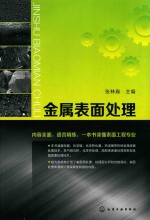
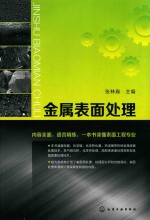
金属表面处理PDF电子书下载
- 电子书积分:12 积分如何计算积分?
- 作 者:张林森主编
- 出 版 社:北京:化学工业出版社
- 出版年份:2016
- ISBN:7122272546
- 页数:343 页
第1章 绪论 1
1.1 表面处理技术的含义 1
1.2 表面处理技术的分类和内容 2
1.2.1 表面处理技术的分类 2
1.2.2 表面处理技术的内容 3
1.3 表面处理技术的作用 6
1.4 表面处理技术的发展趋势 8
第2章 金属表面预处理 10
2.1 表面整平 10
2.1.1 机械磨光 10
2.1.2 抛光 12
2.1.3 滚光 15
2.1.4 刷光 16
2.1.5 喷砂处理 16
2.2 浸蚀 17
2.2.1 钢铁制品的酸洗 18
2.2.2 电化学浸蚀 20
2.3 表面除油 21
2.3.1 有机溶剂除油 21
2.3.2 碱性溶液化学除油 21
2.3.3 电化学除油 23
2.4 表面预处理新技术 25
2.4.1 超声波强化 25
2.4.2 低温高效清洗剂除油 26
第3章 金属电镀 27
3.1 电镀基本原理 27
3.1.1 电镀概念与电镀过程 27
3.1.2 对电镀层理化指标的要求 27
3.1.3 电镀设备与技术的发展 28
3.1.4 金属离子还原的可能性 28
3.1.5 电结晶过程的动力学 29
3.1.6 电沉积过程中金属离子还原时的极化 32
3.1.7 合金电沉积时的极化 35
3.1.8 添加剂对极化特性的影响 39
3.1.9 金属在阴极上的分布 42
3.1.10 电镀液的覆盖能力问题 45
3.2 电镀锌及锌合金 47
3.2.1 概述 47
3.2.2 氰化物镀锌 49
3.2.3 氯化钾型镀锌 51
3.2.4 碱性锌酸盐镀锌 54
3.2.5 硫酸盐镀锌 56
3.2.6 锌镀层的镀后处理 57
3.2.7 不合格锌镀层的退除 60
3.2.8 电镀锌合金 60
3.2.9 锌和锌合金基复合电镀 64
3.2.10 高速电镀锌 65
3.3 电镀铜及铜合金 67
3.3.1 概述 67
3.3.2 氰化物镀铜 68
3.3.3 硫酸盐镀铜 70
3.3.4 焦磷酸盐镀铜 73
3.3.5 其他类型的无氰镀铜工艺 75
3.3.6 铜镀层的后处理 76
3.3.7 不合格镀铜层的退除方法 77
3.3.8 电镀铜合金 78
3.4 电镀镍及镍合金 81
3.4.1 概述 81
3.4.2 普通镀镍(暗镍) 82
3.4.3 光亮镀镍 84
3.4.4 镀多层镍 87
3.4.5 特殊用途镀镍 91
3.4.6 不合格镍层的退除 92
3.4.7 电镀镍合金 93
3.4.8 粉末电镀镍 96
3.5 电镀铬 98
3.5.1 概述 98
3.5.2 镀铬的电极过程 100
3.5.3 镀铬层的结构与性能 102
3.5.4 镀铬电解液的成分及工艺条件 103
3.5.5 电镀铬工艺技术 106
3.5.6 稀土镀铬添加剂的应用 111
3.5.7 有机添加剂在镀铬中的应用 112
3.6 电镀锡 112
3.6.1 概述 112
3.6.2 硫酸盐镀锡 114
3.6.3 磺酸盐镀锡及钢板镀锡 118
3.6.4 碱性镀锡 121
3.6.5 镀层检验、缺陷分析及不合格镀层退除 125
第4章 非金属材料电镀及化学镀 127
4.1 概述 127
4.1.1 非金属材料电镀的历史及应用 127
4.1.2 非金属材料电镀的方法 128
4.1.3 ABS塑料电镀简介 128
4.2 非金属材料电镀前的表面准备 129
4.2.1 消除应力 129
4.2.2 除油 131
4.2.3 表面粗化 132
4.2.4 敏化 136
4.2.5 活化 137
4.2.6 还原或解胶 139
4.2.7 常见非金属材料的镀前处理方法 140
4.3 化学镀 141
4.3.1 化学镀铜 142
4.3.2 化学镀镍 145
4.3.3 化学镀锡 149
4.3.4 化学镀金 150
4.3.5 化学镀银 150
第5章 金属表面转化膜 153
5.1 阳极氧化膜 153
5.1.1 概述 153
5.1.2 阳极氧化膜的形成机理 155
5.1.3 阳极氧化工艺 158
5.1.4 阳极氧化膜的着色 166
5.1.5 阳极氧化膜的封闭 172
5.1.6 微弧阳极氧化 176
5.2 金属的磷化 180
5.2.1 概述 180
5.2.2 磷化成膜机理 181
5.2.3 磷化的工艺流程 182
5.3 钢铁氧化 187
5.3.1 钢铁高温氧化法 188
5.3.2 钢铁常温氧化法 189
5.4 电泳涂装 191
5.4.1 电泳涂装的定义和发展历史 191
5.4.2 电泳涂装的机理及特点 192
5.4.3 电泳涂装工艺 194
第6章 热浸镀 197
6.1 概述 197
6.2 热浸锌 198
6.2.1 热浸锌的用途 198
6.2.2 热浸镀锌层的形成过程 199
6.2.3 常用的热浸锌工艺 200
6.2.4 干法热浸锌工艺流程 201
6.2.5 热浸镀锌层形成过程中的“铁损” 203
6.2.6 热浸镀锌层的厚度控制 204
6.2.7 钢铁合金成分对热浸镀锌的影响 204
6.2.8 熔融锌液中的其他元素对热浸镀的影响 205
6.2.9 锌灰、锌渣与表面质量 205
6.3 热浸镀锡 206
6.4 热浸镀铝 207
第7章 气相沉积技术 208
7.1 概述 208
7.2 物理气相沉积 210
7.2.1 真空蒸镀 211
7.2.2 溅射镀膜 215
7.2.3 离子镀膜 219
7.2.4 物理气相沉积三种基本方法的比较 222
7.3 化学气相沉积 223
7.3.1 化学气相沉积的原理和装置 223
7.3.2 化学气相沉积的分类 224
7.3.3 化学气相沉积镀膜工艺及影响镀层的因素 225
7.3.4 化学气相沉积镀膜的特点和应用 225
7.3.5 化学气相沉积与物理气相沉积工艺对比 227
7.4 等离子体化学气相沉积法 228
7.4.1 等离子体化学气相沉积的种类 228
7.4.2 等离子体化学气相沉积过程和装置 229
7.4.3 等离子体化学气相沉积的特点和应用 229
第8章 化学热处理技术 232
8.1 概述 232
8.1.1 化学热处理的基本原理 233
8.1.2 化学热处理的分类 235
8.1.3 化学热处理的主要特点 236
8.1.4 化学热处理的意义 237
8.2 渗碳 237
8.2.1 渗碳过程原理 238
8.2.2 碳势及其控制 240
8.2.3 主要工艺参数对渗碳速度的影响 241
8.2.4 气体渗碳工艺 242
8.2.5 渗碳后的热处理 244
8.2.6 渗碳后组织和性能的关系 246
8.2.7 渗碳件常见缺陷及防止措施 247
8.3 渗氮 248
8.3.1 Fe-N相图及渗氮层相组成 248
8.3.2 渗氮用钢及其预备热处理 250
8.3.3 气体渗氮工艺 251
8.3.4 渗氮件的检验和常见缺陷 254
8.4 碳氮共渗与氮碳共渗 256
8.4.1 碳氮共渗 256
8.4.2 氮碳共渗 259
8.5 其他化学热处理 261
8.5.1 渗硼 262
8.5.2 渗硫 263
8.5.3 渗金属 264
8.5.4 离子化学热处理 265
8.5.5 复合热处理 265
第9章 高能束表面处理技术 266
9.1 概论 266
9.1.1 高能束表面处理的定义和特点 266
9.1.2 高能束表面处理的类型 266
9.2 激光束表面处理技术 267
9.2.1 激光束与材料表面的交互作用 267
9.2.2 激光束表面处理 269
9.2.3 激光硬化 270
9.2.4 激光表面合金化与熔覆 271
9.2.5 激光非晶化 273
9.3 电子束表面处理技术 275
9.3.1 电子束表面处理的原理 275
9.3.2 电子束加热和冷却 276
9.3.3 电子束表面处理 276
9.4 离子束表面处理技术 277
9.4.1 离子束表面处理原理 277
9.4.2 离子束表面处理设备 279
9.4.3 离子束表面处理技术的应用 280
第10章 处理层表面分析和性能测试 282
10.1 表面分析 282
10.1.1 概述 282
10.1.2 表面分析的分类 283
10.1.3 常用的表面分析仪器 287
10.2 覆盖层质量测试技术 293
10.2.1 覆盖层厚度的测定 293
10.2.2 镀层结合强度测试方法 299
10.2.3 镀层耐蚀性的测试方法 302
10.2.4 镀层孔隙率的测试方法 307
10.2.5 镀层的物理力学性能测试方法 308
第11章 表面处理车间 311
11.1 概述 311
11.1.1 表面处理车间的特点 311
11.1.2 表面处理车间设计内容 311
11.1.3 表面处理车间设计应注意的问题 312
11.2 工艺设计 312
11.2.1 生产纲领的制订 312
11.2.2 表面处理方法设计 313
11.2.3 工艺过程拟定 314
11.2.4 工艺过程表 315
11.3 设备的选择 315
11.3.1 主要设备的选用原则 315
11.3.2 电源设备 316
11.3.3 镀槽设计 319
11.3.4 自动生产线 322
11.3.5 其他设备 325
11.4 车间平面设计及土建 328
11.4.1 车间组成及面积 328
11.4.2 车间平面布局 328
11.4.3 对厂房建筑的要求 330
11.4.4 地面防腐蚀 330
11.4.5 车间通风及采暖 331
11.5 车间日常消耗计算 332
11.5.1 给水及排水 332
11.5.2 蒸汽消耗量计算 335
11.5.3 压缩空气消耗计算 336
11.6 车间日常管理 337
11.6.1 表面处理工艺文件的编制与实施 337
11.6.2 表面处理现场生产的组织形式 337
11.6.3 严格生产中的质量管理 338
11.6.4 表面处理现场应用技术 338
参考文献 343
- 《大数据Hadoop 3.X分布式处理实战》吴章勇,杨强 2020
- 《边缘处守望》山尹著 2019
- 《有色金属冶金新工艺与新技术》俞娟,王斌,方钊,崔雅茹,袁艳 2019
- 《烧结法处理非常规含铁资源研究》王哲著 2018
- 《无机元素原子光谱分析样品预处理技术》吴瑶庆 2019
- 《农村生活污水处理工艺与技术应用》李灵娜著 2019
- 《中国人民大学研究报告系列 中国水处理行业可持续发展战略研究报告 膜工业卷 3》(中国)郑祥,魏源送,王志伟 2019
- 《工业废水处理工艺与设计》高永编著 2019
- 《工业水处理技术》(中国)赵文玉,林华,许立巍 2019
- 《污水处理PPP项目实施方案编制实务》王雁然,方俊,朱立冬 2019