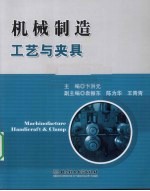
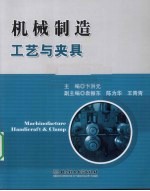
机械制造工艺与夹具PDF电子书下载
- 电子书积分:10 积分如何计算积分?
- 作 者:卞洪元主编
- 出 版 社:北京:北京理工大学出版社
- 出版年份:2010
- ISBN:9787564026073
- 页数:236 页
第1章 机械加工工艺规程的制订 1
1.1 基本概念 2
1.1.1 生产过程和加工工艺过程 2
1.1.2 机械加工工艺过程的组成 2
1.1.3 生产纲领与生产类型 4
1.2 机械加工工艺规程的制订 6
1.2.1 工艺规程概述 6
1.2.2 工艺规程制订 8
1.3 零件的结构工艺性分析 9
1.3.1 零件的结构工艺性分析 9
1.3.2 零件的技术要求分析 11
1.4 毛坯的选择 12
1.4.1 毛坯的类型及特点 12
1.4.2 毛坯选择的原则 13
1.5 定位基准的选择 13
1.5.1 基准的概念及分类 13
1.5.2 工件的定位 15
1.5.3 定位基准的选择 21
1.6 工艺路线的拟定 24
1.6.1 加工方法的选择 24
1.6.2 加工顺序的安排 29
1.6.3 设备与工艺装备的选择 32
1.7 确定加工余量 33
1.7.1 加工余量的概念 33
1.7.2 影响加工余量的因素 34
1.7.3 确定加工余量的方法 35
1.8 工序尺寸及其公差的确定 35
1.8.1 基准重合时,工序尺寸及其公差的计算 35
1.8.2 基准不重合时,工序尺寸及其公差的计算 36
1.9 工艺过程的技术经济性分析 40
1.9.1 工艺过程的技术经济性分析 40
1.9.2 相对技术经济指标的评比 43
本章小结 44
思考题与习题 44
第2章 机床夹具 47
2.1 概述 48
2.1.1 机床夹具的概念 48
2.1.2 机床夹具的作用 48
2.1.3 机床夹具的分类 49
2.1.4 机床夹具的组成 50
2.2 工件在夹具中的定位 51
2.2.1 定位与定位基准 51
2.2.2 定位基准的选择 51
2.2.3 夹具的夹紧装置和定位元件 51
2.2.4 定位误差分析与计算 55
2.3 工件的夹紧 58
2.3.1 夹紧装置的组成及基本要求 58
2.3.2 夹紧装置的选用原则 59
2.3.3 基本夹紧机构 61
2.3.4 复合夹紧机构 63
2.4 典型机床专用夹具 64
2.4.1 车床夹具 64
2.4.2 铣床夹具 68
2.4.3 钻床夹具 72
2.4.4 镗床夹具 76
2.5 现代机床夹具简介 79
2.5.1 机床夹具现代化发展方向 79
2.5.2 组合夹具 80
2.5.3 数控机床夹具 83
2.5.4 自动线夹具 86
本章小结 89
思考题与习题 90
第3章 机械加工精度 93
3.1 概述 93
3.1.1 机械加工精度的概念 94
3.1.2 加工误差的来源和原始误差 94
3.2 工艺系统的几何误差 95
3.2.1 加工原理误差 95
3.2.2 机床的几何误差 95
3.2.3 刀具误差 99
3.2.4 夹具误差和装夹误差 100
3.2.5 调整误差 100
3.2.6 测量误差 100
3.3 工艺系统的受力变形 100
3.4 工艺系统热变形引起的加工误差 108
3.4.1 概述 108
3.4.2 机床热变形对加工精度的影响 108
3.4.3 工件热变形对加工精度的影响 109
3.4.4 刀具的热变形对加工精度的影响 110
3.4.5 减少工艺系统热变形的主要途径 111
3.5 工件内应力引起的加工误差 113
3.5.1 毛坯制造中产生的内应力 113
3.5.2 冷校直带来的内应力 114
3.5.3 切削加工的附加应力 115
3.5.4 减少或消除内应力的措施 115
3.6 保证加工精度的工艺措施 115
3.6.1 直接减少误差法 116
3.6.2 误差补偿法 116
3.6.3 误差转移法 117
3.6.4 “就地加工”法 117
3.6.5 误差分组法 117
3.6.6 误差平均法 118
3.6.7 控制误差法 118
本章小结 122
思考题与习题 123
第4章 机械加工表面质量 124
4.1 概述 125
4.1.1 表面质量的主要内容 125
4.1.2 表面质量对零件使用性能的影响 126
4.2 影响加工表面粗糙度的工艺因素 128
4.2.1 切削加工影响表面粗糙度的因素 128
4.2.2 磨削加工影响表面粗糙度的工艺因素 130
4.3 影响加工表面物理力学性能的因素 132
4.3.1 表面层的加工硬化 132
4.3.2 表面层金相组织的变化 133
4.3.3 表面层的残余应力 134
4.4 机械加工中的振动 136
4.4.1 机械振动现象及其分类 136
4.4.2 机械加工中的受迫振动与抑制措施 137
4.4.3 机械加工中的自激振动及其抑制措施 138
本章小结 143
思考题与习题 144
第5章 典型零件加工工艺 146
5.1 轴类零件加工工艺 147
5.1.1 概述 147
5.1.2 轴类零件加工工艺概述 148
5.1.3 典型轴类零件加工工艺分析 151
5.2 套筒类零件加工工艺 157
5.2.1 概述 157
5.2.2 套筒类零件加工工艺过程及分析 158
5.3 箱体类零件加工工艺 163
5.3.1 概述 163
5.3.2 箱体类零件的加工工艺 166
5.3.3 箱体类零件的加工工艺分析 169
5.3.4 箱体类零件加工工艺过程 174
5.4 圆柱齿轮加工工艺 179
5.4.1 概述 179
5.4.2 圆柱齿轮加工工艺分析 181
5.4.3 圆柱齿轮的加工工艺过程 184
本章小结 189
思考题与习题 190
第6章 机械装配工艺基础 192
6.1 概述 192
6.1.1 装配的概念 192
6.1.2 装配工艺的内容 193
6.2 机械产品的装配精度 194
6.3 装配尺寸链 195
6.3.1 装配尺寸链的基本概念 195
6.3.2 装配尺寸链的建立 196
6.3.3 装配尺寸链的计算 196
6.4 保证装配精度的方法 198
6.4.1 互换装配法 198
6.4.2 选配装配法 198
6.4.3 修配装配法 200
6.4.4 调整装配法 202
6.5 装配的生产类型和组织形式 203
6.5.1 装配的生产类型及其特点 203
6.5.2 装配的组织形式 204
6.6 装配工艺规程的制订 205
6.6.1 制订装配工艺规程应遵循的原则 205
6.6.2 制订装配工艺所需的原始资料 206
6.6.3 装配工艺规程的内容 206
6.6.4 制订装配工艺规程的步骤 206
6.7 装配工艺规程编制实例 209
6.7.1 主轴部件的结构 209
6.7.2 主轴部件的装配技术要求 210
6.7.3 主轴部件的装配工艺过程 210
本章小结 212
思考题与习题 213
第7章 现代机械制造工艺技术 214
7.1 成组技术 215
7.1.1 概述 215
7.1.2 零件的分类编码系统 216
7.1.3 零件分类成组的方法 221
7.1.4 成组工艺的设计方法 223
7.1.5 成组生产的组织形式 224
7.2 计算机辅助工艺设计 225
7.2.1 概述 225
7.2.2 CAPP的类型 226
7.2.3 CAPP的数据库 227
7.3 柔性制造系统 228
7.3.1 概述 228
7.3.2 柔性制造系统的组成 228
7.3.3 FMS中的机床设备和夹具 229
7.3.4 自动化仓库 230
7.3.5 物料运载装置 230
7.3.6 刀具管理系统 230
7.3.7 控制系统 230
7.4 计算机辅助制造和计算机集成制造系统 231
7.4.1 计算机辅助制造(CAM) 231
7.4.2 计算机集成制造系统(CIMS) 232
本章小结 234
思考题与习题 235
参考文献 236
- 《中国制造业绿色供应链发展研究报告》中国电子信息产业发展研究院 2019
- 《葡萄酒工艺与鉴赏 第3版》廖祖宋 2019
- 《高等教育双机械基础课程系列教材 高等学校教材 机械设计课程设计手册 第5版》吴宗泽,罗圣国,高志,李威 2018
- 《化学工程与工艺专业实验指导》郭跃萍主编 2019
- 《美物之道 日本手工艺》(日)柳宗悦著 2019
- 《智能制造高技能人才培养规划丛书 ABB工业机器人虚拟仿真教程》(中国)工控帮教研组 2019
- 《AutoCAD机械设计实例精解 2019中文版》北京兆迪科技有限公司编著 2019
- 《有色金属冶金新工艺与新技术》俞娟,王斌,方钊,崔雅茹,袁艳 2019
- 《洗涤剂生产工艺与技术》宋小平,韩长日主编 2019
- 《经济转型时期中国环境规制政策问题研究》冯卓著 2019
- 《大学计算机实验指导及习题解答》曹成志,宋长龙 2019
- 《指向核心素养 北京十一学校名师教学设计 英语 七年级 上 配人教版》周志英总主编 2019
- 《大学生心理健康与人生发展》王琳责任编辑;(中国)肖宇 2019
- 《大学英语四级考试全真试题 标准模拟 四级》汪开虎主编 2012
- 《大学英语教学的跨文化交际视角研究与创新发展》许丽云,刘枫,尚利明著 2020
- 《北京生态环境保护》《北京环境保护丛书》编委会编著 2018
- 《复旦大学新闻学院教授学术丛书 新闻实务随想录》刘海贵 2019
- 《大学英语综合教程 1》王佃春,骆敏主编 2015
- 《大学物理简明教程 下 第2版》施卫主编 2020
- 《指向核心素养 北京十一学校名师教学设计 英语 九年级 上 配人教版》周志英总主编 2019