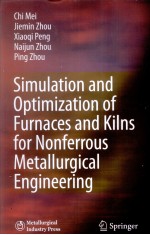
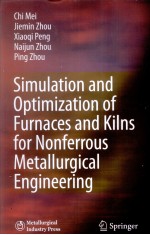
有色冶金炉窑仿真与优化 英文PDF电子书下载
- 电子书积分:12 积分如何计算积分?
- 作 者:梅炽等著
- 出 版 社:北京:冶金工业出版社
- 出版年份:2010
- ISBN:9787502446369;9783642002472
- 页数:340 页
1 Introduction 1
1.1 Classification of the Furnaces and Kilns for Nonferrous Metallurgical Engineering(FKNME) 1
1.2 The Thermophysical Processes and Thermal Systems of the FKNME 2
1.3 A Review of the Methodologies for Designs and Investigations of FKNME 4
1.3.1 Methodologies for design and investigation of FKNME 4
1.3.2 The characteristics of the MHSO method 5
1.4 Models and Modeling for the FKNME 7
1.4.1 Models for the modern FKNME 7
1.4.2 The modeling process 7
References 9
2 Modeling of the Thermophysical Processes in FKNME 11
2.1 Modeling of the Fluid Flow in the FKNME 11
2.1.1 Introduction 11
2.1.2 The Reynolds-averaging and the Favre-averaging methods 13
2.1.3 Turbulence models 15
2.1.4 Low Reynolds number k-ε models 21
2.1.5 Re-Normalization Group(RNG)k-εmodels 25
2.1.6 Reynolds stresses model(RSM) 26
2.2 The Modeling of the Heat Transfer in FKNME 27
2.2.1 Characteristics of heat transfer inside furnaces 27
2.2.2 Zone method 29
2.2.3 Monte Carlo method 33
2.2.4 Discrete transfer radiation model 35
2.3 The Simulation of Combustion and Concentration Field 38
2.3.1 Basic equations of fluid dynamics including chemical reactions 38
2.3.2 Gaseous combustion models 42
2.3.3 Droplet and particle combustion models 48
2.3.4 NOx models 54
2.4 Simulation of Magnetic Field 60
2.4.1 Physical models 60
2.4.2 Mathematical model of current field 61
2.4.3 Mathematical models of magnetic field in conductive elements 62
2.4.4 Magnetic field models of ferromagnetic elements 66
2.4.5 Three-dimensional mathematical model of magnetic field 69
2.5 Simulation on Melt Flow and Velocity Distribution in Smelting Furnaces 69
2.5.1 Mathematical model for the melt flow in smelting furnace 70
2.5.2 Electromagnetic flow 71
2.5.3 The melt motion resulting from jet-flow 75
References 80
3 Hologram Simulation of the FKNME 87
3 1 Concept and Characteristics of Hologram Simulation 87
3.2 Mathematical Models of Hologram Simulation 89
3.3 Applying Hologram Simulation to Multi-field Coupling 92
3.3.1 Classification of multi-field coupling 92
3.3.2 An example of intra-phase three-field coupling 93
3.3.3 An example of four-field coupling 94
3.4 Solutions of Hologram Simulation Models 97
References 98
4 Thermal Engineering Processes Simulation Based on Artificial Intelligence 101
4.1 Characteristics of Thermal Engineering Processes in Nonferrous Metallurgical Furnaces 101
4.2 Introduction to Artificial Intelligence Methods 102
4.2.1 Expert system 103
4.2.2 Fuzzy simulation 104
4.2.3 Artificial neural network 106
4.3 Modeling Based on Intelligent Fuzzy Analysis 107
4.3.1 Intelligent fuzzy self-adaptive modeling of multi-variable system 108
4.3.2 Example:fuzzy adaptive decision-making model for nickel matte smelting process in submerged arc furnace 111
4.4 Modeling Based on Fuzzy Neural Network Analysis 116
4.4.1 Fuzzy neural network adaptive modeling methods of multi-variable system 117
4.4.2 Example:fuzzy neural network adaptive decision-making model for production process in slag cleaning furnace 120
References 123
5 Hologram Simulation of Aluminum Reduction Cells 127
5.1 Introduction 127
5.2 Computation and Analysis of the Electric Field and Magnetic Field 131
5.2.1 Computation model of electric current in the bus bar 132
5.2.2 Computational model of electric current in the anode 133
5.2.3 Computation and analysis of electric field in the melt 134
5.2.4 Computation and analysis of electric field in the cathode 138
5.2.5 Computation and analysis of the magnetic field 140
5.3 Computation and Analysis of the Melt Flow Field 146
5.3.1 Electromagnetic force in the melt 147
5.3.2 Analysis of the molten aluminum movement 148
5.3.3 Analysis of the electrolyte movement 149
5.3.4 Computation of the melt velocity field 150
5.4 Analysis of Thermal Field in Aluminum Reduction Cells 152
5.4.1 Control equations and boundary conditions 153
5.4.2 Calculation methods 156
5.5 Dynamic Simulation for Aluminum Reduction Cells 158
5.5.1 Factors influencing operation conditions and principle of the dynamic simulation 159
5.5.2 Models and algorithm 160
5.5.3 Technical scheme of the dynamic simulation and function of the software system 161
5.6 Model of Current Efficiency of Aluminum Reduction Cells 163
5.6.1 Factors influencing current efficiency and its measurements 164
5.6.2 Models of the current efficiency 166
References 169
6 Simulation and Optimization of Electric Smelting Furnace 175
6.1 Introduction 175
6.2 Sintering Process Model of Self-baking Electrode in Electric Smelting Furnace 176
6.2.1 Electric and thermal analytical model of the electrode 178
6.2.2 Simulation software 182
6.2.3 Analysis of the computational result and the baking process 183
6.2.4 Optimization of self-baking electrode configuration and operation regime 190
6.3 Modeling of Bath Flow in Electric Smelting Furnace 192
6.3.1 Mathematical model for velocity field of bath 193
6.3.2 The forces acting on molten slag 194
6.3.3 Solution algorithms and characters 196
6.4 Heat Transfer in the Molten Pool and Temperature Field Model of the Electric Smelting Furnace 198
6.4.1 Mathematical model of the temperature field in the molten pool 199
6.4.2 Simulation software 203
6.4.3 Calculation results and verification 203
6.4.4 Evaluation and optimization of the furnace design and operation 208
References 210
7 Coupling Simulation of Four-field in Flame Furnace 213
7.1 Introduction 213
7.2 Simulation and Optimization of Combustion Chamber of Tower-Type Zinc Distillation Furnace 215
7.2.1 Physical model 216
7.2.2 Mathematical model 217
7.2.3 Boundary conditions 217
7.2.4 Simulation of the combustion chamber prior to structure optimization 218
7.2.5 Structure simulation and optimization of combustion chamber 220
7.3 Four-field Coupling Simulation and Intensification of Smelting in Reaction Shaft of Flash Furnace 221
7.3.1 Mechanism of flash smelting process—particle fluctuating collision model 223
7.3.2 Physical model 224
7.3.3 Mathematical model—coupling computation of particle and gas phases 225
7.3.4 Simulation results and discussion 227
7.3.5 Enhancement of smelting intensity in flash furnace 229
References 232
8 Modeling of Dilute and Dense Phase in Generalized Fluidization 235
8.1 Introduction 235
8.2 Particle Size Distribution Models 238
8.2.1 Normal distribution model 239
8.2.2 Logarithmic probability distribution model 240
8.2.3 Weibull probability distribution function 241
8.2.4 R-R distribution function(Rosin-Rammler distribution) 241
8.2.5 Nukiyawa-Tanasawa distribution function 242
8.3 Dilute Phase Models 244
8.3.1 Non-slip model 245
8.3.2 Small slip model 247
8.3.3 Multi-fluid model(or two-fluid model) 248
8.3.4 Particle group trajectory model 251
8.3.5 Solution of the particle group trajectory model 256
8.4 Mathematical Models for Dense Phase 257
8.4.1 Two-phase simple bubble model 258
8.4.2 Bubbling bed model 259
8.4.3 Bubble assemblage model(BAM) 261
8.4.4 Bubble assemblage model for gas-solid reactions 265
8.4.5 Solid reaction rate model in dense phase 267
References 272
9 Multiple Modeling of the Single-ended Radiant Tubes 275
9.1 Introduction 275
9.1.1 The SER tubes and the investigation of SER tubes 276
9.1.2 The overall modeling strategy 278
9.2 3D Cold State Simulation of the SER Tube 279
9.3 2D Modeling of the SER Tube 283
9.3.1 Selecting the turbulence model 283
9.3.2 Selecting the combustion model 286
9.3.3 Results and analysis of the 2D simulation 289
9.4 One-dimensional Modeling of the SER Tube 291
References 295
10 Multi-objective Systematic Optimization of FKNME 297
10.1 Introduction 297
10.1.1 A historic review 297
10.1.2 The three principles for the FKNME systematic optimization 298
10.2 Objectives of the FKNME Systematic Optimization 299
10.2.1 Unit output functions 300
10.2.2 Quality control functions 305
10.2.3 Control function of service lifetime 306
10.2.4 Functions of energy consumption 308
10.2.5 Control functions of air pollution emissions 309
10.3 The General Methods of the Multi-purpose Synthetic Optimization 309
10.3.1 Optimization methods of artificial intelligence 309
10.3.2 Consistent target approach 312
10.3.3 The main target approach 314
10.3.4 The coordination curve approach 315
10.3.5 The partition layer solving approach 315
10.3.6 Fuzzy optimization of the multi targets 316
10.4 Technical Carriers of Furnace Integral Optimization 318
10.4.1 Optimum design CAD 319
10.4.2 Intelligent decision support system for furnace operation optimization 320
10.4.3 Online optimization system 327
10.4.4 Integrated system for monitoring,control and management 330
References 334
Index 337
- 《数学物理方法与仿真 第3版》杨华军 2020
- 《通信电子电路原理及仿真设计》叶建芳 2019
- 《智能制造高技能人才培养规划丛书 ABB工业机器人虚拟仿真教程》(中国)工控帮教研组 2019
- 《铜提取冶金》(美)Mark E.Schlesinger 2017
- 《有色金属冶金新工艺与新技术》俞娟,王斌,方钊,崔雅茹,袁艳 2019
- 《微机原理与单片微机系统及应用 基于Proteus仿真》编者 2019
- 《仿真模型枪大全》日本HobbyJAPAN著 2014
- 《计算冶金学》赫冀成,雷洪,王强著 2019
- 《基于MATLAB的机器人轨迹优化与仿真》李辉著 2018
- 《轻型飞机起落架着陆动力学仿真与试验技术》聂宏,薛彩军编著 2019
- 《指向核心素养 北京十一学校名师教学设计 英语 七年级 上 配人教版》周志英总主编 2019
- 《北京生态环境保护》《北京环境保护丛书》编委会编著 2018
- 《指向核心素养 北京十一学校名师教学设计 英语 九年级 上 配人教版》周志英总主编 2019
- 《高等院校旅游专业系列教材 旅游企业岗位培训系列教材 新编北京导游英语》杨昆,鄢莉,谭明华 2019
- 《中国十大出版家》王震,贺越明著 1991
- 《近代民营出版机构的英语函授教育 以“商务、中华、开明”函授学校为个案 1915年-1946年版》丁伟 2017
- 《新工业时代 世界级工业家张毓强和他的“新石头记”》秦朔 2019
- 《智能制造高技能人才培养规划丛书 ABB工业机器人虚拟仿真教程》(中国)工控帮教研组 2019
- 《陶瓷工业节能减排技术丛书 陶瓷工业节能减排与污染综合治理》罗民华著 2017
- 《全国职业院校工业机器人技术专业规划教材 工业机器人现场编程》(中国)项万明 2019