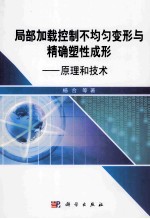
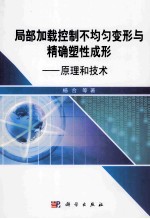
局部加载控制不均匀变形与精确塑性成形:原理和技术PDF电子书下载
- 电子书积分:18 积分如何计算积分?
- 作 者:杨合等著
- 出 版 社:北京:科学出版社
- 出版年份:2014
- ISBN:9787030428707
- 页数:644 页
第1章 绪论 1
1.1 塑性成形的特点及影响因素 1
1.1.1 塑性成形的特点及作用 1
1.1.2 塑性成形的复杂性及主要影响因素 3
1.2 先进塑性成形的发展趋势与学科前沿 5
1.3 精确塑性成形面临的挑战与解决思路 10
1.3.1 面临的三大主要挑战 10
1.3.2 局部加载控制不均匀变形与精确塑性成形成性一体化方法 12
参考文献 13
第2章 精确塑性成形成性一体化研究方法的基础 15
2.1 引言 15
2.2 塑性有限元建模关键技术 16
2.2.1 塑性有限元模拟技术概述 16
2.2.2 塑性有限元模拟技术研究的热点、难点及发展趋势 17
2.2.3 塑性成形过程有限元建模关键技术 21
2.3 晶体塑性理论 24
2.3.1 晶体塑性理论概述 24
2.3.2 变形梯度的乘法分解 25
2.3.3 晶体变形的几何学、运动学和动力学 26
2.3.4 弹性本构关系 29
2.3.5 率相关滑移模型和硬化模型 29
2.4 内变量法 31
2.4.1 内变量法概述 31
2.4.2 微观组织演变内变量建模方法 31
2.4.3 基于位错密度的内变量模型 33
2.4.4 内变量模型参数的确定 34
2.5 元胞自动机原理 34
2.5.1 元胞自动机法的定义与特征 34
2.5.2 元胞自动机法的分类 36
2.5.3 元胞自动机法的构成 37
2.6 失稳起皱的能量法预测原理与方法 38
2.6.1 薄壁件成形中的失稳起皱现象及复杂性 38
2.6.2 失稳起皱预测原理与方法概述 42
2.7 韧性断裂准则 48
2.7.1 材料的韧性断裂 48
2.7.2 常见的韧性断裂准则 51
参考文献 54
第3章 精确塑性成形全过程多尺度仿真建模 58
3.1 引言 58
3.2 全过程宏观有限元建模 59
3.2.1 不均匀变形和组织一体化预测建模 59
3.2.2 多场耦合复杂加载成形-卸载回弹全过程预测建模 81
3.2.3 多约束柔性控制有限元建模 88
3.3 细观晶体塑性建模 98
3.3.1 基于剪应变的晶体塑性模型与高精度稳定算法 98
3.3.2 耦合再结晶的晶体塑性模型 117
3.4 微观组织形态演化元胞机建模 131
3.4.1 钛合金静态粗化元胞自动机模型 131
3.4.2 不连续动态再结晶模型 148
3.4.3 连续动态再结晶模型 169
3.5 失稳起皱精确预测模型 185
3.5.1 管轴压成形失稳起皱预测模型 185
3.5.2 薄壁管数控弯曲起皱解析-有限元预测模型 187
3.5.3 大口径薄壁管弯曲起皱引入微缺陷的解析-有限元高精度预测模型 192
3.5.4 不均匀压下面内弯曲成形失稳模式引入微缺陷的预测模型 203
3.6 韧性断裂精确预测模型 210
3.6.1 韧性断裂准则的适用性判据 210
3.6.2 韧性断裂模型参数表征 214
3.6.3 韧性断裂模型数值化实现 218
3.6.4 韧性断裂模型的验证和应用 225
参考文献 229
第4章 局部加载不均匀压下板带面内弯曲精确成形原理与技术 235
4.1 引言 235
4.2 成形原理 236
4.2.1 成形过程描述 236
4.2.2 应力和应变特征 237
4.2.3 局部不均匀加载的几何条件 238
4.2.4 变形协调方程 240
4.3 板带的宽展效应 241
4.3.1 宽展的特征 241
4.3.2 宽展对应力应变分布的影响 246
4.3.3 宽展对面内弯曲半径的影响 248
4.3.4 影响宽展的因素及影响规律 252
4.3.5 考虑宽展效应的弯曲半径的快速预测 253
4.4 轧辊机构弹性挠动对成形的影响 264
4.4.1 考虑轧辊机构弹性挠动的成形条件 264
4.4.2 考虑轧辊机构弹性挠动的弯曲半径预测 266
4.5 板带面内弯曲成形的精确控制 276
4.5.1 弯曲半径精确控制模型的建立 276
4.5.2 模型影响参数的可控性研究 278
4.5.3 弯曲半径精确控制方法及应用 280
参考文献 286
第5章 管轴压无模约束精确成形原理与技术 288
5.1 引言 288
5.2 管轴压无模约束精确成形原理 288
5.2.1 管轴压无模约束成形基本原理 288
5.2.2 无模约束不均匀变形对管轴压精确成形的作用机制 291
5.2.3 无模约束变形模式转换条件 296
5.3 管轴压精确成形过程失稳预测与控制 301
5.3.1 管轴压成形失稳开裂 301
5.3.2 管轴压成形失稳起皱 303
5.4 管轴压精确成形过程优化与控制 308
5.4.1 成形可行性分析及稳定成形参数范围确定 308
5.4.2 管轴压精确成形过程优化与控制 311
参考文献 315
第6章 钛合金复杂大件等温局部加载成形原理与技术 318
6.1 引言 318
6.2 钛合金复杂大件等温局部加载成形原理 319
6.2.1 钛合金复杂大件等温局部加载成形基本原理 319
6.2.2 钛合金复杂大件等温局部加载成形面临的挑战 319
6.3 不均匀变形机理与宏观缺陷控制 320
6.3.1 局部加载不均匀变形机理 320
6.3.2 局部加载型腔充填理论解析 325
6.3.3 宏观成形缺陷预测与控制 335
6.4 全过程组织演变机制与主动调控 340
6.4.1 钛合金等温局部加载多道次变形微观组织演变机制 340
6.4.2 不均匀变形对不同加载区和过渡区组织和性能的影响机制 351
6.4.3 钛合金等温局部加载三态组织形成条件 364
6.5 钛合金复杂大件等温局部加载成形过程优化控制 375
6.5.1 大型复杂构件不等厚坯料优化设计 375
6.5.2 等温局部加载全过程工艺参数优化与控制 387
6.5.3 大型组合模具优化设计与运动控制 397
参考文献 405
第7章 难变形管材数控弯曲精确成形技术 408
7.1 引言 408
7.2 数控弯曲成形原理及难变形管材弯曲性能 409
7.2.1 数控弯曲成形原理 409
7.2.2 难变形管材弯曲性能 410
7.3 拉压区不均匀变形特征与成形缺陷影响因素 421
7.3.1 数控弯曲拉压区不均匀变形特征 421
7.3.2 数控弯曲成形缺陷特征及其影响因素 424
7.4 成形极限预测与提高技术 433
7.4.1 多缺陷约束成形极限预测方法 433
7.4.2 成形极限提高技术 436
7.5 卸载回弹预测和控制技术 466
7.5.1 回弹预测方法 466
7.5.2 回弹控制技术 471
7.6 工模具设计制造与调模技术 482
7.6.1 数控弯曲工模具选材 482
7.6.2 模具设计及调试知识准则 486
7.6.3 薄壁管材小弯曲半径弯曲的模具结构设计方法 490
7.6.4 薄壁钛管数控热弯成形模具设计方法 494
7.6.5 基于KBE/FE的数控弯管模具设计与成形性评估系统 496
7.7 成形过程优化与控制技术 499
7.7.1 多目标多参数多约束优化数学模型 499
7.7.2 基于不同要求的薄壁管数控弯曲参数优化设计方法 505
7.7.3 初始模具和工艺参数确定方法 507
7.7.4 大直径薄壁管数控弯曲优化设计方法 508
参考文献 523
第8章 大型薄壁异形件复合旋压精确成形技术 526
8.1 引言 526
8.2 不均匀变形特征与关键控制因素 527
8.2.1 带环向内筋结构旋压不均匀变形特征 527
8.2.2 薄壁曲面结构旋压不均匀变形特征 538
8.2.3 不均匀变形行为的关键控制因素 542
8.3 坯料优化设计 543
8.3.1 带环向内筋结构预成形坯料优化设计 544
8.3.2 初始圆板坯尺寸的确定 551
8.4 加载轨迹设计 552
8.4.1 总体设计 552
8.4.2 板坯上开始充筋半径的确定 553
8.4.3 第一次贴模旋压头部成形高度确定 554
8.4.4 不同道次旋压加载轨迹的确定 554
8.5 低成本短周期高精度旋压技术 556
8.5.1 成形参数优化 556
8.5.2 带环向内筋复杂构件的芯模设计与脱模方法 585
8.5.3 单芯模多道次复合旋压新方法 591
参考文献 593
第9章 难变形材料环件辗轧成形技术 596
9.1 引言 596
9.2 坯料尺寸设计 597
9.2.1 坯料尺寸设计方法 598
9.2.2 毛坯尺寸设计流程与应用 604
9.3 稳定成形条件设计方法 607
9.3.1 稳定成形条件数学建模 607
9.3.2 稳定成形条件设计方法的应用 612
9.4 三种不均匀变形行为 614
9.4.1 环件辗轧过程不均匀变形的决定性因素 615
9.4.2 三种不均匀变形行为及其作用 616
9.5 钛合金环件辗轧宏观成形与组织演变规律 622
9.5.1 TA15环件径轴向辗轧全过程组织演变规律 622
9.5.2 TC4钛合金锥形环辗轧宏观成形与组织演变规律 626
9.5.3 TC4钛合金复杂异形环件辗轧填充规律 639
参考文献 643
- 《乌鸦哥哥变形记 可能情况个数》(韩)崔玉仁文 2016
- 《材料成形技术基础》周志明,涂坚,盛旭敏主编 2019
- 《变形记》(奥地利)弗兰兹·卡夫卡 2019
- 《强变形微纳米化工艺》骆俊延,贾建波,徐岩 2019
- 《局部解剖学 第9版 人卫版》崔慧先,李瑞锡著 2018
- 《熊表哥变形记》李牧雨文;何美麒绘 2018
- 《高分子材料成形工艺学》应宗荣编著 2019
- 《脆塑性岩石类材料破坏后区力学特性研究》史贵才编;朱珉责编 2019
- 《中国抗日战争史 第1卷 局部抗战》黄道玄,王希亮著;步平,王建朗主编 2019
- 《局部解剖学习题集》肖宛凝责任编辑;张雅芳 2019
- 《指向核心素养 北京十一学校名师教学设计 英语 七年级 上 配人教版》周志英总主编 2019
- 《《走近科学》精选丛书 中国UFO悬案调查》郭之文 2019
- 《北京生态环境保护》《北京环境保护丛书》编委会编著 2018
- 《中医骨伤科学》赵文海,张俐,温建民著 2017
- 《美国小学分级阅读 二级D 地球科学&物质科学》本书编委会 2016
- 《指向核心素养 北京十一学校名师教学设计 英语 九年级 上 配人教版》周志英总主编 2019
- 《强磁场下的基础科学问题》中国科学院编 2020
- 《小牛顿科学故事馆 进化论的故事》小牛顿科学教育公司编辑团队 2018
- 《小牛顿科学故事馆 医学的故事》小牛顿科学教育公司编辑团队 2018
- 《高等院校旅游专业系列教材 旅游企业岗位培训系列教材 新编北京导游英语》杨昆,鄢莉,谭明华 2019