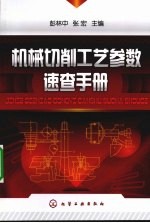
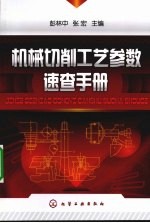
机械切削工艺参数速查手册PDF电子书下载
- 电子书积分:16 积分如何计算积分?
- 作 者:彭林中,张宏主编
- 出 版 社:北京:化学工业出版社
- 出版年份:2010
- ISBN:9787122060495
- 页数:503 页
第1章 机械切削工艺参数基本内容 1
1.1刀具几何参数 1
1.1.1刀具切削部分的组成 1
1.1.2确定刀具几何角度的参考系 1
1.1.3刀具几何角度的定义 2
1.1.4刀具合理几何参数的选择 3
1.2切削用量 7
1.2.1切削运动和工件表面 7
1.2.2切削用量 8
1.2.3切削用量的选择原则 10
1.3工序间加工余量 11
1.3.1加工余量的概念 11
1.3.2影响加工余量的因素 13
1.3.3轴的加工余量 14
1.3.4孔的加工余量 20
1.3.5平面加工余量 27
1.3.6切除渗碳层的加工余量 29
1.3.7齿轮精加工余量 31
1.3.8花键精加工余量 33
1.3.9有色金属及其合金的加工余量 34
第2章 车削加工 40
2.1车刀类型及结构 40
2.1.1车刀的类型及用途 40
2.1.2车刀刀杆的截面形状 40
2.1.3车刀刀杆的悬伸长度 41
2.2车刀切削部分几何参数的选择 41
2.2.1前刀面形状的选择 41
2.2.2几何角度的选择 43
2.2.3刀尖形式(过渡刃)的选择 45
2.2.4断屑槽形的选择 46
2.3常用车刀的类型及尺寸 48
2.3.1高速钢车刀条 48
2.3.2硬质合金焊接车刀 49
2.3.3可转位车刀 61
2.3.4机夹车刀 70
2.4外圆车削工艺参数 93
2.4.1硬质合金及高速钢车刀粗车外圆和端面的进给量 93
2.4.2硬质合金外圆车刀半精车的进给量 94
2.4.3高速钢车刀外圆纵车的切削速度 95
2.4.4硬质合金车刀外圆纵车的切削速度 96
2.4.5刀具寿命改变时车削速度的修正系数 97
2.4.6工件材料改变时车削速度的修正系数 97
2.4.7毛坯表面状态改变时切削速度的修正系数 100
2.4.8刀具材料改变时切削速度的修正系数 101
2.4.9车削方式改变时切削速度的修正系数 101
2.4.10主偏角κr对切削速度的修正系数 101
2.4.11加工铝合金及铜合金的切削速度 102
2.4.12涂层硬质合金车刀的切削用量 102
2.4.13陶瓷车刀的切削用量 103
2.4.14立方氮化硼车刀的切削用量 105
2.4.15金刚石车刀的切削用量 106
2.4.16车外圆工艺参数选用实例 107
2.5内孔车削工艺参数 109
2.5.1内孔车刀 109
2.5.2硬质合金及高速钢镗刀粗镗孔的进给量 110
2.5.3镗孔的其余切削用量及微量调节切深方法 112
2.6切断及切槽工艺参数 113
2.6.1常用切断刀的种类 113
2.6.2常用切断刀的几何参数 116
2.6.3常用切断刀的主切削刃形状 116
2.6.4切槽及切断的切削用量 118
2.6.5常用车槽方法和刀具 120
2.7车细长轴工艺参数 121
2.7.1细长轴的加工特点 121
2.7.2车削细长轴常用装夹方法 122
2.7.3车削细长轴车刀的几何参数 125
2.7.4车削细长轴常用的切削用量和能达到的加工质量 126
2.7.5车细长轴工艺参数选用实例 126
2.8车削薄壁工件的工艺参数 129
2.8.1薄壁工件的车削特点 129
2.8.2防止和减少薄壁工件变形的方法 129
2.8.3正确选择工件的装夹方法 129
2.8.4车削薄壁工件工艺参数选用实例 131
第3章 螺纹加工 133
3.1车削螺纹 133
3.1.1螺纹车刀角度及修正 133
3.1.2螺纹车刀的刀尖宽度尺寸 135
3.1.3螺纹车刀的对刀及安装 136
3.1.4螺纹车削方法 138
3.1.5螺纹车削用量 140
3.1.6车削多头螺纹的分度方法 142
3.1.7车削螺纹时挂轮的计算 144
3.1.8常用螺纹车刀 151
3.1.9车削螺纹工艺参数选用实例 151
3.2用丝锥和板牙加工螺纹 167
3.2.1用普通螺纹丝锥攻螺纹 167
3.2.2锥形丝锥攻螺纹 174
3.2.3其他常用螺纹攻螺纹前钻头直径的确定 178
3.2.4板牙套螺纹 179
第4章 铣削加工 184
4.1铣刀 184
4.1.1铣刀主要几何角度的代号和选择 184
4.1.2铣刀主要结构参数的选择 187
4.1.3常用标准铣刀的类型及规格 191
4.2铣削用量 210
4.2.1铣削用量的定义 210
4.2.2铣削用量的选择 212
4.2.3铣削进给量 213
4.2.4确定铣削用量的常用表格 217
4.2.5铣削用量选用实例 274
4.3铣离合器工艺参数 275
4.3.1铣矩形齿离合器 275
4.3.2铣尖齿离合器 280
4.3.3铣矩齿形离合器 282
4.3.4铣梯形齿离合器 283
4.4铣花键轴工艺参数 284
4.1.1用单刀铣削矩形齿花键轴 284
4.1.2用组合铣刀铣削矩形齿花键轴 286
4.5铣齿轮工艺参数 287
4.5.1铣直齿圆柱齿轮 287
4.5.2铣齿条 287
4.5.3铣斜齿圆柱齿轮 288
4.5.4加工实例 290
4.6铣凸轮工艺参数 294
4.6.1凸轮传动的三要素 294
4.6.2等速圆盘凸轮的铣削 295
4.6.3等速圆柱凸轮的铣削 297
4.7精铣平面 297
4.7.1精铣平面对铣刀的要求 297
4.7.2精铣对工艺系统的要求 298
4.7.3精铣对铣床的要求 299
4.7.4精铣平面的铣削用量 299
4.7.5铝合金的精铣 300
第5章 难加工材料的切削加工 302
5.1高强度钢的切削工艺参数 302
5.1.1高强度钢的切削加工特点 302
5.1.2切削高强度钢的刀具材料 302
5.1.3高强度钢的车削工艺参数 303
5.1.4高强度钢的铣削工艺参数 305
5.2高锰钢的切削工艺参数 306
5.2.1高锰钢的切削加工特点 306
5.2.2切削高锰钢的刀具材料 308
5.2.3高锰钢的车削工艺参数 308
5.2.4高锰钢的铣削工艺参数 308
5.3不锈钢的切削工艺参数 310
5.3.1不锈钢的切削加工特点 310
5.3.2切削不锈钢的刀具材料及几何参数选用原则 310
5.3.3不锈钢的车削工艺参数 311
5.3.4不锈钢的铣削工艺参数 312
5.4高温合金的切削工艺参数 313
5.4.1高温合金的切削加工特点 313
5.4.2切削高温合金的刀具材料 314
5.4.3高温合金的车削工艺参数 314
5.4.4高温合金的铣削工艺参数 318
5.5钛合金的切削工艺参数 319
5.5.1钛合金的切削加工特点 319
5.5.2切削钛合金的刀具材料 319
5.5.3钛合金的车削工艺参数 320
5.5.4钛合金的铣削工艺参数 321
第6章 刨削和插削加工 323
6.1刨刀 323
6.1.1常用刨刀的种类和用途 323
6.1.2刨刀几何参数的选择 324
6.2刨削用量 325
6.2.1刨削用量的定义 325
6.2.2进给量与背吃刀量 325
6.2.3刨削速度 330
6.3刨削薄板工件的工艺参数 334
6.3.1薄板工件的刨削要点 334
6.3.2在牛头刨床上加工薄板工件 335
6.3.3在龙门刨床上加工薄板工件 337
6.4常用强力刨刀及精刨刀的工艺参数 340
6.4.1常用强力刨刀的工艺参数 340
6.4.2常用精刨刀的工艺参数 344
6.5插刀 348
6.5.1插刀的类型与用途 348
6.5.2插刀主要几何角度的选择 349
6.6插削用量 350
6.6.1插削进给量 350
6.6.2插削速度 351
第7章 齿轮加工 353
7.1滚齿工艺参数 353
7.1.1齿轮滚刀的类型与用途 353
7.1.2常用标准滚刀的类型及规格 355
7.1.3切削用量及其选择 360
7.1.4滚齿加工的调整 364
7.1.5滚切大质数齿轮 370
7.2插齿工艺参数 375
7.2.1插齿刀的类型与用途 375
7.2.2常用标准插齿刀的类型及规格 376
7.2.3切削用量及其选择 381
7.2.4插齿加工的调整 385
7.3剃齿工艺参数 387
7.3.1盘形剃齿刀 387
7.3.2剃齿余量的确定 389
7.3.3切削用量及其选择 390
7.3.4常用剃齿方法及比较 391
7.3.5剃齿加工的调整 393
第8章 磨削加工 397
8.1普通磨料磨具 397
8.1.1普通磨料的品种、代号、特性及应用范围 397
8.1.2普通磨料的粒度号及其选择 398
8.1.3普通磨具的硬度及其选择 399
8.1.4普通磨具的结合剂及其选择 400
8.1.5普通磨具的组织及其选择 401
8.1.6普通磨具的强度及其选择 401
8.1.7普通磨具的形状和尺寸的选择 402
8.1.8普通磨具的标志 408
8.2超硬磨料磨具 408
8.2.1超硬磨料的品种、代号及应用范围 408
8.2.2超硬磨料的粒度及其选择 409
8.2.3超硬磨料结合剂及其代号、性能和应用范围 410
8.2.4浓度代号及选择 410
8.2.5砂轮、磨石及磨头的尺寸代号及术语 411
8.2.6砂轮、磨石及磨头形状代号、主要用途 411
8.2.7超硬磨具的标记方法 414
8.3磨削液及磨削工艺 415
8.3.1磨削液 415
8.3.2砂轮的平衡与修整 417
8.3.3磨削用量的选择 419
8.4外圆磨削工艺参数 420
8.4.1外圆磨削用量 420
8.4.2细长轴的磨削 423
8.5内圆磨削工艺参数 429
8.5.1内圆磨削用量 429
8.5.2内圆磨削时砂轮直径选择 434
8.5.3薄壁工件的磨削 434
8.6平面磨削工艺参数 437
8.6.1平面磨削用量 437
8.6.2薄片零件的平面磨削 443
8.7无心磨削工艺参数 445
8.7.1无心磨砂轮和导轮速度 445
8.7.2无心磨粗磨的磨削用量 445
8.7.3无心磨精磨的磨削用量 446
8.7.4切入式无心磨磨削用量 447
8.8高精度低粗糙度磨削工艺参数 448
8.8.1高精度低粗糙度磨削的特点 448
8.8.2高精度低粗糙度磨削时砂轮的选择 449
8.8.3高精度低粗糙度磨削工艺参数的选择 450
8.8.4超精磨削实例 452
8.9高速磨削工艺参数 454
8.9.1高速磨削的特点 454
8.9.2高速磨削时砂轮的选择与修正 454
8.9.3高速磨削的磨削用量选择 455
8.10宽砂轮磨削工艺参数 456
8.10.1宽砂轮磨削的特点和适用范围 456
8.10.2宽砂轮磨削砂轮的选择 456
8.10.3宽砂轮磨削工艺参数的选择 457
8.10.4宽砂轮磨削实例 457
8.11刀具刃磨工艺参数 459
8.11.1刀具刃磨时砂轮的选择 459
8.11.2铣刀和拉刀的刃磨 460
8.11.3铰刀的刃磨 464
第9章 钻孔、扩孔、铰孔 469
9.1麻花钻 469
9.1.1标准麻花钻的切削角度 469
9.1.2标准麻花钻的刃磨和修磨 470
9.1.3高速钢麻花钻的类型和规格 471
9.1.4硬质合金麻花钻的类型和用途 474
9.1.5硬质合金浅孔钻的类型和规格 476
9.1.6扩孔钻的类型和规格 476
9.1.7锪钻的类型和规格 477
9.2中心钻 479
9.3铰刀 479
9.3.1铰刀的结构要素和几何参数 479
9.3.2铰刀主要几何参数的选择 479
9.3.3常用铰刀类型、规格范围及标准代号 482
9.4钻孔的切削用量 484
9.4.1钻孔的进给量 484
9.4.2高速钢钻头钻不同材料时的切削用量 486
9.4.3群钻的切削用量 486
9.4.4小钻头的切削用量 489
9.4.5钻中心孔的切削用量 489
9.4.6硬质合金钻头钻不同材料时的切削用量 491
9.4.7硬质合金可转位钻头(浅孔钻)的切削用量 494
9.4.8扁钻的切削用量 495
9.4.9麻花钻钻深孔时切削用量减少率 498
9.5扩孔及锪钻加工的切削用量 498
9.5.1高速钢及硬质合金扩孔钻的进给量 498
9.5.2锪钻加工的切削用量 499
9.6铰孔的切削用量 499
9.6.1高速钢及硬质合金机铰刀的进给量 499
9.6.2高速钢铰刀的切削用量 500
9.6.3硬质合金铰刀的切削用量 501
参考文献 503
- 《葡萄酒工艺与鉴赏 第3版》廖祖宋 2019
- 《Maya 2018完全实战技术手册》来阳编著 2019
- 《高等教育双机械基础课程系列教材 高等学校教材 机械设计课程设计手册 第5版》吴宗泽,罗圣国,高志,李威 2018
- 《化学工程与工艺专业实验指导》郭跃萍主编 2019
- 《慢性呼吸系统疾病物理治疗工作手册》(荷)瑞克·考斯林克(RikGosselink) 2020
- 《战略情报 情报人员、管理者和用户手册》(澳)唐·麦克道尔(Don McDowell)著 2019
- 《实用内科手册》黄清,阮浩航主编 2016
- 《美物之道 日本手工艺》(日)柳宗悦著 2019
- 《基层医疗卫生机构安全用药手册》黎月玲,熊慧瑜 2019
- 《同仁眼科手册系列 同仁儿童眼病手册》付晶编 2018