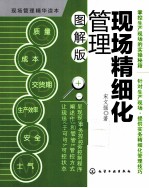
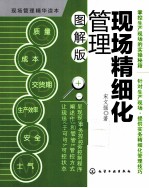
现场精细化管理 图解版PDF电子书下载
- 电子书积分:10 积分如何计算积分?
- 作 者:宋文强著
- 出 版 社:北京:化学工业出版社
- 出版年份:2011
- ISBN:9787122105448
- 页数:220 页
1 现场管理精细化,向细节要效益 1
1.1 四个故事引发的思考:细节决定成败 2
1.2 现场管理:五大要素与六大目标 6
1.3 对现场进行精细化管理,精益求精 8
1.4 现场精细化管理的基本流程:PDCA循环 10
1.5 八大利器提升现场精细化管理水平 15
2 利器一:5S,夯实现场精细化管理的基础 17
2.1 5S活动,让生产现场更精细 18
2.2 整理:物品数量最优化,简化现场管理对象 19
2.3 整顿:物品放置合理化,创造整洁有序的现场 23
2.4 清扫:现场清扫标准化,改善环境与设备 30
2.5 清洁:5S活动制度化,维持巩固现场改善成果 34
2.6 素养:5S管理习惯化,形成良好企业文化 38
2.7 案例:来鑫公司5S样板区推进计划 44
3 利器二:可视化,打造一目了然的精细化现场 49
3.1 地面划线:规范化的放置与定位 51
3.2 标识牌:一目了然的小看板 53
3.3 安全可视化:醒目刺激的警示与提醒 56
3.4 颜色:直观高效的辨识方法 59
3.5 形迹管理:物品放置的精确定位 61
3.6 办公可视化:提高行政业务效率 62
3.7 案例:南海公司可视化规范与推进计划 64
4 利器三:TPM全员设备维护,实现设备“零故障” 69
4.1 TPM:全员参与设备的维护保养 70
4.2 TPM的核心:操作员工自主进行设备维护 72
4.3 第一步:设备清扫训练,进一步了解设备 74
4.4 第二步:制订清扫规范,推进设备清扫活动 75
4.5 第三步:改善污染发生源和清扫困难部位 77
4.6 第四步:开展OPL活动,进行总点检训练 80
4.7 第五步:制订设备点检规范,开展设备自主维护 85
4.8 第六步:点检与维护的可视化、效率化 89
4.9 第七步:全员参与现场改善,自主维护常态化 91
4.10 案例:海尔如何推进全员参与TPM活动 95
5 利器四:防错法,实现产品质量“零缺陷” 99
5.1 质量管理的核心:预防出现产品质量问题 100
5.2 防错法:提前预防质量问题的有效手段 102
5.3 自动检测:防错法的基础 103
5.4 自动报警:传递警示信息 106
5.5 自动选择:避免人工判断失误 107
5.6 自动定位、自动对齐:避免安装错误 109
5.7 自动停止:避免严重后果的出现 111
5.8 案例:丰田汽车公司防错法应用 112
6 利器五:KYT危险预知训练,实现人员“零事故” 119
6.1 安全:消除隐患、预防事故发生 120
6.2 KYT危险预知训练:危险分析的班组活动 121
6.3 KYT课题来源:“吓一跳、冒冷汗”事件记录法 122
6.4 小组进行KYT讨论分析的四步法 124
6.5 企业开展KYT活动的五阶段 127
6.6 KYT行动落实:“手指口述”安全确认法 129
6.7 案例:宝泉电路板厂KYT活动纪实 131
7 利器六:动作经济原则,提升现场作业效率 135
7.1 动作改善的故事:吉尔布雷斯与砌砖 136
7.2 动作经济原则:优化动作,提升效率 137
7.3 人体动作改善五原则:作业改善的基础 138
7.4 工装夹具改善二原则:减少疲劳、提升效率 144
7.5 作业环境改善二原则:科学布局、身心舒适 149
7.6 案例:UPS公司如何办理最快捷的运送? 155
8 利器七:OEC管理,实现日常管控的精细化 159
8.1 海尔OEC管理法:日事日毕,日清日高 160
8.2 OEC管理法三大体系之一:目标体系 162
8.3 目标体系的工具:总账、分类账、明细账 163
8.4 OEC管理法三大体系之二:日清控制体系 166
8.5 日清控制体系的工具:日清栏、3E卡、日清表 167
8.6 OEC管理法三大体系之三:激励体系 172
8.7 激励体系的工具:SST(索酬、索赔、跳闸)机制 173
8.8 OEC管理的每日运行:一账、三表、七步骤 174
8.9 案例:OEC管理法在海尔冰箱厂质量管理中的应用 175
9 利器八:精益生产,精细化的生产制造 179
9.1 从“丰田生产方式”到“精益生产” 180
9.2 消除七大浪费,实现精益生产理念 181
9.3 拉动式生产:适时适量适物 186
9.4 看板:拉动式生产的典型工具 187
9.5 流线化生产:实现精益生产的布局方式 192
9.6 单元式生产布局:流线化生产的最佳应用 195
9.7 案例:佳能公司的单元式生产方式 198
10 综合案例:华丰汽车公司现场精细化管理纪实 201
10.1 5S管理为现场自主管理奠定基础 202
10.2 视化助力现场全方位精细化管理 204
10.3 拉动式生产与看板系统实现零库存 206
10.4 U型单元式生产布局提升生产柔性 209
10.5 安灯(Andon)等自动化防错法降低产品不良 210
10.6 全员参与TPM,“我们的设备我们管” 212
10.7 作业优化提升生产加工效率 215
10.8 “创意提案”活动带动全员参与现场改善 217
10.9 KYT危险预知活动落实安全生产零事故 218
- 《管理信息系统习题集》郭晓军 2016
- 《少儿电子琴入门教程 双色图解版》灌木文化 2019
- 《MBA大师.2020年MBAMPAMPAcc管理类联考专用辅导教材 数学考点精讲》(中国)董璞 2019
- 《信息系统安全技术管理策略 信息安全经济学视角》赵柳榕著 2020
- 《卓有成效的管理者 中英文双语版》(美)彼得·德鲁克许是祥译;那国毅审校 2019
- 《危险化学品经营单位主要负责人和安全生产管理人员安全培训教材》李隆庭,徐一星主编 2012
- 《管理运筹学》韩伯棠主编 2019
- 《ESG指标管理与信息披露指南》管竹笋,林波,代奕波主编 2019
- 《战略情报 情报人员、管理者和用户手册》(澳)唐·麦克道尔(Don McDowell)著 2019
- 《穿越数据的迷宫 数据管理执行指南》Laura Sebastian-Coleman 2020