
18.16 阳极氧化膜绝缘性 381
18.17 阳极氧化膜抗变形破裂性 381
18.18 阳极氧化膜抗热裂性 382
18.19 薄阳极氧化膜连续性 382
18.20 耐沸水性 382
18.21 光反射性能 383
18.21.1 镜面光泽度的测量 383
18.21.2 反射率测量 383
18.22 涂层加工性能 384
参考文献 385
附录 386
附录1 我国主要变形铝及铝合金牌号以及主要合金化元素的成分 386
附录2 我国主要铸造铝合金的牌号及主要合金化元素成分 388
附录3 铝阳极氧化槽液的化学分析规程 388
附录4 有关阳极氧化膜及高聚物涂层的性能与试验方法国家标准和国际标准一览表 394
- 《大数据Hadoop 3.X分布式处理实战》吴章勇,杨强 2020
- 《NiFe2O4基惰性阳极材料的烧结行为及应用性能》杜金晶,王斌著 2019
- 《烧结法处理非常规含铁资源研究》王哲著 2018
- 《无机元素原子光谱分析样品预处理技术》吴瑶庆 2019
- 《农村生活污水处理工艺与技术应用》李灵娜著 2019
- 《中国人民大学研究报告系列 中国水处理行业可持续发展战略研究报告 膜工业卷 3》(中国)郑祥,魏源送,王志伟 2019
- 《工业废水处理工艺与设计》高永编著 2019
- 《工业水处理技术》(中国)赵文玉,林华,许立巍 2019
- 《污水处理PPP项目实施方案编制实务》王雁然,方俊,朱立冬 2019
- 《图像处理与图形界面(GUI)设计案例教程》李娜,张丽君 2019
- 《市政工程基础》杨岚编著 2009
- 《家畜百宝 猪、牛、羊、鸡的综合利用》山西省商业厅组织技术处编著 1959
- 《《道德经》200句》崇贤书院编著 2018
- 《高级英语阅读与听说教程》刘秀梅编著 2019
- 《计算机网络与通信基础》谢雨飞,田启川编著 2019
- 《看图自学吉他弹唱教程》陈飞编著 2019
- 《法语词汇认知联想记忆法》刘莲编著 2020
- 《培智学校义务教育实验教科书教师教学用书 生活适应 二年级 上》人民教育出版社,课程教材研究所,特殊教育课程教材研究中心编著 2019
- 《国家社科基金项目申报规范 技巧与案例 第3版 2020》文传浩,夏宇编著 2019
- 《流体力学》张扬军,彭杰,诸葛伟林编著 2019