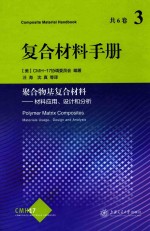
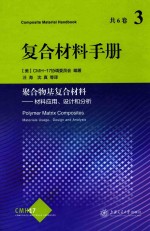
复合材料手册 3 聚合物基复合材料 材料应用、设计和分析PDF电子书下载
- 电子书积分:22 积分如何计算积分?
- 作 者:美国CMH-17协调委员会编著;汪海,沈真等译
- 出 版 社:上海:上海交通大学出版社
- 出版年份:2015
- ISBN:9787313122056
- 页数:848 页
第1章 总论 1
1.1 手册介绍 1
1.2 手册内容概述 1
1.3 第3卷的目的和范围 3
1.4 材料取向编码 3
1.4.1 层压板取向编码 3
1.4.1.1 铺层顺序记号 3
1.4.1.2 铺层百分比记号 4
1.4.2 编织物取向编码 5
1.5 符号、缩写及单位制 5
1.5.1 符号及缩写 6
1.5.1.1 组分的性能 11
1.5.1.2 单层与层压板 12
1.5.1.3 下标 13
1.5.1.4 上标 14
1.5.1.5 缩写词 15
1.5.2 单位制 18
1.6 定义 19
参考文献 42
第2章 复合材料结构研制概述 43
2.1 引言 43
2.1.1 为什么复合材料是不同的 43
2.1.2 不同的研制方法 44
2.1.3 本章的局限性 45
2.2 复合材料的力学行为 45
2.2.1 材料术语和坐标系 45
2.2.2 材料级力学性能 46
2.2.3 铺层顺序问题 47
2.2.4 环境影响 49
2.2.5 损伤的影响 50
2.2.6 变异性问题 51
2.2.7 设计用力学性能 52
2.3 材料的选择 53
2.3.1 结构材料 53
2.3.1.1 纤维类型 53
2.3.1.2 复合材料的形式 54
2.3.1.3 树脂类型 54
2.3.1.4 纤维形式 55
2.3.1.5 胶黏剂类型 56
2.3.1.6 夹层材料类型 57
2.3.2 附属材料 57
2.3.3 材料选择考虑的因素 59
2.4 制造工艺的选择 61
2.4.1 工艺步骤和方法 61
2.4.2 模具成形方法 65
2.4.3 质量保证过程 66
2.4.4 工艺选择的考虑因素 68
2.5 结构概念 69
2.5.1 基本结构类型 69
2.5.2 连接类型 70
2.5.3 零件的装配 72
2.5.4 整体化的大型复合材料结构 73
2.5.5 装配成完整的结构 74
2.6 缺陷和损伤问题 75
2.6.1 一般缺陷和损伤的考虑 76
2.6.2 缺陷和损伤来源 76
2.6.2.1 制造来源 76
2.6.2.2 使用损伤来源 77
2.6.3 缺陷和损伤特性 77
2.6.4 使用中缺陷和损伤的检测 78
2.6.5 设计和开发过程中缺陷和损伤的处理 79
2.6.5.1 总体设计和研发的考虑 79
2.6.5.2 具体的设计思路和方法 80
2.6.5.3 飞机检查程序的制定:冲击评估 81
2.7 寿命的考虑 82
2.7.1 环境退化 82
2.7.2 维护问题 82
2.7.3 与“任务谱”变化有关的问题 82
2.7.4 环境管理 83
2.8 发展规划纲要 83
参考文献 84
第3章 飞机结构取证和符合性 86
3.1 引言 86
3.1.1 概述(背景) 86
3.1.2 目的和范围 87
3.2 认证考虑 87
3.2.1 产品研发(初始适航) 87
3.2.2 持续适航 88
3.2.3 产品改型(变更的产品) 89
3.2.4 具有资质的工作人员和团队 90
3.3 规章 91
3.3.1 结构、设计和构型 91
3.3.2 产品批准 94
3.3.3 持续适航(维护) 95
3.4 设计验证 96
3.4.1 设计和工艺文件 96
3.4.2 材料/胶黏剂鉴定 97
3.4.3 环境暴露和液体相容性 98
3.4.4 结构胶接 99
3.4.5 模具和零件固化 100
3.4.6 生产中出现的缺陷 101
3.4.7 结构一致性工艺 101
3.4.8 结构验证(静强度和损伤容限) 102
3.4.9 颤振验证(气动弹性稳定性) 106
3.4.10 防火,阻燃和热问题 106
3.4.11 闪电防护 107
3.4.12 耐坠损性 108
3.5 生产——必需的 109
3.5.1 生产实施 109
3.5.2 制造质量控制 110
3.5.3 缺陷处理和制造记录 114
3.5.4 生产过程变更 114
3.6 维护——技术问题 115
3.6.1 修理设计和工艺验证 115
3.6.2 团队合作和处置 116
3.6.3 损伤检出和表征 118
3.6.4 修理工艺(螺接和胶接) 120
3.7 指南和报告 121
3.7.1 咨询通报 121
3.7.2 政策声明 124
3.7.3 技术报告 124
第4章 复合材料结构的积木式方法 126
4.1 引言与原理 126
4.2 基本原理与假设 130
4.2.1 降低风险 131
4.3 方法 131
4.3.1 失效模式 132
4.3.2 分析 133
4.3.3 材料评定与许用值(试样级) 134
4.3.4 设计细节许用值(元件试验级) 134
4.3.5 关键结构的预生产保证(组合件试验级) 134
4.3.6 全尺寸结构验证——部件级试验 135
4.3.6.1 全尺寸静力试验 135
4.3.6.2 全尺寸飞机的耐久性和损伤容限试验 136
4.4 具体应用考虑 136
4.4.1 飞机原型 136
4.4.1.1 对DoD/NASA原型飞机结构生成的聚合物基复合材料许用值 136
4.4.1.2 DoD/NASA原型飞机的PMC复合材料积木式结构研发 139
4.4.1.3 DoD/NASA原型复合材料飞机结构的许用值和积木式试验任务小结 143
4.4.2 工程制造发展(EMD)飞机和生产型飞机 144
4.4.2.1 DoD/NASA工程制造发展型和生产型飞机结构PMC复合材料许用值的生成 144
4.4.2.2 DOD/NASA工程制造发展型EMD和生产型飞机的PMC复合材料积木式结构研发 146
4.4.2.3 DoD/NASA工程制造发展型EMD和生产型复合材料飞机结构许用值和积木式试验任务小结 152
4.4.3 商用飞机 152
4.4.3.1 引言 152
4.4.3.2 积木式方法 153
4.4.3.3 复合材料路线图 155
4.4.3.4 商用的积木式方法 156
4.4.3.5 A组,材料性能的确定 157
4.4.3.6 B组,确定设计值 158
4.4.3.7 C组,分析验证 161
4.4.3.8 波音777飞机复合材料主结构的积木式方法 161
4.4.4 公务飞机和私人飞机 168
4.4.4.1 高性能飞机 168
4.4.4.2 轻型飞机和微型机 172
4.4.5 旋翼飞机 172
4.4.5.1 设计许用值试验 174
4.4.5.2 设计研发试验 176
4.4.5.3 全尺寸验证试验 178
4.4.6 运载火箭和宇宙飞船 181
4.5 特定工艺和材料形式的特殊考虑和变化 183
4.5.1 室温 183
参考文献 183
第5章 材料和工艺——变异性对复合材料性能的影响 185
5.1 引言 185
5.2 目的 186
5.3 范围 186
5.4 组分材料 187
5.4.1 纤维 187
5.4.1.1 碳和石墨纤维 187
5.4.1.2 芳纶 189
5.4.1.3 玻璃 192
5.4.1.4 硼 198
5.4.1.5 氧化铝 199
5.4.1.6 碳化硅 200
5.4.1.7 石英 202
5.4.1.8 超高分子量聚乙烯 205
5.4.2 树脂 208
5.4.2.1 概述 208
5.4.2.2 环氧 208
5.4.2.3 聚酯(热固性) 208
5.4.2.4 酚醛 209
5.4.2.5 双马来酰亚胺 209
5.4.2.6 聚酰亚胺 210
5.4.2.7 热塑性材料 211
5.4.2.8 特种与新型树脂体系 214
5.5 产品成形工艺 215
5.5.1 织物和预成形件 215
5.5.1.1 机织物 215
5.5.2 预浸渍的形式 217
5.5.2.1 预浸无捻粗纱 217
5.5.2.2 预浸带 217
5.5.2.3 预浸织物和预成形件 218
5.5.2.4 预压实热塑性塑料片材 219
5.5.3 定义生产使用时材料的“批料”或“批次”的详细指南 219
5.6 装运和贮存过程 221
5.6.1 包装 221
5.6.2 运输 221
5.6.3 打开包装与贮存 221
5.7 制造工艺 221
5.7.1 手工铺贴 221
5.7.2 自动铺带/单向带自动铺叠 223
5.7.2.1 背景 223
5.7.2.2 效益/能力 223
5.7.2.3 变异性来源 224
5.7.3 自动铺丝/纤维铺放 224
5.7.3.1 背景 224
5.7.3.2 纤维铺放工艺流程 225
5.7.3.3 效益/能力 226
5.7.3.4 材料产品形式 226
5.7.3.5 专门考虑的问题 228
5.7.4 编织 230
5.7.5 纤维缠绕 231
5.7.6 拉挤 232
5.7.7 夹层结构 232
5.7.8 胶黏剂胶接 233
5.7.9 预结合水分 234
5.7.10 胶接质量 235
5.8 固化和压实工艺 239
5.8.1 真空袋成形 239
5.8.2 固化炉固化 239
5.8.3 热压罐固化工艺 240
5.8.3.1 一般说明 240
5.8.3.2 变异性来源 240
5.8.4 模压成形 241
5.8.5 整体加热模具 241
5.8.6 拉挤型模固化和压实 241
5.8.7 树脂传递模塑(RTM) 242
5.8.8 热成形 245
5.9 装配工艺 246
5.10 工艺过程控制 246
5.10.1 通用工艺过程控制方案 246
5.10.1.1 经验方法 247
5.10.1.2 基于传感器的主动控制 247
5.10.1.3 基于模型的被动控制 247
5.10.2 实例——热固性复合材料的热压罐固化 247
5.10.2.1 固化度 248
5.10.2.2 黏度 249
5.10.2.3 树脂压力 249
5.10.2.4 空隙预防措施 250
5.10.2.5 流动 250
5.11 制订材料与工艺规范 251
5.11.1 规范的类型 251
5.11.1.1 材料规范 251
5.11.1.2 工艺规范——控制终端产品 251
5.11.2 规范的格式 251
5.11.2.1 范围 251
5.11.2.2 适用文件 251
5.11.2.3 技术要求/工艺过程控制 252
5.11.2.4 验收检验和鉴定试验 252
5.11.2.5 交付 252
5.11.2.6 说明 252
5.11.2.7 批准的来源及其他 252
5.11.3 规范示例 252
5.11.3.1 行业规范 253
5.11.3.2 军用规范 253
5.11.4 结构管理 253
5.12 确定复合材料鉴定时的变异源 253
5.12.1 引言 253
5.12.1.1 除批次外来自其他来源的复合材料性能变异性 255
5.12.1.2 常规鉴定方法和许用值计算 256
5.12.2 嵌套式鉴定方法的发展和应用 257
5.12.2.1 研发背景 257
5.12.2.2 碳纤维/环氧树脂鉴定方法 262
5.12.2.3 数据审查 264
5.12.2.4 数据分析 268
5.12.2.5 嵌套式实验进展的回顾和结论 271
5.12.3 用回归法进行嵌套式鉴定数据许用值计算实例 272
5.12.4 供应商C制造供应商A材料的鉴定 275
5.12.4.1 引言 275
5.12.4.2 鉴定计划 276
5.12.4.3 工艺批的热压罐固化程序 280
5.12.4.4 工艺和试验批进度 280
5.12.4.5 供应商C S2 G/Ep材料的变异源 290
5.12.4.6 总结 292
5.12.5 使用嵌套式方法的设计许用值 293
5.12.6 嵌套式鉴定成本问题 294
5.12.7 总结 302
参考文献 303
第6章 生产用材料与工艺的质量控制 307
6.1 引言 307
6.2 材料采购质量保证程序 307
6.2.1 规范和文件 307
6.2.2 供应商阶段的材料控制 308
6.2.2.1 工艺过程控制文件(PCD) 308
6.2.2.2 统计过程控制(SPC) 308
6.2.2.3 交付试验 309
6.2.3 用户阶段的材料控制 310
6.2.3.1 批次验收/来料检验 310
6.2.3.2 贮存期和外置时间控制 311
6.3 零件制造检验 311
6.3.1 工艺过程检验 311
6.3.2 无损检测(NDI) 312
6.3.3 破坏性试验(DT) 313
6.3.3.1 背景 313
6.3.3.2 用途 313
6.3.3.3 破坏性试验方法 314
6.3.3.4 实施指南 314
6.3.3.5 试验类型 315
6.4 材料和工艺过程变化的处理 316
6.4.1 引言 316
6.4.2 新材料或工艺过程的鉴定 316
6.4.2.1 问题说明 316
6.4.2.2 业务情况 316
6.4.2.3 差异与风险 316
6.4.2.4 技术上的可接受性 318
6.4.2.5 许用值的建立和等同性确认 318
6.4.2.6 生产准备状态 318
6.4.2.7 经验教训 318
6.4.3 差异和风险 319
6.4.3.1 差异 319
6.4.3.2 风险评估 321
6.4.3.3 风险分析 322
6.4.4 生产准备状态 322
6.5 改进工艺的统计工具 323
6.5.1 工艺反馈调整 324
6.5.2 实验设计 326
6.5.3 Taguchi 332
参考文献 332
第7章 复合材料设计 333
7.1 与复合材料设计相关的特有问题 333
7.2 设计过程 334
7.3 材料和工艺的选择 334
7.3.1 材料的选择 335
7.3.2 制造工艺的选择 336
7.3.3 质量控制 336
7.3.4 可生产性 336
7.3.5 模具 336
7.3.6 环境的影响 336
7.4 结构概念 336
7.4.1 层压板、夹层结构和加筋结构 336
7.4.2 铺层选择 336
7.4.3 剪裁特性 336
7.5 零件详细设计 337
7.5.1 弹性特性 338
7.5.2 层压板设计考虑 338
7.5.3 热相容性/低热膨胀系数(CTE) 339
7.5.4 复合材料/金属界面 339
7.5.5 保障设计 339
7.5.6 连接设计 339
7.5.6.1 机械紧固件连接 339
7.5.6.2 胶接连接 340
7.5.7 损伤阻抗/损伤容限 342
7.5.8 耐久性 342
7.5.9 雷击 342
7.6 优化 342
7.7 经验教训 342
参考文献 355
第8章 层压板分析 357
8.1 引言 357
8.2 单层的基本性能和细观力学 357
8.2.1 假设 358
8.2.1.1 材料的均质性假设 358
8.2.1.2 材料的正交各向异性假设 358
8.2.1.3 材料的线性假设 358
8.2.1.4 残余应力 358
8.2.2 纤维(增强)复合材料:应力-应变性能 358
8.2.2.1 弹性性能 358
8.2.2.2 黏弹性性能 358
8.2.3 纤维(增强)复合材料:物理性能 359
8.2.3.1 热膨胀和湿膨(泡)胀 359
8.2.3.2 热传导和湿扩散 360
8.2.4 厚板复合材料三维单层性能 360
8.3 层压板刚度分析 360
8.3.1 层压板理论 360
8.3.2 层压板的性能 361
8.3.2.1 薄膜应力 361
8.3.2.2 弯曲 363
8.3.2.3 热膨胀 366
8.3.2.4 湿膨胀 367
8.3.2.5 传导 367
8.3.3 模量值在分析中的应用 367
8.3.4 湿热分析 368
8.3.4.1 对称层压板 369
8.3.4.2 非对称层压板 369
8.3.5 厚板复合材料三维单层性能 370
8.4 层压板面内应力分析 370
8.4.1 机械载荷引起的应力 370
8.4.2 由温度和湿度引起的应力 371
8.4.3 网格分析 373
8.4.4 非线性应力分析 375
8.5 一般层压板强度估算 376
8.5.1 单层强度和失效模式 376
8.5.1.1 轴向拉伸强度 377
8.5.1.2 轴向压缩强度 379
8.5.1.3 基体模式的强度 381
8.5.2 层压板级失效模式 383
8.5.2.1 拉伸 383
8.5.2.2 压缩 384
8.5.2.3 基体裂纹 385
8.5.3 单向带横向拉伸性能的影响 386
8.5.4 铺层顺序对强度的影响 386
8.5.5 由单层强度到层压板强度 387
8.6 层压板面内强度估算 388
8.6.1 从单层到层压板的分析方法 390
8.6.1.1 初始层失效 390
8.6.1.2 后续失效 394
8.6.2 纤维失效分析方法(层压板级失效) 394
8.6.2.1 最大应变理论用于玻璃纤维复合材料 394
8.6.2.2 缩减最大应变理论用于碳纤维复合材料 395
8.6.2.3 用最大应变理论估算强度 397
8.6.3 应力集中处层压板强度估算 398
8.7 层内与层间应力及失效分析 401
8.7.1 面外载荷 401
8.7.2 层间应力 401
8.7.2.1 边缘效应 402
8.7.2.2 层厚突变 403
8.7.2.3 弯曲层压板中的层间应力 403
8.7.3 分层 403
8.7.3.1 压缩 405
8.7.4 应变能释放率断裂力学计算 406
8.7.4.1 引言 406
8.7.4.2 确定应变能释放率的主要步骤 408
8.7.4.3 计算G 411
8.7.4.4 模式混合的确定 415
8.7.4.5 二维和三维的实际应用 416
参考文献 417
第9章 结构稳定性分析 426
9.1 引言 426
9.2 压缩屈曲和压损 426
9.2.1 平板的屈曲 426
9.2.1.1 引言 426
9.2.1.2 初始屈曲 427
9.2.1.3 单轴载荷——所有边简支的长平板 427
9.2.1.4 单轴载荷——所有边固支的长平板 429
9.2.1.5 单轴载荷——三边简支、一非受载边自由的长平板 429
9.2.1.6 单轴和双轴载荷——所有边简支的平板 429
9.2.1.7 单轴载荷——加载边简支、非加载边固支的平板 430
9.2.1.8 铺层顺序对屈曲的影响 430
9.2.2 压缩后屈曲和压损 433
9.2.2.1 分析模型 436
9.2.2.2 压损曲线的确定 438
9.2.2.3 筋条压损强度的确定 439
9.2.2.4 转角半径和填充料的影响 441
9.2.2.5 细长比修正 441
9.2.2.6 疲劳影响 442
9.2.3 小结 442
9.3 剪切屈曲 442
9.4 加筋壁板的稳定性 442
参考文献 442
第10章 连接的结构特性 444
10.1 背景 444
10.2 引言 445
10.3 胶接连接设计 446
10.3.1 被胶接件厚度的影响:被胶接件破坏与胶接破坏的关系 446
10.3.2 连接几何形状的影响 447
10.3.3 被胶接件刚度不匹配的影响 448
10.3.4 胶黏剂韧性响应的影响 448
10.3.5 复合材料被胶接件的性能 450
10.3.6 胶接缺陷的影响 451
10.4 胶接连接的应力分析 452
10.4.1 胶黏剂的一般应力 452
10.4.1.1 胶黏剂剪应力 453
10.4.1.2 剥离应力 457
10.4.2 等厚度被胶接件的单搭接和双搭接 459
10.4.2.1 胶层在弹性响应范围内的连接特性 459
10.4.2.2 热应力影响 467
10.4.2.3 塑性对连接应力的影响 469
10.4.2.4 复合材料被胶接件横向剪切和铺层顺序的影响 472
10.4.3 斜削和多阶梯被胶接件 473
10.4.4 T连接 482
10.4.5 有限元建模 482
10.4.5.1 重要性和挑战 482
10.4.5.2 应力分析例子 483
10.4.5.3 结论摘要 485
10.5 胶接连接的断裂分析 485
10.6 胶接连接耐久性 486
参考文献 488
第11章 螺栓连接设计和分析 492
11.1 背景 492
11.2 引言 493
11.3 螺栓连接分析 493
11.3.1 连接中的载荷分配 493
11.3.2 螺栓连接局部破坏分析 496
11.3.3 失效准则 501
11.4 螺栓连接设计 502
11.4.1 几何形状 502
11.4.2 铺贴和铺层顺序 502
11.4.3 紧固件选择 502
11.5 螺栓连接疲劳 503
11.5.1 载荷模式的影响 504
11.5.2 连接几何形状的影响 504
11.5.3 接头接触细节的影响 505
11.5.4 层压板铺层比例的影响 505
11.5.5 环境的影响 505
11.5.6 试件厚度的影响 505
11.5.7 剩余强度 506
11.6 试验验证 506
参考文献 507
第12章 损伤阻抗、耐久性和损伤容限 510
12.1 概述 510
12.1.1 原理 511
12.1.2 复合材料相关条款 512
12.1.3 飞机损伤容限 512
12.1.4 通用指南 514
12.2 飞机条例、要求和符合性 515
12.2.1 民航条例和指南 516
12.2.1.1 含损伤结构静强度 517
12.2.1.2 损伤容限和疲劳 518
12.2.2 损伤类型 523
12.2.2.1 第一类损伤 523
12.2.2.2 第二类损伤 524
12.2.2.3 第三类损伤 524
12.2.2.4 第四类损伤 524
12.2.2.5 第五类损伤 524
12.2.2.6 影响损伤分类的因素 525
12.2.3 载荷和损伤的关系 525
12.2.4 符合性方法 528
12.2.4.1 确定性符合性方法 529
12.2.4.2 概率或半概率符合性方法 533
12.3 设计的发展和验证 537
12.3.1 损伤设计准则 537
12.3.1.1 第一类损伤 537
12.3.1.2 第二类损伤 538
12.3.1.3 第三类损伤 539
12.3.1.4 第四类损伤 539
12.3.1.5 未定义事件造成的大型损伤 539
12.3.2 验证 539
12.3.2.1 第一类损伤 540
12.3.2.2 第二类损伤 540
12.3.2.3 第三类损伤 541
12.3.2.4 第四类损伤 541
12.3.2.5 全尺寸试验 541
12.3.3 第五类损伤的处理 545
12.3.4 附加的设计研发指南 547
12.4 缺陷和损伤检测 547
12.4.1 飞机服役期检测程序 548
12.4.2 损伤检测数据的研发 549
12.4.3 检测计划研发 550
12.4.4 环境退化和意外损伤评级系统 551
12.4.5 机群领先飞机计划 552
12.4.6 检出概率研究 552
12.5 损伤阻抗 552
12.5.1 影响因素 553
12.5.1.1 对以前冲击研究结果的概述 553
12.5.1.2 穿透冲击 555
12.5.1.3 高速冲击 557
12.5.1.4 材料类型和形式的影响 557
12.5.1.5 损伤的深度 558
12.5.1.6 层压板厚度的影响 559
12.5.1.7 结构尺寸影响 561
12.5.1.8 夹芯结构 563
12.5.2 设计问题和指南 565
12.5.2.1 用对冲击的研究来确定关键损伤 566
12.5.2.2 结构布置和设计细节 566
12.5.2.3 机械冲击 567
12.5.2.4 鸟撞 567
12.5.2.5 地面冰雹 567
12.5.2.6 飞行冰雹 569
12.5.2.7 雷击 570
12.5.2.8 操作和踩踏载荷 570
12.5.2.9 外露的边缘 572
12.5.2.10 液体渗入 572
12.5.2.11 过热 572
12.5.2.12 老化 572
12.5.2.13 化学污染 572
12.5.2.14 修理拆卸 572
12.5.3 试验问题 572
12.5.4 分析方法 572
12.6 耐久性和循环载荷下的损伤扩展 572
12.6.1 影响因素 572
12.6.1.1 循环应力比R和谱效应 573
12.6.1.2 环境 573
12.6.2 设计问题和指南 573
12.6.2.1 设计细节 573
12.6.2.2 损伤容限的若干考虑 574
12.6.3 试验问题 574
12.6.3.1 复合材料的分散性分析 575
12.6.3.2 寿命因子方法 579
12.6.3.3 利用分散性分析的载荷放大因子 581
12.6.3.4 极限强度方法 586
12.6.3.5 谱的截除和截取 587
12.6.3.6 试验环境 589
12.6.3.7 损伤扩展 589
12.6.4 分析方法 590
12.6.4.1 耐久性和损伤起始分析 590
12.6.4.2 损伤扩展分析 597
12.6.4.3 累积寿命预测 600
12.7 剩余强度 601
12.7.1 影响因子 601
12.7.1.1 损伤阻抗与剩余强度的关系 601
12.7.1.2 带冲击损伤的结构 601
12.7.1.3 带有穿透损伤的结构 610
12.7.2 设计内容和指南 620
12.7.2.1 铺层顺序 620
12.7.2.2 夹层结构 620
12.7.3 试验内容 620
12.7.3.1 试样冲击试验 621
12.7.3.2 加筋板冲击试验 621
12.7.3.3 夹层板冲击试验 621
12.7.3.4 加筋板大型穿透损伤试验 621
12.7.3.5 夹层板大型穿透损伤试验 621
12.7.4 分析方法 621
12.7.4.1 大尺寸穿透损伤 621
12.7.4.2 单一分层和脱胶 628
12.7.4.3 冲击损伤 632
12.7.4.4 切口和凹槽 636
12.8 应用/实例 637
12.8.1 旋翼机 637
12.8.1.1 损伤 637
12.8.1.2 环境 637
12.8.1.3 与关键失效模式有关的试验加载条件 637
12.8.1.4 试验载荷——载荷放大因子(LEF) 638
12.8.1.5 谱截除 638
12.8.1.6 剩余强度试验 638
12.8.2 商用飞机(波音777尾翼扭力盒段) 639
12.8.2.1 耐久性-环境 639
12.8.2.2 耐久性-机械载荷 639
12.8.2.3 损伤 640
12.8.2.4 损伤容限-“无扩展”试验 640
12.8.2.5 损伤容限-剩余强度 641
12.8.2.6 检测计划 642
12.8.3 通用航空(Raytheon星舟号) 642
12.8.3.1 引言 642
12.8.3.2 损伤容限评估 643
12.8.3.3 使用经历 648
12.8.3.4 结论 649
12.9 支持性说明 650
12.9.1 符合性 650
12.9.1.1 飞机实际可能遇到的冲击能量威胁 650
12.9.2 损伤阻抗 652
12.9.2.1 编制冰雹威胁分布 652
12.9.3 耐久性和损伤扩展 653
12.9.3.1 耐久性和损伤起始实例研究 653
12.9.3.2 损伤扩展实例研究 656
12.9.4 剩余强度 658
12.9.4.1 无构型缺口强度封闭预测方法的比较 658
12.9.4.2 为确定Mar-Lin参数Hc和n的NASA/Boeing ATCAS方法 661
12.9.4.3 利用构型因子预测结构损伤容限的实例 662
12.9.4.4 与实施应变-软化相关的问题 665
12.9.4.5 应变-软化在缺口压缩中的应用 668
12.9.4.6 R曲线实例 669
参考文献 671
第13章 缺陷、损伤和检测 686
13.1 缺陷和损伤 686
13.1.1 缺陷和损伤的起源 686
13.1.1.1 制造和修理 686
13.1.1.2 使用 687
13.1.2 损伤类型 688
13.1.2.1 基体瑕疵 688
13.1.2.2 分层和脱胶 689
13.1.2.3 纤维断裂 689
13.1.2.4 裂纹 690
13.1.2.5 刻痕、划伤和坑槽 690
13.1.2.6 凹痕 690
13.1.2.7 贯穿 690
13.1.2.8 受损伤紧固件孔 690
13.1.2.9 磨蚀 690
13.1.2.10 热损伤 690
13.1.2.11 雷击损伤 691
13.1.2.12 组合损伤 691
13.1.2.13 由液体侵入夹层壁板造成的损伤 691
13.2 检测方法 691
13.2.1 无损检测 691
13.2.1.1 目视检测 691
13.2.1.2 敲击试验/兰姆波 692
13.2.1.3 超声检测 692
13.2.1.4 X射线照相 694
13.2.1.5 剪切成像法 695
13.2.1.6 热成像法 696
13.2.1.7 湿度计 697
13.2.1.8 胶接试验器 697
13.2.1.9 涡流法 697
13.2.2 破坏检测 697
13.2.3 实例 698
13.2.3.1 目测检查 698
13.2.3.2 超声波检测 699
13.2.3.3 X射线照相 701
13.2.3.4 剪切成像 703
13.2.3.5 热成像 704
13.2.3.6 有损检测(横截面) 707
参考文献 709
第14章 可支持性、维护与修理 710
14.1 引言 710
14.2 重要考虑事项 711
14.3 使用经验 712
14.4 检测 715
14.5 损伤评定 717
14.5.1 评定人员的授权 717
14.5.2 评定人员的资格 717
14.5.3 损伤评定的信息 717
14.5.4 对修理场所的考虑 718
14.6 修理设计和证实 719
14.6.1 修理设计准则 719
14.6.1.1 构件的刚度 720
14.6.1.2 静强度和稳定性 720
14.6.1.3 耐久性 721
14.6.1.4 损伤容限 722
14.6.1.5 相关的飞机系统 722
14.6.1.6 空气动力光顺性 722
14.6.1.7 重量与平衡 723
14.6.1.8 工作温度 723
14.6.1.9 环境 723
14.6.1.10 周围的结构 724
14.6.1.11 临时修理 724
14.6.2 证实要求 725
14.7 复合材料结构的修理 727
14.7.1 引言 727
14.7.2 损伤清理和修理部位的准备 728
14.7.3 螺栓连接修理 728
14.7.3.1 概念 728
14.7.3.2 材料 729
14.7.3.3 分析 730
14.7.3.4 修理程序 730
14.7.3.5 螺栓连接修理举例 731
14.7.4 胶接修理 732
14.7.4.1 概念 732
14.7.4.2 材料 733
14.7.4.3 分析 734
14.7.4.4 修理程序 755
14.7.4.5 胶接修理举例 758
14.7.5 夹层结构(蜂窝芯)修理 758
14.7.5.1 修理概念 759
14.7.5.2 芯子的修复 759
14.7.5.3 修理程序 760
14.7.5.4 夹层结构修理举例 761
14.7.6 修理质量保证 761
14.7.6.1 过程中的质量控制 761
14.7.6.2 修理后的检测 762
14.8 金属结构的复合材料修理(CRMS) 763
14.9 维护文件 764
14.9.1 确定允许的损伤限 764
14.9.2 修理限制 765
14.10 考虑可支持性的设计 766
14.10.1 前言 766
14.10.2 可检性 767
14.10.2.1 一般设计考虑 767
14.10.2.2 检测的可达性 768
14.10.3 材料选择 768
14.10.3.1 引言 768
14.10.3.2 树脂和纤维 768
14.10.3.3 产品的形式 770
14.10.3.4 胶黏剂 770
14.10.3.5 可支持性问题 771
14.10.3.6 环境的有关问题 771
14.10.4 损伤阻抗、损伤容限和耐久性 772
14.10.4.1 损伤阻抗 772
14.10.4.2 损伤容限 773
14.10.4.3 耐久性 773
14.10.5 环境适应性 773
14.10.5.1 取消/减少重金属 774
14.10.5.2 关于除漆要求的考虑 774
14.10.5.3 修理材料的存储期和存储稳定性 774
14.10.5.4 清洁要求 774
14.10.5.5 无损检测要求 775
14.10.5.6 寿命结束时的废弃考虑 775
14.10.6 可靠性和可维护性 775
14.10.7 互换性和可更换性 775
14.10.8 可接近性 776
14.10.9 可修理性 776
14.10.9.1 一般设计方法 777
14.10.9.2 修理设计问题 779
14.10.9.3 编织、机织或缝纫结构的修理 780
14.11 后勤要求 780
14.11.1 培训 780
14.11.2 备件 782
14.11.3 材料 782
14.11.4 设施 783
14.11.5 技术数据 784
14.11.6 支持设备 785
14.11.6.1 固化设备 785
14.11.6.2 冷藏室 786
14.11.6.3 打磨/抛光棚 786
14.11.6.4 NDI设备 786
参考文献 787
第15章 厚截面复合材料 790
15.1 引言和厚截面的定义 790
15.2 厚截面复合材料3D分析要求的力学性能 791
15.2.1 复合材料2D分析 792
15.2.2 复合材料3D分析 792
15.2.2.1 单向层3D性能 793
15.2.2.2 多向正交各向异性层压板的3D性能 793
15.2.3 理论性能确定 794
15.2.3.1 3D单层性能确定 794
15.2.3.2 3D层压板性能确定 796
15.2.4 试件设计考虑 800
15.3 厚截面复合材料结构分析方法 800
15.4 厚截面复合材料3D分析所要求的物理性能分析 800
15.5 厚截面复合材料的工艺分析方法 800
15.6 失效准则 800
15.7 影响厚截面许用值(即安全裕度)的因素 800
15.8 厚板的验证问题 800
参考文献 800
第16章 坠毁适航及能量管理 802
16.1 概论和一般指导原则 802
16.1.1 每节内容的组织 802
16.1.2 坠毁适航的原则 802
16.1.3 与复合材料相关的问题 803
16.1.4 专门名词 805
16.1.5 目前的研究和发展 806
16.1.6 规范车体和安全标准的回顾 808
参考文献 809
第17章 结构安全管理 812
17.1 简介 812
17.1.1 背景 812
17.1.2 目标及范围 814
17.2 安全风险管理概述 814
17.2.1 定义 814
17.2.2 安全风险管理过程 814
17.2.3 危险识别和初始安全评估 815
17.2.4 风险分析和策略 815
17.2.5 风险评估和缓解措施 815
17.3 结构安全和规章 816
17.3.1 资料来源 816
17.3.2 规章 816
17.3.3 指导文件 817
17.4 结构安全评估考虑 817
17.4.1 设计 818
17.4.2 制造 818
17.4.3 维护 818
17.4.4 操作 819
17.4.5 适航要求 819
17.4.6 结构完整性 819
17.4.6.1 寿命周期考虑 820
17.4.7 实例说明 821
17.4.7.1 261航班 821
17.5 结构安全管理过程 822
17.5.1 结构描述 822
17.5.2 不安全状态和损伤威胁的识别 822
17.5.3 风险分析 822
17.5.4 风险评估 823
17.5.5 风险缓解 823
17.6 结构安全管理的应用 825
17.6.1 应用:对被修理部件而言,很少依赖OEM所带来的问题 825
17.6.2 应用:涉及金属胶接的不符合规范的超常修理 825
17.6.3 应用:有关复合材料不符合规范的超常修理 827
参考文献 829
第18章 环境管理 831
18.1 引言 831
18.1.1 范围 831
18.1.2 再循环的专门术语 831
18.2 再循环的基础结构 834
18.2.1 再循环基础结构开发模型 834
18.2.2 基础结构需求 835
18.2.3 再循环教育 835
18.3 复合材料再循环经济学 835
18.4 复合材料废料物流 836
18.4.1 工艺废料 837
18.4.2 已用过的复合材料废料 837
18.5 减少复合材料废料物流的来源 838
18.5.1 恰好及时和刚好够用的材料投放 838
18.5.2 电子商务数据管理 839
18.5.3 废料最小化指南 839
18.5.3.1 预浸料 839
18.5.3.2 树脂 839
18.5.3.3 纤维 839
18.5.3.4 固化剂 839
18.5.3.5 热压罐材料 839
18.5.3.6 包装材料 839
18.5.4 轻重量 839
18.6 复合材料零部件和材料的再利用 840
18.6.1 复合材料零部件的再利用 840
18.6.2 加工成较小的零部件 840
18.7 材料交换 840
18.7.1 初级材料的再分配 840
18.7.2 复合材料交换服务机构 840
18.7.2.1 未用过材料的管理 841
18.7.2.2 包装 841
18.7.2.3 管理文件编制 841
18.7.2.4 未用过材料说明书 841
18.7.2.5 DOD(国防部)再出售限制 841
18.8 复合材料再循环 841
18.8.1 可拆卸和可再循环的设计 841
18.8.1.1 紧固件 842
18.8.1.2 胶黏剂 842
18.8.1.3 混杂复合材料 842
18.8.2 再循环后勤 842
18.8.2.1 收集和运输 842
18.8.2.2 纤维和基体的识别 843
18.8.3 复合材料再循环工艺流程 843
18.8.3.1 尺寸减小 843
18.8.3.2 基体的除去 844
18.8.3.3 纤维的再利用 844
18.8.3.4 除去基体的产品 845
18.8.3.5 其他再循环和工艺方法 845
18.8.4 废预浸料的再循环 845
参考文献 846
- 《材料导论》张会主编 2019
- 《材料力学 上》杨在林,杨丽红主编 2011
- 《NiFe2O4基惰性阳极材料的烧结行为及应用性能》杜金晶,王斌著 2019
- 《食品接触材料中成分迁移特性及实践》张双灵著 2018
- 《化学化工材料与新能源》张军丽著 2018
- 《材料力学 第2版》严圣平,马占国 2018
- 《纳米颗粒复合电刷镀技术及应用》董世运著 2019
- 《材料成形技术基础》周志明,涂坚,盛旭敏主编 2019
- 《高分子材料》刘瑞雪,高丽君,马丽主编 2018
- 《材料科学与工程基础》赵长生,顾宜主编 2019