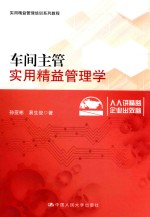
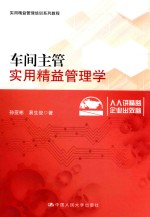
车间主管实用精益管理学PDF电子书下载
- 电子书积分:9 积分如何计算积分?
- 作 者:孙亚彬,易生俊著
- 出 版 社:北京:中国人民大学出版社
- 出版年份:2016
- ISBN:9787300207933
- 页数:197 页
第1章 精益的车间 1
第1节 车间为什么要精益? 3
【案例1】福特汽车的没落 3
【理念1】价值的源头 4
【案例2】日本的精益实践 6
【理念2】精益思想的产生 8
第2节 车间主管的角色 10
【案例1】绝不隐藏问题 10
【理念1】精益推行的主要场所 11
【案例2】丰田的职业导师 13
【理念2】培养精益素养 14
第2章 丰田生产方式 19
第1节 准时化 21
【案例1】拥堵的价值流 21
【知识1】识别价值流 22
【案例2】单件流的问世 27
【理念2】无间断的流程 27
【案例3】保险杠的拉动式生产 28
【理念3】需求拉动式生产 29
第2节 自动化 31
【案例1】人与设备的最初结合 32
【理念1】快速反应力 33
【案例2】金钱线上的浪费 34
【理念2】暂时停止制度 35
第3章 现场环境管理 37
第1节 生产布局合理化 39
【案例1】叉车厂的动线型布局 39
【知识1】单元设计精益化 46
【案例2】模具厂的规范化布局 50
【知识2】现场布局规范化 53
第2节 7S管理 59
【案例1】不可忽视的环境问题 60
【理念1】7S:精益化的基础 61
【案例2】消除7S推行障碍 65
【理念2】7S推行效果管控 69
第4章 物料设施管理 73
第1节 物料管理 75
【案例1】自行车树型BOM图 75
【理念1】生产物料统筹 77
【案例2】追求零库存 79
【理念2】存货控制 80
第2节 基础设施管理 82
【案例1】工具架的定置管理 82
【知识1】定置管理 84
【案例2】日本电装的TPM落实 90
【理念2】全员生产保全TPM 91
第5章 生产操作管理 95
第1节 生产方式选择 97
【案例1】计划管理大变革 97
【理念1】生产计划安排 98
【案例2】面向波动的计划应变 101
【理念2】增加生产的柔性 103
第2节 生产效率提升 107
【案例1】壳体制造的并行工程 107
【知识1】缩短生产周期 109
【案例2】借作业标准书实施改善 115
【知识2】标准化管理 116
【案例3】丰田的看板制度 120
【知识3】目视管理 121
第3节 生产质量控制 126
【案例1】WIP控制与优化过程 126
【理念1】强化标准在制品控制 128
【案例2】混乱的质量控制过程 132
【理念2】全面质量控制的推进 135
第6章 班组建设 141
第1节 精益班组建设 143
【案例1】依靠人而非设备 143
【理念1】精益的深层动力 144
【案例2】日本的精益改善小组 145
【理念2】精益人员组织 146
【案例3】丰田TWI人才培养方案 151
【理念3】精益人才养成 152
第2节 员工士气管理 155
【案例1】“特许”绝不允许 156
【理念1】工作纪律管理 157
【案例2】名企的员工沟通 159
【理念2】沟通管理 161
【案例3】斯瓦伯的交接班引导 163
【理念3】工作交接管理 163
第7章 持续改善 167
第1节 细节与习惯 169
【案例1】花王的利润增长 169
【理念1】从小做起 170
【案例2】单点改善的局限性 171
【理念2】整体化改善 173
【案例3】未能实现预期的改善 174
【理念3】精益改善要落到实处 174
第2节 精益改善机制 176
【案例1】3U备忘录 176
【理念1】问题记录与分析 178
【案例2】大野耐一圈 179
【理念2】从现场发现精益 181
【案例3】海尔日事日清工作法 182
【理念3】日事日清,日清日高 183
第3节 鼓励改善 184
【案例1】不同的提案制度 185
【理念1】精益提案制度 186
【案例2】来自基层的改善 188
【理念2】鼓励基层参与 189
后记 191
参考文献 192
课纲 193
- 《管理信息系统习题集》郭晓军 2016
- 《MBA大师.2020年MBAMPAMPAcc管理类联考专用辅导教材 数学考点精讲》(中国)董璞 2019
- 《信息系统安全技术管理策略 信息安全经济学视角》赵柳榕著 2020
- 《卓有成效的管理者 中英文双语版》(美)彼得·德鲁克许是祥译;那国毅审校 2019
- 《危险化学品经营单位主要负责人和安全生产管理人员安全培训教材》李隆庭,徐一星主编 2012
- 《管理运筹学》韩伯棠主编 2019
- 《中学物理奥赛辅导:热学 光学 近代物理学》崔宏滨 2012
- 《ESG指标管理与信息披露指南》管竹笋,林波,代奕波主编 2019
- 《医学物理学》洪洋 2020
- 《战略情报 情报人员、管理者和用户手册》(澳)唐·麦克道尔(Don McDowell)著 2019
- 《大学计算机实验指导及习题解答》曹成志,宋长龙 2019
- 《中国当代乡土小说文库 本乡本土》(中国)刘玉堂 2019
- 《异质性条件下技术创新最优市场结构研究 以中国高技术产业为例》千慧雄 2019
- 《中国铁路人 第三届现实主义网络文学征文大赛一等奖》恒传录著 2019
- 《莼江曲谱 2 中国昆曲博物馆藏稀见昆剧手抄曲谱汇编之一》郭腊梅主编;孙伊婷副主编;孙文明,孙伊婷编委;中国昆曲博物馆编 2018
- 《中国制造业绿色供应链发展研究报告》中国电子信息产业发展研究院 2019
- 《中国陈设艺术史》赵囡囡著 2019
- 《指向核心素养 北京十一学校名师教学设计 英语 七年级 上 配人教版》周志英总主编 2019
- 《《走近科学》精选丛书 中国UFO悬案调查》郭之文 2019
- 《大学生心理健康与人生发展》王琳责任编辑;(中国)肖宇 2019