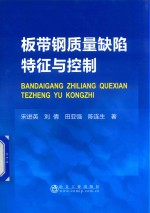
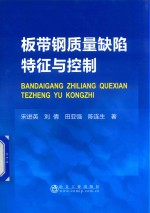
板带钢质量缺陷特征与控制PDF电子书下载
- 电子书积分:10 积分如何计算积分?
- 作 者:宋进英,刘倩,田亚强等著
- 出 版 社:北京:冶金工业出版社
- 出版年份:2017
- ISBN:9787502470340
- 页数:209 页
1 绪论 1
2 检测手段及分析原理 3
2.1 超声波清洗器 3
2.1.1 超声波设备概述 3
2.1.2 超声波清洗设备构成 4
2.1.3 超声波清洗机的主要参数 4
2.1.4 超声波清洗特点 5
2.1.5 超声波清洗中应注意的几个问题 6
2.2 光学显微镜 7
2.2.1 普通光学显微镜 8
2.2.2 显微镜的使用方法 12
2.2.3 使用显微镜应注意的事项 13
2.2.4 显微镜的保养与维护 13
2.3 扫描电子显微镜 14
2.3.1 扫描电镜的基本结构和原理 14
2.3.2 扫描电镜样品要求与制备 17
2.3.3 扫描电子显微镜的操作 19
2.4 X射线能谱分析 28
2.4.1 实验原理 28
2.4.2 试样的制备 30
2.4.3 实验参数的选择 31
2.4.4 实验步骤 32
2.4.5 应用实例 34
3 边裂缺陷 38
3.1 试验材料及方法 40
3.2 由夹杂引起的边裂 40
3.2.1 夹杂物的类型 40
3.2.2 钢中夹杂物的来源及成因 41
3.2.3 典型实例检测及原因分析 42
3.2.4 整改措施 44
3.3 由聚集气泡引起的边裂 44
3.3.1 典型实例检测及原因分析 44
3.3.2 气泡来源及形成机理 45
3.3.3 整改措施 46
3.4 因横向冷却的不均而引起的边裂 47
3.4.1 典型实例检测 47
3.4.2 原因分析 47
3.4.3 整改措施 48
3.5 由钢板边部脱碳严重而引起的边裂 48
3.5.1 典型实例检测 48
3.5.2 原因分析 50
3.5.3 整改措施 51
3.6 由轧制工序引起的边裂 51
3.6.1 冷轧板带生产概述 51
3.6.2 冷轧工序引起边裂缺陷的典型实例检测及分析 53
3.6.3 冷轧工序引起边裂缺陷的整改措施 55
3.6.4 热轧板带生产概述 55
3.6.5 热轧工序引起边裂缺陷的典型事例及分析 56
3.6.6 热轧工序引起边裂缺陷的整改措施 58
3.7 铸坯本身存在较多的角横裂引起的边裂 58
3.7.1 铸坯角横裂形成机理 58
3.7.2 典型实例检测 60
3.7.3 角横裂引起的边裂缺陷形成机理 62
3.7.4 整改措施 63
4 起皮缺陷 64
4.1 试验材料及方法 65
4.2 由夹杂物聚集引起的起皮 66
4.2.1 典型实例检测 66
4.2.2 原因分析 67
4.2.3 整改措施 67
4.3 由氧化通道引起的起皮 67
4.3.1 典型实例检测及分析 67
4.3.2 整改措施 69
4.4 由皮下气泡引起的起皮 69
4.4.1 皮下气泡来源 69
4.4.2 外来气泡行为特征 70
4.4.3 典型实例检测及原因分析 70
4.4.4 整改措施 71
4.5 由氧化铁皮压入引起的起皮 72
4.5.1 典型实例检测 72
4.5.2 氧化铁皮压入的原因 73
4.5.3 整改措施 74
5 结疤缺陷 75
5.1 试验材料及方法 75
5.2 铸坯切割时返渣积瘤压入所致的结疤 76
5.2.1 典型实例检测 76
5.2.2 原因分析 78
5.2.3 整改措施 79
5.3 转炉碱性渣所致的结疤 79
5.3.1 终期转炉钢渣成分控制 79
5.3.2 典型实例检测 81
5.3.3 原因分析 82
5.3.4 整改措施 82
5.4 缩孔引起结疤 83
5.4.1 缩孔(松)简介 83
5.4.2 典型实例检测及原因分析 84
5.4.3 整改措施 85
5.5 精炼渣引起结疤 86
5.5.1 精炼渣分类及特点 86
5.5.2 精炼渣的主要成分与作用 87
5.5.3 典型实例检测及原因分析 88
5.5.4 整改措施 89
5.6 轧制工艺引起结疤 89
5.6.1 典型实例检测 89
5.6.2 原因分析 91
5.6.3 整改措施 91
6 氧化铁皮压入缺陷 92
6.1 氧化铁皮产生来源 92
6.2 氧化铁皮的类型及形成机理 92
6.3 实验材料及方法 94
6.4 一次氧化铁皮的形貌及产生原因分析 94
6.4.1 典型实例检测 94
6.4.2 原因分析 96
6.4.3 整改措施 96
6.5 二次氧化铁皮的缺陷形貌及产生原因分析 97
6.5.1 典型实例检测 97
6.5.2 原因分析 98
6.5.3 整改措施 99
6.6 三次氧化铁皮的缺陷形貌及产生原因分析 99
6.6.1 典型实例检测 99
6.6.2 原因分析 100
6.6.3 整改措施 101
6.7 红色氧化铁皮缺陷形貌及产生原因分析 101
6.7.1 典型实例检测 101
6.7.2 原因分析 102
6.7.3 整改措施 103
7 孔洞缺陷 104
7.1 试验材料及方法 104
7.2 孔洞缺陷类型及研究现状 104
7.3 夹杂引起的孔洞缺陷 106
7.3.1 夹杂物影响钢板质量的作用机理 107
7.3.2 夹杂物的数量、尺寸及分布对轴承钢质量的影响 107
7.3.3 含Ti元素夹杂引起的孔洞缺陷 108
7.3.4 复合夹杂引起的孔洞缺陷 111
7.3.5 Al2O3夹杂引起的孔洞缺陷 112
7.3.6 夹杂引起孔洞缺陷的整改措施 114
7.4 异物压入引起的孔洞缺陷 114
7.4.1 异物压入引起的“坑状”孔洞缺陷 115
7.4.2 异物压入引起的“疤状”孔洞缺陷 115
7.4.3 异物压入引起孔洞缺陷的整改措施 116
7.5 轧辊异常引起的孔洞缺陷 117
7.5.1 轧辊异常现象 117
7.5.2 典型实例检测及原因分析 117
7.5.3 整改措施 118
8 线状缺陷 119
8.1 试验材料及方法 120
8.2 气泡引起的线状缺陷 120
8.2.1 典型实例检测 120
8.2.2 原因分析 121
8.2.3 整改措施 121
8.3 划伤引起的线状缺陷 121
8.3.1 热轧划伤在冷轧过程中引起的线状缺陷 121
8.3.2 冷擦伤引起的线状缺陷 123
8.4 夹杂引起的线状缺陷 125
8.4.1 典型实例检测 125
8.4.2 原因分析 126
8.4.3 整改措施 126
8.5 氧化铁皮压入引起的线状缺陷 127
8.5.1 典型实例检测及原因分析 127
8.5.2 整改措施 128
9 分层缺陷 129
9.1 试验材料及方法 129
9.2 钢板分层缺陷及形成原因 129
9.2.1 连铸坯的初始缺陷 130
9.2.2 夹杂物的影响 132
9.3 带状组织引起的分层缺陷 133
9.3.1 典型实例检测 133
9.3.2 原因分析 133
9.3.3 整改措施 133
9.4 保护渣引起的分层缺陷 134
9.4.1 典型实例检测 134
9.4.2 原因分析 135
9.4.3 整改措施 135
9.5 硫化物引起的分层缺陷 135
9.5.1 典型实例检测 135
9.5.2 原因分析 136
9.5.3 整改措施 136
9.6 异常组织引起的分层缺陷 136
9.6.1 典型实例检测 136
9.6.2 原因分析 137
9.6.3 整改措施 138
9.7 折叠引起的分层缺陷 138
9.7.1 折叠缺陷的定义 138
9.7.2 折叠缺陷形式 138
9.7.3 典型实例检测及原因分析 140
9.7.4 整改措施 141
10 焊管冷弯开裂缺陷 142
10.1 试验材料及方法 142
10.2 焊管简介 142
10.2.1 无缝焊管原始材料的生产 142
10.2.2 直缝埋弧焊接钢管 143
10.2.3 螺旋焊管 144
10.3 非金属夹杂引起的焊管冷弯开裂缺陷 145
10.3.1 非金属夹杂概述 145
10.3.2 非金属夹杂的评定 145
10.3.3 硅酸盐类夹杂引起的焊管冷弯开裂缺陷 146
10.3.4 硫化物引起的焊管冷弯开裂缺陷 147
10.4 锆系耐材脱落引起的焊管冷弯开裂缺陷 149
10.4.1 铝碳-锆碳复合浸入式水口 149
10.4.2 铝碳-锆碳复合浸入式水口损毁机理 150
10.4.3 二氧化锆的物理性质 150
10.4.4 二氧化锆的晶型稳定 151
10.4.5 典型实例检测及原因分析 152
10.4.6 整改措施 153
10.5 加工硬化程度过高引起的焊管冷弯开裂缺陷 153
10.5.1 加工硬化及加工硬化曲线 153
10.5.2 加工硬化机理 155
10.5.3 典型实例检测及原因分析 159
11 冷轧镀锌板典型缺陷 161
1 1.1 试验材料及方法 161
11.2 表面漏镀缺陷 162
11.2.1 典型实例检测 162
11.2.2 原因分析 163
11.2.3 整改措施 163
11.3 黑点缺陷 163
11.3.1 典型实例检测 163
11.3.2 原因分析 164
11.3.3 整改措施 165
11.4 线状缺陷 165
11.4.1 典型实例检测 165
11.4.2 原因分析 166
11.4.3 整改措施 166
11.5 孔洞缺陷 166
11.5.1 典型实例检测 166
1 1.5.2 原因分析 167
11.5.3 整改措施 167
12 40Mn链片断裂 168
12.1 试验材料及方法 168
12.2 非金属夹杂物引起的链片断裂 169
12.2.1 典型实例检测及原因分析 169
12.2.2 整改措施 170
12.3 带状组织引起的链片断裂 171
12.3.1 典型实例检测及原因分析 171
12.3.2 整改措施 172
12.4 C、Mn元素含量偏低引起的链片断裂 173
12.4.1 典型实例检测及原因分析 173
12.4.2 整改措施 173
12.5 淬火加热时表面脱碳引起的链片断裂 173
12.5.1 典型实例检测及原因分析 174
12.5.2 整改措施 174
12.6 淬火冷却速度不足引起的链片断裂 174
12.6.1 典型实例检测及原因分析 174
12.6.2 整改措施 175
13 硫化物夹杂及成分偏析对610L钢冷弯开裂的影响 176
13.1 试验材料及方法 176
13.2 钢中硫化物 177
13.2.1 钢中硫化物的分类 177
13.2.2 钢中硫化物的形成原因 178
13.3 偏析缺陷 179
13.3.1 偏析缺陷的概念 179
13.3.2 偏析缺陷的分类及形成原因 179
13.4 610L钢组织中的成分偏析 180
13.4.1 典型实例检测及原因分析 180
13.4.2 610L钢成分偏析的整改措施 181
13.5 610L钢断口硫化物分析 182
13.5.1 典型实例检测及原因分析 182
13.5.2 针对硫化物夹杂的整改措施 183
13.6 结论 184
14 冶金锯片用65Mn钢球化退火后矫直断裂 185
14.1 试验材料与方法 185
14.2 脆断形貌与组织 186
14.3 脆断断口及产生机理 187
14.4 热轧板粗大渗碳体片层产生机理 189
14.5 偏析原因与改进措施 191
14.6 结论 192
15 冶金锯片用65Mn热轧窄带钢硬度不均 193
15.1 试验材料及方法 193
15.2 化学成分不均对硬度的影响 194
15.3 珠光体片层间距对硬度的影响 195
15.4 带状组织对硬度的影响 196
15.5 脱碳层对硬度的影响 197
15.6 结论 198
16 冶金锯片用65Mn钢珠光体组织与性能的窄范围控制 199
16.1 试验材料及方法 199
16.2 终轧温度对组织和力学性能影响 200
16.3 终轧后冷速对组织和力学性能影响 201
16.4 卷取后冷速对组织和力学性能影响 203
16.5 结论 204
参考文献 205
- 《影响葡萄和葡萄酒中酚类特征的因素分析》朱磊 2019
- 《高含硫气藏开发腐蚀控制技术与实践》唐永帆,张强 2018
- 《钢铁行业污染特征与全过程控制技术研究》周长波等 2019
- 《带钢连续热镀锌》李九岭著 2019
- 《生活垃圾焚烧飞灰中典型污染物控制技术》朱芬芬等编著 2019
- 《海河干流水环境质量与经济发展模式研究》于航白景峰,张春意 2019
- 《钢铁烧结烟气多污染物过程控制原理与新技术》甘敏,范晓慧著 2019
- 《汉语韵律的多维特征及其认知功能》吴洁敏,朱宏达著 2019
- 《真菌毒素控制集成解决方案 第二届MycoKey国际真菌毒素大会论文集》冯洁 2018
- 《医疗机构内新型冠状病毒感染预防与控制相关流程》河南省卫生健康委员会编写 2020
- 《指向核心素养 北京十一学校名师教学设计 英语 七年级 上 配人教版》周志英总主编 2019
- 《北京生态环境保护》《北京环境保护丛书》编委会编著 2018
- 《指向核心素养 北京十一学校名师教学设计 英语 九年级 上 配人教版》周志英总主编 2019
- 《高等院校旅游专业系列教材 旅游企业岗位培训系列教材 新编北京导游英语》杨昆,鄢莉,谭明华 2019
- 《中国十大出版家》王震,贺越明著 1991
- 《近代民营出版机构的英语函授教育 以“商务、中华、开明”函授学校为个案 1915年-1946年版》丁伟 2017
- 《新工业时代 世界级工业家张毓强和他的“新石头记”》秦朔 2019
- 《智能制造高技能人才培养规划丛书 ABB工业机器人虚拟仿真教程》(中国)工控帮教研组 2019
- 《陶瓷工业节能减排技术丛书 陶瓷工业节能减排与污染综合治理》罗民华著 2017
- 《全国职业院校工业机器人技术专业规划教材 工业机器人现场编程》(中国)项万明 2019